本文为“2018年度中国两化融合暨智能制造应用领先暨最佳实践奖”参评案例。本次活动将评选出2018年度,为中国两化融合暨智能制造领域带来突出效益的最佳实践工程,全面介绍企业推进两化融合或者智能制造的步骤、重点与难点、获得效益等,分享建设过程中的经验,供广大制造业行业企业学习供鉴。
一、企业简介
大连中远海运川崎船舶工程有限公司是原中远造船工业公司与日本川崎重工业株式会社、南通中远海运川崎船舶工程有限公司合资兴建的大型造船企业。公司成立于2007年7月18日,注册资金26.2亿元人民币,是中远造船和川崎重工继南通中远川崎后,投资建设的第二家现代化大型船舶企业。经过多年积累和发展,公司培养造就了一支高素质员工队伍,现有从业人数达2147人,其中本工1594人,队伍结构合理,文化教育程度较高,业务能力较强。公司经营和营利能力良好,2017年销售收入20.8亿元。
自公司成立以来,设计建造的船型包括2万箱级超大型集装箱船、30.8万吨超大型油轮、30万吨级矿砂船、20.5万吨散货轮、5.8万吨散货船、6.1万吨散货船、8.1万吨散货船。储备的船型包括6.4万吨散货船、汽车滚装船、重吊船和LNG天然气运输船等。大连中远海运川崎以“建世界一流船厂、造世界一流船舶”为目标,积极推行质量、环境、职业健康安全管理标准,充分借鉴日本川崎重工和南通中远海运川崎先进的造船技术、制造工艺和管理体系,并结合实际,创新超越,着力打造国内领先、世界一流、行业内最具竞争力的造船企业。
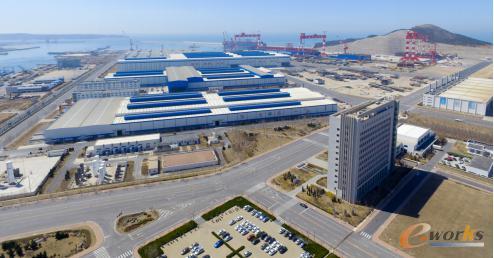
图1 大连中远海运川崎船舶工程有限公司
二、企业在智能制造方面的现状
公司运用高精度感知控制、智能机器人技术,契合企业先进工艺流程,已自主开发定制了以下智能设备和生产线:全面数码打印机是世界首台实现钢板全幅面数码印字工艺的智能设备,它为预处理后的钢板打印上所有的加工信息,这些信息覆盖钢板整个加工周期,为后道工序智能识别提供了必要基础;先行分段智能焊接机器人和管材智能焊接机器人在保障高焊接质量的同时,使生产效率提高2至3倍,已达到世界先进、行业领先水平;FCB/RF焊接设备可支持40mm厚板单面焊接双面成形,是国内首台;型钢自动切割生产线和条材自动加工生产线已实现无人化/少人化作业。
公司综合运用TRIBON/AM12、NAPA等软件,集成CAD/CAPP/CAM系统,实现100%三维数字化建模、模拟仿真检验、异地协同设计、产品数据全生命周期管理。
公司基于集成框架和数据分析技术,结合公司管理模式分别定制了ERP系统和MES系统。ERP系统集供、销、存、工时、成本管理等功能,实现资源平衡、协同优化、辅助决策;MES系统集拉动式排程、生产过程采集与分析、质量控制等功能,实现设备与信息系统之间的互联互通,设备/产线数据采集,生产指令快速下达、生产过程可视化等管理。
公司通过不断的攻关,已初步建立了以数字化、模型化、自动化、信息化、可视化、集成化为特征的智能化造船和生产管理体系,实现了研发、设计、生产、管理等环节全面融合、协同运行。通过项目初步的信息化智能化改造,公司在钢材利用率、全员劳动生产率、造船生产率、单位土地产能均居行业前列,已经成为中国船舶工业的先进企业。
三、参评智能制造项目详细情况介绍
以“智能船厂”为规划最终目标,通过信息化数字化改造,智能设计,智能装备,智能车间一步一步完成智能船厂的总体规划。
针对厂区和车间工艺流程及布局架构优化设计、先进设计技术应用和产品数据管理系统建设、智能制造装备应用、制造运营管理平台及与关联系统的集成、以及信息安全保障制度和技术进行的实施。整个项目以需求、技术创新、结构优化为驱动组织实施。从船型研发设计、造船生产管理、物流管理,到制造工艺、企业管理的全过程信息化管理平台,使公司数字化设计、生产装备智能化升级、工艺流程优化、精益生产、可视化管理、质量控制等方面得到大幅提升。
公司引进川崎重工先进造船技术、制造工艺和管理体系,结合自身实际情况,通过制造执行系统(MES)建立了拉动式生产计划管理体系,对设计及周边系统、ERP系统进行二次开发,实现了100%数字化建模、多专业异地并行设计协同作业;利用工业互联网和传感器信息采集技术,实现智能设备与设计、业务系统互联互通,并能实时采集、分析生产数据,为生产管理和决策提供依据。目前已完成全面数码打印机、先行分段智能焊接机器人、FCB/RF焊接设备、型钢自动切割生产线、条材自动加工生产线、管材智能焊接机器人等15条智能化设备和生产线。
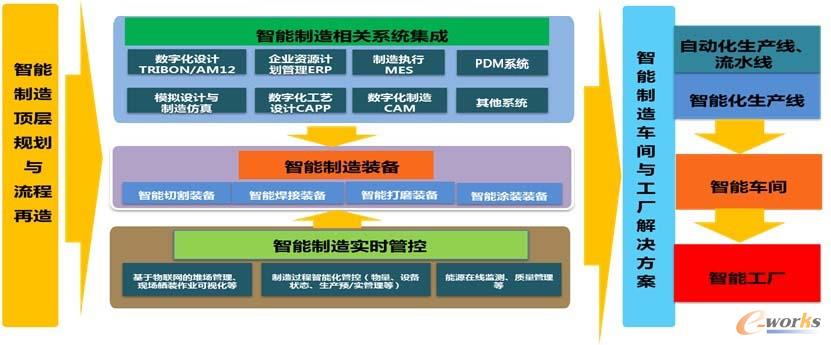
图2 智能制造项目概况
1.项目背景介绍
当前,全球造船市场面临新一轮科技革命和产业变革,制造业“数字化、自动化、信息化、网络化、智能化”已成为变革的发展趋势。实现由造船大国向造船强国的转变,智能制造是必由之路;也是我国实现弯道超车的重要途径。为进一步提高市场竞争力,在快节奏生产中保障船舶建造的质量、缩短建造周期,以智能制造为手段,建设智能船厂及数字化车间,推动发展高技术、高附加值船舶建造技术,是我国船舶工业发展的必要条件。船舶制造也正朝着设计智能化、产品智能化、管理精细化和信息集成化等方向发展,世界造船强国已经提出打造智能船厂的目标。
公司积极落实国家《智能制造发展规划(2016-2020年)》,提出智能制造构架蓝图和实施策略,以“全面数字化+核心智能化”为目标,以信息化促进智能化,通过扩大智能化设备应用,完备信息化管理体系,励志成为造船行业智能制造典范,并也于2018年成功被工信部评为了智能制造试点示范企业。
大连中远海运川崎在成功复制川崎重工的工艺流程、作业基准、信息化技术以及管理理念的基础上,通过先进信息化技术和自动化装备应用全面推进智能化造船。本项目针对厂区和车间工艺流程及布局架构优化设计、先进设计技术应用和产品数据管理系统建设、智能制造装备应用、制造运营管理平台及与关联系统的集成、以及信息安全保障制度和技术进行的实施。整个项目以需求、技术创新、结构优化为驱动组织实施。
公司通过吸收、创新、集成,建立了从船型研发设计、造船生产管理、物流管理,到制造工艺、企业管理的全过程信息化管理平台,使公司数字化设计、生产装备智能化升级、工艺流程优化、精益生产、可视化管理、质量控制等方面得到大幅提升。
公司主要信息平台及数据流如图3:
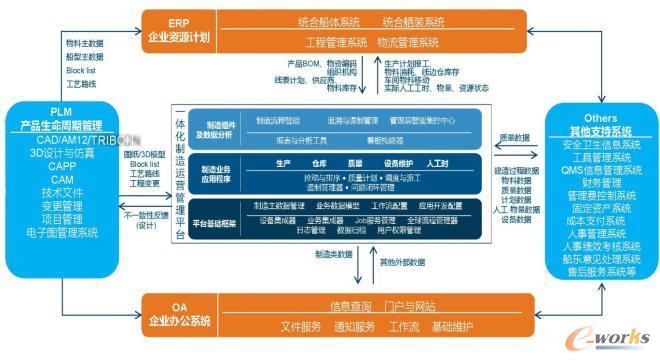
图3 主要信息平台及数据流
公司引进川崎重工先进造船技术、制造工艺和管理体系,结合自身实际情况,对设计及周边系统、ERP系统进行二次开发,实现了100%数字化建模、多专业异地并行设计协同作业;利用工业互联网和传感器信息采集技术,实现智能设备与设计、业务系统互联互通,并能实时采集、分析生产数据,为生产管理和决策提供依据。
公司积极响应国家“中国制造2025”发展规划,根据自身发展需要,加大对智能化生产设备的应用投入,对各生产线实施智能化升级。目前已引进完成全面数码打印机、先行分段智能焊接机器人、FCB/RF焊接设备、型钢自动切割生产线、条材自动加工生产线、管材智能焊接机器人等智能化设备和生产线。
此外,公司建立了完善的信息安全保障体系,于2014年初通过ISO/IEC:27001信息安全管理体系认证,具备网络防护、应急响应等信息安全保障能力,在确保自身信息安全的同时为客户提供最可靠的信息安全保障。
2.项目实施与应用情况详细介绍
(一)项目系统模型建立与运行情况
公司厂区布局根据国际先进的工艺流程,以中间产品为导向,按照“壳、舾、涂”一体化工艺流程理念设计而成,通过U字型布局,提高厂内物流效率,减少无效工时和资源的浪费。这样的布局满足精益建造理念。
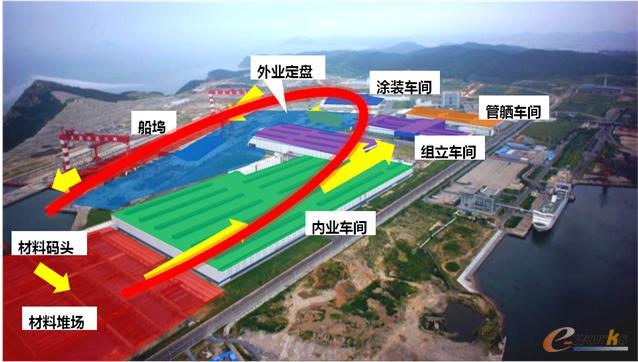
图4 厂区U字形布局
车间产线布局按照工艺的设定,产品按生产节拍有序流动,既不滞后也不过剩,保障作业负荷均衡化、物流高效化。板材和型材都是在内业车间按部件装配、平面和曲面分段分道加工的,然后再连续不断的提供给部件装配、平面分段流水线和曲面分段流水线,这样不但节约了堆放场地和理料时间,且有效缩短了物流距离,减少中间库的停滞。
公司建立的精益建造模式,从产品设计到生产环节充分贯彻精益管理、减少浪费的理念。二次开发的ERP系统与设计TRIBON系统高度集成,使设计研发、生产制造、采购、财务、管理等实现数据共享。
在结构设计阶段,分别输出各区划详细设计图和肋骨型线图,然后分别进行建模和光顺检查,在模型发行后进行分割,分割后经条材/型钢自动处理程序,形成条材/型钢加工数据,通过光纤分别传输至条材/型钢加工设备,自动加工。经分割后进行套料,生成CL数据,经数据转换后,NC数据传输至数控切割机进行数控加工,印字数据传输至全面数码印字机进行印字。
(二)先进设计技术应用和产品数据管理系统(PDM)建设情况
公司设计系统采用TRIBON系统及其升级产品AM12系统,并广泛运用于船、机、电等各专业。包括船体构造、管系、主要机器设备等在内的所有部件,均运用三维的TRIBON系统在计算机内设计完成。在船型开发的最初阶段,公司研发团队追求船型的最优推进性能,对船舶预估的性能指标反复优化,获取最佳航速、船体型线,据实船营运中的验证结果,均优于预报值,船舶的整体营运效能优良。
进入详细设计阶段,公司研发团队在研发过程中综合运用了流体力学、结构力学、轮机、电气及自动化等各个学科内容,应用CFD、NAPA、TRIBON、CAE、CAD等专业开发工具,进行有限元分析、疲劳强度计算、解析等,精细控制全船物量,针对船体结构有效计算与分析,控制空船重量,保证船体结构疲劳寿命和结构安全合理以及重要设备的装配精度。
最后到生产设计阶段,公司研发团队根据工艺技术标准,提供最适合于工艺需求、最佳施工性的生产信息,强化精细设计,全面展开生产信息过程中,细化每个操作步骤和方法,将设计信息转化为工艺信息,最终形成生产数据传递到车间设备终端。产品数据管理架构图如图5所示:
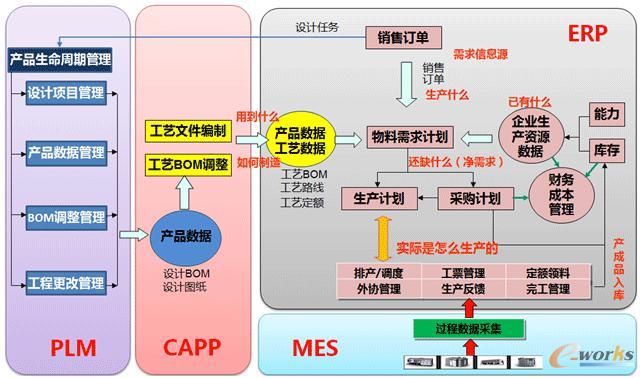
图5 产品数据管理架构图
(三)关键技术装备应用情况
近年来,公司大力推进以数控技术、通讯技术、控制技术和网络技术等先进技术为基础的智能制造装备应用,先后实施了全面数码打印机、先行分段智能焊接机器人、管材智能焊接机器人、FCB/RF焊接设备、型钢自动切割生产线、钢板数控切割生产线等先进智能制造装备。
1)全面数码打印机
公司设计并定制了全国唯一的全面数码打印机。该设备是世界首台实现钢板全幅面数码印字工艺的智能设备,它为预处理后的钢板打印上所有的加工信息,这些信息覆盖了钢板的整个加工周期,为后道工序智能识别提供了必要基础条件。
2)先行分段智能焊接机器人
本加工线布置于内业车间2F中央通道南侧,用于小分段工件的制作,包括装配、焊接、修补、背烧等作业内容,使用了智能传感技术、机器人技术。流水线整体操作简单、自动化程度高、安全性能高、节能环保。整条流水线只需配员一名。
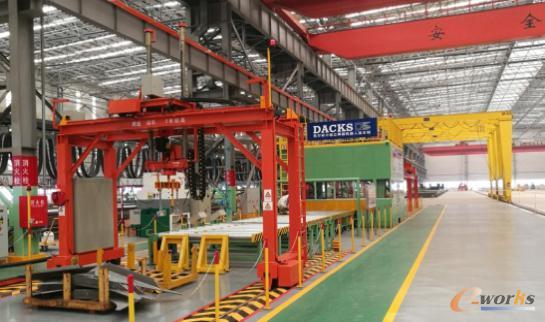
图6 先行小组焊接机器人生产线
3)FCB/RF焊接设备
FCB/RF焊接设备应用于平面生产流水线作业,一组两台,可实现对拼接在一起的主板高速焊接,最大可焊接40mm厚板且做到单面焊双面成形。FCB法应用于相同板厚的焊接,RF法应用于不同板厚的焊接,此法为国内首例,FCB/RF焊接设备是按照公司定制设计和工艺要求配套生产的最先进的焊接设备,国内首台。
4)型钢自动切割生产线
公司依据生产工艺流程、精度管理方式、场地条件、设备设施等情况,规划、实施了型钢自动切割生产线。该生产线实现了从进料→切割→搬出全过程的智能制造。通过实施该生产线,实现了物料信息传输智能化以及物料切割智能化。
5)条材自动加工生产线
条材是分段制造的主要部材之一,它的特点是数量多,大部分部材比较短小。公司依据精益建造模式,规划和实施了条材自动加工生产线,大大提高了效率,降低了劳动强度。其控制系统与上游设计系统无缝连接,包括印字、划线、切割数据全部来源于设计系统。
6)管材智能焊接机器人
该设备适用于中径管的定长切割下料及与船用搭焊法兰的半自动装配、自动焊接、管子在各工位间自动传输,形成焊接流水线,并且各工位在特殊情况下可以单机手动操作。设备加工口径范围为65A-200A。共有2台焊接机器人,可以同时进行作业。配员2人,8H作业可完成约64根直管加工(包括切断、定位、焊接)。通过机器人技术的应用,优化了作业流程,原先由人工录入信息、手工调节割炬角度、手写管信息变更为设备自动读取加工信息、调校参数、自动喷码,极大的提高了作业效率和精度。
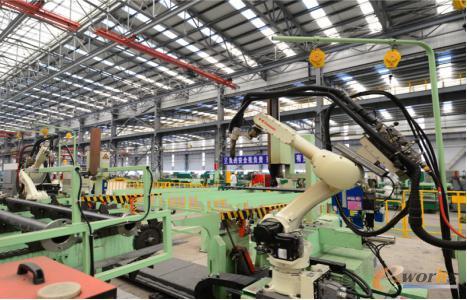
图7 管材智能焊接机器人
(四)生产过程数据采集与分析系统建设情况
1)车间加工可视化
公司对车间内9台等离子切割机、2台型钢切割机、1台全面数码打印机实施硬件升级改造,增加传感器并设置OPC数据采集服务器和数据库服务器,另外架设Web发布服务器用于可视化页面设计。
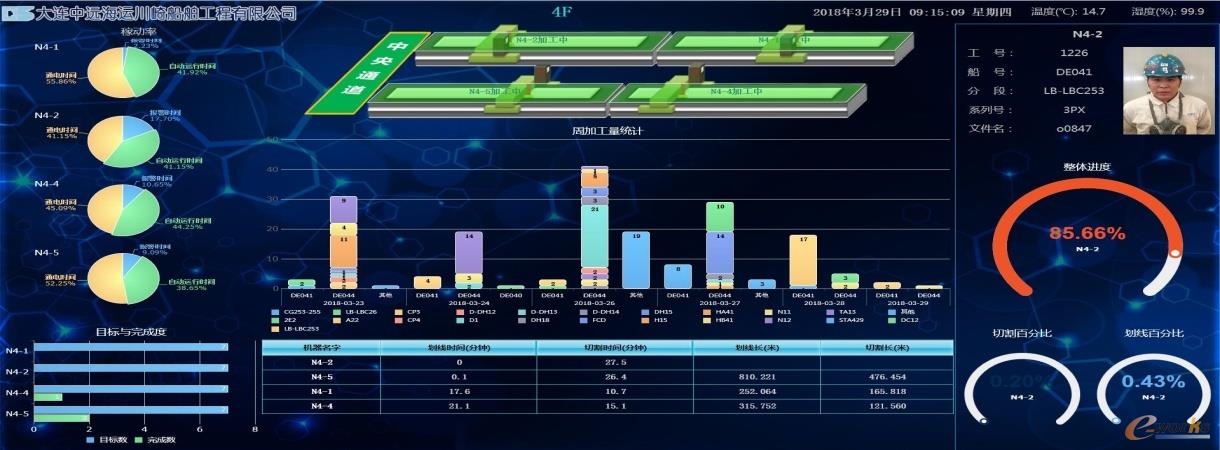
图8 车间可视化系统页面
通过在车间内布置大屏幕,使管理人员可以随时掌握现场实时生产信息。显示器上可查询的信息包括:设备有效运行比率、当日计划与完成情况、产线设备运转情况、周加工量统计、当日设备加工量统计、单台设备实施加工状况展示、作业人员信息。
2)吊机远程监控系统
门式起重机是船舶建造的重要配套设备,服务于船坞内船舶分段的搭载,也用于在平台内进行船体分段的预合拢建造工作。为保障起重机作业安全,设置了运行监控系统。系统架构分四层,分别为:起重机端数据源层、无线数据传输层、数据解析存储层及数据UI呈现层。运行监控系统(CMS)主要功能有监控,故障分析,状态显示等,包括:起重机状态(开关机、大车偏斜、故障信息文本、电缆卷筒状态)、作业时起重重量(1-4#钩+副钩)、起升高度(1-4#钩+副钩)、运行速度(1-4#钩、上/下小车、大车刚腿速度、大车柔腿速度)。系统具备报警及超载、超速保护功能,有效提高作业数据可追溯性和起重机的安全性。
(五)制造执行系统(MES)与企业资源计划系统(ERP)建设情况
1)制造执行系统(MES)建设情况
随着船舶智能化制造的推广实施和成组技术的应用,内业、组立、外业、涂装等船舶制造中间产品的生产过程的控制对缩短船舶建造周期,提高造船效率的作用日益明显,数字化车间正在取代船坞成为船舶制造中新的物料和信息资源的集散地。因此,运用信息系统对造船企业车间层的管理将日益重要。制造执行系统(MES)是对制造企业执行层进行全方位管理的信息系统,在企业集成信息管理系统中,起着承上启下的桥梁作用。它可以帮助船舶企业解决企业资源计划与生产现场信息联系不紧密的问题,如生产过程计划的执行与生产现场的控制缺乏优化的调度与协调、企业生产能力难以得到合理评估、生产成本难以有效控制等问题,使企业信息管理系统能够及时、快速、有效地运行,从而提高企业整体管理水平,适应敏捷制造和精益生产的要求。
建立拉动式的生产计划管理体系
公司建造实行的是拉动式计划管理体系。根据现有订单、劳动力、场地、设备、资金等资源,结合接单计划、人员招聘计划、设备改造计划等,以保障准时交船、均衡生产为原则,制定年度线表计划。
船舶建造工程计划的基础是根据线表制定的起工、进水、交付三大节点,在起工与进水区间,外业编制预合拢搭载计划表和定盘计划表;定盘计划确定后,组立科在得到大组立搬出时间节点,开始编制大组立计划;预合拢搭载计划、定盘计划、大组立计划确定了船舶建造过程中各个大节点,作为实际生产排产的依据。
针对多船建造中预合拢搭载和大组预定制作太过繁琐的现状,公司根据现有厂区布局、设备状况和生产管理特点,融合ERP系统的功能和数据,导入了工程计划管理系统,为合理、高效地安排工程计划提供依据。该系统能够通过直观的画面,达到同时输出单船、多船预合拢搭载、大组预定表的功能,还能够结合每周、每月的生产安排,达到合理安排各船分段加工顺序的目的,大幅度地节省了手工制作预定表的工时。
建立多功能的生产过程采集与分析系统
公司在多个生产环节建立了数据采集和分析系统,能充分采集制造进度、现场操作、质量检验、安全状况等生产现场信息。各坞、各船项目、各分段、各工种等的制造进度、主要工程节点、生产质量、物料配送情况等生产现场信息都有专门的信息化工具采集、整理、分析。
在生产过程中如果发现质量问题,现场作业人员可通过自主开发的不合格品系统和设计联络单系统发起质量问题处理流程,这两个系统分别对应外购品质量问题和自主设计质量问题对应。通过系统可以汇总各生产环节相关质量问题信息,便于过程管理,明显缩短各类质量问题处理周期,为产品质量提供保障。
为了应对在船舶建造过程中,由于船东要求或者现场的问题反馈,设计人员需要变更施工图纸的需求,我司自主开发了改正图管理系统。设计人员通过该系统可实时将改正图纸下发到现场作业班组,作业者可现场打印图纸,快速实施改正,同时生产管理者可跟踪每一条设计改正的落实情况,及时跟踪反馈。该系统大大缩短了改正图纸下发的时间,实现了集中式管理。
2)企业资源管理系统(ERP)系统建设情况
公司ERP系统(D-MACS系统)有助于规范企业的管理运作,能够为合理调配和平衡企业的各方面资源(如人力、资金、信息、物料、设备、时间、方法等)提供良好的工具,从而极大地改善企业管理低效与混乱的状况。在设计部门和采购、财务部门应用的D-MACS系统主要包括:综合船体系统和综合舾装系统,支付系统、成本系统等,在制造部门应用的有管加工管理系统、工时统计系统、生产管理系统等。
D-MACS系统超越了传统MRP(制造资源计划)的概念,吸收了按时生产(JIT)、优化生产、全面质量管理(TQM)等先进的管理思想,极大地拓展了管理信息系统的范围。该系统的主要宗旨是将公司的各方面资源(人力、资金、信息、物料、设备、时间、方法等)充分调配和平衡,为公司加强财务管理、提高资金运营水平、减少库存、提高生产效率、降低成本等提供了强有力的工具,同时为高层管理人员经营决策提供科学的依据,有效地提高了盈利,最终全面加强了公司的信息化管理水平,提高了企业的市场竞争力。造船生产企业的管理信息是指整个生产经营过程中产、供、销、存、人、财、物的有关信息,D-MACS系统将管理信息分解为设计、采购、库存、生产、材料主文件以及成本等几大子模块。设计模块按实际的需要录入所需材料号、计划使用日期、计划使用数量等并提出采购申请计划;采购模块根据采购申请计划实施采购;仓库管理模块负责材料入出库管理、库存管理和切割材料的回收管理等;支付模块根据实际的入库材料数量并经过支付申请、支付审核、支付认可,最后实施支付;而作业票模块则合理制定各工段的生产计划;工时模块录入实际的工时数;成本归集模块核算经费、材料费、劳务费以及制造费。正是通过这些大量的原始数据的录入,形成以物料需求计划为核心,把管理的各个模块集成起来,形成了一个通过信息流反映物流状况,追踪和控制物流运行的管理模型系统。
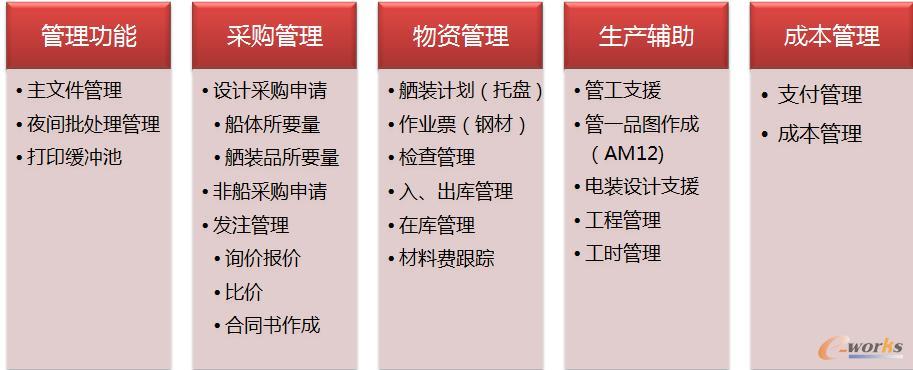
图9 D-MACS系统主要功能模块
(六)工厂内部网络架构建设及信息集成情况
公司工业互联网平台在物理上实现了上层信息系统与底层智能生产线设备之间的互联互通:通过全厂区覆盖公司局域网、车间生产线大范围进行智能化改造、核心信息化系统高度集成、建设先进的数据网络中心等,使得底层智能设备可以接收上层信息系统传输的操作指令和加工数据进行自动加工。同时,底层智能设备可向上层信息系统实时反馈生产状态信息。
在业务上,通过对各业务部门流程的梳理和优化,以数字化研发、设计、制造、测试与试验、管理为手段,打通船舶数字化研发、设计、制造、管理生产线主线。实现了横向连接公司设计、制造、设备、采购、人事、财务、安全、管理、质量、营业等各个部门,纵向连接从船舶产品营销、研发(基本设计、详细设计、生产设计)、生产制造的全过程。
(七)信息安全保障情况
公司于2014年1月取得ISO/IEC:27001资质认证,同年2月通过过日本川崎重工(KHI)信息安全专项审核,以“Excellent”的成绩通过,并且在某些方面要优于其日本同行业企业。
信息安全保障技术方面,为保障异地协同设计数据安全,我们采用双运营商双线路热备,专线间采用VPN加密隧道形式保障数据传输安全,对重要数据实施了异地容灾备份,并进行不定期演练;对于本地数据,采用内网管控软件与加密软件进行管控,可对用户实施分级授权、行为审计、访问控制等手段,有效的防范重要数据外泄或被篡改等信息安全事件;制度方面建立了应急响应、业务连续性管理、信息资产识别和风险控制、内部审计等方面的管理规定。
3.效益分析
当前中国造船工业具有劳动强度大、工作环境恶劣等普遍性特点。大连中远海运川崎的智能制造项目,是以数控技术、通讯技术、控制技术和网络技术等先进技术为基础,将与制造过程有关的设备(如全面数码打印机、工业机器人等)同上层控制计算机集成,形成一个系统,可实现制造设备的集中控制管理,实现制造设备之间、制造设备与上层计算机之间的信息交换,通过辅助设计系统进行数据处理,并传输至数控切割机和工业机器人,实现自动化作业。特别是全球首创的全面数码打印机为零件赋予了身份信息,未来为后续智能制造技术的应用提供了无限的可能。此项目可有效减少人工成本、减轻劳动强度、改善作业环境、提高生产效率、降低产品不良品率,从而持续提升企业竞争能力。通过该项目使公司已具备实施全面智能船厂的条件,经实践证明,项目是可行的,完全具备在造船行业推广示范的条件。
1)项目顺应造船市场发展要求,符合国家政策导向
当前,全球造船市场面临新一轮科技革命和产业变革,制造业“数字化、网络化、智能化”已成为变革的发展趋势。中国“十三五”期间,我国的船舶工业发展明确了围绕《中国制造2025》,建设海洋强国、造船强国的战略目标。而实现由造船大国向造船强国的转变,智能制造是必由之路。也是我国实现弯道超车的重要途径。为进一步提高市场竞争力,在快节奏生产中保障船舶建造的质量、缩短建造周期,在船厂实施智能制造已经势在必行。
2)公司具备良好的基础条件,使项目实施具备可操作性
通过不断的攻关,大连中远海运川崎已初步建立了以数字化、模型化、自动化、可视化、集成化为特征的智能化造船和生产管理体系,实现了研发、设计、生产、管理等环节全面融合、协同运行。通过项目初步的智能化改造,公司在钢材利用率、全员劳动生产率、造船生产率、单位土地产能均居行业前列,已经成为中国船舶工业的先进企业。
3)项目实施后可有效提升公司竞争力
项目的实施,将极大程度缩短设计、制造周期,使得产品质量和建造效率达到世界先进水平;同时有效促进了管理人员经营决策的科学化,为加强企业管理、提高资金运营水平、减少库存、提高效率和产品质量、降低成本等提供了强有力的保障。
本文为e-works原创投稿文章,未经e-works书面许可,任何人不得复制、转载、摘编等任何方式进行使用。如已是e-works授权合作伙伴,应在授权范围内使用。e-works内容合作伙伴申请热线:editor@e-works.net.cn tel:027-87592219/20/21。