Suzaki对精益改善的不懈追求,赋予了这家小型汽车零部件企业强大的生命力,使其在面临破产危机时成功逆转局面。通过极致的精益管理和对丰田TPS的深刻理解,让Suzaki在没有大量信息化投入的情况下,依然能够保持高效的生产运转。这不仅是精益生产的成功案例,也是小型企业在资源有限的情况下,通过创新和坚持不懈的努力,实现卓越制造的典范。
2024年6月24日上午,e-works 第八届日本精益制造考察团参观了Suzaki株式会社。作为丰田的供应商,Suzaki很早就接受了丰田生产方式(TPS)的指导,通过不断地进行精益改善,能完全按照车企的节拍生产配套零部件而不积压库存,并将快速换模和看板管理做到了极致。公司前任董事长鷲崎幹夫老先生热情接待了考察团一行,亲自为团员们讲解了Suzaki的精益生产实践,并带领考察团参观了生产现场。
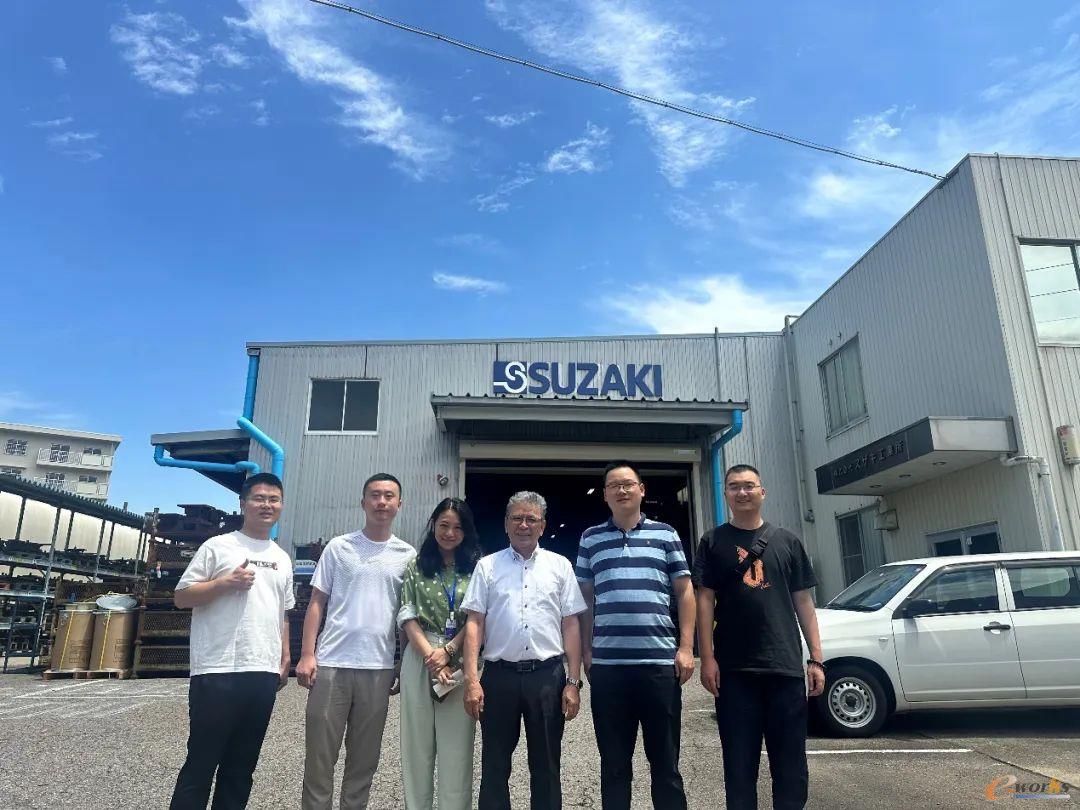
鷲崎幹夫先生(右三)与考察团合影
Suzaki是一家小型汽车零部件企业,产品线包括冲压成型、焊接和零部件组装等环节。大约70%的产品是为丰田系配套,主要客户包括丰田岐阜汽车车身公司等。该公司占地面积约4500平方米,员工60名。
在日本泡沫经济破裂的艰难时期,Suzaki公司面临破产的危机。然而,在时任董事长鷲崎幹夫先生的领导下,公司实施了丰田TPS,建立了高效的生产流程,坚持不懈地努力消除生产过程中的浪费,并不断进行改进,得益于这些努力,公司最终扭转了颓势,成功在激烈的市场竞争中生存下来。
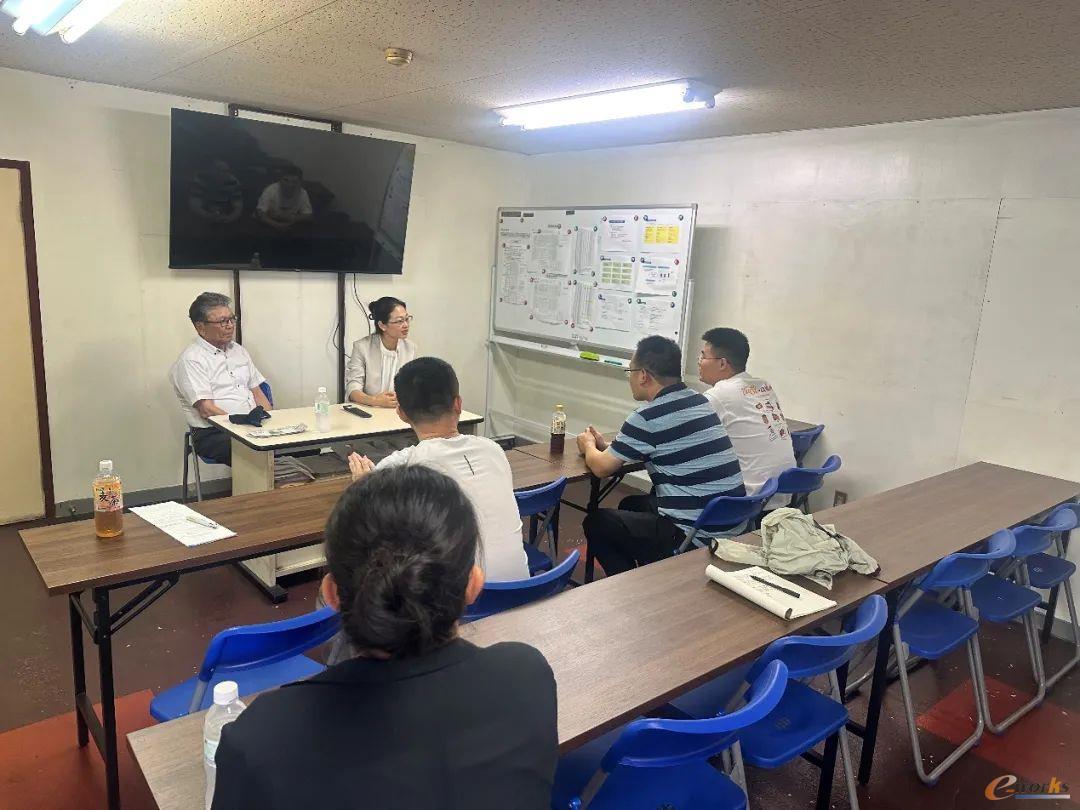
考察团成员与鷲崎幹夫先生交流
1 看板是Suzaki最引以为傲的精益实践
在e-works考察过的众多制造企业中,不少企业应用了信息系统来管理生产,但在Suzaki工厂,考察团的成员注意到,并未看到太多的信息系统和显示屏。相反,展现在团员眼前的是各种看板卡片,这些卡片被插在箱子或者小格子里。卡片上的内容简单明了,有的是双面的,正面标记了箱子的种类、数量、客户编码,反面则显示了工厂内部的编码和物料图片等,相当于带着图片的物料编号;有的卡片上可以粘贴数字,对应的是动态库存。
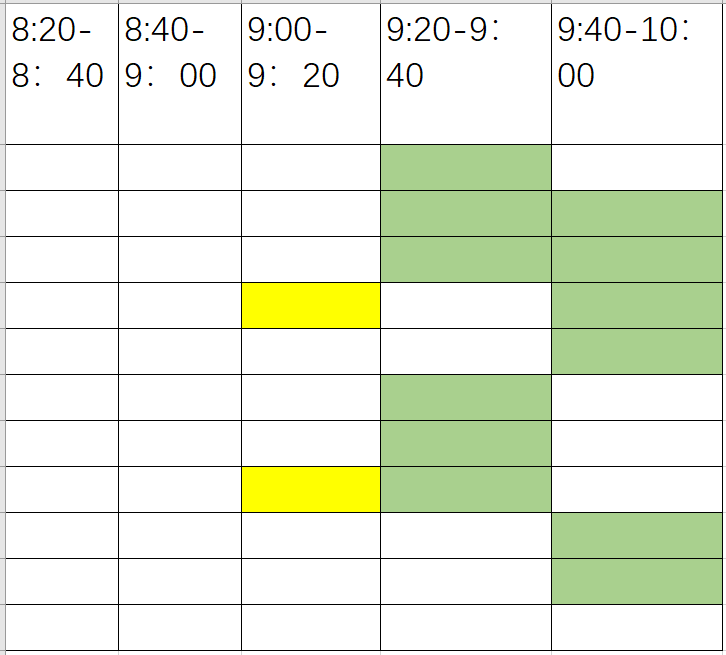
Suzaki小格子示意图
在车间里,团员还看到了有很多小格子的塑料架,这种架子可以到处移动,但是它并不是物料车,而是一个移动的看板架。在这个架子上,一个个小格子将看板架分成了几十甚至上百块,每个格子里都放着若干卡片,最上层则是时间表。举例来说,当架上的时间是9点20时,若是这一列的格子里还有卡片,则说明有工序没有完成,因为每当完成一个工序,卡片就会被抽走,附在完工工序的箱子上。当格子里还有卡片出现时,班组长就会审视问题,并及时解决。
这样一目了然的做法是在几十年前信息系统还未普及的时候就开始了,这样的小方格在Suzaki工厂里有好几个,它们各自关联,形成了一个完美的闭环。小格子+看板卡片的形式让生产过程不需要信息系统的参与,就能做到计划排产和追踪产品信息。对于员工而言,由于这种做法一目了然,并且不必参与太多的信息化培训,很快就能上岗作业。
值得一提的是,该企业能用原始的看板完成工作,还要得益于客户的准确计划。丰田的TPS生产不仅帮助自己做到极致精益,同时也让其供应商们一齐提高了精益水平。Suzaki公司在生产前三个月内得到的丰田订单,准确率大概在90%,而在生产前的一个月内可以拿到近100%的准确计划。正是由于上游客户订单的准确性,才能让 Suzaki做出符合节拍的小格子来满足生产节奏。
对于类似Suzaki这种规模较小的企业,信息系统的建设和维护本身就需要人员的和资金的投入,在产品数量不多,产能固定的情况下,这样极致的精益,同样可以替代一部分信息系统以保证整个生产的高效运转。
2 一秒换模给柔性生产提供了可靠保障
鷲崎幹夫先生谈到,为了达到终极的Just In Time,即按照客户的节拍去供货,同时又不让自己有过多库存,Suzaki工厂建立了柔性生产模式,一个柔性屋台里(柔性生产单元),可以生产多种产品。以汽车座椅框架的生产为例,为了加工不同尺寸的汽车座椅架,在这个柔性生产单元内,就需要实现模具的快速反复切换,只有减少换模时间,才能在客户要求的时间内完成订单。为了达到SMED(快速换模),Suzaki的模具都是由Suzaki的研发人员,根据加工机台、加工方式和人员操作特点来设计的,这样的模具能在一秒钟之内就迅速换好,为Suzaki实现柔性生产提供了有力支撑。
3 Poka-Yoke(防呆防错)保证产品质量
Poka-Yoke是精益制造过程中运用的一种技术,用于防止人为错误,实现零缺陷质量控制,并实施安全措施。在Suzaki工厂,考察团员没有看到专门的质量检测的环节和人员。鷲崎幹夫先生解释说,这是因为员工的培训过程中,产品操作手册已经明确包含了质量检测的标准,要求员工在操作过程中确保不合格的产品不会传入下一道工序,从而有效预防了质量问题的发生。
同时,Suzaki还将检查分为连续检查、自我检查和根源检查。连续检查是下道工序的操作员立即向上道工序反映问题,停止生产改正错误;自我检查是操作员自己对工作进行检查;根源检查则是操作员检查那些还未铸成大错的小问题。Poka-Yoke的核心就是把一个个小问题逐一解决,从而寻找到问题的根源,杜绝问题的发生。
考察团员们在参观时还注意到,在焊接的过程中,所有需要的焊头都会按照顺序摆放好,这样能提高焊接的效率。在参观焊接座椅前后调解管的单元时,鷲崎幹夫先生还介绍了一个精益的小案例。由于塑料储货箱的熔点低,焊接后的管子温度较高,放在塑料箱里经常会将箱子融化。因此,工程师们根据箱子的熔点,算出焊接管的冷却时间,做了一个置物架,当置物架放满16个焊接管,就可以再逆序放进塑料储货箱里。这个置物架不仅可以冷却钢管,还能防止焊接错误,如果焊反钢管,就不能正确放入架子上,一举两得。相较于增加温度传感器或应用机器视觉防错装置,这样的做法,更为简单高效,且经济成本低廉,非常值得同类型的小型企业学习。
后记
在本次考察中,Suzaki株式会社的参观成为了难忘的一站。对精益改善的不懈追求,赋予了这家小型汽车零部件企业强大的生命力,使其在面临破产危机时成功逆转局面。通过极致的精益管理和对丰田TPS的深刻理解,让Suzaki在没有大量信息化投入的情况下,依然能够保持高效的生产运转。这不仅是精益生产的成功案例,也是小型企业在资源有限的情况下,通过创新和坚持不懈的努力,实现卓越制造的典范。
本文为e-works原创投稿文章,未经e-works书面许可,任何人不得复制、转载、摘编等任何方式进行使用。如已是e-works授权合作伙伴,应在授权范围内使用。e-works内容合作伙伴申请热线:editor@e-works.net.cn tel:027-87592219/20/21。