工业4.0的实施有助于企业在自动化系统(包括用于城市供水和废水处理的多泵系统)的运行中实现最佳性能、提高可靠性和节约成本。使用传统的专有控制平台则无法完全利用这些优势。
开放平台通过促进不同系统和设备的集成和互操作性,为协作和创新奠定基础,从而实现工业4.0。开放,是泵的控制以及所有自动化系统发展的一个未来趋势。
各种泵的系统之间差别很大,控制它们的设备亦是如此。一般来说,处在泵控制器两端的是专用控制器和通用控制器,如可编程逻辑控制器(PLC),通过编程可以控制多泵系统以及外围功能,甚至控制整个泵站。
01 用于泵控制系统的专用控制器vs.PLC
专用控制器针对泵的应用进行了优化,定义了特征/功能集,它易于选择,并能获得制造商的支持。相比之下,PLC 可通过编程提供任何所需的功能,并可提供多种硬件平台和通信选择,以便集成到工厂网络中。
这两种方法已经使用了几十年,对于特定应用每种方法都有其优势。然而,它们也都有缺点。专用控制器通常是固定设计,没有升级或迁移到新技术的选项。PLC需要专有平台的特定知识才能进行编程和支持,而第三方编程的特性/功能集是自定义的,很难在系统的整个生命周期内提供支持。
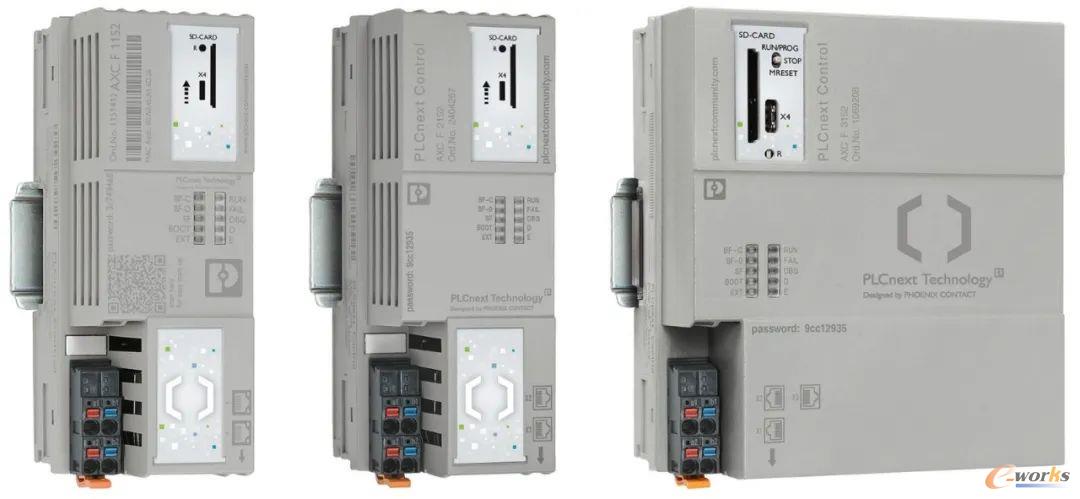
▲开放式控制平台允许在不受专有系统限制的情况下实施自动化项目。
相对于专用控制器,尽管PLC有更多选项迁移到新平台,但从传统PLC系统过渡到最新平台,可能既耗时又昂贵——即使是同一制造商的产品也是如此。专用控制器和PLC共有的其它缺点,包括用于过程可视化的选项有限,以及可能需要额外编程和配置的专用硬件。
理想的泵控制器应可以结合专用控制器和基于PLC的控制器的最佳特性。它建立在一个开放式平台上,该平台支持在来源不同的各种编程环境中开发应用程序。最重要的是,理想的控制器很容易与其它系统和设备集成,从而实现实时数据共享和分析,为泵系统的运行做出更好的决策。
02 为泵的控制和应用提供开放式平台
在自动化领域,开放式平台为何具有如此多的优势?开放式平台能够使用先进技术和应用,如工业物联网(IIoT)、机器学习和云通信,以提供更大的连接性、互操作性和灵活性。此外,开放式平台可实现:
■ 互操作性:开放式平台允许不同的系统和设备进行通信、协同工作,并无缝集成各种技术和数据源,从而提高效率。
■ 数据共享:开放式平台实现了不同系统和应用之间的数据共享,这对过程优化和提高效率至关重要。
■ 协作:开放式平台为制造商、编程人员、供应商、系统集成商和客户之间的协作奠定了基础,从而提供更具创新性的产品和服务。
■ 灵活性:开放式平台使制造商能够快速、轻松地采用新技术和过程,从而灵活应对不断变化的市场条件和需求。
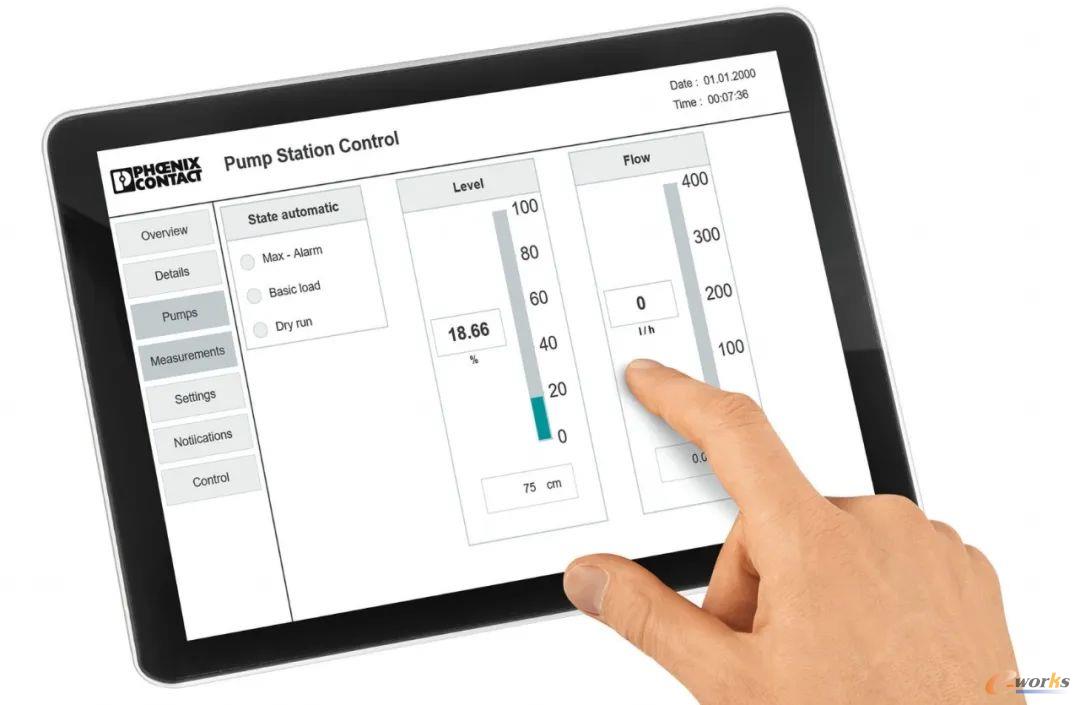
▲开放式PLC可以轻松获取实时数据,同时还可以连接到常见的云平台,如亚马逊的AWS和微软的Azure。
03 在Linux上实现自动化的优势
Linux 因其开源性、灵活性、稳定性、安全性和经济性而成为广受欢迎的开源平台。在配置Linux操作系统的工业硬件上运行泵的控制应用,除了提供启动和停止等基本功能外,还可以提供更多高级功能。增强的应用功能可能包括:
■ 预测性维护:利用数据分析和机器学习算法,预测多泵系统何时需要维护,实现主动维护,减少停机时间,提高系统的可靠性和弹性。
■ 实时监控:对泵系统进行实时监控,可以深入了解各个泵和系统的性能,从而在出现问题时快速高效的实施干预。
■ 提高效率:通过识别需要改进的领域,数据分析可以帮助优化泵系统。例如,数据可用于确定单泵最节能的运行工况,从而降低能耗和运行成本。
■ 提高自动化程度:更多数据有助于实现更多决策的自动化,从而减少手动干预的需要。例如,根据需求变化自动控制各个泵的速度,可确保系统以最高效率运行。
■ 增强协作:更大范围的集成,允许泵系统不同部分之间以及泵系统和外围系统之间进行更多协作。这使得数据能够实时共享,从而实现快速有效的决策。
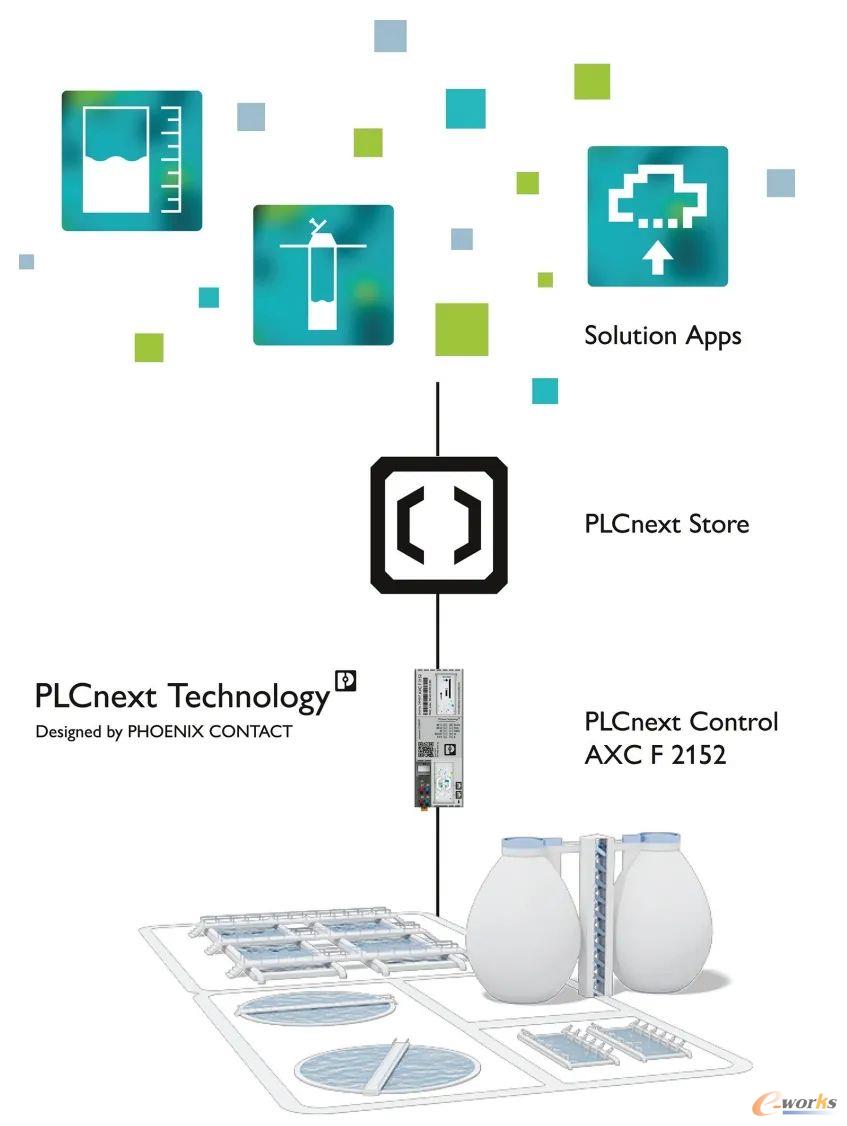
▲像菲尼克斯电气的PLCnext Store这样的中心市场,可以将软件开发人员与用户连接起来,以实现泵的系统控制的高级功能。
如今,泵制造商提供的产品已经越来越多地使用数据来提高效率,减少停机时间。一些平台允许客户远程监控和管理泵,使用数据分析和机器学习算法来优化泵的性能。
04 开放过程自动化
工艺优化和降低成本的目标并不局限于泵系统。理想的泵控制器可以支持任何泵或泵系统,并易于集成到其它系统中,以在全厂范围内提高效率、降低成本。
一些供应商提供可用于任何泵系统的先进平台。通过提供有关维修时点或更换泵的详细信息,使用实时监控来优化泵的性能并降低生命周期成本。这种方法的缺点是,它是一个封闭的专有系统,安装成本高昂,并且需要订阅服务来维持对数据的访问。
理想的泵控制器可在一个平台上处理控制和高级功能,以最大限度地降低成本和支持需求。它构建在诸如Linux等开放平台上,允许集成先进的组件,提供云连接,并支持不同来源、不同编程语言的应用。
当然,这一切并不局限于泵控制。开放过程自动化的概念在过程行业中越来越受欢迎,在这些行业中,工厂大规模升级或更换系统的成本非常高昂,而且需要长时间停机才能完成。
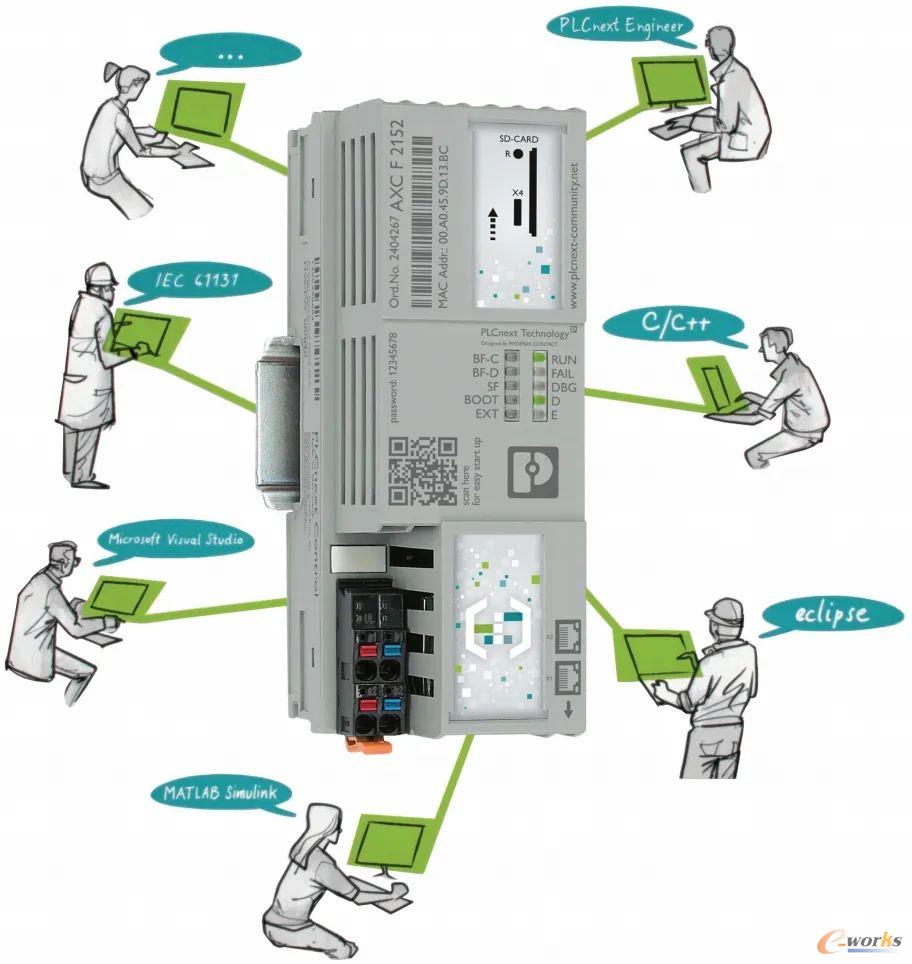
▲ PLCnext Control允许并行编程,并将熟悉的IEC 61131-3编程语言与高级语言(如C/C++、C#或MATLAB Simulink)相结合。
开放过程自动化(OPA)正在为过程自动化系统开发一种新的标准。它的目标是为过程自动化系统创建一个开放、可互操作和安全的标准,允许用户混合和匹配来自多个供应商的硬件和软件,从而实现更大的灵活性和创新。
开放过程自动化的优势包括能定制和优化过程自动化系统以满足特定需求;使用标准、现有商用组件来降低成本并提高效率;并使用安全、可互操作的组件来改善网络安全。它代表着过程自动化行业的一个重大转变,从封闭、专有的系统,到具有更大灵活性和创新的、开放的可互操作系统。
尽管开放过程自动化成为泵控制的主流方法还需要一段时间,但其基础——工业系统的开放式平台——现在已经出现。在Linux平台上运行的泵控制应用也是如此,它们代表了泵控制的未来。
关键概念:
■ 了解开放平台如何实现互操作性、协作和灵活性。
■ 了解在Linux平台上如何运行泵的控制应用,可以增强互操作性。
思考一下:
您的控制系统目前在集成方面所面临的任何挑战,是否可以通过开放式控制平台来解决?
▲本文来自于控制工程中文版杂志(CONTROL ENGINEERING China)2024年1-2月刊《封面故事》栏目:开放过程自动化将如何塑造泵控制的未来?
本文来源于互联网,e-works本着传播知识、有益学习和研究的目的进行的转载,为网友免费提供,并以尽力标明作者与出处,如有著作权人或出版方提出异议,本站将立即删除。如果您对文章转载有任何疑问请告之我们,以便我们及时纠正。联系方式:editor@e-works.net.cn tel:027-87592219/20/21。