本文为“2020年度中国智能制造最佳实践奖”参评案例。本次活动将评选出2020年度,为中国智能制造领域带来突出效益的最佳实践工程,全面介绍企业推进智能制造的步骤、重点与难点、获得效益等,分享建设过程中的经验,供广大制造业行业企业学习供鉴。
一、企业简介
大连亚明汽车部件股份有限公司(简称“大连亚明”),中国汽车压铸件行业20强企业,国家级工业互联网试点示范企业,国家级制造业与互联网融合发展试点示范企业,公司主营业务为汽车压铸件生产、模具制造、机械加工、等,公司为上汽大众、福特、通用、奔驰、丰田等国内外整车和动力总成工厂等客户生产各种型号的压铸件。公司坚持以市场为导向,保质量、促增长的核心理念,创世界一流压铸企业,做最受社会信赖公司。
大连亚明主要产品有汽车变速器壳体、离合器壳体、下缸体总成、变矩器壳体、CT端盖等。在复杂汽车零部件及模具制造方面已具有世界先进的设计及生产工艺装备。作为国家工业互联网试点示范企业和行业标杆智能工厂,已初步形成了数字化、可视化、网络化的生产管理模式。
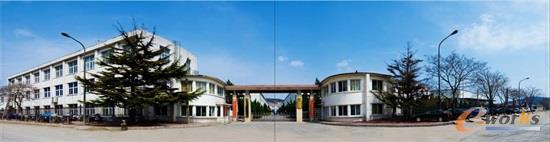
图1 大连亚明汽车部件股份有限公司
二、企业在智能制造方面的现状
大连亚明近年来通过企业车间智能化改造与信息化开发,已建设汽车压铸件及模具生产智能化柔性制造的智能工厂,并全面提升了企业的管理智能决策水平。
1)目前已实施的内容如下
(1)建立智能工厂的总体设计模型、工艺流程及布局模型,并完成数字孪生仿真;
(2)完成了包括高端压铸机、高端数控机床、机器人自动取件系统、机器人智能喷涂系统、自动切边系统、数据采集系统、模温智能传感与检测系统、AGV智能小车等智能制造核心装备的智能化集成应用;
(3)深度开发和优化车间制造执行系统(MES),实现产品全生命周期智能化闭环管控;
(4)通过设备智能化改造,建立生产过程数据采集和监控系统,实现生产过程数据实时上传。
(5)多场景5G应用,包括数据采集与上传、工业视觉检测、AGV智能物流等。
2)主要应用场景
(1)压铸/模具生产管理和追溯系统
在底层建立规范化、标准化的产品数据信息定义,在顶层建立基于功能化、模块化的数据信息的柔性化设计体系,同时提供基于规范化产品数据的标准流程管理。
产品基本数据规范化、标准化:基于企业ERP系统建设初期所进行的基础数据规范化的工作基础,统一产品设计数据的编码格式、二维及三维设计软件,建立标准设计模板,统一数据格式以及应用软件版本,实现数据在CAD、CAE、CAM等系统间的自由流通共享。统一数据存储规范,并通过制定特定数据签署归档流程以及实行档案管理人员提前归档审查等措施,对统计的数据进行完整性、正确性、编码唯一性检查,对电子文档进行安全集中存储,并做好资料版本控制,实现各部门间产品信息的同步更新。
产品数据管理流程化:产品数据的录入程序,开发多种文档类别支持功能,在各类资料中根据各职能部门的不同级别的人员,赋予不同的权限,保证数据信息的安全,允许对资料进行修改、删除、查询,支持精确检索和模糊检索。建立关联关系,使得文档能够与其他业务对象之间可进行交叉查询。建立标准化的设计变更程序,设计人员在PDM系统中填写设计变更单,之后进行逐级电子审签。确认通过电子审签后,各单位按照设计变更单进行方案设计、图纸或零部件的变更。
柔性化产品设计能力提升:产品图纸及文档资料进行分类管理,对标准件、自制件和材料库的种类进行压缩,提高零部件重用性、降低设计变更次数,通过关联影响分析,提高零件变更的程序化和制度化,推进研发过程向产品系列化、零件通用化和功能模块化转变,提高图纸的借用、引用和参考设计,从源头降低生产成本。通过PDM系统创建产品结构,提供简单和易用的图形化方式来定义、浏览、修改产品结构树,快速生成新的产品结构,并自动生成产品明细表,实现产品的快速换型设计和柔性化设计。
PDM与ERP、CAPP系统集成建设:针对不同系统间信息孤岛的问题,研究基于数据模型的集成方法,集成数据模型是PDM与ERP系统中数据结构的逻辑描述。运用PDM的工作流程管理CAD/PDM/CAPP/ERP数据集成办法,把PDM与CAPP、ERP应用软件集成过程分为三个层次。
(2)设备数据采集与控制应用
通过数字化车间设备联网,接入信息化网络系统,实时获知设备状态,并采集生产产量与工艺参数等数据。通过对采集数据的分析,实现设备的预防性维护、保证了设备的有效运行、同时实现了产品加工过程工艺参数的有效追踪。
通过物联网与智能感知技术实现车间生产信息采集和集成。压铸机、数控加工中心、机器人的状态数据实时采集并传送给总线网络,然后通过服务器对数据进行判断、处理传给工业总线和数据中心。
数据采集主要通过工业互联网采集数字化智能装备的实时运行数据。
通过移动设备人工设备采集生产报工等信息,构建网络化、数字化车间生产现场的信息数据交换平台。
运用信息感知、网络互连等信息技术,建立全生产过程智能平台。通过在大连亚明建设信息物理融合网络并基于相应的安全协议和领域应用标准,将生产过程相关的设备、资源、物料、客户、生产者等实现实时连接、精确识别和有效交互。
(3)基于5G技术的多场景应用
基于5G的压铸件缺陷检测技术应用:借助5G技术低延时、高带宽的优势,将工业视觉所产生的大容量现场数据(如实时图像)快速传输至数据处理平台。,进一步提高多个作业场景的自动化、智能化程度,将工业视觉分别应用至压铸件内外部缺陷检测场景、螺栓拧紧场景、螺纹漏加工检测场景、码垛机器人与AGV应用场景,涉及到的工业视觉传感器包括:工业相机、激光传感器、红外传感器等。将一系列涉及检测工序的结果数据反馈至产品质量追溯系统,服务于产品质量提升与制造工艺改进。
基于5G的铸件制造数字孪生技术研发:制造阶段的数字孪生将极大的提高车间管理人员对车间实时动态的了解与控制,同时能够对未来可能发生的运行问题,进行提前的预判。制造阶段的数字孪生涉及到与大量异构设备实时通讯的问题,既有通讯需求,又强调实时性,因此,本项目车间物联网采用5G技术、华为云平台进行建设。为了进一步发挥5G通讯优势,采用安全可控的企业云平台作为海量数据储存端。最后通过对关键制造设备建模与数据关联,实现数字孪生的建立。
3)取得的效益
通过车间智能化建设,生产效率提高42%,不良品率降低33%,营运成本可降低22%,产品研制周期缩短33%,单位产值能耗降低15%。项目实施后,将充分利用能源,提高资源的利用率,对促进地方循环经济可持续发展、提高产业竞争力、保护生态环境、降低能源消耗和构建资源节约型社会都具有十分重要的意义。大连亚明成为国家级工业互联网试点示范企业,国家级制造业与互联网融合发展试点示范企业,对行业企业数字化转型起到良好的借鉴作用。
三、参评智能制造项目详细情况介绍
1.项目背景介绍
1)项目重要性
汽车产业是推动新一轮科技革命和产业变革的重要力量,是建设制造强国的重要支撑,是国民经济的重要支柱。在汽车产业高速发展的同时,巨大的汽车保有量带来的能源、环保、交通等问题也日益凸显。节能和轻量化已成为汽车工业的重要发展方向。本项目的研究产品为新能源汽车零部件方向,属于国家重点支持的领域。
2)项目迫切性
当前,汽车发达国家纷纷提出产业升级战略,加快推进产业创新和融合发展。发展中国家也在加紧布局,利用成本、市场等优势,积极承接国际产业和资本转移。中国深化改革全面推进,汽车产业国际化发展进程提速。产业边界日趋模糊,互联网等新兴科技企业大举进入汽车行业。传统企业和新兴企业竞合交融发展,价值链、供应链、创新链发生深刻变化,全球汽车产业生态正在重塑。面对全球汽车制造业的变革与机遇,中国汽车零部件制造企业想要占领市场就必须加快由传统制造模式向智能制造模式的转变。
随着国内汽车工业的发展,我国汽车零部件压铸行业技术水平也得到很大提升,但与国际先进企业相比,仍然存在诸如熔炼、压铸过程能耗高、产品报废率居高不下,产品表面质量不高,工艺集中度和智能化程度低,制造消耗品资源循环利用率低、生产效率低等,“低质、低价”的现象仍然严重,高端市场被发达国家垄断,如美国、欧盟和日本占据了全球市场的85%左右,国内70%的市场份额被进口产品占据。为了更好适应市场竞争力的需要,对成本、效率以及安全的要求也要不断提高,因此,企业就必需向智能化、节能型企业发展,以转变企业经济增长方式来增厚企业利润空间,为自身持续的经济增长开辟全新的空间。
为了更好适应市场竞争力的需要,对成本、效率以及安全的要求也要不断提高,因此,企业就必需向智能化、节能型企业发展,以转变企业经济增长方式来增厚企业利润空间,为自身持续的经济增长开辟全新的空间。
3)项目实施前的企业痛点问题
机器设备使用传统的控制系统;设备维护检测需人工识别、检测;产品输出录入手动操作、纸质记录;数据生产状态呈手工/静态数据;车间物流配送为传统叉车配送,工厂内产品流转过程耗费大量人力;工厂内设备、车间与企业管理者之间呈现孤立状态;上下游供应商、销售商之间无信息互通共享。
4)生产过程中的主要问题
统计员:企业上云前需要统计员通过EXCEL表格填报统计信息,打印纸质文档,请示领导审批,下发纸质文件,传递生产订单,制定物料需求计划,制定排产计划。容易出现生产需求分析不准备,工单传递不及时的问题。
操作工:需要逐层去传递生产消息,手工记录生产看板,手工录入数据,纸质档传递数据。会造成数据传递不全面、不及时、存在误差、造成时间和生产效率延误的问题。
设备维修工:当设备出现问题时,需要操作人员去通知班长组,逐层去通知设备维修工维修,并补交经领导审批的维修单;设备维修人员需要到设备、产线周边去不定期巡视设备运转参数和状态。会造成人员、时间和生产效率的延误;同时会伴随相应的安全隐患。
车间主任:对于生产过程产量、效率、能耗、人工工时等数据的分析模式比较少,分析内容不明显。数据的采集只能通过手工录入、纸质记录或现场查看等形式,容易出现误差并在安全隐患。
5)项目主要目标
本项目通过提升汽车关键压铸件的智能制造水平为出发点,通过对压铸件及其模具制造过程中的数据采集、在线检测、智能物流、可视化生产管控等关键技术的应用,基于混合云模式,开发有自主知识产权的数字化工厂管理平台,实现产品全生命周期管理系统PLM、ERP、MES等系统的高效协同与集成。满足产品设计、仿真验证、工艺、制造、检测、物流等全生命周期各环节的智能化需求,研发精准、敏捷的数字化生产管理系统,建设压铸件及模具智能制造数字化车间。为我国汽车压铸件核心制造装备和核心功能部件制造水平的发展提供新的动力,也为我国压铸行业的数字化转型提供可复制可推广的范本。
6)项目技术路线
本项目围绕感知、控制、决策、执行四大关键环节,自上而下将数字化工厂建设分为5个层级。
(1)核心智能制造设备层。通过整合车间ERP、产品生命周期管理系统PLM、MES等核心应用系统,构建智能化核心决策平台;
(2)数字化车间层。产品设计以计算机辅助设计系统,产品制造以MES系统为决策核心,生产资料数据建立数据库;
(3)实时数据感知层。以工业互联网的基础,充分应用智能传感器构建检测、过程控制、识别等系统;
(4)核心支撑软件与先进制程控制层。以单机控制设备串联向离散式控制系统升级;
(5)数据驱动决策层。工业机器人、专机、物流设备等是终端执行装置,承接上层的决策命令。
2.项目实施与应用情况详细介绍
1)项目目标任务
本项目基于汽车关键压铸件的快速响应需求,以构建模具设计、制造到压铸件生产全流程的数字化工厂为目标,项目主要内容包括:
(1)组建智能化设计平台。包括构建三维数字化研发设计与仿真系统、CAE模拟仿真系统、CAM仿真加工系统。
(2)核心智能制造设备系统集成。包括:压铸车间、模具车间、机加车间,核心智能装备包括大型压铸单元、数控加工中心、智能装配检测设备、智能物流输送装备的关键技术攻关和系统集成。
(3)建立智能化制造系统。包括:建立覆盖制造过程的可视化生产管控中心、建议包含工艺数据、设备数据、产品数据等实时数据采集与传感系统。
(4)建立基于数据驱动的智能管理与决策平台。通过整合车间ERP、MES、PLM等核心应用系统,搭建智能设计、智能制造、数据采集及管理决策平台,建立涵盖智能化设计、智能化装备、智能化制造、智能化经营的智能制造系统框架。实现生产车间的实时感知、优化决策、动态执行。
2)项目实施内容
2.1 智能化设备平台建立
(1)智能化设计平台集成了压铸件及模具的设计(CAD)、压铸过程仿真(CAE)、压铸件及模具制造(CAM)系统,该平台以计算机辅助设计和仿真分析软件如UG、ANYCASTIN为工具,实现压铸件的结构设计、工艺性分析、浇注系统设计、模流分析、模具设计与制造、压铸件的深加工等全过程的数据传递与闭环反馈,实现从设计到最终产品全生产过程的质量控制和效率提高。
(2)建立产品数据管理系统(PLM),通过关键制造工艺的数值模拟以及加工、装配的可视化仿真,建设数字化研发工艺设计系统,全面提升研发设计水平和效率,缩短产前准备周期,加快产品上市时间,促进企业提升效益和核心竞争力。
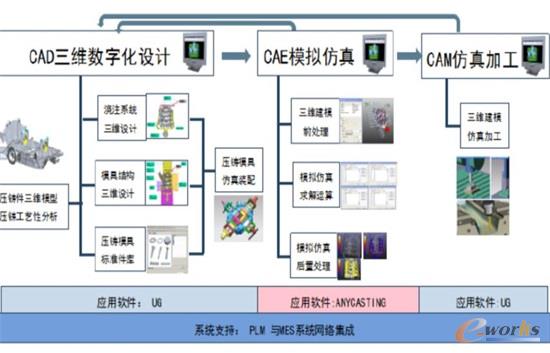
图2 数字化车间设计平台
2.2 核心智能制造装备集成
(1)压铸车间、模具车间、机加车间,核心智能装备包括大型压铸单元、数控加工中心、智能装配检测设备、智能物流输送装备的关键技术攻关和系统集成。
(2)通过提供智能控制、可视化工具,实现全过程的高效人机交互及整体协同优化运行。运用信息化手段管理和优化全局生产流程,实现从产品定单开始、直到产品交付的整个生产管理流程自动化。
(3)建立涵盖生产全过程的车间数据模型,进而通过运用二维码/条码等移动数据采集技术,实现物料流通全过程的自动采集和主动采集,有效避免手工录入的缺点,实现铝合金压铸产品及压铸模具上下游全流程的可追溯。
(4)建立数字化工厂软件体系。以提高生产效率,减低生产成本、缩短交货期,改善客户服务为目标,建立涵盖产品的研发设计、生产制造、企业管理、物流/供应链、客户关系管理等制造企业的各个业务领域的数字化工厂软件体系。
2.3 搭建基于物联网的实时数据采集与传感系统
(1)通过物联网与智能感知技术实现车间生产信息采集和集成。压铸机、数控加工中心、机器人的状态数据实时采集并传送给总线网络,然后通过服务器对数据进行判断、处理传给工业总线和数据中心。
(2)数据采集方式主要通过工业互联网采集数字化智能装备的实时运行数据。
(3)通过视频监控等获取生产现场环境数据。
(4)通过移动设备人工设备采集生产报工等信息方式完成,构建网络化、数字化车间生产现场的信息数据交换平台。
(5)运用信息感知、网络互连等信息技术,建立全生产过程智能平台。通过在大连亚明建设信息物理融合网络并基于相应的安全协议和领域应用标准,将生产过程相关的设备、资源、物料、客户、生产者等实现实时连接、精确识别和有效交互。
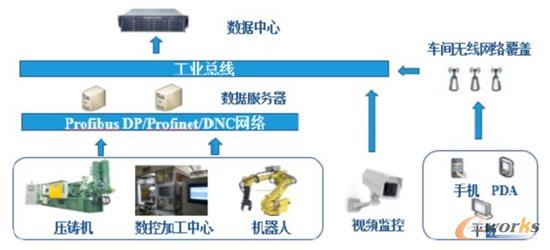
图3 车间数据采集系统示意图
2.4 建立覆盖制造过程的可视化生产管控中心
(1)采用电子看板实现制造过程可视化
生产数据通过工业以太网实时传输到工厂的数据库,通过大数据挖掘技术,实时分析各生产车间的生产进度、效率、品质等信息;通过监控生产车间的设备运行状态,及时发布设备故障监控信息,合理进行调度;通过生产库存分析,进行物料的预警监控。所有的数据经过汇总,通过中央看板集中显示,管理者可根据生产信息进行快速决策与管理。
(2)建立生产车间的Andon预警系统
根据实时数据采集系统采集的数据,建立生产车间Andon系统,用来指示机器运行状态,监控包括机器停机,质量问题,工装故障,操作员延误,材料短缺等在内的各类异常情况,提示生产异常状况处置措施。
(3)采用先进的实时信息推送系统实现车间云端管控
开发邮件、短信、微信等多种信息推送方式,及时反馈异常情况和生产过程的状态信息,根据分析评估的结果发出异常处置指令或关闭异常,对生产过程进行移动化的管理与控制,实现云端管控,使管理向移动化转变。
2.5 建立基于数据驱动的智能管理与决策平台
智能管理与决策平台是一个综合性的管理与决策平台,集成了包括PLM、ERP、MES、WMS等信息系统。
(1)建立智能管理与决策平台平台,涵盖了从产品订单开始到制造、销售、服务的产品全生命周期管理模式,通过邮件、短信、手机、电脑和电子看板等手段随时随地了解生产的实时进程。管理人员可以进行阶段性的财务与人力资源调整、生产过程的及时应变与调整,实现对生产过程的智能管控。
(2)智能管理决策模块架构如图6。系统根据客户下单需求,运用PLM系统进行产品研发,通过ERP进行资源规划,实现企业生产资源优化配置。
(3)闭环管理的车间制造执行系统(MES)建设。
a.对生产主线、物流主线、交付主线等制造过程的关键环节进行分析和梳理;
b.基于MES生产信息的闭环管理,明确各系统间的信息共享的类型,构建各系统间的信息接口,实现各环节的信息无缝连接和无障碍流通,形成制造全过程的闭环管理;
c.MES执行与生产计划拉动,通过信息系统打通工序间的计划流;
d.MES车间互联架构,通过数据采集装备(RFID、Andon/视频监控、传感器)和数据采集与监视控制系统(SCADA)采集产品在生产过程中位置、生产状态、工艺参数等实时信息,实现智能控制。
(4)在生产过程中,运用信息感知、网络互连及人工智能等技术,建立全过程生产可视化平台。建立涵盖生产全过程的车间数据模型。通过二维码/条码、无线PDA等移动数据采集技术,实现物料流通全过程的自动采集和主动采集,有效避免手工录入的缺点,实现锻造产品上下游全流程的可追溯。
(5)通过相关智能控制、智能决策及可视化工具,实现全过程的高效人机交互及整体协同优化运行。
(6)运用信息化手段管理和优化全局生产流程,实现从产品定单开始、直到产品交付的整个生产管理流程自动化。
(7)通过人工智能算法的实施,对复杂问题作出正确的决策,实现生产节拍与能源消耗的多目标优化。

图4 智能管理决策模块示意图
2.6 数字化车间系统建设
(1)压铸车间、加工车间和装配车间的数字化全覆盖建设
轻量化汽车压铸件生产由压铸车间、加工车间和装配车间组成。零件毛坯压铸成型后,通过物流系统转到下序车间,进行下道工序生产,最终通过物流系统完成入库、发运流程。
产线设备状态、工艺参数、生产信息经数据采集系统实时上传给MES和现场看板,实现整条线的互联互通及实时控制。在各生产车间主要通过生产信息采集系统完成生产全过程的数字化和可视化管理,通过对大量生产数据的快速分析和实现智能决策和动态执行。
(2)实现模具生产数字化车间建设
实现大型精密模具高效柔性生产的智能制造,是针对复杂模具开展智能制造技术研究,已经初步实现模具设计,生产,检测,管理全过程的数字化和智能化,实现生产过程的优化控制。
(3)PDM、ERP、MES、WMS等系统集成
对包括ERP、MES、PLM、APS、WMS、PDM等信息系统进行集成。MES与上层ERP、PDM等业务系统进行集成,MES和底层生产设备控制系统一起构成企业的神经系统贯穿工厂生产的市场、研发、计划、采购、制造、销售、服务和财务等流程;ERP根据管理的需要,从PDM系统中获得产品数据中的零件基本记录和物料清单(BOM);在ERP系统应用基础上,通过集成制造执行系统MES解决生产现场科研试制问题,ERP系统中物料管理、订单管理、生产管理、库存管理、销售管理、财务管理、产品数据、人力资源8个主要功能模块和PDM/MES之间紧密集成协同工作。
3.效益分析
通过本项目的实施,生产效率提高42%,不良品率降低33%,营运成本可降低22%,产品研制周期缩短33%,单位产值能耗降低15%。项目实施后,企业核心竞争力进一步提升,大连亚明成为国家级工业互联网试点示范企业,国家级制造业与互联网融合发展试点示范企业,对行业企业数字化转型起到良好的借鉴作用。
1)本项目实现的技术指标
(1)完成数字化车间设计、数字化工艺流程规划及产线布局,数字化建模比例达到80%以上;
(2)建立数字化设计与仿真软件研发设计体系,应用UG/CAXA/ANYCASTING/AUTOCAD/PLM等数字化设计与防真软件及管理软件;
(3)应用PLC/SCADA/嵌入式组态软件等组建智能化自动化装备,机床与工业机器人包括智能压铸机、数控加工中心、六轴工业机器人、智能传感与控制装备包括SCADA数据采集系统、定量炉、集中熔化炉,智能检测与装配装备包括模温检测与控制系统、智能测漏系统;
(4)实现制造过程现场数据采集以及物流配送应用AGV技术,产线可视化数据面板覆盖率达到80%;
(5)建成面向柔性化生产的MES系统,制造过程数据透明化,实现基于制造数据的智能化调度;
(6)建成MES、ERP、WMS、PLM等管理系统,基于各系统的生产过程数据的分析与优化,形成智能化管理与决策平台。
2)本项目实现的核心智能制造装备指标
(1)高端压铸装备:大型压铸机、智能切边设备、模温测控系统。
(2)智能传感与控制装备:PLC数据采集系统,条码采集系统,伺服系统,液压与气动系统,机器视觉传感器,位移传感器、分散式控制系统。
(3)智能检测与装配装备:在线无损检测系统设备,工件防错检测、基于大数据的在线故障诊断与分析设备、柔性可重构工装的对接与装配装备。
(4)智能物流与仓储装备:AGV、车间物流智能化成套装备。
3)项目实现的经济效益和社会效益
高品质的产品推广应用带动整车企业的跨越式发展,通过与整车企业开展广泛的合作,进一步促进了国内汽车工业特别是新能源汽车工业的发展。在我国大力发展智能制造的大背景下,带动整个国内汽车行业的智能制造水平的发展,使其焕发出新的活力。大连亚明项目实施后,充分利用能源,提高资源的利用率,对促进地方循环经济可持续发展、提高产业竞争力、保护生态环境、降低能源消耗和构建资源节约型社会都具有十分重要的意义,同时对带动地方经济发展,实现区域资源优化配置都具有十分重要的意义。
现在东北工业在经历低迷,从90年代开始,在市场经济竞争中,计划体制下的矛盾显现,东北老工业基地陷入困境,在管理机制、产品结构等方面逐渐脱离市场方向,企业竞争力较弱。作为老工业基地,东北正在实现“工业摇篮”的第二次腾飞,智能制造是东北传统产业转型升级的必由之路。大连亚明作为汽车关键压铸件制造行业的领先企业,率先全面实施智能制造新模式应用,将设计、生产、物流环节依靠数字化、信息化全部打通,实现个性化和快速反应式的生产,大大提高企业的核心竞争能力和市场应变能力,也为东北制造业的振兴提供示范引领作用。
4)对国产智能制造核心技术装备及系统解决方案带动作用
大连亚明目前已经组建专业软件开发团队,致力于开发行业数字化智能工厂解决方案软件,把大连亚明的智能制造经验及成果,转化为行业解决方案和产品,为国内外压铸及模具企业提供可落地的智能化改造服务,带动同行业的智能制造数字化转型的普及和发展。
5)智能制造经验和模式应用推广情况
本项目针对汽车关键复杂零部件铸造加工行业生产流程长、加工工序多、物料转运复杂、工艺过程复杂的特点,搭建了覆盖铸造、机加工的数字化车间平台,在设备互联互通的基础上,实现全过程的质量数据、生产数据、物料数据、人员操作数据、设备数据的采集,建立生产全过程质量追踪,以压铸机为核心,前端工艺拉动生产,后端工艺推动生产,减少中间在制品积压,提高生产效率。同时,结合行业的特点:质量管理严格、设备资产重、能源消耗高、产品库存量大,突出信息化系统在质量追溯、设备管理、能源管理的功能,以达到控制质量、降低成本、提高效率的目的。目前,已有多家行业企业引入了大连亚明的智能制造产品和模式,大连亚明已经组建自己的智能制造开发团队,为行业用户提供数字化工厂建设解决方案和服务。
6)对提升行业国际竞争力的作用
本项目立足国产核心智能制造装备进行数字化车间建设,将摆脱过去核心制造装备依赖进口的困局,对于打破国外技术和市场垄断具有重要作用,带动更多的压铸企业以及其他行业的企业应用国产核心装备,提高智能装备供应商的营收能力。
本项目的实施及应用,将有助于各类国产装备提升数字化,信息化,智能化水平,特别是在效率、节能、安全及可靠性方面将有质的提升,通过应用示范和不断完善推动多品种的国产智能装备提升其核心竞争力。
大连亚明的主要客户为奔驰、丰田、大众等知名国际汽车巨头企业,本项目实施后,引入了先进的管理理念,成为了行业标杆智能工厂,并显著增强大连亚明的企业国际竞争能力,为大连亚明应得大批订单,加快了汽车零部件国产化进程,本项目也将使汽车零部件制造行业更快融入国际产业链体系,获得良好市场效益,从而为国内汽车零部件行业带来示范和带动作用。
本文为e-works原创投稿文章,未经e-works书面许可,任何人不得复制、转载、摘编等任何方式进行使用。如已是e-works授权合作伙伴,应在授权范围内使用。e-works内容合作伙伴申请热线:editor@e-works.net.cn tel:027-87592219/20/21。