随着新能源汽车产销量的大幅增长,新能源汽车不可或缺的核心零部件-电驱动系统行业也在高速发展,并取得了显著的进步。在新能源汽车行业快速发展的今天,电动汽车领域的领军企业-蔚来在其电驱动系统的市场布局和技术开发等方面取得了显著进展。
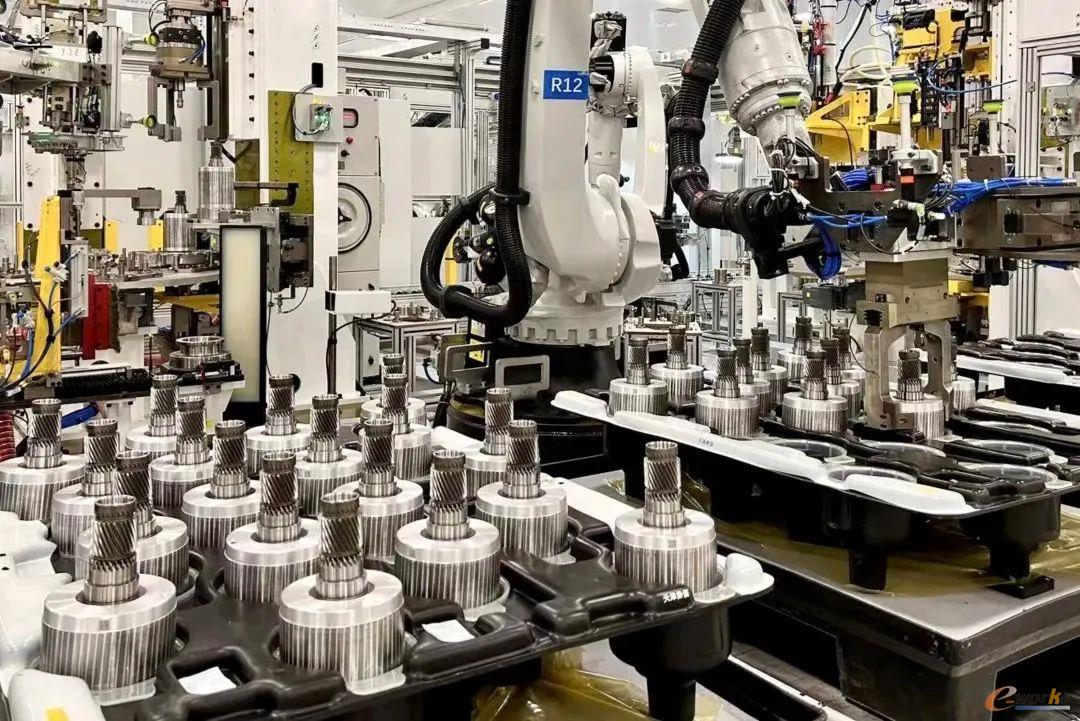
总部位于上海的中国跨国汽车制造商蔚来,于 2015 年开始研制其专有的电驱动系统,并进行大规模制造。通过持续的研发和创新,蔚来扩大了其EDS电驱动系统在国内外市场的影响力,并凭借在性能、可靠性和先进性方面的竞争优势,赢得了广泛认可和良好声誉。
面临的挑战
电驱动系统作为高度定制化产品,其创新正朝着高度集成化、标准化和模块化的方向发展,以提升效率、降低成本并增强整车性能,这对电驱系统核心零部件的质量和装配工艺提出了更严格的标准。蔚来对新一代自主开发的电机输入轴齿进行了创新设计,优化了电机的扭矩性能,以改善高速运行时的驾驶感受,同时也对噪声控制提出了更高的要求。快速变化的市场需求加速了产品迭代,因此,蔚来需要灵活调整生产线以适应新产品各种工艺参数。
电机自动化装配面临的挑战主要包括技术复杂性、精确性要求高、自动化程度需求、设备可靠性和可维护性、生产效率与成本控制等方面。
力控齿轮装配解决方案
在优化电驱动性能和产品质量方面,通过新工艺来实现产品性能优化。在蔚来EDS车间的齿轮装配应用中,柯马作为系统集成商使用了库卡机器人搭载ATI机器人工具快换装置和六维力/力矩传感器来实现斜齿齿轮的装配和柔性生产。
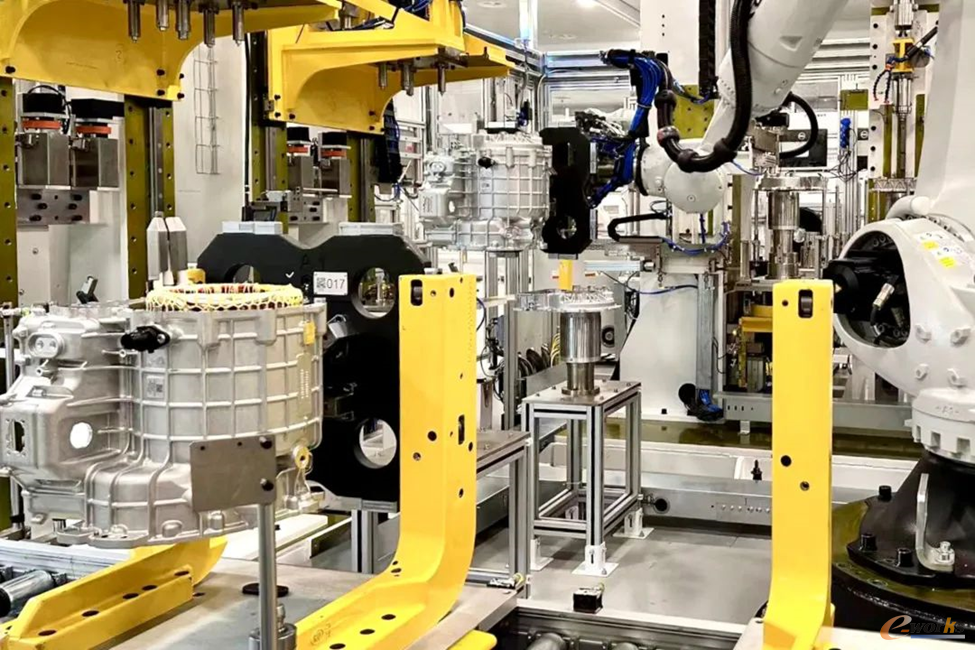
六维力传感器通常安装于机器人末端,用于检测作业中的机器人与环境之间的多维交互力/力矩,并将交互力/力矩反馈给机器人力控制系统。此次在蔚来EDS车间,为了满足客户要求和机器人的柔性生产,使用的两台六维力/力矩传感器(Omega160和Delta)均安装在机器人工具快换装置的工具侧与抓手之间,机器人通过进行不同工件的抓取从而进行齿轮装配,这种安装方式也是国内首次尝试,该工作站从2023年10月份交付到现在1年多时间,运行稳定。
取得的成果
通过使用ATI的Omega160高达0.1%测量误差的中大型六维力和力矩传感器和Delta中型传感器,精确严格的控制装配过程中的接触力和啮合的行程,有效的避免损坏齿轮的表面,提高装配质量,ATI的传感器还具有极高的可靠性,故障率极低,大大降低了生产过程中的停机风险。
ATI的六维力传感器在齿轮自动化装配中起到了关键作用,有效防止了齿轮损坏,提高了装配的质量和效率。
01 精确的力和力矩测量:六维力传感器能够测量物体在笛卡尔坐标系下三个轴向的力和力矩。在齿轮装配过程中,这种精确的测量能力使得机械臂能够感知每个齿轮的受力情况,确保每个齿轮安装到位,同时避免因过度用力而损坏齿轮或其他部件。
02 自动调整力度和位置:由于六维力传感器提供的高精度和敏感度,机器人能够在装配过程中自动调整力度和位置,保证装配的精确性和一致性。
03 实时监控和调整力反馈:六维力传感器能够实时监控装配过程中的力变化,并根据这些数据调整机器人的姿态,确保装配动作的顺畅和精确。
04 与机器人软件包完美结合:配合机器人软件包,可实时读取并显示数据,便于用户调试分析,同时与机器人软件包完美匹配。
05 提高生产效率和产品合格率:六维力传感器能够感知微小力变化,确保齿轮装配动作的顺畅和精确,通过实时监控和调整力反馈,机器人能够自动完成装配和测试,极大地提高了生产效率和产品合格率。
本文来源于互联网,e-works本着传播知识、有益学习和研究的目的进行的转载,为网友免费提供,并以尽力标明作者与出处,如有著作权人或出版方提出异议,本站将立即删除。如果您对文章转载有任何疑问请告之我们,以便我们及时纠正。联系方式:editor@e-works.net.cn tel:027-87592219/20/21。