1 引言
近年来,处于战略转型期的我国武器装备制造业以建设数字军工、智能军工为导向,全面推进信息化、数字化建设。“十二五”期间,以设计开发三维化、工艺制造无纸化、业务流程自动化、总装集成可视化为目标,着力推进信息化基础平台的建设和专业数字化能力的提升。
而工艺环节作为产品研制过程中的重要一环,目前还主要依托CAPP系统,以文字描述和静态图形的方式编制二维电子工艺卡片,不能充分利用已有的三维模型成果,严重落后于总体所全三维的数字化设计模式。特别是对机加工和总装装配工艺,单纯通过文字表述和二维简图很难准确表达工艺要求,这已成为提高工艺编制效率、提升工艺创新能力和制约型号全三维数字化研制模式发展的瓶颈问题。在此背景下,作者提出了建设基于PLM的三维数字化协同工艺系统,以工艺信息对象化管理、结构化存储、关联化组织、可视化展示为目标,试图将传统的二维电子工艺卡片转变为基于三维模型编制的图文并茂、可人机交互的现场作业指导书,真正架起从设计到制造的数字化工艺桥梁,从而最大限度地提高现场操作工人对设计意图、工艺要求的快速理解和准确操作。本文以某航天制造所基于PLM平台的三维数字化协同工艺系统建设为例,详细阐述了三维数字化工艺设计的核心需求、系统平台的框架构建以及由此带来的业务模式创新与变革。
2 基于PLM的三维数字化工艺核心需求分析
2.1 需求背景
随着型号数字化研制工作的快速推进,设计环节已全面采用了MBD(Model Based Definition)技术,即将产品所有的工艺加工信息、属性信息及综合制造信息等都附着在产品的三维模型中,摒弃了传统以二维工程图为核心的产品设计模式。为应对全三维设计模式对工艺规划与设计带来的挑战以及工艺创新发展的自身需求,对现有PDM系统进行升级改造,建设基于PLM(Product Lifecycle Management)的三维数字化协同工艺系统成为企业必然选择。
产品全生命周期管理(Product Lifecycle Management,PLM),是指通过统一的信息模型对产品全生命周期中各阶段的数据进行管理、转换和使用。作为PDM系统的延伸和拓展,PLM将成为连接ERP/MES/TDM等系统的中心纽带。
2.2 三维数字化协同工艺核心需求分析
a.基于三维设计模型实现工序模型和工序简图的快速设计。支持对三维模型及其轻量化模型进行底层处理,包括三维模型工艺批注、装配仿真、三维工装设计等。
b.结构化工艺设计和组织管理。通过结构化的工艺设计,实现不同工艺数据之间的关联与组织管理,并支持对焊接等特种工艺类型的参数化设计。
c.工艺检验一体化设计。在工艺文件中增加检验点和检验工序编辑功能,将检验融入到工艺设计过程中,并对检验术语、符号、参数等形成检验知识库,供工艺人员编辑检验卡或设置检验点时选用,以提高检验要求的规范性和高效性。
d.多专业工艺并行协同设计。需实现基于工序流程驱动的多个专业工艺可并行协同设计。
e.现场工艺执行及更改管理。实现路卡级别的现场工艺执行与更改的电子化管理,以替代现行的纸质通知单据,并实现现场工艺更改的有效管控和统计。
f.基于工艺资源库和工艺知识库的快速工艺设计。整合工装、设备、刀具、量具、仪器仪表等工艺资源数据构建工艺资源库,对常用工艺术语、典型工艺、通用工艺等进行统一维护管理构建工艺知识库,以实现工艺资源的快速调用和工艺知识的有效积累。
3 三维数字化协同工艺系统总体框架
3.1 系统概述
建设与PDM系统同一底层架构的三维数字化协同工艺设计与管理系统,工艺编辑按照树状结构化方式进行组织管理,工序/工步直接与PBOM上对应的零部件节点关联,工艺资源、三维工艺模型、工艺文档等数据直接与对应的工序/工步相关联,所有工艺数据均按照PBOM层级关系进行组织和展示。工艺输出同时支持二维/三维、视频动画等多种工艺表达形式。
3.2 系统框架构成
基于本所PDM系统建设基础,结合以上核心需求,构建基于PLM的三维数字化协同工艺系统。主要构建模块包括:三维结构化工艺设计与管理、工艺检验一体化管理、多专业工艺协同设计管理、现场工艺执行与更改管理、工艺资源与工艺知识管理等。系统功能框架如图1所示。
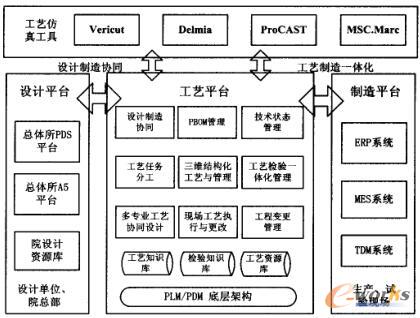
图1 三维数字化工艺系统框架设计
3.2.1 三维数字化工艺设计与管理
在数字化工艺编辑器中,工艺员基于与工艺任务相关联的PBOM零部件和MBD模型进行工艺设计,包括结构化的工艺文件编制、工艺资源选择、工艺仿真、结构化检验参数定义、三维工装设计等。工序/工步、工艺资源以对象化的形式关联管理,工艺规程整体以树状结构化方式组织和展现。通过网络化关联管理,确保某一工艺数据更改后相关数据的关联更新;通过基于工序/工步级的工艺组织和更改,将传统工艺文件以“册”或“本”为单位的粗粒度管理方式转变为以“工序”为单位的精细化管理方式,避免工艺文件更改需整体更换或换页的传统弊病。三维数字化工艺编辑器如图2所示。
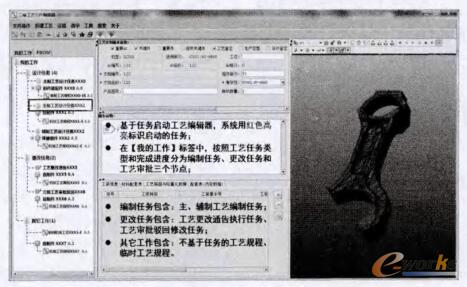
图2 三维数字化工艺编辑器
中间工艺模型的设计,可利用Creo的柔性建模能力,基于对三维设计模型特征参数的继承应用,快速生成。
工艺设计完成后,可生成WEB和PDF两种形式进行签审和发布。WEB版可满足浏览交互、查看三维模型,针对每道工序/工步进行文字批注,利用CreoView对工序中间模型进行三维可视化批注。PDF格式主要用于辅助浏览和纸质文件打印下发,不支持批注及三维模型浏览。WEB输出格式如图3所示。
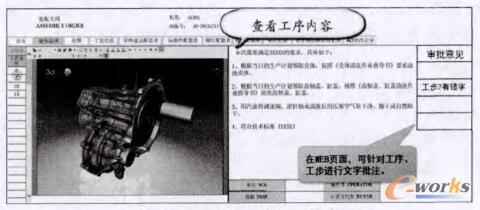
图3 WEB版工艺输出格式
3.2.2 工艺检验一体化管理
传统模式中,由于工艺与检验是两个独立的过程,检验时需重复描述相关工艺内容,并且由于没有检验知识库,检验要求填写不规范,受人为因素影响大,难以精确表达检验要求,操作过程效率较低。此外,所有检验实测记录都是通过纸质方式记录和管理,难以实现快速追踪和灵活分析。
将检验过程融入工艺设计过程中,实现工艺检验一体化设计与管理,可从根本上解决以上问题。即在工艺设计过程中同步完成检验点的设置和检验要求的设计,检验内容的签审及更改与工艺规程同步进行。
现场各类检验记录表单直接基于工艺输出,不再单独编制。通过PLM与MES系统的集成,可直接通过MES端从PLM系统工艺规程中集成获取对应类型的电子检验表单,执行实测数据记录与保存。实现现场检验记录的电子化管理和输出,为后续检验记录的分析和应用提供基础数据。通过对各专业检验知识的梳理总结,建设统一维护管理的检验知识库,可大幅提高检验设计的规范性、准确性和高效性。
3.2.3 多专业工艺协同设计管理
将不同专业分别独立编制工艺的传统模式转变为基于结构化文件的多专业并行协同设计模式,即多人可共同合编同一份工艺,并统一地编辑、输出与管理。
型号工艺师根据设计要求,确定出主制工艺任务及对应的专业类型,主制专业的工艺员在编制主制工艺的过程中,可根据需要,随时发起“辅制工艺任务”,并指派给相应专业的辅制工艺员。主、辅工艺之间的协同通过“辅制工艺任务”驱动,如存在多个辅制工序,需逐个下达“辅制工艺任务”。辅制工艺与主制工艺可同时进行,并且主辅工艺员之间可相互查看各自编制的工艺规程,并能自动输出基于工序级的主辅组合工艺路线。
3.2.4 现场工艺执行与更改管理
现场工艺是指车间生产制造过程中,与每一张路卡对应的具体工艺规程。路卡是由车间调度员基于PLM系统传递的主辅组合工艺路线开具的,每道工序对应一张路卡。现场工艺更改就是指由于车间生产设备、计划变更等临时原因(包含返工、返修),需要对该道工序生产过程中所使用的现场工艺进行更改。
现场工艺更改不能基于正式工艺规程更改,只能基于实例化工艺规程(从正式工艺规程中派生出一份新的、独立的工艺规程)进行更改,具体流程如下:
现场工艺发生首次更改,这时现场工艺用的是正式工艺规程,则首先需要将该正式工艺规程实例化,再在实例化工艺规程基础上修改。如现场工艺发生非首次更改,这时现场工艺用的是实例化工艺规程,则可以直接在实例化工艺规程上进行修改。因此,现场工艺发生更改前,与路卡对应的工艺规程是正式工艺规程(经过完整签审流程并正式发布的规程),现场工艺发生更改后,与路卡对应的工艺规程是实例化工艺规程。现场工艺每发生一次更改,都要实例化一次工艺规程。
PLM系统在接收到现场工艺更改任务后,首先将主、辅工艺规程分别进行实例化。工艺员在工艺编辑器内对现场工艺进行更改并提交签审,正式发布后,PLM系统将更新后的工序路线推送到MES端,MES系统对路卡进行更新。工艺员可在工艺编辑器中,基于正式工艺查看对应的现场更改记录和对应的实例化工艺规程。现场工艺更改方式如图4所示。
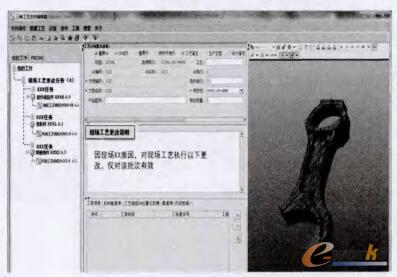
图4 现场工艺更改界面
通过路卡级别的现场工艺执行管理,可实现现场工艺更改的电子化流程、系统化管理和更改前后的可视化对比,有效提高现场工艺更改的可追踪性。
3.2.5 工艺资源与工艺知识管理
a.工艺资源数据管理与应用
工艺制造资源是工艺设计过程的重要组成部分。在基于三维环境的工艺系统中,工艺制造资源为数字化工艺设计提供基础信息、加工方法、设备和材料等资源的选择,为制造过程仿真提供支撑数据和信息,因此,对工艺制造资源进行有效的组织和管理是建立集成度更高、数据更规范、使用更便捷的三维数字化工艺系统一个重要基础。
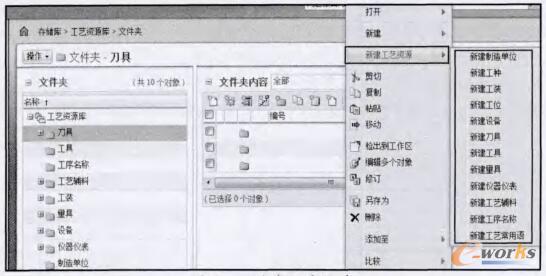
图5 工艺资源库构建
构建企业级的工艺制造资源库,需以结构化的数据组织方式将企业庞杂的各种工艺标准、规范、设备、工装乃至供应商信息有序的关联管理起来,并详细地描述它们之间的依存和约束关系。同时建立相应的日常维护制度,实现对各类资源的动态管理,确保所有资源能够及时更新。工艺资源库构建方式如图5所示。
b.工艺知识数据管理与应用
工艺知识数据主要是指企业工艺部门在长期工艺设计过程中积累形成的工艺规范、工艺常用语、通用工艺、典型工艺等专家知识和宝贵经验。系统中可以建立用于存储公用知识的工艺知识库,也允许工艺员在本地终端建立个人工艺知识库。公用工艺知识包括典型工艺(工艺模板)、标准工序、常用术语等经过认定的内容,个人知识库包括个人近期常用模板及习惯性用语等。
4 业务模式创新与变革分析
a.通过构建与设计数据接收统一的工艺管理平台,可实现基于单一平台完成从设计制造协同、工艺规划、工艺设计、工装设计、工艺签审与变更、技术状态管理及与ERP/MES集成的完整业务过程。避免不同环节切换不同系统,提高工作效率。同时,业务数据基于单一平台的无缝传递,可有效避免多系统集成带来的数据准确性和同步性等问题。
b.通过三维数字化工艺编辑器的引入,工艺员可充分利用已有的MBD三维模型,灵活选择三维工序模型、二维工艺简图、可视化模型工艺批注、仿真动画等多种形式的工艺表达方式,快速生成工艺图解和操作动画等多媒体数据。对现场操作工人来说,通过利用三维模型的直观性、可交互性等优势以及相关工艺资源、工艺文档的快速查阅,大幅提高工作效率。
c.通过工艺检验一体化设计与管理,实现了各专业工艺检验信息的规范化设计、电子化记录和结构化管理,通过与ERP/MES系统集成,实现车间工艺、制造、质量的一体化管理,为后续型号质量追溯、产品数据包的自动生成提供有效数据支撑。
d.通过基于全工艺流程的多专业工艺协同设计及应用,可实现基于工序流程驱动的多专业并行协同设计,促进主、辅工艺协同的规范化和协同效率。通过采用主辅工艺组合的工序级路线执行方式,细化了整个制造流程管控的颗粒度。
e.基于工艺资源的工艺设计模式,只允许选取工艺资源库中已有的数据,确保工艺数据的准确性、规范性和一致性,从而提高工艺设计规范性和工艺标准化水平。构建与工艺编辑器紧密集成的工艺知识库,建立基于知识重用的结构化工艺设计模式,可基于典型工艺派生工艺文件或基于工序模板快速编制相关工序,从而不断提高工艺编制效率和工艺设计水平,对工艺知识和经验的有效积累和重用具有重要意义。
5 结束语
针对已有IT基础和实际业务特点,提出构建基于PLM的三维数字化协同工艺系统。分析了企业三维数字化工艺的核心需求,详细论述了系统建设内容和关键流程,并在此基础上,简要分析了系统建成后的业务模式创新与变革。通过该系统在企业的建设实施,有效推进了三维数字化工艺的建设进程,为企业三维数字化协同研制能力的快速提升奠定坚实基础。
本文来源于互联网,e-works本着传播知识、有益学习和研究的目的进行的转载,为网友免费提供,并以尽力标明作者与出处,如有著作权人或出版方提出异议,本站将立即删除。如果您对文章转载有任何疑问请告之我们,以便我们及时纠正。联系方式:editor@e-works.net.cn tel:027-87592219/20/21。