通过围绕航天复杂机电产品开展基于模型的系统论证分析和方案设计工作,不仅可以助力补齐前述航天产品依托系统模型开展型号正向研制的技术短板,还有助于构造系统、分系统、单机设备之间数据交互链路,从而最终形成支撑型号研制工作全过程的单一真相源及其数字主线。
1 前言
随着信息技术的飞速发展,利用各类数据资产实现管理模式、创新模式、研制模式、运营模式、服务模式、保障模式的创新已成为企业在激烈复杂市场环境下的不二选择,全球国防军工领域标杆企业无一例外地致力于以此打造自身全方位的竞争优势。为此,美国国防部于2018年6月正式发布《国防部数字工程战略》,用以指导整个行业数字工程转型的规划、开发和实施,并推动从以文档为中心的线性采办流程向以数字模型为中心的数字工程生态系统的转变,次年又发布了以规范化模型开发及集成应用、可持续验证的真实信息源、配套支撑架构和环境以及模型与实物有效融合等为核心内容的《国防部数字现代化战略》。在此背景下,国内航天领域科研院所也致力于基于模型的系统工程在相关型号的推进和探索工作,并有效地促进了箭、弹、星、船、器各类航天产品正向研制能力的有效提升
[1][2][3]。
另一方面,国内航天领域既往基于模型的系统工程实践多集中在系统、分系统乃至体系层级,涉及单机设备的探索实践仅见诸若干文献
[4][5],而围绕航天复杂机电产品的探索更鲜有述及。这一方面使得作为单一真相源的系统、分系统模型无法在实际型号研制的全过程发挥更大的作用,同时也无法形成通过各层级系统模型串接和驱动的型号研制完整过程和数据交互链路,难以更好地满足型号产品数字化交付的迫切要求。
通过围绕航天复杂机电产品开展基于模型的系统论证分析和方案设计工作,不仅可以助力补齐前述航天产品依托系统模型开展型号正向研制的技术短板,还有助于构造系统、分系统、单机设备之间数据交互链路,从而最终形成支撑型号研制工作全过程的单一真相源及其数字主线。
在前期航天复杂机电产品基于模型的系统工程实践中,MBSE实施团队从系统论证分析和方案设计过程入手,开展了一系列有益的探索和尝试。本文给出了围绕这些探索和尝试的阶段性总结,其中第2节介绍了航天复杂机电产品基于模型系统工程实践所关注的问题及其总体目标,第3节介绍了围绕航天复杂机电产品基于模型的系统论证和方案设计过程所做的工作及其配套MBSE协同平台相关成果,第4节作为本文的总结与结论给出了前期工作突破的技术瓶颈、相关成果、工作体会以及后续工作考虑。
2 制约航天复杂机电产品研制的瓶颈问题及MBSE业务目标
一个重要的航天系统会由大量的单机设备组成,每个单机设备都是一个复杂的机电产品。以往在单机设备上或多或少可以找到国外引进开发的痕迹,说明我们更多进行的是逆向工程,仿制跟研。如今我国在航天领域取得了长足的发展,从跟跑到并跑再到领跑,有些领域已“前不见古人”,传统的开发模式也难以适应新时代对我国航天装备的研发需求。
航天复杂机电产品目前存在的制约研制效率和交付质量、影响产品研制成本的若干瓶颈问题主要包括:
1)知其然不知其所以然,产品缺少正向设计过程的推演分析,难以提升系统方案论证、分析、设计的质量与效率;
2)只关注总体的性能指标,缺少对产品需求的全面论证与分析,对更改的影响域分析与需求的追溯和闭环不够;
3)基于文本的信息交互难以有效支持跨层级、多专业的高效协同设计,难以实现产品快速迭代设计;
4)设计师的知识和经验碎片化的存储方式难以实现围绕产品研制相关知识的有效管理,无法实现这些知识的有效传承和高效利用。
为了有效提升复杂机电产品需求分析、系统论证与方案设计、数字化协同设计与验证、嵌入式软件开发与实现、设计资源共享与重用等各环节的工作效率和交付质量。其总体要求涉及:
1)以构建系统模型为核心,形成从需求出发进行系统设计的正向开发流程;
2)与实际工作相结合分析系统建模所涉及的具体组成要素、形成系统模型的描述方式、构建方法,并形成指导后续系统建模的参考模型和模型模板;
3)打造基于模型的协同开发环境,打通各工程软件的信息和数据接口,构建由模型驱动的、支持跨层级、跨专业协同工作的新型研制模式;
4)对设计过程用到的知识和业务流程进行封装,构建支撑业务需求的模型资源库,实现知识的固化和重用。
3 航天复杂机电产品基于模型的系统工程实践
基于上述MBSE业务目标,并结合国内外标杆企业MBSE建设经验,提出了如图1所示的MBSE应用框架,其中除了涉及模型构建和应用过程外,还涉及模型资源库、工程开发软件和信息系统等支撑手段以及支撑跨层级、跨专业协同设计的MBSE协同研发平台。
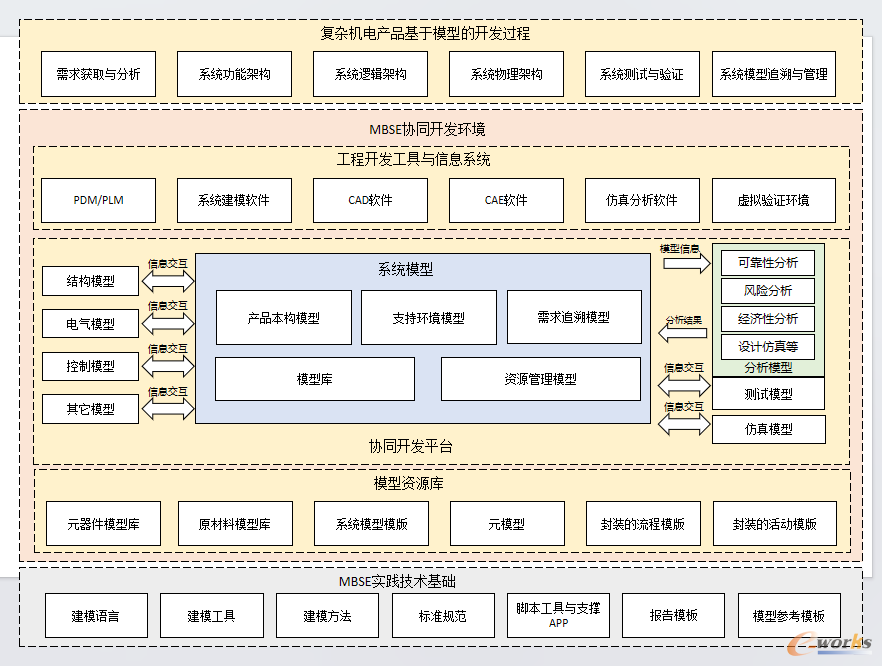
图1 复杂机电产品系统模型应用综合架构
航天机电产品在MBSE应用上,与航天工程大系统还是有一定的差异。大系统更关注的是业务需求获取和定义的过程,航天机电产品作为系统的单机,更侧重将系统定义的黑盒向白盒展开的过程。因此在航天复杂机电产品的系统建模上,选取了SysML语言,参考MagicGrid的方法论,结合工程实际,突出业务重点,开展了探索应用工作。
3.1 建模流程
●需求获取及分析
根据总体单位下达的任务需求文档进行条目化整理,以需求表的形式构建顶层输入需求;用模块定义图对利益相关方、系统周边环境进行分析和描述,同时以用例图和活动图对产品应用场景进行展开分析和描述;以内部模块图对产品与周边环境的交互关系进行分析和描述。整个过程是个循环迭代的过程,直至得到较为全面的描述产品的系统需求模型。
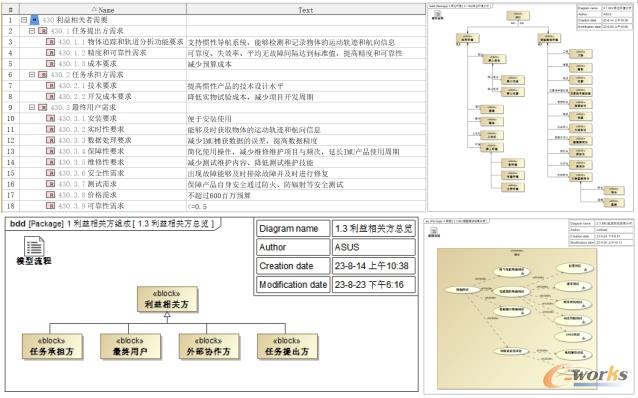
图2 任务需求、周边环境、利益相关方、用例示意图
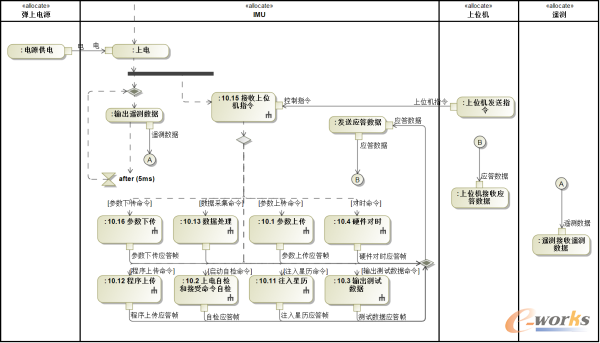
图3 弹上应用场景下地面运行活动图示例
●系统功能分析
由于航天机电产品的承研单位一般都是专业配套所,经过多年积累已经形成了若干成熟的系统功能架构和支撑单元,这些都是从需求导向设计的工程基础,一般我们会把它们建成基础模型库,便于新产品设计时进行调用。通过活动图对用例以下的功能活动进行细化分析和描述,得到产品功能层的组成,同时将功能层的组成作为泳道继续丰富其他内部活动流程。在此基础上,整理得到系统的功能架构并得到其内部组成的交互关系(图4)。
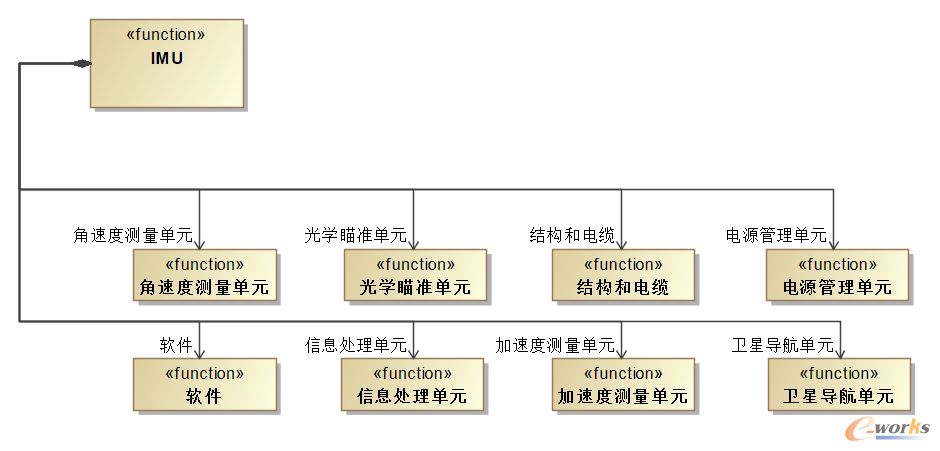
图4 产品功能层组成
●系统逻辑构架设计
航天机电产品的承研单位在工程实践过程中,形成了很多三化产品,这些标准化的产品具有明确的逻辑架构,在做新产品设计时,要充分利用已形成的三化资源,降低新产品的开发风险。通过对三化设计资源的配置,再补齐其他部组件的逻辑接口,从产品功能架构进行进一步精化得到逻辑架构(图5)。
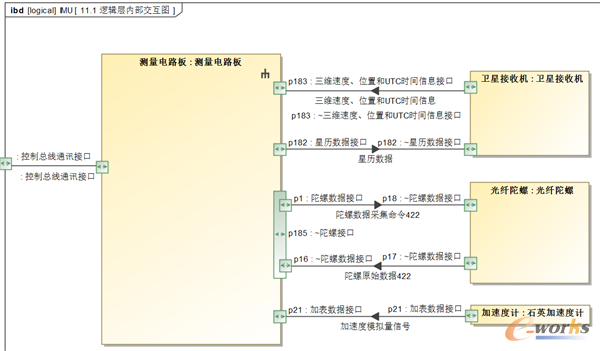
图5 逻辑层接口交互示例
●系统物理架构设计
从产品逻辑架构向物理架构演化的过程,需要注意的是该过程无法仅仅依赖系统设计师独立完成,需要分部件的主管设计师、结构、电路的专业设计师一起协同完成。这个过程不仅仅是专业设计师需要采用专业的建模工具软件,对于系统设计师来说也需要更专业的开发工具来辅助开发。对于复杂机电产品来说,内部电气互联关系的定义一般是由系统设计师完成的。这个阶段的产品电气设计模型就需要细化到电缆一级,电缆不再是模型中的一根连线,而是一个内部模块,如图6所示。

图6 电气设计IBD图
在细化电气设计上使用系统建模软件开发效率不高,因此我们开发了配套的辅助设计App,电气辅助设计工具能读取系统模型的电气设计IBD图,解析得到各分部件的电气互联关系,利用工具内部的模型库,可以提供图形化的视图辅助进行电连接器的选型。同时工具还可以对电连接器的型号、点号数量、针孔、接插匹配关系及信号的输入输出匹配关系进行错误检查,避免设计师的低级错误。
●分部件技术要求的综合
分部件的技术要求分布在各层级的若干张BDD、IBD及参数图中,无法向下级单位或设计师传递,还需要进行分部件技术要求的综合汇总。构建分部件的技术要求模版,模版内是需求条目,在系统模型构建过程中,不断地将设计得到的功能要求、接口定义要求、分配的性能指标、设计约束等信息与对应分部件的相关需求条目建立追溯关系,最终形成分部件的需求表。
●建立追溯关系
在系统模型构建过程中,使用追溯矩阵建立系统需求与用例、功能与活动、逻辑与功能等之间的追溯关系,通过追溯图我们可以对需求及其相关元素的追溯关系进行清晰的浏览(图7)。
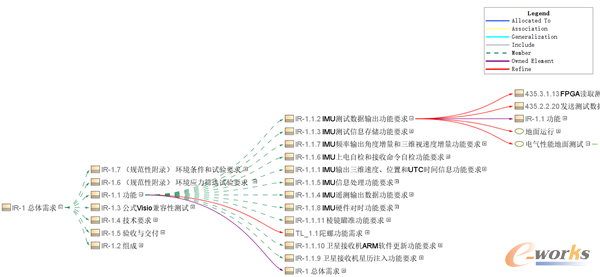
图7 全流程需求追溯(局部)
为了方便设计师开展系统建模活动,还构建了向导式的建模流程模板,如图8所示。其中给出了所涉及的各个步骤以及这些步骤可以参考或复用的模板、样例和模型库等内容。
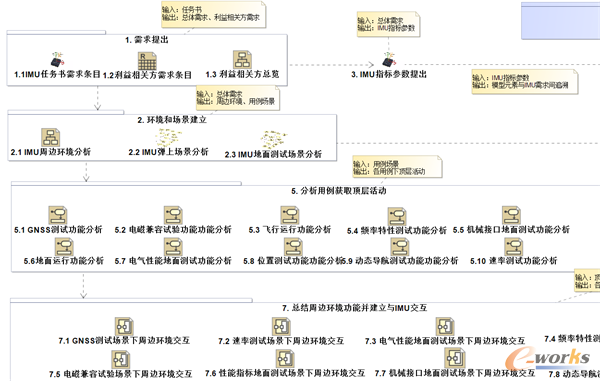
图8 基于模型向导式的系统论证分析和方案设计过程
3.2 MBSE协同平台
复杂机电产品的设计是由多专业的设计师共同完成的,考虑到系统模型、各个专业领域模型相互之间密切的信息交互关系,还需要构建MBSE协同平台,打通各工程开发软件和信息化系统之间的信息和数据接口,支持跨层级、跨专业的协同研发工作。
MBSE协同平台可以实现需求追溯与管理:涉及通过解析系统模型在平台上向分部件设计师发布任务需求,并对设计结果与需求进行追溯管理;平台可以实现基于流程驱动的协同设计:涉及打通与PDM、系统建模工具、结构设计工具、电路设计工具以及物理场仿真分析工具的信息接口,通过对开发流程和各个环节设计活动的封装,实现了模型格式的自动转换、数据自动填充、信息自动提取和报告自动生成;平台可以实现对设计仿真数据和模型的管理:涉及对开发过程中迭代的模型进行版本控制;平台可以实现对模型资源库的管理:涉及专业开发用到的元器件、原材料模型,以及系统建模用到的元模型、分部件三化模型、分部件技术要求模版模型等。
通过MBSE协同平台建设,形成了衔接系统总体及其相关专业的协同工作环境,实现了系统模型和相关专业领域模型间的数据信息的协同交互。图9给出了MBSE设计仿真平台在型号研制过程中承担的作用。
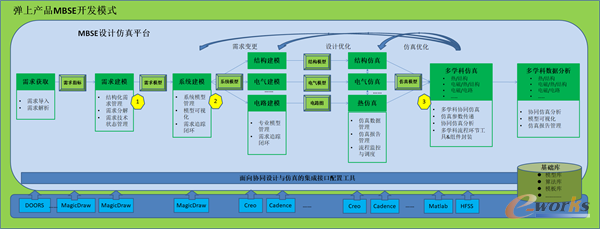
图9 以MBSE协同平台为支撑的产品研制过程
4 体会与展望
通过前期围绕复杂机电产品的MBSE实践和有益探索,基本掌握了系统与各专业一体化建模与信息交互、基于模型的系统分析与验证、模型信息交互、工具链集成等关键技术,基本解决了如何基于系统模型开展需求论证与分析、进行系统方案论证与设计、助力不同专业领域的模型交互与协同开发、促进型号开发模型知识有效传承和高效利用、实现MBSE开发模式与型号研制过程有机融合等问题。
围绕前期实践工作的主要体会:
1)系统模型不能独立于产品研制过程,必须围绕产品研制关键问题去充分发掘系统模型的价值与作用,避免目标不清晰、方向不明确而导致的为建模而建模的情况发生;
2)基于模型的系统工程与复杂机电产品研制过程的融合,其本身就是一个复杂的系统工程,它不仅涉及建模语言、建模工具等技术方面的工作,还涉及项目策划、过程规划、模型规划、管理要求、型号支撑、数据准备、工具链贯通等多个方面的规划和推进,唯有如此方有可能经过努力后达到预期的目的;
3)基于模型的系统工程实践是一个只有开始没有结束的长期实践,既无法一蹴而就也不存在可以直接照搬照抄、直接借鉴的普适性案例,必须围绕明确的目标、聚焦关键的型号研制问题,开展长期的努力和反复的探索,才有可能分阶段达到预期的效果;
4)在具体实践过程中,需避免将建模工作与实际研制工作人为地割裂开来的情况,努力促进相关人员深入掌握模型构建和模型应用所需的关键技能,才有可能切实形成将专业建模能力转化为模型综合应用的能力。
开展MBSE工作对于研发单位有三点价值:
1)助力树立正向设计的价值导向
采用MBSE的设计方法和理念就是要建立从需求出发的正向设计的价值导向,我国航天事业从跟跑到并跑,如果还要到领跑,困扰的不仅是技术问题,更是方向问题。方向来源于问题导向,来源于需求导向,来源于价值导向。不管是技术设计还是其他经营开发活动,尤其是长链条的业务活动,底层工作往往迷失了方向。盲目地机械式的工作不一定产生正向的结果,有可能越做越错,造成畸形发展,反而积重难返。强调基于模型的正向设计,就是统一思想,“不忘初心,方得始终”。
2)形成建模用模的技术氛围
无论是民用市场还是航天领域,市场中产品的声明周期都在变短,研发迭代的速度都在不断加快。从概念创新到产品落地的时间越来越短,需要配套的产品研发模式也进行适应性升级换代。另外航天产品统型化、标准化的要求,客观上加剧了市场竞争,要求研制单位必须要降本增效;同时面对总体不断变化的需求,以实物为验证手段的研发模式也无力为继,前期MBSE实践,有助于形成建模用模的技术氛围,让基于模型的设计和仿真验证活动逐渐成为后续型号业务的标准范式和专业能力提升的有效抓手。
3)引导企业向数字化转型的战略导向
现代企业必然是数字化企业,数字化企业的核心是模型,模型的本质是知识。为此在前期MBSE实践中,通过对产品生命周期中各种过程数据、信息和知识的整理,结合信息化系统,初步建立便于系统集成和应用的产品模型和过程模型,用于开展多学科,跨部门、跨企业的产品协同设计、制造和管理。
后续工作思路:
1)深化系统模型在指导测试验证、质量与可靠性分析、型号风险评估、型号决策分析等方面的作用,通过深入挖掘系统模型的价值,实现其与产品研制过程更加紧密的融合;
2)进一步形成更为完善的过程规范、作业指导书等配套标准,以便进一步规范和推广基于系统模型的系统设计工作;
3)摸索建立基于模型的技术状态管理机制,将传统的基于文档的线下审查活动转变为通过MBSE协同平台开展基于模型的在线技术状态审查和确认。
参考文献
[1]王为,彭坤 MBSE技术在我国载人航天器研制中的应用[J].航 天 器 工 程,2022,31(6):69-75
[2]彭坤,袁文强等 基于模型的载人登月飞船系统设计应用探讨[J].载人航天,2022,28(1):5-13
[3]焦洪臣,雷勇等 基于MBSE的航天器系统建模分析与设计研制方法探索[J]系统工程与电子技术. 2021,43(09):150-159
[4]刘红杰,窦骄等 一种基于MBSE的小卫星测控分系统建模设计方法[J] 系统工程与电子技术. 2021,43(09):58-65
[5]冯忠伟,王征等 基于MBSE技术的航天器电气系统设计技术[J] 计算机测量与控制 2023(网络首发) 1-6
本文为e-works原创投稿文章,未经e-works书面许可,任何人不得复制、转载、摘编等任何方式进行使用。如已是e-works授权合作伙伴,应在授权范围内使用。e-works内容合作伙伴申请热线:editor@e-works.net.cn tel:027-87592219/20/21。