本文为“2022年度中国智能制造最佳应用实践奖”参评案例。本次活动将评选出2022年度,为中国智能制造领域带来突出效益的最佳实践工程,全面介绍企业推进智能制造的步骤、重点与难点、获得效益等,分享建设过程中的经验,供广大制造业行业企业学习供鉴。
一、企业简介
广汽乘用车有限公司(下称“广汽乘用车”)是由广州汽车集团股份有限公司(下称“广汽集团”)设立的全资子公司,位于广州市番禺区化龙镇金山大道东633号,公司成立于2008年7月21日,注册资金超159亿元,员工约1.2万人,致力于生产销售具有国际先进水平的整车、零部件、动力总成、汽车用品以及进行汽车工程技术的研究和开发,为国家高新技术企业。
自2010年12月首款车上市至今,广汽乘用车已陆续推出影豹、GA8、GS4、GS8、影酷、M6、M8、GS3影速等多款燃油及混动车型,从紧凑型、中型、中大型、豪华型,涵盖轿车、SUV、MPV全矩阵。其中,中国商务豪华MPV创领者传祺M8持续领跑自主中高端MPV市场;传祺影豹一上市迅速成为自主运动轿车销量NO.1,荣获第九届轩辕奖中国年度汽车;全新第二代GS8依托GPMA架构L平台,突破国产品牌二十万价格的天花板;传祺GS4上市至今已收获133万+用户的口碑和信赖,获得五星安全评价。广汽传祺累计产销已超320万辆,并荣获2017年度广东省政府质量奖、2019中国品牌强国盛典年度新锐品牌、J.D.Power中国新车质量(IQS)八连冠等实力荣誉和权威认证。
面向未来,广汽乘用车将延续传承,肩负起向新能源科技企业转型的任务,在“一祺智行 更美好”的品牌口号指导下,紧随汽车“新四化”的浪潮,与时俱进,开拓创新,为用户创造更愉悦的移动出行贡献力量。

图1广汽乘用车有限公司
二、企业在智能制造方面的现状
依托广汽集团GDA2.0战略升级,广汽乘用车在智能制造方面持续加大投入,2022年实现数字化转型达到50%的目标。在数字制造方面,形成智慧工厂整体三期规划,支持定制化生产销售的同时实现单台车成本可视化。在数字供应方面,强化产供联动供应模式,推行供应链移动化、透明化、自动化,实现供应数据实时可视、业务异常及时预警,形成“001”效应,即零库存、零停线和100%透明化。在数字研发方面,通过产品和工艺两大数字化平台,100%打通产品开发的数据链,提升上下游协同效率与设计质量。
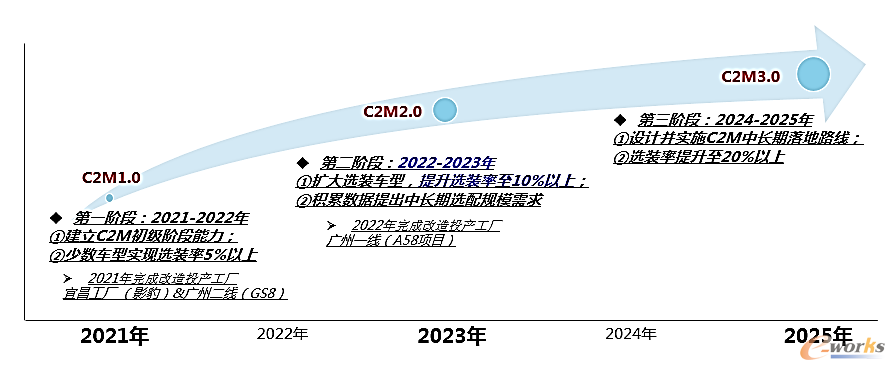
图2 总体规划阶段图
三、参评智能制造项目详细情况介绍
1. 项目背景介绍
当前,汽车市场消费需求持续疲软,车企面临巨大压力,顾客的消费观念也由被动接受逐渐转变为主动接受,过往的规模化生产销售模式已经难以为继。带给车企的挑战是如何提升数字化、智能化、定制化的能力,为顾客提供个性化的购车体验。
面对新兴商业模式,为满足顾客个性化定制需求,2020年公司将顾客需求与供应端直连,顾客端到制造端信息互通做为今后一段时期的发展重点。终极目标是通过互联网将不同的生产线连接在一起,运用云计算、大数据等先进技术进行数据的即时交换,按照顾客的产品定制要求,设定适合的生产工序,最终生产出个性化的产品并准时交付给客户。通过客户直接参与产品创新等方式,在满足其多样化需求的同时,提高消费者的粘性和忠诚度。
2. 项目实施与应用情况详细介绍
(1)项目建设方案
本项目以汽车的个性化定制与智能制造为目标,通过对3D模型、BOM技术、柔性制造及物流标准化等核心技术及模块的攻关突破,建设广汽传祺C2M个性化定制平台。平台整合了产品研发端、生产制造端与物流供应链端的核心数据,串联C2M业务过程,支撑定制化产品全生命周期协同,并依托公司已有的柔性高效生产线,搭建数字化特色服务体系,通过产品模块化设计和个性化组合,实现汽车的个性化定制与智能生产,从而满足用户的个性化需求,推动公司定制化选装业务的发展,促进广州及周边地区汽车产业链整体数字化转型升级。
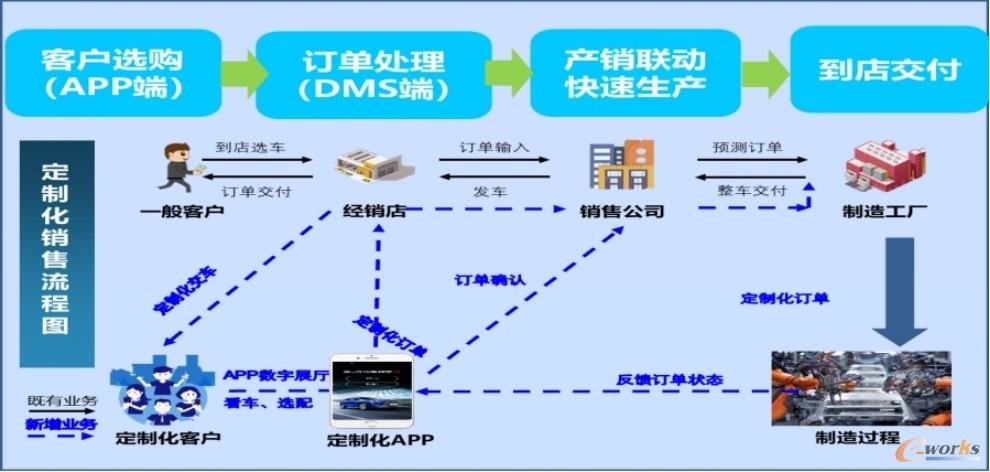
图3 广汽传祺C2M规模化个性化定制平台服务流程图
客户可基于广汽传祺APP定制化功能提供的大量的多样化的配置项进行个性化选装。客户订单确定后被系统转化为业务数据,经企业级BOM数字化管理平台工程配置器解析后传递给制造端产供业务中台进行订单与数字排程处理。生管物流系统(GPS)收到生产订单后将零部件需求发送到上游的各个供应商与物流商,MES系统根据指示生产出满足客户需求的个性化车辆。通过互联网、数字化将研产供销连接在一起,运用庞大的数据化系统进行数据及时交换,按照客户的订单要求,设定物流模式、生产计划与制造工序,最终生产出个性化的定制产品。
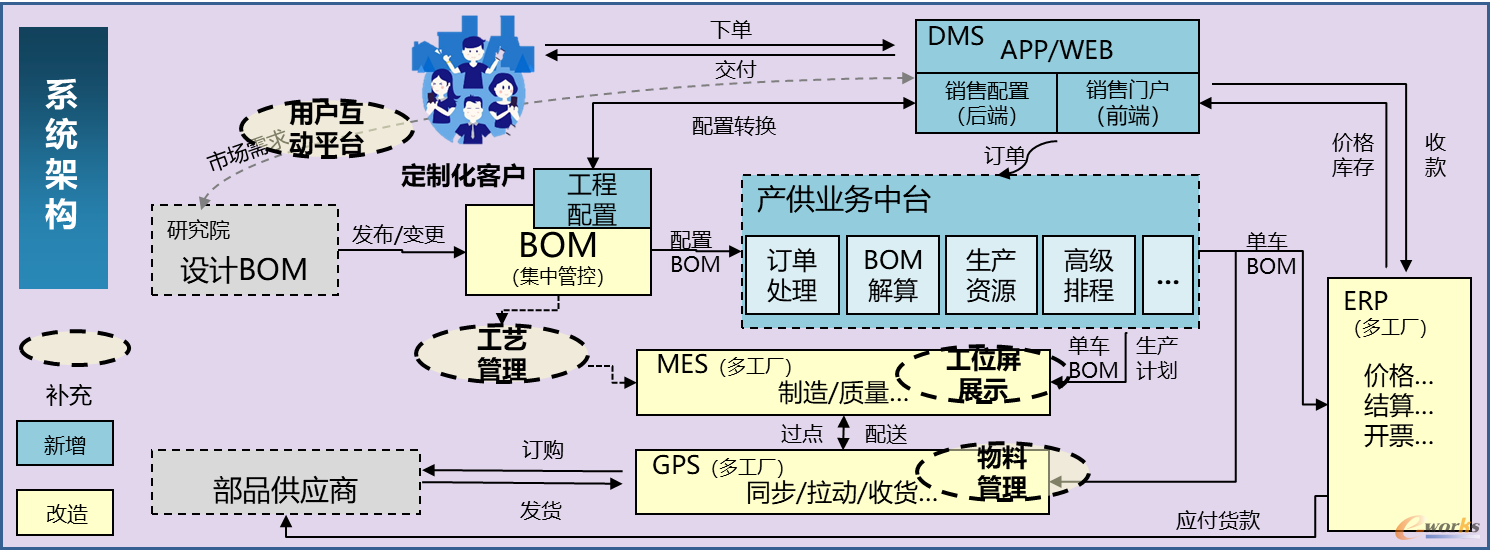
图4 广汽传祺C2M个性化定制平台系统架构图
(2)项目建设情况
1)企业级BOM数字化管理平台
企业级BOM数字化管理平台包含销售/配置、早期、工程、样车、工艺、工厂、备件等BOM数据管理。在满足定制化方面,客户的每一次选配都需要对其进行有效性的验证,包括工程配置器验证选配是否符合设定的选装规则,同时通过产供业务中台请求数据检查库存、排产等,并向供应商检索库存、生产、物流等状况,最终综合上述结果给出后续的方案,组合成可交付的定制车辆。
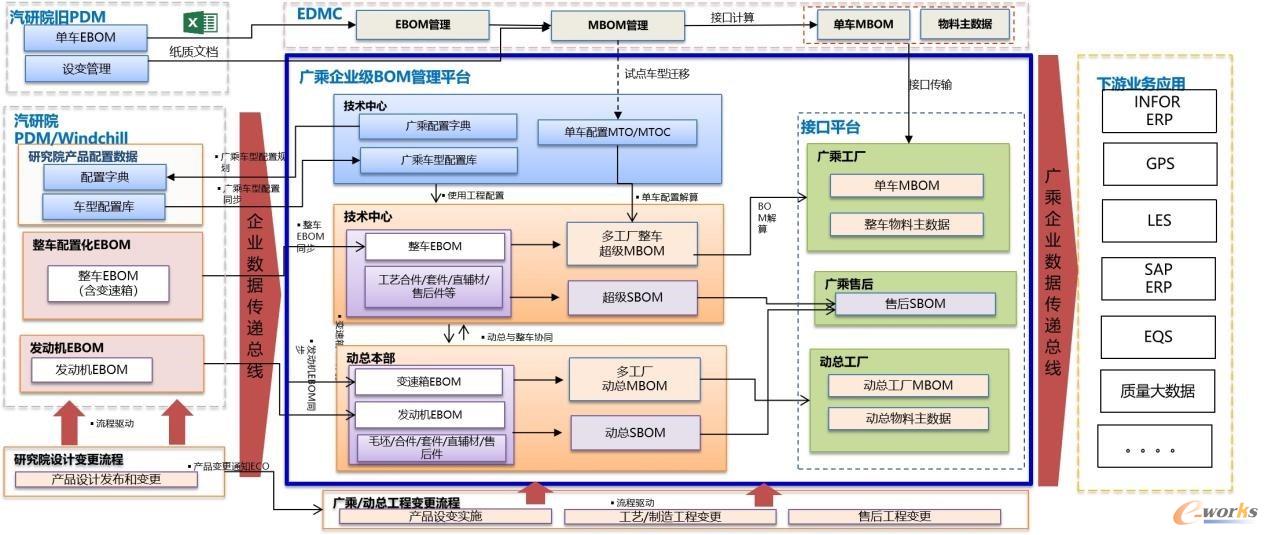
图5 企业级BOM数字化管理平台系统整体建设蓝图
2) 生管物流定制化信息流
为确保顾客的选装订单能够快速满足,针对选装池零件订购专项开发了生管物流系统进行精细化管理。生管物流系统关于定制化模式主要从选装池零件系统推移管理,选装池零件系统订购管理,选装标识指示及备件防错等系统模块进行优化升级。
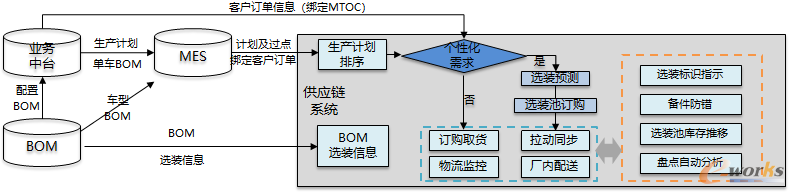
图6 生管物流系统工作流程
3) APP客户端改造
车辆配置选装包作为行业发展趋势,为满足客户个性化定制需求,以客户体验为中心,适应市场发展需要,提高产品竞争力,对广汽传祺APP进行升级改造,主要分选配下定、订单可视化及消息推送等三部分进行改造完成。
4) 生产工艺柔性化配套
广乘工艺产线规划定位为高自动化、高柔性、高品质保证能力整车生产线。经过不断的产线优化升级,已基本实现在冲、焊、涂、总各工艺领域多车型混线柔性生产。
焊装柔性化——焊接、搬运、涂胶、滚边等工艺的自动化率达到100%。高效柔性焊装生产线,主线应用柔性输送定位系统、分总成线应用模块化柔性工作站,采用全伺服定位地板柔性总拼系统、GateFramer+Flextrack+NC车身柔性总拼系统等先进技术,实现多车型多平台共线生产,1分钟内实现车型快速切换。
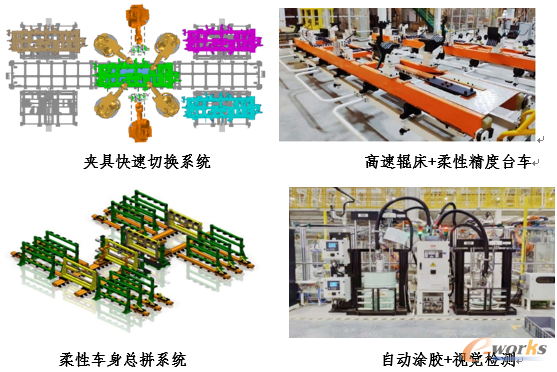
图7 焊装高柔性
涂装柔性化——车身喷涂100%机器人化,喷涂采用56台机器人,保证高品质生产作业的同时,全面削减高风险岗位。车底涂胶100%机器人化,基于3D视觉定位系统和高精度定量输出系统,实现机器人车底涂胶,保证车身高密封性能的同时。
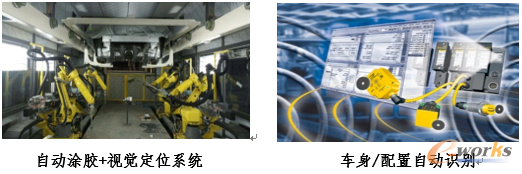
图8 涂装高柔性
总装柔性化——立体式底盘系统合装设备,整体实现车身扶正、NC校正、自动拧紧、合车100%自动化。玻璃、座椅、轮胎均能实现自动定位、自动识别、全自动安装,采用“多机器人协同运动”+3D视觉引导技术”实现行业领先的高精度自动化装配;轮胎智能化全自动装配技术为行业效率最高。
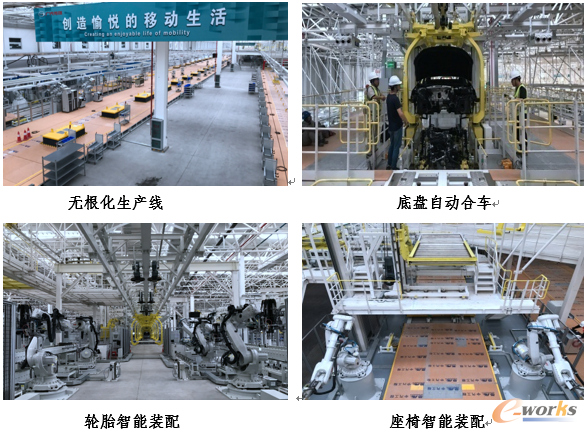
图9 总装高柔性
核心技术及项目创新性分析——工厂秉承广汽乘用车的绿色环保理念,加持多项行业顶尖的环保生产技术,力求打造世界级的生态工厂。
5) 定制化BOM及整车编码技术
个性化定制最重要的是要满足每个用户订单的车型编码及BOM解算,以便在生产过程中能够快速识别。
整车编码技术——整车编码是要对产品进行重定义,分为三部分:A车型属性、B可选配置、C固定配置。对可选配置要进行单独配置定义,如下图所示。
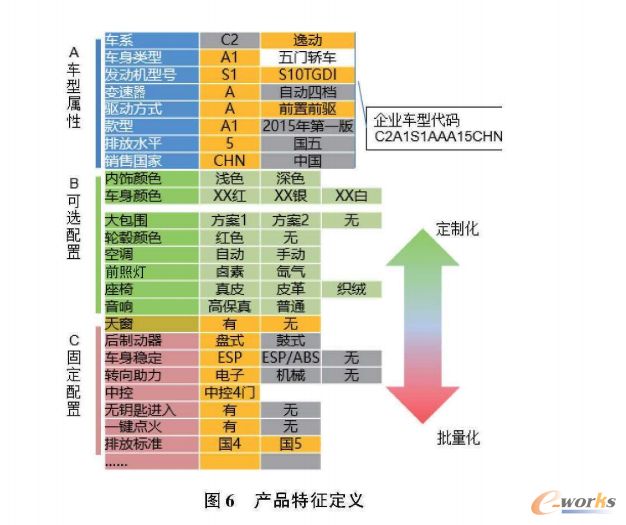
图10 产品特征定义
个性化定制的车型必须按照用户订单的选配内容进行系统自动编码,按照整车编码的规则,整车编码的数量与产品的选配数量有关,且个性化定制需要一个系统自动地根据用户订单的选配类型生成整车编码。
编码器系统接收到DCS (经销商系统)的用户订单后,按照预先定义的编码逻辑进行整车的编码,然后传到BOM系统进行整车BOM的解算,同时与ERP等系统进行信息交互。
BOM 技术——整车BOM结构在个性化定制中起着决定性的作用,传统的BOM结构是树状的,无法根据车型的不同配置选项进行产生新的BOM信息。要满足个性化订单的整车BOM必须需要配置BOM (超级BOM)结构。超级BOM结构是采用模块化设计思路进行BOM的搭建,主要分为两层结构,第一是通用的模块化部分,主要是整车结构第一层和第二层,这个层级对所有的汽车都是通用的;第二是与项目/产品有关的部分,主要是整车的结构的第三层和第四层,这个层级对项目/产品本身用途、特性有关系。
6) 模块化设计及定制化协同
个性化订单在生产过程中是通过订单不同的选配进行生产的,就需要主机厂具备模块化设计和智能制造的柔性化生产能力。
模块化设计——汽车的整车架构划分为闭合件、底盘、车身、驾驶舱、电子系统、车身附件等6个大模块,再逐步细分为中模块和基础模块,并从顶层至底层按照三个层级划分各具体模块,为推进设计模块化、采购模块化、装配模块化的开发管理奠定基础。
从可行性分析报告转化为零部件的技术开发要求,与供应商进行技术交流后定点定价并开发验证,最终完成实物的设计开发。
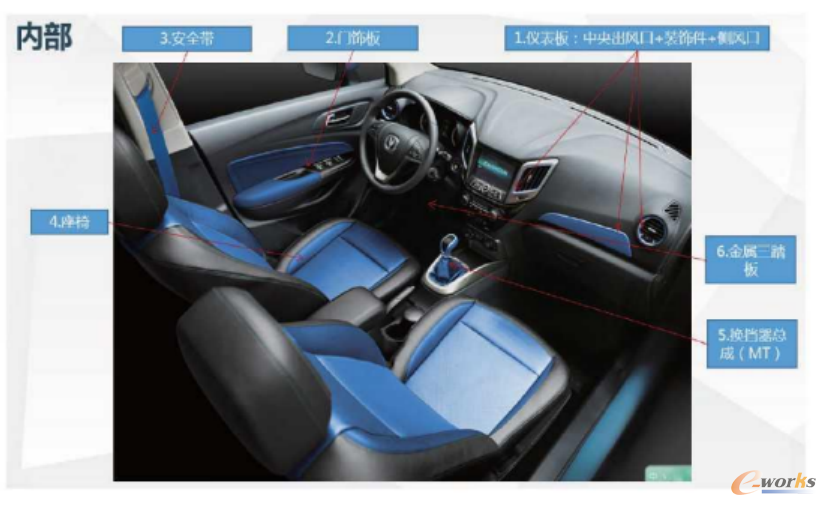
图11 模块化设计下的实物图
物料匹配技术——在大批量个性化定制模式下,为满足可重构性在装配维度中的准确性、经济性,打包物料采用按灯拣货系统,不能打包物流的大件应进行排序生产,保证零件准时供应,同时生产线(或车辆)需要增设在线识别防错装置,指导工人、设备操作。
生产柔性技术——主要是指汽车模块化设计和个性化组合技术、基于产品工艺优化与柔性装配约束的计划排产技术。
7) 客户端3D模型定制技术
用户在进行自我配置过程中,可通过广汽传祺APP实现对汽车外观、内饰等元素的选配,并可在APP中进行在线VR/AR看车。通过实施VA/AR数字化中心库赋能全车型最真实的3D画面为大家带来了足不出户就能真实查看汽车所有配置的最佳体验,同时满足了客户随时随地寻车、看车、问车、试车的一站式服务体验,也极大地增加了品牌与客户之间的沟通粘性。
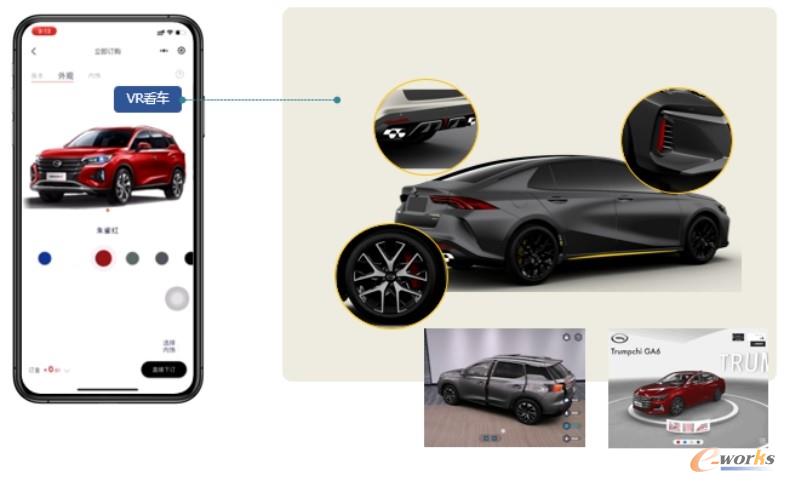
图12 在线VR/AR看车
(3)项目创新性分析
1)搭建数字化特色服务体系
本项目搭建的数字化特色服务体系,通过打通“客-店-厂”服务生态圈,挖掘车辆全生命周期的价值,以实现进一步提升品牌的服务空间和质量。
广汽传祺APP可为用户提供一键掌控、一键直联、一键趣享三大数字体验,囊括60+项线上服务,全面覆盖买车、养车、修车、用车、出行等服务场景以及售前-售中-售后全生命周期,形成了“全场景、全周期”的服务特色。
依托大数据、人工智能、物联网等新技术,搭载手机端的“服务可视化生态平台”,实现了从生产制造、到服务实施,再到体验评价的全流程可视化,并创新推出可视化救援服务、智能养车提醒、透明车间等智能服务。用户可在手机端一键掌控车辆状况,有效解决了以往看不到、不透明、不清楚、不放心、不满意的痛点。
为了让消费者实现直连厂家,直接与厂家客服、工程师在线互动,对车辆进行远程问诊,广汽传祺创新打造智能互联APP,可一键直达厂家中央救援中心,救援网点覆盖1000+地级市,并确保100%秒级响应,10分钟内出动救援,市区30分钟内抵达,24小时保障用车体验,切实解决了用户救援服务等待的焦虑。而在2020年,最远单程救援距离达到了1034km。
不仅如此,广汽传祺APP还推出了立体式定制化服务体验。其在业内首创的代步车服务,仅需在线免押办理使用手续即可,帮助车主们解决了维修期间无车可用的困境。截至当前,投入的 8000多辆代步车已提供了超过254万次代步车服务。而其依托APP社区部落和线下车主俱乐部,打造的用户互动生态网络,则为用户构建了第二个朋友圈,让他们可以一键趣享智能车生活。
2)实现定制生产过程简单化、系统化及柔性化
维护简单化:在定制化场景下,MES系统新增工艺特征码模块,模块可上传每个车型零件号对应的工艺特征码以及工位号等信息。工艺/制造部门可线下按车间、车型维护的工艺特征码以及工位号等信息上传MES系统,MES系统获取BOM系统最新下发的单车BOM与特征码模块里面的零件信息进行交集实现单车BOM零件带工艺特征码及工位号信息。MES根据每个MTOC匹配的特征码信息按照工位号排列串联发给下游设备、系统。对比MTOC维护方式可实现人为维护系统出现的错误,同时维护工时极大的减少。
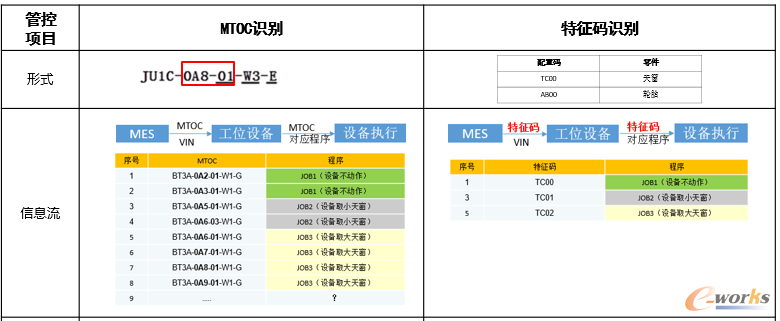
图13 MTOC维护简化
零件分拣系统化:定制化环境下,零件派生增加许多,采用纸质版分拣零件不能有效保障人员分拣的正确性,同时也不利于分拣效率的提升。因此导入广汽亮灯系统,通过系统连接BOM系统自动在需要分拣的零件货架上亮灯引导员工分拣实现零件分拣的准确性,同时作业员不需要看指示票分拣零件也提升了分拣的效率。
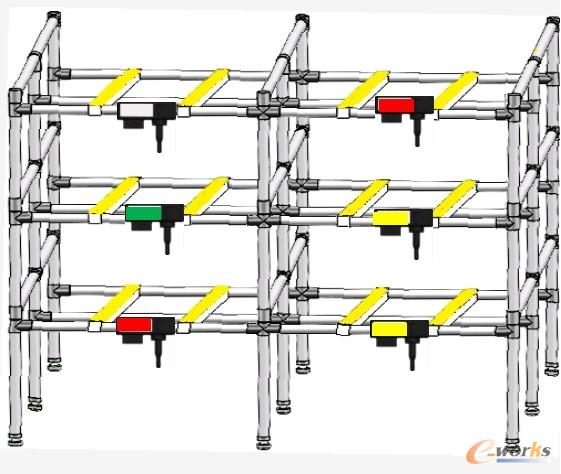
图14 广汽亮灯指示防错
装配可视化:为了保证生产线上的作业员清晰的了解本辆产品车需要装配的零件信息,导入岗位电子屏并与MES相连,MES自动获取BOM信息并建立MTOC与装配零件信息的匹配关系,并根据总装每个工艺段车辆过点信息、时间实时在岗位屏显示当台车装配零件信息,从而引导作业员装配。
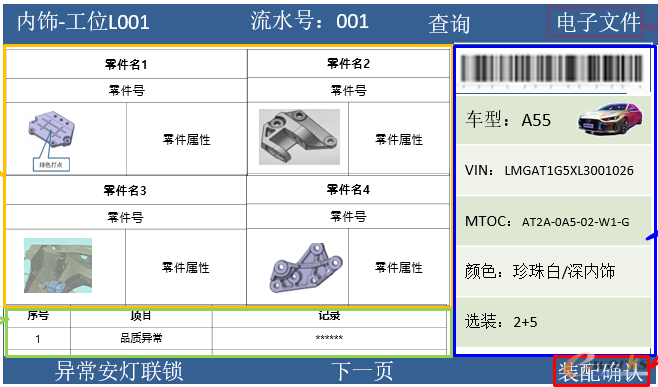
图15 装配可视化
3)实现定制物流模式标准化
A、针对销售的选装订单建立快速、灵活的生销模式
传祺现在的产销模式是销售提前预测各车型各派生未来3个月需求预测,由生管物流部根据销售的预测向供应商发布零件预测,供应商依据预测准备生产、材料等,来保证零件按计划供应。
在选装模式下,由于有多个选装包可选,使单一车型的派生从原来几个变成几百种,以传祺影豹车型为例,不同选装包的组合就有200多种。这样就导致销售对于市场需求的预测难度加大,预测的准确性会影响零件的供应与库存,同行企业也因此导致了大量选装零件的呆滞。
因此,生管物流部与销售公司建立“定制化订单”的生销模式:1、为了不因错误的预测导致大量零件呆滞,我们会根据顾客的实际选装订单发布零件预测及排产。2、结合零件的供应周期和生产周期,明确生产交付周期≤30天,订单交付周期≤45天。3、针对少部分供应周期较长的零件(如进口件等)建立战略库存来快速满足选装订单的生产。
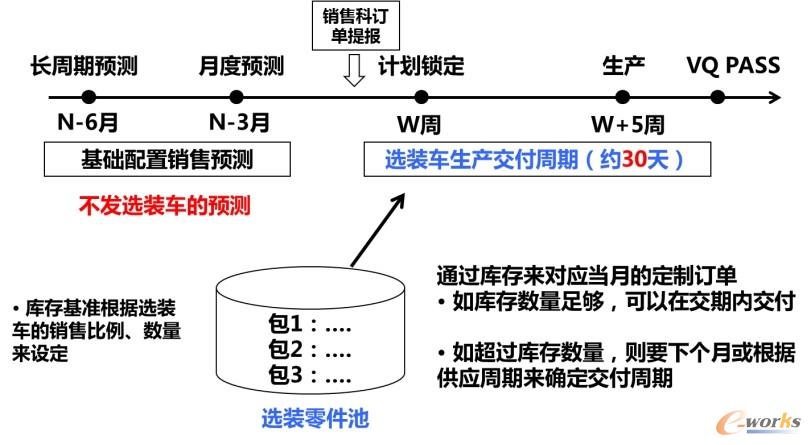
图16 “定制化订单”的生销模式
B、实现供应链数字化 快速响应生产需求
终端顾客明确需求后,需要以最快的速度响应生产和交付,这对供应链的响应速度提出了极高的要求。
为了使供应商能快速响应选装订单的零件供应,我们联合采购部到每家涉及选装零件的供应商协商供应周期的压缩。经过沟通整合,生产周期的优化,89点选装中61点零件可满足零件订单交付周期在16天内。
利用数字化平台打通终端客户及上游供应商的信息通道,终端选装订单的零件信息需求即刻推送到供应商端进行零件生产,实现上下游联动,达到供应链的快速响应。
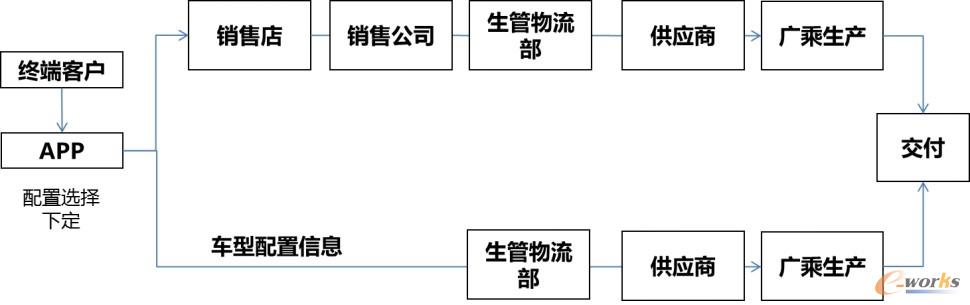
图17 供应链定制化快速反应模式
C、规划柔性化、智能化的物流配送模式
基于每位顾客的选装定制需求不一致,会出现对应1台(MTOC)为单位的生产切换,存在线上每一辆车的MTOC都不一样的极端现象;选装车派生多,存在混线生产、专用件多的情况。
对应选装车批量少,切换频繁的特点,为减少线边切换的难度,提升物流效率,选装包相关零件物流模式采用“同步物流、零脱批模式”进行管理,实现零件柔性物流配送模式。
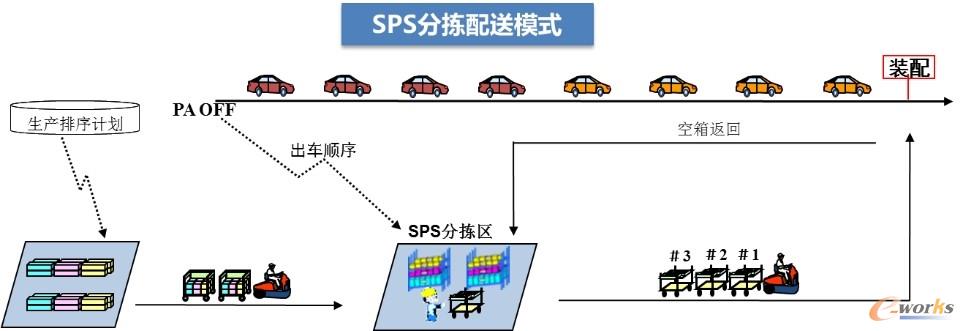
图18 SPS分拣配送模式
实施SPS分拣配送模式,根据每个车的“ID”匹配物料订单,由系统下发指令,指示员工拿取物料,每车配送一套物料,并通过SPS小车随车送料,实现零件配送准时化,同时减少线边人员取件与辨识零件的时间,节省生产线边的库存与面积。
为了使单台套的物料车可以自动的准确的配送上输送线,发明了一种料车自动上下线装置,包括料车移载机构、料车限位装置、输送线滑板、料车、控制机构,料车限位装置为两个,分别设在料车移载机构的两端,输送线滑板设在料车移载机构一端且位于料车限位装置外侧,控制机构与料车移载机构电连接,料车运行至料车限位装置后可启动控制机构通过料车移载机构转运至输送线滑板或者从输送线滑板转运出去。
3. 效益分析
1)经济效益
本项目通过搭建数字化特色服务体系,可为用户提供一键掌控、一键直联、一键趣享三大数字体验,囊括60+项线上服务,全面覆盖买车、养车、修车、用车、出行等服务场景以及售前-售中-售后全生命周期,形成了“全场景、全周期”的服务特色。
依托大数据、人工智能、物联网等新技术,建设以广汽传祺APP为核心的“服务可视化生态平台”,实现了从生产制造、到服务实施,再到体验评价的全流程可视化,并创新推出可视化救援服务、智能养车提醒、透明车间等智能服务。用户可在手机端一键掌控车辆状况,有效解决了以往看不到、不透明、不清楚、不放心、不满意的痛点。
以企业级BOM数字化管理平台与生管物流系统为核心,依托公司已有的柔性高效生产线,通过产品模块化设计和个性化组合,实现汽车的大规模个性化定制与智能生产,从而满足用户的个性化需求,推动公司定制化选装业务的发展,促进广州及周边地区汽车产业链的整体升级。
项目期内,项目实现营业收入510390万元,利润65218万元,累计缴税21383.51万元。未来一年内预计本项目新增项目收入1272250万元,项目利润385277万元,项目税收82459万元。
2)社会效益
广汽乘用车始终致力于打造人与自然和谐相处的汽车生态,把节能、环保、减排、降耗以及循环利用列为规划建设最重要的前置条件,构建了绿色、节能、环保的世界级生态工厂和造车体系。
I、本项目的实施使公司突破既有产销模式、实现用户需求驱动的跨越式发展。
本项目以"模块化设计、智能化生产、协同化运作”为特征的汽车大规模个性化定制的智能制造新模式,颠覆了“从工厂到用户"的传统生产思维,转为“以用户需求为驱动”的个性化生产,通过产品模块化设计和个性化组合,满足用户的个性化需求,推动公司定制化选装业务的发展。
II、本项目对汽车制造供应链产业生产方式改革,可加深公司与产业链企业上下游之间的合作,实现广州地区汽车制造产业链行业整体竞争力的跨越式提升。本项目的实施将是一次对汽车制造供应链产业长期渐进的生产方式改革,通过本项目的实施,可实现信息高效畅通、生产交付过程零库存供应链流程,促进公司与产业链企业上下游间协同共建理想的供应链流程,实现广州地区汽车制造产业链行业整体竞争力的跨越式提升。
III、通过本项目的实施,符合《广州市推动规模化个性定制产业发展建设“定制之都”三年行动计划(2020-2022年)》的政策导向。
本项目打造具有特色的数字化特色服务体系与“广汽传祺C2M规模化个性化定制平台”,有利于在广州市形成完善的汽车整车规模化个性定制产业制造体系、产业创新体系和产业运营服务体系,促进广州汽车制造产业综合竞争力进入国内先进行列,并提升公司综合实力,带动广州市内汽车制造产业链数字化转型升级。