豫新公司智能化改造主要涵盖了智能设计、智能经营和智能生产,并通过工业网络的构建和安全保障体系的完善实现MES与PLM、ERP的系统高效协同集成。本部分主要对豫新公司智能化改造项目的创新点与取得的效果进行了详细阐述。
基于产品全生命周期智能化改造的实践(上)
三、“智能化改造”模式创新点
(一)MES与PLM、ERP系统的高效协同与集成
以PLM为信息为核心技术数据,其中PLM与ERP双向集成主要包括设计信息与物料信息;PLM与MES单向集成主要包括工艺信息;ERP与MES集成主要包括生产订单与产成品入库。MES和仓储物流的集成实现物料实时追踪和预警,将物料信息与ERP的供应商管理系统进行信息共享;PLM将产品的工艺路线、参数等信息与MES进行互通,进行换型、物料、工艺等生产准备;通过系统集成,打通空调系统产品制造从计划层、控制层到设备层的数据链,实现制造全流程资源要素信息交互,设备、物料、人员等资源通过现场网络进行动态配置,实现工厂的智能生产。
1.PLM与ERP双向集成
PLM系统中的物料编码及物料结构录入到U8系统中,PLM系统中的工时录入到U8编码的自定义项中,PLM系统中增加分工判别标识,对应U8系统中的仓库名称、领料部门名称。
U8系统中的库存、库位、保管员信息,体现在PLM系统中图纸的基本属性页面。
2.PLM到MES单向集成
PLM系统中CAPP模块的工艺BOM信息写入到MES系统的基础数。
3.ERP与MES双向集成
ERP系统中的生产订单信息写入到MES系统。
MES系统中的产成品报工入库信息写入到ERP系统,生成待审核的入库单。
(二)复杂曲面成型技术
1.B型管成型技术
国内B型管成型机与国际先进设备均采用13组成型辊轮作为一套模具,加工效率低、精度不足。本项目关键装备实现模具分段设计,B型管打点成型工艺,旋转摆切的切断结构,点胶系统喷涂钎剂,从而保证产品的加工质量。
模具设计:分段结构便于换型,由一名操作工即可完成。
成型工艺:打点成型工艺导入,提升流道内紊流度,提高芯体换热效率。
切断结构:采用旋转摆切,切断速度快,切口变形量<0.2㎜。
钎剂涂覆:采用先进的点胶系统喷涂,控制精度达0.1g/m。
防错系统:采用视觉传感照相识别,100%在线监测钎剂涂覆质量。
该技术已申报发明专利,并已授权,专利号ZL201510296272.5,专利名称:一种B型扁管成型工艺及其成型模具。并荣获河南省科学技术厅颁发的“科学技术成果奖”,证书编号为9412018Y1087。
(二)在线检测技术
视觉传感在线检测技术,已经应用在豫新公司多个关键装备上。如总成装配线、B型管成型机、芯体转运装备、电池冷却器组装装备等。
系统配备:机器人检测、故障诊断系统,全方位在线检测错装、漏装情况,与追溯系统关联,保存检测结果便于追溯数据来源:机器人携带视觉检测头采集产品信息数据分析:机器人进行分析比对并记录产品检测数据。
(三)质量追溯
通过在车间建立产品档案,记录生产过程中的原材料批次信息、开完工时间信息、加工人员信息、加工工艺路线等信息。对于检测工序,还会记录检测的指标及相关的检测值,从而在系统中建立完整的产品生产跟踪档案,方便后期进行产品的正向及逆向质量追溯,快速定位质量问题。
1.原材料追溯
原材料追溯主要通过定义供应商原材料批次、原材料单件码、投料验证,完成原材料追溯。原材料批次由采购部统一定义原材料批次,并打印出标签粘贴至各物料的最外层包装上。原材料单件码指原材料在采购入库时,本身就带有的单件条码。各原材料在仓库完成分拣并配送至车间后,由车间操作工在投料时完成上料验证。MES系统记录原材料与产成品的关联关系,从而形成原材料追溯链条。
2.生产过程追溯
生产线均采用单件追溯,各单件记录从投料到下线完工的相关生产过程信息,从而形成闭环的质量信息追溯。主要通过员工在MES内的开工、报工、质检等操作,通过与工位机的集成,获取过程质量记录信息。
通过MES系统和SCADA系统的集成对接,以及数据库对现场加工过程数据的实时采集和存储,形成了物料的在线生产过程、产品的质量追溯档案,可以实现在线监控和查询。在MES系统中通过产线配送单查询、工位物料在制查询、设备物料在制查询、投料查询、报工查询、质检记录查询等功能页面,可对生产过程中所需的原材料、操作人员、报工工位、报工时间、质检记录等生产过程信息进行查看,如图14所示。
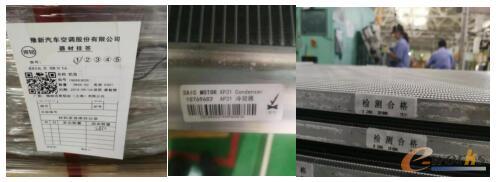
图14 生产过程追溯
四、实施基于产品全生命周期智能化改造实施效果
(一)直接效果
1.质量绩效提升
自项目正式立项至今,根据公司智能制造项目指标要求,电动空调系统产品不良率由0.6%降至0.4%,降低33.3%。
通过对往年自工程不良的分析,对自工程不良的种类进行汇总,产品不良主要有以下几个方面:漏打零部件(螺钉、卡子等)、标牌错贴、壳体断裂、漏贴海绵、相似件错装等缺陷,根据这些常见不良模式进行分析、对策,防呆、防错方案设计,总装车间多年来共计完成投入自动化全过程防错生产线5条,主要用于生产上汽乘用车、东风日产和东风乘用车等市场的产品;该5条生产线均为全过程防错生产线。包含有:激光位置检测防错点50个;通过红外、激光传感器,检查产品风门位置是否运转到位,防止模式混乱流出;传感器防错、漏取点共计92个;取件计数,顺序防错,防止小件的错漏装,螺钉计数全工位覆盖;对各个工位的螺钉进行计数,完成后产品方可放行。
重点零部件、相似零部件扫描防错全工位覆盖;对重点零部件可以根据部件上的条码或二维码进行单台追溯,在工控机上可进行正逆向查询。相似零部件可进行条码或二维码识别判断,防止相似件的错装。
防异物落入全工位覆盖,可根据产品不同随时增减,调整位置;主要防止螺钉、卡子小件掉落产品内部,造成空调异响。
2016年自工程不良率=不良总数/产出总数=3563/593696=0.6%
2020年(1-11月)自工程不良率=不良总数/产出总数=1526/391539=0.39%
不良率降低率=(2016年不良率–2020年不良率)/2016年不良率=(0.6%-0.39%)/0.6%=35%
结论:通过智能化改造手段,产品不良品率降低了35%。
2.客户满意度提升
豫新公司通过产品全生命周期智能化改造模式创新的应用,在产品保证、质量追溯等当面取得了较大的进步,在主车厂市场质量绩效得到明显提升,助推某市场SSC评价(对供应商质量绩效的评价)得分在2020年提升至一级水平,另外一重要客户在2020年零公里不良方面同期相比下降53.7%,有效地保证了产品的质量和交付。
(二)衍生效应
1.经济效益
豫新公司以市场为导向,通过新建生产线或对原有生产线进行智能化改造,提升电动空调系统生产效率和产品质量,生产线大量使用工业机器人、高档数控设备、智能检测、专用高效装配等设备,建立PLM、ERP、MES等系统的集成和数据互通,实现了机器人转运、机器人焊接、RFID识别,在线视觉检测防错等技术的全面应用。项目实施以来,豫新公司换热器产能由之前的350万台/年提升至500万台/年以上,空调总成产品产能由之前的150万套/年提升至200万套/年以上,生产效率和质量水平显著提升,公司营业收入由2015年的5.4亿增加至2020年的9.2亿,复合增长率为8.1%(2020年受疫情影响略有下降)。经营模式向智能制造的转型升级在其中发挥作用非常明显。
2.设计验证能力明显增强
项目智能设计模块的完善与提升,通过CATIA与PLM集成,实现线上协同设计功能,所有数模可实现一键调用;通过函数定义特征尺寸和知识工程库文件的方法,实现产品的数字化研发,三维数模设计效率提升30%;通过PLM与CAPP集成、定制工艺文件映射关系、新建工艺知识库等,实现设计、工艺一体化、工艺全过程在线策划等功能,工艺文件编制效率提升40%,工艺数据传递准确率达到100%;通过各项模型仿真、流场仿真、应力仿真等获得了产品性能各项参数据,充分验证了产品设计的各项功能,实现了产品设计全生命周期的转型,有效提升了本单位技术创新能力,也为类企业树立了良好的技术创新示范。
本文为e-works原创投稿文章,未经e-works书面许可,任何人不得复制、转载、摘编等任何方式进行使用。如已是e-works授权合作伙伴,应在授权范围内使用。e-works内容合作伙伴申请热线:editor@e-works.net.cn tel:027-87592219/20/21。