一、前期探讨
《工业软件与工业APP》主要介绍了工业软件和工业APP的概念及其在工业生产中的应用。
(1)工业软件
工业软件是通过代码表达工业相关业务逻辑的软件,涵盖了从产品设计到生产的各个环节。
在产品设计阶段,使用PLM(产品生命周期管理)系统来管理产品的设计、变更和相关数据;CAD(计算机辅助设计)、CAE(计算机辅助工程)和CAM(计算机辅助制造)等工具支持产品设计、仿真和制造过程。
ERP(企业资源规划)系统用于管理企业的资源,包括销售、采购、库存、财务等业务模块。
APS(高级计划与排程)和MES(制造执行系统)负责生产计划的制定和执行,确保生产过程的高效和可控。
SCADA/?skæd?/系统用于数据采集与监视控制,配合PLC(可编程逻辑控制器)实现设备的自动化控制。
(2)工业APP
工业APP是工业软件的新形态,运行在工业互联网平台上,具有微服务化和云化的特点,支持低代码开发。
工业APP主要由工业工程师使用低代码工具构建,聚焦于解决特定工业场景中的问题。
与传统的工业软件相比,工业APP更加灵活和易于定制,能够快速响应市场需求变化。
《工业互联网:工控安全》讲述了:
(1)工业控制系统的概念、关键组件(SCADA、DCS、PLC、RTU、FCS、IED、传感器与执行器)。
(2)以石油输送管道监控系统为例,说明了各组件如何配合工作。但缺少直观图示。
(3)标准
IEC 62443系列标准:全面的安全要求。
NIST SP 800-82:工业控制系统安全最佳实践。
GB/T 20281-2015:工业控制系统专用防火墙标准。
ISA/IEC 62443:工业网络安全标准。
NERC CIP标准:电力行业的关键基础设施保护标准。
API Standards:石油和天然气行业的安全标准。
IEC62264-1标准层次结构模型如下图所示,企业资源层、生产管理层多采用信息领域相关的通用技术,其他层多采用工业控制系统特有技术。
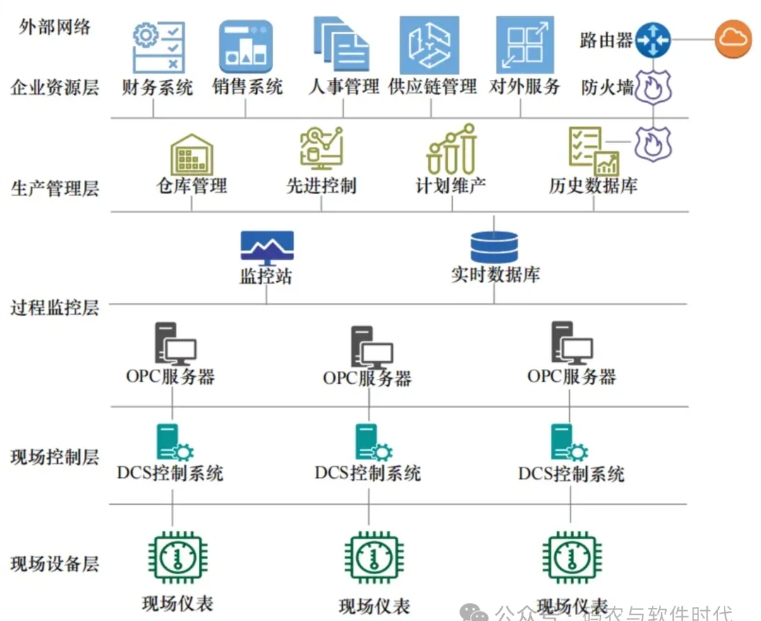
图1
二、工控系统
工业控制系统是什么?有哪些组成部分,各自的作用是什么?如何配合一起协作工作?
1. 基本信息
工业控制系统(Industrial Control System,ICS)是一种用于监控和控制工业过程的系统。其主要功能为数据采集、监视显示和控制执行。
工控系统的核心组成部分有:
(1)PLC(Programmable Logic Controller,可编程逻辑控制器)
(2)SCADA(Supervisory Control and Data Acquisition,数据采集与监控)
(3)DCS(Distributed Control Systems,集散控制系统)
(4)SIS(Safety Instrumented System,安全仪表系统):SIS是工业控制系统中的一个关键组件,通常用于确保生产过程的安全。SIS的主要功能是实现对生产过程的安全监控和控制。SIS可以连接到PLC,通过PLC获取生产过程的数据,并通过PLC发送控制命令。SIS可以实现对生产过程的安全监控和控制,帮助用户确保生产过程的安全和稳定运行。
(5)RTU(Remote Terminal Unit,远程终端单元)
(6)MTU(Master Terminal Unit,主终端单元):MTU是工业控制系统中的一个关键组件,通常位于中央控制室。MTU的主要功能是实现对生产过程的集中监控和控制。MTU可以连接到PLC,通过PLC获取生产过程的数据,并通过PLC发送控制命令。MTU可以实现对生产过程的实时监控和控制,帮助用户更好地管理和优化生产过程。
(6)HMI(Human Machine Interface,人机交互界面)
2. 概念澄清
有关DCS、SCADA、HMI的关系如下进行了解读:
(1)《DCS和SCADA》讲述了SCADA系统就像中枢神经系统,而DCS就像条件反射。两者可以有机结合在一起。而两者的区别在于:SCADA更适合需要远程监控和数据采集的场合,而DCS更适合需要高级控制逻辑和策略的复杂工业过程。
(2)《HMI和SCADA》说明了SCADA系统包括这些物理现场设备以及用于监控和控制这些设备的中央监控中心和HMI。而HMI是SCADA系统的一个组成部分,为用户提供了一个用户界面来与SCADA系统进行交互。
除了上述的概念之外,还可能会遇到上位机、下位机、操作员站、工程师站等。
(1)上位机和下位机通常用于描述控制系统中的不同层次。上位机通常指的是控制系统中的高级层次,如计算机、服务器等,它们负责处理和管理控制系统中的数据和信息。下位机通常指的是控制系统中的低级层次,如PLC、RTU等,它们负责采集和处理控制系统中的数据和信息。
(2)操作员站和工程师站通常用于描述控制系统中的不同角色。操作员站通常指的是控制系统中的操作员,他们负责操作和控制控制系统中的设备和过程。工程师站通常指的是控制系统中的工程师,他们负责设计和维护控制系统中的设备和过程。
还会遇到组态和组态软件。
组态一词来源于英语中的“configuration”,译为“配置”更为直接。但在工业自动化控制中,通常被译为“组态”,用于描述配置和管理控制系统中的设备和过程的方法。
组态软件是一种用于“配置”控制系统的软件,通常提供图形化的界面和工具,使得用户可以方便地进行组态操作。组态软件通常包括设备的配置、参数的设置、数据的采集和处理、控制逻辑的编写和实现等功能,可以提高控制系统的灵活性和可扩展性。
那么,组态软件和SCADA/DCS关系是怎样的?
SCADA和DCS是两种系统,它们通常使用组态软件进行配置和管理,可以提高控制系统的灵活性和可扩展性。
3. 基本结构
工业控制系统的基本结构如图所示。
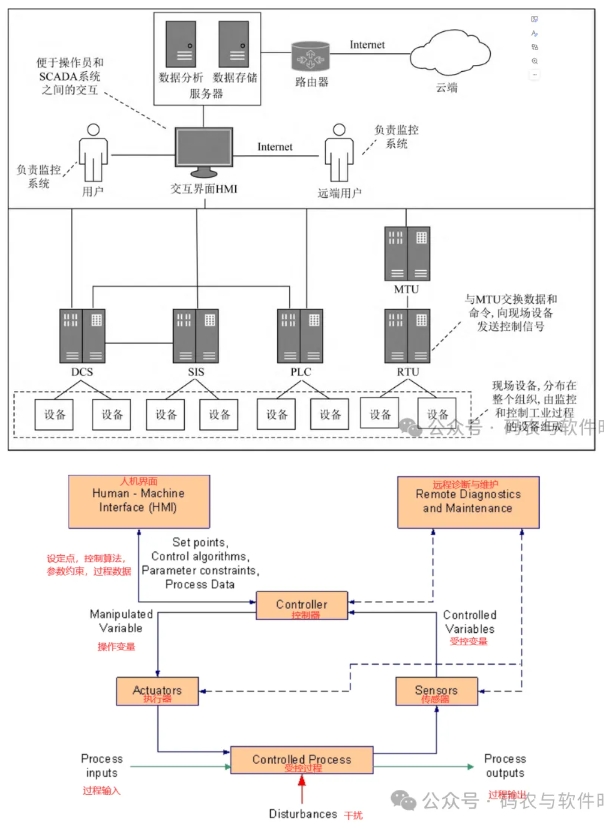
图2
三、PLC
1. 基本组成
PLC构成中核心为处理器、实时操作系统以及集成开发环境IDE(图片来自参考资料)。
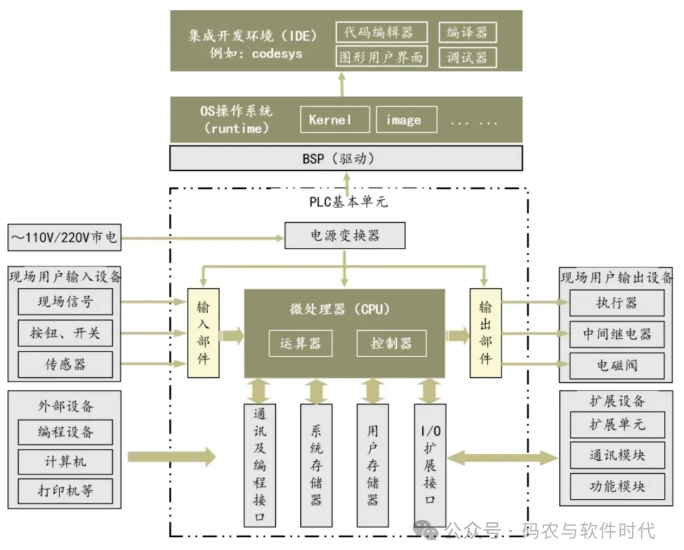
图3
PLC的设计注重实时性和可靠性,其架构如下:
(1)中央处理单元 (CPU):执行控制程序。
(2)输入/输出 (I/O) 模块:专门用于处理来自现场设备的信号。
(3)存储器:分别存储程序和数据,有时会使用非易失性存储器来保存程序和重要的数据,即使断电也不会丢失。
(4)通信接口:用于与其他设备通信。
2. 操作系统
PLC通常采用实时操作系统,主流的商业操作系统有:VXworks、Windows Intime等,开源操作系统有:Linux RT。
(1)VXworks:由美国风河公司开发,系统整体性能与稳定性高,市场占有率不到10%。
(2)Windows intime:由微软公司开发,系统整体性能与稳定性较高,市场占有率约20%。
(3)Linux RT(Real-Time Linux):开源实时系统,厂商必须具备较强的操作系统开发能力,市场占有率约70%。
3. PLC编程
PLC编程是为了实现工业自动化控制或满足特定的生产工艺要求,采用逻辑运算、顺序控制、定时、计数等操作对现场设备和生产过程进行控制。简单来说,我们购买的PLC就像是一台仅有基础操作系统的计算机,本身并不包含任何特定功能的应用软件。通过编程,我们可以将控制程序写入PLC中;当PLC运行这些程序时,就能实现对现场设备的有效控制。
PLC编程语言可分为图形化语言和文本化语言。其中,图形化语言又分有梯形图(Ladder Diagram,LD)语言、功能模块图(Function BloeDiagram,FBD)语言和顺序功能流程图(Sequential Function Chart,SFC)语言。文本化语言又分为指令表(InstructionList,)语言与结构化文本(Structured Text,ST)语言。
四、SCADA
SCADA系统的发展历程如下:
(1)20世纪70年代,使用专用计算机和专用操作系统。
(2)20世纪80年代,使用通用计算机和UNIX操作系统。
(3)使用分布式计算机网络和关系数据库,具有更高的数据处理能力和数据存储能力,可以更好地满足工业自动化控制的需求。
SCADA系统的实现通常是Web应用,也就是通过Web界面进行前端显示(数据采集与系统监控)。
五、DCS
DCS系统通常包括HMI、现场仪表、PLC等。
六、新一代工控体系架构
《面向工业智能化时代的新一代工业控制体系架构》白皮书中指出,工业生产体系架构正从传统的ISA-95五层金字塔架构演变为以“计算”为中心的云/边/端三层体系架构。
在“云/边/端”这一架构下,
L3的MES和L4的ERP、PLM等软件系统将迁移至云端。
SCADA系统的实时展示设备的状态和数据等功能,将与数字孪生技术相结合,形成更强大的可视化系统;而SCADA系统的现数据采集与预处理、实时决策与控制、生产过程优化和异常检测等功能,将与边缘计算相结合,形成工业控制的边缘层。
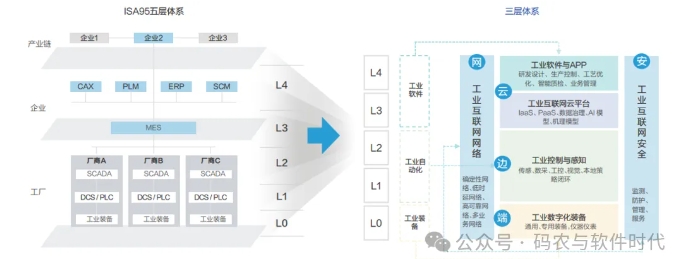
图4
新一代工控体系架构以“计算”为核心,服务于“数据流转”。它涵盖了从工业现场数据采集,到边缘层数据预处理及多维信息融合,再到云端智能应用的全过程,确保数据能够无缝流转。
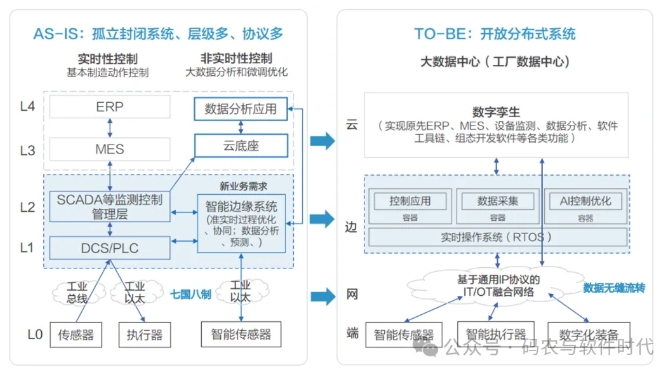
图5
图中的“七国八制”指的是工业现场中使用的多种不同的通信协议和标准,这些协议和标准在不同的设备和系统之间存在不兼容性,导致数据交换和集成的复杂性。
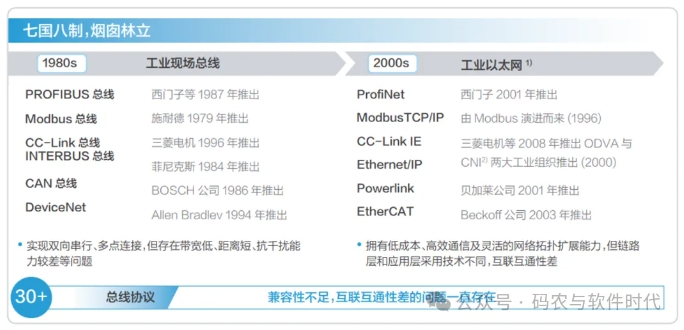
图6
基于通用IP协议的IT/OT融合网络则是指通过采用统一的IP协议,实现信息技术(IT)和操作技术(OT)的融合,从而简化网络架构,提高数据的无缝流转和系统的开放性。
这意味着在工业控制系统中,无论是IT设备(如服务器、交换机等)还是OT设备(如PLC、传感器、执行器等),都使用IP协议进行通信。
然而,实现基于通用IP协议的IT/OT融合网络是一个复杂的过程,需要长期的努力。
总的来说,新一代工业控制体系将发生如下变化:
(1)在架构上,正演变为以“计算”为中心的云/边/端三层体系架构。
(2)在网络技术上,确定性网络(DetNet、TSN)、带宽升级。
本文来源于互联网,e-works本着传播知识、有益学习和研究的目的进行的转载,为网友免费提供,并以尽力标明作者与出处,如有著作权人或出版方提出异议,本站将立即删除。如果您对文章转载有任何疑问请告之我们,以便我们及时纠正。联系方式:editor@e-works.net.cn tel:027-87592219/20/21。