本文为“2023年度中国智能制造最佳应用实践奖”参评案例。本次活动将评选出2023年度,为中国智能制造领域带来突出效益的最佳实践工程,全面介绍企业推进智能制造的步骤、重点与难点、获得效益等,分享建设过程中的经验,供广大制造业行业企业学习供鉴。
一、企业简介
青岛鼎新电子科技有限公司(以下简称“鼎新电子”)于2006年5月成立,隶属于海尔集团卡奥斯COSMOPlat,是一家专业从事智能控制器开发及生产的企业,企业职工约600余人,每年研发投入占比在3%以上。鼎新电子专注于智能家电控制板的研发和生产近17年,整体研发创新能力强,市场开发及售后服务保证体系完善。依托在技术能力、生态资源方面的深厚积累和沉淀,鼎新电子融合物联网、大数据、云计算、人工智能、新一代信息技术,构建了覆盖电子、家电、电机、汽车等行业的智能互联工厂。

图1 青岛鼎新电子科技有限公司
鼎新电子始终秉承“人单合一、创新发展”的企业精神,致力于打造PCBA智能控制器标杆工厂,主营的白色家电智能控制器产品占海尔集团份额的50%左右。凭借专业化、精细化、数字化、智能化等优势,鼎新电子荣获工信部创新领航应用案例、国家级质量标杆企业、山东省智能工厂、山东省质量标杆企业、山东省晨星工厂、山东省绿色工厂、青岛市智能工厂、青岛市质量标杆企业、青岛市绿色工厂、青岛市“专精特新”企业等多项荣誉。2022年,鼎新电子通过国家智能制造成熟度三级认定、国际IPC QML审核认证,是青岛市100强企业、山东省数字经济重点项目。
二、企业在智能制造方面的现状
鼎新电子建立了基于工业互联网平台的、以运营决策大数据平台为中心的一整套协同管理系统。该系统汇聚内外部各环节主体,整合和优化业务流、信息流,将工艺设计、计划调度、物流配送、生产作业等工作流程中收集到的综合服务数据推送到运营决策系统,打通了工艺设计、计划和制造三个环节。通过APS系统自动给出排产建议,再到SAP系统进行订单下达,MES自动关联到各制造工序,制程问题通过ANDON系统触发报修,再根据WMS统一进行出入库管理,鼎新电子减少了过程中的沟通成本,业务实现线上跟踪,精准预测,快速响应。这不仅缩短了产品的交付周期,还促进了PCBA产品智能制造全产业链的数字化转型。
通过先进的机理算法,能够精准预测机器健康状态,为客户提供关键设备实时、在线、智能、远程的状态监控;通过智能化分析,给出设备维护方案并辅助决策,降低设备非计划停机时长、安全事故风险、运维成本。在制程中,一是实现故障追溯,运用知识库和模型双驱动辅助决策,提前预警消除潜在风险,分析故障,溯源可能的原因,给出最佳解决方案,降低损失。二是多系统融合(MES系统、WMS系统、SCADA系统、安灯系统、CQM系统、SAP系统、APS系统、ITPM系统、VMI系统、PLM系统等),打通生产系统、信息化系统、智能化系统,提供统一平台、统一管理、统一服务,形成电子器件制造业智慧管理体系。三是实现主动式管理,依托深度学习及知识计算,实现全场景主动管理。以问题为导向,聚焦管理短板,提升管理效能。
协同管理系统已经应用于企业的多个环节。在智能分拣环节,可以大幅降低成本,提高速度。在设备健康管理环节,在实时监控设备运行数据基础上,基于特征分析与机器学习技术预测设备故障,在遇到设备突发故障时,能快速诊断出故障、定位故障原因、提供对应解决方法。在仓储物流环节,AGV的使用,可以满足省人效率提升。在质量管控环节,可以实现物料、在制品、产成品全流程质量监控和后期追溯问题。在能源管理环节,可以动态监控能源数据,提供优化决策支持。在生产作业环节,实现过程可视化管理。
通过数字化和信息化的深度融合改造,鼎新电子在设备投资方面,通过引入智能化设备,实现减员提效目标,全自动化生产线单班次用人降低50%。在信息化投入方面,建设了以MES为核心的数据采集和应用系统项目,实现从原材料加工到成品装卸的有效监控。在人机交互环节,引入自动触发报警、自动停机等功能,在提高安全生产管理能力的同时,也极大提升企业的信息化管理水平。在创新方面,应用RFID、SLAM、氮气波峰焊焊接、激光导航等技术,实现了企业精细化管理,尤其是生产制造过程的管理,利用MES优化车间制造过程,提高企业生产透明的趋势更加明显。在经济性方面,实现产值的提升,其中外单生态产值达到2倍提升,生产效率提升26%、运营成本下降25%、订单准时交付提升7%、研发周期缩短30%、资源综合利用率提升26%、真正做到安全零事故。
三、参评智能制造项目详细情况介绍
鼎新电子以精益化、标准化、自动化、信息化、数字化、绿色化“六化”为核心进行全流程智能制造改善。通过对每一个参与环节进行分析,逐点、线、面进行深入,然后逐步推进关键工序的自动化建设,总体围绕先试点后推广的原则,同时结合信息化的推广应用,实现智能工厂建设的逐步推进。
鼎新电子具体实施路径是纵横轴匹配的两维战略:高精度指引下的高效率。纵横轴的关系是相互融合,相互促进,即用户价值越大,企业价值越大。从高精度上来看,工厂全要素、网器、全流程与用户零距离互联,用户体验的小数据和全流程资源实时零距离对接,资源在满足用户体验的过程中实现自身的价值最大化。精准抓住用户需求,实现由为库存生产到每台产品都直发用户。从高效率上来看,用户定单下达后,模块商资源实时对接需求,可变模块和不可变模块同步生产,高效自动化生产线生产的是不可变模块的,柔性生产线生产的是可变模块,即生产和需求是完全一对一匹配。既能满足用户个性化定制需求,又能满足高效生产。
1. 项目背景介绍
在智能制造建设之前,鼎新电子面临着一系列业务痛点和亟待解决的问题。首先,制造过程复杂且成本高昂,这使得生产效率低下,难以满足市场需求。其次,企业内部资源整合不力,导致跨部门沟通时效慢、效率低下,制约了企业的整体运营效率。再者,原有信息系统积累了大量历史数据,但如何实现这些数据的迁移和再利用,成为了一个重要的问题。最后,如何充分发挥数据价值,将其用于驱动生产和管理决策,也是鼎新电子需要解决的难题。
为此,鼎新电子决心通过智能制造、技术创新等,为企业的持续发展奠定坚实基础。鼎新电子在智能制造实践过程中始终坚持“总体规划、分阶段实施、效益导向、重大突破”的建设方针,坚持长远性,考虑企业身处的市场和环境,注重多角度的总体分析,全面优化资源配置。同时,注重科学创新,对行业趋势和技术创新进行深入研究和预测,以便选择正确的创新方向。此外,建立并完善创新管理体系,确保创新持续稳定,以推动鼎新电子的进一步发展。
2. 项目实施与应用情况详细介绍
为实现高效率,鼎新电子对企业的智能制造技术升级,通过大数据、物联网技术、智能成套设备、AGV、SCADA、工艺仿真、APS等先进技术和智能化装备的应用,实现工厂人机物的互联互通,实现企业端到端的信息融合,提升企业柔性制造能力。
1)工艺设计环节
在工艺设计环节,鼎新电子实现了基于工艺设计、生产、检验等系统的集成。通过工艺信息下发、执行、反馈、监控的闭环管控,构建横向和纵向融合发展关系,确保生产经营持续进行,从而提升整个工厂各部门间的赋能支持能力和协同效率,实现工艺设计与制造网络化协同。
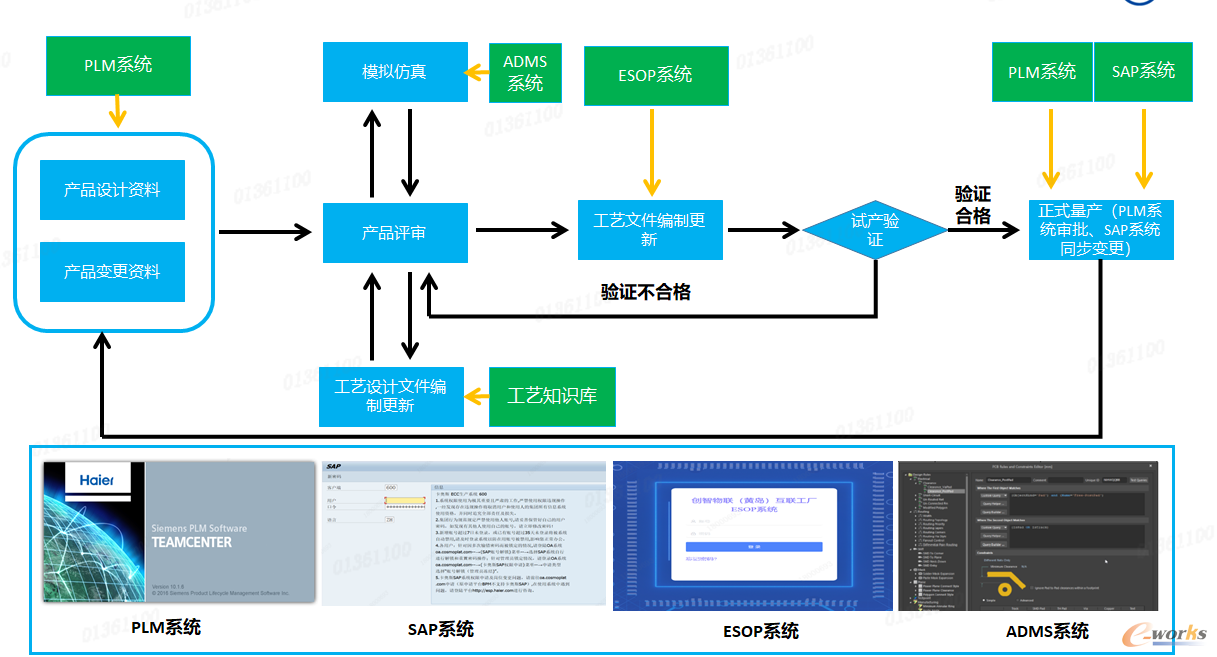
图2 工艺设计网络化协同管理
2)生产作业环节
以精益生产和约束理论为指导,为不同类型的生产构建先进适用的制造执行系统MES,实现整个车间业务流程的透明化、可视化管控。内容包括:不同车间类型的工作计划的制定、工作计划的批准和过程监控、车间加工物料的跟踪和管理、车间设施的运行和监控、生产技术准备管理、工具管理和制造过程质量管理与质量追溯、车间绩效管理、车间可视化管理。

图3 生产作业先进过程控制
3)制程安灯环节
通过安灯系统提升异常故障响应速度,加强车间生产过程的管理,信息传递做到快捷化,工序过程透明化,提高生产组织效率,激发工作人员积极性。首先,可记录每次异常报警的种类、响应时间和处理用时,为生产管理的分析和后期的持续改善提供数据依据。其次,安全问题紧急报警,减少突发的紧急事件处理响应时间,从而减少因此而产生的生产停顿时间。最后,可促进生产现场各部门无间合作,缩短生产线等待时间,及时反映生产中的问题,确保生产活动顺畅进行。异常发生时触发部门发起报警推送(消息推送方式为腕表、iHaier),一级处理部门需在5分钟之内给予响应,30分钟内给予处理,超过时限逐级上报至二级,二级超时上报至三级。完成形成现场报修、线上反馈、线上闭环模式,拉通整个公司的线上运营效率。
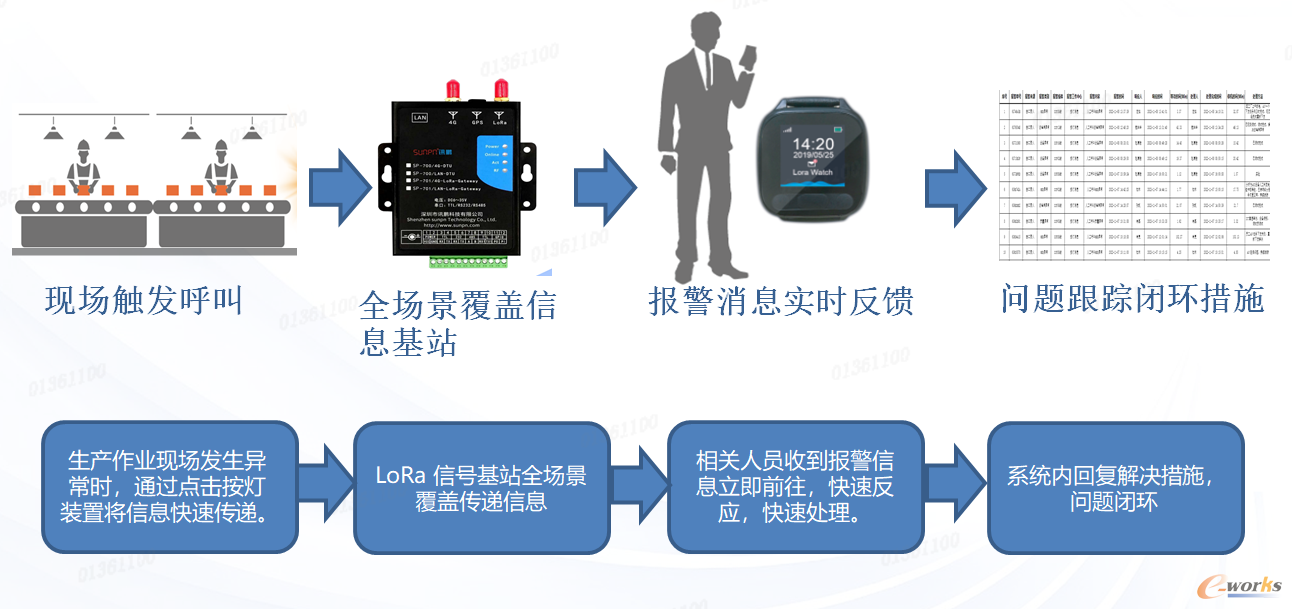
图4 安灯触发场景
4)质量管控环节
搭建了一整套完整的质量精准追溯系统及管理流程,在MES平台的基础上,导入产品工艺路径,设置进行追溯的工序及工序中要关联的质量信息。每一个产品都有唯一的二维码进行追溯管控,实现生产过程正向全要素追溯及物料反向追溯,做到产品全生命周期的追溯管理,实现从原材料来料检验、入库、生产配送、物料上线使用、过程工艺参数、过程检测信息、人员信息等全流程、全要素追溯管控。
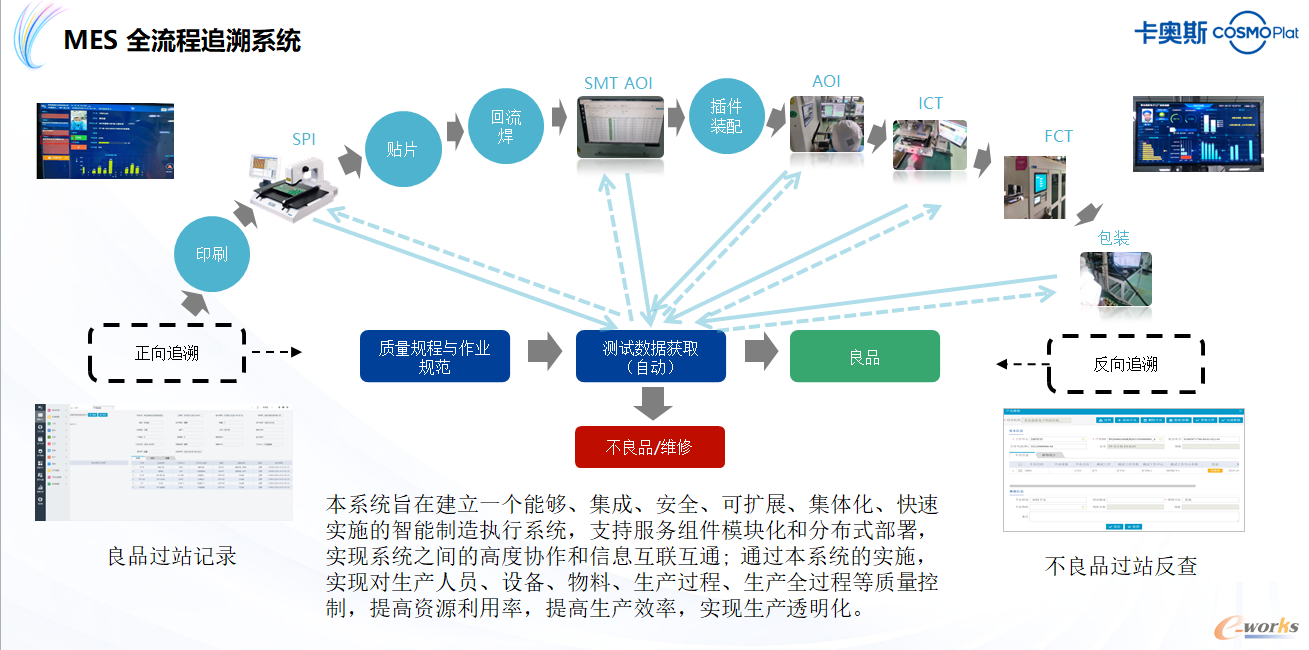
图5 全流程追溯系统
5)设备管理环节
运用数字孪生技术,实时洞察设备运行状态,保障线体高效生产。运用物联网技术、远程监控技术,通过建立故障知识库和预测模型,预测故障失效模式,开展预测性维护,实现省人化和提高运转率。
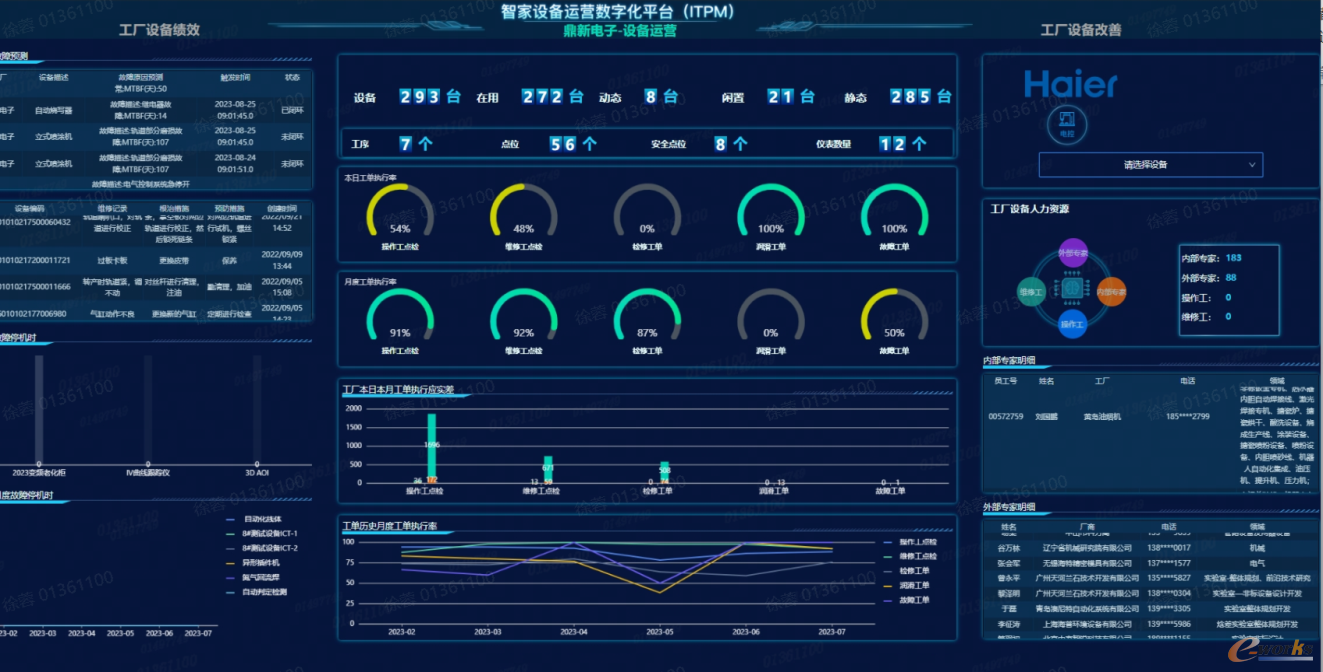
图6 设备运营数字化平台

图7 数字孪生交互系统
6)在能源管理环节
通过EMS智慧能源管理系统进行能源管理,对工厂能源整体的输送/使用等环节进行实时监管与监控。
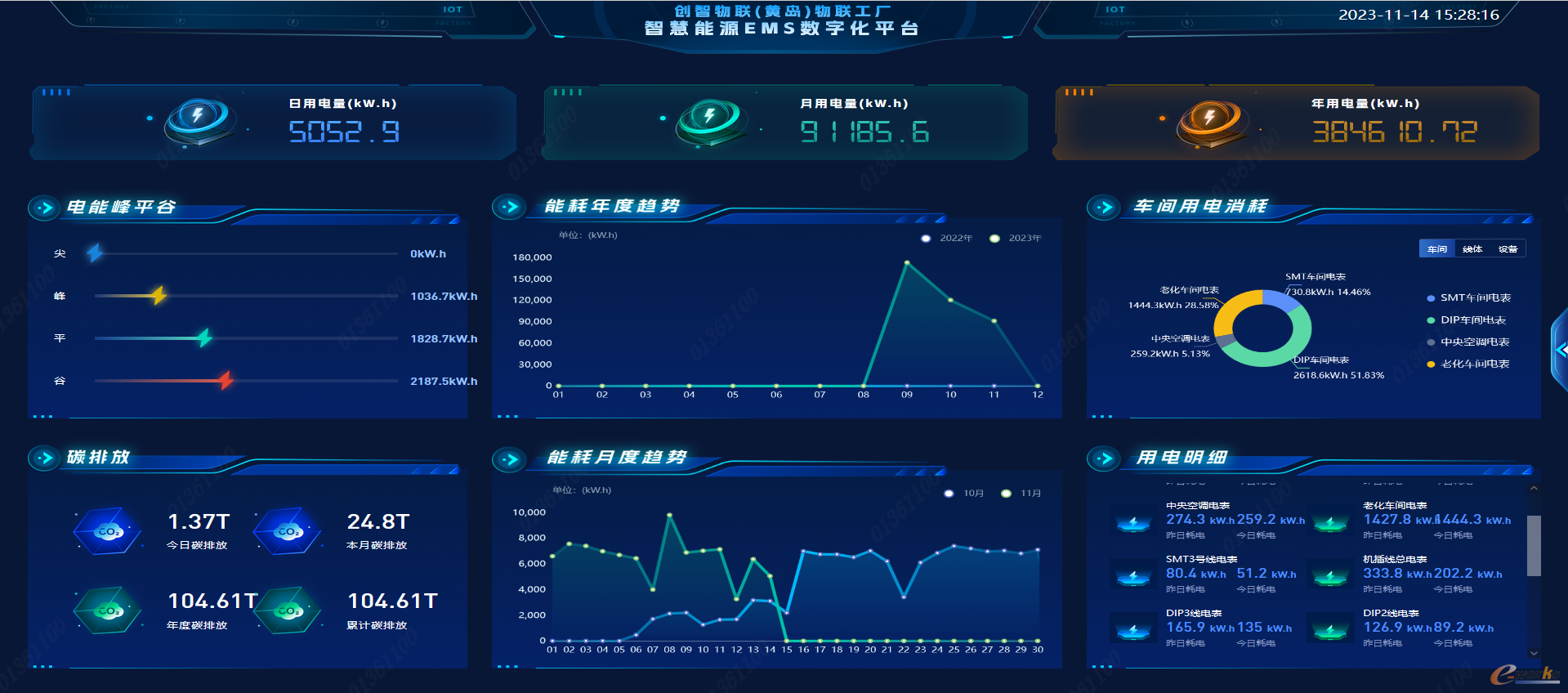
图8 智能能源管理
7)在仓储物流环节
通过部署智能物流与仓储装备等,通过精准配送计划、自动出入库(进出厂)、自动物流配送和跟踪管理,实现精细仓储管理和高效物流配送,提高物流效率和降低库存量。运用SAP、COSMO、MES进行系统化作业,从供应商配送到原材料仓入库、出库,全部采用系统支持,实现物流系统与智能生产系统的全面集成。
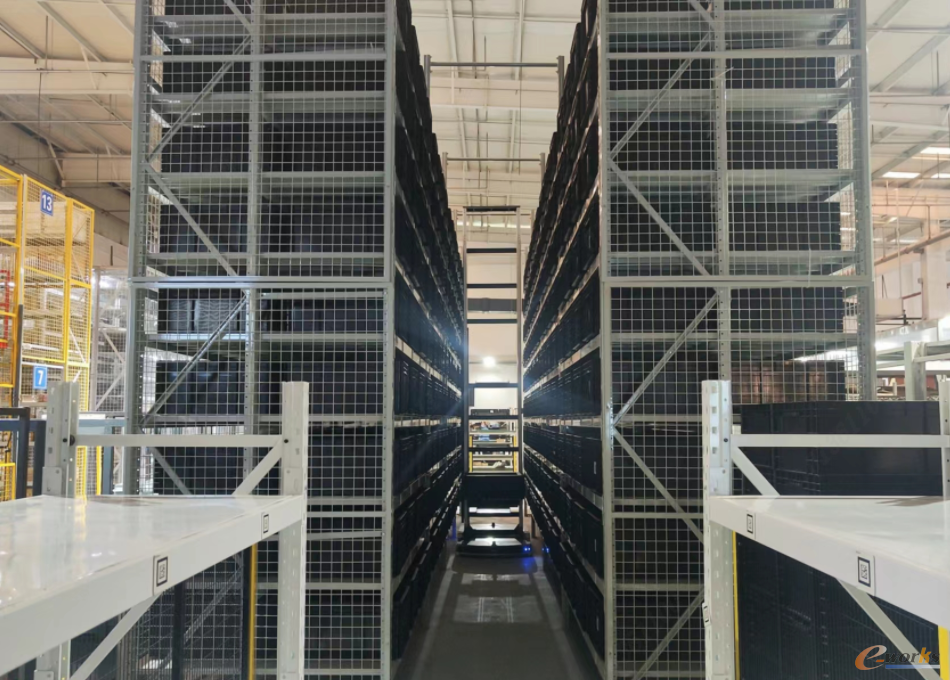
图9 高密度仓
3. 效益分析
1)经济效益
鼎新电子智能工厂的建设,将进一步发挥企业的整体优势,优化资源配置,提高生产效率、产能和制造品质,为企业的快速发展奠定基础。核心业务指标:自动化线实现省人50%,生产效率提升26%,空间节约50%、整体人员节省10%、能源节约30%、 产品合格率超过95%、运营成本下降25%、订单完成周期缩短32%、关键设备数控化率提升60%、智能制造成熟度达到四级水平。
在实现信息系统集成方面,鼎新电子构建运营决策大数据平台实现内外部协同,集成计划排产、生产追踪、物料管理、质量控制、设备管理等功能,同时为生产部门、质量部门、工艺部门、订单部门、工程技术部门、物流部门等提供车间管理信息服务。通过MES与WMS、APS、PLM、SAP、OA等系统集成实现业务流程和数据打通。项目实施后,实现计划和生产整体协同,有效支撑生产节拍降低和生产过程质量提升。
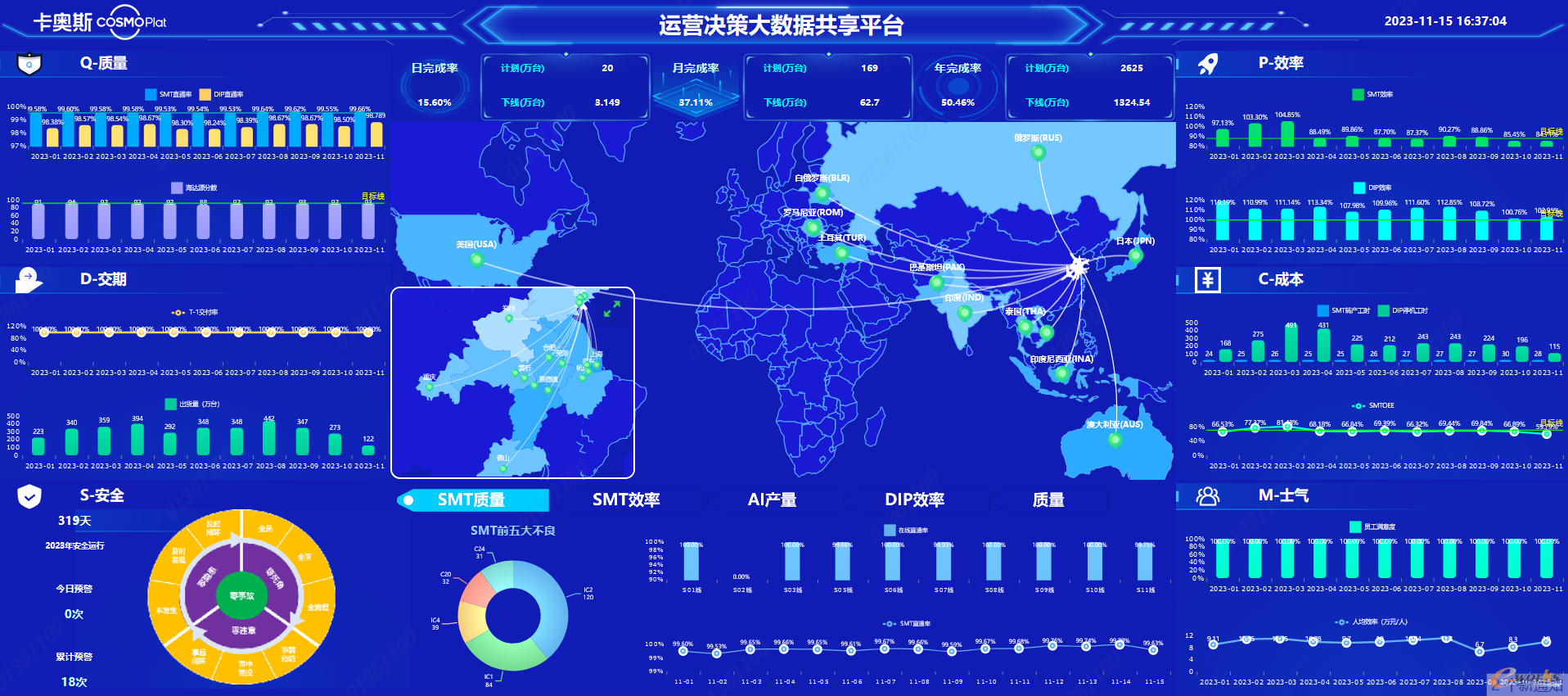
图10 运营决策大数据共享平台
2)社会效益
鼎新电子智能工厂制造体系的建立,加快了企业技术成果转化速度,全面提升企业竞争力,并通过资源共享、联合开发及沟通交流,拉动相关装备行业技术水平提升。例如,在高端检测装备方面,形成设备开发、制造能力,并在自动化、柔性和材料利用率方面超越进口装备。
3)环境效益
一方面通过能源管理系统建设,实现了对能源介质使用参数的采集以及关键高能耗设备状态的实时监控,通过信息化平台实现了能耗状态的透明化、信息化管理,从而达到节能降耗的目的。另一方面通过自动化、智能化设备的改造和新增投入,建立环境友好的智能化生产体系,从而减少噪音、粉尘、有害气体排放等污染,实现环境优化改善的目标。