1 简介
在钢铁生产过程中,脱硫是一个至关重要的环节,它对于提高钢材质量和满足环保标准具有重要意义。本文旨在深入探讨LF(Ladle Furnace)炉脱硫的动力学过程[1],并结合人工智能技术,对脱硫系数进行预测,以优化脱硫效率和钢材质量[2]。
在以往传统的LF脱硫计算的过程中,需要根据化学元素的相互作用系数、钢水活度、钢渣成分等因素对脱硫过程的影响,在此基础上,对钢渣的硫容量进行精确计算,进一步的基于硫容量的大小计算钢液中硫的去除速度和程度。这个计算方法复杂,且可操作性不强,其中钢渣的成分化验就是一个非常耗时的过程,往往需要经历取样、磨碎制样、压饼、检测几个过程,化验一个钢渣成分样品往往需要5小时的时间[3]。然而LF炉冶炼一炉一般不超过45分钟。因此传统的脱硫计算方法并不适应于实际的生产过程。
随着人工智能的发展,多输入多输出的高纬度空间数据建模成为了可能,钢渣成分的信息往往已经蕴含在进站钢水温度、造渣料加入量、钢水成分等信息当中[4]。我们可以将脱硫动力学微分方程中关于硫容量的系数以及其他参数进行整合,形成了一个新的参数——脱硫系数,对脱硫微分方程进行了求解。这一数学模型的建立,使我们能够准确地描述不同时刻钢液中的硫含量变化。通过这一模型。这一参数的引入,简化了脱硫过程的数学描述,并提高了预测的准确性。相较于传统的脱硫计算方法,该方法准确性、可靠性高。
为了进一步优化脱硫过程,我们采用了人工智能技术的机器学习算法,对脱硫系数进行预测。通过输入造渣料的种类和数量、钢水的温度、钢水的初始成分等关键参数,我们的模型能够准确地预测出脱硫系数,从而为实际生产过程中的脱硫操作提供有价值的参考。
2 脱硫动力学参数整合
基于硫容量的脱硫微分方程原形式[5]如下:
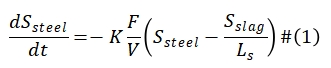
式中:K为传质系数,ms-1;F为熔渣界面面积,m2;V为钢水体积,m3;Ssteel为钢水中的硫含量,%;Sslag为钢渣中的硫含量,%;Ls为硫分配比,是一个基于硫容量计算所得的参数。
很显然,要对上述方程精确求解是非常困难得,首先必须获得当前时刻钢渣中的硫含量,其次要根据钢渣中CaO、SiO2、Al2O3的含量,钢水成分以及交互作用系数,钢水活度等信息计算得出硫容量,进而计算得出硫分配比Ls。上述计算是非常复杂的,而且由于钢渣成分化验耗时太长,在实际计算的过程中,可操作性不强。
为此我们对上述方程进行了简化:
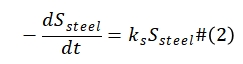
将K、F、V、L合成一个脱硫系数ks进行计算,并对微分方程进行必要的简化。很显然,在预测一炉钢的脱硫曲线时,需要得知ks的大小。根据传统的分析结果可知,ks与渣成分、钢水成分、底吹强度、钢水温度有关。
在计算过程中需要避免的是将渣成分纳入到计算输入中,因此对渣成分的形成进行了进一步的分析。钢渣由两部分构成,一部分是转炉下渣残留,一部分是LF炉造渣硫构成。
在LF炉在进站调渣的过程中,钢渣已经处于脱硫的状态,因此可以根据钢水中被脱除的硫与钢渣中增加的硫含量来对钢渣重量进行估测[6]。进而根据加入的石灰量、铝粒量计算得出钢渣中的CaO和Al2O3的含量。
那么推测可知,钢渣中的CaO含量的信息已经隐含在转炉出钢成分和LF造渣料加入的过程了[7]。因此本文提出了以下人工智能神经网络算法的构想。
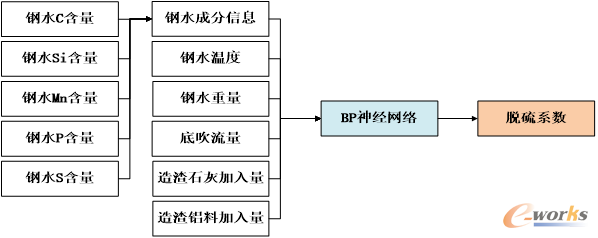
图1 神经网络参数设计
神经网络包括生物和人工两种。生物神经网络是生物大脑中的网络,帮助生物思考和行动。人工神经网络是模仿动物神经网络行为的数学模型,通过调整节点连接关系处理信息。BP神经网络是其中应用最广的,它是一种按误差逆向传播算法训练的多层前馈神经网络,具有输入层、隐含层和输出层,层间连接通过权重体现。其核心步骤包括正向和反向传播:数据从输入端开始,经过层层计算和传播,直至得到最终结果。这个过程是通过每个节点的输出作为下一个节点的输入来完成的,即正向传播。
3 模型的验证
本文根据BP神经网络模型进行建模,以钢水的状态信息作为输入参数,预测脱硫系数ks,实时预测钢水中硫的含量变化
[8]。本文采用了一个输入层、三个隐含层、一个输出层的神经网络结构,激活函数采用了relu、tanh、sigmoid三种形式进行寻优搜索。表1为网格调优的结果,在不同的触发函数、神经元个数的情况下,模型的表现情况、测试集与训练集平均、标准差R2分数。
表1 模型网格调优结果
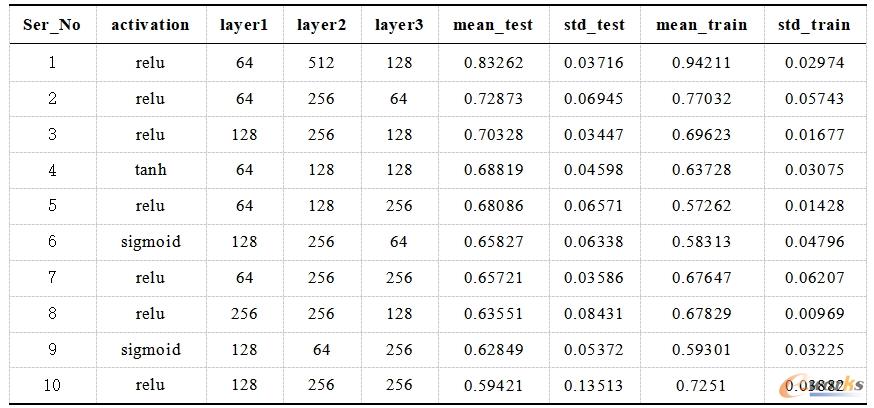
通过大量的神经网络模型结构进行筛选,找到了训练集和测试集得分较高的模型结构为,激活函数relu,第一隐含层神经元个数64个,第二隐含层神经元个数512个,第三隐含层神经元个数128个。训练得分94分,测试得分83分。
通过使用网格调优的方式,挑选精度最高的1#和2#神经网络模型结构损失函数下降情况,如图2(a)、(b)所示。训练损失和验证损失均在一定训练周期后趋于稳定,说明模型有效。
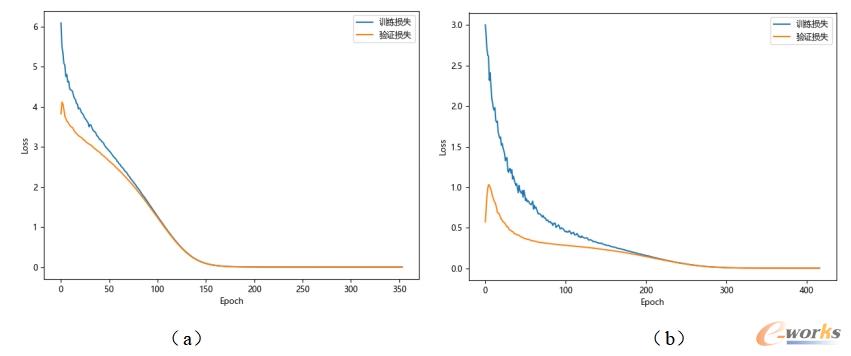
图2 loss损失曲线对比(左为最优)
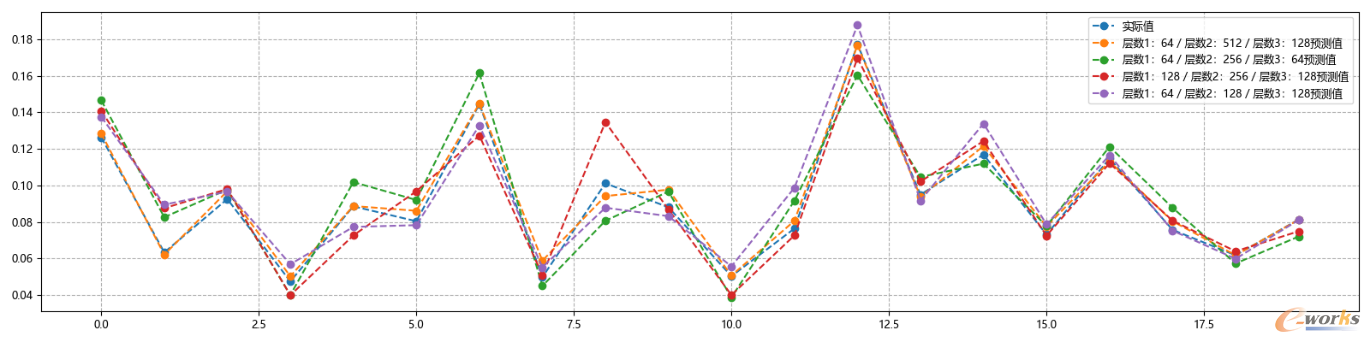
图3 表中前四模型预测精度交叉验证对比
图3对比了表1中前四中模型结构在验证集中的表现。在触发函数为RuLe的情况下,第一隐含层神经元数量为64,第二隐含层神经元数量为512,第三隐含层神经元数量为128时,模型精度最高,预测值最靠近真实值。
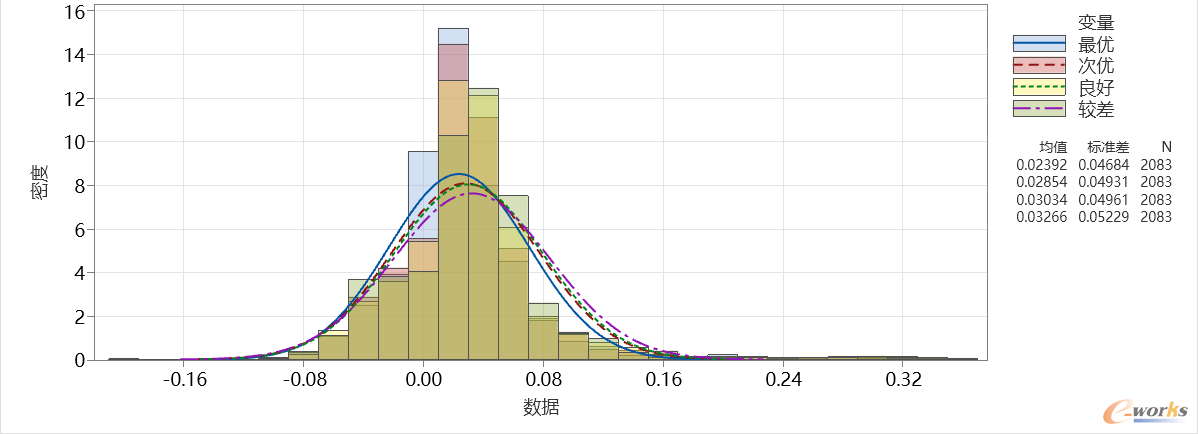
图4 偏差分析
通过误差分析统计,对比了表1中前四种模型的误差。均值偏差越接近0,预测值与真实值越接近,标准差越小,不同组数据之间预测偏差越小。1#模型经验证是最为理想的模型。
获得模型以后,邯钢建立了LF炉的在线预测模型,通过钢水成分、钢水重量、钢水温度、底吹流量,造渣石灰加入量、造渣铝料加入量,对脱硫系数进行了预测。并按照脱硫系数,对脱硫过程中各个时刻的钢水硫含量进行了准确预测。预测的界面如图5所示:
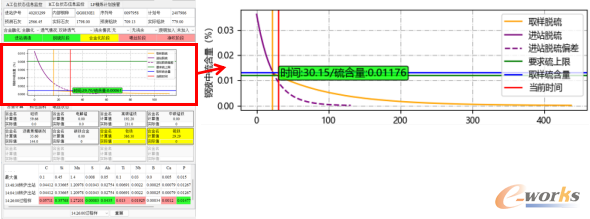
图5 脱硫实时曲线
图5为界面上显示的实时脱硫曲线,能够给出当前精炼时间下,钢水中的硫含量情况,给出脱硫指导,预测钢水的脱硫状态。
模型通过实时获取的钢水信息,对最近50炉钢水脱硫系数与实测系数进行了跟踪验证比对,如图6所示。脱硫系数偏差在0.01以内,达到预计使用要求。
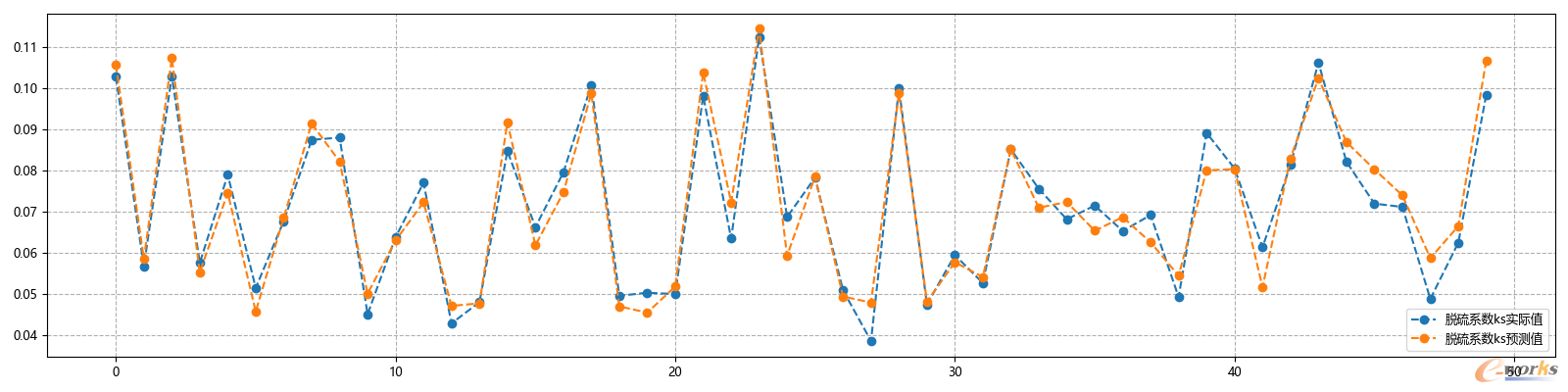
图6 最优脱硫系数ks的精度图
最终实现具备10分钟形成白渣,脱硫效率由82%提高到90%,缩短精炼周期,对LF炉深脱硫工艺,从原料加入到过程操作实现模型化生产。当前已达成,脱硫命中率由96%提高到97.5%。
通过样品夹杂物快速分析,建立钢水成分,记录过程参数与夹杂物相关性,对生产过程进行纠偏指导,实现高品质钢质量稳定性提升。
4 脱硫精度对比
通过对脱硫系数的预测,可预估当前钢水中的硫含量,对当前钢水中的硫进行监控,避免仅凭经验预测脱硫状态,达到提高脱硫命中率的效果。
通过对模型进行调整优化,近50炉详细预测实际对比如图10所示。数据为LF出站取样化验数据与脱硫模型预测值在同一时刻的数值对比。硫含量偏差小于等于0.002%,满足现场操作判断要求。
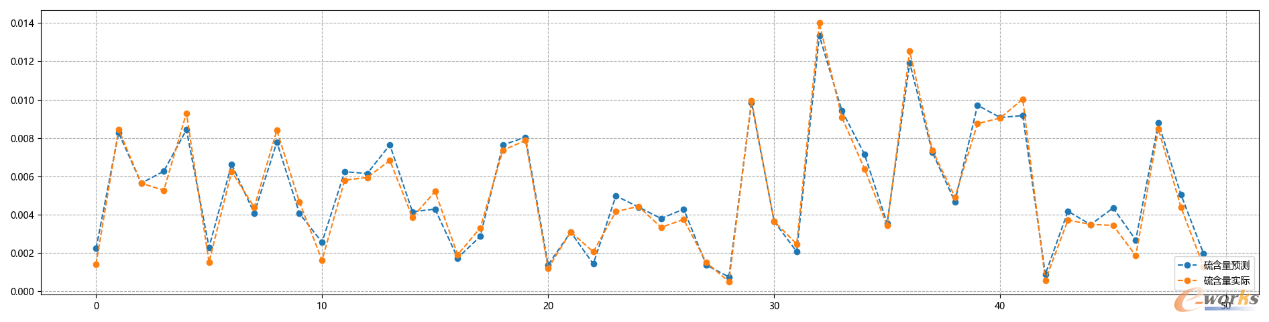
图7 LF出站硫含量与预测值偏差
本模型取得的有益效果包括降低了脱硫时间,通过模型可以精准判断LF出站时刻,由此避免了不必要的脱硫等待,从而缩短了脱硫时间。精炼时间精炼的对比分析如表2所示。
对邯钢常见5个钢种进行了统计分析,平均缩短时间在7分钟以上,减少了脱硫等待时间,降低了由于脱硫等待而损失的热量,减少了通电时间与能耗,提高了生产效率,降低了生产成本。
表2 模型实施前后精炼脱硫时间对比
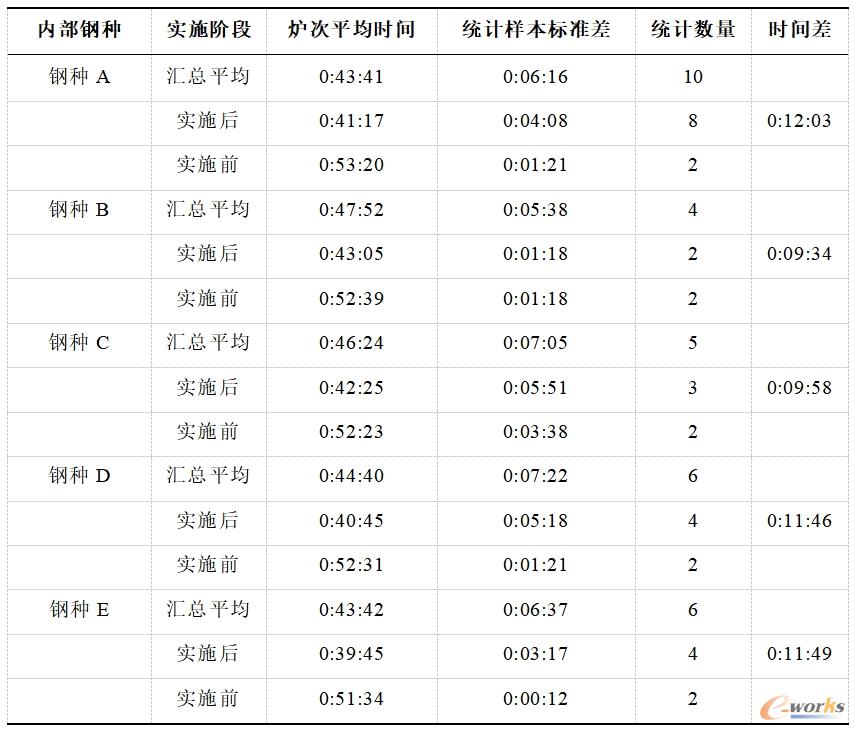
据炼钢厂数据测算,精炼周期平均缩短5分钟,每分钟温度损失1℃,吨钢温度成本0.35元估算,可降低生产成本1.75元/吨钢;LF一号精炼炉年产能按照200万吨估算,可创效350万元。
参考文献:
[1]马桂芬, LF炉快速脱硫工艺的开发. 天津市,天钢联合特钢有限公司,2020-12-28.
[2]王飞宇.LF精炼炉快速脱硫工艺研究[J].山西冶金,2023,46(11):168-170.DOI:10.16525/j.cnki.cn14-1167/tf.2023.11.062.
[3]初仁生,刘金刚,李战军,等.一种LF炉快速脱硫生产低碳钢的方法:CN201911008825.7[P].CN110735018A[2024-05-29].
[4]严旭梅,陈超,王楠,等.基于随机搜索算法和AdaBoost模型预测LF精炼过程脱硫率[J].材料与冶金学报,2023,22(05):430-436+443.DOI:10.14186/j.cnki.1671-6620.2023.05.004.
[5]吴铿,梁志刚,张二华,等.LF精炼过程中硫分配比和脱硫动力学方程研究[J].金属学报, 2001, 37(10):4.DOI:10.3321/j.issn:0412-1961.2001.10.014.
[6]张宝景,张朝发.LF脱硫精炼渣的发展[J].四川冶金, 2011, 33(2):4.DOI:10.3969/j.issn.1001-5108.2011.02.001.
[7]方莉莉,王建军,周俐,等.LF炉混合型精炼渣脱硫的实验室研究[J].安徽工业大学学报:自然科学版, 2008, 25(1):3.DOI:10.3969/j.issn.1671-7872.2008.01.004.
[8]谷峰.LF炉精炼造渣制度研究与模型的建立[D].东北大学,2012.DOI:10.7666/d.J0119648.
本文为e-works原创投稿文章,未经e-works书面许可,任何人不得复制、转载、摘编等任何方式进行使用。如已是e-works授权合作伙伴,应在授权范围内使用。e-works内容合作伙伴申请热线:editor@e-works.net.cn tel:027-87592219/20/21。