本文为“2024年度中国制造业优秀CIO”参评材料。本次将评选出在企业成功规划和实施智能制造项目,带领各方积极推进项目实施并达到预期效果,为企业带来实际效益的制造业企业的优秀CIO。
一、企业简介
合肥美的洗衣机有限公司(简称“合肥美的洗衣机”)位于安徽省合肥市高新技术开发区柏堰科技园玉兰大道88号,占地850亩(56万平米),2006年4月正式开始动工建设,2007年5月正式投产,累计投资超过20亿元。公司经营“小天鹅”、“美的”、“COLMO”及“东芝”等多个驰名品牌,在职员工3800余人,目前拥有11条洗衣机生产线,配有电子、钣金、注塑、模具等自制件生产车间。是国内最大、集研产销为一体的全品类洗衣机生产基地。
公司依托M.Iot美的工业互联网平台建设,行业内率先创新T+3商业模式,通过订单全流程可视、无缝智慧物流、制造自动化升级、智能质量管理等维度实施全价值链数智化运营,构建了端到端柔性供应链控制塔和数字孪生平台,助力智能制造转型。近三年在未增加线体的情况下,实现产值增长60%、订单交付周期缩短56%、人均效率提升51.6%、单台制造成本下降28%。
公司荣获全球可持续灯塔工厂、全球端到端灯塔工厂、国家级绿色工厂、国家工业互联网试点示范项目、国家5G工厂、省级工业互联网平台、省十大工业互联网项目等多项荣誉称号。
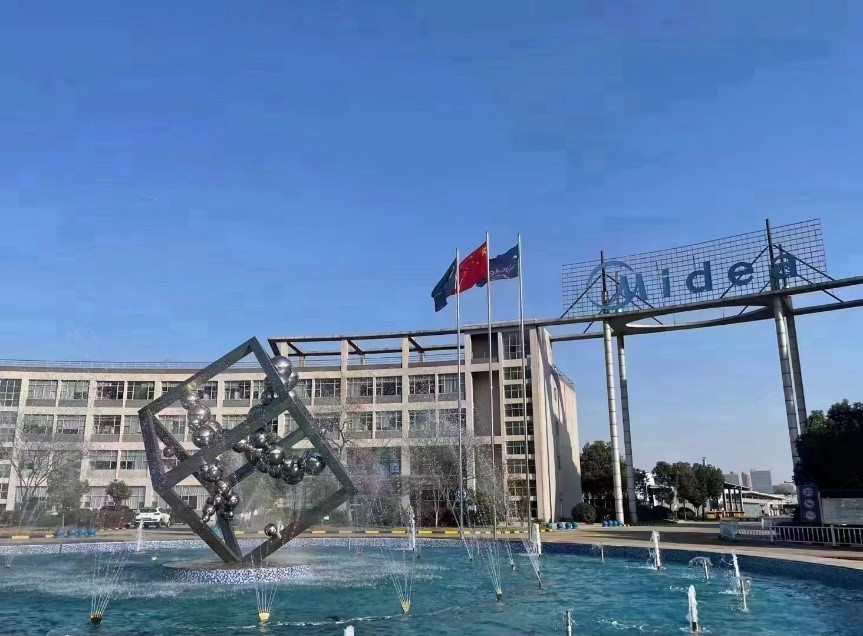
图1 合肥美的洗衣机有限公司
二、CIO个人简介
王侃侃就职于合肥美的洗衣机有限公司,主要负责数智化转型管理相关工作,于2011~2012年参与日本籍专家IE高级培训班;2014—2015年参与精益革新学院学习培训;2016年参与DBS转型及精益工具培训;2017~2020年多次参与IE、MBS、战略转型相关培训和实践学习;2017年参加全球化人才高研班培训;2020年参与麦肯锡灯塔工厂认证;2021~2024年多次参加数字化战略规划培训、大数据平台建设、新场景应用培训;2024年参加安徽省工业互联网数字化转型与人才培养高研班;2024年主导麦肯锡可持续灯塔工厂认证。
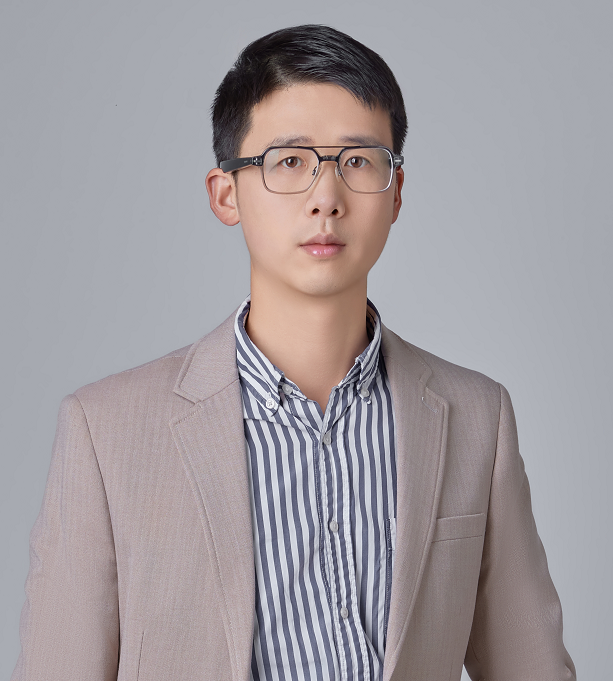
图2 合肥美的洗衣机有限公司CIO 王侃侃
三、个人信息化从业经历及主要业绩
王侃侃就作为数智化负责人,工作期间推进公司五智品质建设、可持续发展数字化平台建设、智慧园区建设、智能物流建设、数字化复合型人才建设、效率管理以及精益管理等工作。
一、信息化:主导工厂信息化顶层设计、战略落地、新技术应用、人才建设及基础运维,核心业绩如下:
1、五智品质建设:将AI视觉和AI声纹技术深度应用于人员、设备、物料、关键质控点的智能检测与防错,通过边缘算法、小样本算法、大数据云计算、智能判定深度应用标贴、装配、行为识别、声纹等场景,实现产品市场不良下降超50%。
2、可持续发展数字化平台建设:持续探索并重构端到端绿色可持续新能力,在产品设计端、制造端、物流端部署多种类数字化技术融合人工智能集成应用,实现端到端碳排可视分析、预警改善,合规运营,高效推动范围1、2、3碳排节降,构建可持续发展生态业务链,碳排范围1&2下降36%,范围3下降26%。
3、集团首创:大数据与各模块信息中心拉通,实时决策,实现数据的分层和闭环管理,通过数据应用改善周,沉淀“数据应用方法论”,数据驱动经营管理改善。
4、集团首创智慧园区建设:全价值链数字转型升级,工厂九大功能(计采、人员、设备、工艺、品质、物流、EHS、能源)运营场景0→1.0→2.0覆盖迭代升级。数字孪生平台(虚拟交互,四级设备管理模式),基于智能终端(AI摄像头、无人机、传感器等),融合多系统(SCADA、EAM、MES、DMS、FEMS、QMS等)数据互联互通,实现总装、注塑、钣金、电子多业务领域智能交互,全流程效率提升45%。
5、智能物流集团首创:物流数字孪生及大物流仿真,结合5G全覆盖,北斗及AI摄像,实现供方车辆入厂、在厂轨迹以及卸货效率实时可视,提升园区物流效率和安全管理,RFID、UWB等先进技术的自动库存管理,通过先进技术应用,实现自动仓储管理,提升物流效率,成品仓库面积下降30%,减少外租仓费用超500万。
6、数字化复合型人才建设:数字化1级超1000人,数字化2级34级,数字化绿带10认,数字化黑带6人,其余复合型人才输出120余人。
二、智能制造:效率管理+精益管理
一)效率管理:效率模型、产出提效、少人化、日常管理体系
1、效率模型及体系搭建迭代:
①负责各模块效率指标分解,月度人员编制,月度开班计划,月度支撑效率指标达成改善项目规划,月度效率分析。②员工工人管理方法论沉淀。③基于淡季下效率提升模型。
2、产出提效,负责内销产品围绕岗位标准化&线速标准化提速、外销产品围绕客户产品优化&剧本差异化提速、设备专线围绕设备稳定性&设备专机提速&岗位标准化提速、新线快速上量方法论沉淀。多品类线突破性改善快速复制推广应用,沉淀三步走方法论。
3、少人化,负责建立全员岗位标准库,以350战略为牵引,开展多维度少人化实施落地,优化人工成本。从管理驱动(ECRS、辅助饱和度分析等)到向技术驱动(自动化、工艺研究等)的转变。
4、日常管理体系,负责快速响应机制建立,日常管理体系导入推进。
二)精益管理:精益体系搭建、MBS、精益物流、信息化、LCIA
1、精益体系搭建,精益改善项目主导,精益改善项目制度建立,评价体系建立从无到有,内部资深培训讲师和辅导老师。
2、MBS,①完成MBS黑带(SW、PSP)、MBS绿带(VSM、TPM、PSP、DM)认证,整体负责MBS工具导入普及,新精益体系搭建,完善人才体系,输出绿带黑带人员。
②畅流体系搭建主要针对标准作业、TPM、SMED、柔性制造等输出标准流程,五表一书,三级人才体系,持续改善,氛围营造。
3、精益物流,负责物流布局年度规划,线体配套布局优化,物流上线器具&配送模式改善。
4、信息化,承接信息化落地(设备、品质)信息化方案研讨、实施、应用。
5、LCIA,负责自动化项目导入实施,内部简易自动化自制应用。
三)工作业绩:
1、效率提升:①效率连年提升近20%②产出提升外销杂品线由2525提升至3500,近三年累计提升39%,高速线3766提升至4280,提升12%③设备专线由2208台提升3027台,提升37%(设备提速第一阶段MCT由16.2s下降到14.3s,设备提速第二阶段MCT由14.3s下降到13.5s,第三阶段13.5s→12.0s);④快速上量方法论沉淀(2周达成老线标准产出)⑤员工工人管理方法论沉淀(员工流失下降50%)。
2、少人化:近三年通过新工艺、产品可制造性、自动化、ECRS改善落地实现优化200人,同时输出GAB岗位库,岗位标准库。
3、MBS:①开展MBS改善周40余次,培养黑带10科,绿带42人次,改善周2.9个/月,沉淀输出标准改善流程和课件涉及7个科目-VSM,SW、TPM,PSP,SMED等方法论,培育人才,IE团队不断成长,已成为工厂改善的中坚力量(作战参谋部)。
4、14~19年多次参与并设计大物流方案(15年预装与总装衔接改善,实现一个流优化,消除二级计划,消除4个断点,优化29人,库存优化400平方;15年~16年设计执行厂房布局调整;17年参与新建线布局检讨实施;18~19年检讨未来布局调整规划;19~20年参与新基地物流布局规划检讨;21~22年参加新建线布局优化调整)。
5、LCIA:重点主导标杆线建设(POU→QEP→LCIM)
①POU标杆线:打造工厂首条POU标杆线。POU覆盖率97%,其中A类物料达成88%,B类物料100%, POU标杆线底座POU改善荣获集团上半年亮点秀铜奖;
②QEP标杆线:联合品质、自动化、IE、信息化打造工厂首条QEP标杆线。QEP覆盖率151%,三级防呆覆盖率90.38%,其中附件防呆荣获集团上半年亮点秀银奖;
③LCIM标杆线:联合研发、自动化、工艺、IE人员,组建团队对波轮和滚筒低成本智能化线进行设计。单台制造成本下降34%,品质合格率由95%提升至98.2%,自动化率提升至53%,LCIA提升至56%。其中滚筒标杆线获得集团银奖,并输出集团第一期LCIM优秀BKMC。
6、联合管理推进:搭建输出5大纬度联合管理体系,打造输出3大标杆区域,2条标杆线,输出工厂到分厂三级人才体系,横向建立BKMC案例库。
四、近2年在企业主要推进的智能制造项目
随着全球经济的快速发展和科技的不断进度,传统制造业在提升生产效率、降低成本、提高产品质量的同时,还需应对日益严峻的环境保护和可持续发展要求。特别是在全球碳中和目标的推动下,绿色制造和智能制造已成为制造业转型升级的必然趋势。洗衣机合肥工厂在近两年响应集团“双全”战略要求及T+3全价值链为主轴的创新牵引下,积极推进端到端的数字化建设,结合八大智慧物流场景、品质数智化、智慧能源管理、数字孪生平台等,实现从传统精益工厂向数字精益工厂、智能制造工厂和绿色可持续灯塔工厂的转型之路。
1)项目实施
①“黑灯工厂”建设:企业数字化转型过程中,老旧设备问题突出,生产数据、生产效率均无法达到智能制造转型需求,部分产品制造工艺急需升级,2024年,完成钣金分厂彩板工艺变革,拆除2条喷涂线体,布局彩板箱体自动化线体;注塑分厂完成12台1800吨注塑机替换升级,同步进行制造布局升级,搭建产品智能立库,运营设备智能终端、5G技术运用、智能AGV,实现自制件全流程信息互联互通,助力“黑灯工厂”快速升级。
②基于“T+3”的产销一体智慧物流平台:通过MES协同、物流信息化协同(安得物流-安得到车App信息共享)、直发装车时效监控持续深化融合“一个码、一个流、一盘货”,量变到质变,沉淀物流新机制、新方法、新打法在智能物流平台MLS试点的基础上,结合5G、物联网RFID、UWB和AGV等新技术对仓储进行智能化管理等方式方法提升物流系统,实现了整体效率的提升,RFID齐套管理:厂家自主入库,通过物料码、人码、器具码实现3码绑定入库,系统齐套检讨,实时监控物料齐套情况。实时配送指引:通过生产实时效率拉通当前订单生产进度,精准预测下一工单上线时间,为配送员通过精准配送指引。下一需要配送的工单会变成绿色字体并实时根据计算更新上线时间。AGV、悬挂链智能配送:应用悬挂链实现自制件、大件等自动输送上线,小件类利用AGV实现自动配送配送上线,自动对接线边POU工装。
③5G+设备智能管理:已完成工厂级至设备级的分级管理和工业互联网数字孪生可视化平台搭建,滚筒线创新应用3D组态技术。A类设备SCADA联机数609台,联机率达到100%;首创低成本的注塑机联机方案,注塑机基础生产数据准确采集并展示,实现了设备自动报障,注塑、钣金模具上下机日常管理等功能。“数字化双胞胎”通过5G大带宽、低时延的特性,映照(模拟)、监控、诊断和控制洗衣机生产线设备;能够在虚拟SCADA平台里面完成人机交互和调试,设备工艺参数根据不同产品型号的技术要求进行实时调整,达到高效的柔性生产、智能生产
④绿色可持续管理体系:实施建立微电网(光储一体),运用工业物联网技术,构建智慧能源管理平台,优化能源管理机制,推动园区能源绿色可持续发展,助力国家“双碳”目标。整体智慧能源管理平台上线409块智能电表,覆盖整个园区重点能耗区域和机台,实现了能耗数据实时采集 分析 监控 ,在此基础上优化用能计划,通过大数据分析历史用能情况,系统自动推荐区域设备能耗目标值,同时结合年度节能管控和降耗项目的导入设定能耗预警值,当实际用能达到预警值时进行智能预警,自动推送预警信息至责任人,根据预警信息及时处理异常点,(机台匹配,设备故障,原材料不良等)。
2)实施成效
①创新效率提升显著。产品研发周期平均缩短56%,服务响应时间平均缩短20%,单位产品成本平均下降50%,销售增长率平均提升5.8%。
②运营水平改善明显。运营成本平均下降23%,库存周转率平均提升达125%,产品不良率平均下降50%,资源综合利用率平均提升达15%,设备综合利用率平均提升达28%。订单准时交付率平均提升达50%,订单准时交付率平均提升50%。
③节能减排成效显著。绿电占比提升至57%,单位产品综合能耗平均降低28%,单位产品二氧化碳排放平均降低20%。
五、个人在智能制造工作中的体会
1) 战略规划与顶层设计
合肥工厂智能制造建设初期,明确了以提升生产效率、降低成本、提高产品质量为核心的战略目标。通过集团战略顶层设计,制定了详细的实施方案,涵盖了智能制造的各个方面,包括技术路线、实施步骤、资源配置等。
2)精益转型:核心理念是通过消除浪费、持续改进、以业务为中心和全员参与等方式,自上而下统一精益语言,统一精益工具,培养复合型人才,解决全链路实物流断点,提升企业的运营效率和竞争力,实现长期的可持续发展。
3)技术创新与应用
我们积极引入和应用物联网(IoT)、大数据分析、人工智能(AI)、机器人技术等先进技术,提升生产自动化和智能化水平。同时,集团注重自主研发,开发了多种智能制造系统和设备,如智能生产线、智能仓储系统、多系统集成平台等。
① 物联网与大数据
通过传感器和物联网设备,实时采集生产过程中的各种数据,建立了完善的数据管理体系,打通端到端数据链路。利用大数据分析技术,对采集的数据进行深入分析,支持生产过程中的智能决策和优化,实现632全流程系统标准化、数字化T+3、数字化1.0、数字化2.0等重大变革。
② 人工智能与机器人技术
工厂在生产线上广泛应用机器人技术,实现了多种复杂操作的自动化。例如,在武汉美的暖通工厂,机器人臂在精确控制的环境下进行组装、焊接、检测与包装等操作。AI在视觉检测方面的应用,具体包括静态视觉检测和动态视觉检测,提升了生产效率和产品质量。
4)数据驱动与智能决策
通过数据采集与管理,实时监控生产过程中的各种数据,利用大数据分析技术进行深入分析,支持生产过程中的智能决策和优化。例如,通过数据分析打破设备运营壁垒,对设备的关键部件进行故障预测维护,提升设备使用效率。
5)人才培养与团队建设
美的为员工提供了系统的技能培训,提升他们的技术水平和操作能力,搭建复合型人才组织。建立了跨部门的协作团队,确保各部门之间的信息共享和协同工作,推动智能制造项目的顺利实施。
6)持续改进与优化
建立了有效的反馈机制,及时收集和处理生产过程中出现的问题。根据反馈和数据分析结果,持续优化生产流程和技术应用,不断提升智能制造水平。