2024年12月8-15日,e-works成功举办了2024第九届日本精益制造考察活动。在此次深度探索行程中,考察团通过实地参观工厂、观摩专业展会、聆听前沿技术讲座及参与深入的专题研讨等多种形式,全面了解了日本制造业的最新发展动态,以及智能制造的前沿趋势和实际应用。
本次考察是e-works组织的第40次国际交流活动,由e-works CEO黄培博士亲自带队,携20余位知名企业高管,参访了世界工业机器人巨头FANUC、高效率加工技术领导者牧野机床、全球知名综合性企业集团三菱电机、日本精益生产的鼻祖丰田汽车及丰田产业技术纪念馆、日本领先的汽车零部件供应商三五株式会社、全球制造业巨头川崎重工、日本最大的运动鞋品牌之一亚瑟士(ASICS)。此外,考察团还聆听了日本能率协会举办的精益化和智能制造的专题讲座,观摩了亚洲知名的日本工业展——福冈展,深入探讨了日本制造业持续领先的秘诀。
考察的第一站来到了FANUC总部,稻叶善治会长、山口贤治社长和机器人销售事业部本部长岛田直树先生等FANUC高层领导会见了考察团。作为全球领先的工业机器人制造商,FANUC自1972年成立以来,不断发展壮大,现已成为拥有众多员工、工业机器人累计交付超100万台、年营业额庞大的行业巨头。秉持着对于工厂自动化的不懈追求与探索,FANUC形成了以数控和伺服技术为基础发展的FA事业部、应用了基础技术的机器人事业部和智能机械事业部为支柱的布局,业务遍及全球107个国家和地区。
考察团近距离参观了FANUC的可靠性评价大楼、机械加工工厂、机器人组装工厂、伺服电机制造工厂、修理工厂和中央技术中心,实地体验了机器人组装机器人的应用场景,并进行了深入交流。FANUC广泛引入机器视觉传感器、力觉传感器和AI技术,发布了一系列新型的协作机器人、并联机器人和智能装备。FANUC公司精益求精的专业能力、高性能和高可靠性的产品、以客户为中心和持续创新的企业精神给考察团成员留下深刻印象。
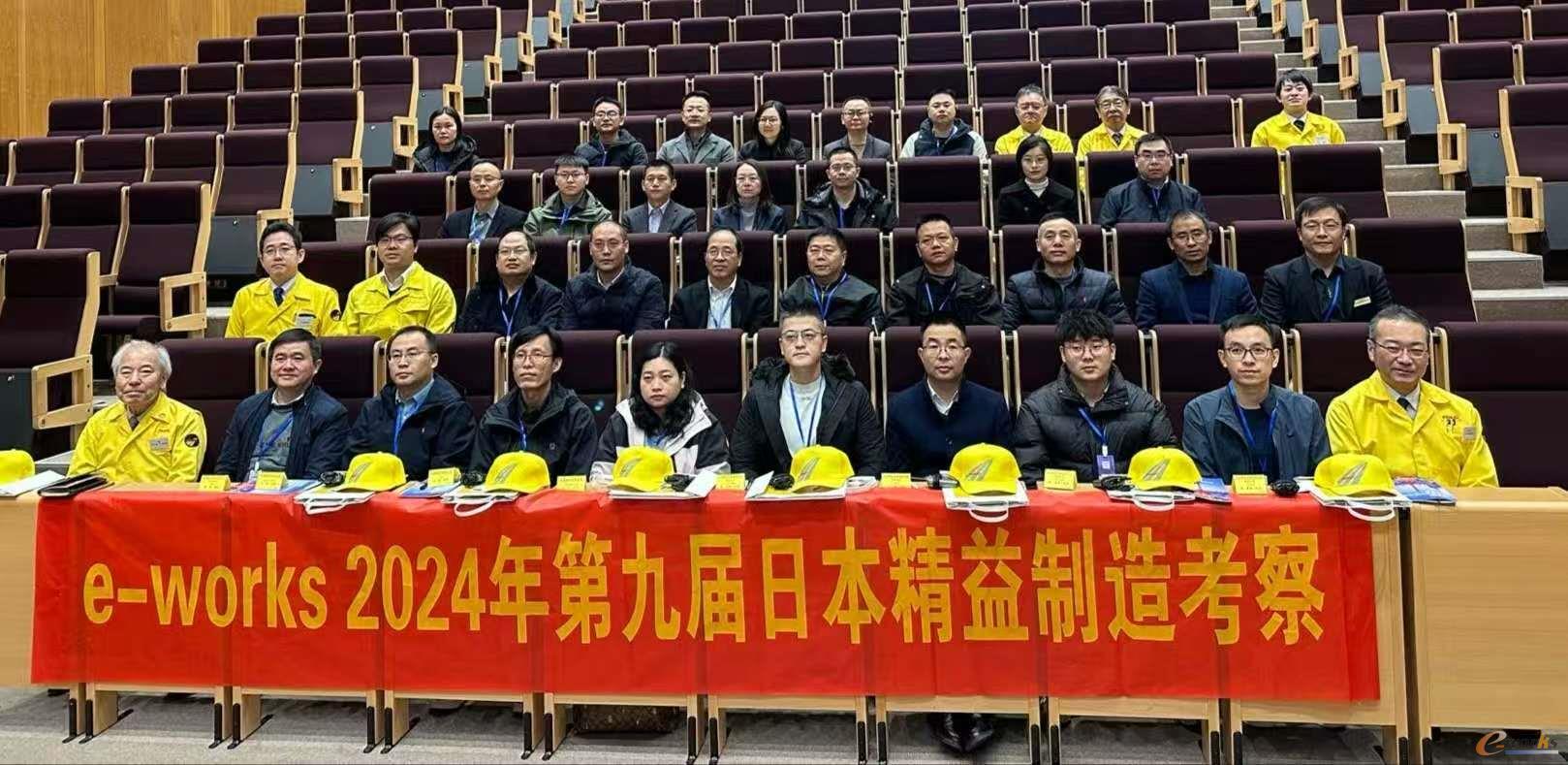
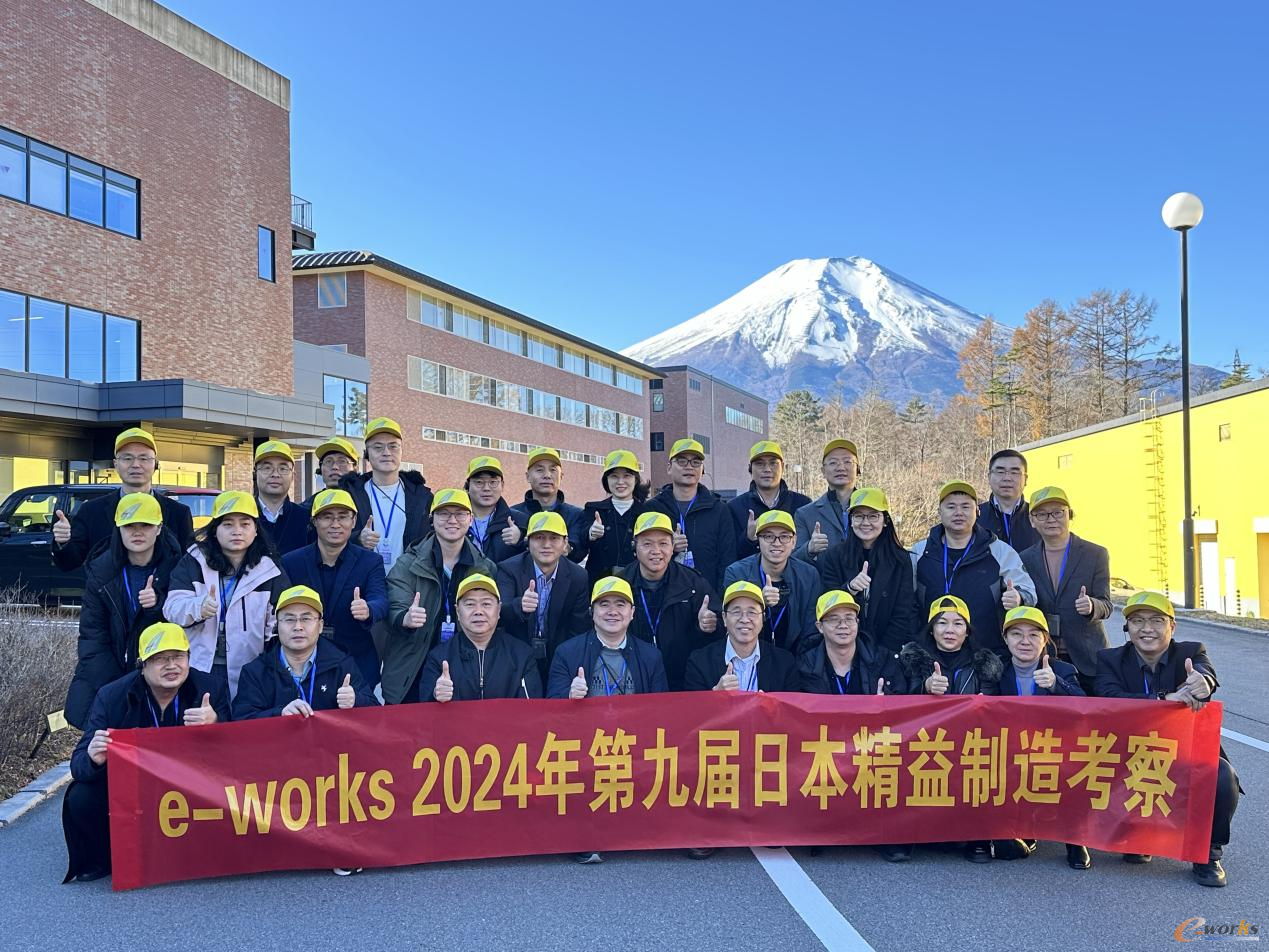
考察团在FANUC合影
第二站,考察团访问了全球机床行业领先企业牧野机床。牧野机床始建于1937年,主要生产立式和卧式铣削加工中心,以高质量、高精度著称,重点服务模具加工、零部件加工和飞机零部件加工领域。历经八十余载的发展,牧野机床深厚的历史底蕴为企业积累了丰富的经验和技术沉淀,也见证了制造业在时代浪潮中的不断演进。与时俱进的生产模式与管理理念为广大的制造业发展提供了学习和借鉴。
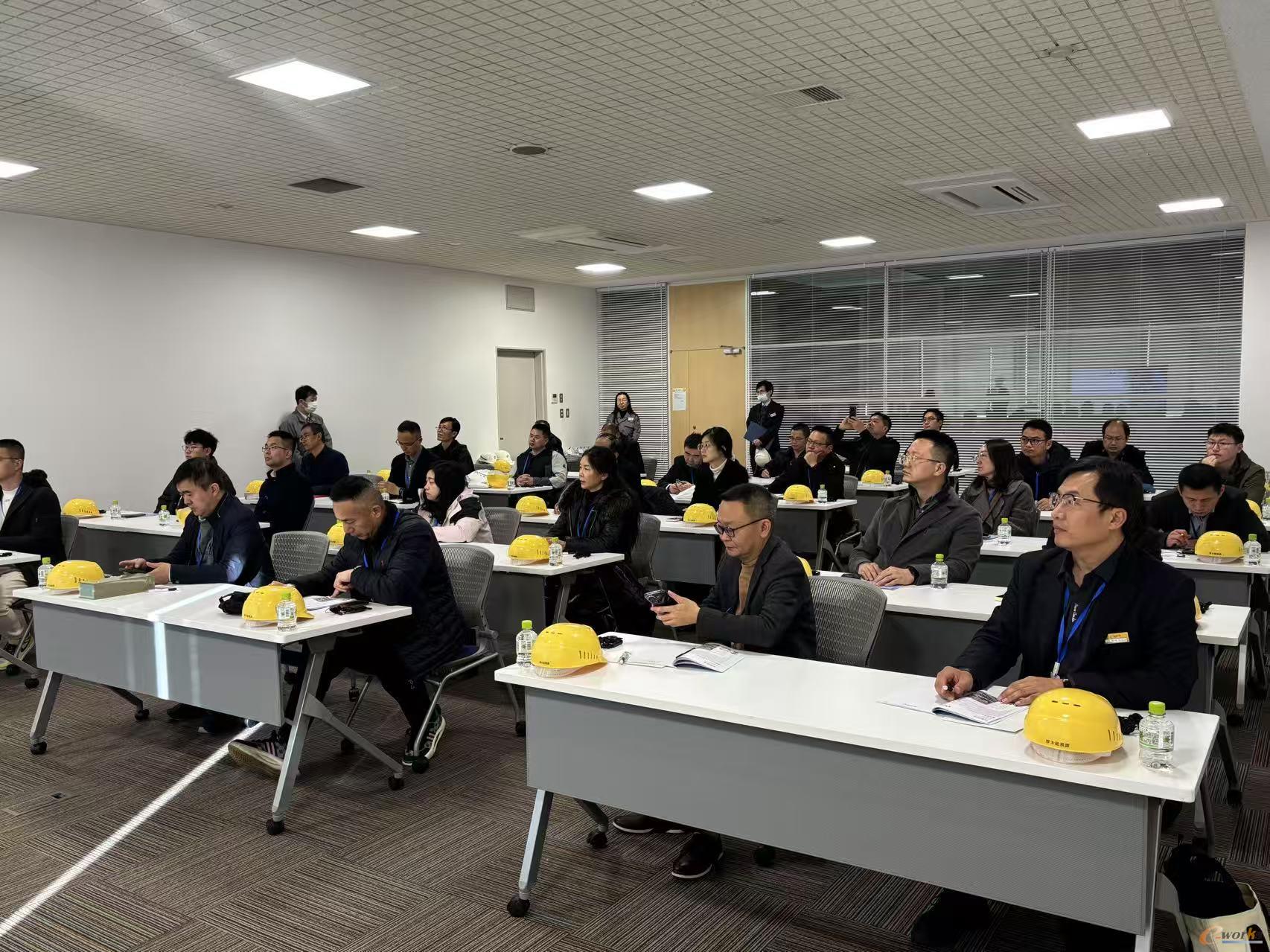
考察团在牧野机床座谈交流
考察团现场参观了厚木工厂的机加工、总装车间,以及主轴工厂。牧野机床在高端精密的加工能力、出色的柔性制造水平、严格的生产环境管控和质量第一的企业管理理念给考察团团员留下深刻印象。其中,柔性制造系统(FMS)深深地吸引了大家,通过将线边立体库、机器人、视觉传感等先进技术进行综合集成应用,实现了零件加工的全自动化。同时,工厂运用了恒温系统,通过在不同高度的位置安装多个温度传感器来监控车间内温度变化,实现恒温管控,确保了机床的高刚性和高精度。
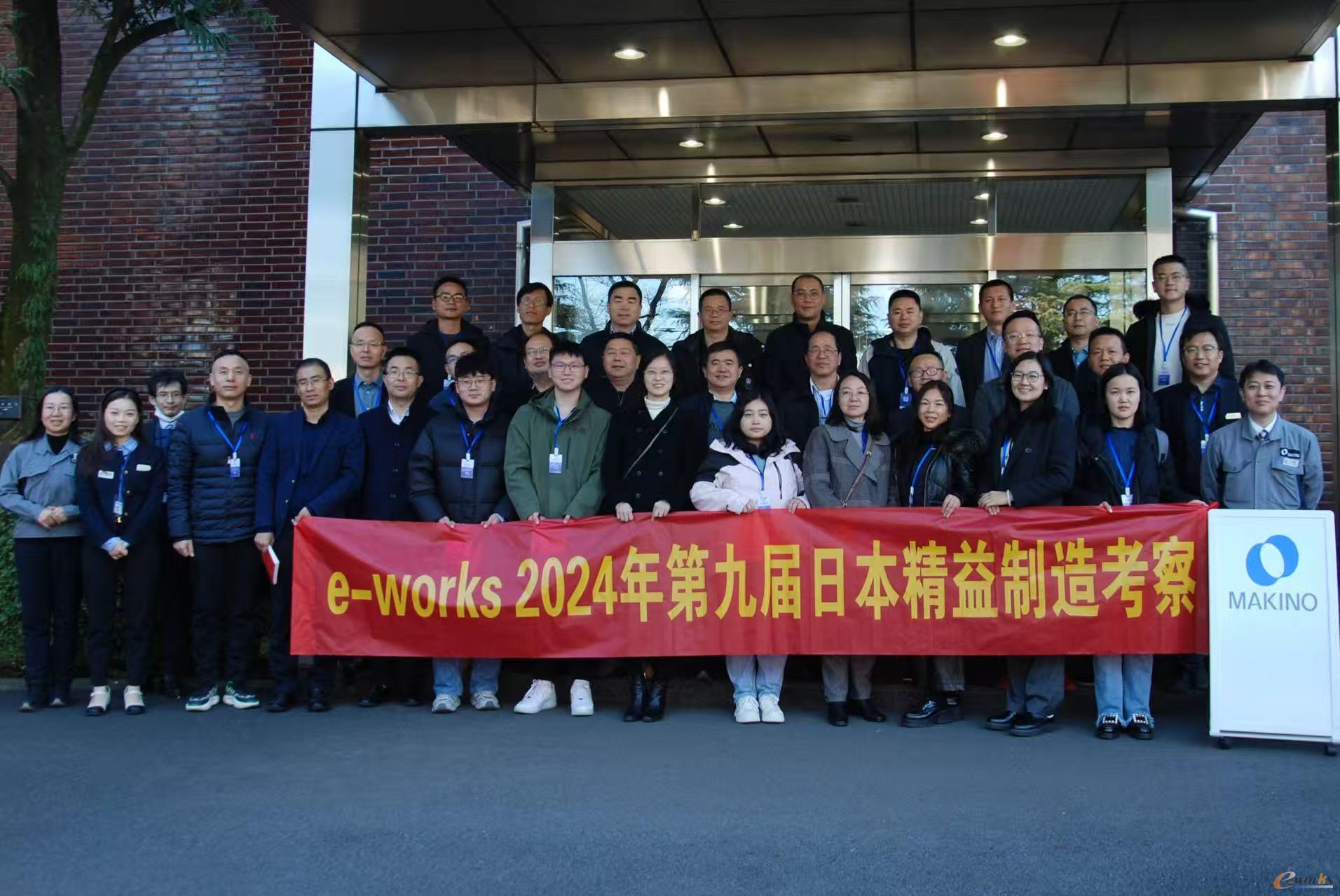
考察团在牧野机床合影
第三站,日本能率协会咨询公司(Japan Management Association Consulting, JMAC)。作为日本知名咨询公司,JMAC自成立以来一直致力于全球企业经营改革和人才培养等咨询服务,并且早在1986年就开始对中国企业提供涵盖精益研发、整合供应链管理、精益生产、流程再造、数字化、经营质量等咨询服务。
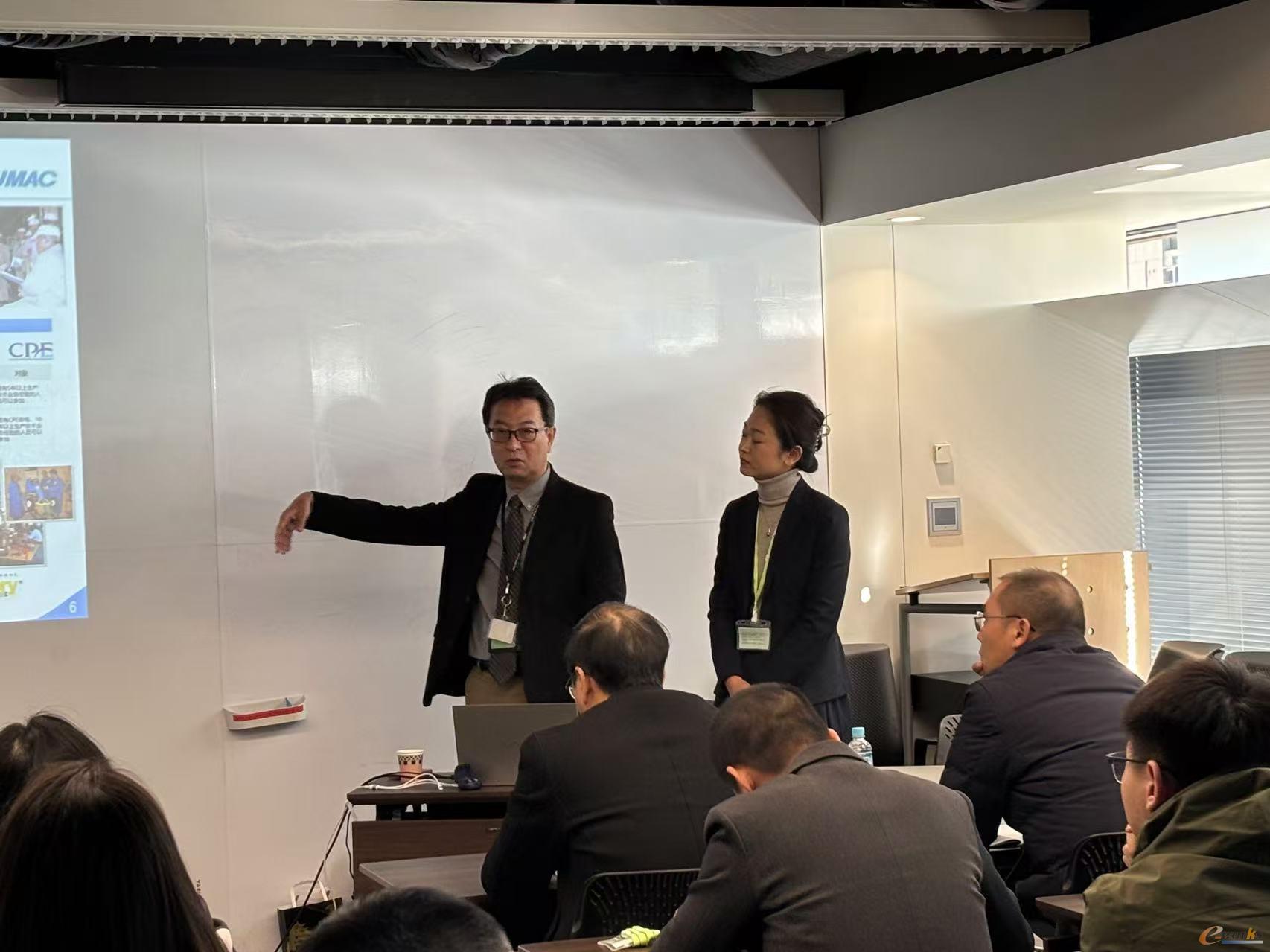
JMAC专家西冈英树老师授课
考察团现场聆听了JMAC专家关于《精益生产实践与智能制造推荐方法》的课程。课程从日本文化和日本人的价值观讲起,解读了日本企业的经营方式与创新之道,分析了丰田汽车生产方式产生的背景、精益生产的理念与实践,讲解了5S管理、按灯系统、价值流分析,以及如何推进PDCA循环等持续改善的精益生产具体方法。日本企业注重团队协作与集体智慧,强调全员参与和持续改进,从而驱动着精益生产在各个环节的实施。此外,通过对数字技术和智能制造如何与精益生产相结合的深入探讨,为考察团成员推动企业持续创新和增强竞争力,推进精益生产和智能制造提供了思路与借鉴。
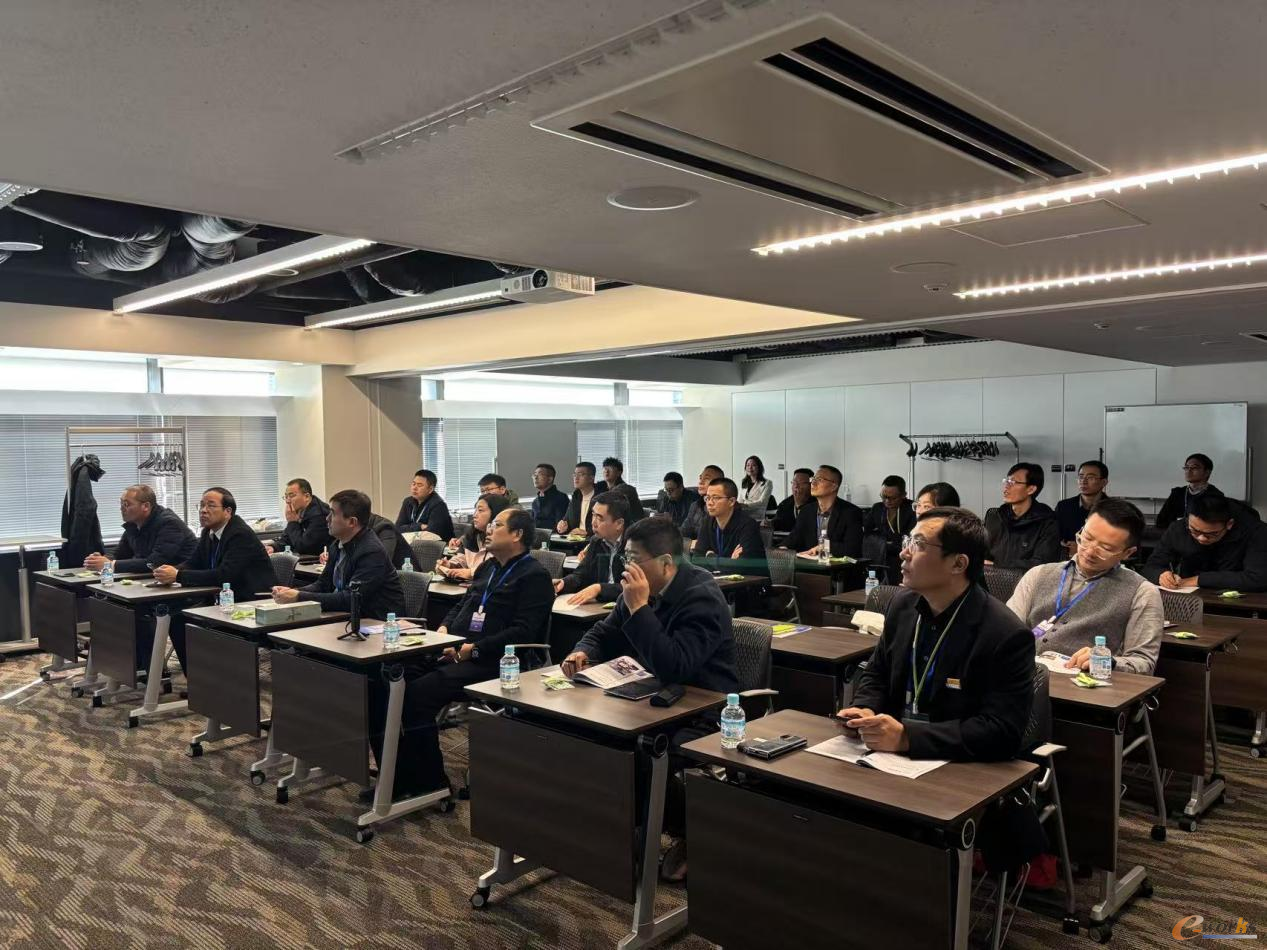
考察团聆听JMAC讲座
第四站,丰田产业技术纪念馆。作为日本丰田集团运营的企业博物馆,丰田产业技术纪念馆建于丰田自动织机制作所的遗址之上,于1994年建成开放,可以说是丰田集团的发源地。纪念馆以近代日本的工业化为主题,主要介绍了丰田集团从纺织、铸造发展至汽车产业的峥嵘历史。
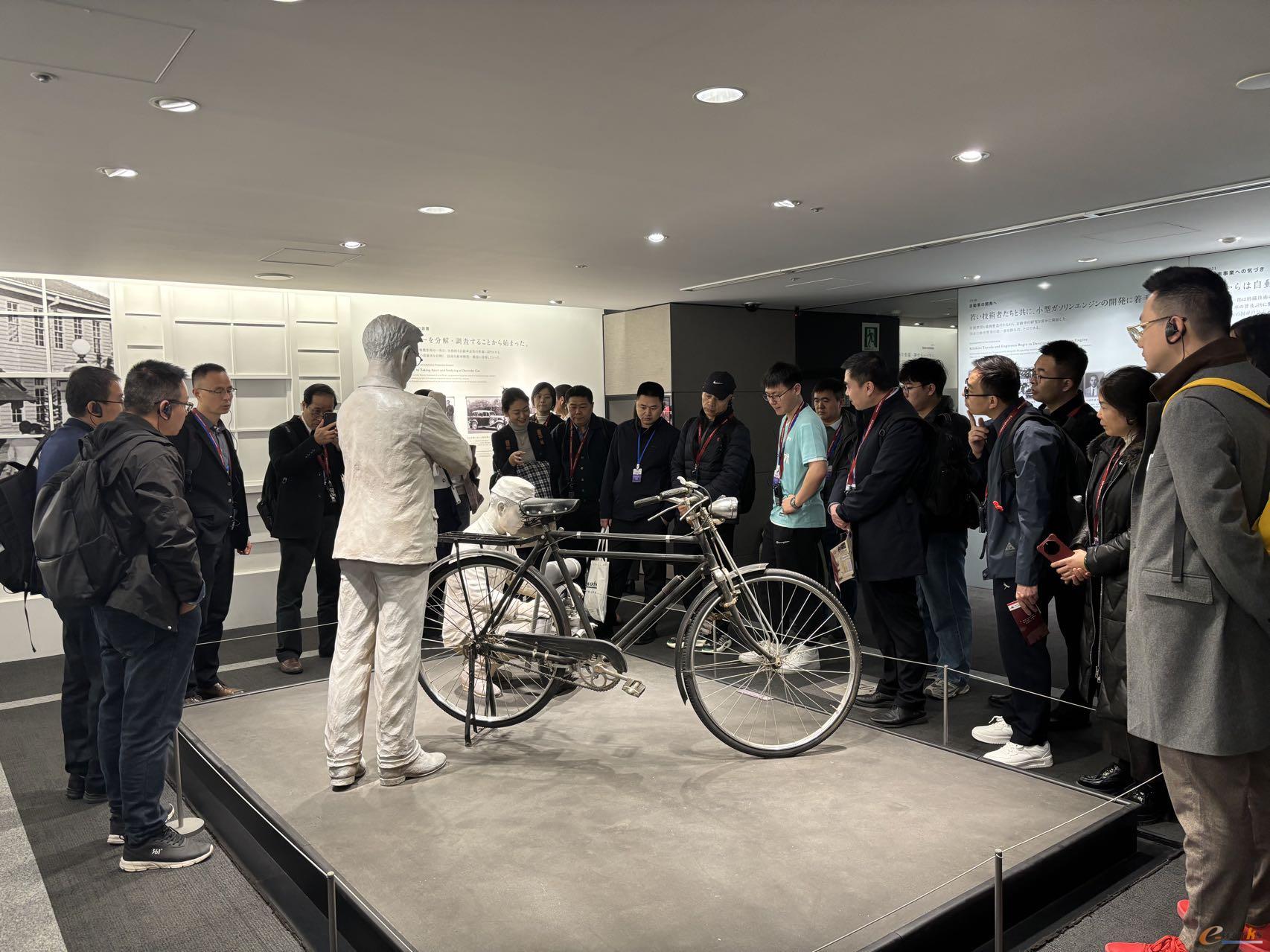
考察团参观丰田产业技术纪念馆
通过参观,考察团全面了解了丰田从纺织机械到世界领先汽车制造商的辉煌历程,从丰田佐吉发明的自动织布机,到“丰田生产方式”(TPS)的精益生产理念;从使用传统的木质梭子的半自动织机,到喷水织机、喷气织机;无不生动展现了丰田技术创新与持续改进的力量。在“汽车制造区”,考察团看到了丰田从第一款轿车到现代混合动力汽车和氢能源汽车的进化,以及曲轴加工、模锻、冲压、车身焊接、喷涂和总装等汽车制造工艺的直观动态展示,从手工生产方式到自动化、智能化生产方式的变迁,感受到了丰田不断追求卓越、“精益求精”的精神。

考察团在丰田产业技术纪念馆合影
第五站,三五株式会社八和田山工厂。三五公司成立于1946年,专注于汽车部件特别是排气系统和发动机零部件的设计、制造和销售,是丰田汽车的一级供应商。八和田山工厂成立于1990年,主营制造汽车排气系统和车身总成业务,拥有员工392名,2023年销售额达711亿日元。
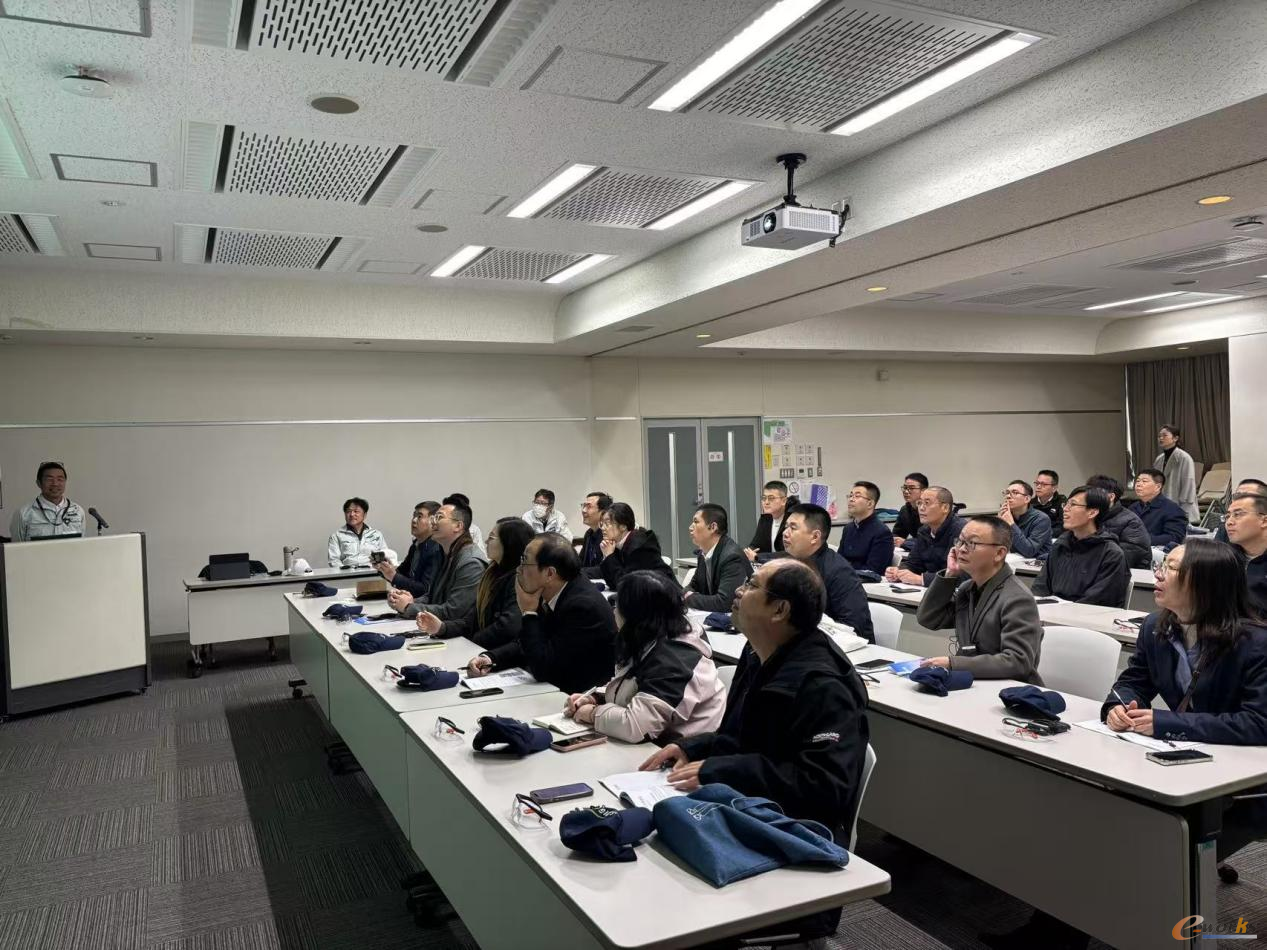
考察团在三五株式会社八和田山工厂座谈交流
通过工厂实地参观,考察团了解到,三五公司深入践行了丰田生产方式(TPS)和精益生产理念,针对多品种少批量的产品,采取人机协作的低成本自动化生产模式。针对批量较大的产品,公司在生产自动化的基础上,基于AGV的广泛应用实现物流搬运自动化和自动配送;同时,通过践行看板管理,实现及时生产;以及基于生产设备布局的调整,工装夹具的小型化、简易化、共通化改善,换型时间缩短了十倍。三五公司通过持续推进生产效率提升、减少浪费、提高产品品质,灵活应对需求变化的精益生产管理模式,为广大制造企业发展提供了借鉴。
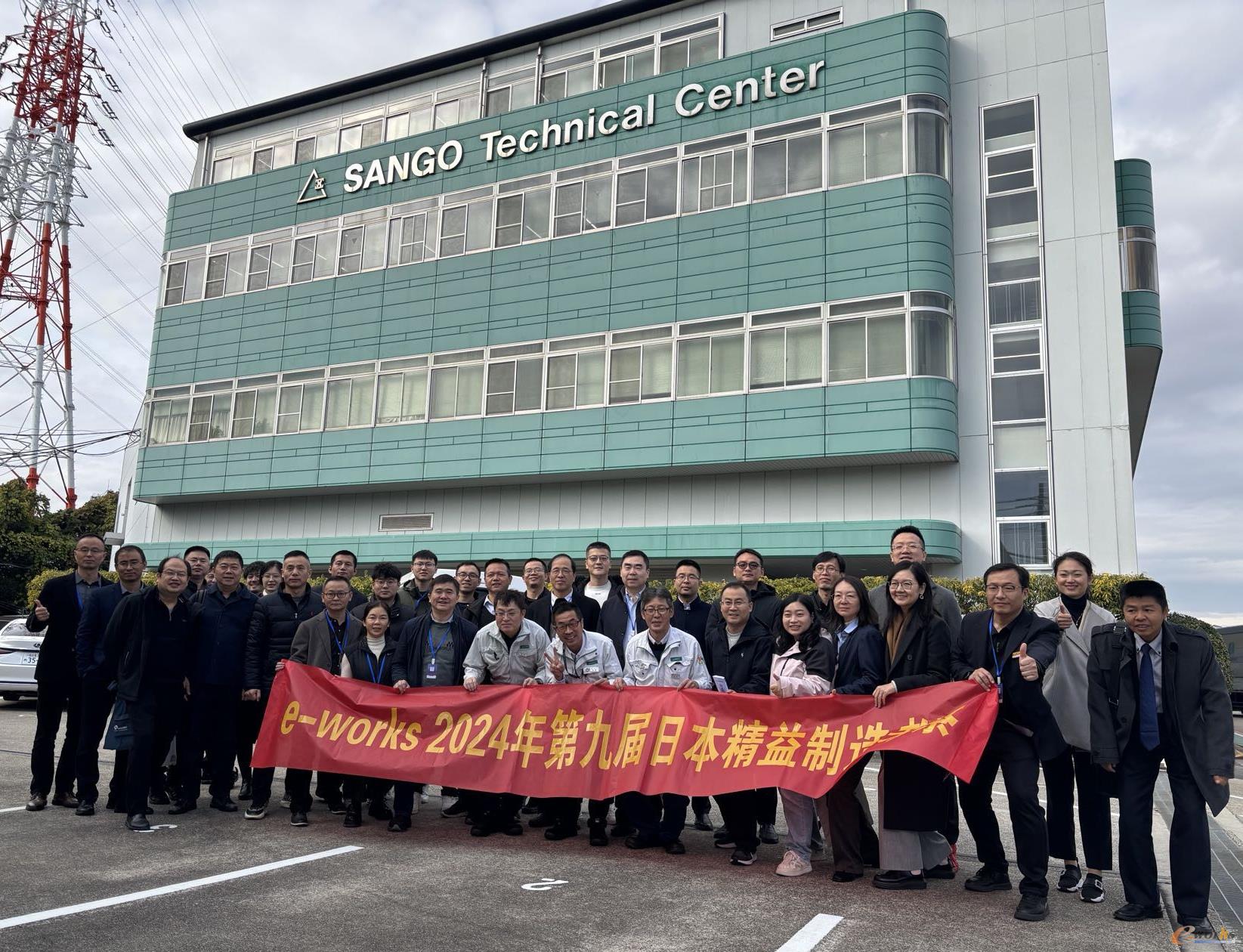
考察团在三五株式会社八和田山工厂合影
第六站,三菱电机名古屋制作所。作为三菱电机首个生产通用马达的工厂,也是三菱电机工厂自动化(FA)生产中心,三菱电机名古屋制作所素有“母亲工厂”之称,2024年恰逢其成立100周年。
三菱电机名古屋制作所100周年
考察团全面了解了三菱电机的智能制造和数字化解决方案,实地走进了伺服电机工厂和PLC制造工厂,并深入参观了FA展示厅,体验了三菱电机FA产品的实际应用案例,并与三菱电机的专家进行了深入的交流。三菱电机名古屋制作所的伺服电机工厂积极推进面向自动化的设计和制造工艺的持续改进,实现了定子铁心自动绕线,通过柔性自动化产线进行高效组装与检测;PLC工厂通过推进三菱电机提出的e-F@ctory综合解决方案,显著提升了生产效率和产品品质,节约了能耗。此外,三菱电机提出的智能制造改善水平评估标准SMKL(S Smart、M Manufacturing、K Kaizen、L Level)更是值得借鉴和推广。

考察团在三菱电机名古屋制作所合影
第七站,川崎重工。川崎重工成立于1878年,是日本代表性的综合工业制造企业之一,产品涵盖陆、海、空运输机械、工厂设备到产业机械,主要产品包括摩托车、飞机整机和零部件、工厂设备、精密机械、机器人、摩托艇、燃气轮机、船舶和铁路车辆等。
川崎重工双臂SCARA协作机器人抓取柔性材料的演示
考察团聆听了川崎重工的发展历程、组织架构和主要产品介绍,并深入观摩了其工业机器人展厅,主要包括其工业机器人、双臂协作SCARA机器人和并联机器人在汽车、电子、医疗、食品等行业的典型应用,如车身焊接、涂装、物流码垛、晶圆搬运、药品搬运和手术机器人等。其中,川崎重工的远程遥控喷涂机器人应用、用双臂协作SCARA机器人搬运柔性电路板、焊接自动线的安全控制等应用实践吸引了考察团成员的浓厚兴趣。
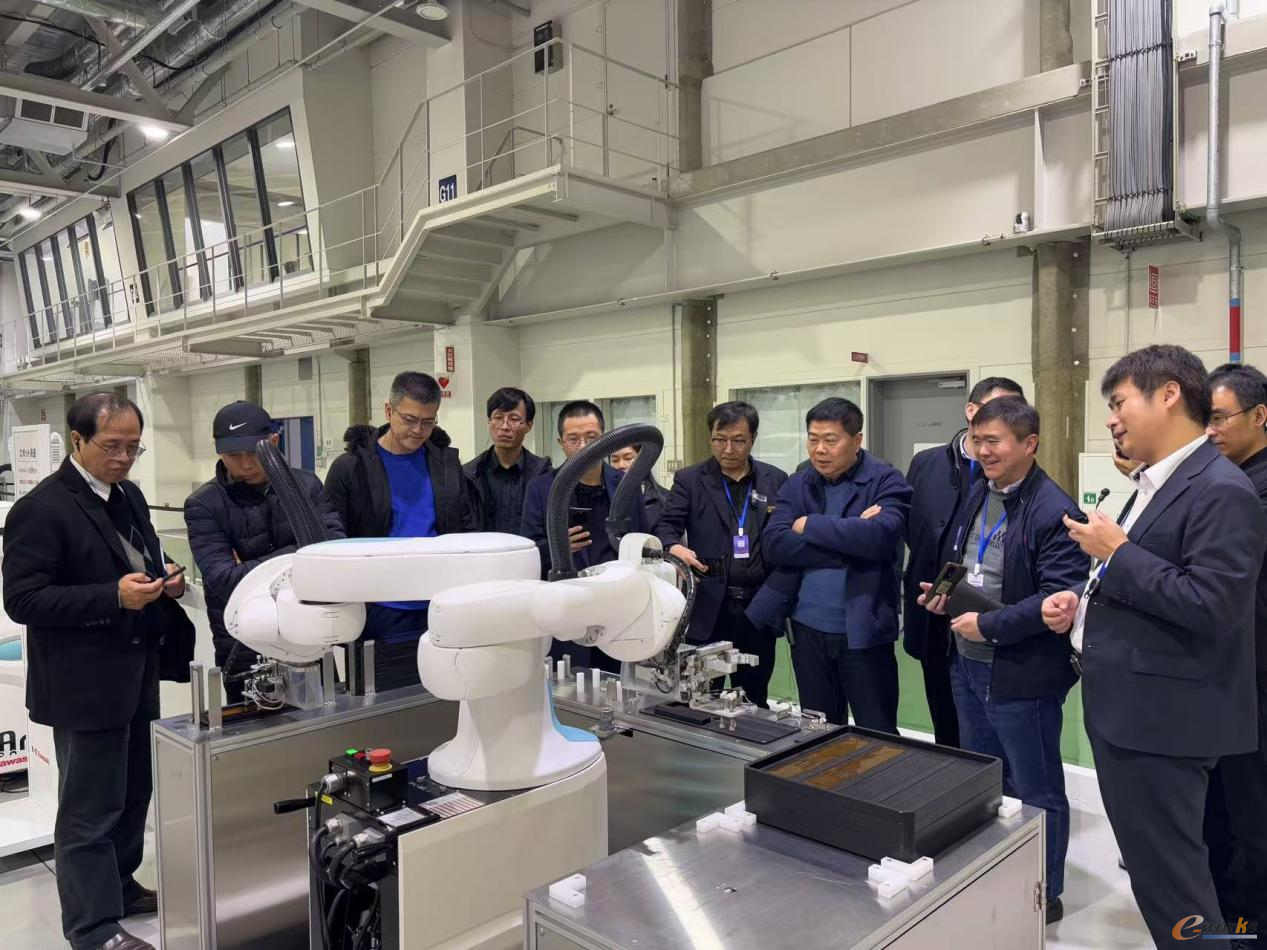
考察团参观川崎重工工业机器人展厅
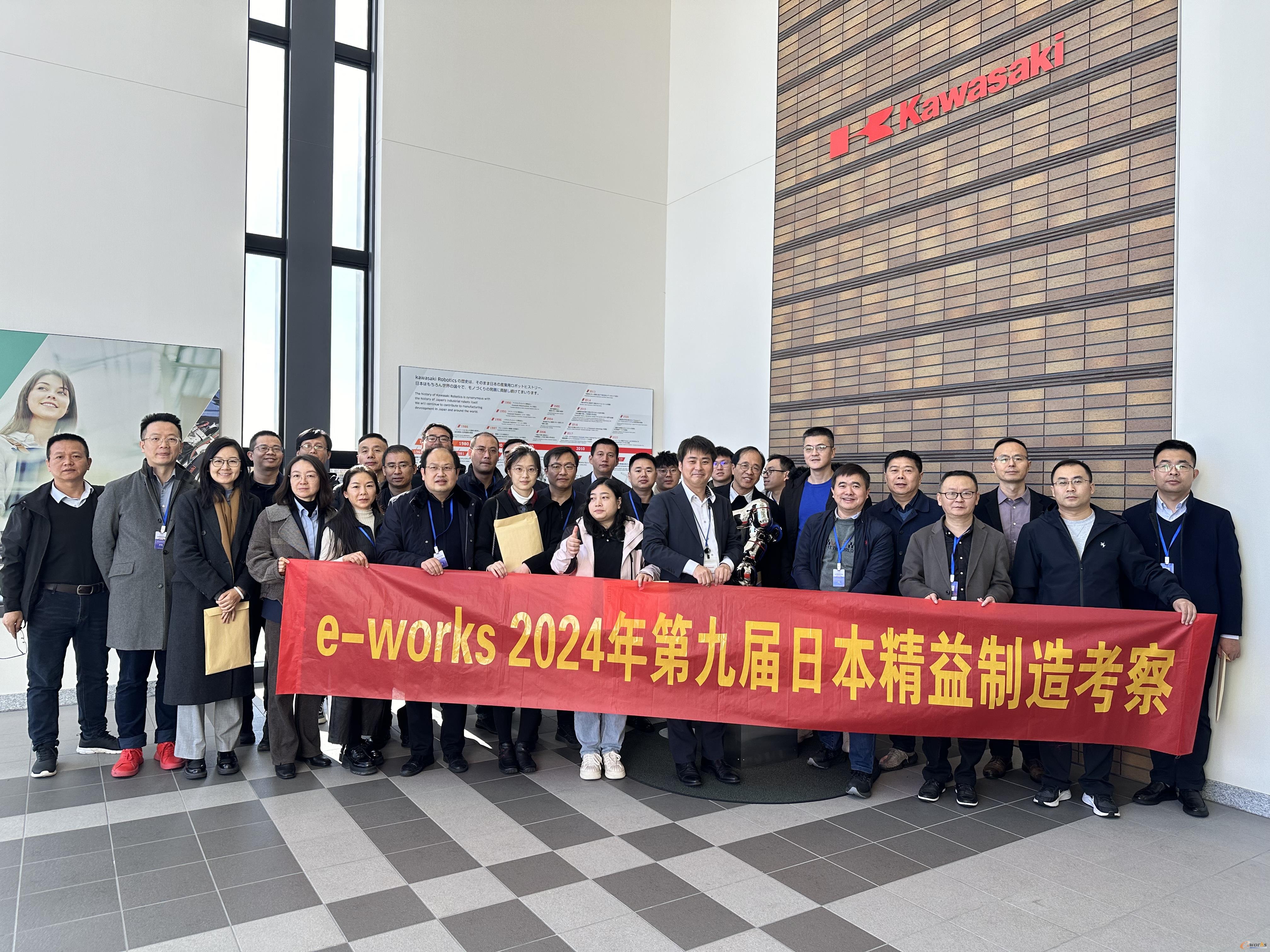
考察团在川崎重工合影
第八站,ASICS运动研究所。作为“世界四大慢跑鞋”里唯一的亚洲品牌,ASICS成立于1949年,其人体工学研究所成立于1990年,现有100多名研究人员,是专注于运动科学研究和产品开发的机构,目标是通过科学研究和创新,提升运动员的表现和运动体验。
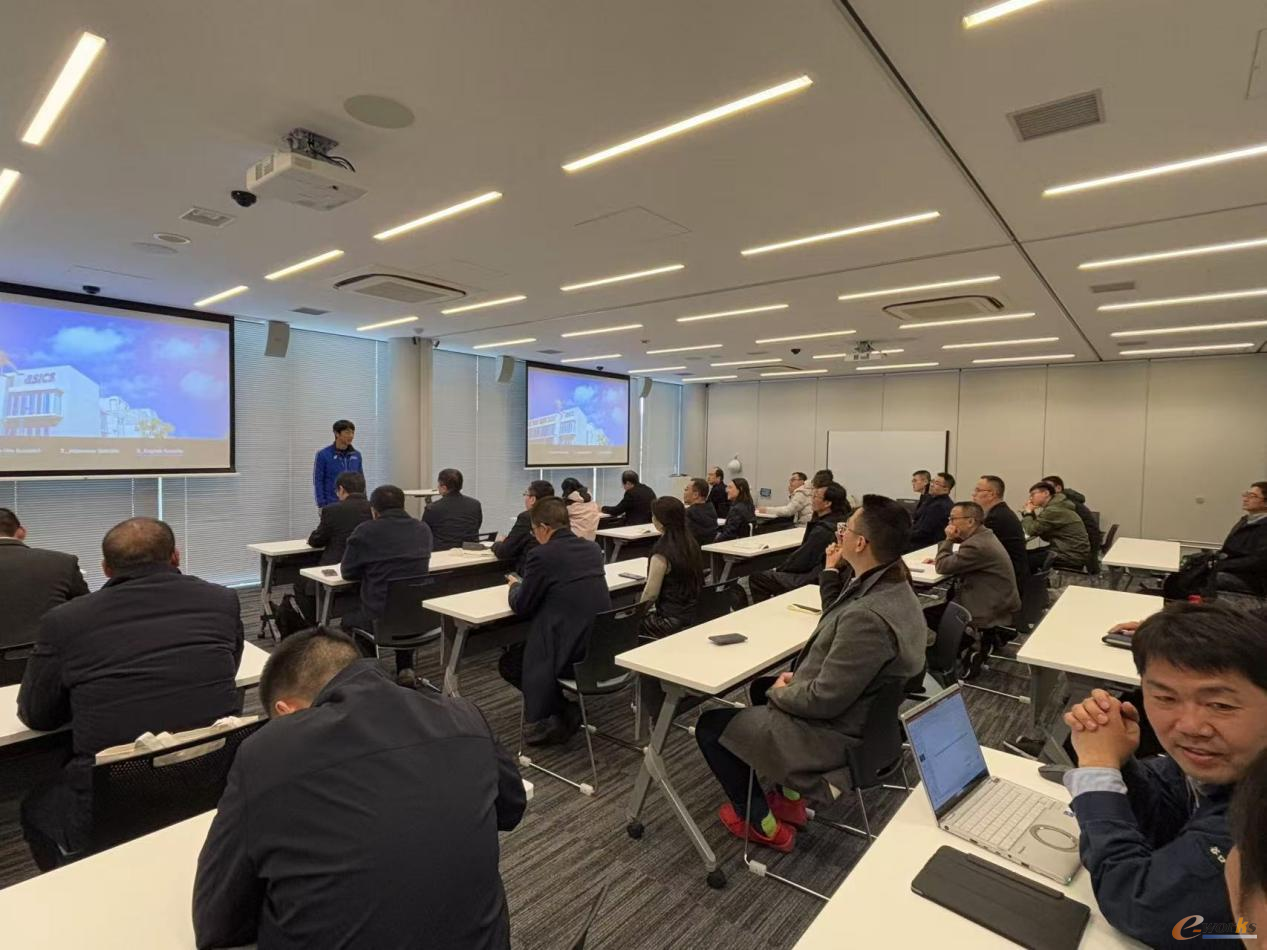
考察团在ASICS运动研究所座谈交流
考察团实地参观了ASICS材料处理研究室、人体机能测试实验室等多个实验室和车间,观看了通过运动员跑步,用动作捕捉加传感器来记录其运动鞋对其身体指标影响的现场测试展示。ASICS人体工学研究所长期致力于开展各种人类运动形态、材料、结构、制造加工技术分析和研究;其研究成果包括运动鞋的减震技术、支撑技术、透气技术等,这些技术的应用提高了运动员的舒适度和运动效果。另外,ASICS与达索系统深度合作,利用数字技术和增材制造的方式为客户提供运动鞋个性化定制服务。
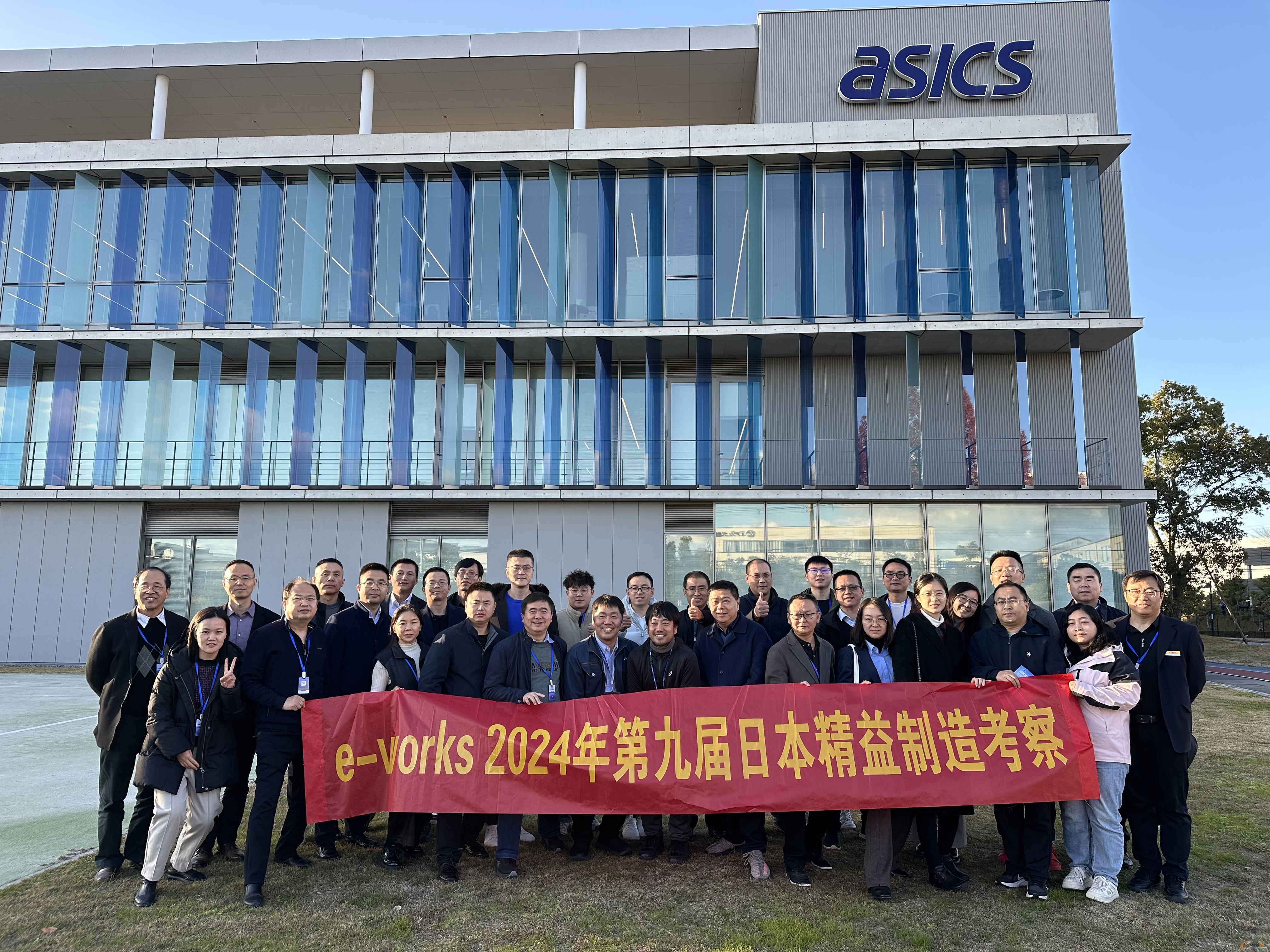
考察团在ASICS运动研究所合影
第九站,丰田汽车九州工厂。该工厂成立于1991年,现有员工7000多名,月产汽车3万台,主要生产雷克萨斯NX、UX、ES和RX四种车型,是丰田汽车在日本的第二大生产基地。目前九州工厂已累计生产900多万台车,其中90%的车辆为出口订单。
考察团参观了其第一工厂的焊接车间和总装车间。在“百臂群舞”的机器人车身焊接车间里,考察团成员详细了解了混线的定制焊接线,点焊、熔焊和激光焊三种工艺由1700个高度协同的机器人实现了自动化生产,每辆车身需要进行4000多个焊点、800多个坚强点的加工;在总装车间检测环节,大家观摩到对每辆雷克萨斯车辆的全方位检测过程,在1个小时内要对1800个检测点进行检测,并通过电子看板实时了解了车间的生产状态。不同于国内企业24小时不间断生产的特点,九州工厂生产班次为每日两班,且每日24点至6点为维护人员的设备保全(TPM)工作时间,以避免因设备故障造成非计划性停机。
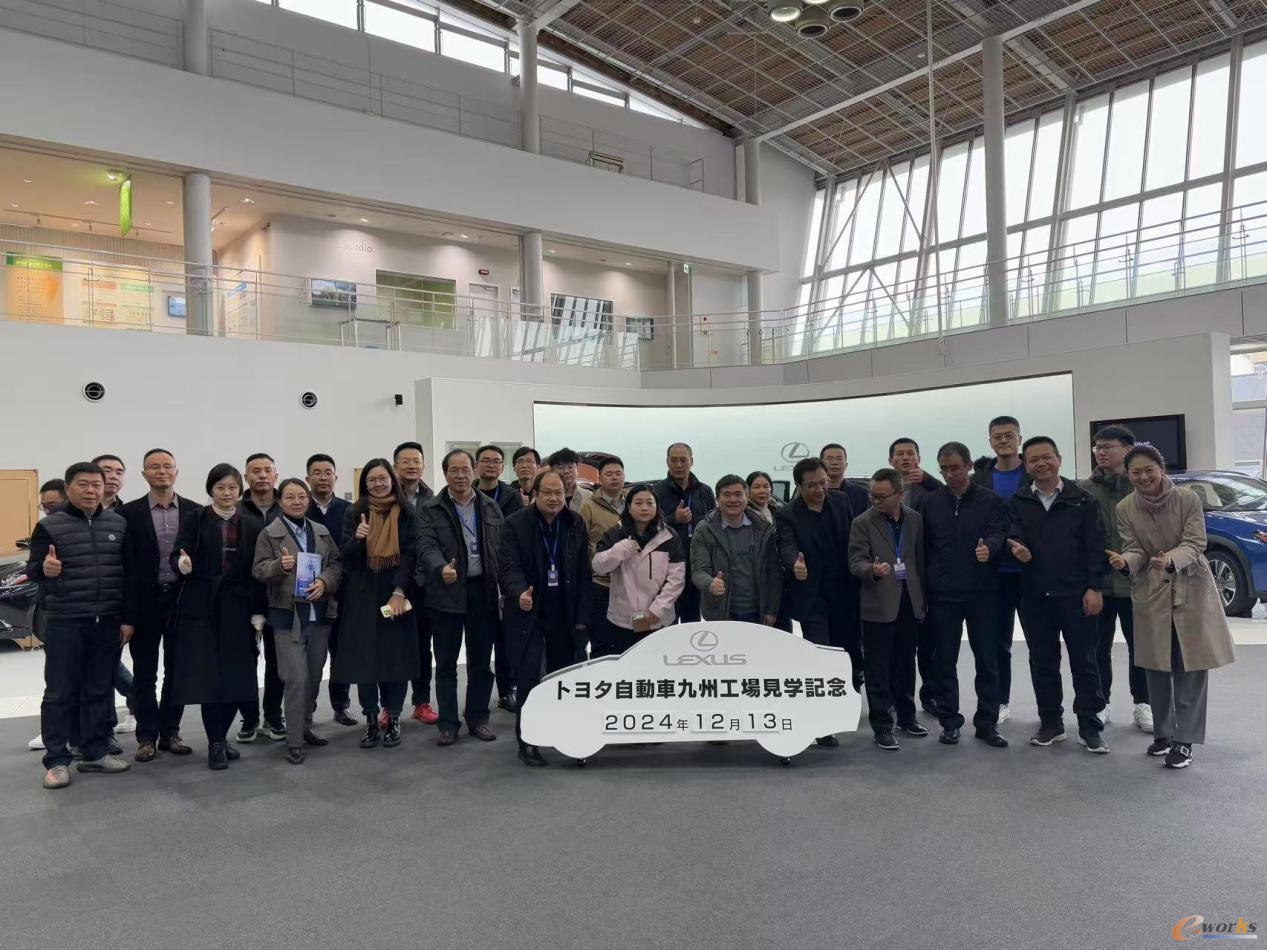
考察团参观丰田汽车九州工厂
第十站,日本工业展福冈展。作为日本九州地区最大的制造业盛会之一,福冈展主要分为软件和硬件两大展区,以及设计工程机制造解决方案、机械要素及技术、工厂五金及机电设备、工业AI/IOT、国际增材制造及3D打印、国际测量/测试及传感器、工业数字化、工业ODM/EMS、工业控制系统网络安防、工业设备智能维护等十个子展,汇聚了来自日本海内外知名企业展示的机械零部件、运动控制、DX(数字化转型)解决方案、3D打印增材制造、工厂设施和测量仪器。
展会现场,考察团实地走进了基恩士(KEYENCE)、米思米(MiSUMi)、海克斯康、SellBOT、OKI、UNIPULSE、TECHS等数字化与工业自动化厂商展台,观摩了协作机器人加平衡吊,通过高压空气形成磁浮气垫,通过AR眼镜远程指导维修等应用的应用展示。值得一提的是,考察团还观摩了中望软件展台,以及来自中国的电火花加工设备和增材制造设备的企业展台,深切感受了我国企业正在积极出海的热潮。

考察团观摩日本工业展福冈展
至此,第九届日本精益制造考察已圆满落幕,全体考察成员均表示收获匪浅!
在为期一周的精益制造研学旅途中,考察团通过工厂参观、技术讲座、内部研讨、展会观摩等多种形式,深刻体会了日本制造的精髓,以及以丰田生产模式为重要成果的精益思想在不同企业的发展和应用实践,并对日本行业领先企业的经营理念、产品定位、生产制造以及人才培养模式等有了更加深刻的认识。考察团成员纷纷表示深受启发,有很多方面值得学习和借鉴:
(1)践行精益理念,注重持续改善
在日本企业中,精益理念不仅是一种管理工具,更是一种企业文化。其中,持续“改善(Kaizen)”的策略更是日本企业管理中非常重要的理念,涉及高层领导、管理人员乃至一线员工,是日本企业竞争成功的关键。例如,三五株式会社深入践行了丰田生产方式,针对小批量、多品种的产品生产实际,不是一味追求生产的自动化率,而是强调人机协同和持之以恒的精益改善。针对小批量的产品,为适应日益复杂的焊接和组装需求,自动化率由之前的近100%,降低到现今的60%左右,就是通过人的柔性来替代自动化的刚性;同时通过十年的时间,运用多种精益工具,将工装夹具从轻量化、简易化、通用化等方面进行改善,将换型时间缩短了十倍,因此构建了生产效率提升、灵活应对需求变化的精益生产管理模式。在JMAC专家关于《精益生产实践与智能制造推荐方法》的课程中,也提到日本企业注重团队协作与集体智慧,强调全员参与和持续改进,从而驱动着精益生产在各个环节的实施,为考察团成员推进企业的精益管理、推动企业持续创新和增强竞争力也提供了思路与借鉴。
(2)关注产品质量,追求极致制造
日本企业追求Monozukuri,即造物理念,追求极致制造。本次考察的企业中,FANUC和牧野机床都十分关注产品可靠性与质量。例如,FANUC的“可靠性评价大楼”是其诸多的研究楼中最大的一栋,配备了诸多大型设备,可进行特殊或恶劣条件下、长时间、同时多样的评价测试,体现了FANUC对产品可靠性与质量的重视;牧野机床加工和装配车间均运用恒温系统,通过在不同高度的位置安装多个传感器来监控车间内温度变化,实时测量并报告数据,确保加工车间始终保持在23±1度,装配车间±0.4度,从而保证生产高精度与高质量的机床。
(3)不盲目追求自动化,注重人机协同
日本企业非常关注投资回报率(ROI),并不盲目追求自动化,更强调机器与人的协调配合。针对大批量生产产品,企业会采用自动化产线;但针对多品种、小批量的产品,则会充分考虑产线、设备、工艺的柔性以及人机协同。例如,牧野机床在产品生产中应用了大量柔性制造系统,并十分注重一个流生产方式的应用;三五株式会社则从全自动化转向适度自动化,通过工装夹具的小型化、简易化、共通化的持续改善,来提高多品种、小批量产品生产的换型速度;丰田汽车在焊接环节应用了机器人全自动化作业,总装环节则在物料配送以及整车输送自动化的基础上,以人机协同的方式完成定制化装配与质量检测为主。
(4)以客户为中心,注重产品与工艺创新
日本企业十分关注客户的需求,并将其放在核心位置。通过全面了解客户需求,围绕客户需求进行产品设计开发,不断进行升级和创新,从而保持企业竞争力。例如,FANUC在物料出入库环节,为平衡客户的效率提升与成本控制需求,将机器人集成视觉传感系统、力觉传感系统,实现自动识别、自动感知的智能化、精准化作业,虽然机器人成本较高,但整体仓储物流自动化建设成本实现了下降;川崎重工工厂正在研发半导体产线的物流搬运机器人,以助力企业实现更为灵活、轻盈、精准的晶圆搬运作业;ASICS与达索系统合作,利用数字技术和增材制造的方式,为客户提供运动鞋个性化定制服务。
(5)务实推进数字化转型DX和绿色转型GX
日本企业非常重视通过数字化转型,实现质量、成本和交付的持续改进。如三菱电机名古屋制作所利用数字化手段支持多品种小批量的混流生产流程,实现快速换型;并提出了SMKL指标16宫格,横坐标从现场制造单元到供应链协同、纵坐标从数据采集到基于数据的分析改善,建立了一个非常有效的定位现状、长期目标和技术路线图的手段。在绿色转型方面,川崎重工面对能源变革的挑战,积极参与低碳和零碳技术的研发与推广,比如氢燃料电池、绿色电力电网技术和碳捕获、利用与封存(CCUS)技术,以及制造电动车等环保节能设备,从而促进能源的合理化、高效率利用,以实现降碳、节能、减排。
当前,我国正全力推进新型工业化,积极培育新质生产力,推进制造强国、质量强国建设。与此同时,我国众多优秀制造企业也在积极出海,致力于国际化发展。在我国制造业转型升级的关键阶段,企业需要更加积极地走出去,开拓视野,学习借鉴国际优秀制造企业的实际经验和成功之道。e-works长期坚持组织智能制造国际研学,为我国制造业转型升级提供了有效的途径。
本次考察的更多详细内容,请查看e-works特别报道:
2024第九届日本精益制造考察
e-works作为致力于推进智能制造与两化深度融合的第三方专业服务机构,将通过考察、论坛和实训等多种形式,持续为广大制造企业提供更多与知名企业面对面学习交流的机会。
本文为e-works原创投稿文章,未经e-works书面许可,任何人不得复制、转载、摘编等任何方式进行使用。如已是e-works授权合作伙伴,应在授权范围内使用。e-works内容合作伙伴申请热线:editor@e-works.net.cn tel:027-87592219/20/21。