以智能制造的柔性制造、高效传输、科学决策为导向,大型钣金冲压线体设计方案集成了先进的快速换模系统、废料自动处理系统、IFIX数据采集系统、工业机器人技术、大型伺服冲压设备、光电感应系统及智能化集中控制系统,前后端分别链接MES信息化管理系统和WCS智能化仓储系统,形成了高效的钣金冲压加工智能制造应用模式。
1.引言
客户市场的需求变化是决定企业未来发展方向的重要依据,随着时代的发展与世界文化交流的日益紧密,客户对制造业产品的个性化、多样化、功能维度融合化要求也在逐渐提高,各大设计软件层出不穷,功能日新月异,与之对应的是前端产品的快速更新换代,这就要求制造业企业在生产过程中要随时应对订单变化带了的生产资料切换问题。以钣金冲压加工行业为例,切换过程中主要涉及设备、模具、工艺、材料的切换,而传统的离散型生产模式容易形成孤岛作业,信息无法得到及时流通,不能有效帮助管理者快速决策,生产过程中各种浪费层出不穷,产品质量得不到稳定有效的保障,对于企业的发展极为不利。
为解决传统手工生产模式下的冲压线体切换低效问题,需结合先进的行业应用技术,开发更加先进的钣金冲压线体。近年来,随着钣金加工行业对MES系统、快速换模系统、废料自动处理系统、IFIX数据采集系统、工业机器人技术、大型伺服冲压设备、WCS仓储系统、光电感应系统及智能化集中控制系统的集成研究不断深入,各大先进软硬件的集成配置越来越全面地出现在新建的冲压线体,大连理工大学齐婉莎等学者对车间布局与生产排产过程中的精益化设计进行了系统地论述
[1],这对于智能化大型冲压线体的集成与建设具有重要参考意义。
2.应用背景
传统的冲压线体存在切换速度慢、生产效率低、工序周转次数多、产线人员密集等问题,线体信息化软件应用较少,模具切换系统、废料处理系统、信息化集中管理看板等各项配套不健全,制约着冲压车间生产层面智能制造发展。
离散型的资源配置,无法发挥其整体应用的最大价值,只有通过智能化改造升级,集成各项资源的优势,发挥资源的最大效能,才能促进整体生产效益的提升。因此,基于智能制造发展背景,项目通过集成快速换模系统、废料自动处理系统、IFIX数据采集系统、工业机器人技术、400吨大型伺服冲压设备、光电感应系统及智能化集中控制系统进一步开发基于快速切换理念的大型冲压线体,其前后端分别链接MES信息化管理系统和WCS智能化仓储系统,形成高效的智能冲压生产模式,线体生产模式配置如图1所示。
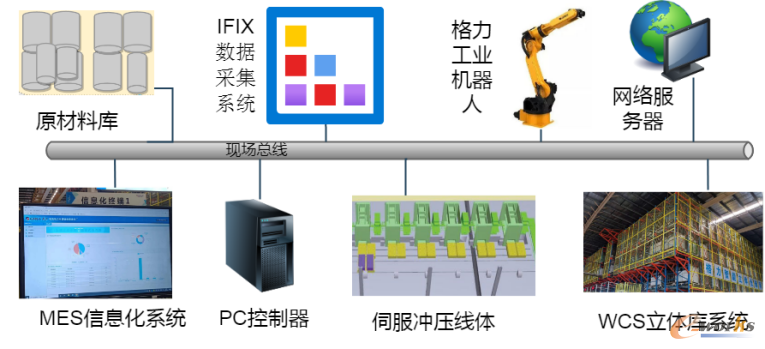
图1 大型冲压线体生产模式配置
3.智能化集成应用方案设计
精益化、信息化与自动化的融合应用是实现智能化生产的前提。冲压生产线以6台400t伺服冲压设备为基石,伺服冲压设备采用左右紧凑型的精益布局方式排列,为消除交叉物流,线体前端靠近原材料库,后端靠近立体仓库,整体实现精益一个流生产,线体配置了7台格力工业机器人,每台冲压设备之间和线体前后上下料端各配置1台工业机器人。线体的生产计划由MES系统直接下发,系统提前进行计划预排,以便原材料与模具的提前准备,减少内部切换时间,模具采用一键切换的自动换模台车,片料站采用一备一用可快速切换,针对不同的零件,工业机器人控制系统提前调试好了动作程序,一切信息准备就绪后,由PLC集成数字化控制系统进行各大硬件的联动控制。冲裁过程中产生的废料落到设备地基中间的废料传输装置,由地下输送线统一回收到废料站,零件则按照固定节拍下线输出,经装笼打包送入WCS立体库。整个生产过程采用光电传感器、计数器、红外扫描装置进行数据的采集,由IFIX系统进行集中处理显示,方便管理者进行远程监控与异常的快速响应处理,智能化冲压线体集成架构如图2所示。
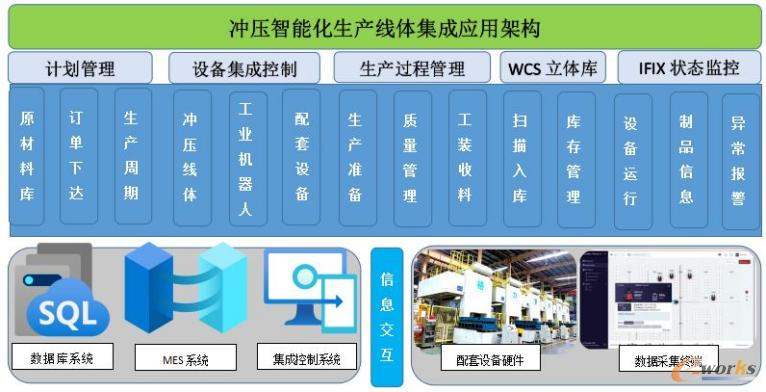
图2 智能化冲压线体集成架构
4.冲压线体硬件配置
4.1 伺服冲压设备的应用
伺服压力机作为一种高精度高技术水平的现代化冲压设备,其在多设备联动集成的应用优势显而易见,是实现冲压智能化生产的基础支撑。6台400T伺服冲压设备组成的伺服冲压线采用系统集成控制的方式,各设备通过冲压控制信号系统形成连贯的同步动作,通过PLC控制系统与工业机器人控制系统进行联动,保障钣金零件的顺利传输,同时PLC系统通过现场总线与IFIX系统进行信息交互,线体各设备信息及生产状态信息均实时传输到终端显示页面,大智能化冲压线体集成应用如图3所示。
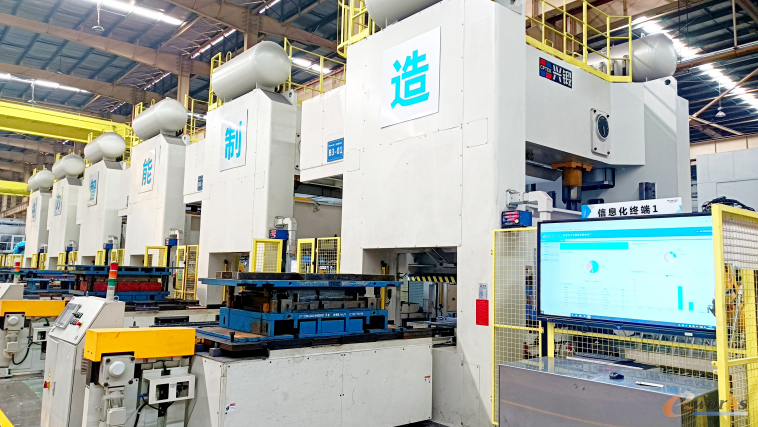
图3 智能化冲压线体集成应用
伺服压力机的核心技术为伺服电机控制及其整体控制系统,伺服电机与传统步进电机相比,运行过程中能够提供更加精准的转速及位置控制,在驱动技术、节能环保、精确控制等方面均有巨大优势,由伺服马达驱动的压力机,冲压力直接由伺服马达的扭力输出转变而成,低速大扭矩伺服电机和齿轮实现直接驱动,减少了中间传动变速环节,确保传动过程的可靠性和能量转换效率。伺服电机系统带有有运行监测装置,实时监测伺服电机的工作状态,保障异常能及时被发现报警,冲压过程中通过光电感应系统,实时监控钣金零件的生产状况,对异常的钣金零件偏移问题及时进行报警停机,信息推送通知绑定的技术人员进行处理。
4.2 工业机器人的应用
工业机器人的应用,以推动高速高效自动化生产为目标,配合高速伺服冲压设备,实现冲压设备的生产联动。线体搭载格力自主开发的GR系列工业机器人,不同类型零件切换过程中只需要在系统选定对应的动作程序,更新端拾器的挡块与吸盘位置,即可实现线体传递方式的快速切换,最大程度上减少了内部切换工作,提升了设备整体稼动率。基于工业机器人的不同产品的夹具进行通用化设计,且在线边放置,每类零件均提前进行示教调试,当线体硬件准备完毕后,可针对生产需要进行一键切换动作程序,人工只需对动作精度进行检测,对有偏差的动作稍作调整即可,减少了对机器人调试员的技术要求。通过工业机器人实现线体板料的传输供应,板料切换由左右磁力分张台车完成,台车自动开进开出、自动定位。
工业机器人的应用实现了线体伺服冲压设备之间零件的自动传输定位及与设备联动生产,其多台机器人集中控制系统通过与PLC进行连接,可由PLC对信号进行统一调度集中处理,从而实现各配套系统的信号联动,达成高效、高质量保障生产的目标。
4.3 模具快速切换系统
模具快速切换系统可以实现模具一键切换,减少外部等待时间,提高作业效率,其主要包括自动换模台车、自动夹模器、氮气弹簧、光电感应、集成控制系统等装置,在启动模具切换时,各信号指令经过线体终端处理后传输到PLC集中控制系统,待所有切换条件满足即可实现模具的自动切换。
自动化换模系统是整个方案布局的关键内容之一,模具采用一备一用的方式,人工可在线体生产时提前准备模具,每个模具需经过前后台车工位及里外设备传输工位,共3个位置状态。不同钣金零件需要切换模具时,集中控制系统发送可以换模的信号到自动换模装置,随即进行模具的自动切换,系统在发出信号时至少要具备以下条件:设备滑块开到下死点位置、设备内上/下模具夹紧器松开、设备滑块返回上死点,在接收到换模完成信号之前,滑块不能进行冲压性运动、压机内模具辊道上升完成,自动化模具切换控制系统如图4所示。
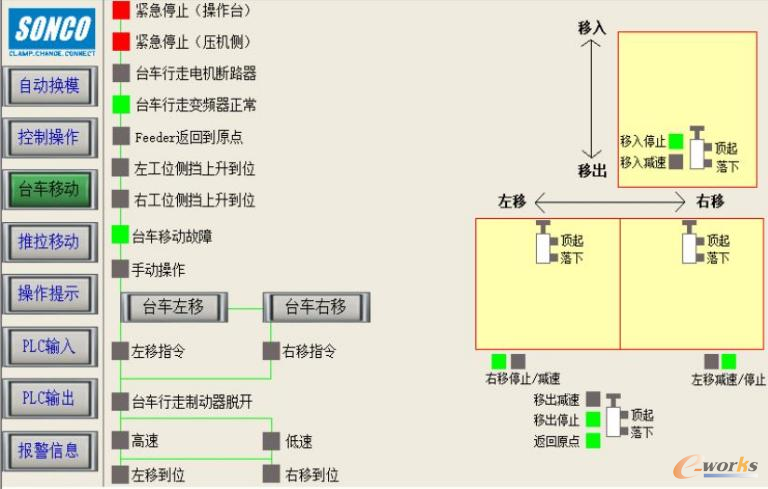
图4 线体模具快速切换控制系统
5.设备状态信息采集系统
设备状态信息采集基于工程组态软件,线体各项数据联通交互均在屏幕可视化管理,并运用COM/DCOM、VBA等一系列工业标准技术,实现所有的应用组件都可以无缝集成到一个系统中,通过中间接口技术,与MES系统、PLC控制器等进行信息交互,耿乙文等学者对一种采用iFIX技术的软件系统与关系数据库通信方式实现进行了相关研究,这对线体信息化管理中组态软件iFXI技术的应用起到了重要指导作用
[2]。线体应用的组态软件信息交互过程管理结构如图5所示,管理者可依据组态软件的实时监控信息对生产中的问题进行提前预判与干涉,减少线体生产过程中的故障发生,提高线体稳定性。
应用工业组态软件,通过图形化工具直观地建立面向设备状态的实时窗口,生成容易操作和理解的画面,在运行和组态环境之间可快速地完成测试和对画面的修改,同时保持实时报警和数据采集,并通过PLC数据、光电感应装置进行集中处理反应,实现对生产过程中线体各项参数的监控,以及快速配置生产所需的相关工装、模具、原材料,减少线体的停机等待,实现快速切换。实际过程可通过进一步系统开发拓展模块,对系统现有的数据采集和监控状态进行改进,以应对公司订单的战略性调整或周期更替变化,且拓展部分与原有的数据不冲突,可将已有标准化的数据部分备份保留,随时启用。
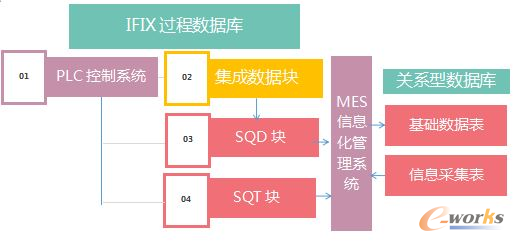
图5 设备状态管理数据交互结构
6.信息化管理系统的应用
面对当前订单复杂、产能有限的生产情况,通过MES系统准确地进行计划的预排与生产资料的提前准备,通过WCS智能立体仓储系统实现物料的自动出入库管理,并能够反馈实时库存数据,以指导生产计划的精准最大限度减少在制品的库存量。
结合现有订单生产模式和资源配置开发家用钣金MES排程系统,线体的订单由家用钣金MES系统依据相关约束条件和排程逻辑下达到信息控制中心,订单信息包括零件编码、零件数量、原材料编码、原材料规格、模具编码(可跳转到模具位置查询)、图文信息、加工工时等基础信息。考虑到产品切换等待问题,线体的生产任务采用一备一用,即MES系统同一时间指派了两个订单,前一个订单为在制订单,后一个为预备订单,在制订单完工后,预备订单则自动转为在制订单。预备订单在3天周期内的上线订单库里面进行择优筛选,其筛选条件则通过对比在制订单的零件编码、原材料编码、模具位置、工装编码等关键信息,周期内同编码零件订单进行合并生产,并通过计数器采集合格零件的下线数量,提醒班组长进行订单区分入库,同时对不同零件编码的订单按照相关性矩阵排布,得出最优预备订单,最大程度减少了生产资料的切换。按照与在制订单同时MES与WCS交互模块调度立库下达原材料出库任务及上个订单原材料入库任务,开始进行加工前准备,通过订单交叉运行,减少内部切换时间,减少机床待机,提高设备稼动率,最终实现高效生产。
7.小结
面对日益复杂的现代化市场需求发展,制造业需要更加柔性化的生产应用模式来实现订单的快速交付,而智能化大型冲压线体的集成应用,整合了工厂的优势资源,通过信息化系统、自动化装备的集成应用,形成了高效智能化的钣金冲压生产应用模式,是国家智能制造发展背景下的制造业典型生产应用模式。
参考文献
[1]齐婉莎.基于精益生产的某车间设备布局与排产研究[D].大连:大连理工大学,2017.
[2]耿乙文,伍小杰.基于IFX技术的软件与关系数据库通信[M].北京:机械工业出版社,2005.
本文为授权转载文章,任何人未经原授权方同意,不得复制、转载、摘编等任何方式进行使用,e-works不承担由此而产生的任何法律责任! 如有异议请及时告之,以便进行及时处理。联系方式:editor@e-works.net.cn tel:027-87592219/20/21。