本文通过Altair公司的OptiStruct软件中的形貌优化技术对钣金舱门进行优化设计,并对其优化结果与机加舱门进行比较。分析结果表明,钣金压窝成形相比机加成形舱门,在刚度无明显变化的条件下,重量减少49.3%,达到了优化设计的目标。
1 概述
某型飞机舱门位于飞机尾部双曲面舱段的底部,需在空中设备作业时打开,因为空气动力及舱门机构的要求,需要舱门门体满足足够的刚度和轻量化设计。机加成形的舱门虽能满足所要求的强度、刚度等条件,但由于制造工艺复杂,制造成本高,制造周期长,使其成为影响整个舱门系统研制进度的原因之一。通过对钣金零件进行优化,使其能满足机加零件的刚度特性。
Altair公司的OptiStruct软件作为一款面向产品设计、分析和优化的工具,提供了先进、全面的优化方法,目前已广泛应用于飞机结构设计中。常用的结构优化技术有拓扑优化、形貌优化、尺寸优化、自由尺寸优化、形状优化和自由形状优化等技术。形貌优化是一种形状优化的高级形式,即在钣金件结构中寻找最优的加强筋分布的概念设计方法,用于设计薄壁结构的强化压痕,在减轻结构重量的同时满足强度刚度等要求。形貌优化的特点是不删除材料,而在设计区域中根据节点的扰动生成加强筋。
本文正是应用OptiStruct软件的形貌优化技术对钣金舱门进行优化,寻找加强筋的位置分布及形状,并将优化后的舱门刚度强度分析与机加成形舱门进行对比。
2 形貌优化设计流程
形貌优化是在已有的钣金零件上寻找加强筋,使其刚度增加。OptiStruct软件进行形貌优化的流程为:
(1)在CATIA中建立结构的几何模型;
(2)将CATIA模型导入HyperMesh,并建立有限元模型,赋予相应的材料和属性;
(3)对有限元模型设置载荷和边界条件,建立相应的载荷工况;
(4)设置形貌优化参数,包括定义优化设计变量及设计空间(可设计区域);定义用于评测目标函数和约束条件的响应;定义优化设计约束和目标。
(5)运行Optistruct进行形貌优化分析。
(6)验证结果。
具体优化的流程如图1所示。
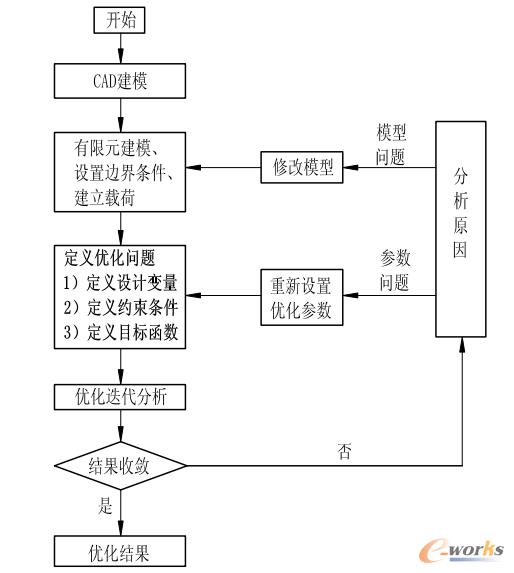
图1 优化分析流程
3 舱门的形貌优化设计
(1)对机加零件进行分析
舱门机加零件如图2所示,尺寸为700mm×350mm,重量为4.195Kg,其肋为田字分布,两侧的空余部分为与接头的连接区域。舱门底板厚度为3mm,肋板厚度为5mm。其材料为7050-T7451,材料属性为E=72000N/mm
2,μ=0.33,ρ=2.8×10
-9Ton/mm
3。对零件进行有限元建模,设定约束条件,增加载荷,建立相应的工况。图2的CAE模型中黄色部分为约束,载荷为沿蒙皮法向向外的均布载荷。应用OptiStruct进行有限元分析,并通过HyperView查看结果。
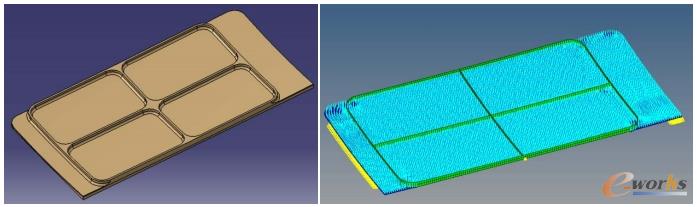
图2 舱门机加零件CAD及CAE模型
由图3分析结果得出,舱门最大变形为0.907mm,最大应力为39.58MPa,满足刚度强度要求。但由于其处于飞机双曲面舱段,制造复杂。
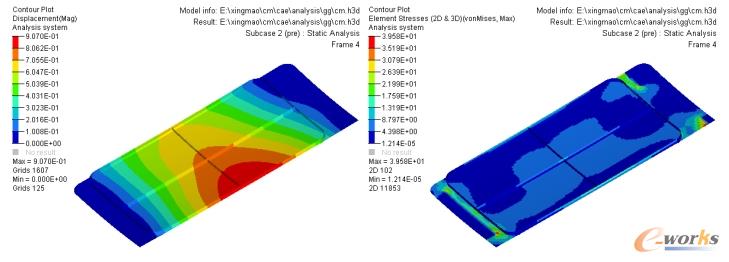
图3 舱门机加零件分析结果
(2)钣金零件形貌优化
将舱门设计为由内外蒙皮铆接而成的组合件,厚度均为1.5mm,材料均为2A12-O,在内蒙皮上寻找肋的凸起位置及形状。在CATIA建立CAD模型,并导入HyperMesh中,合理划分有限元网格。根据机加件形状及实际制造工艺,在内蒙皮上设置设计区域和非设计区域,赋予相应的材料属性,施加与3.1节中相同的约束、边界条件及载荷工况。如图4,其中黄色区域为内蒙皮寻求加强筋的设计区域,蓝色区域为内蒙皮非设计区域,绿色零件为外蒙皮。由图3可知,在舱门肋包围部位,应力和位移都很小,所以可将钣金内蒙皮设计区域寻求肋的包围部分挖空,其挖空大小根据装配的防差错设计由零件所处框位决定。
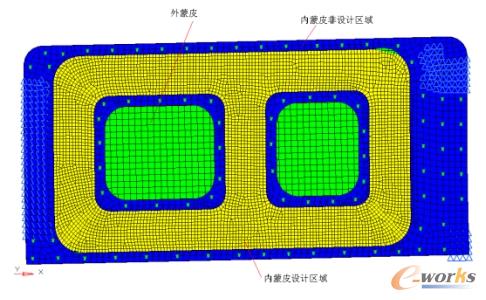
图4 钣金零件的CAE模型
进入HyperMesh中面板Analysis-optimization-topography,创建设计变量,设置优化参数,如图5。其中设计区域的网格大小为5,由minimum width定义为平均网格大小的1.5~2.5倍,设置最小宽度为10。拔模角度和拔模高度根据制造工艺及经验分别设置为60°和35。
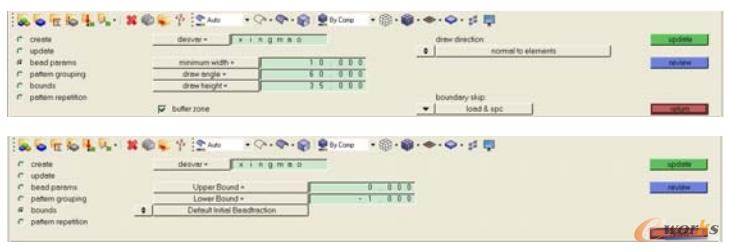
图5 形貌优化设置参数
创建位移和应变能的响应。根据图3的变形结果及实际要求,设置图6中节点位移的upper-bound为1;设置的优化目标函数为零件的应变能最小。
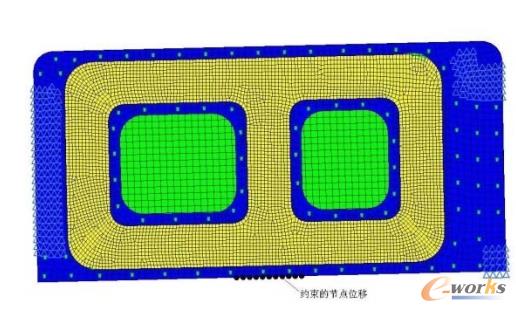
图6 设置约束图
进入Analysis-OptiStruct面板提交计算,当出现OPTIMIZATION HAS CONVERGED时,优化结束,通过HyperView查看结果文件。
优化计算经过27步迭代完成,结果如图7所示。
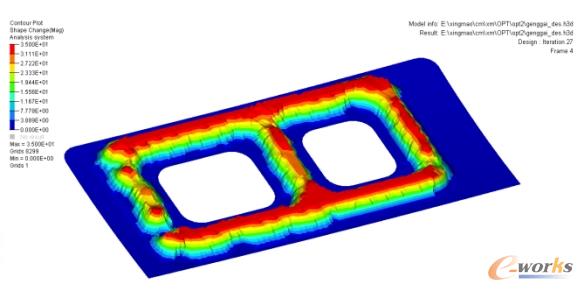
图7 形貌优化结果
(3)优化结果的读取与分析
对图7的优化结构进行分析读取,结合实际制造工艺情况。建立优化后的CAD模型,如图8。将优化后模型导入HyperMesh,建立有限元模型,施加同3.1节相同的约束、边界条件和载荷工况,重新应用OptiStruct进行有限元分析,应用HyperView查看结果。结果文件如图9所示。
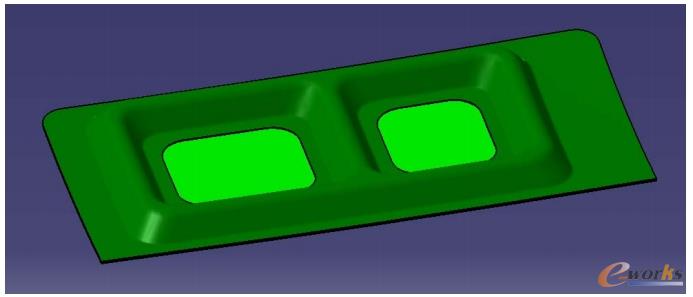
图8 优化后舱门CATIA模型
由图9可以看出,优化后模型的最大变形为0.802mm,最大应力为62.8MPa,与机加件的计算结果相比,变形减小0.105mm即减小了11.6%,刚度得到了增强;应力增加22.22MPa,但远小于材料的极限应力。同时优化后模型重量为2.126Kg,重量减轻了49.3%,达到了增加刚度、减轻重量的优化目标。
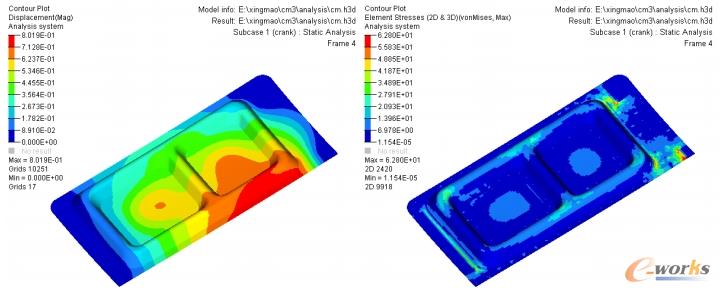
图9 优化后模型计算结果
4 结论
本文应用OptiStruct软件中的形貌优化技术对钣金舱门进行了优化,得到了加强筋的位置分布及形状,优化结果不仅使舱门增加了刚度、减轻了重量,也使舱门的制造工艺方法大大简化,缩短了研制周期,节约了制造成本。结果表明,OptiStruct优化技术能够为工程设计人员提供结构概念性设计及详细设计方法,有助于提高工程设计人员的设计水平和工作效率。
5 参考文献
[1]张胜兰,郑冬黎,郝琪,李楚林等.《基于HyperWorks的结构优化设计技术》. 北京:机械工业出版社,2007.
[2]洪清泉,赵康,张攀.OptiStruct&HyperStudy理论基础和工程应用[M].北京:机械工业出版社,2013.
[3]牛春匀编.实用飞机结构设计[M].北京:国防工业出版社,1991.
本文来源于互联网,e-works本着传播知识、有益学习和研究的目的进行的转载,为网友免费提供,并以尽力标明作者与出处,如有著作权人或出版方提出异议,本站将立即删除。如果您对文章转载有任何疑问请告之我们,以便我们及时纠正。联系方式:editor@e-works.net.cn tel:027-87592219/20/21。