今年以来,受新冠疫情冲击,全球制造业都遭受重创。工业制造企业也意识到推进数字化转型是应对市场与社会环境不稳定性、不确定性的最佳途径。随着国内疫情进入常态化防控阶段,工业制造企业的数字化转型需求也加速被激发。然而,对工业制造企业而言,推进数字化转型却面临能源与数字化的双重挑战。
施耐德电气认为,无论是离散工业,还是流程工业都应该做到“四维融合”,即从能源和自动化融合、从终端到云端垂直维度的整合、从设计运营到维护服务全生命周期数据的融合,以及从厂级管理到企业级集团级的管理的维度实现数据打通。而对工业制造企业而言,要实现“四维融合”,施耐德电气绿色智能制造将综合运用信息技术、运营技术、数据技术、能源技术和通讯技术,融会贯通,并帮助其实现生产和经营的信息化、自动化、数字化、绿色化和网络化,即“五化合一”。
数字化转型顶层规划则需要遵从“七步法”,即从梳理业务,到提升组织效率,到应用系统、数据、技术、生态体系,最后形成路线图。在施耐德电气看来,工业流程的复杂性与工艺的繁复性决定了工业制造企业的数字化转型不能简单复制、一蹴而就,需要“先医后药、先软后硬、小步快跑、效益第一”。
因此,施耐德电气提供"从咨询到落地"的绿色智能制造整体解决方案,通过顶层设计来推动各个子系统的规划和部署,进而实现从数字化到软硬件解决方案的有效落地。
从离散工业到流程工业,绿色智能制造成效卓著
施耐德电气既是绿色智能制造的践行者,也是绿色智能制造的赋能者。一方面,施耐德电气自身通过推进绿色智能制造成果喜人,不仅入选了工信部《第四批绿色制造名单》,获得“绿色供应链管理示范企业”称号;今年9月施耐德电气在中国上海、天津、重庆、西安和厦门的6家工厂进入工信部“绿色工厂”公示名单,而此前其位于上海、武汉、天津、北京、广州和无锡六地的7家工厂也于2018年和2019年先后通过工信部评审,荣膺国家级“绿色工厂”称号。
此外,武汉工厂作为施耐德电气“智能制造和绿色节能生产基地在全球的典范”,也于2018被达沃斯世界经济论坛评为发展中的“灯塔工厂”。另一方面,施耐德电气也通过将自身沉淀和总结的绿色智能制造经验对外输出,向中国宝武、神龙汽车、江苏金旺、宜宾锂宝、汉威电子、三宁化工、中国石化海南炼化、宁德时代等众多企业提供数字化转型升级服务,帮助其打造数字化、智能化工厂,推动其绿色可持续发展,并这一过程中形成了涵盖离散工业、流程工业及混合工业的绿色智能制造整体解决方案。
携绿色智能制造成果亮相2020工博会
2020年9月15日,第22届中国国际工业博览会在国家会展中心(上海)拉开帷幕。作为常态化疫情防控前提下首个线下举办的国家级工业展会,施耐德电气携绿色智能制造成果亮相,以施耐德电气武汉灯塔工厂、宜宾锂宝、三宁化工及中国石化海南炼化等的绿色智能制造典型实践案例,全面呈现了施耐德电气在助力离散工业与流程工业实现高效率、高品质的排产布产、物料管控、单位成本、设备维护、质量追溯,以及缩短工厂建设周期,提升生产运营效率,降低维护成本与能耗,满足安全与环保需求等方面的显著成效。
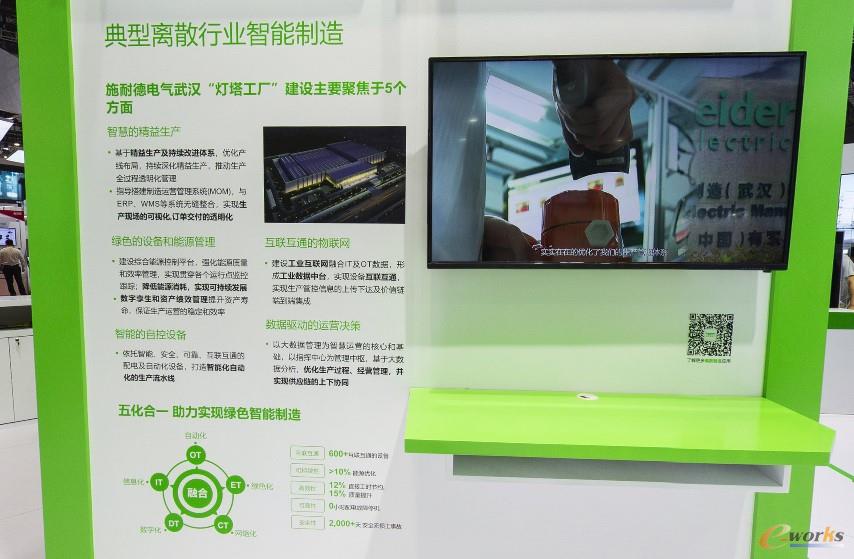
施耐德电气武汉灯塔工厂案例
比如,施耐德电气武汉灯塔工厂通过聚焦智慧的精益生产、绿色的设备和能源管理、智能的自控设备、互联互通的物联网以及数据驱动的运营决策5个方面的建设,实现600+设备互联互通,超过10%能源优化,直接节约工时12%,质量提升15%,0小时配电故障停机以及2000+天安全无损工事故。
今年年初,新冠疫情暴发,武汉成为疫情重灾区,然而处于风暴中心的施耐德武汉工厂不仅成功经受住了疫情的严峻考验,而且复工复产后仅用时不到2个月,产能就达到甚至突破100%。这其中,不仅有集团层面的联动全球资源进行协同支持,以及自身深挖产能潜力,更有数字化技术发挥的重要作用。
得益于较早地采用数字化技术,以自动化、信息化、数字化、精益化为方向进行数字化转型,施耐德电气武汉工厂复工复产后不仅有效协调了生产订单优先级,做到计划与资源的优化配置,也提升了供应链交付能力,进而更好地为客户提供及时准确的服务。
值得一提的是,施耐德电气通过聚焦“短链系统、合作共生、数字化赋能、绿色可持续”四个方向,经过多年积累,在Gartner公布的2020年度全球供应链25强中位列第4名,并继续保持工业制造类企业当中的第一名。
而在经历此次疫情后,施耐德电气中国区供应链数字化转型业务总监顾俊也表示,包括施耐德电气在内很多企业也开始反思供应链布局和策略,而在他个人看来,未来将采取更加平衡的策略,同时兼顾供应链的效率与韧性,提升抗冲击能力。
其实,不仅是施耐德电气武汉工厂,通过与施耐德电气合作推进绿色智能制造,宜宾锂宝、江苏金旺智能、三宁化工以及中国石油海南炼化等的成效也非常显著。
比如,宜宾锂宝通过与施耐德电气合作,开展锂电池正极材料生产系统的智能制造项目建设,共同制定数字化蓝图,整个智能制造项目从顶层开始规划、分步实施,成功搭建了生产执行过程信息化管理技术方案,实现了从上游原材料到下游产品质量控制一体化,全过程溯源的信息化管理模式,不仅保证了产品的一致性和质量稳定性,溯源水平位居行业前列,而且在生产管理方面也实现了各板块业务数据的集成统一及生产制造执行过程的信息化自动管控,使生产制程能力CPK达到1.67,在国内乃至亚洲都处于先进水平。据介绍,宜宾锂电也希望与施耐德电气继续携手,以实现锂电池行业的高效和可持续发展。
以数字孪生打造“虚拟工厂”,提升数字化运维水平
除了绿色智能制造实践案例,施耐德电气在本届工博会现场展出的锂电池生产线数字孪生互动沙盘、化工油气数字孪生互动沙盘,以及AVEVA数字孪生与施耐德电气融合的数字化解决方案也备受关注。
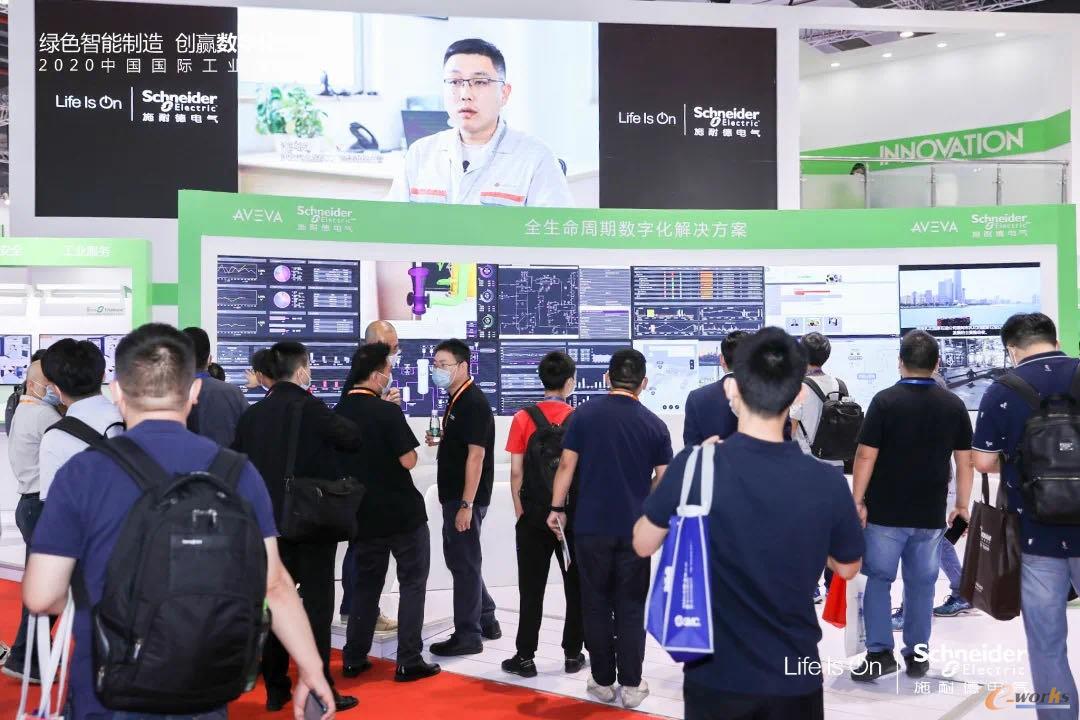
AVEVA数字孪生与施耐德电气融合的数字化解决方案
其中,AVEVA数字孪生与施耐德电气融合的数字化解决方案,以12连屏的方式展示了从工厂设计建造、生产工艺仿真、工厂运营、设备监控,到资产性能管理、数据分析的全流程。据介绍,该解决方案具有能够为工业客户提供对资产生命周期以及运营生命周期的完整数字孪生展示,全面发挥数字孪生的效用,帮助企业应对复杂环境、排忧解难,实现能源和生产效率的快速提升等优势。而全流程、全生命周期是该方案的核心所在。
2017年,施耐德电气并购了英国工程软件公司AVEVA,究其原因,这一方面是看重了后者作为工程和工业软件领域的领导者,为造船和海洋工程、石油和天然气、造纸、电力、化工和制药等工业领域提供全生命周期解决方案及服务的能力;另一方面也是工业领域数字孪生技术不断发展的背景下,施耐德电气自身为工业客户提供资产生命周期以及运营生命周期的完整数字孪生解决方案的现实需要。在收购AVEVA后,二者也着手共同打造AVEVA数字孪生与施耐德电气EcoStruxure融合的数字化全生命周期解决方案。
施耐德电气高级副总裁、工业自动化业务中国区负责人庞邢健在接受记者采访时也表示,数字孪生对于企业的价值将越来越大,但数字孪生并不是简单地建一个仿真模型或贴上数字标签,而是需要通过数字化手段真正地获取工艺、装置,包括装置的运转的实时信息,同时能够将各种专家库结合起来,施耐德电气将其称之为“灵动的数字孪生”,即要打通从设计建造到运行维护的全生命周期。
此外,庞邢健还透露,随着订阅模式越来越成为市场的热点,AVEVA的各种软件和施耐德电气的数字化业务也将逐渐转向订阅模式,通过云端部署,来降低工业客户特别是中小企业客户的总体拥有成本。
本文为e-works原创投稿文章,未经e-works书面许可,任何人不得复制、转载、摘编等任何方式进行使用。如已是e-works授权合作伙伴,应在授权范围内使用。e-works内容合作伙伴申请热线:editor@e-works.net.cn tel:027-87592219/20/21。