在汽车车门钣金的结构设计中,需考虑车门上窗框在密封胶条反力作用下的变形量。在冲压模具制造之前,设计窗框预弯曲以抵消或减小窗框变形量,或者在焊接夹具上设计矫形调节余量,以满足车身外观面差要求。文章据此详细阐述了车门预弯设计的方法思路及某车型应用实例。
1、车门钣金预弯设计行业背景及现状
汽车在人们的日常生活中,已经扮演了举足轻重的地位,而且汽车也由一种交通工具逐步演变为物质生活的必需品。随着汽车工业的多样化发展,消费者对于汽车的消费期望和产品期待也日益攀高,汽车舒适性和外观感觉也是消费者关注的焦点,而车身总成的外观感觉就是消费者最直接的感官因素。
车身总成中,车门同样承担着非常重要的关键要素。汽车车门在汽车白车身中是一个相对独立的总成,是由车门钣金和车门附件组成,车门总成是通过铰链和限位器与侧围连接,并且与车身侧围及翼子板等周边件需满足车型自身标准要求的间隙和面差。为了保证防雨防尘、隔音降噪对密封的要求,在车门总成与车身之间布置一道或两道密封胶条,形成密封空间,但密封胶条的压缩会给车门反作用力,此作用力就是造成车门钣金变形的首要原因。在整个车门系统中,一般上下铰链和门锁啮合处是车门与侧围的三个固联点,车门四周的胶条压缩产生的反作用力是车门钣金变形的主要作用力,由于三个固联点均布置在窗框以下,且形成较稳定的三角形结构,所以车门钣金变形的发生主要在上窗框部位,且成类似线性分布,由车门外板上止口边附近至窗框上沿变形量依次增大(不同车型随着A、B、C 柱截面系数的不同而变形趋势各不相同)。
为了消除或减小实车状态车门上窗框的这种反作用力变形量,目前各汽车制造厂主要有两种处理方式:其一较常用的方法是在焊接夹具上进行矫形调整,操作较为直接,但不易控制,需多次调整并结合实车状态进行反复修正,最终达到理想的状态;其二是在数据状态考虑预变形量,需在钣金设计时进行反向的预变形,主要是基于CAE 分析的窗框变形量为依托,对车门钣金工艺数据进行预弯曲变形处理,以便在钣金冲压模具制作时进行变形量调整,达到实车状态下更为满足车型标准的外观面差。
经过大量数据调研,总结出了各个车系品牌对于车门钣金预弯设计的不同方法和思路:欧美系绝大部分车型采用了第二种方法,设计车门钣金预弯数据;日韩系较大部分车型同样采用了第二种方法;自主品牌车系几乎全部车型都采用了第一种方法,采用焊接夹具矫形方案。具体参见表1(仅示例汽车品牌,具体车型不进行公开)。
表1 车门钣金预弯现状调研
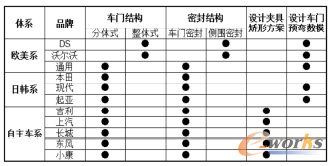
此调研是对各品牌下不同车型大量采集数据对比分析,为表达清晰简明扼要,表1 中列取的是汽车品牌下某一款代表车型的数据,仅仅是大量数据中最具代表性的一组数据。
首先,从车门结构上来分析,分体式内板和整体式内板的车型预弯思路有所不同。整体式车门因门框难以调整,所以几乎所有的整体式车门车型都采用了第二种方案,进行弯数模的设计,在冲压模具阶段进行预弯处理;而分体式车门由于在焊接夹具上可以对窗框Y 向做一定矫形调整,因此分体式车门设计的车型大部分都采用第一种方案,没有设计预弯数模,也有少部分采用第二种方案。
其次,从车系区别上来看,欧美系和日韩系方案较为统一,自主车系与之不同。欧美系和日韩系车型,不论分体车门还是整体式车门,绝大部分采用第二种方案,设计预弯3D 数模,但其中本田某车型因密封胶条反作用力较小,对钣金的挤压变形也很小,所以没有采取任何预弯处理;自主系车型大多是分体式车门,且均采取第一种方案措施,进行焊接夹具的矫形调整,这种情况可能跟自主厂家大多没有掌握车门3D 数模预弯的设计方法有关。
2、必要性与优点
从此次调研结果来看:对于整体式车门,由于面差调试困难,强烈建议设计预弯3D 数模;对于分体式车门,如果密封条作用力很小,设计上可以不做预弯数模,如果密封条作用力大,窗框变形量大于1mm 的,为避免矫形带来尺寸的不稳定,也需要设计预弯3D 数模。总而言之,预弯3D 数模的设计主要是为了抵消由于密封条反作用力对窗框的挤压变形,同时避免了繁琐的焊接夹具矫形调整。
为了能够直观了解密封胶条对于车门钣金挤压变形的影响程度,结合某款双道密封的上市车型,如图1 所示进行了如下一项试验,间隔200-300mm 测量除门槛位置的32 个选点的面差数据:
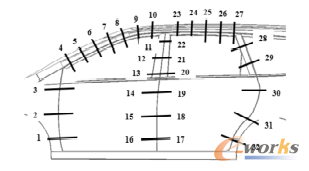
图1 密封条作用力对车门变形的影响
首先拆除车门头道密封条和侧围门框密封条,并测量前后车门周圈与侧围的面差,每间隔200-300mm 共选取32 个点进行测量并记录,标记为A 组数据,详细见表2(前后门分开测量,即测量前门时后门需安装两道密封条,测量后门时前门需安装两道密封条)。
表2 拆除两道密封条测量面差值
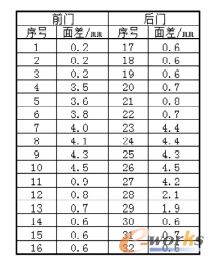
其次安装上车门头道密封条,并测量前后车门周圈与侧围的面差,每间隔200-300mm 共选取32 个点进行测量并记录,标记为B 组数据,详细见表3(前后门分开测量,即测量前门时后门需安装两道密封条,测量后门时前门需安装两道密封条)。
表3 仅安装车门头道密封条测量面差值
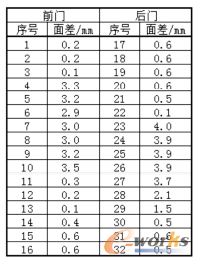
然后再安装侧围门框密封条,并测量前后车门周圈与侧围的面差,每间隔200-300mm 共选取32 个点进行测量并录,标记为C 组数据,详细见表4(前后门分开测量,即测量前门时后门需安装两道密封条,测量后门时前门需安装两道密封条)。
表4 安装两道密封条测量面差值
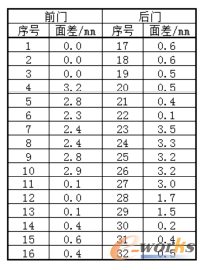
对以上三组测量数据进行整理总结,可以得到单独头道胶条对车门钣金挤压变形的影响量以及两道密封条共同作用对车门钣金挤压变形的影响量,详细见表5。
表5 密封条对车门钣金挤压变形影响量
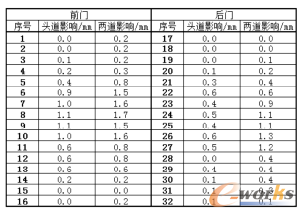
通过表5 数据,可以直观的看到该车型密封胶条作用力对车门钣金的挤压变形程度及主要变形区域。数据显示该车型密封条挤压前门钣金变形量主要分布在0.3mm至1.7mm范围内,后门钣金变形量主要分布在0.1mm 至1.3mm 范围内,前门钣金变形量较大;前门头道胶条作用力影响变形程度大于门框胶条约占70%,后门头道胶条作用力影响变形程度与门框胶条相当均占50%;超过1.0mm的变形量主要分布在前后门上窗框部分,靠近门锁啮合点及铰链部位变形量最小。
实车状态下,超过1mm 的变形量已经是肉眼可以分辨的范围内了,1mm外观面差的偏差也已经达到影响车辆外观品质体验的程度,所以在CAE 分析密封胶条挤压作用时,通常我们将车门钣金超过1mm 变形量作为需要进行钣金变形处理的基准。钣金变形处理的思路方法前文也进行了粗略介绍,主要是焊接夹具矫形调整方案和3D 数模预弯处理方案,或者两种方案结合实施也是比较明智的选择,同时两种方案的优缺点也是显而易见的。
第一种方案采用焊接夹具矫形调整的弊端较多,稳定性不是很好,需要配合返修来解决面差的问题,而且矫形量与收益是不对等的,矫形1mm 才能获得0.5mm 的收益,矫形量越大效果越不稳定,而第二种方案设计预弯3D 数模有利于减少甚至消除车门焊接夹具矫形调整量,避免由于调整量太大引起不稳定,所以车门钣金设计预弯数模才是车门设计发展趋势,特别是自主车系的汽车厂家迫切需求掌握这门设计方法。
3、车门钣金预弯设计的方法介绍
车门钣金3D 预弯数模的设计方法一直是大部分自主车系汽车厂家未知的领域,所以相关技术知识是各大自主车企努力探索的方向。事实上,车门钣金预弯设计的方法虽然比较复杂繁琐,但却也是条理清晰的,它是完全依托CAE 分析结果进行的一种逆向思维的计算方法,主要包括以下几个阶段。
3.1 车门钣金数据挤压变形CAE 分析
一款车型的车门钣金是否需要进行预弯曲变形处理,首要的决定因素就是车门钣金变形CAE 分析结果。首先,需要提供给CAE 分析部门车门钣金及侧围原始3D数据、分析方法关键要素和相对应的约束条件。原始数据主要包括车门钣金焊接总成、车门上下铰链、车门锁体及锁扣总成、车门头道密封条总成、门框密封条总成、侧围钣金焊接总成以及相应的连接件和焊点信息。关键要素主要包括铰链轴线、密封条压缩负荷及压缩方向。约束条件主要是上下铰链安装点和门锁啮合点三处固联点。

如图2 所示,CAE 分析中将上铰链安装点、下铰链安装点及门锁啮合点三处固联点固定,在头道密封条和门框密封条密封压缩区域(或上铰链以上至门锁之间区域)对车门钣金施加均布载荷,载荷大小同胶条压缩载荷相当。通过CAE分析软件,计算出车门钣金各个点的位移量图,并用不同颜色表示位移大小区间,如图3。
3.2 制作预弯曲数据
预弯数据制作过程是最为复杂的一个步骤,是根据钣金变形量的CAE 分析结果逐步调整修改,最终拟合出与位移后数据偏差最小的预弯3D数据。
本文来源于互联网,e-works本着传播知识、有益学习和研究的目的进行的转载,为网友免费提供,并以尽力标明作者与出处,如有著作权人或出版方提出异议,本站将立即删除。如果您对文章转载有任何疑问请告之我们,以便我们及时纠正。联系方式:editor@e-works.net.cn tel:027-87592219/20/21。