为了解决设备运维管理问题,东希科技自研了设备预测性维护系统,该系统以真实的系统运行数据为基础,利用机器学习和自然语言处理等技术工具,为东方希望集团建立起设备智能化运维管理标准,实现了对集团千里之外的设备“悬丝诊脉”,提高了集团的智能化水平。
一、背景
在过程工业中,“三高(高价值、高使用率、高维护率)”设备的正常运行是保障工厂高效、可靠和安全生产的关键。如何使工厂在提升产能的同时,降低设备维护成本,提升关键设备的可用性,减少非计划性停车成为过程工业中越来越重要的课题,当前不少企业已逐步建立起了数字化运维平台,尽管已经提升了运维数据的保存与管理仍然面临潜在故障预警难、故障排查效率低、维修经验不闭环、预防措施不及时等诸多问题和挑战。
二、建设预测性维护系统
为了解决设备运维管理问题,东希科技自研了设备预测性维护系统,该系统以真实的系统运行数据为基础,利用机器学习和自然语言处理等技术工具,为东方希望集团建立起设备智能化运维管理标准,实现了对集团千里之外的设备“悬丝诊脉”,提高了集团的智能化水平。

图1 设备运维进化史
预测性维护系统的两项核心技术为:在线监测技术和故障诊断技术,在线监测技术使用传感器等数据采集设备连续采集关键设备状态数据,而故障诊断技术能对采集到的数据做分析并形成设备状态结论。而智能诊断模型在设备预测性维护的过程中发挥了至关重要的作用,在搭建东方希望智能诊断的过程中,主要经历了一下几个过程:
模型选择
在设备预测性维护中有两种主流的智能算法模型开发方式,一种是从收集大量高质量的数据,选取合适的深度学习模型进行模型训练,另一种是收集有足够代表性的高质量小数据,结合行业知识构建模型,两种方式各有优劣。东希科技在自研设备预测性维护系统时,以小数据驱动为主,利用传统数据处理+机理模型+专家经验的方法不断迭代优化模型,并针对部分业务模块辅以深度学习等算法,以“小数据为主,大数据为辅”的方式驱动整体算法的升级。
数据预处理
在数据预处理方面,硬件采集回传的数据容易受到外界环境的影响,存在大量无效信号、停机误报等情况,导致回传数据质量不高且影响后续的数据分析工作,东希科技的主要解决方案有以下几种:
1.针对含有下位机漏判误信号的数据,这种数据的特点是:误信号种类多、形态差异大,通过建立误信号识别模型,进行波形识别、频谱识别避免了无效信号导致的误报。
2.针对停机导致的误报数据,建立停机判断模型针对停机门限、设备定制化启停等现象自动识别,避免停机导致的误报。
3.针对受混合工况影响误报数据,建立工况划分模型,对转速、咬钢信号、电流等指标综合分析,避免混合误报。
特征提取
基于大量历史数据和专家经验进行特征提取,按照行业设备、故障类型、用途等进行指标划分和指标衍生,为模型搭建提供高质量的训练数据。
最终训练出符合集团业务场景的,高准确率的智能诊断模型。
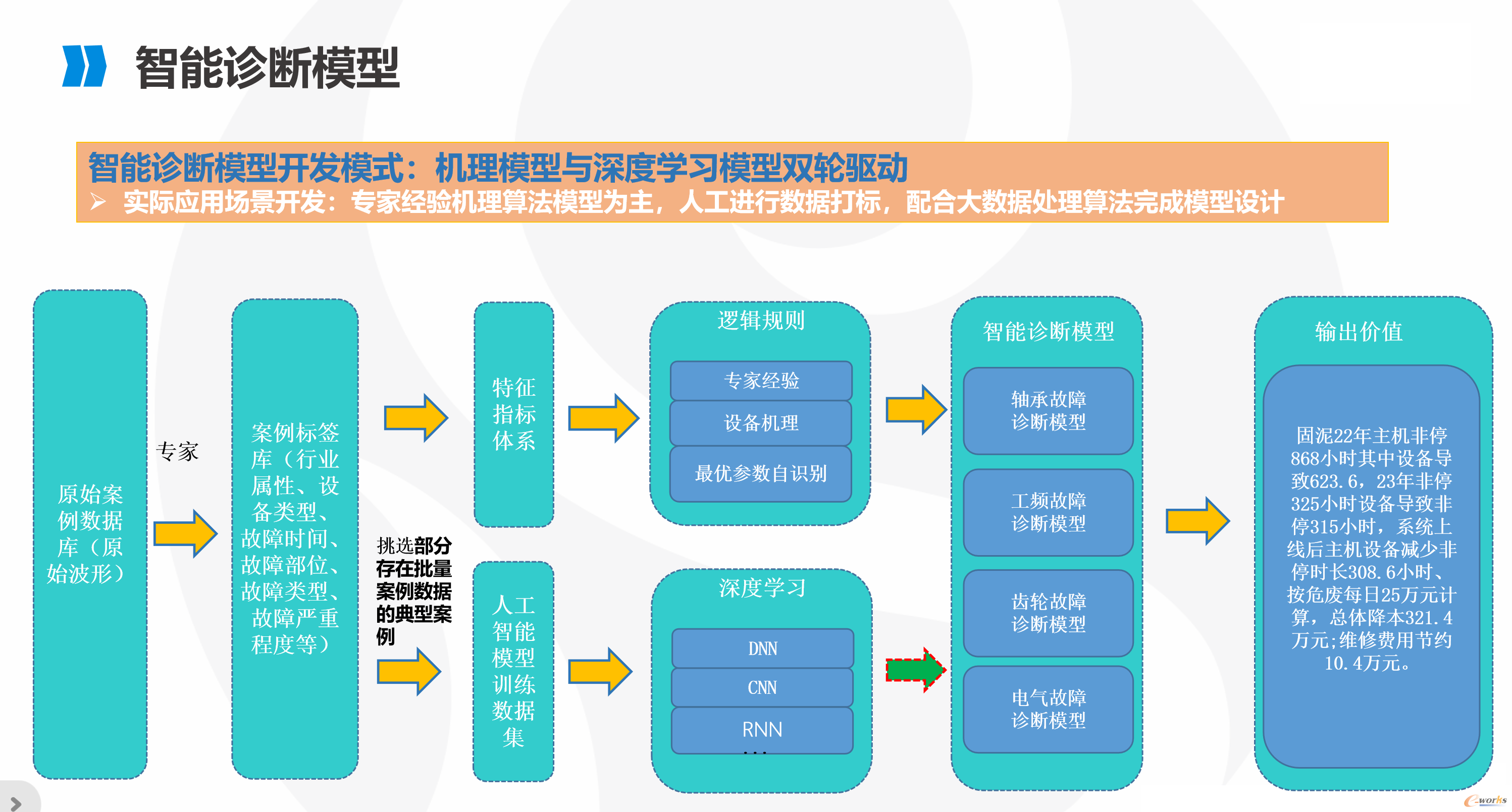
图2 智能诊断模型介绍
三、设备预测性维护成果
设备的预测性维护系统在东方希望集团的水泥、铝业、光伏各板块的应用为集团关键设备管理的水平提升起到了重要作用。以固阳水泥公司(东方希望集团子公司)为例,在设备的预测性维护系统推广应用后,消除设备振动超标4820次,巡检效率提升50%。
固阳水泥的设备预测性维护工作跨越3个年头,历经5个重要阶段。2021年集团设备处首次提出预测性维护概念,并开始与当时先进的设备监测企业进行对标;2022年2月正式立项对1#熟料线进行设备诊断在线监测试点;2022年4月开始经过理论验证后开始自研设备诊断系统;2022年11月完成温度、振动、电流三种类型设备整合,系统具备推广条件;2023年3月实现了固泥公司生料、危废、水泥等24台关键设备的在线监测。

图3 东方希望最佳实践案例-固阳水泥设备诊断
工厂侧价值
1.保障连续生产
基于可靠、真实的设备运行数据,实现设备当前运行状态的判断和未来状态的预测,可精准定位故障部件、分析故障根因、全面监测故障劣化趋势、评估故障部件剩余寿命,将维护维修决策由临时、事后抢修等转变成计划、预测性维修,可有效减少非计划停机次数,保障生产效益。
2.保障设备安全
通过对设备状态的判断和预测,避免设备故障引起的连锁反应,可最大限度地降低安全事故风险。
3.节约成本
“过修”导致大量备件库存,“欠修”导致事后抢修。使用预测性维护系统可实时掌握设备状态,预测性维护维修最大限度减少“过修”或“欠修”,优化备件库存,减少备件资金占用。
集团价值
1.整合专家资源,形成专业力量
各工厂的设备运维能力存在显著差异,过去,东方希望集团主要通过学习比赛、集中培训等方式来提升工厂设备维护人员的运维能力,但效果有限。预测性维护系统将专家资源得到有效整合,通过平台整合集团专家力量为所有工厂提供设备维护服务,实现设备管理人才的集中培养和最大化利用,从而提升整个集团的运维水平。
2.建立设备管理统一标准,实现管理变革
预测性维护系统的建设帮助集团搭建设备诊断中心,实现设备数据的标准化接入,避免信息孤岛,统一设备的运维模式,同步智能化建设。通过实时监控设备状态,实现设备的集中管理解决监管难题,快速推广成功经验,实现认知和管理变革。
3.数据驱动的设备管理,促进智能化转型
要实现集团智能化转型,仅靠长期集中管理是不够的,还需要数据支撑。预测性维护系统不仅可以提取数据中的特征和规律,还能在智能算法层面对关键设备状态数据进行智能分析和深层利用。这样的数据支撑能够为设备的维修、备件采购、运维管理和决策提供有力支持,从而推动集团的智能化转型。
参考文献:
[1]机械设备振动故障监测与诊断第二版[M].机械设备.2017
本文为e-works原创投稿文章,未经e-works书面许可,任何人不得复制、转载、摘编等任何方式进行使用。如已是e-works授权合作伙伴,应在授权范围内使用。e-works内容合作伙伴申请热线:editor@e-works.net.cn tel:027-87592219/20/21。