本文为“2020年度中国智能制造最佳实践奖”参评案例。本次活动将评选出2020年度,为中国智能制造领域带来突出效益的最佳实践工程,全面介绍企业推进智能制造的步骤、重点与难点、获得效益等,分享建设过程中的经验,供广大制造业行业企业学习供鉴。
一、企业简介
南京中远海运船舶设备配件有限公司(以下简称“南京船配”)是中国远洋海运集团有限公司重要的船用配件专业制造与服务型高新技术企业,是国内船用柴油机气阀制造领军企业,尤其在气阀国产化方面,积极响应国家工业强基计划,坚持通过以自主创新研究掌握核心关键技术,以专利许可认证提高整机装配率,持续增强气阀制造技术能力与水平。2020年公司年营业额11465万元左右,员工160余人。
公司40余年来,一直坚持技术创新,引领企业发展,是国家“高新技术企业”、工信部“两化融合管理体系贯标试点企业”、“江苏省科技型中小企业”,先后参与或承接国家工信部、中远海运集团、中远海运重工、中海油、南京远洋等科技项目14项。建有江苏省研究生工作站、南京市工程技术研究中心、南京市职工创新工作室、江苏省示范智能车间及江苏省首批四星级上云企业。通过数十年的积淀和努力,公司已成功被MAN,PEILSTICK,YANMAR等国际一线柴油机制造商认可并配套,公司于2017年5月成功获取MAN D&T全系列Dura-spindle认可证书,这标志着公司正式进入二冲程新造机配套领域,打破了二冲程柴油机排气阀杆被进口品牌垄断的局面,填补了国内空白。
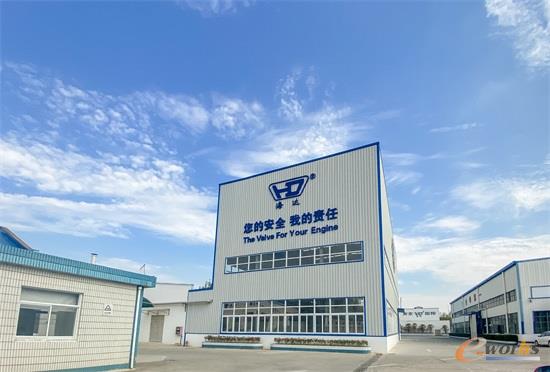
图1 南京中远海运船舶设备配件有限公司
二、企业在智能制造方面的现状
近年来公司不断加大研发投入,围绕标准化、数字化、自动化、信息化,大力推进智能制造,搭建以工艺为核心产品CAPP/PLM数据库,自主研发了MES系统,二次开发设备组态监控SCADA系统。具备ERP进销存、TQC全面质量管理、WMS仓储管理、数控车模拟分析,有限元分析等软件资源。设计并定制包括机器人焊接工作站、阀座智能加工单元、自动探伤流水线、智能制坯单元、超音速喷涂智能单元等一系列智能加工单元。
围绕产品数字化,建立数字化设计仿真验证平台,完成电镦-锻及后处理关键工序有限元分析模型,搭建电镦-锻质量免疫管理数据库系统,实现电镦—锻工艺优化和新产品开发试验周期由6-12月提高到3-6月,成功率由75%提高到85%以上,毛坯产出合格品率由80%提高到90%以上。
梳理整合产供销业务流程,自主开发了“人机料单合一”生产制造执行系统(MES),并对接ERP、PLM、WMS,实现产能评估、排程排产、作业派工、看板作业、报检报工、总检入库、物流发货全流程的单据电子化、流程可视化。
基于工艺优化整合,通过工艺设备成组互联,开展工段级设备集成自动化。完成包括电镦-锻制坯单元、电弧熔丝增材制造工作站、HVOF超音速熔覆绿色喷涂工作站、阀座机加工智能单元、荧光渗透探伤流水线等关键加工设备数字化集成,实现加工单元智能化、无人化生产,实现“工艺到设备、作业到工位”的智能管控。
引进海克斯康智慧质量管理系统(SQ),基于产品标准建立各工序检测方案知识库并结构化检测数据库,通过无线量具、检测设备数字终端等物联感知仪器仪表,现场采集检测数据并自动对比评判,开展在线检验、质量动态监控,实现质量控制由事后检测向过程控制、事前预防转变。
三、参评智能制造项目详细情况介绍
1.项目背景介绍
气阀是船舶动力系统核心零部件,受国内基础材料及制备工艺水平的制约,国内低速柴油机气阀长期依赖进口,核心零部件受制于人,严重制约我国“海洋强国”战略推进。
作为国内专业研制船用气阀的领军企业,我司50年来始终致力于核心技术研发及生产工艺改进。然而,受制于传统工艺装备及粗放生产组织模式,业务流程条块分割、研发手段匮乏、新品开发滞后,成果产业化脱节,生产过程中质量波动大、效率低、成本高,缺乏核心竞争力。
面对国内船舶配套产业发展的重要机遇,我司围绕战略优势能力需求,提出通过市场、管理、制造三大转型,以两化融合为主线、智能制造为主要手段,从技术创新应用、组织管理变革入手,推进数字化转型。
本项目基于“作业直接到工位、工艺直接到设备、管控数据直接到管理层”的顶层设计目标,围绕产品实现过程,横向整合产、供、销业务信息系统,纵向集成生产制造流程,重构产销协同-数字流贯通生产运营体系,实现作业到工位、工艺到设备、数据到管理,全面提升质量、效率、效益水平,实现高质量发展;基于物联感知采集,构建设备-信息-质量智慧管控平台,积累沉淀工业知识,并对设计-制造-服役大数据开发利用,建立自主知识产权专家系统,开展产品全生命周期管理尝试,彻底打破国外技术垄断,助力我司由制造向参与设计、制造服务一体化战略转型;并对接供应链上下游,探索价值链“端到端”商业模式变革,实现船舶配套关重件自主可控。
2.项目实施与应用情况详细介绍
本项目借助工业互联网、搭建私有云计算平台,实现数据的集成、分析和挖掘,搭建基于数据中台的大数据平台,整合并抽取设计、制造、检验、采购等业务系统数据,建立信息管控平台,借助各信息终端,以图表化管控数据指导生产经营活动,实现运营指标可视化及BI决策辅助;通过业务流程数字化集成并对接生产集控平台,搭建智能车间数字模型,仿真实体业务场景,从作业源头实时采集原始数据,映射到数字模型,实现虚实同步、透视化智能车间。

图2 南京船配智能制造示意图
1)基础设施建设情况
采用工业以太网、现场总线布设,基于多模态接口开展物联感知采集。通过设备组态、人机交互,条码标识应用,实现车间产线层面设备、工艺、人员、物料信息系统终端互联互通,支持制造数据和物料流动的实时监控,实现作业到工位、工艺到设备、数据到管理,完成两个数字车间集成总控,数字工厂初具雏形。
完成服务器虚拟化及私有云建设,实现ERP、MES、PLM、SCADA、TQC、WMS各信息子系统及其客户端数据云端化服务迁移;和联通运营商合作,通过服务器托管,完成异地备份,应用防火墙、ACM网络行为管理等硬件,采取漏洞扫描、运维审计等防护措施,搭建网络信息安全防护体系,确保网络信息系统实现安全可控。
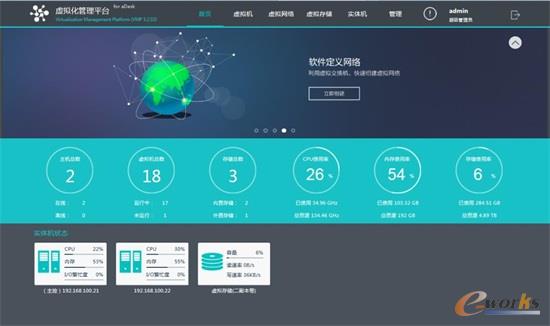
图3 服务器虚拟化及云平台建设
基于工艺优化整合,通过工艺设备成组互联,开展工段级设备集成自动化。完成包括电镦-锻制坯单元、电弧熔丝增材制造工作站、HVOF超音速熔覆绿色喷涂工作站、阀座机加工智能单元、荧光渗透探伤流水线等关键加工设备数字化集成;完成包括光学检测、接触式检测及机械性能试验等检测设备数字化改造。
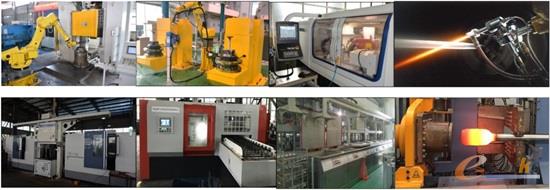
图4 装备数字化集成
2)平台及应用系统建设情况
(1)综合设计仿真平台
围绕产品数字化,建立数字化设计仿真验证平台,完成电镦-锻及后处理关键工序有限元分析模型,通过CAD、DEFORM、MSC.MARC、CAPP、PLM、数控车等专业软件对产品进行参数化设计及工艺路线仿真,实现包括图纸工艺在内的产品全属性数字化存档、电子化调用,编码对应、建立产品数字模型及工艺知识库,并通过产品生命周期管理(PLM)软件进行统一管理。基于该仿真验证平台,先后完成3种材料、30多个新品开发,并据此建立了关键工序知识库。
开发低能晶界密度与动态再结晶晶粒尺寸的伴生关系唯像模型、动态再结晶动力学方程等子程序;梳理大型电镦工艺运动关系、接触关系及参数加载特点,建立兼顾计算精度及效率的电镦多场多尺度动态耦合有限元分析模型;构建内禀变形参数与电镦决策变量的转换关系,结合有限元分析及多目标控制函数,以变形机制精确约束评判决策变量加载范围,从而构建多目标跨尺度联动精确分析模式,构建产品仿真设计模型,大幅缩短新品开发周期。
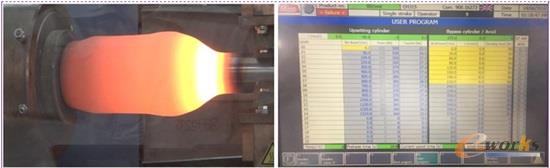
图5 仿真加工图
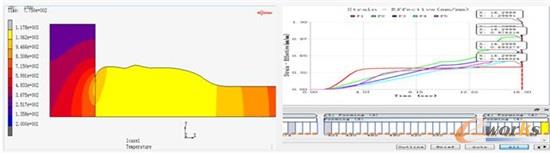
图6 仿真数据截图
(2)设计制造一体化
围绕工艺标准化,建立了以工艺为核心的产品数据管理系统(PLM),完成技术文档电子化、结构化归档,确保设计制造数据同源继承,实现工艺图纸电子化签审、归档、发布、作业推送。
梳理整合产供销业务流程,自主开发了“人机料单合一”生产制造执行系统(MES),并对接ERP、PLM、WMS,实现产能评估、排程排产、作业派工、看板作业、报检报工、总检入库、物流发货全流程的单据电子化、流程可视化。
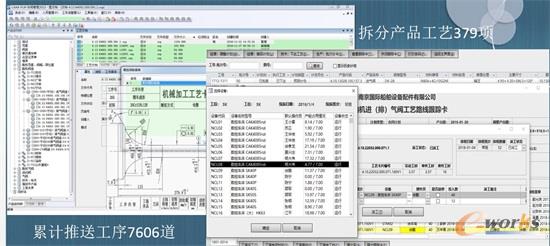
图7 工艺优化
对接业务信息系统,基于亚控组态软件,二次开发并完成关键设备组态监控(SCADA),实现设备状态、工艺参数、设备能耗实时可视化监控,并对过程重要数据进行采集、存储,逐步沉淀工业数据供查询溯源,为后续知识库建立奠定基础。
通过SCADA实现,设备组态互联。设备组态监控系统实现车间现场设备的组态监控、设备管理、现场视频监控、能耗管理、人员管理、设备加工指令推送、设备运行参数实时采集及产品质量追溯与MES制造执行系统直接对接形成对生产任务的闭环管控。
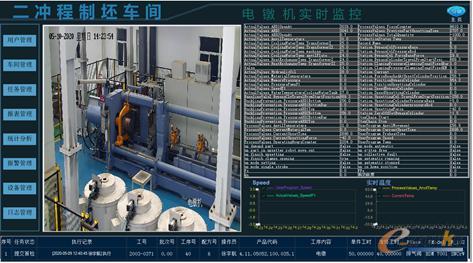
图8 设备组态监控系统
(3)全流程质量管控
引进海克斯康智慧质量管理系统(SQ),基于产品标准建立各工序检测方案知识库并结构化检测数据库,通过无线量具、检测设备数字终端等物联感知仪器仪表,现场采集检测数据并自动对比评判,开展在线检验、质量动态监控,实现质量控制由事后检测向过程控制、事前预防转变。
搭建智慧质量管理平台
智慧质量管理平台作为全面质量管理的中枢系统,首先是和公司PLM系统对接获取气阀的工艺标椎并形成监测方案;然后智慧质量管理平台对接MES系统通过MES系统的生产计划模块下达的检验指令触发相应的检测方案并执行,反馈检测结果到MES系统;最后智慧质量管理平台对接各类测量工具,通过“人、机、料、法”要素的整合,指定具体检测的人员、工具、产品及方法,采集质量数据。
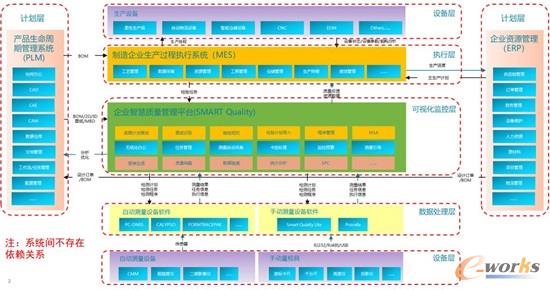
图9 智慧质量管理平台
通过智慧质量管理平台与现有MES系统、PLM系统及测量工具对接,实现质量数据的实时采集、记录及反馈检验结果,保障质量的可控、可调及可追溯。实现气阀生产全流程工艺优化,有效掌控气阀生命周期的目标。
编制质量管理方案
智慧质量管理平台可以直接调取PLM结构化中标椎化工艺直接生成检验计划,对于非结构化的图纸具备接口抓取功能,同时也可以在PDF类型的文件上通过用户手动标记的方式,编制具有视频引导的检测计划。
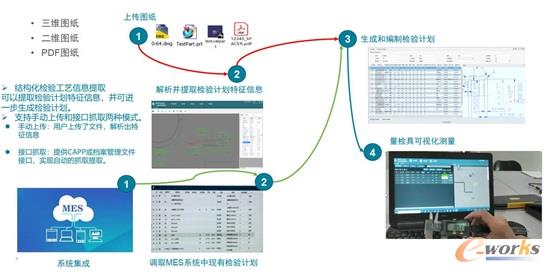
图10 质量检测方案编制流程
质量管理方案的执行
生产车间现场布设固定式检验站以及移动式检验台,智慧质量管理平台通过调取MES系统的检验指令,触发自己检验计划,依据检验计划拆分相关检验任务到具体的检验设备,并通过视频引导的方式,固化检验员操作流程,获取质量数据。
质量可视化报表分析及展示
智慧质量管理平台展示综合可视化看板,主要包括:测量任务统计信息展示,以仪表盘方式显示所有测量任务的统计信息,包括总数、已完成、未完成比率信息;测量结果统计信息显示,以仪表盘方式显示所有测量结果的统计信息,包括测量总数、合格数量、不合格数量比率信息;测量设备统计信息展示及测量设备利用率信息展示。
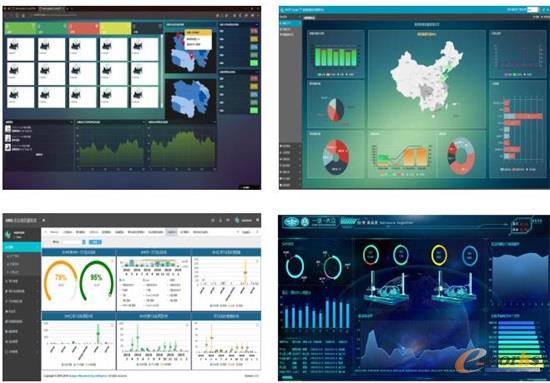
图11 质量可视化报表展示
(4)库存管理
通过和现有ERP系统进行任务对接,实现公司小五金库房的无人化管理。相关任务流程如下:ERP系统下达出入库任务-》任务同步到无人仓库-》无人仓库通过人脸识别系统确定来人身份以及相应的任务单据-》仓库自动开门并通过灯光引导的方式,指导员工拿去相应仓位的物品-》在员工确认后核减相应的库存数据,操作视频监控下完成全程可追溯。无人仓库同时具备工具(主要为量具)的借用以及到期提醒功能。
3)主要创新点和解决的技术难点
集成与智能控制等多领域技术群体突破和交叉融合建立气阀制造全流程设备-信息-质量智能管控平台,属国内首次。
气阀制造过程涉及下料、电镦—锻、后处理等多道工序,涉及多种加工、处理设备及搬运机器人,这些工序和机器的工作要统一管理和协同工作,涉及全流程工艺装备垂直集成、物联感知采集处理、在线监测及自反馈控制、海量数据集成与智能化处理等多项关键技术,定制化开发的智能制造执行系统获取和同步数字化工厂的生产数据,通过认知技术系统支持智能化处理,管控平台又要具备多模态接口(集成、标准、交互)支持制造数据和物料的流动以实现车间和生产线层面的智能化生产。这些工作涉及集成与智能控制等多领域技术群体突破和交叉融合。
3.效益分析
1)项目实施结束后预计所取得的直接效果
本项目大幅缩短质量改善周期,实现气阀生产全流程工艺优化,有效掌控气阀生命周期。借助信息化、数字化技术,在高端智能装备应用基础上,搭建智慧质量管理系统,形成自主核心竞争力,为企业转型升级提供换道超车的重大机遇。
受益于全流程业务透明化,促进了部门协同、精益生产。生产节拍加快,库存占比下降,盘活流动资金约400万元,产能挖潜近20%。
得益于工艺设备成组互联、集成自动化,产品质量稳定性提升,全员劳动生产率提升了55%,劳动强度及安全风险降低;
基于数据驱动创新,打破国外技术垄断,实现船舶配套核心零部件自主可控,研发周期缩短了50%、试验成本降低一半以上,有望快速替代进口、获得国内80%以上市场份额;
横向整合、纵向集成,实现生产全过程数据流和业务流的融合,并基于质量、效率、效益开展数据挖掘利用,促进自主知识产权工艺数据库建立,助力公司成为全球船用气阀隐形冠军,示范了由传统零配件制造企业向研发、制造、服务一体化转型升级,为国内众多实体制造企业数字化转型提供借鉴。
2)项目成果的市场分析和技术成果应用分析
项目实施将使公司全面突破高规格气阀制造关键技术壁垒,除了实现覆盖国内主要中低速柴油机机型的自主化配套外,还将使主要中低速柴油机机型气阀均获得国际主机厂的认证,为公司产品顺利进入全球采购渠道、实现市场份额由国内迈向海外奠定基础,结合智能化提质、增效,预计公司主营业务收入将有大幅度增长、成本将明显下降。
本项目建设实现船用柴油机气阀,高性能、数字化、智能化工厂建设和示范应用,产业化方面大幅降低新产品开发周期,提高产品合格率,具备对气阀生产过程中动态数据采集、监控,并进行处理的能力,实现信息化系统的建立而形成的产业化能力用于促进对大规格气阀的开发和生产优化,快速进行大规格气阀国产化工作,填补国内空白,解决高技术船舶关键部件发展瓶颈。
本文为e-works原创投稿文章,未经e-works书面许可,任何人不得复制、转载、摘编等任何方式进行使用。如已是e-works授权合作伙伴,应在授权范围内使用。e-works内容合作伙伴申请热线:editor@e-works.net.cn tel:027-87592219/20/21。