本文为“2024年度中国智能制造最佳应用实践奖”参评案例。本次活动将评选出2024年度,为中国智能制造领域带来突出效益的最佳实践工程,全面介绍企业推进智能制造的步骤、重点与难点、获得效益等,分享建设过程中的经验,供广大制造业行业企业学习供鉴。
一、企业简介
广汽传祺汽车有限公司是广州汽车集团股份有限公司(简称广汽集团)的全资子公司,成立于1997年6月,总部位于广州市天河区珠江新城,是国内首家实现A+H股整体上市的大型国有控股股份制汽车集团,总市值超过1,000亿。面对2030年,广汽集团力争成为智能新能源汽车领域的世界一流科技企业。
广汽传祺是广汽集团为提升核心竞争力,实现可持续发展而打造的国产品牌,主要致力于生产销售具有国际先进水平的传祺品牌整车。围绕品牌高质量发展理念,广汽传祺主动适应国家经济发展新常态,抢抓行业发展新机遇,打造高品质产品,走出了一条“品牌领先、品质驱动,持续高质量发展”的道路。
二、企业在智能制造方面的现状
广汽传祺是广汽集团为提升核心竞争力,实现可持续发展而打造的国产品牌,主要致力于生产销售具有国际先进水平的传祺品牌整车。围绕品牌高质量发展理念,广汽传祺主动适应国家经济发展新常态,抢抓行业发展新机遇,打造高品质产品,走出了一条“品牌领先、品质驱动,持续高质量发展”的道路。
在“碳达峰”“碳中和”的大背景下,广汽集团发布“NEXT计划”,围绕能源科技、智能出行及产业集群,打造三大生态支撑。
承接集团计划,广汽传祺确定了“电动化+智能化”双核驱动发展战略,吹响二次创业转换新能源赛道的冲锋号。
经过10余载的技术沉淀,通过开放合作和自主研发,传祺成为唯一拥有双混动技术路线的品牌。一条路线是正向自研GMC双电机串并联混动系统;另一条路线是与丰田合作的THS混动系统,实现了广汽第三代2.0TM发动机和丰田第四代THS混动系统的完美结合。广汽传祺已累计约3万用户市场验证,技术/品质成熟,是中国品牌混动发展的引领者。
围绕国家智能化数字化发展战略,开展“五化两平台·三生态”GDA2.0行动计划。搭建敏捷的运营平台及整合的数字技术平台,形成具有智能网联生态、用户运营生态及网络安全生态的全价值链智能运营体系。
构建智能数字化运营系统,如广汽全生命周期质量管理系统、研发质量管理系统、供应商质量管理系统等,完成研发、设计、采购、生产、检测、仓储、物流、销售、服务等业务全过程全链条数据采集检测,确保质量形成过程可视化。
目前广汽传祺初步使用了以下质量领域基础信息管理系统:
①供应商管理系统,包括供应商准入,评价和审核管理,首件管理等业务功能。
②质量问题管理系统,实现品质问题闭环管理。
③车辆监控服务平台,实现车辆部分运行数据异常监控及维修方案的电子化管理。
④具备部分品质数据统计功能的质量大数据系统。
⑤其他信息化基础应用软件,例如生产过程制造,市场售后质量等品质基础信息管理。
三、参评智能制造项目详细情况介绍
1、项目背景介绍
业务现状:集团各自质量系统成熟度各不相同,且存在严重的信息孤岛问题。
制造端新车领域品质信息没有系统,承载依然通过线下表格管理;虽然制造,供应和售后端有基础品质信息系统,但均是线下操作再手动上传系统,在系统上并没有形成业务联动,并且各个系统孤立,数据未打通;制造端和研发端的部分信息未联通,且G3各系统数据未打通。
课题:
(1)全过程品质流程系统建设
新建并初步串联各孤立的品质信息,形成一体化质量信息管理系统,完善内部基础数据采集管理,形成制造端质量信息一体化。构建问题模块,实现线上问题管理和再发防止业务开展,基于现有数据开发统计功能,实现数据整理和信息展示。
(2)集团内其他质量系统对接
从系统层面对接,根据已达成一致的业务流程进行G3质量系统对接(广乘制造端和广研设计端),实现系统线上流程,数据流转和数据统计。
2、项目实施与应用情况详细介绍
项目目标:
(1)建设多部门协作的问题解决和跟踪平台,实现系统业务主动驱动,推进在源流的品质闭环改善,提高问题解决速度和效率;
(2)通过横展和再发防止,提高设计/制造/供应领域在前工序的先行对应,提高新车、量产及市场品质水平。
(3)完善和规范各种问题的统一处理工作流程,如设计分析问题、用户体验问题、内控问题等,以及横向展开和再发防止流程;
(4)通过统一的零件代码和故障码对质量问题进行系统分类,建立质量问题库,提高开发和解决问题的能力。
(5)多类型多样式质量分析统计查询报表和实时风险/协调信息推送,管理层实时了解从产品开发到售后市场发生的所有问题进展及风险,为决策提供数据;
(6)日常会议直接使用系统组织和联络,信息实时共享,提高信息整理和沟通效率。
项目实施效果:
创新点1:质量全生命周期问题闭环管理
通过系统接口与数字营销系统、供应商管理系统和研究院研发质量管理系统,实现质量问题数据对接,建立统一全过程问题管理平台,实现从生准、量产、市场到客户品质体验全过程质量问题源流改善,横向展开、检出分析、经验库、新车再发防止检证、标准流程优化等在整个过程的品质问题闭环管理。
创新点2:质量问题横向展开
横向展开模块通过GQS系统与供应商管理系统和研究院研发质量管理系统对接,实现了市场品质问题,制造品质问题,新车品质问题和体系问题,在四地工厂之间,供应商之间和新车型之间的风险排查,风险对策及对策效果跟进等过程的闭环管理。避免同一问题原因在不同产线,不同供应商和不同车型再次发生。
创新点3:检出显在化分析
当市场品质和量产品质及其他领域,问题源流改善后,从流防的角度向前各环节分析,还有哪些途径可以提前发现问题,严把质量各关卡。将问题推送到新车评价,全检,抽查及试验工程师手中,由工程师分析是否有检出和显在化项目缺失并制定改善对策,以完善检证观点、检证标准和检证方法等。
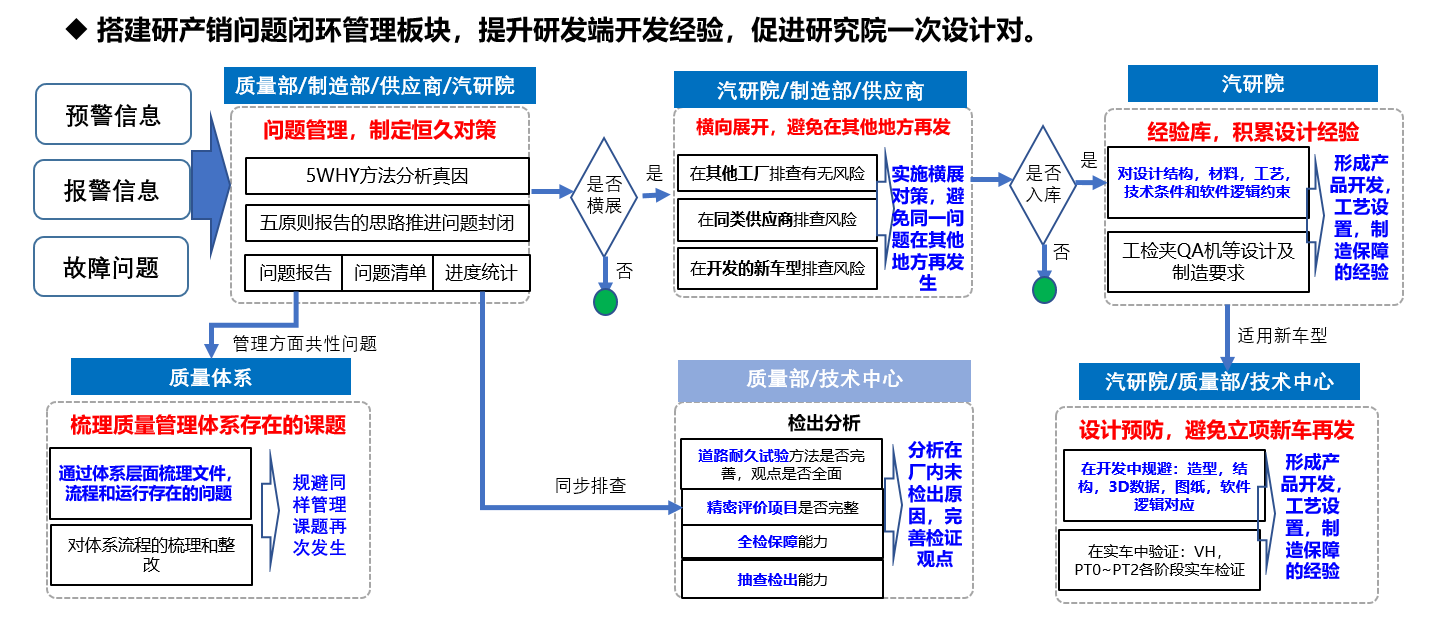
图1 问题管理
3、效益分析
通过该项目的实施,实现内部质量问题的线上管理,已达成共享意向的质量数据跨领域100%有效传递以完善经验库。实现设计、制造、供应商等质量跨企业的线上信息100%传递和业务。线上流程覆盖问题管理、横向展开和再发防止,使质量问题明确对策时长缩短约17%,沟通效率提升60%;质量问题源流整改对应率提升21%,避免任务跟踪遗漏。
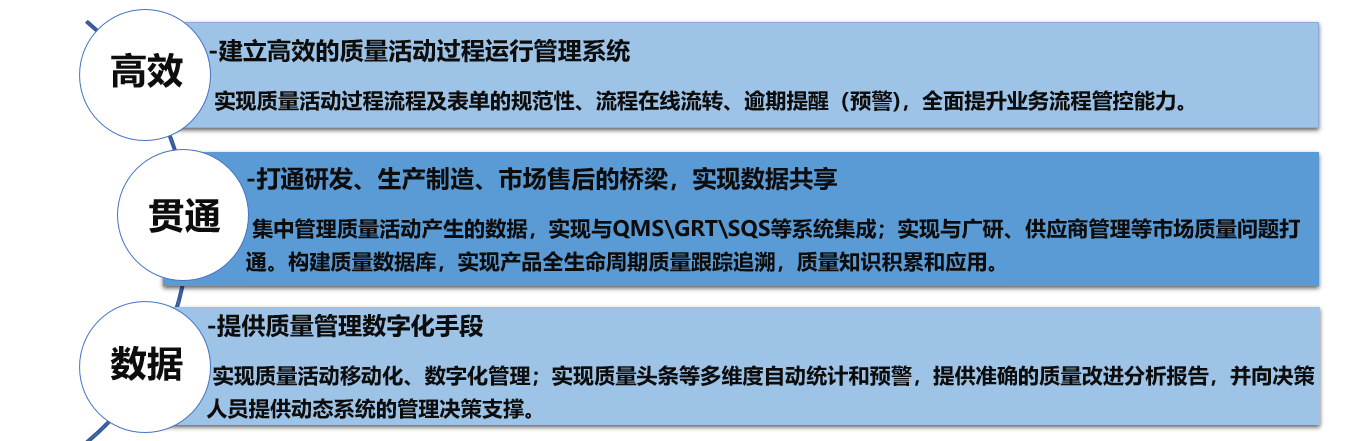
图2 转型收益
通过数字化转型,能够风险预知和助力决策,聚焦客户体验(功能好,问题对应速度快),为客户提供更多更好的选择;形成可量化的指标,衡量汽车品质在行业的水平,衡量数字化在行业的水平;
推进制造业质量管理数字化是一项系统性工程,要以提高质量和效益、推动质量变革为目标。发挥主体作用,强化数字化思维,持续深化数字技术在制造业质量管理中的应用,创新开展质量管理活动。