针对飞机零部件设计的特点,研究了全三维设计环境下知识驱动的飞机零部件智能建模技术。首先分析不同类型的零部件设计方法,梳理MBD模型的建模流程,然后结合工程需求研究了零部件智能设计关键技术,最后基于CAA二次开发技术对CATIA软件进行定制开发和扩展,建立支持零部件快速规范构建的辅助设计工具集。工程实践证明,该方法有效提高了工程师的设计效率,促进了全三维设计技术在型号研制中的应用。
随着全三维设计技术的广泛应用,三维模型已贯穿于设计制造的各个环节,不仅实现了设计理念和方式的变革,保证了设计制造数据的唯一性,也成为航空企业数字化产品的核心知识与重要资源。基于MBD(ModelBasedDefinition)的全三维设计是以集成的三维模型为核心,通过全三维定义技术来实现产品信息完整地表达,使三维模型除了包含几何信息外,还详细描述了零部件的模型属性、工程注释、连接关系、尺寸公差、加工工艺和检验要求等属性信息,使MBD模型成为产品研制的唯一依据,为产品设计、试验打样、工艺规划、工装设计和加工制造等研制环节提供统一的数据支持。但是,在应用CATIA软件建模过程中,许多复杂、繁琐的问题也日益凸现,如重复性工作多、费时费力,需要花大量时间、精力检查模型的规范性,设计知识、经验不能很好保存,难以进行创造性工作等。因此,如何更好地积累设计过程中的经验,避免设计师不必要的重复劳动,成为全三维数字化设计应用面临的一个重要问题。
针对全三维设计的上述问题,本文提出一种飞机零部件智能设计方法,基于组件应用架构CAA(Component Application Architecture)二次开发技术对CATIA软件进行定制开发,扩展功能,实现辅助工具与商业软件的高度集成,保证设计数据规范化能够快速重用,形成零部件设计知识库,支撑全三维关联设计的智能设计环境构建,为基于模型的航空产品设计、制造、服务一体化奠定了良好的基础。
1 基于MBD的全三维设计技术分析
按照产品组织形式,MBD模型可分为零件和装配模型,包含几何信息和非几何信息。零件MBD模型是由零件几何模型、属性信息、公差标注和制造等信息组成,其中,以三维实体的形式描述零件的几何形状,以CATIA软件的参数形式描述材料、重量、设计要求和版次等属性信息。装配MBD模型是一个特殊的零件,也叫8001模型,用来描述该装配件的下级零件之间的装配连接关系以及紧固件信息。
通过对型号研制中零部件设计流程的分析与梳理,设计人员在线开展工作,业务流程如图1所示。首先创建零部件节点后,应用设计工具构建点、线和面等几何实体,然后根据零件类型创建三维标注模板,添加零件工程注释,提取装配MBD模型连接定义中的标准件信息,完善模板中的材料、重量、版次和设计说明等属性信息,然后对几何模型和属性信息进行规范化检查,最后生成各类报表,提升数据成熟度后启动数据签审及发放流程。
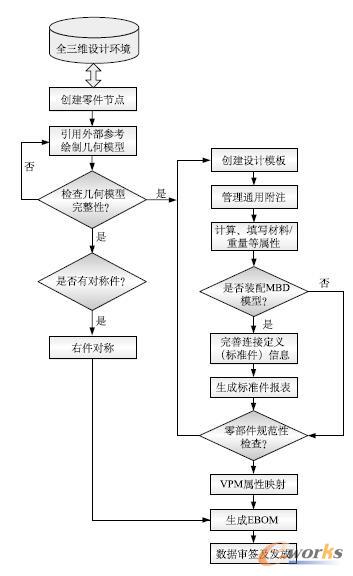
图1 全三维零部件设计流程
通过对零部件设计流程的梳理,发现应用MBD技术进行产品设计时,除了构建三维几何实体模型外,模型属性信息的查询、添加、修改和检查等操作繁琐,耗费时间长,易出现低级错误;建模知识经验不易积累,更难以重复利用。此外,飞机设计、制造配套的文件体系仍多以二维为主,不能适应全三维设计的需求。
(1)材料、工程注释和加工工艺等属性信息的创建与组织,因型号不同而具有较大差异性,手动填写时不规范且工作量大,同时,需要与材料库、附注库等信息库集成;
(2)长桁、框及角片等典型结构件,因设计师不同而具有多种设计方法或流程,不易提取设计数据且难以重用模型;
(3)零部件设计完成后,无法准确地检查几何元素和属性信息是否完整、合理,零件之间是否存在干涉,通常在数据审签环节被发现后需要重新迭代;
(4)工程材料清单(Engineering Bill Of Materials,EBOM)是设计数据向制造环节传递的一项必要文档,设计师从产品三维模型复制提取时,内容繁多、数据冗长,经常出现不必要的错误。
2 面向知识的零部件智能设计方法
通过分析在全三维设计环境中不同类型零部件的设计特点及存在问题,有必要对全三维设计模板、基于特征的典型结构件构建、零件规范化检查和属性映射等关键技术进行研究,集成已有的设计知识经验,减轻设计师的重复劳动,开发适用于型号研制的全三维设计工具,建立飞机零部件设计知识库,实现知识驱动的飞机零部件智能设计与建模。
2.1 基于XML的全三维设计模板构建
全三维设计模板用来在零件特征树上组织和管理零部件的非几何信息,零件模板包括材料描述、设计依据、模型属性、工程注释等属性信息。模型属性描述零件的重量、版次、对称性等信息;工程注释包含热处理、表面处理和油漆涂层等设计给出的工艺信息。装配件模板与零件模板略有不同,增加了“连接定义”,表示该装配件中零件与零件的连接关系。属性类别用CATIA软件的几何图形集表示,属性信息用参数变量表示,如图2所示。
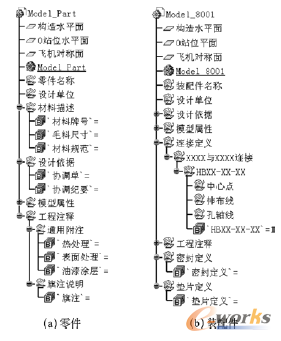
图2 全三维设计模板
全三维设计模板与零件编码库、材料库、工程附注库及标准库等实现信息共享交互,能够支持产品快速编码,辅助设计快速获取所需信息,自动计算零部件重量、重心及惯性矩等属性,实时积累设计知识。同时,可以通过XML文件的配置,实现符合不同型号需求的零件标准特征树的规范化、自动化构建。
2.2 基于特征的典型结构件的快速设计
特征设计是全三维设计技术的又一显著特点,是为某种工程应用而预先构想的模型,也是零件几何模板的一种体现形式。基于MBD的特征定义,能够更真实的表达设计意图,使知识的抽取及利用变得更容易。
基于特征的典型结构件的快速设计,是通过总结、提炼零件设计知识和标准规范文件,优化特征建模流程,建立典型零件特征设计模板库,进而应用CATIA二次开发及知识工程技术,构建基于特征的典型零件快速设计工具。设计师选择标准参数以及参考元素后,在零件模板上实例化生成典型特征,如下陷、减轻孔等,实现典型零件的规范化、最优化设计。图3为基于特征的典型结构件的设计流程。
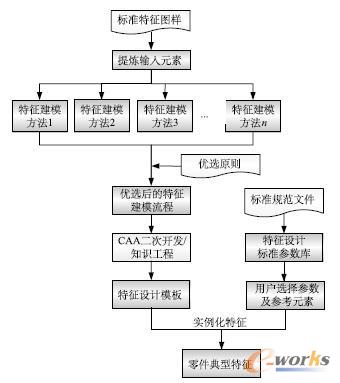
图3 基于特征的典型结构件的设计流程
2.3 零部件规范化检查
产品数字化模型未采用统一的设计规范,是全三维设计技术应用过程中最常见的问题,不合理的建模顺序使数模无法参数化、系列化设计,没有材料或质量等信息导致CAE部门无法进行强度、重心分析工作,不能满足VPM系统对产品数据管理的要求等。
零部件规范化检查面向数字化设计与制造,解决手工状态下MBD模型检查过程中工作量大、效率低的问题,快速准确地检查产品设计模型的规范性和合理性,使设计师把更多的精力用于具有创造性的工作中。
规范化检查知识分为几何类与非几何类2种。几何类检查,如圆角半径检查、当前工作对象检查、零件更新检查、重量等属性值检查等;非几何类检查,如结构树规范性检查、命名(编码)规范性检查、参数对应关系检查等。
本文来源于互联网,e-works本着传播知识、有益学习和研究的目的进行的转载,为网友免费提供,并以尽力标明作者与出处,如有著作权人或出版方提出异议,本站将立即删除。如果您对文章转载有任何疑问请告之我们,以便我们及时纠正。联系方式:editor@e-works.net.cn tel:027-87592219/20/21。