从1956年第一辆中国自主造车在长春下线,到2003年整合产业链资源成立专业化载重车公司,再到现在构建覆盖"研-产-供-销-服"的智能生态,一汽解放的进化轨迹折射出中国制造业“从无到有,从专到优”的世纪转型。而今,这个曾用钢铁洪流支撑起共和国工业脊梁的企业,正经历着更深刻的蜕变:在客户需求碎片化与技术创新浪潮的双重挤压下,传统制造模式响应滞后、成本刚性的痼疾日益凸显,一汽解放25万辆年产销规模的背后,是毋庸置疑的数字化变革。
这场变革的本质,是数据要素对制造基因的重构。在全球商用车产业向智能化加速转型的浪潮中,一汽解放借鉴学习外部经验,引入国际先进的TOGAF企业架构方法论,对数字化转型的愿景进行了系统性的分层分级梳理,结合自身特点,完成了15个业务领域端到端的架构设计,为数字化转型稳步推进提供框架牵引。
在此基础上,一汽解在研发领域重构31个流程,构建覆盖“研-产-供-销-服”的大研发数智化平台,实现研发效率提升20%,设计活动上线率达90%。变革之下,是一场从“数据筑基”到“协同突围”再到“智能跃升”的数字化三级跳,更是中国装备制造业构建自主创新体系的生动实践。
第一跳 筑基:数据标准化重构研发基因
当行业仍普遍陷入纸质图纸与孤岛式研发,面临设计工具碎片化、变更管理低效的困境时,一汽解放率先启动数据基因重组工程,开启了其向前跃进的第一跳——“D”阶段,数据标准化。
自2001年起,一汽解放以PTC Windchill系统为数字中枢,构建起覆盖整车研发全周期的数据治理体系,进行产品数据管理(Data)的体系建设,为后续的协同创新奠定基础。借力于此,一汽解放将零散的零部件数据、BOM结构与设计文档纳入统一数字资产库进行集中管理,为研发流程注入标准化血液。同时,打通CAD工具链,实现Creo、CATIA、AutoCAD等设计工具的深度集成,确保设计数据的审批、电子签名和工程变更流程实现线上管控,更让研发合规性从“人治”转向“数治”。“D”阶段的技术基于Windchill版本的逐步升级,通过定制贴合企业业务的功能和流程超过180项,一汽解放不仅解决了设计数据分散的问题,最终使研发效率提升20%,也为后续协同创新奠定了坚实的数字底座。
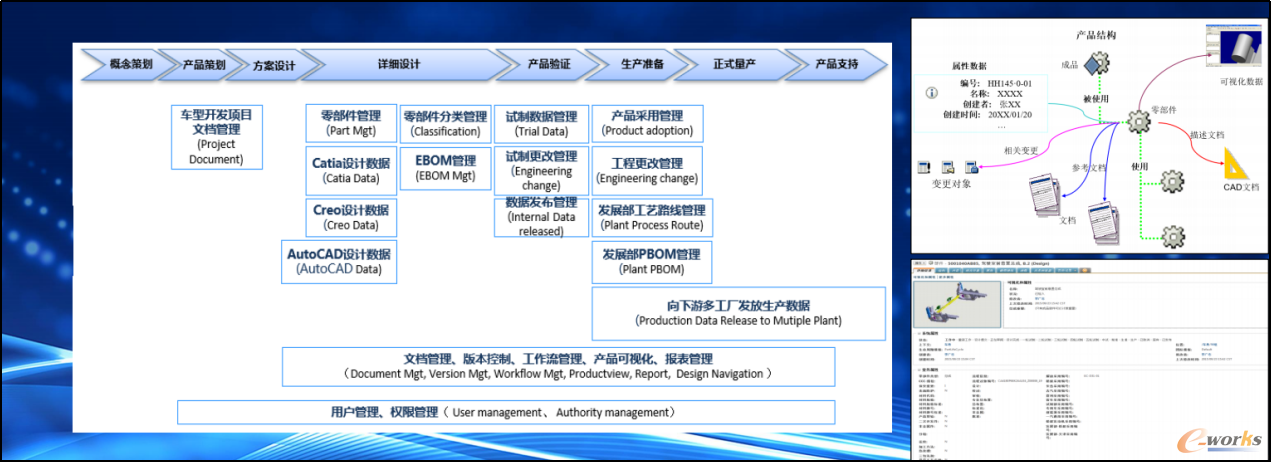
图1 “D”阶段-基础产品数据管理
第二跳 突围:全价值链协同创新
随着汽车行业模块化与定制化需求激增,单纯的数据集中已无法满足全价值链高效协同需求。2015年至2019年,一汽解放进入“C”阶段——协同产品开发(Collaboration)的关键阶段,直指研发体系深层痛点:EBOM搭建标准混乱导致工艺制造环节频繁返工,试制部门仍依赖线下获取设计数据,国产CAD工具与PDM系统的兼容断层,更成为协同链条上的堵点。面对这些挑战,一汽解放基于PLM系统,构建起多专业、多领域、多工具的协同体系,贯穿需求管理、设计文档管理、问题与变更管理等全流程。多专业协同方面,整车、动力、传动等各专业基于配置化EBOM协同开展车型设计开发工作,同时设立专门的配置化BOM管理组织和角色人员,确保数据的统一性和高效性。多领域协同方面,采购、工艺、制造等领域的代表在产品开发早期提前介入,通过流程驱动和系统接口实现设计数据的同源、及时和可追溯。多工具协同上,整车总布置设计师能够直接读取车身、电气等专业的设计数据,确保异构设计工具在线协同,提升数据的及时性和准确性。
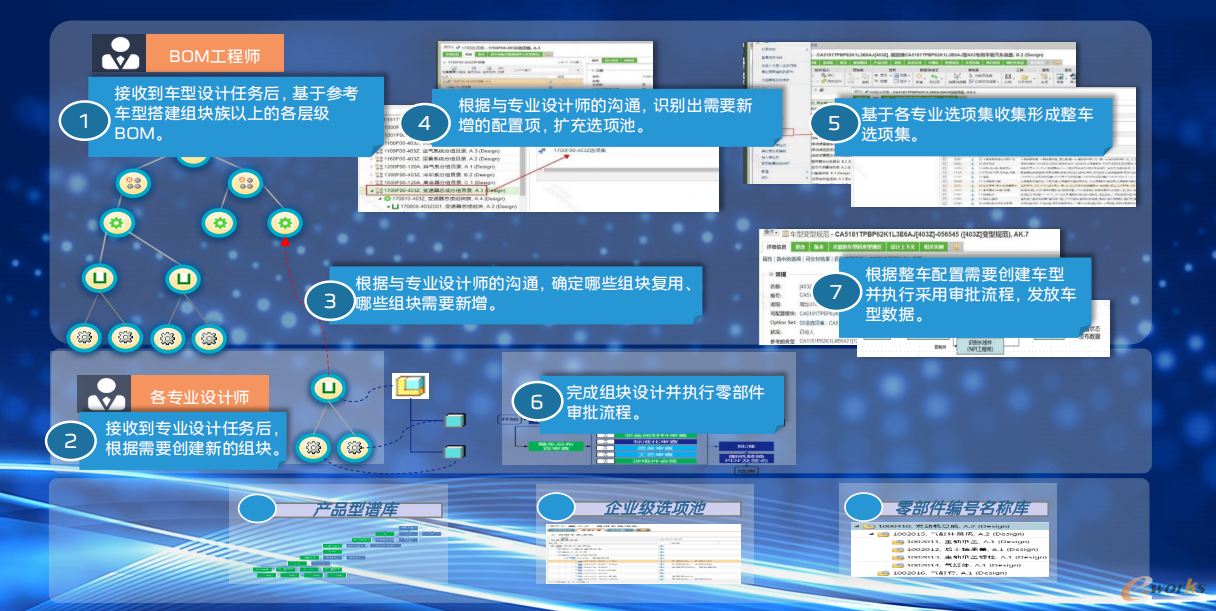
图2 “c”阶段-多专业协同
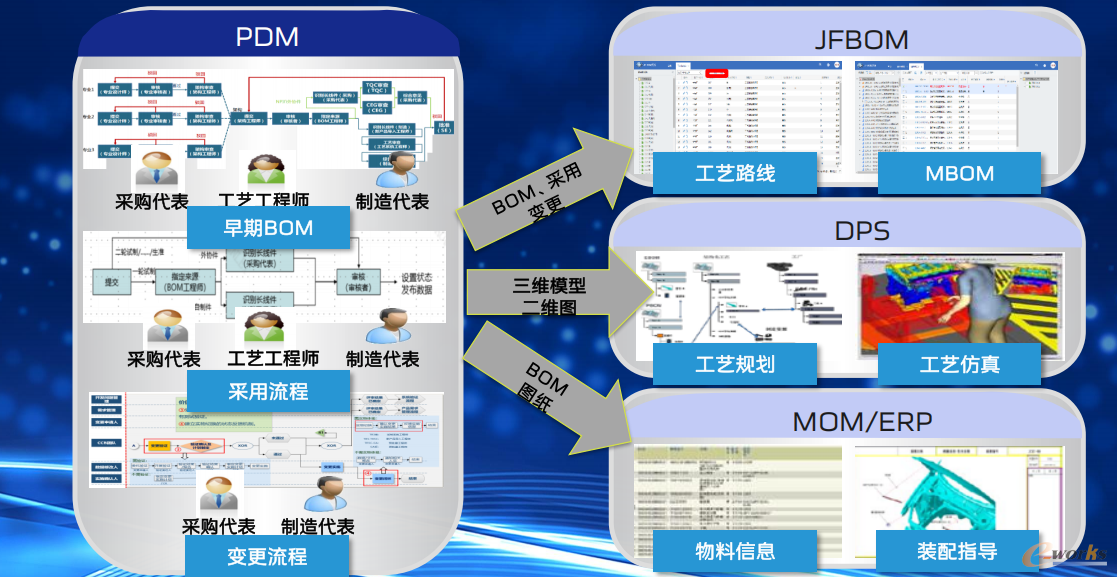
图3 “C”阶段-多领域协同
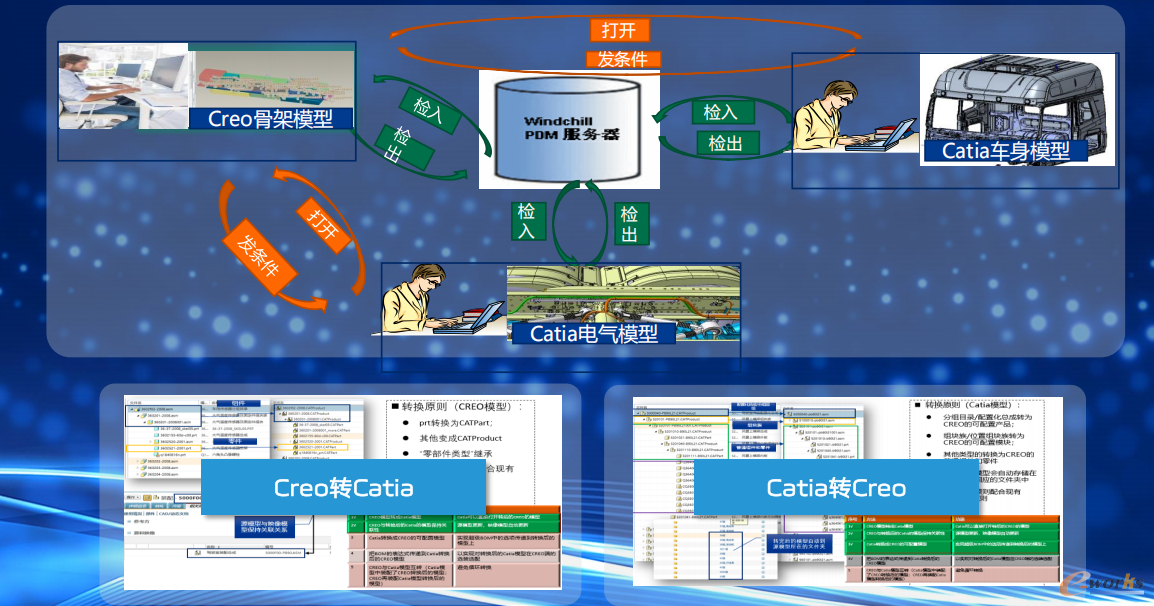
图4 “C”阶段-多工具协同
这一阶段的突破,标志着一汽解放从单一的数据管理迈向了全价值链的协同创新。这种以数据流动性打破部门壁垒的转型,使研发周期压缩成为可能,更在行业内首创了多专业在线协同的标准化范式。
第三跳 跃升:智能驱动的集成研发
步入智能研发新时代,一汽解放将数字化转型推向系统集成与模型驱动的新高度。2020年以后,一汽解放进入新一阶段——“I”阶段,集成式研发与智能化协同(Intelligence)。
一汽解放以IPD-IT集成架构为核心,逐步实现产品开发过程和产品模型的全面数字化支撑,同时PLM系统作为核心数据引擎,驱动着全三维设计模式的创新突破。基于PDM打造全过程、异构软件协同的数字化设计平台,Creo整车可直接获取Catia模型配置,实现车身与电气专业部件的选装选配。以PLM作为产品研发数据的核心数据源头,一汽解放消除了数据烟囱,确保产品数据按照开发过程的需求及时、准确地流转到研、产、供、销、服等各领域,为车型产品的高质量交付提供保障。
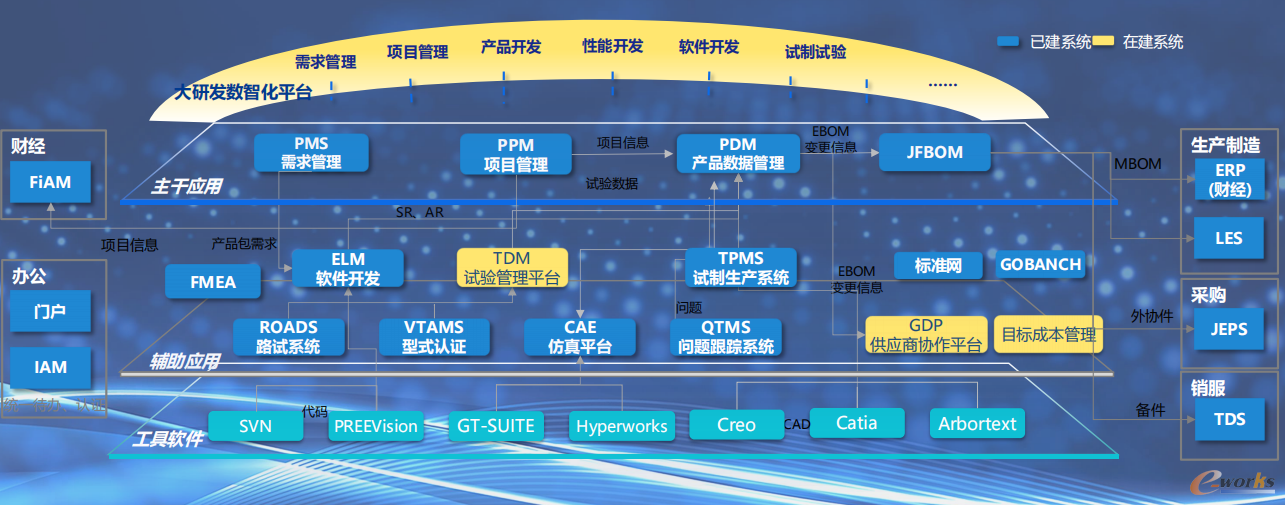
图5 “I”阶段-支撑集成式研发的关键平台
尤值一提的是,一汽解放全三维设计模式的创新是“I”阶段的一大亮点。针对公司全三维设计存在的问题,一汽解放基于解放研发数字化转型业务全景,通过全三维设计环境优化、全三维规范体系建设,实现基于模型的设计、仿真及应用一体化。其中,一汽解放团队基于Creo软件进行二次开发,创新性使用设计上下文工具通过勾选配置或零部件的方式创建及更新骨架(替代复制几何),实现骨架条件快速创建与更新,实现整车与专业间TOP-DOWN和DOWN-TOP闭环的在线实时协同设计。同时,一汽解放团队首创自动生成实例三维技术,创新性使用定位总成管理位置变化组块,使用坐标记忆技术记录组块所有位置,基于变型规范,系统自动扫描EBOM与CAD BOM,排除多余组块,自动创建或更新位置准确的实例或多配三维,实现基于用户订单自动生成位置准确的实例三维。
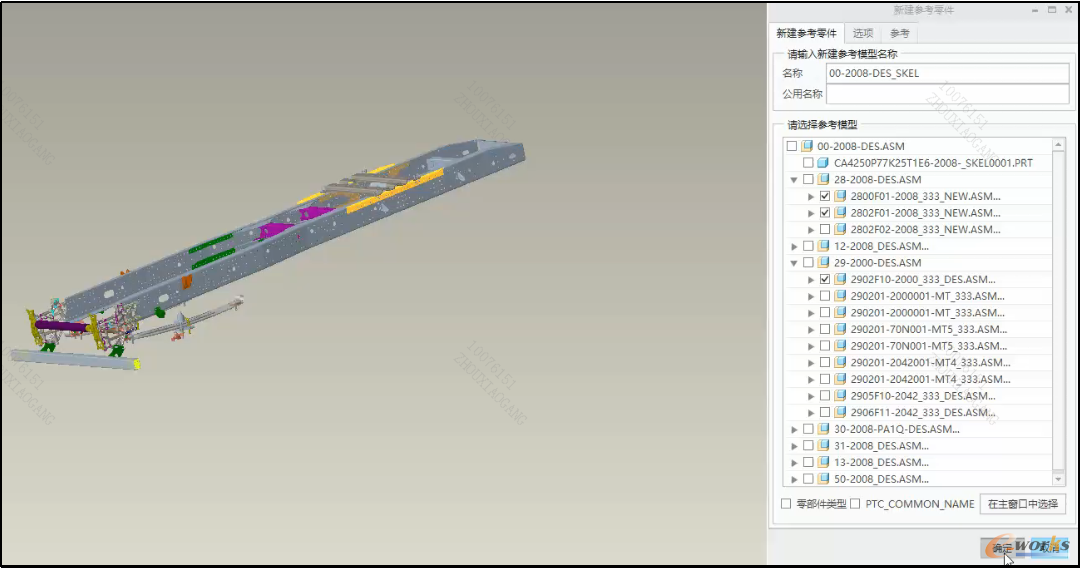
图6 骨架条件创建工具
通过智能驱动的集成研发,亚洲首辆全配置整车三维模型由此诞生,设计效率呈现指数级跃升:全三维设计效率提升40%,其中骨架条件创建效率提升80%、管束三维设计效率提升81%、整车大装配打开效率提升90%、自动生成实例三维位置准确达100%。
此外,一汽大众通过搭建“四化仿真平台”,打通设计-仿真-试验研发全场景业务,连接PDM、PPM等10多个系统,实现研发效率提升20%以上。这一阶段的智能化协同,不仅提升了研发效率,更为未来基于模型的设计、验证、工艺、制造和服务提供了唯一准确的数据源。
后记
回望一汽解放二十年的数字化转型之路,“客户主导的渐进式创新”是其方法论精髓。D-C-I的三阶演进,本质是需求牵引与技术驱动的动态平衡:当数据筑基阶段解决“看得见”的问题(设计效率),协同突围阶段攻克“够得着”的痛点(跨部门损耗),智能跃升阶段则瞄准“想不到”的可能(研发范式创新)。这种转型逻辑对制造业具有普适启示:数字化转型需遵循“业务痛点-技术方案-组织适配”的螺旋上升路径,避免陷入“为了数字化而数字化”的误区;同时,核心系统的自主可控至关重要,一汽解放基于PTC Windchill系统进行的多项定制开发,正是其能实现技术突破的关键。
站在新起点,一汽解放的实践仍在深化。当行业热议“软件定义汽车”时,其研发体系已延伸出数据服务新业态——基于二十年积累的研发数据资产,正孵化出预测性维护、远程诊断等智能服务产品,并加速布局AI驱动的智造生态。这种从“制造产品”向“经营数据”的进化,或许正是中国制造业穿越周期、制胜未来的密钥。
正如一汽解放所信仰的,追求卓越是一场永无止境的征程,面向未来,一汽解放正以“永无止境的追求”践行领军者担当,用更强的创新主动、更大的创新投入、更快的创新步伐,向着成为“中国第一,世界一流”的绿色智能交通运输解决方案提供者加速前进。