表面安装技术(又称为SMT, Surface-mount technology),是一种电子装联技术,是目前电子组装行业里最流行的一种技术和工艺。本文介绍了SMT技术的发展历程、工艺流程、智能化设备等内容。
一、SMT简介
表面安装技术(又称为SMT,Surface-mount technology),是一种电子装联技术,是目前电子组装行业里最流行的一种技术和工艺。这种技术是在PCB焊盘上印刷锡膏,然后放上表面贴装元器件,再经过回流焊使锡膏熔化,让各元器件与PCB板焊接装配的技术。其中的元器件又被简称为表面安装元件(SMD,surface-mount devices),包括电阻、电容、晶体管、集成电路等等。
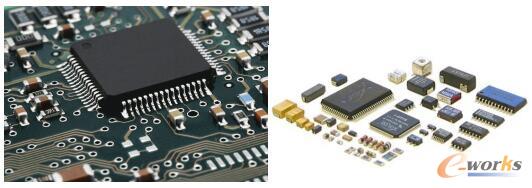
采用SMT技术的PCB板(左)及表面安装元件SMD(右)
二、SMT发展
SMT起源于20世纪60年代,最初由美国IBM公司进行技术研发,之后于80年代后期渐趋成熟,成为了主流的电子产品元器件安装技术。在此之前,通孔插装技术(THT,Through-hole technology)是主要的安装技术,通孔插装技术起源于50年代,在50年代到80年代之间流行,后其应用逐渐减少,但其无法被完全取代,目前仍有应用。采用THT技术安装的元件也叫THD(Through-hole devices)。
通孔插装技术不同于SMT技术,且非常易于区分,如下图中,左侧是通孔插装技术焊接的元件。采用THD焊接的元件,其引脚完全贯穿了PCB板,在PCB板的另一面,可以看到元件的引脚伸出板面。而右侧采用SMT技术的元件,则只是焊接在PCB表面,其引脚没有穿过PCB板,故在PCB板的另一面,看不到任何引脚。
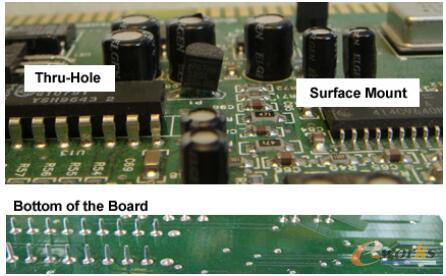
通孔插装技术与表面安装技术
进入20世纪90年代以来,全球采用通孔组装技术的电子产品逐年下降,而采用SMT的电子产品则快速增加。
我国SMT的应用起步于80年代初期,最初从美、日等国成套引进了SMT生产线用于彩电调谐器生产。随后SMT技术应用于录像机、摄像机及袖珍式高档多波段收音机、随身听等生产中,如今在计算机、通信设备、航空航天电子产品中也得到广泛应用。
三、SMT优点及缺点
SMT技术优点:
●电子产品体积小,重量轻
●采用SMT的电路板可靠性高、抗振能力强
●焊点缺陷率低
●高频特性好
●生产流程易于实现自动化,可提高生产效率
●降低成本,节省材料、能源、设备、人力、时间等
SMT技术缺点:
●不适用于大型,高功率或高压部件
●维修困难,需要熟练的操作人员和更昂贵的工具
●焊脚小,焊接可靠性降低
●SMD元件小,元件表面标记字符不易读取
四、SMT工艺流程
1.SMT工艺流程分类
根据电子元器件的不同和产品的需要,元器件在PCB上的焊接状态主要分为单面全贴、双面全贴、单面混装、双面混装等。
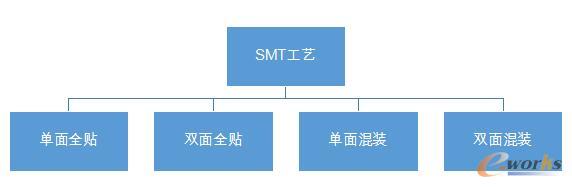
SMT工艺分类
单面全贴,即全部表面贴装元器件在PCB的一面。
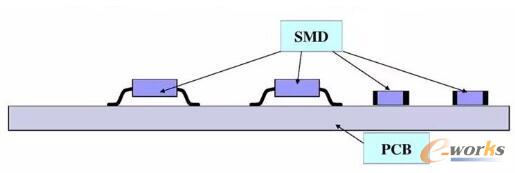
单面全贴示意图
双面全贴,即表面贴装元器件分别在PCB的A、B两面。双面全贴PCB保证了PCB板的美观性和功能性,充分利用PCB板空间,实现PCB板面积最小化。
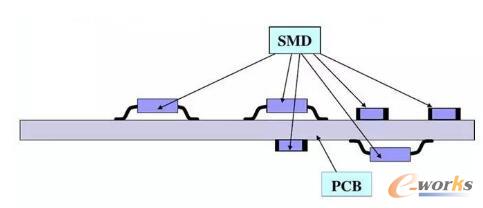
双面全贴示意图
单(双)面混装,是指除上述两种情况之外的,在PCB上除了表面安装元件(SMD)外,还有过孔插装元件(THD)。单面混装是指插件和表面贴装元器件都在PCB的单面,双面混装则是插件和表面贴装元器件在PCB的两面。
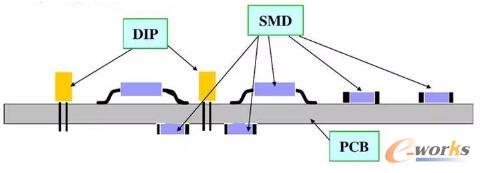
双面混装示意图
这里说明一下,为什么叫混装。混装主要指的是PCB上既有表面安装元件SMD,又有过孔插装元件THD。由于这两种元件的焊接工艺不同,因此做了区分。SMD元器件一般采用回流焊接,而过孔插装元件THD一般采用波峰焊接。两种焊接工艺如下图所示。过孔插装元件一般是将元件插装在PCB板上后,将PCB板的下面浸入到熔融焊槽,让熔融焊料与引线接合,完成焊接。而回流焊则采用专用设备回流焊炉焊接,下文将作详细介绍。
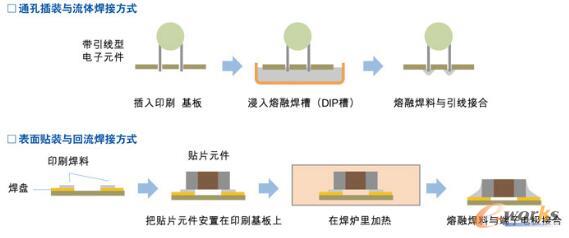
通孔插装与表面安装的焊接方式示意图
2.SMT主要工艺介绍
单面全贴的SMT主要工艺分为三步:施加焊锡膏、贴装元器件(也称贴片)、回流焊接。在实际的生产过程中还会安排AOI检测等环节。下面分别介绍预涂锡膏、贴片、回流焊的工艺过程。
第一步:施加焊锡膏
其目的是将适量的焊膏均匀的施加在PCB的焊盘上,以保证贴片元器件与PCB相对应的焊盘在回流焊接时,达到良好的电气连接,并具有足够的机械强度。
常温下,由于焊膏具有一定的黏性,可将电子元器件粘贴在PCB的焊盘上,在倾斜角度不是太大,也没有外力碰撞的情况下,一般元件是不会移动的,当焊膏加热到定温度时,焊膏熔融再流动,液体焊料浸润元器件的焊端与PCB焊盘,冷却后元器件的焊端与焊盘被焊料互联在起,形成电气与机械相连接的焊点。
下图为锡膏印刷示意图。在PCB板上覆盖一块模板(也称钢网),模板上对应PCB焊盘的位置有开口,刮刀将锡膏刮动时,锡膏由模板开口进入,并附着在下方的PCB焊盘上,取下模板,则PCB板焊盘上就完成了锡膏印刷的过程。
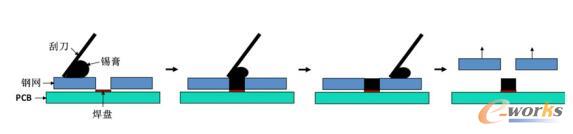
锡膏印刷截面图
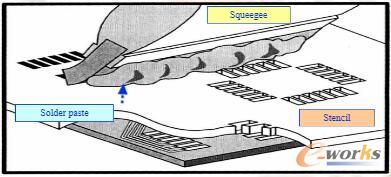
锡膏印刷示意图
第二步:贴装元器件
本工序是用贴片机或手工将片式元器件准确的贴装到印好焊膏的PCB表面相应的位置。贴装方法有两种,采用贴片机贴片以及采用手工贴片。
贴装机贴片生产效率高、设备投资大,适合批量较大、供货周期较紧的情况。
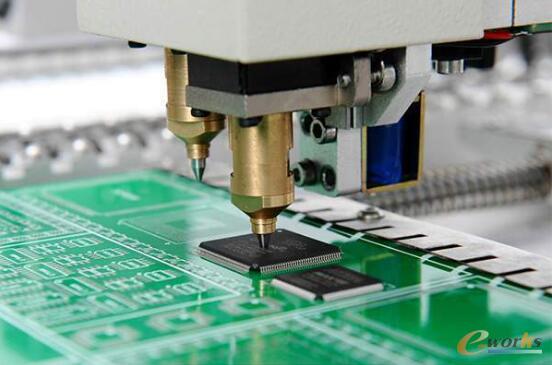
贴片机贴片
手工贴片操作简便、成本较低、生产效率须依操作的人员的熟练程度,适合中小批量生产。人工手动贴装主要工具:真空吸笔、镊子、IC吸放对准器、低倍显微镜或放大镜等。
第三步:回流焊接
回流焊的本质就是“加热”,其工艺核心就是传送带的速度和回流温度曲线的设定。传送带的速度决定了每阶段的加热时间。回流温度曲线,根据功能可划分为4个区,即预热区、保温区、回流区和冷却区。以下是典型的SMT温度特性曲线。
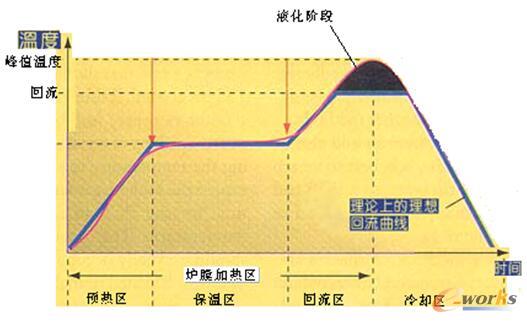
回流焊温度曲线
预热:将PCB温度从室温提升到预热温度。这时,焊膏中的溶剂和气体蒸发掉,助焊剂润湿焊盘、元器件端头和引脚。焊膏软化、塌落、覆盖了焊盘,将焊盘、元器件引脚与氧气隔离。
保温:使所有元件充分预热,达到一致温度,特别是较大的元器件,并保证助焊剂充分挥发,以免不同元件之间的温差造成焊接不良。
回流:这一阶段温度迅速上升,焊膏达到熔化状态,液态焊锡对PCB的焊盘、器件端头和引脚润湿、扩散、漫流或回流混合形成焊锡接点。
冷却:PCB进入冷却区使焊点凝固。
双面全贴、单(双)面混装在此基础上,增加了其他工艺,更为复杂。如下图为双面全贴的工艺流程,增加了翻面,同时要采用两次回流焊。
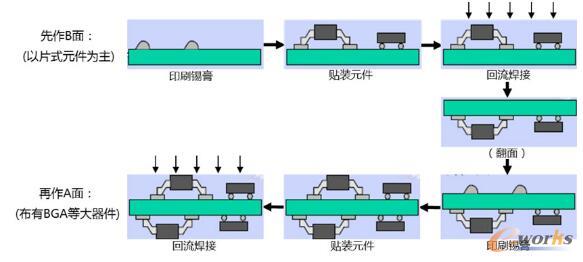
双面全贴的工艺流程
下图为单面混装流程,在回流焊之后,安装插孔元件,再采用波峰焊。对于混装流程,专门发展出了先进的混装工艺,如选择性焊接、通孔回流焊和使用屏蔽模具等方式,能够极大地提高混装效率。
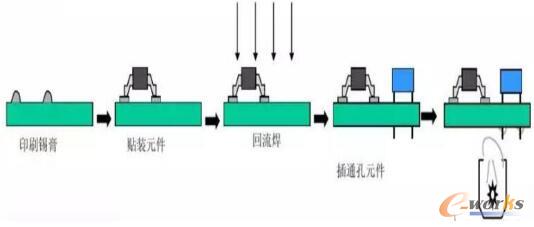
单面混装流程
五、SMT设备
SMT生产线通常包括以下设备:贴片机、锡膏印刷机、回流焊炉、波峰焊、检查设备。
贴片机:又叫拾放机,是SMT生产线的核心设备,把元器件拾起后放置到印刷板上。衡量指标有:贴片速度、精度和智能性等。
锡膏印刷机:用于焊膏印刷到PCB上。可分为半自动焊膏印刷机与全自动焊膏印刷机。
回流炉:把PCB上用于焊接元器件的焊膏熔化并形成优良的焊接。
波峰焊:用于焊接通孔插装元器件。
检查设备:检查生产过程的不良,如SPI设备、AOI设备。
典型的生产线示意图。
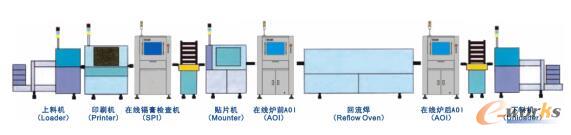
SMT典型生产线示意图
六、SMT智能化应用
SMT生产线正朝着高品质、高效率、高稳定性、柔性化、信息化、无人化、可视化的方向发展。整个SMT行业的发展离不开各个设备厂商、软件厂商的协同发展,在各个生产工序,出现了一些新型的智能化产品,为SMT产线的智能化发展打下基础。
1.贴片机
贴片机是SMT产线首要核心设备,用来实现高速、高精度、全自动贴放元器件,关系到SMT生产线的效率与精度,是最关键、最复杂的设备。众多设备里贴片机成本往往会占到整条生产线投资额的60%以上。
贴片机的贴装速度极快,通常需要专人实时照看,负责及时上料。现在,有些智能化的贴片机配备了自动AGV小车,可以实现自动上料,如FUJI Smart Factory Platform NXTR。该产品借助新研发的传感器技术和智能加载车,密切对应排产计划、进行全自动补料和全自动换线,实现表面贴装工序中零贴装不良、零作业员、零停机目标,是智能化生产的代表性产品。
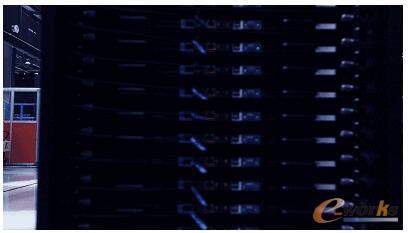
贴片机自动上料(动图)
2.回流焊
回流焊接设备正朝着高效、多功能、智能化的方向发展,出现了具有独特的多喷口气流控制的回流焊炉、带氮气保护的回流焊炉、带局部强制冷却的回流焊炉、可以监测元器件温度的回流焊炉、带有双路输送装置的回流焊炉、带中心支撑装置的回流焊炉等。除了上述这些新型回流焊炉外,智能化回流炉也已经出现了,其调整运转由内置计算机控制,在window视窗操作环境下可很方便使用键盘或光笔输入各种数据,又可迅速地从内存中取出或更换回流焊工艺曲线,节省调整时间,提高生产效率。
3.3D SPI
SPI(Solder Paste Inspection)主要的功能就是以检测锡膏印刷的品质,包括体积,面积,高度,XY偏移,形状,桥接等。此工序可以在贴片前尽早将印刷不良拦截,降低维修成本,实现过程控制。传统的SPI设备采用的是2D检测方式,只能从获取锡膏的平面图像,对于高度方向的印刷缺陷无法识别,而3D SPI能够获取锡膏的3D图像,更全面地对锡膏的质量进行判断,减少误判。该技术的代表产品有韩国PARMI在线3D SPI锡膏检测仪,其运用Laser(激光三角测量技术)的检测原理进行检测。
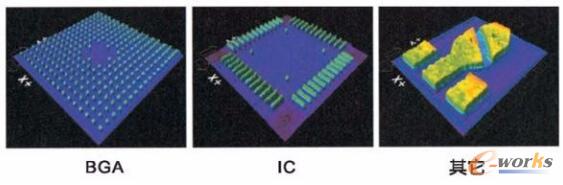
3D SPI 检测成像
4.3D AOI
AOI检测设备在回流焊工序之后,采用机器视觉实现焊接后的产品检测。如今,元器件的尺寸越来越小,如03015(0.3毫米x0.15毫米)的微贴片元件,一般的2D AOI难以检测如此小尺寸的元器件不良。现在,三维AOI正在发展成熟,它可以检测出2D AOI无法检测出的微小元器件的焊接不良。代表性的产品有矩子JUTZE在线AOI自动光学检查机。
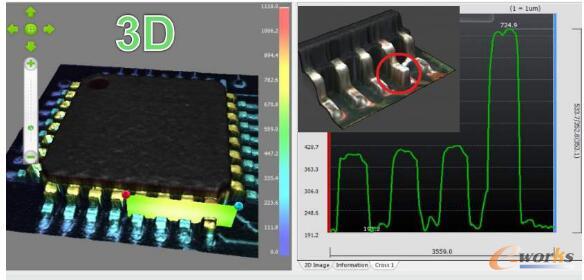
3D AOI检测
5.离线编程
在SMT生产中,仍有一些流程需要手工操作才能导入新产品,需要根据工程师的经验调整流程参数。通常,需要将PCB导入生产线进行首次测试,在每个工艺步骤后进行目视检查,并根据结果进行调整。这些任务占用机器的正常生产,并需要更多的物料进行测试,这大大降低了生产设备的利用率。
对于智能工厂而言,可以根据软件系统来进行虚拟生产,而无需真实产线和物料即可完成这些测试。例如,通过ASM Printer Programming(DEK Offline Programming)能够实现离线编程,程序员可以用SIPLACE Pro里已经存在的板子去编辑DEK印刷机程序。通过这种方式,可以在不占用印刷机的情况下进行编程,从而使生产设备达到更高的利用率。
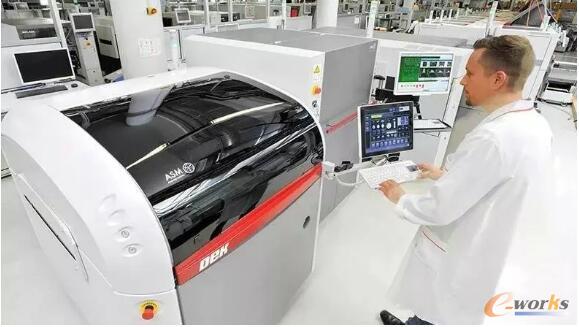
印刷机离线编程
本文为e-works原创投稿文章,未经e-works书面许可,任何人不得复制、转载、摘编等任何方式进行使用。如已是e-works授权合作伙伴,应在授权范围内使用。e-works内容合作伙伴申请热线:editor@e-works.net.cn tel:027-87592219/20/21。