将工业技术模型化、软件化,普及数字化研发工具,提升智能制造供给支撑能力,助力企业在设计、工艺、生产等过程中的技术攻关和集成应用,是加速攻克我国重大技术装备、解决高端供给不足问题的关键手段。
1 引言
针对大型装备结构复杂、协同难度大等问题,借助工业互联网技术,建设面向装备的建模、数据集成与管理的系统平台,可有效支撑装备数字化管理、平台化设计、网络化协同等新模式。构建复杂装备常用的智能化模型库,支撑制造企业在价值链维度(横向)、生产维度(纵向)以及产品生命周期维度(端到端)的集成应用需求,实现数字化转型。
2 方案背景
我国正处于实施“十四五”规划的关键时期,是建设制造强国、构建现代化产业体系、实现制造业高质量发展的重要阶段。其中,重大技术装备是制造强国的重点领域,是产业结构升级的重要引擎,加快重大技术装备与工业软件融合创新,是实现制造业高质量发展的重点措施。
2.1 工业技术软件化是攻克重大技术装备的关键手段
将工业技术模型化、软件化,普及数字化研发工具,提升智能制造供给支撑能力,助力企业在设计、工艺、生产等过程中的技术攻关和集成应用,是加速攻克我国重大技术装备、解决高端供给不足问题的关键手段。
2.2 面向大型成套装备的平台创新是产业数字化转型的重点抓手
以国产大型成套复杂装备研制为牵引,利用网络化协同设计平台,管理产品全生命周期数据,实现产品模型的构建、沉淀与共享,提升产品的研制效率、质量和运营维护能力,可显著示范带动我国重点行业数字化转型发展。
2.3 装备协同研发新模式给国产软件带来新机遇
针对大型装备结构复杂、协同难度大等难点,借助工业互联网技术,建设面向装备的建模、数据集成与管理的系统平台,可有效支撑装备数字化管理、平台化设计、网络化协同等新模式,也是突破工业软件“卡脖子”技术的重要机遇。
因此,亟需研发大型成套复杂装备的网络化协同设计系统,突破工业软件“卡脖子”的核心技术,构建复杂装备常用的智能化模型库,支撑制造企业在价值链维度(横向)、生产维度(纵向)以及产品生命周期维度(端到端)的集成应用需求,实现数字化转型。
3 方案价值
3.1 提升供应链管控水平
基于数字孪生的供应链网络协同计划与执行监控的实现,将有助于推动大型成套复杂装备网络协同制造有序、协调、可控和高效的开展,其意义主要体现在以下几个方面:
●推动大型成套复杂装备供应链网络的深度融合与有机协同,提升供应链管控质量
大型成套复杂装备的研制必然伴随着复杂、动态、不确定以及一定程度的模糊性,传统的依靠手工粗放的管理方式已经难以适应大规模协同的复杂产品研制。本项目从供应协同网络的数字化、结构化、模型化的角度,通过适应VUCA的计划实现供应链协同网络的精细化与协调化的执行。
●引入数字孪生技术实现供应链执行的虚实同步,提升供应链管控水平
通过将数字孪生技术引入到大型成套复杂装备供应链管控中,将有助于推动供应链管控过程与装备成套研制结果的统一与融合,一方面提供全供应链的深度与全面的综合监控,另一方面为基于模型的成套供应关键特性提供分析奠定了基础。
3.2 提升产品技术状态管理能力
利用网络化协同设计系统管理模式,企业能够打通原来多层次、跨部门的BOM流转通道,将BOM涉及到的多个环节统一到一个平台进行管理,实现BOM在不同部门间的无缝流转,确保BOM信息的准确性以及审批的及时性,同时还实现了BOM的全程实时跟进,通过生成多个不同的BOM版本以及高亮显示有差异的组件,轻松实现成本监控。对于同一个项目产生的采购及出库,系统还提供采购/库存申请/库存发货订单合并处理,自动汇总同一个项目的BOM成本,并使订单与项目或合约直接关联,轻松实现项目成本追踪。
3.3 为大型装备成套服务运作协同与优化提供理论方法体系
基于精益思想的大型装备成套服务运作计划控制协同优化方法:执行层次,将精益思想融入运作计划与控制过程中,分析了运作计划控制的具体影响因素和结构,辨析了质量-工期-成本三目标之间的关系,引入田口质量损失函数,建立了基于成本费用关系的质量-成本-工期协同模型。构建了计划控制多层次、多项目、多目标的协同优化模型。结合实际需求,对模型进行了优化处理,设计了仿真+遗传算法,并通过实例验证了模型和算法的有效性。
创建了协同个体利益与集体利益的大型装备成套服务联邦资源合作博弈模型组合优超与资源贡献率方法建立了协同个体利益与集体利益最大化的合作博弈模型,既实现个体的优超又达到整体的核心,保证了合作的稳定性。为实现网络化协同设计环境下大型装备成套服务资源协同目标提供了理论方法。
建立了多层次、多项目、多目标的大型装备成套服务运作计划控制协同优化模型引入田口质量损失函数,提出了基于成本费用关系的质量-成本-工期三目标协同思路,建立了计划控制多层次、多项目、多目标的协同优化模型。并对模型进行了优化处理,增强了模型的可操作性和实用性。为实现云网络化协同设计模式下大型装备成套服务运作过程整体协同优化奠定了理论基础。建立了支撑和实现网络化协同设计模式的大型装备成套服务运作协同与优化理论方法体系。研究结果表明,提出的协同逻辑框架具有宏观指导意义,设计的复合协同机制体系实现了全方位协同目标,建立的协同优化模型和算法通过实例验证具有有效性和实用性。系统地实现了对资源的选择和优化配置、服务过程的计划控制等集中协同管理,保证了设计资源服务的无缝、稳定、绿色、环保、高品质地进行,达到了大型装备成套服务协同与优化的效应,提高了大型装备成套服务项目的整体效率和效益。为大型装备企业从制造商向服务集成商转型提供了理论依据和科学方法。
设计了全方位协同的大型装备成套服务复合协同机制体系基于协同管理序参量即组织协同、过程协同、信息协同、资源协同和目标协同五个维度,设计了实现全方位协同目标的复合协同机制体系,有助于消除运作中的冲突,减少内耗,充分发挥各自的效能,提高整体协同效应。
4 方案创新点
4.1 一体化、通用底层平台技术
CAXA PLM协同管理支持可配置、可扩展、模型驱动的一体化基础平台,满足不同地域、不同行业、不同规模的企业对产品生命周期管理的共性需求,是数码大方面向管理软件领域提供的一个通用基础管理平台。该平台中包括一套基础服务、多个定义工具和一套二次开发体系,用于支持在EAP上快速进行管理软件的配置和定义,并支持对现有的应用模式进行修改和扩展。CAXA PLM协同管理(EAP平台)支持设计、工艺、制造、销售、采购等各部门应用集成。
4.2 统一原模型驱动技术
在产品统一数据模型中引入元模型,为数据建模提供了语义定义和约束表达。在语法上,统一数据模型的建立采用了标准的统一建模语言;在实现上,产品数据建模过程集成了图形化建模环境。通过文档类型定义和可扩展标记语言的生成规则定义,完成了元模型的解析和利用,并把元模型转换成可扩展标记语言文件。在元模型的基础上构造应用,并对元模型进行解析,使不同应用系统能在元模型层次上交换数据信息。在统一模型的基础上,进一步实现元模型到开发环境的映射和转换,建立元模型驱动的开发方法。元模型驱动技术,实现了企业设计、工艺、制造数据贯通与协同,也为平台带来强大的二次开发能力。
4.3 与CAD深度集成
深层次解析CAD模型数据,支持2D图纸信息和3D模型信息与BOM信息的双向关联,使用代理机制自动化处理复杂模型的轻量化,通用的2D图纸红线批注和签名反写技术。
国内首创图文混排技术:能够将CAD图形、工程符号、工艺文字混合编排,实现所见即所得工艺编制方式。
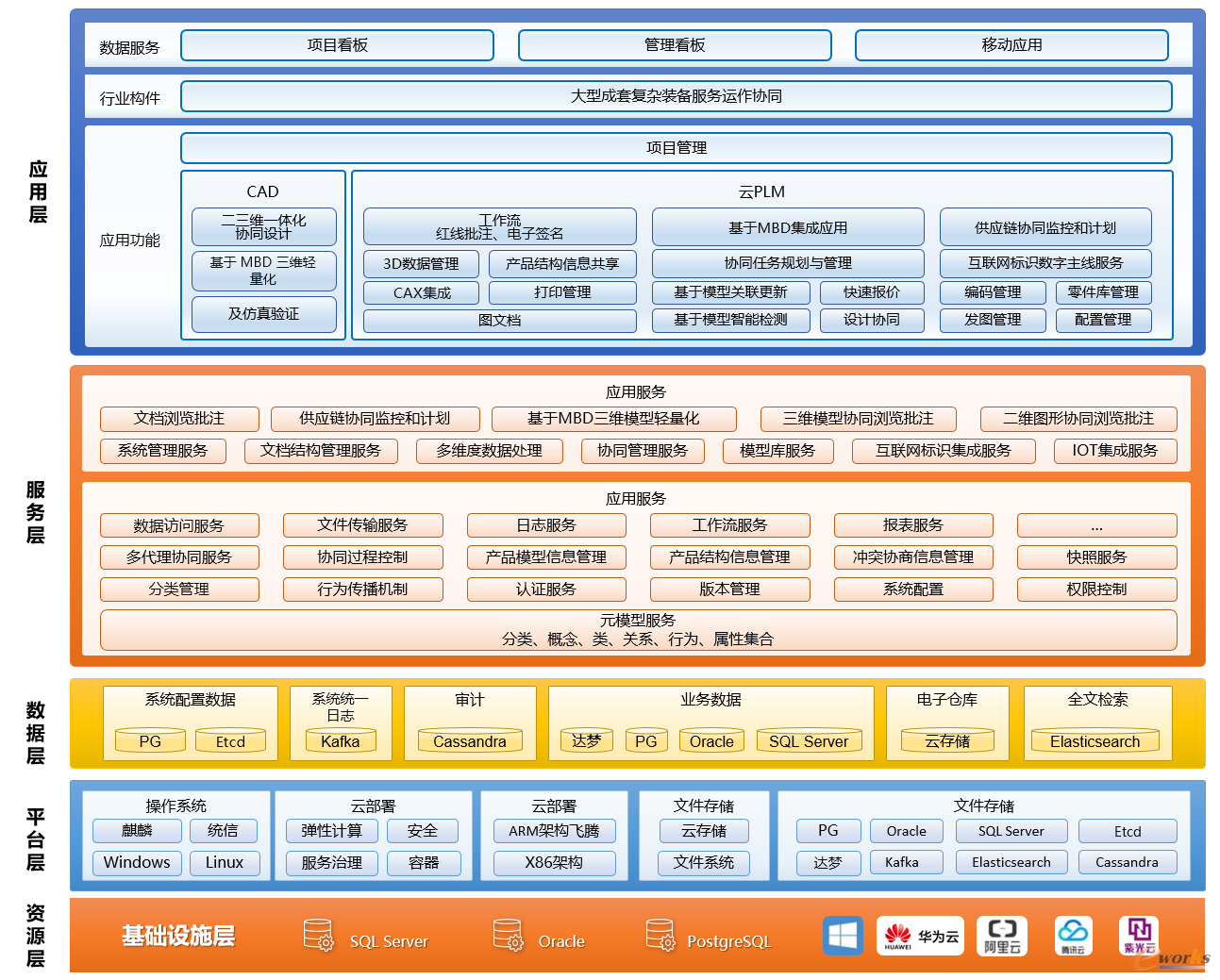
图1 大型成套复杂装备的网络化协同设计PLM系统框架
4.4 基于MBD的设计、工艺、制造一体化技术
所见即所得的图文混排工艺编制方式和支撑特殊工程符号的表格工艺编制方式使用同一套结构化数据,结构化工艺数据支持按字段进行权限控制,无编码报表技术科快速配置输出各类统计分析报表。
通过和具有模型修改能力的三维设计环境的集成,在满足轻量化模型导入的同时,也支持其他数据原格式的导入,减少了因为轻量化造成的模型错误。同时,在仿真中也可以直接对产品、资源等进行修改,达到快速优化的目的。
5 方案应用实例
兰石集团始建于1953年,前身是由新中国“一五”期间156个国家重点项目中的两项——兰州石油机械厂和兰州炼油化工设备厂合并而成,至今已走过60多年的辉煌历程。兰石集团是我国建厂时间最早、规模最大、实力最强的集石油钻采、炼化、通用机械研发设计制造为一体的能源装备大型龙头企业集团,2019年在中国机械工业百强企业排名第33名。
5.1 企业痛点与需求
内部制造过程缺乏协同控制,部分过程数据没有实现线上电子流,无法保证各车间各前置生产排程的一致性,无法及时了解生产现场的执行进度、在制品、质量等信息。
各系统和软件各自为战,信息化系统基础数据结构和接口设计不统一,集成困难,存在信息孤岛。
原系统业务功能单一,数据和流程覆盖不全,存在系统盲点;存在大量数据重复录入,工作效率低;工序复杂、工单数量庞大导致线上数据过于复杂。
5.2 方案设计
兰石集团通过与数码大方公司合作,进行总体规划,建立兰石集团统一的CAD/PDM/CAPP/MES/ERP信息化系统与研发、管理平台,实现兰石集团各子公司和全国基地、研究院的全业务集成贯通,实现分布式协同制造能力以及智能化产品研发、制造与管理基础。PLM与数字化工厂系统建设与应用紧扣四个协同的需求,在全集团建立贯通设计-工艺-制造的模块化管理模式、建立贯通销售、设计、工艺、采购、质量、生产、售后各业务环节的产品全生命周期协同模式、建立全业务规范化、数字化、智能化、无纸化制造的应用模式。系统核心涵盖数字化研发、数字化工厂两部分。
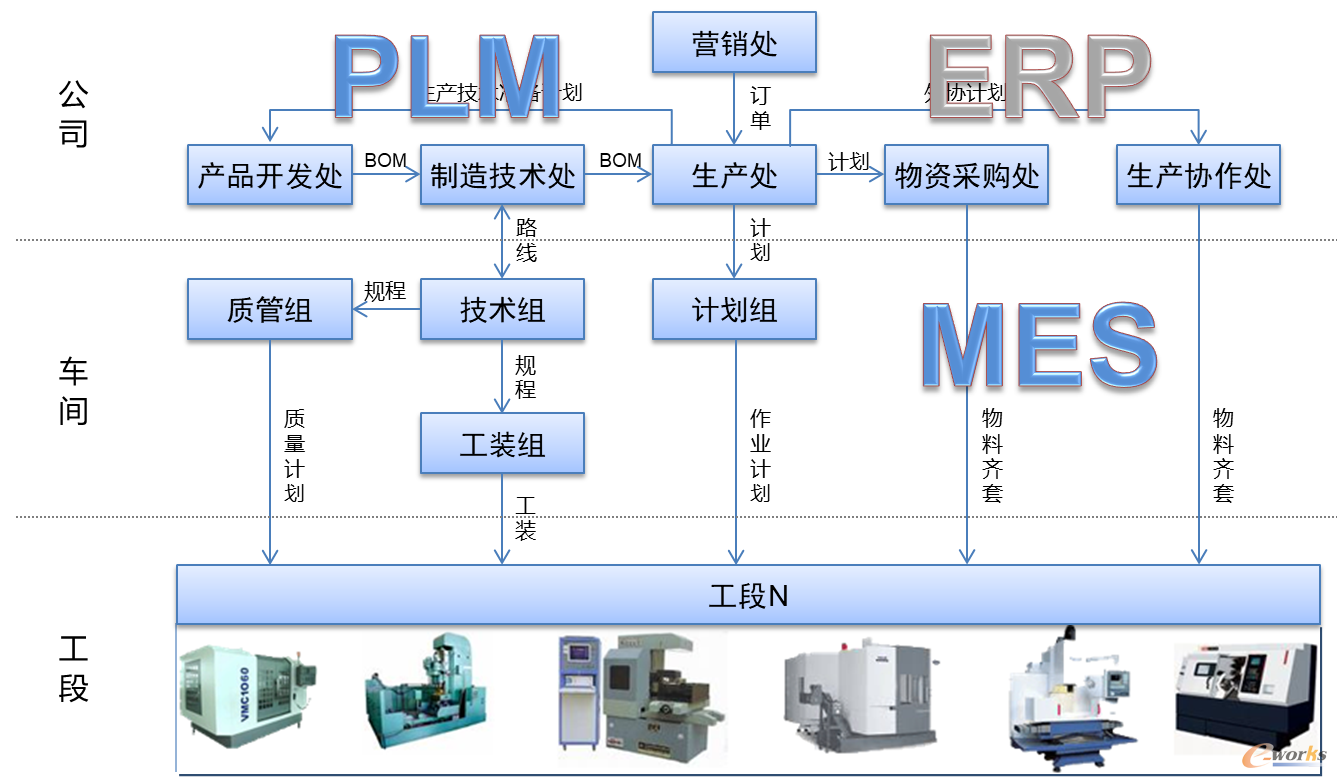
图2 兰石集团实现一体化集成体系
●数字化研发PDM/CAPP
产品研发与工艺的数字化:通过模块化、参数化等技术及三维CAD、PDM、CAPP系统的应用,建立标准规范的技术体系,使得产品及工艺设计实现从传统的图纸传递向数据传递的转变,不仅将技术人员从繁琐重复的劳动中解放出来,极大的提高工作效率,而且可以实现知识资产积累,做到知识共享与快速传递。
●数字化工厂DNC/MES
智能化生产:建立覆盖全部生产车间的从DNC设备透明到MES过程透明,到与ERP闭环优化的应用体系,通过计划、库房、采购、检验各环节对物料的全过程跟踪,保证生产用料的配套性,为及时交货打基础。
通过与设计工艺的一体化集成,实现对材料、加工、装配、焊接等检验的全过程控制,杜绝漏检、错检。
通过对产品过程数据的及时有效采集及各业务流程关键节点的有效管控,提高计划的可执行性,实现对各级人员的科学考核,真正发挥计划的核心作用。通过各业务流程环节的全面贯通及生产现场的实时监控,基于互联网,不仅实现覆盖产品全生命周期的全过程质量追溯,而且企业各级领导以及用户可以在任何时间、任何地点,查看产品生产情况,为领导决策提供及时、准确、有效的依据。
5.3 方案对客户的价值
●实现现代化企业的运营管控
实现计划优化、可视化生产现场管理、高度透明的生产展示和全过程质量追溯、全面的数据集成;实现信息充分共享、完善的信息统计分析,满足不同角色业务活动的需要;实现动态感知、实时分析、多要素透明可视、及时高效处理问题、业务决策智能辅助、作业精准执行,满足车间生产管控、健康监视、高效运营的要求,减少生产过程中计划、执行、保障等环节的问题,保证整体生产节拍,实现生产质量的全面管控。
●形成完全集成的一体化集成体系
制造执行系统(MES)、其他业务系统(PLM、ERP、CAPP)等数字化应用环境的集成,实现设备、车间、企业级的垂直集成。构建运营集成应用使能平台,封装流程、权限等基础服务,建立安全可靠的各应用集成的通用服务封装方式。
●实现制造过程的监控协同
面向运营、工艺、生产、保障等环节,基于垂直集成后的应用使能平台,根据管控维度及角色构建相应的监控视图,实现生产过程中多要素的可视化动态展示、生产问题及时处理及追踪等。
●实现数据的统一、规范化管理
对生产过程所需的BOM数据、工艺数据、计划数据、资源数据以及设备运行状态数据、质量数据等进行统一管理,后续逐步向建立技术、质量、问题方案知识库,提高数据的规范化水平和重用效率。
6 结论
大型成套复杂装备的网络化协同设计PLM系统理是以产品数据为核心,解决从用户需求、订单信息、产品开发、工艺设计、生产制造、维护维修整个生命周期过程中的不同类型数据管理、过程管理以及跨部门、跨区域和供应链协同工作的软件系统及解决方案。方案具有实施好,交付快,即时享有协同价值等优势,能帮助企业最大程度发挥产品数据的流通与重用价值,降低部门间的协同成本,提升协同效率。
本文为e-works原创投稿文章,未经e-works书面许可,任何人不得复制、转载、摘编等任何方式进行使用。如已是e-works授权合作伙伴,应在授权范围内使用。e-works内容合作伙伴申请热线:editor@e-works.net.cn tel:027-87592219/20/21。