“上医治未病,中医治欲病,下医治已病。”这是《黄帝内经》针对健康诊断给出的三重境界。
对于工业企业的关键设备而言,无论是带“病”运行还是处于“亚健康”,都会给企业带来损失,可能是意外停机导致的更高成本支出,也可能是巨额的生产损失以及安全隐患和事故等。据ISA数据显示,全球制造商每年因停机遭受的损失总计约为6,470亿美元。因此,关键工业设备的健康诊断十分重要,那么如何才能做到“上医治未病”呢?答案无疑是“预测性维护”。
PHM作为实现预测性维护与智能运维的关键技术,可以帮助企业在事故发生之前较长时间里实现故障预测与健康管理,达到“治未病”的效果,其应用日益受到业界的广泛关注。本文将对PHM的发展与内涵、PHM的体系架构与功能模块、在工业领域的应用等进行解读。
PHM技术的缘起
PHM(Prognostics and Health Management)即故障预测与健康管理,起源于上世纪欧美发达国家,最早应用于航空航天领域。回顾PHM的发展,需求牵引、技术进步是贯穿其不断发展的主线。
●故障诊断拉开序幕
20世纪60年代,在“阿波罗登月计划”执行中,出现了一系列设备故障酿成的悲剧,直接引发了1967年,美国在宇航局(NASA)倡导和海军研究室(ONR)主持下,开创性地启动了机械故障预防的研究工作,标志着现代装备故障诊断正式拉开序幕。
早期,飞机航电系统为分立式结构,由彼此独立的子系统组成,故障诊断主要依靠外部测试方法,即人工在地面上利用专用或通用测试设备和被测对象连接,以获取其状态信息后进行故障检测和隔离。随着飞机系统变得复杂,一些重要的系统和设备,需要操作人员实时了解其运行状态,及时处理故障,因此机内测试(Built-in Test,简称BIT)被引入飞机中。BIT是测试技术的一个分支,是在系统和设备内部提供的检测、隔离故障的自动测试能力。随着技术的进步,还先后出现了融入人工智能的智能BIT、综合BIT、自适应BIT等。
●综合诊断的提出与发展
20世纪80年代后期至90年代,复杂装备的故障诊断仍出现测试性差、诊断时间长、BIT虚警率低、保障费用高等问题,究其原因,主要是由于自动测试设备、维修辅助手段、BIT、技术信息、人员和培训等各诊断要素独立工作造成的。因此,“综合诊断”的概念被提出。综合诊断强调通过考虑和综合构成诊断的所有要素,使武器装备诊断能力达到最佳的结构化设计和管理过程,一经提出,便获得了美英等国的认可,并相继开始研究综合诊断方案。
●PHM应运而生
20世纪90年代末,信息技术的蓬勃发展和广泛应用,推动了综合诊断系统向测试、监控、诊断、预测和维修管理一体化方向发展,同时其应用也不再局限于飞机的电子系统,而是扩展到电子、机械、结构、动力等各个主要分系统,形成综合的诊断、预测与健康管理系统的时机已经成熟。另外,随着武器装备集成度、复杂度及信息化程度的不断提高,事后维修和定期维修这类维修方式已经无法满足现代战争对装备保障的要求,在这种情况下,应用于民用领域的CBM(Condition Based Maintenance,基于状态的维修)理论被军方引入,旨在通过对武器装备状态的实时监测,及时发现早期故障并进行维修,以提高战备完好性和任务可靠性。此外,大容量存储、高速传输和处理、信息融合、MEMS、网络等技术的迅速发展,也为PHM的诞生提供了技术基础。基于此,在美军研发F-35的JSF项目中,以预测技术为核心的PHM概念被首次提出,而F-35战机也成为了第一个真正实现PHM(故障预测)的应用。
总的来看,PHM是在传统的状态监测和故障诊断技术基础上发展起来的一项新的维修保障技术,是设备维修模式从事后处置、被动反应,到定期检查、主动预防,再到事先预测与综合规划管理不断深入的结果。
何为PHM?
历经几十年的理论研究与应用发展,PHM已成为工业企业实现远程运维、保障重大装备可靠性重要核心技术,实践智能工厂建设的重要手段,正在引领全球范围内新一轮制造业维修保障体制的变革。那么究竟什么是PHM?
PHM是一种新兴、多学科交叉的综合性技术。它利用传感器实时监测产品或系统运行的各类状态参数及特征信息,借助各种智能算法和推理模型来评估产品或系统的健康状态,在其故障发生前进行预测,并结合各种可利用的资源信息为后勤保障人员提供一系列维护决策支持。
PHM聚焦于复杂和重大工业系统,预测与健康管理是其核心与关键,也是其与CBM的最大区别。预测即根据历史和当前的监测数据,预先诊断部件或系统完成其功能的状态,包括确定部件或系统的剩余使用寿命(RUL)或正常工作的时间长度;健康管理即根据诊断、评估、预测的结果等信息,结合可用的维修资源(如备品备件等)和设备使用要求等知识,对任务、维修与保障等活动做出适当规划、决策、计划与协调。
PHM的工作原理是:基于大部分复杂装备或者其相关部件会表现出退化特性,即随着使用时间的增加,会出现健康衰减、性能下降,而在早期出现故障到真正发生故障之间都会有一定的时间区间,这个时间区间即是剩余使用寿命(如下图),通过RUL的预测,企业能在设备发生故障前根据预计时间段,确定最佳的维修时机和方案;另一方面,故障真正发生之前也会有一定的征兆,并且故障征兆、故障原因、故障部位之间存在着某种线性或非线性的映射关系,找到这种映射关系,就能在故障发生前,对发生故障的原因和部位进行预测。
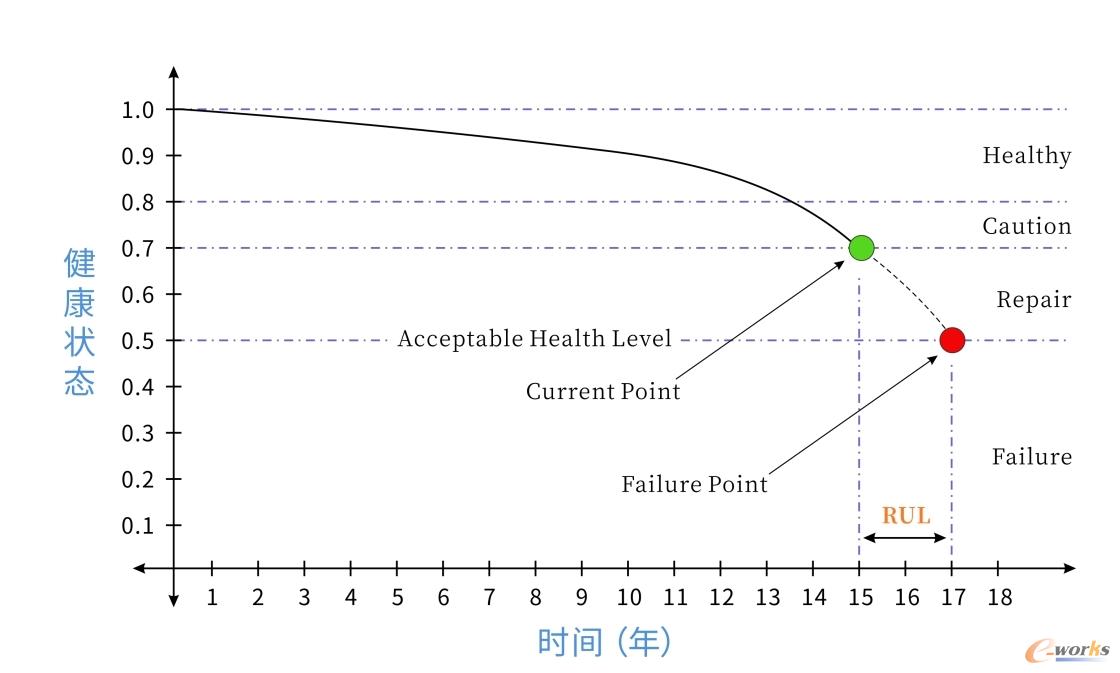
某产品健康状态衰退曲线
归纳来看,PHM是一项集状态监测、故障检测隔离、故障诊断、性能趋势预测、剩余寿命预测、维护决策与资源管理等功能于一身的综合技术。通过这一技术,不仅解决了是否修、何时修的问题,而且可在设备发生故障前确定成本效益最优的维护时机、更精准的定位故障点与故障原因、制定科学有效的健康管理策略,真正做到知微见著、防患于未然,从而有效降低甚至消除潜在的停机、减少设备的维修费用和提高维修准确性、实现设备价值最大化。简单来说,PHM能实现在合适的时间对准确的位置做正确的维修。
相较于传统的维修模式,PHM将基于事件驱动的维修(事后维修)、时间驱动的维修(定期维修)等基于当前健康状态的故障检测与诊断,变成了基于未来健康状态的预测;将以故障的发生、出现为判断依据的这种维护理念,提升为设备健康为目的的一种管理和维护手段,是一种更具前景的维护保障技术。
PHM体系结构与七大功能模块
对于PHM体系结构,业界普遍参照OSA-CBM(Open System Architecture for Condition-Based Maintenance),用于指导构建机械、电子和结构等领域的各种类型的PHM系统。具体由数据获取、特征提取、状态监测、健康评估、故障预测、维修决策与集成控制7大功能模块来实现。
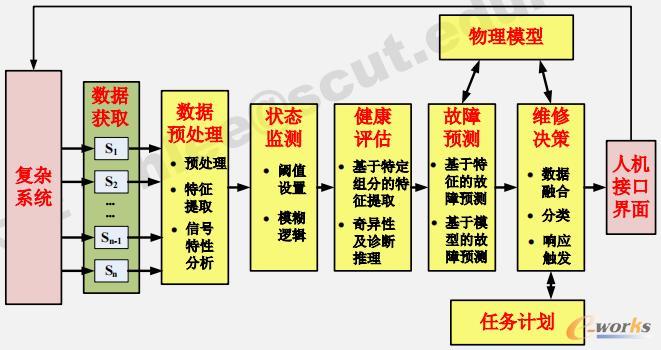
PHM最为典型的体系结构CBM
(来源:华南理工大学吴贤铭智能工程学院副院长李巍华教授演讲PPT)
1、数据获取
采用光纤传感器、微机电系统、智能传感器等先进的传感器技术,采集所需的物理量(如压力、温度、电流),并按照定义的数字信号格式输出数据。
2、特征提取
对单/多维度信号进行预处理,如滤波、求均值、谱分析、主分量分析、线性判别分析等常规信号处理、降维方法,来提取一些能表征设备状态的特征。
3、状态监测
将实际提取的特征输入至状态监测系统,并与不同运行条件下的先验特征(主要通过阈值判别、模糊逻辑等方法来确定阈值)进行比对,对超出了预先设定阈值的提取特征,产生报警信号。
4、健康评估
依据状态监测的情况、健康历史和负载情况,综合评估设备的健康状态。其首要功能是判定对象当前的状态是否退化,若发生了退化则需要生成新的监测条件和阈值,并形成故障诊断结果(故障位置及原因)或故障发生的可能性。
5、故障预测
综合利用前述各部分数据信息,在考虑未来载荷情况下根据当前健康状态推测未来,进而预报未来某时刻的健康状态,或者在给定载荷曲线的条件下预测剩余使用寿命。对于剩余使用寿命的预测,在算法上比较复杂,可以通过基于机理模型或数据驱动或混合模型等方法,来对故障进行预测,以获得设备的剩余使用时间、故障点、故障类型等处理信息。
基于机理模型的方法,是通过大量失效样本的分析,以深入了解设备的失效机理、失效路径等,来建立基于失效物理的模型,以对未知故障和弱故障进行有效预知和识别,需要较强的领域知识;基于数据驱动的模型,是结合大数据分析与人工智能技术来对特征值进行学习,预测未来故障,需要的数据量较大。混合模型即是两者的结合,也是相对较好的方法,通过机理分析快速构建失效物理模型,模型的保真度和准确度,由基于数据驱动的方法来弥补。
6、维修决策
根据健康评估和故障预测提供的信息,以任务完成、费用最小等为目标,对维修时间、方法等做出优化决策,进而制定出维护计划、保障建议与措施。
7、集成控制
主要是实现人-机、机-机之间的数据交流,包括集成状态监测、健康评估、故障预测、维修决策等功能产生的信息并可视化,以及产生报警信息后可控制设备停机等功能。
PHM在工业领域的应用
作为密集应用大数据的典型工业领域,PHM被认为是工业互联网的杀手级应用,是工业智能化最先发挥价值的场景之一。近年来,随着传感器、人工智能、工业互联网、大数据等技术的蓬勃发展与广泛应用,PHM行业应用迎来了快速发展。
学术界和工业界都在加强PHM的研究和开发,涌现了一批专注于PHM的提供商以及专业解决方案,如东华测试、容知日新、威锐达、东昊测试、博华科技、江凌测控等;还有部分厂商基于工业互联网、工业大数据等平台推出了故障预测与健康管理方案。PHM的应用范围也在不断拓展与延伸,已从军工领域延伸至民航、船舶与重工、轨道交通、风电、石化、半导体等多个领域,业务场景不仅覆盖了飞机、动车环、环保车辆等移动化场景,还包括各垂直行业的工厂、产线、风电场等固定化场景。以下将选择几个重点行业进行分析:
在风电行业,PHM系统应用需求强烈,普及也尤为快速。众多风机厂商已建立自己的设备健康管理系统,以提前检测风力发电机组故障,避免运行事故,降低风机运行维修成本。如中国海装开发了以风电装备故障预测性维护和智能排程调度为核心的风电机组诊断预警平台,实现了风电运行状态的远程实时监视、风控率和风功率的预测、风资源的合理调配等;远景能源以EnOS工业互联网平台为基石,推出针对风机关键部件的健康管理(PHM),通过五级健康状态,为风机提供更精准的智能运维服务;浙江运达风电自主研发的PHM,实现了对桨叶、变桨系统、传动链、变流器等核心部件的全方位健康监测,预警准确率高于85%。此外,容知日新、天数风眼、威锐达等厂商也推出了专业风电PHM解决方案。
在机床加工领域,PHM被越来越多地应用于数控机床刀具磨损和主轴的状态监测、健康评估、故障诊断与预测。通过采集主轴运行的参数,对机床运行状态和效率进行实时监控,评估主轴的当前健康状况,并基于大数据分析、深度学习等进行机床故障诊断与寿命预测,包括机床是否在加工、主轴是否有异常,主轴是否需要更换等等;还可以对数控设备的断刀状况进行实时监测,分析出刀具磨损的状态,对断刀进行预警。
例如,牧野机床自主研发了ProNetConneXIIoT解决方案为客户提供机床远程运维支持以及主轴诊断,以最小化机床停机时间,延长机床寿命。富士康通过与创新奇智合作推出了以PHM为核心的无忧刀具主轴项目,将刀具生产效率提高30%,降低60%的意外停机,减少50%监控机台所需劳动力,质量缺陷率从6‰降至3‰,库存周期降低15%,节约16%的成本。
在航空航天行业,PHM的应用相对成熟,并已从最早的战斗机,拓展到直升机和民航客机上。波音、空客等国际航空制造巨头通过AHM、AIRMAN等PHM系统,帮助客户实现飞机的故障预测与健康管理,我国首型大型客机C919也已安装由航天测控自主开发的PHM系统。
PHM在设备价值高、机理复杂、运维需求量大等行业需求旺盛,但当前整个工业领域的PHM仍处于起步阶段。从技术角度,要实现PHM,除了海量的数据基础和大数据分析技术外,还需要有效结合行业知识、专家经验等形成更准确的模型,而这此正是当前很多企业推进PHM应用的难点所在;另外,当前大部分PHM厂商的解决方案还不够成熟,聚焦状态监测与故障预测的居多,真正可以实现健康管理的很少,而能打通从感知监测、诊断到预测、维护管理整个闭环的方案则更少,在一定程度上影响了PHM的落地和企业对PHM价值的认可。
小结
当前,工业企业愈来愈重视关键设备的运行维护,并将其作为痛点来解决,PHM作为“治未病”的重要手段,在降低维护成本、减少故障次数、提高设备生产率等方面优势明显。据美国国家科学基金会的一项研究表明,通过研究并部署PHM技术,可以给工业带来了超过8.55亿美元的经济效益,达到近于零的计划外停工时间,并得到更为优化的维护策略。相信,未来PHM的应用将更加普遍与深入。
参考资料
从修复性维护到预测性维护风机维护策略的发展趋势
大白话科普PHM技术
宋华振:大话预测性维护
航空领域军机的机电产品的故障预测和健康管理技术综述
本文为e-works原创投稿文章,未经e-works书面许可,任何人不得复制、转载、摘编等任何方式进行使用。如已是e-works授权合作伙伴,应在授权范围内使用。e-works内容合作伙伴申请热线:editor@e-works.net.cn tel:027-87592219/20/21。