2006年12月左右,宝钢炼钢厂从意大利达涅利引进了4cc全连铸机组流水线,4cc机组采用的是一机两流的生产模式。自投产后,宝钢炼钢厂就致力于全套设备的国产化替代,在研究设备的同时,发现了诸多设计及生产运维问题。近些年,宝钢炼钢厂开始引入AI技术,借助AI技术逐步提升了设备运营及管理水平。
1.问题分析
连铸设备投产后,为降低运营成本,需要对设备进行国产化改造,常规的国产化改造只是对设备的零部件进行测绘(机组购置时,因多重原因,图纸不全),然后由宝钢机械厂按图生产备件。设备自开机以后,非大修不会关停整条流水线,设备会因长时间在恶劣条件下生产出现故障,导致生产出的板坯出现表面划伤,而划伤的板坯不适合于轧制,只能降价销售给小型钢厂重新回炉,这种情况不仅影响企业的经营性利润,还会逐渐影响钢材市场的平稳供给,鉴于此,在多方合力下,宝钢炼钢厂计划对这些情况进行逐一排查和整改。
1.1 零件优化设计
由于达涅利连铸设备零部件图纸缺失,测绘虽然能确定主要尺寸,但对于尺寸公差,形位公差都不能确定。可以通过实际生产积累经验,逐步确定合适的公差范围,但是此过程耗费时间长。经过多年实际生产发现,部分零件的材料、形状都有可提升的空间,但是对于如何优化设计,需要经验丰富的技改人员长期坚持才能有所收获。
1.2 设备维修管理
4cc流水线整体占地面积颇大,子件因一机两流又可正反复用,周边配以工业电机,作为驱动辊的动力来源。整条流水线的工作,也依靠各零部件通力合作才能生产质量达标的板坯。不同设备平均无故障运行时长不一,即使对于单设备而言,其子件平均无故障运行时长也不一致,这就对生产提出更高的要求,即:如何在各零部件寿命不一致的情况下,依旧保持良好的生产状态,并生产出合格的产品。
2.AI技术的引入
对于炼钢企业而言,工程师的成长之路异常艰难,在岗的又多为资历较老的工程师和技师,他们对于老设备的改造游刃有余,但对于达涅利4cc这种新技术新工艺的设备却缺乏必要的技改经验。如果给予一定的时间,配合部分尝试,确实可以提升国产化水平,但是中间过程所需时间较长,然而全球炼钢新设备、新技术已然成熟,等现有国产技改完成后就会面临落后的局面。
点检人员也试图通过台账的方式,分别记录4cc连铸线的每一个子部件的使用寿命,期间遇到的问题有:①全新子件引入后,确实可以预估下一次的维修时间,且误差在可接受的范围内,然而随着周边设备的轮替,单一新设备的维修计划又会成为整个系统中的随机事件。②流水线需要多个部件协同工作,仅预测单一部件的故障时间并不能保障生产进度,需要多维度考虑,并且大量的统计工作非点检记录可完成。
2.1 创成式设计
以4cc流水线为例,其子件有:1个结晶器,1个S0零号断,3个SA扇形段,3个SB扇形段,1个SC扇形段,1个SD扇形段和10个SE扇形段。以S0零号段模型为例,又由段框,从动辊,驱动辊,油气润滑管道组件等组成,详见图1。

图1 S0零号段及4cc流水线产品结构
对于制造业企业而言,如何既快又好地完成产品研制是企业发展面临的重要挑战。好的设计需要大量设计方案的迭代,每个设计方案都不是一蹴而就的,需要设计团队投入足够的时间和精力。企业可以通过研发团队的人海战术及改造研发工具来提升效率,但是传统研发工具对于效率的提升已经到了“天花板”。
随着人工智能、并行计算、云计算等技术的崛起,传统的数字化研制手段也迎来了新生,PTC公司推出的Creo 7.0一站式解决方案,帮助零经验设计人员快速完成设计和仿真。该方案由两个部分组成,一是融入人工智能技术和并行计算技术的创成式设计,二是整合ANSYS实时仿真引擎的CreoSimulation实现边设计边仿真。因4cc机组零部件优化结果涉及企业核心知识产权,故以其他示例来阐述具有AI技术的创成式设计。
在Creo中输入产品设计要求,软件即可自动生成一个或多个设计方案,软件可代替设计师自主完成设计。如图2所示,需要在左图灰色透明区域中避开红区设计一个零件,在跑道内壁固定的情况下,能承重350公斤并且该零件重量不超过0.2公斤,同时要求能够通过数控机床加工或模具加工出来,右图是Creo创成式设计自生成的可3D打印的零件结果。
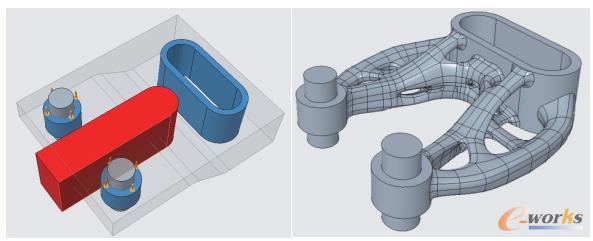
图2 避障及模型生成
Creo GTO根据用户的约束和要求(包括材料和制造流程)创建经过优化的产品设计。完全在Creo设计环境中快速探索创新的设计选项,减少开发时间和成本。AI驱动的GTO帮助用户提供更高质量、低成本且可适用于制造的设计。其具体功能包括:
●无缝设置。只需选择设计空间,添加载荷和约束,定义目标,材料,和制造过程。
●使用强大的AI驱动的优化引擎快速生成设计。
●支持从传统制造到增材制造的常见制造要求。
●能够预览和询问优化设计以及仿真结果。
●交互过程结果通过对几何图形和设置的编辑而动态更新。
●自动将优化结果重建为丰富的B-REP表示几何或细分模型。
利用云计算和并行计算多项优化研究,一次生成大量的设计结果,显著提高生产力。用户可以快速评估和比较更多的设计方案,选出最优方案,然后再将它引入Creo,供下游使用。Creo GDX支持多模态,可以利用高性能计算能力生成多种设计解决方案,优化目标和获得更好的仿真结果。创成式设计以传统设计方法为基础,将计算能力和AI优化技术应用于组件设计。创成式设计可以帮助设计人员减少特定组件材料的重量和用量,同时保持其结构完整性。生成的解决方案可以使用单个组件替代小型组件,从而降低制造成本和材料清单的复杂性。
2.2 预测式维修
故障预测是根据评估设备零部件当前状态和相关的历史数据对零部件未来的状态进行预计。故障预测一般包括三种类型:第一种是对小的时间范围内部件状态的预计,确定设备零部件的完好程度,判断是否能够完成下次计划任务。第二种是预计在出现设备部件某一具体故障出现之前剩余的时间,判断还有多长时间就必须更换该部件。第三种是通过对相似设备部件使用过程故障出现的规律,研究对新装备或使用的设备进行故障预测。在维修备件供应保障的诸多因素中,装备的故障预测一直是设备运维难以解决的问题。准确的故障预测不仅是预测维修的前提,也是控制装备使用过程中维修备件库存成本、提高设备使用效率的关键。
如上文所提,点检人员根据以往经验,对设备进行台账记录,以此作为相关历史数据的一部分,希望借此台账数据,发现4cc连铸线预测性运维的依据,如图3所示。

图3 扇形段维修履历
目前,伴随着IIoT等新技术的发展,数字化系统可以利用物联网技术将采集到的大量的设备运行数据,快速地传输至云端平台以供实时运算和决策,这些数据包括连铸设备的运行过程、发生的事件和报警信息等。以图4为例,通过系统记录SE10每次下线时,单次所累计的炉数,自动计算总体累计炉数。
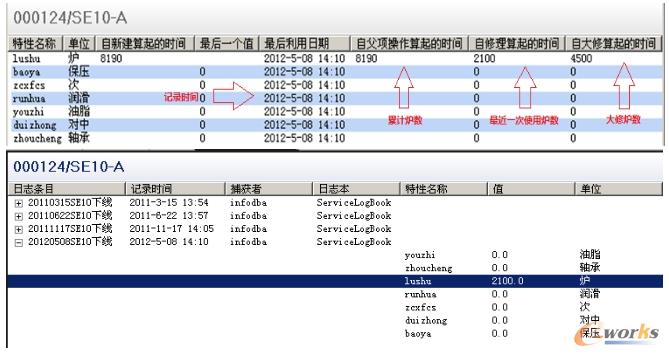
图4 参数统计
人工智能中的机器学习是最近几年最受关注的预测建模技术之一,目前人工智能在连铸系统维护中的应用,主要是针对设备故障数据进行智能分析,通过分析数据库中存储的历史运行数据、历史故障信息,总结出规律性故障周期,并形成未来一段时间内连铸设备的维护计划。技术人员通过周期性维护计划,对设备进行定期巡检、更换和保养,从而实现周期维修。而通过机器学习技术,利用设备运行历史数据集,训练机器学习模型,从而实现对设备的剩余使用寿命RUL进行预测。
人工智能技术中的机器学习方法被广泛应用于RUL预测,其中主要的预测模型包括:支撑向量回归模型、多层感知机、卷积神经网络和循环神经网络等。其中的卷积神经网络是一种用来学习或提取数据特征的预测模型,其结构包括卷积层和池化层以及全连接层。近年来,卷积神经网络逐渐成为设备健康监测与故障诊断的关键工具之一,利用卷积神经网络算法可以有效提升故障预测模型的准确性与可靠性。通过样本直接输入机器学习模型,训练RUL预测模型,是目前RUL研究中采用最多的方法之一。主要步骤包括建立数据样本、数据的特征工程、选择预测模型和利用数据样本及对模型进行训练。其中,数据样本的建立是基于全生命周期的设备运行历史数据,按照时间循序排布。设备的运行数据组成特征组,设备正常运行状态到设备失效时间的差值作为标记。设备的运行参数采集后形成样本数据,经过预处理后作为输入数据输入到机器学习模型中,机器学习模型CNN直接输出RUL预测值。如图5所示:

图5 RUL预测过程
●收集数据:通过布置与不同连铸设备中的各类传感器来采集关键设备运行过程中的状态数据,包括保压压力、润滑油脂量、对中值等,收集多源传感器的信息。
●数据分析与预处理:连铸设备的数据集通常由多传感器和点检人员收集而来,在实际工程中会存在互相干扰,因此在数据集中应清洗人为和环境等因素导致的异常数据,消除不相关或冗余的特征数据。
●建立数据集:将设备运行的历史数据进行分类,关联釆集到的设备运行数据、故障类型和RUL的数据,从而建立时序特征数据集,最终得到可用于故障预测模型训练的数据集:D={(X,Y,RUL)}
式中,X为采集到的设备运行数据,作为故障预测模型中的输人数据;Y和RUL分别为对应的连铸子零部件的故障类型和设备的剩余使用寿命,亦即预测模型中的输出数据。
构建模型:在RUL预测中,构建设备故障预测模型是实现预防性维修的核心工作,故障预测模型的本质是拟合预测模型与RUL实际历史数据模型,拟合程度越高就越可以提高预测的精确性。卷积神经网络(CNN)模型能够挖掘数据集中各种特征间的交互关系以及特征的时序信息,从而实现对RUL预测函数的拟合。通过以上数据集的训练和RUL预测模型的训练,通过调整模型参数包括窗口大小、卷积核数量等以达到预测模型的最优化,从而实现对故障函数最高程度的拟合实现RUL的准确预测。最后将训练得到的RUL预测模型将于云端数据平台下发至边缘计算设备,应用于设备故障的预测性维修实践中。
3.总结
人工智能进入制造业领域,发展并不如语义识别等领域迅速,但在制造业应用场景比较广泛,也因起步晚,所以尚留有缺陷。随着人工智能的兴起,设备运行的样本数量也将增加,随着数据增多,预测模型将越来越准确,设备的运维也必将打开新的局面。
本文为e-works原创投稿文章,未经e-works书面许可,任何人不得复制、转载、摘编等任何方式进行使用。如已是e-works授权合作伙伴,应在授权范围内使用。e-works内容合作伙伴申请热线:editor@e-works.net.cn tel:027-87592219/20/21。