本文为“2024年度中国智能制造最佳应用实践奖”参评案例。本次活动将评选出2024年度,为中国智能制造领域带来突出效益的最佳实践工程,全面介绍企业推进智能制造的步骤、重点与难点、获得效益等,分享建设过程中的经验,供广大制造业行业企业学习供鉴。
一、企业简介
浙江伟星新型建材股份有限公司成立于1999年,2010年3月在深交所挂牌上市。公司专业研发、制造和销售各类高品质的PP-R、PE等新型塑料管道,产品主要应用于建筑给排水、采暖、市政供水、排水排污、燃气等领域。目前公司在浙江、上海、天津、重庆、西安以及泰国建有制造基地。2023年公司总资产72.92亿元,净资产57.49亿元,营业收入63.78亿元,净利润14.32亿元,净利润率22.91%。
公司入选“中国主板上市公司价值百强”、“中国上市公司创新能力指数百强”,连续10年获评“中国中小板上市公司价值五十强”,公司还荣获“全国五一劳动奖状”、“中国轻工业百强企业”、“中国轻工业塑料行业十强企业”、“浙江省商标品牌示范企业”、“浙江省人民政府质量奖”、“浙江省智能工厂”、“浙江省绿色工厂”等荣誉。
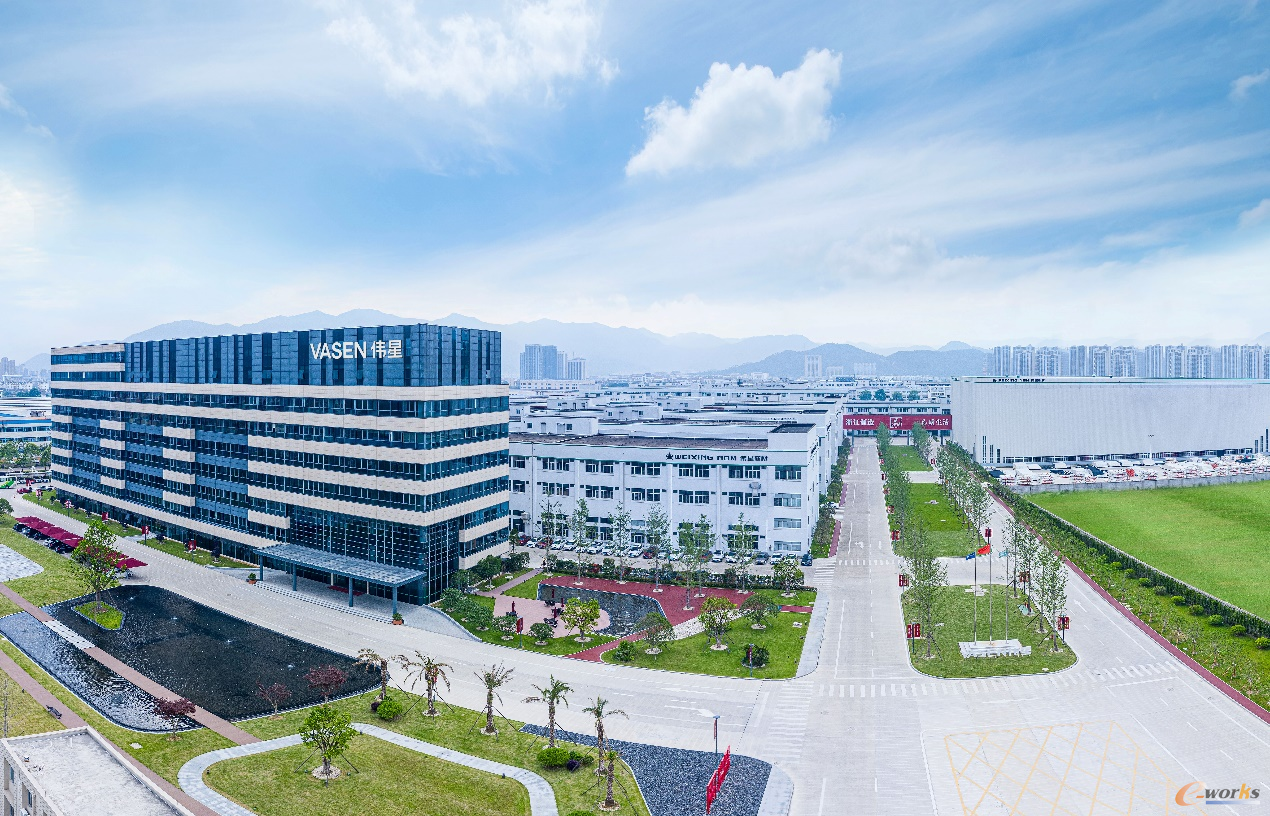
图1 浙江伟星新型建材股份有限公司
二、企业在智能制造方面的现状
伟星新材针对高性能塑料管道产品研发、生产制造与服务的难点、痛点与关键技术瓶颈,以伟星新材为项目责任单位并联合知名高校院所和工程服务商,聚集各类创新资源,发挥各自特色优势,共同建设伟星新材未来工厂并探索建立可供行业借鉴推广的智能制造新模式。通过关键自动化装备、智能在线检测、智能仓储物流、物联网与信息系统的开发、部署与应用,全面提升功能性塑料管道制造过程的数字化和智能化水平及关键智能制造装备的研制水平,显著提高产品的生产效率、产品质量与可靠性,降低运营成本、单位产值能耗,切实缩短产品研制周期,实现企业质量、效率、动力的三大变革。通过本项目的实施,企业要在装备研制、软件开发和标准制定等方面形成自主知识产权优势,进一步增强自主创新能力和核心竞争力,成为行业智能制造领导者,树立示范标杆引领全行业走向高质量发展之路,推动塑料管道生产过程从劳动密集型向技术密集型转变,为企业创造了可观的经济效益:
(1)构建了数字化设计研发平台,导入多种BIM设计工具和PDM管理系统,提升研发效率,加快产品研发过程。本项目还构建了供产销全流程闭环交付体系,优化了工厂布局和管件和管道生产工艺流程,通过星管家系统和订单系统等精确获取市场和产品需求,并通过ERP、MES、供应商协同平台等工业互联网系统快速组织生产。在生产过程中,通过设备联网系统、工艺专家数据库等实现工艺参数的快速下达和实时监控。通过本智能制造项目实施,管道和管件类产品研制周期缩短了35.4%。
(2)实施了全价值链质量数字化管控新模式,自主研发了检测管理系统、防伪防窜货系统、一码追溯系统等相应的信息系统,实现产品质量信息自上而下的全过程可追溯性,并通过生产过程的大数据分析平台,实现了生产质量信息的可视化监控。本项目实施后管道和管件产品的不良品率降低了55%。
(3)研发和实施了17项智能制造核心技术装备,在生产上实现了管件和管道产品生产自动输送料、自动搬运、自动装配、自动包装,在检测上实现基于机器视觉、激光传感等技术的智能检测,在物流上实现了以立体仓储为核心的智能物流,再加上全流程的数字化信息采集与智能化控制,本项目实施后,使用工数量减少了近三分之一,人均年产值提高54%。
(4)通过智能制造一系列项目的实施,伟星新材建立了高性能塑料管道智能制造新模式,引领管道行业自动化、数字化、智能化水平的整体提升,使伟星新材在管道行业的市场和品牌影响力更加突显。PPR管材管件市场占有率提升至12%,客户满意度提升至95.2%,伟星品牌价值提升至97.82亿元。
三、参评智能制造项目详细情况介绍
1.项目背景介绍
随着智能制造建设推进对质量管理的数字化转型提出了更高的要求,现阶段的质量信息化管理仍处于初级阶段,质量数据应用分析及质量管理水平与卓越质量(4.0)的管理要求差距较大。主要体现在以下几点:
(1)缺少统一的质量管理平台:各工业园各产品线操作/管理存在差异,分系统分平台操作(燃气管件一码追溯系统、PP-R管材MES系统),信息化程度差异大,数据交互缺失,产业与各工业园信息无法及时共享;
(2)质量标准和产品图纸缺少信息化管理,现场使用仍以纸质为主,质量信息不能及时、准确传递,导致无法进行有效及时品质管控;
(3)缺少质量数据的应用分析:没有系统平台将质量检验结果应用于生产过程质量管控和改进,同时质量检验结果无法管控业务流程(原料检验未合格已用于生产,出厂检测未完成已发货);
(4)缺失质量分析和质量预测,预警手段不足,生产过程质量异常分析及时性差(从检验质量向预防质量转型);
(5)传统的质量数据分析及报表形式,导致质量管理人员效率低,质量管理无法做精做细。
2.项目实施与应用情况详细介绍
2.1、项目目标
围绕质量4.0,以ISO9000质量管理体系为框架,基于H0平台,建立“一站式”全价值链质量管理新模式(QMS),实现质量数据的互通共享,提升产品质量,降低成本和风险。
(1)“一体化”质量数据采集、监控及预警系统,实现全业务链质量信息反馈(问题改进闭环),将各系统中(MES\SCC\SRM\LIMS)质量管理业务全价值链集成拉通,促进数据互通共享、提升质量管理协同水平。
(2)“一站式”智能质量管理平台,通过关键指标过程能力分析及实时监控、预警系统,提高质量风险预防、分析和解决效率,实现智能制造。同时结合提供多维度数据报表实时分析,为管理决策提供数据支持。
(3)“一中心”产业标准管理平台,产业物料标准、产品标准、设计标准、原辅料标准的集成管理,实现关键质量的统一治理,持续改进提升品质竞争力。
2.2、总体方案
以全面质量管理为目标,推动质量领域数字化建设,全面提升产业质量管控能力。具体的方案是实现“541”质量工程,1就是统一的QMS系统,5就是五个平台能力的建立:①建立质量标准平台,实现“一物一标准”;②建立检验数据平台,实现”一物一追溯“;③建立问题管理平台,实现质量问题的闭环;④建立变更管理平台,实现变更可视可控可查;⑤建立质量分析平台,实现质量数据应用分析。4就是品质工作的4个业务流程的数字化,包括研发品质、供方品质、制程品质、和市场品质。通过5+4+1最终达成质量数据透明,质量问题改善闭环,产品质量的稳定。
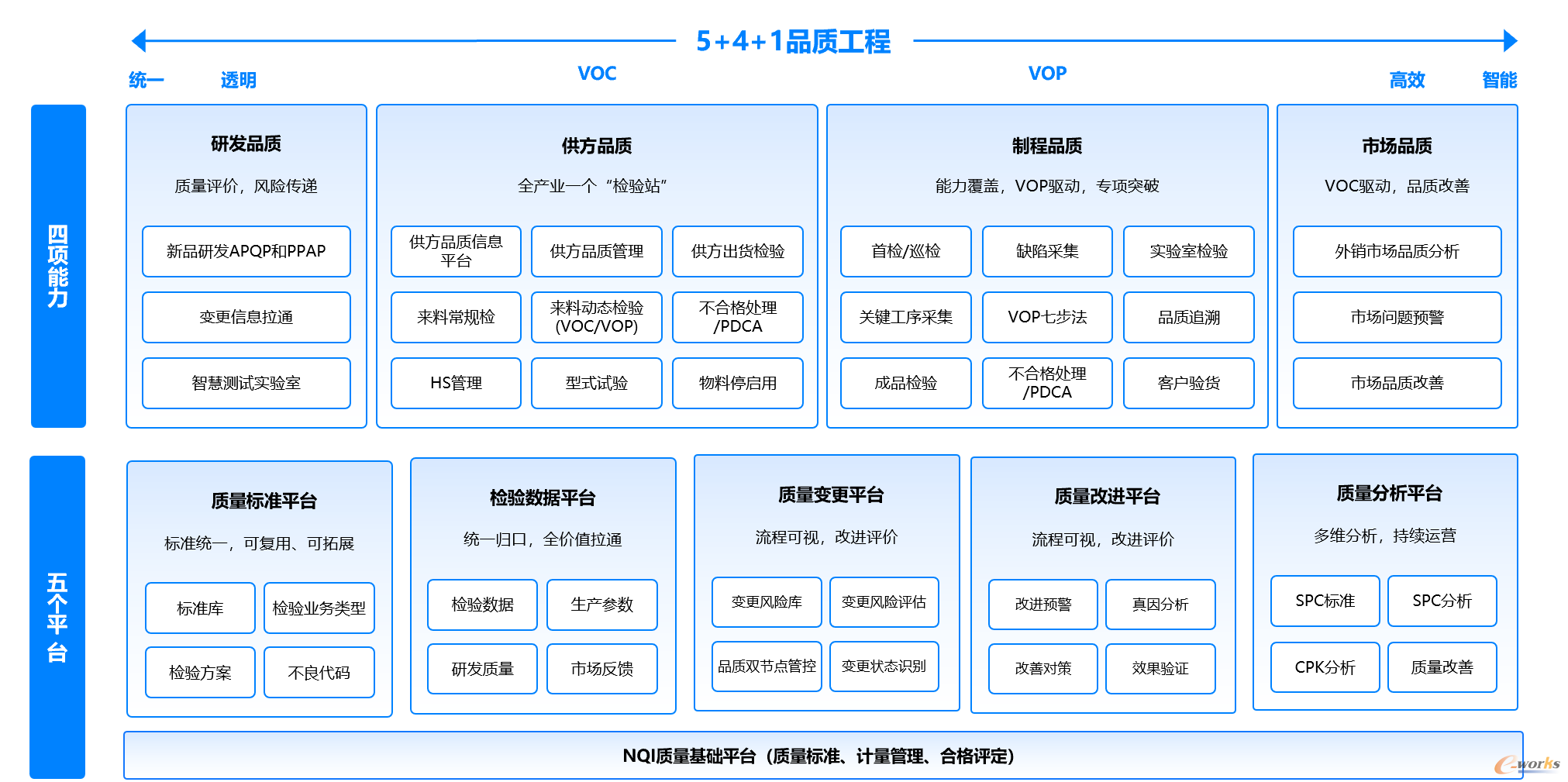
图2 总体方案
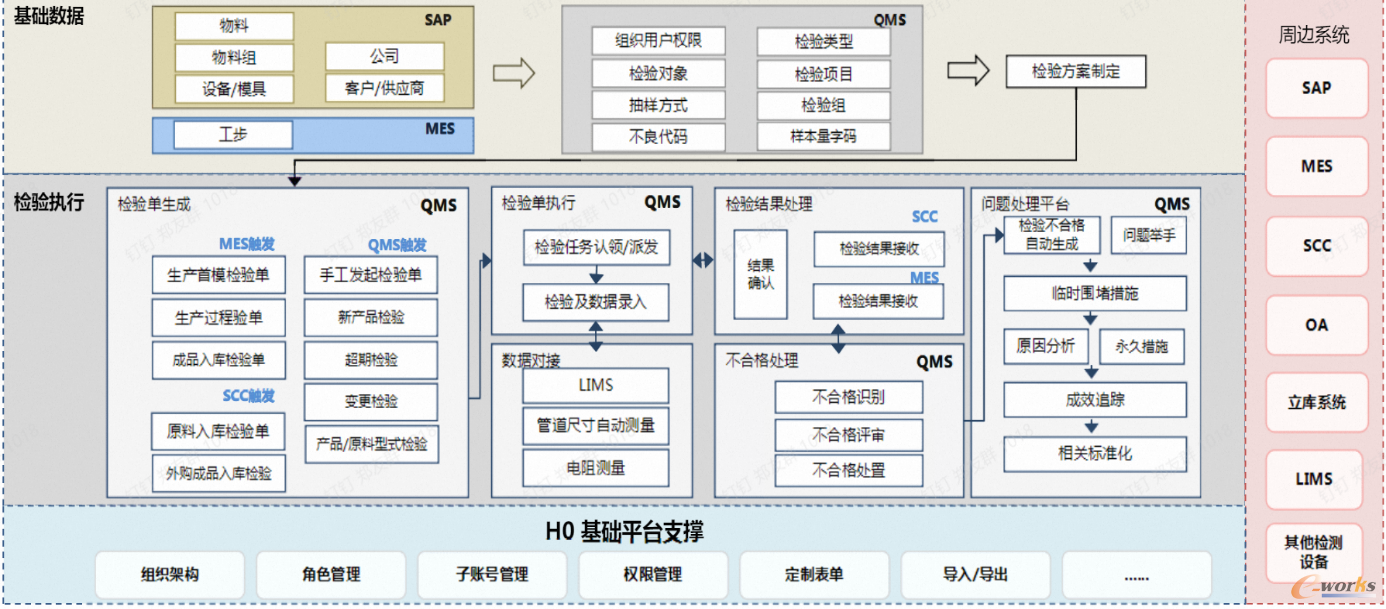
图3 功能方案
2.3.核心功能
通过“541”全价值链质量管控新模式的建设,实现质量检测业务“在线化、标准化、无纸化、自动化”;实现多系统协同交互,打通与其他业务模块信息化系统,跨部门质量业务协同;实现质量数据归口管理及报表分析,可实现质量数据追溯及质量分析改进等业务管理;实现未来智能质量管控,系统通过开发实现质量趋势分析、质量预警、质量预测,实现预防式质量管理。明细功能如下:
(1)建立质量标准库,梳理质量检验方案制定流程,实现“一物一标准”检验方案,所有工业园区全部统一平台、统一标准;
(2)建立研发质量平台,确保产品的设计和制造过程符合质量标准和客户要求,有效管理和跟踪客户提出的质量要求和协议,减少质量风险;
(3)建立供方质量平台,从源头把控质量,联动SRM系统,每批次送货自动生成来料检验单,检验结果联动SRM系统,作为供应商绩效考核的重要依据;
(4)建立制程质量平台,拉通生产过程中涉及的各运营系统,实现实物质量控制的闭环,确保每一生产环节都达到预定的质量标准;
(5)建立售后质量平台,通过完善的售后质量管理,以实现客户问题和需求的及时响应,提升客户服务的质量,增强客户对企业的信任和满意度;
(6)建立问题管理平台,将纠正预防措施单、质量事故单、不合格评审单等内容进行统一数字化管理;
(7)建立质量体系平台,按照ISO9001标准标准实施讲体系审核在线化管理,实时追踪和管理审核进度和结果,帮助组织更好地管理和控制审核过程,提升质量管理水平和绩效;
(8)引入SPC模块,基于质量标准库、质检数据、不合格信息、问题管理等数据,实现制造过程的稳态监控,质量报表的在线完成,进一步提升质量管理能力;
(9)建立计量器具的全生命周期管理,确保计量器具的合格使用、有效鉴定、可溯源。
3.效益分析
1)供方质量管理成效:公司通过不断完善供方质量管理,从2017年至2023年PP-R、PE 大宗原料采购成本节约9%;原辅料一次性采购合格率从2017年的92.3%提升至2023年的98.5%;采购误期率从2017年的0.13%降至2022年的0.06%。
2) 制程质量管理成效:现场质量管理重点做好“5到位”,即质量关键控制点识别到位、产前准备到位、产中检查检验到位、过程问题快速响应到位、产后总结分析到位,实现产品一次交检合格率大于98.5%;
3)建立质量管理大数据(数字化平台),实现质量形成过程显性化、可视化。组织研发、设计、采购、生产、检测、仓储、物流、销售、服务等业务全过程全链条数据采集检测分析;并针对产品质量安全打造“一码追溯系统”,将全过程的信息进行整合,做到一物一码,精准定位质量信息。
4)构建质量追溯责任体系,根据数字化质量追溯信息,开展质量责任追溯,明确质量问题各环节责任人,及时开展改进措施,明确奖惩。
本文为e-works原创投稿文章,未经e-works书面许可,任何人不得复制、转载、摘编等任何方式进行使用。如已是e-works授权合作伙伴,应在授权范围内使用。e-works内容合作伙伴申请热线:editor@e-works.net.cn tel:027-87592219/20/21。