本文为“2024年度中国智能制造最佳应用实践奖”参评案例。本次活动将评选出2024年度,为中国智能制造领域带来突出效益的最佳实践工程,全面介绍企业推进智能制造的步骤、重点与难点、获得效益等,分享建设过程中的经验,供广大制造业行业企业学习供鉴。
一、企业简介
中电建武汉铁塔有限公司(简称“武汉铁塔”) 成立于1958年,是世界500强中国电力建设集团有限公司下属中电建装备集团全资子企业。公司注册资金1.5亿元,是国家高新技术企业、国家级专精特新小巨人企业,拥有华中地区最大的智能制造基地。公司深耕精工钢结构产品制造领域,具备钢结构、输电线路电力铁塔(10kV—1100kV等级全覆盖)、钢管塔、5G通讯塔、光伏支架、风电塔筒等产品的研发和制造能力,主营产品为大电网智能输电线路铁塔。目前,公司员工三百余人,2024年实现营收19.3亿元。
武汉铁塔是国内输电线路铁塔制造行业的“国家队”,通过内生式增长与外延式发展相结合的战略举措,保持了行业领先地位。根据公开招标资料统计,2024年国家电网、南方电网总计招标340.34亿元,武塔公司中标12.03亿元,占比3.54%,市场份额第一名。此外,武汉铁塔完成阳逻新厂区生产基地投产,规划产能20万吨,产品覆盖全系列全电压等级,规模优势凸显。依托华中区域优势,公司形成产能布局合理、产品交付能力强等竞争优势。同时,凭借业内领先的质量控制体系和售后服务能力,公司产品获得了中国电力电气行业铁塔十大品牌的荣誉,赢得了国内外客户的广泛赞誉和信赖。
二、企业在智能制造方面的现状
武汉铁塔在智能制造领域取得了显著进展,通过产品设计、质量管控、工厂建设、生产作业、设备管理、能源管理、环保管理、供应链服务这八个关键环节的典型场景应用,实现了全面数字化与智能化制造。公司集成了物联网、计算机、网络技术,搭建了智能化生产及集团管控系统,旨在打造大数据支撑、网络化共享、智能化协作的智慧供应链体系。同时,公司对老旧设备进行数据通讯和技术改造升级,打通与关键生产设备的数据链接,实现数字化系统与智能化设备互联互通,率先在行业推行智能制造生产管理模式。
在研发设计方面,公司采用了道亨TWSolid铁塔三维实体放样软件、Solidworks结构设计软件、3D3S通用结构设计分析软件等设计工具,以及ANSYS、SAP2000等仿真分析软件。在生产计划、制造、质量管理、采购、物料方面,公司采用了智能化生产及集团管控系统(生产管理系统)和国家电网供应链管理平台。在热浸镀锌过程管控和能源管理方面,公司分别采用了热浸镀锌生产线监控平台和ECM能源管理平台。
公司与设备制造商共同研发了自动化焊接机器人,实现了24小时连续作业,焊接速度高达1200mm/min,标志着公司在智能化装备技术应用方面取得了重大突破。公司引入了机器视觉在线检测技术,应用于输电铁塔构件制孔作业,实现了数据的实时传输与在线智能检测,进一步提升了产品质量。此外,公司引进了自动化焊接机器人、数控角钢冲孔生产线、数控角钢钻孔生产线、自动化激光切割机、智能化镀锌生产线等先进智能设备,降低了生产运营的成本,提高了原材料的利用率,还显著提升了生产能力和效率,增强了企业的整体竞争力。
三、参评智能制造项目详细情况介绍
武汉铁塔的智能制造工厂实践由三个建设阶段组成:电力铁塔三维实体放样系统、智能化生产及集团管控系统(生产管理系统)、热浸镀锌生产线监控平台。公司通过以智能化生产及集团管控系统为主,在平台的产品设计管理和生产管理环节分别衔接铁塔三维实体放样系统和热浸镀锌生产线监控平台,形成三位一体架构;通过建立产品全生命周期管理系统和智造车间管理系统,并在系统之间相互集成,与车间智能仓库和自动化生产线相结合,从而建立高效柔性、人机协同和动态调度的智能制造示范工厂。
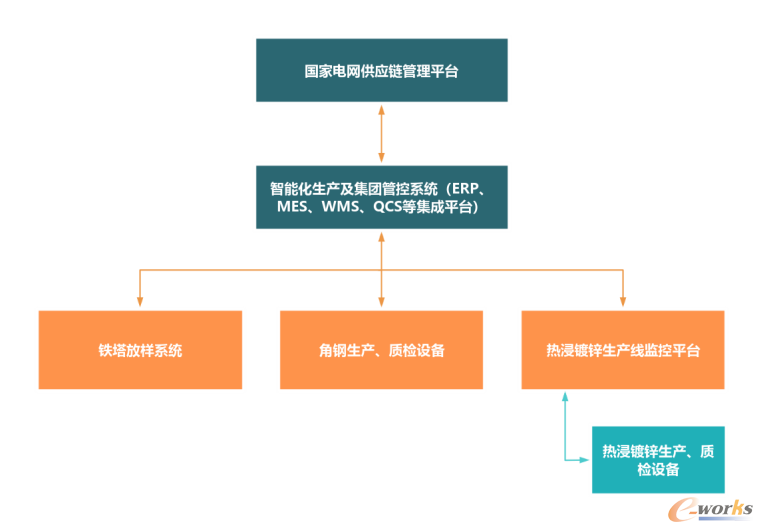
图1 总体架构
整体业务流程由智能化生产及集团管控系统通过网络从国家电网供应链管理平台自动获取生产订单,并建立以工程、塔型、塔位、工件号为数据主键的工件档案,此档案作为各系统数据互联的桥梁。依托智能化生产及集团管控系统和热浸镀锌生产线监控平台,各生产环节得以顺畅衔接。不断完善的工件档案不仅可向国家电网供应链管理平台反馈数据,实现智能化协同,还能在本地平台运用智能算法,进一步优化材料、能耗及人工成本节约策略,确保各环节协调统一、相互促进,共同推动智能制造工厂的高效运行。
1. 项目背景介绍
武汉铁塔采用传统电力铁塔三维设计软件进行放样时,难以覆盖设计工作的全部流程,存在制作工艺卡、NC数据处理繁琐,且与后续下料优化程序对接不畅。其次,公司订单具有多品种、小批量、交货期短、急件插单频繁的特点,而现有的生产组织模式依赖人工分解订单和调度,导致自动化程度低、效率低下,且难以实时跟踪生产进度。此外,目前公司镀锌生产的流程涉及多个环节和人工操作。为此,公司搭建了电力铁塔三维实体放样系统、智能化生产及集团管控系统(生产管理系统)、热浸镀锌生产线监控平台,实现研发效率、生产效率和管理水平的进一步提升。
2. 项目实施与应用情况详细介绍
1)产品数字化研发与设计
公司通过攻克完全参数化整塔模型、兼容各型三维数字化模型、集成分析计算、网络协同设计、可无缝对接智能化生产及集团管控系统等关键技术,打造了能覆盖放样到出图全流程的电力铁塔三维实体放样的系统,可无缝对接智能化生产及集团管控系统。电力铁塔三维实体放样系统建设具有如下特点:
a.放样自动化:通过三维放样自动生成铁塔主材、斜材和典型连接节点,大幅降低人工建模工作量,提升放样效率。
图2 电力铁塔三维实体放样系统
b.加工信息全息化:以三维模型为载体,附属工艺、制造等在内的各类加工信息,构建铁塔信息模型,形成完整的加工信息流,实现三维模型与生产设备的无缝对接。
c.试组虚拟化:以现有放样三维模型为基础,在前期基础上将模型导入平台系统,实现构件自动检测预警,为铁塔批量数字化生产提供依据。
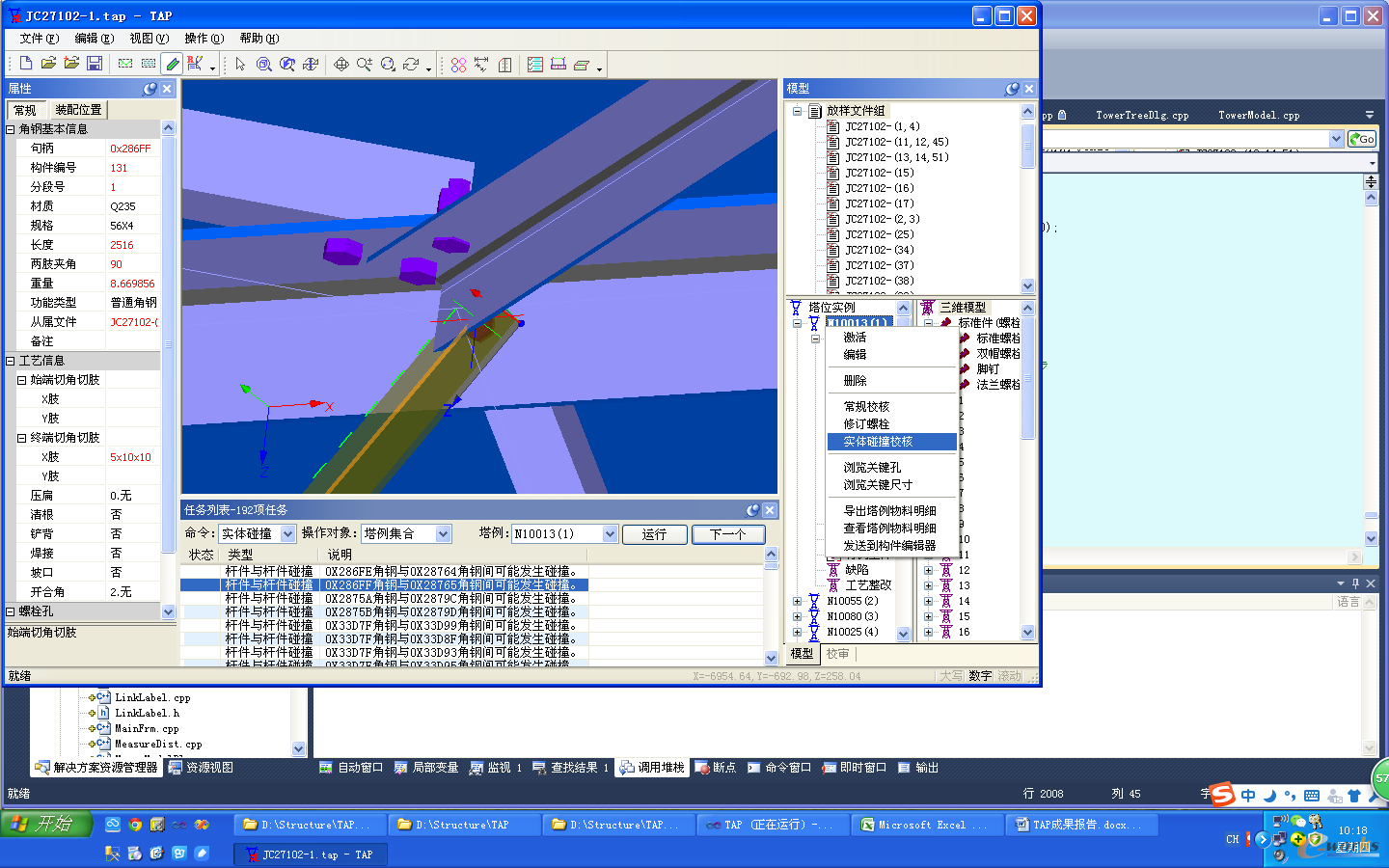
图3 铁塔试组实体碰撞检测
d.交付数字化:契合国家电网供应链管理平台建设,构件铁塔数字化模型,实现铁塔的数字化交付,同时也为电力铁塔常态化运维、应急抢修等全生命周期管理提供数据支撑。
2)智能化生产管控
该系统集成了MES、ERP、WMS、QMS等系统模块,为企业提供制造数据、生产调度、库存、质量、工作中心/设备、采购、项目看板、生产过程控制、数据集成分析等管理模块。员工可在工作站进行操作,管理者可以通过实时监测中心进行管理,实现制造协同。系统实施预期达到的效果如下:
a.放样模块对接道亨放样系统
生产计划制定后开始安排放样工作,按照塔型参数确定塔型配段,并整理相关图纸资料。指定放样任务负责人,在道亨放样软件中同步任务,进行塔型的具体放样操作,生成塔头框架、设置塔身横担等模块形状,输入结构参数并完成校对。放样成果数据同步到系统放样模块中进行放样成果管理,为车间生产与成品管理提供数据支撑。
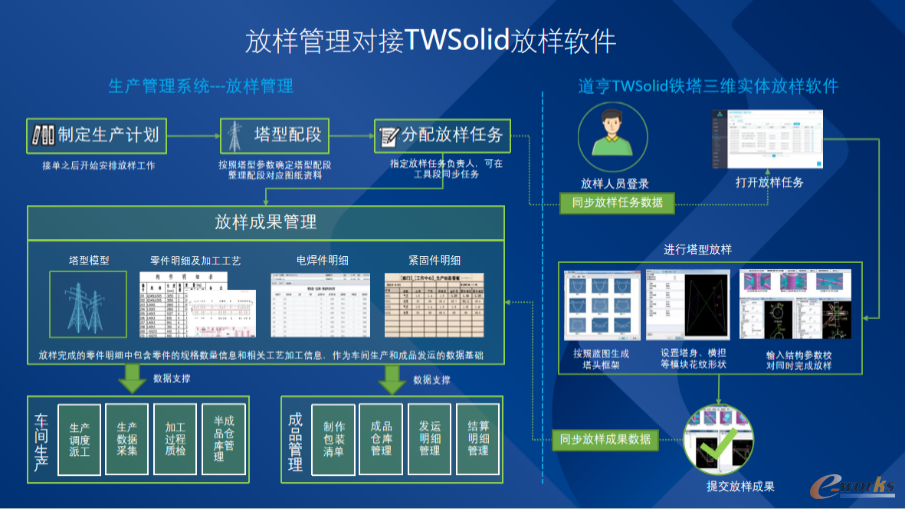
图4 放样模块对接道亨放样系统
b.出入库业务对接原材料仓库模块
通过终端自动可靠采集、自动判别、自动处理、自动控制所采集的原材料数据,利用条码技术将原材料到货验收、原材料入库、原材料出库、成品发运等信息自动同步到智能化生产管控系统,最大限度降低人工操作所带来的弊端,减少数据传递错误可能。
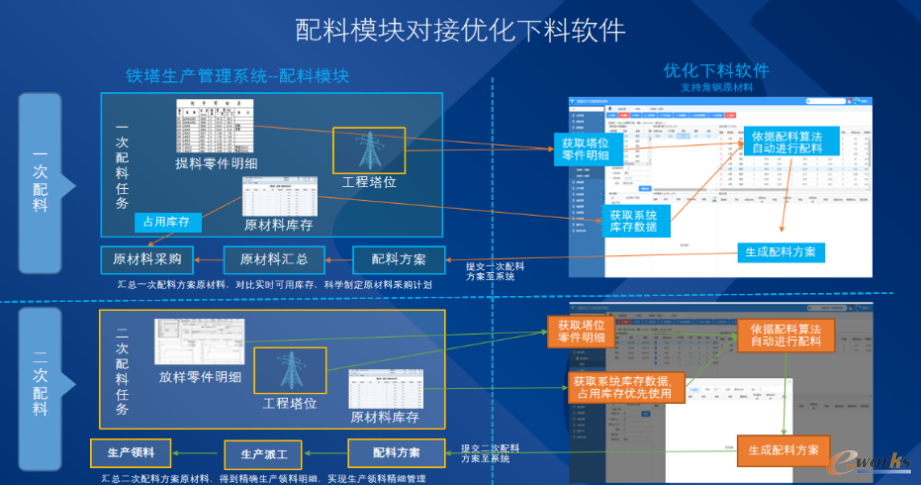
图5 配料模块对接优化下料软件
c.加工工艺数据对接车间设备机台
生产派工中心根据工程加工明细、工艺卡等信息,按工序筛选将生产任务派发至设备,设备与生产派工中心进行指令解析、排产信息下达、工艺参数解析、设备实时监控数据、报警故障处理、加工结束后处理信息交换,并通过设备数据采集与扫码采集方式,将有关信息传至生产管理决策中心, 完成设备生产统计、产线状态方针预警、设备运行预警、设备数据采集与监控。
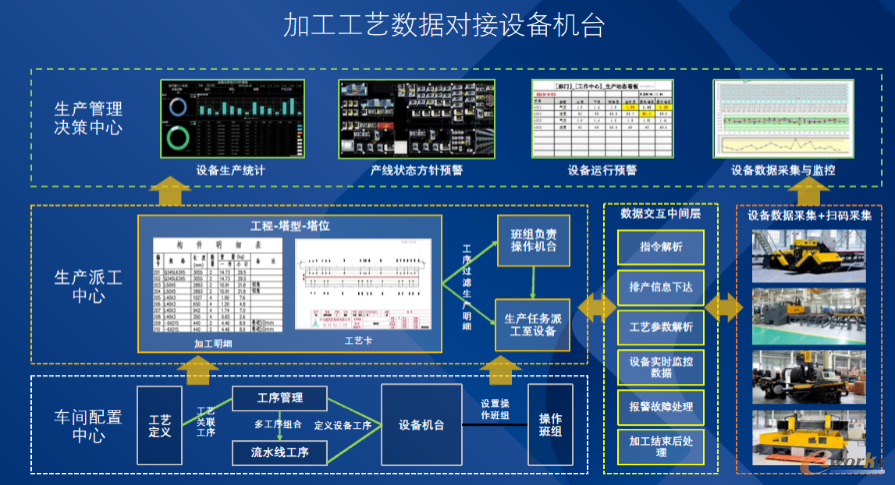
图6 加工工艺数据对接车间设备机台
d.铁塔加工数据结构化
按照塔型(按工程进行存储)-配段(塔型包含固定的配段集合)-塔参(塔型不同呼高对应不同塔参,对应同塔型下不同配段组合)- 塔位(线路中一个或多个塔位对应一个塔参)方式进行加工数据结构化。
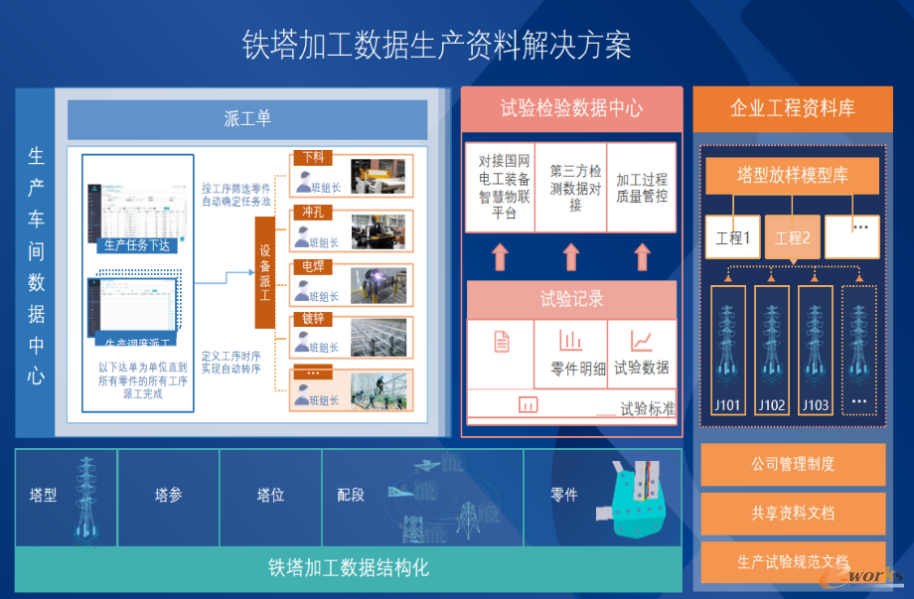
图7 铁塔加工数据结构化
3)数字化热浸镀锌生产管理
为进一步提升热浸镀锌业务的管理能力,公司搭建了热浸镀锌生产线监控平台,并与智能化生产管控系统实现衔接。该平台从生产管理系统获取订单,建立工单、批次单两级管理模型,关联经过物联网改造的生产设备、环保设备、质检设备,将加工状态返回生产管理系统采集监控、工单信息、炉窑等数据后,以多媒体形式呈现在现场指定位置安装的显示屏上。热浸镀锌生产线监控平台具有如下特征:
a.锌层厚度测量:镀件镀锌完成后,采用特定的锌层厚度测量仪和手机APP测量镀件的锌层厚度,测量20个点,系统自动核算测点的平均值并上传结果到平台。
b.产量成本统计:系统统计分析每日每班次的镀锌产量、挂次、人工、加锌量、合金量、锌液面值和锌耗。其中人工、加锌量、加合金量、锌液面等数值需手动输入。每挂次的重量可由称重系统自动称重导入数值。通过锌消耗量=锌液面差*每毫米锌重量+加锌量+加合金量的公式,计算得出锌消耗量。
c.生产排产:在完成产线、班组、客户、产品分类等基础信息,以及工程名称、塔型、南网/国网标准、基数、产品分类等工单信息录入后,以工单、挂次来进行生产排产。
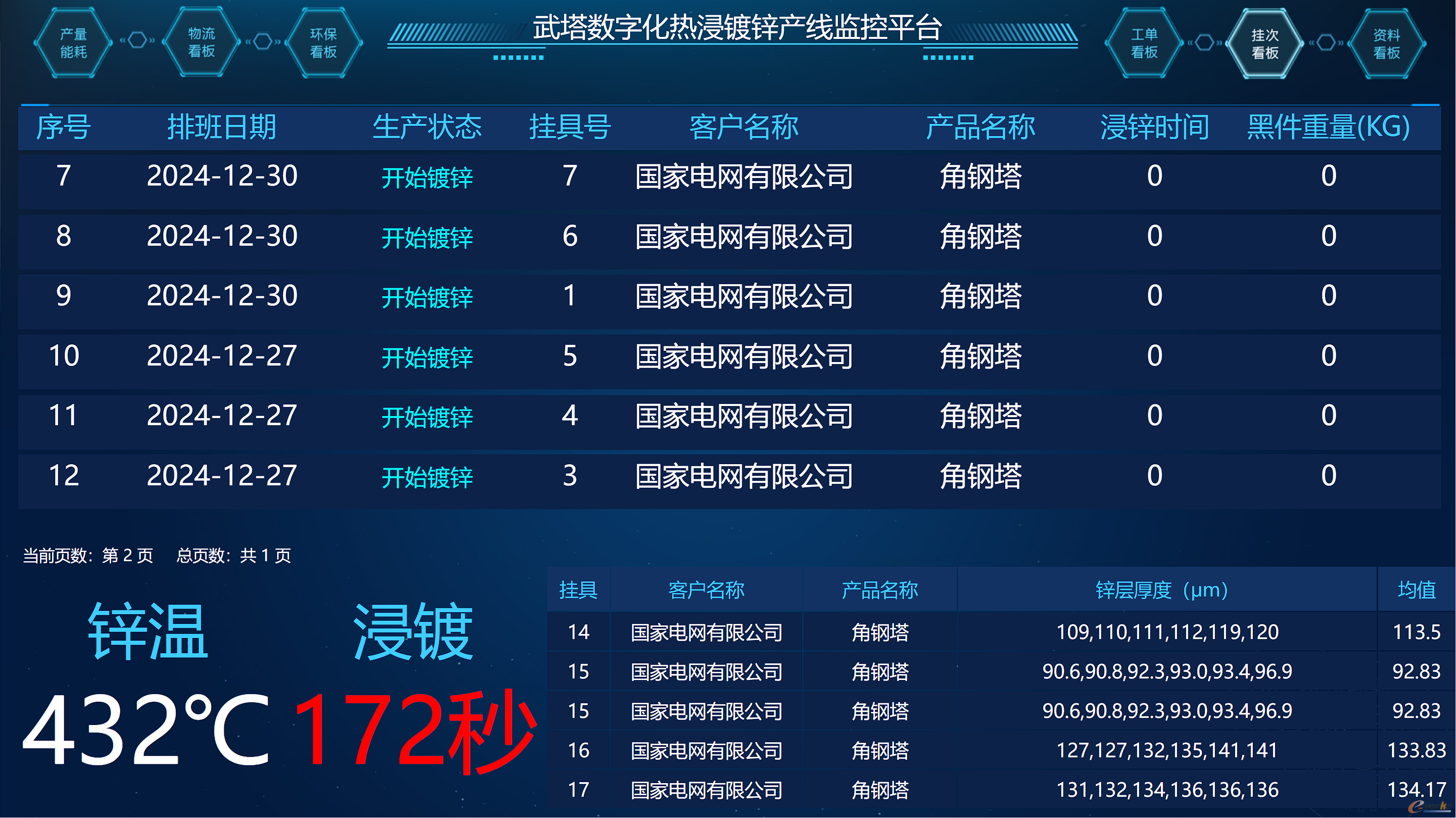
图8 挂次看板
d.环保设备参数收集:系统通过网络与各环保设备的PLC连接,采集环保设备运行参数,形成看板数据,展示在环保看板上。

图9 环保看板
e.炉窑参数收集:系统通过网络与各炉窑设备的PLC连接,采集炉窑设备运行参数,形成看板数据,展示在炉窑看板上。

图10 炉窑看板
f.看板展示:系统采集监控、工单信息、炉窑、能耗等数据后,以多媒体形式呈现在现场指定位置安装的显示屏上。一共配备炉窑、监控、挂次、环保设备、电气能耗和资料管理五块显示屏。
3. 效益分析
通过智能制造工厂实践,武汉铁塔获得了如下效益:
(1)电力铁塔三维实体放样系统
电力铁塔三维实体放样系统搭建完成后,提高了公司产品设计水平,缩短了放样周期,加速了产品制造周期,降低了生产成本,提升了公司的交货能力、技术人员研发工作效率,使得公司竞争力大幅提升,经济效益明显。建设完成后,技术人员效率提升了40%,以500kV工程为例,放样周期由原来的平均5天降低为平均3天。此外,该系统能够与智能化生产及集团管控系统实现数据共享,减少二次录入工作。
(2)智能化生产及集团管控系统
本系统在本行业创新性地建立了能覆盖产品全生命周期的智能化生产管控系统,通过生产过程、工单进度等流程管理实现对生产订单所有执行过程控制和管理,大大提高企业生产效率,实现生产的管理规范化。通过系统对数据的智能化分析反馈,公司生产管理机构设置更合理、业务流程更科学、人工需求更低,运营成本下降10%。智能化生产管理使生产一线人员生产效率提高10%,单位产品成本下降4%,质量损失率下降10%,研发周期缩短20%,对市场响应速度更快,产品生产周期大幅缩短。同时,该系统可与国家电网供应链管理平台智能化协作,使公司售后服务更先进。项目的建设应用,使公司的管理水平极大提高。
(3)热浸镀锌生产线监控平台
热浸镀锌生产线监控平台的实施,实现了锌层测厚、设备状态监控等工作的数字化,扩充了热镀锌业务生产管理工具,助推镀锌工艺提升。今年电力铁塔产品锌耗从2023年39.24kg/吨降至36.79kg/吨,同比降低6.24%。2024年1-12月,镀锌生产量为92047吨,平均锌锭单价2.5万/吨,总计为公司节约成本近500万元,有力推动公司技术创新、转型升级,为公司高质量发展赋能增效。