本文为“2021年度中国智能制造最佳应用实践奖”参评案例。本次活动将评选出2021年度,为中国智能制造领域带来突出效益的最佳实践工程,全面介绍企业推进智能制造的步骤、重点与难点、获得效益等,分享建设过程中的经验,供广大制造业行业企业学习供鉴。
一、企业简介
北京首钢股份有限公司(简称“首钢股份”)是首钢集团所属的境内唯一上市公司。首钢股份于1999年10月由首钢总公司独家发起募集设立,1999年12月在深圳证券交易所上市(证券代码:000959)。
首钢股份拥有迁钢公司、首钢智新迁安电磁材料有限公司,控股首钢京唐钢铁联合有限责任公司、北京首钢冷轧薄板有限公司等钢铁实体单位,具有焦化、炼铁、炼钢、轧钢、热处理等完整的生产工艺流程。首钢股份拥有国际一流装备和工艺水平,具有品种齐全、规格配套的冷热系全覆盖板材产品序列。其中,电工钢、汽车板、镀锡板、管线钢、家电板,以及其它高端板材产品处于国内领先地位。首钢股份紧密跟踪客户需求,通过加强交货组织和质量管控,加快先期介入推进步伐,提高客户需求响应力度等措施,为客户提供优质产品和增值服务。
首钢股份坚持向世界一流水平看齐,汽车板产品实现铝镇静钢、IF钢、高强IF钢、烘烤硬化钢、低合金高强钢、双相钢、相变诱导塑性钢和热成型钢等全系列整车供货产品全覆盖,强度级别达到1000MPa,市场占有率跻身国内前三。

图1 北京首钢股份有限公司
二、企业在智能制造方面的现状
首钢股份具有炼铁、炼钢、轧钢、热处理等完整的生产工艺流程,拥有国际一流装备和工艺水平,具有品种齐全、规格配套的热系全覆盖板材产品序列,拥有年产780万吨铁、800万吨钢、780万吨热轧板卷的生产能力,汽车板、管线钢、家电板以及其它高端板材产品处于国内领先地位。在“十三五”期间首钢股份以“两化融合”、“中国制造2025”、“工业互联网”等国家战略为方向,不断尝试在信息化、智能化和工业化高层次深度融合发展方面创新实践,稳步推进企业数字化转型。
2017年7月-2019年6月,首钢股份完成了“首钢钢铁产销一体化经营管理系统”建设,产销一体化系统做为跨地域、多基地、一贯制的协同管理平台,涉及生产、质量、销售、采购等11个业务领域、50套信息系统,构建了一体化代码体系、一体化采购体系、一体化营销体系、一贯制制造管理体系、供应链生态协同体系、设备全生命周期管理体系以及业财一体化体系,实现了跨基地的物质、信息、资金三流合一,实现了数据、系统和业务的“纵向贯通、横向集成”,实现了产销一体化、管控一体化、业财一体化,提高了公司生产经营的精益化和智能化水平。
同时,为有效支撑首钢股份数字化转型发展要求,实现更深层次的数据驱动和智能决策,2018年以大数据及云平台为核心的数据中心正式投用,该数据中心按国际标准T3等级建设,配备计算和存储资源419台套、安全管理设备29台套、接入网络互联专线21条,能够满足各基地业务数据异地灾备的连续性要求,实现基础信息资源配置向共享、节能、稳定、高效的发展方向转变。大数据平台采用分布式数据仓库+HADOOP平台混合架构,实现现场工艺生产数据和业务运行数据采集超过18万余项,全类数据日增长量超过80G、折合吨钢5.7M。基于海量的生产运营数据,首钢股份正在尝试通过大数据挖掘应用、人工智能等技术手段,开展数据监控分析、业务辅助决策、生产过程控制与分析优化、生产管控优化等领域的智能决策探索,实现数据对业务的驱动。
在数据监控分析和业务辅助决策方面,“十三五”末期首钢股份开始推进业务模型构建,实现业务过程数据的一键分析、异常因素的自动揭示、可能原因的智能推荐。目前已有40项业务决策模型投用,直击业务难点、打通数据壁垒,如产品性能风险管控可提升3倍分析效率、物料标准化周期管控可降低约1.2万吨半成品库存、投料率分析可辅助降低酸洗带出品1.47%等,在提升流程管控效率和决策智能化水平的同时,创造了实际的价值效益。而就如何确保源数据的准确性及跨系统传输数据的完整性,有效释放和缓解人力资源的问题上,首钢股份启动了RPA流程自动化项目,实施了15个RPA软机器人。目前已在数据自动录入、业务系统自动操作、跨系统数据核对等方面推行了44个自动运行的业务流程。各流程效率均有3到5倍的提升,平均可节约工时41.3小时/天,且做到了业务操作零错误,初步达到了为公司引入数字化劳动力、提升人力价值的目的。
在现场生产管控优化方面,首钢股份也在积极尝试机器学习算法在过程控制领域的应用和对外方一二级系统的消化完善,开展了“轧制力优化”、“质量缺陷分析判定”、“燃烧过程最佳策略”等过程控制优化模型的研究,进一步提升了过程控制模型的控制精度。基于图像识别的钢包洁净度自动判级、钢包顶升位置智能检测、钢板表面缺陷自动判级等场景也逐步趋于成熟,大大增强了生产过程的感知能力。现场工艺数据采集平台、工艺控制模型优化等均为“十四五”时期推进生产控制层的工业互联网建设奠定了良好的技术储备。
三、参评智能制造项目详细情况介绍
1. 项目背景介绍
首钢产品定位以高端家电、汽车以及制造用钢为主。电工钢生产规模居全国第二,汽车板市场占有率全国第二,成为包括日系、德系等前十重点车企供应商,并连续三年蝉联宝马、长城、北汽等车企第一大供应商。高端用户追求零缺陷交货,对生产过程中质量稳定性要求更为严格,依赖人工过程控制无法实现过程的精准管控,缺陷发生率较大。因此首钢以“追求零缺陷、实现高精度、提高客户满意度”为目标,搭建大数据平台,利用在线检测、机器学习、图像识别、数据建模等技术,实现质量过程监控与判定、表面质量智能检测与判级、全工序质量缺陷追溯以及过程能力评价分析等,以机器智能决策,提升了产品过程质量的管控能力,从而在快节奏和大规模生产下提高产品的稳定性,降低成本损失,满足客户个性化需求。
主要问题表现在:
(1)产品质量过程管控以人工管控为主,检验结果依赖检测人员的经验,具有片面性,检验效率低,质量事故一旦发生就是批量事故,无法及时调整,损失不可挽回。
(2)产品对表面质量要求比较高,轧钢工序表面质量缺陷数量和种类多,传统表检仪分类准确率不足80%,需岗位人工评审,严重影响后工序的生产,跨工序的质量缺陷追溯异常困难。
(3)产品质量数据来源众多,存在大量异构数据,不同粒度数据分布在不同平台,在进行质量分析中数据收集和整合耗费了分析人员大半的时间,缺少统一平台和方法对庞大的质量数据开展有效的开发和利用。
项目主要目标:
- 自动判定率提高到100%
- 判定周期缩短到5分钟之内
- 临时封闭率下降15%
- 现货发生率下降4%
- 返修率下降0.7%
- 缺陷分类准确率提高10%
2. 项目实施与应用情况详细介绍
2.1项目规划
整个项目以打造一贯制质量控制体系为核心,全面梳理质量管理的现状、目标及差距,对组织机构、业务流程进行优化。收集、整合炼钢、热轧、冷轧的生产过程数据,结合六西格玛管理理念,利用统计方法、数学模型及技术,实现生产过程数据的监控、诊断、挖掘,打造一体化管理平台,达到钢铁制造企业“用数据说话”的管理目标。
(1)搭建一贯制管控平台,结合六西格玛管理理念,利用SPC控制图及多种统计图形,进行多工序、全流程过程质量分析与监控,并优化产品质量设计,提升生产管控和质量过程控制水平,实现一贯制质量管控。
(2)结合在线判定技术,实现全流程过程质量监控与跟踪,快速在线质量判定,强化过程控制,实现分类分段管理,降低生产成本,实现全流程的动态质量控制。为生产用户提供了在线判定、质量预警、质量控制等多方面的功能,使质量判定自动化、智能化,从铁水进站开始进行质量监控,减少后道工序的不合格产品生成机率,避免不必要的产品浪费和人力、财力损耗,对推动高端板材的生产起到了积极的作用。
(3)利用数据仓库及机器语言建模技术,寻找最优模型,精确定位质量要因,实现产品质量持续改进,提高客户满意度。
钢铁全流程过程质量管控,基于“两化融合”的方法论,结合六西格玛及PDCA的管理理念,将信息系统与质量管理完美结合。利用图像识别、精准的数据标注技术、人工智能卷积神经网络(FCN)、缺陷特征提取、统计方法、数学模型及技术,研发质量监控、判定、诊断和优化分析方法,实现了融数据监控、诊断、挖掘、决策于一体的可扩展、高可配的全流程过程质量管控,满足精细化质量管控要求,实现产品质量全面提升。
2.2功能介绍
全流程过程质量管控包括智能质量过程判定、跨工序质量追溯分析两个部分。
智能质量过程判定实现了过程、表面以及性能的判定与监控。将多源异构数据融合,结合数字化的产品质量控制规则,实现在线实时监测产品制造工艺过程是否波动和自动判定产品等级;实现表面质量缺陷的采集、识别、归类、判级、上下工序缺陷的传递以及自动推荐处置意见;实现了性能管控的自动预测、分析与异常推送。
跨工序质量追溯分析实现跨工序质量缺陷统计探索性分析、智能化追溯及快速定位。利用统计分析工具,将工艺过程控制和表面缺陷相关的数据进行深度分析和挖掘。 利用过程能力指数、SPC 统计分析、聚类算法等高级分析工具和方法解决快速定位问题,实现产品质量的持续改进。业务流程如图2所示,功能架构如图3所示。
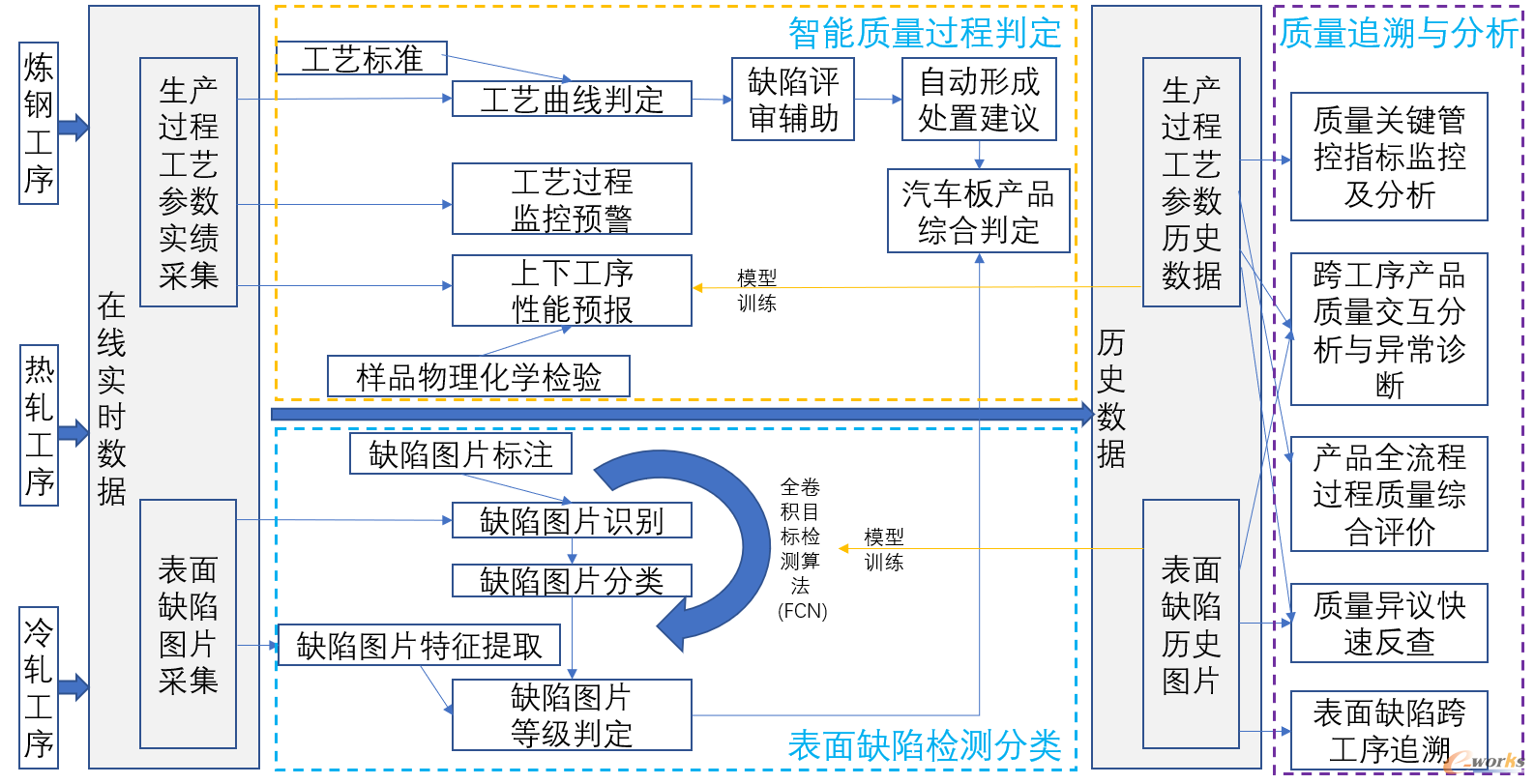
图2 业务流程图
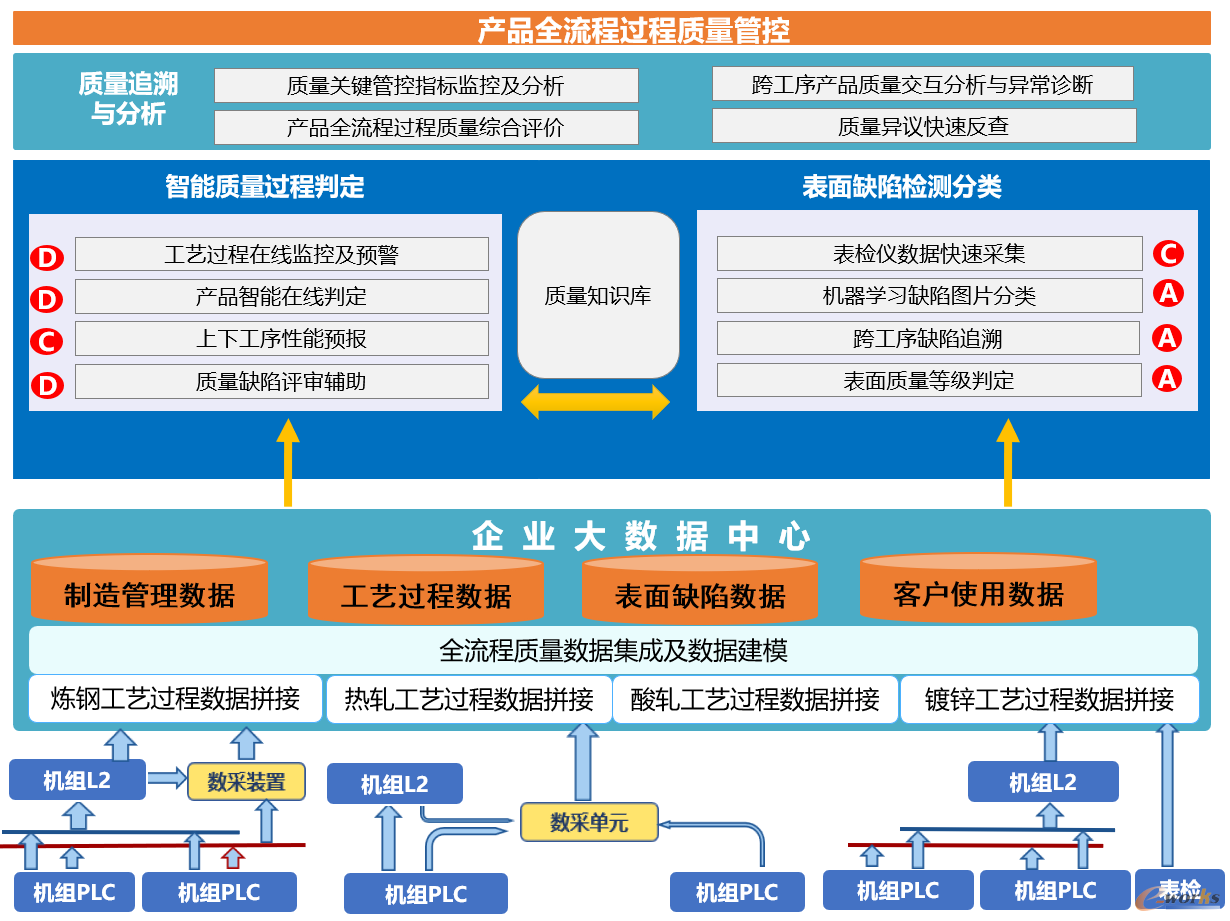
图3 功能架构图
智能质量过程判定
为实现炼钢、热轧、冷轧全流程质量一体化管控,利用流数据处理、多源异构数据融合、特征提取、关联分析与预测、人工智能卷积神经网络等技术,构建质量模型库、知识库、规则库、约束库、规则库,实现板带钢性能、表面、尺寸、板型、成分、工艺等在线质量自动判定与监控预警。为质量问题定位、产品质量提升提供依据和途径。
(1)实时数据采集与融合
通过工业大数据平台,利用实时数据流处理和多源异构数据融合技术,对L1、L2、L3以及L4系统中数据进行毫秒级颗粒度采集,实现跨工序、多数据源、差异结构、不同粒度的工艺、质量数据的实时数据流处理及数据融合,实现统一集中信息共享,对物料生产过程中的时间、位置、事件、状态、图片等数据进行跨时空融合转换。数据处理技术流程如图4所示。
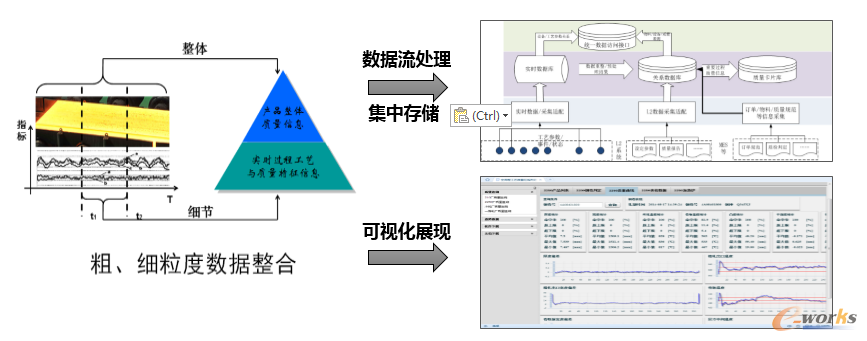
图4 数据处理技术示意图
(2)过程质量监控及预警
为实现工艺过程参数的实时预警和机组判定,保证产品质量全程一致性,对重要工艺过程参数、质量参数进行实时在线监控、预警和判定,向操作人员提供作业预警信息,保证批次内产品质量稳定性。预警方法主要提供了简单的参数超限报警方法、SPC 统计控制方法、神经网络模型预测方法等,各工艺参数控制限可根据企业技术标准或设定参数等进行灵活配置。 另外为了保证产品过程质量一致性,研发了基于规则推理的产品质量在线判定引擎,对过程工艺参数和质量参数进行物料全长的评级,评级结果作为质量判定的重要依据。
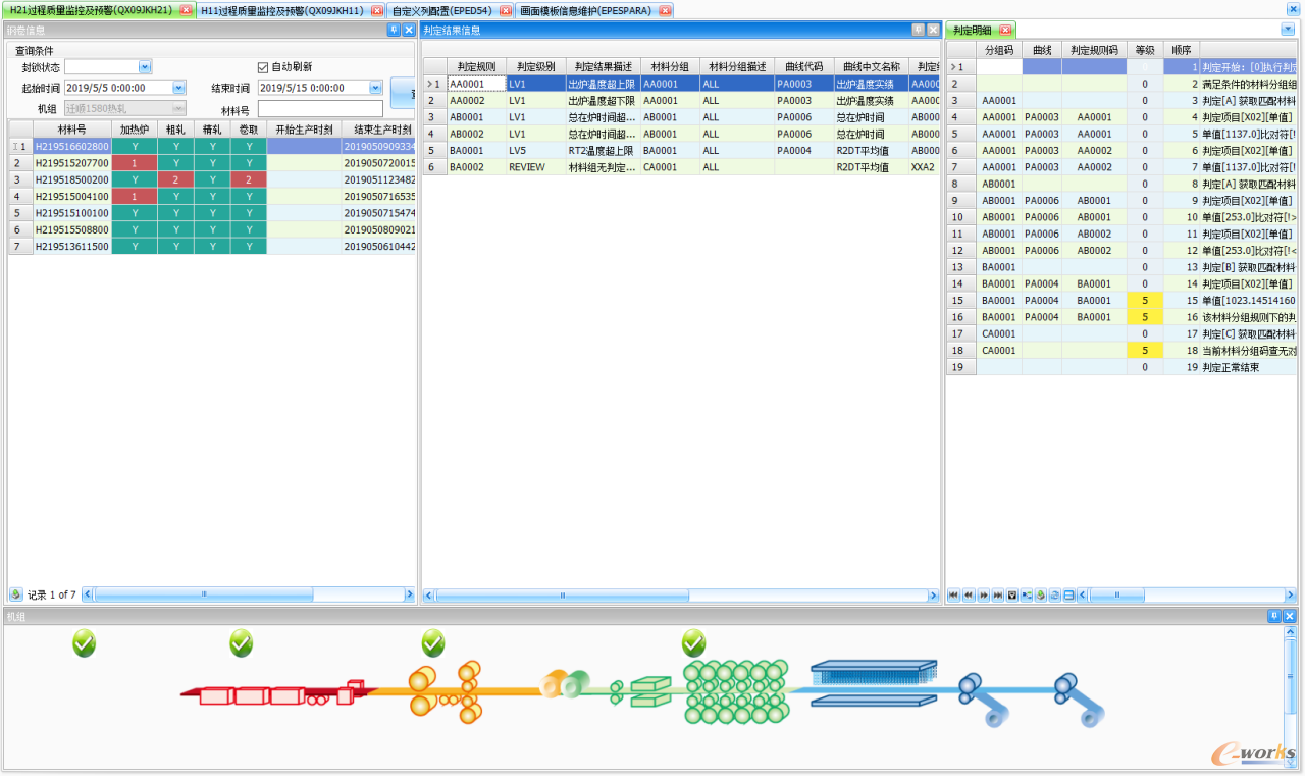
图5 过程质量监控功能
(3)精准质量在线判定
1)基于客户需求的分段判定
基于工业大数据平台采集、融合后的数据,通过特征提取技术,针对不同客户需求、不同品种牌号,以生产过程各工序质量控制要求为基准建立可配置的、分类分段的在线判定规则库,实现炼钢、热轧和冷轧的全流程质量在线判定。质量在线判定对产品质量作出的判断,为产品的降级处理或分段销售打下了基础。
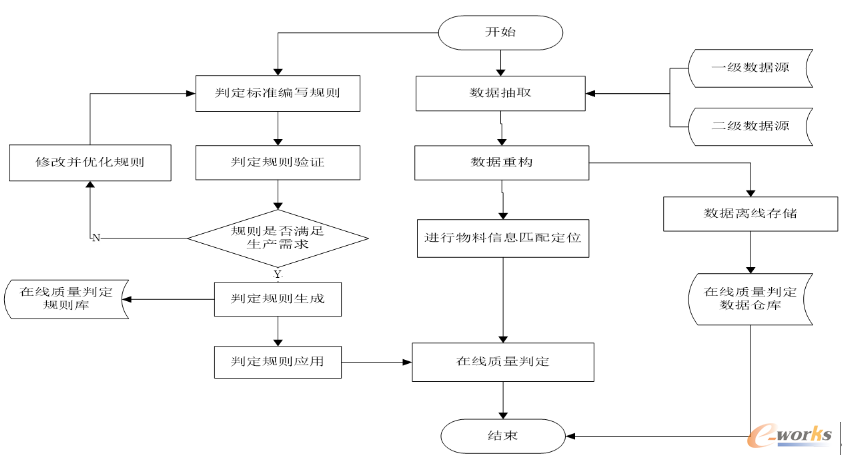
图6 工艺在线判定流程图
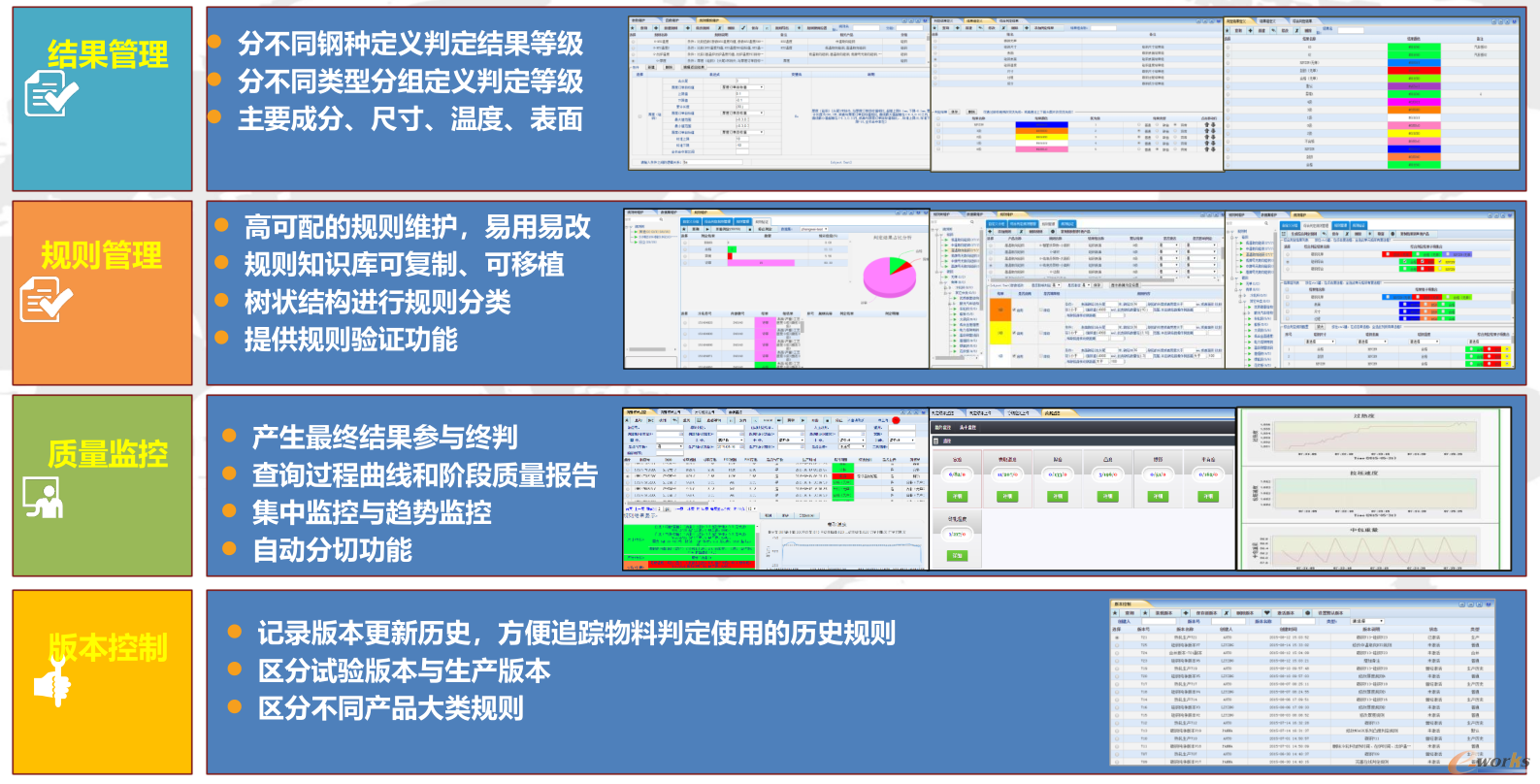
图7 工艺在线判定核心功能示意图
2)基于图片识别的表面分类
板带钢产品的表面质量是最重要的评价指标之一,板带钢表面夹杂物、氧化皮、孔洞等缺陷不仅影响产品的外观质量,而且还会降低产品的抗腐蚀性、耐磨性和其它强度性能。目前我国大多数钢铁企业采用闪频光检测、基于 CCD 成像检测等表检系统,但表面缺陷识别的准确率均不高,检出率和分类率约为80%,因此亟待实现高精度表面识别及在线表面判定。
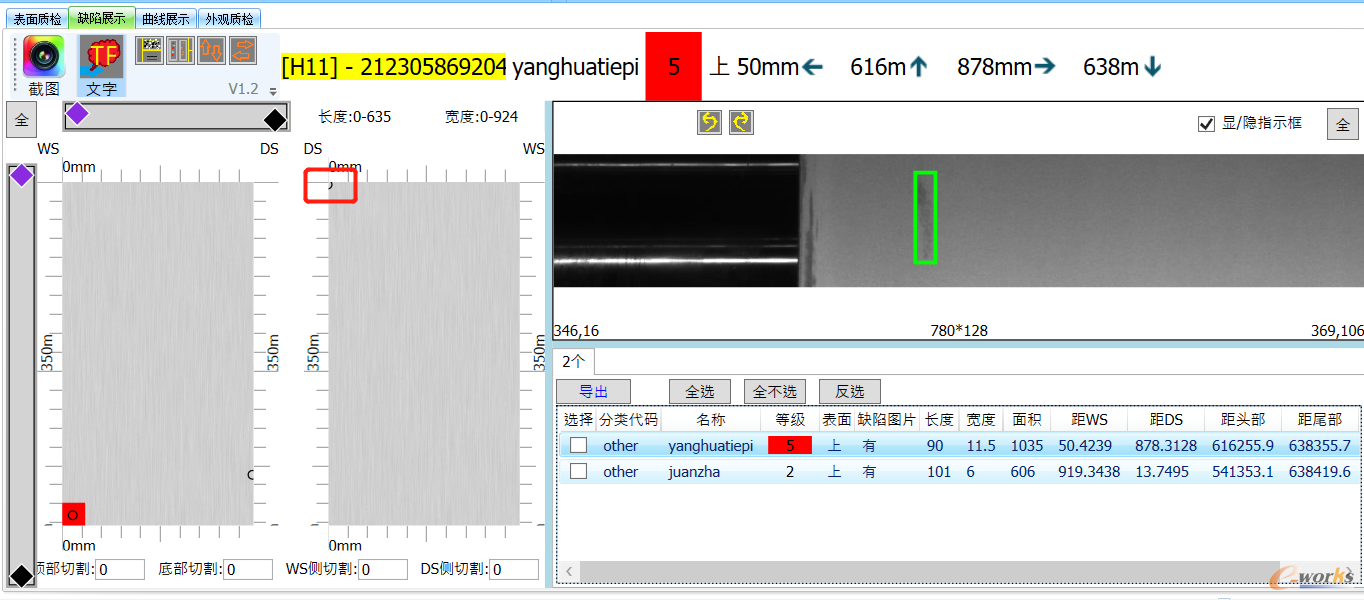
图8 表面判定系统界面
表面判定模块利用高效的数据采集技术、精准的数据标注技术、人工智能卷积神经网络(FCN)、缺陷特征提取、依据配置规则的缺陷合并、依据规则的缺陷分级,实现板带钢表面缺陷识别及在线判定,提高缺陷整体的识别率。同时针对细小缺陷特征丢失现象,采用多尺度特征金字塔融合算法将自顶向下的上采样与自底向上的下采样特征图按像素融合,对Faster R-CNN算法进行改进,提高对细小缺陷的检测和识别率。技术实施步骤如图9所示。
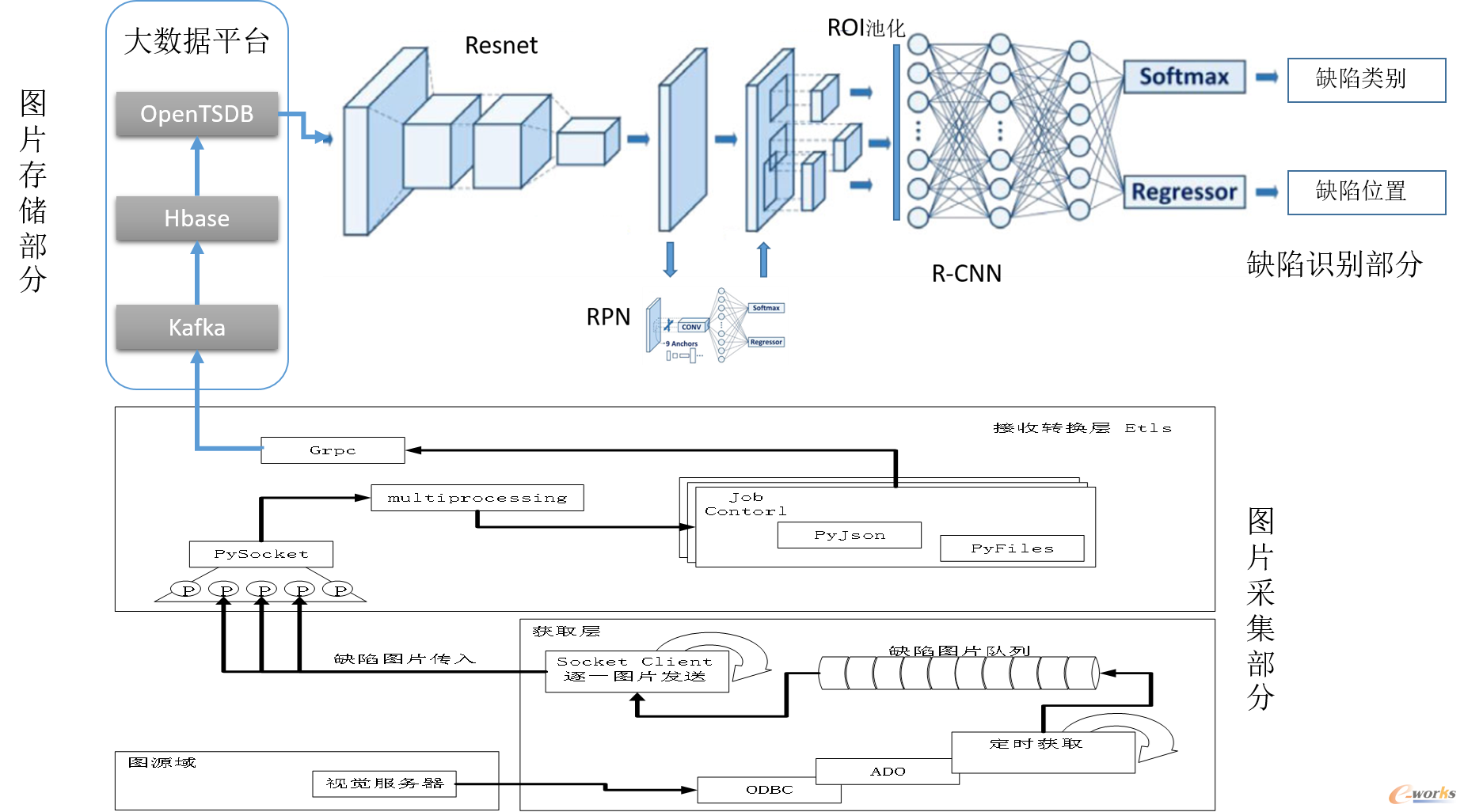
图9 带钢表面缺陷识别技术方案实施步骤图
3)基于多元回归的性能预测
利用相关性分析及特征值预测在海量数据中查找产品性能相关的关键影响因子,挖掘现有工艺方案、工艺标准中的生产工艺规律和生产指标特性。利用物理冶金学模型和信息化技术,对生产过程中各种物理冶金现象进行综合数值模拟,依据各关键指标之间的复杂关系和作用机制,对其中稳定可靠的品种推导前后工艺环节的性能预测模型。性能预测功能界面如图10、11所示。通过数据自动收集与模型运算,直接预测轧后的产品性能,作为轧线“余材充当”和“精准选样”的依据,取消牌号的开卷、取样及性能检验,降低取样成本,提高成材率。
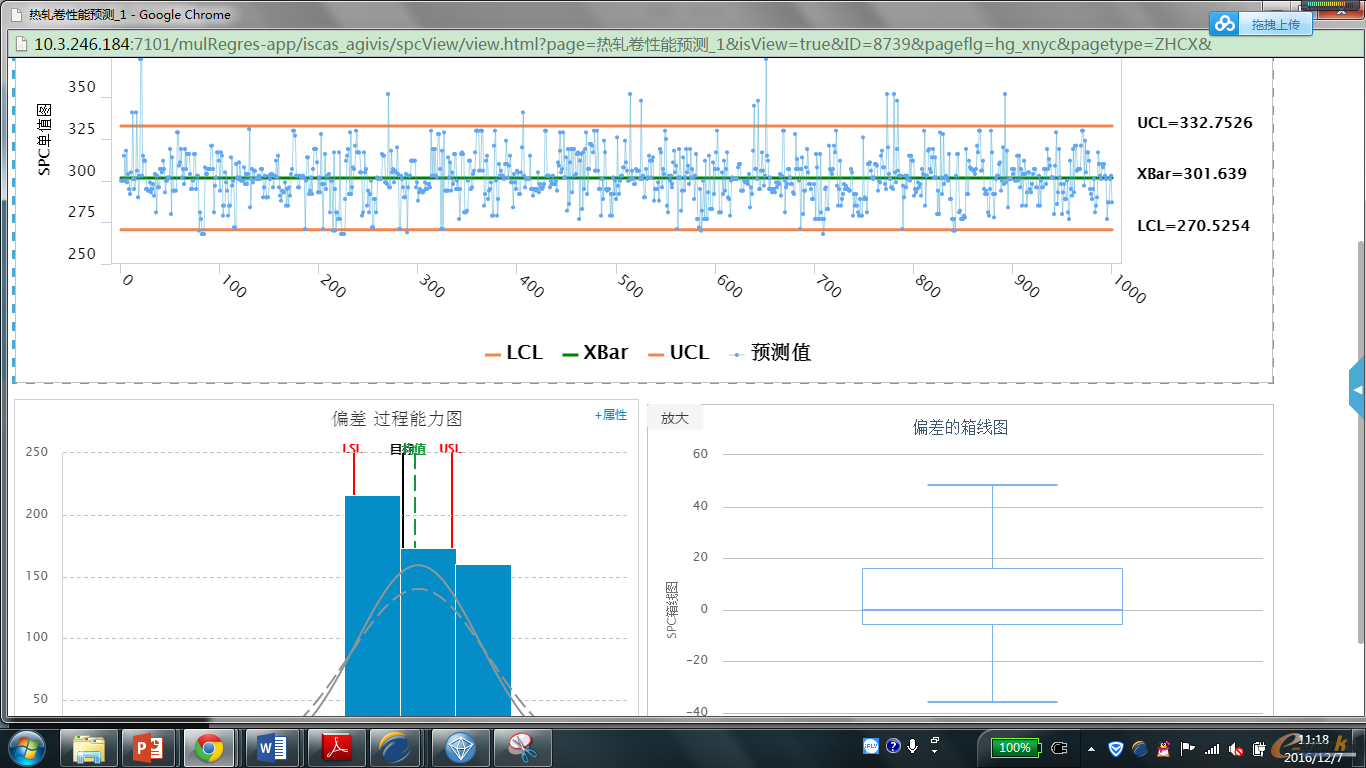
图10虚拟数据预测,用于试制产品性能预测
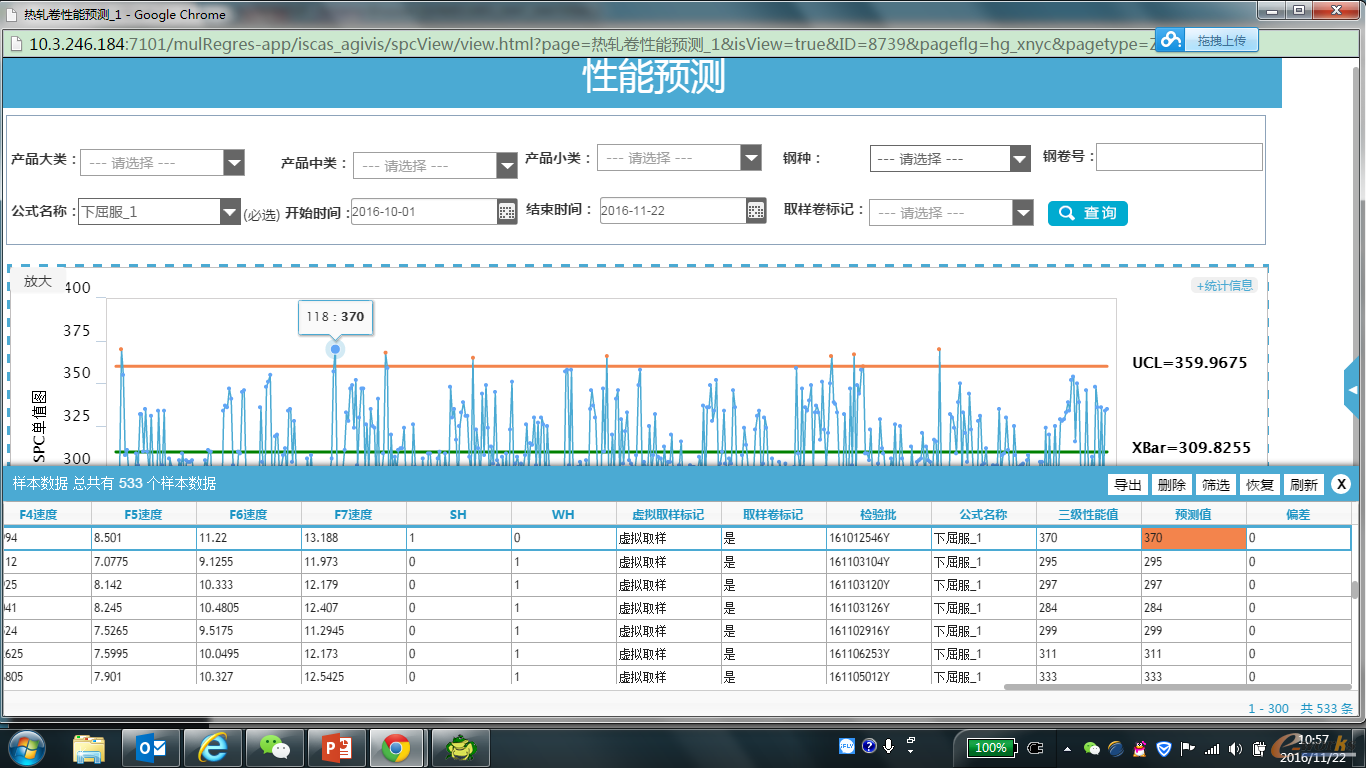
图11 单值预测
4)基于决策模型的智能分切
面向质量缺陷处置环节,利用物料规格、订单要求、尺寸、性能、表面类综合判定结果等数据进行多维度的综合分析及推理。构建质量处置决策模型,引用时空转换技术、关联分析及预测算法,考虑物料质量异常部位、分切后产品的完整性、设备计长误差、工序位置平移、表面缺陷、外观缺陷、性能缺陷、分切后订单的兑现等诸多因素,一键式得出缺陷处置指令。构建智能分切知识库,根据质量判定规则,挖掘曲线特征值和钢种大、中、小类、厚度、宽度规格的评审结果对应关系,确定缺陷点,再根据连续标准将缺陷进行合并,给出曲线处置意见及缺陷距头尾位置,指导切头切尾等后工序任务,为连退、镀锌、重卷等工序智能分切提供支撑,减轻各生产环节产生的质量缺陷对成品的影响。
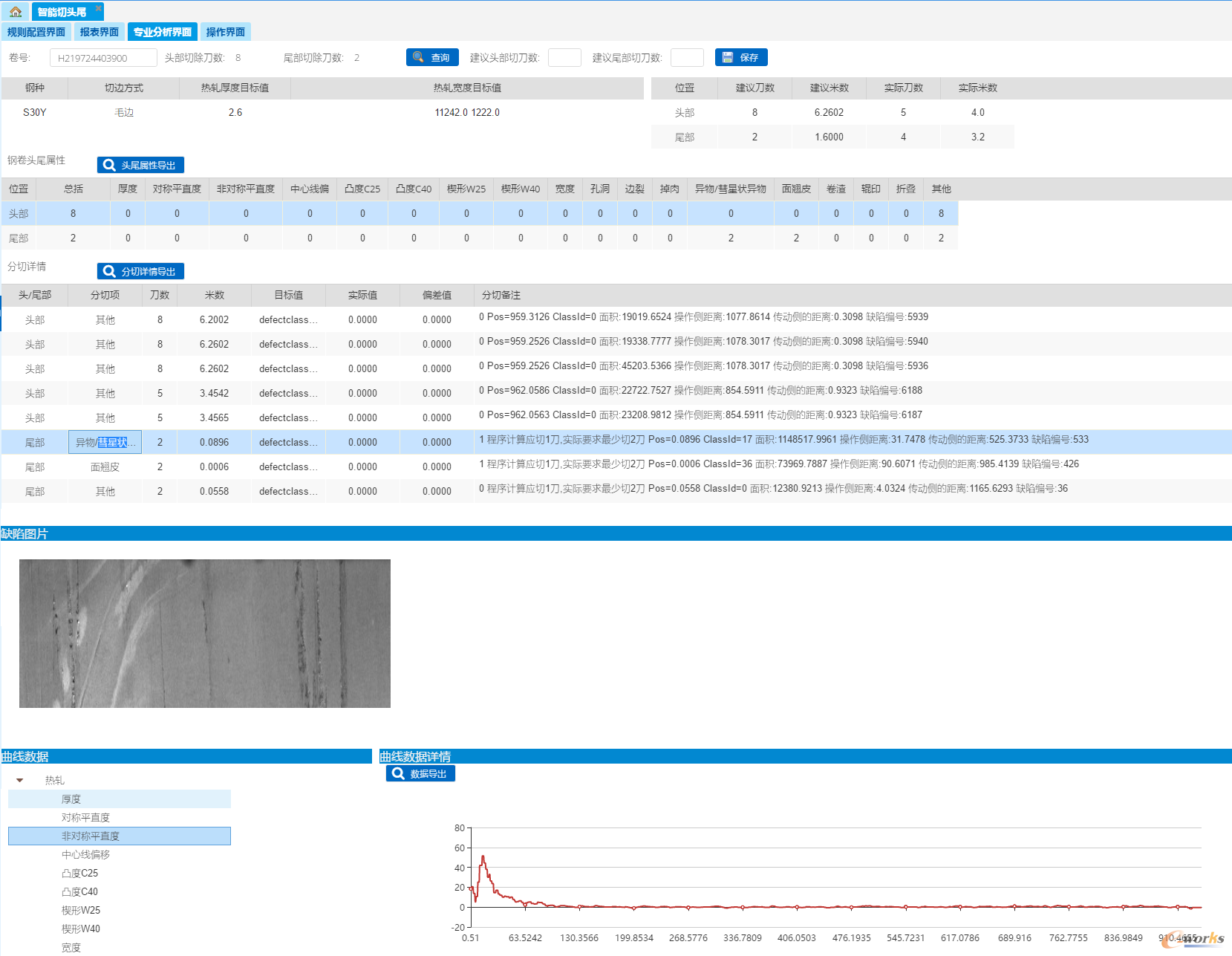
图12智能分切功能界面
全流程质量追溯及分析
全流程质量追溯及分析将智能质量过程判定和表面缺陷检测分类形成的结构和非结构数据,都存储到工业大数据平台中。主要支撑质量关键管控指标监控及分析、产品全流程过程质量综合评价、跨工序产品质量交互分析与异常诊断、质量异议快速反查和表面缺陷跨工序追溯等。
利用系统提供的样本散点图、样本运行图、均值运行图、箱线图、等值线图、相关性散点图、频度分布图、Pareto 图等多种常用统计分析图进行数据探索性分析,利用过程能力指数、SPC 统计分析、聚类算法、关联规则、决策树分类、参数差异性分析、序列模式分析、工艺规则提取等高级分析工具和方法解决快速定位问题,利用仿真和工艺优化功能等实现工艺参数或规则知识的优化,实现产品质量的持续改进。质量分析图形化展示如图13所示。
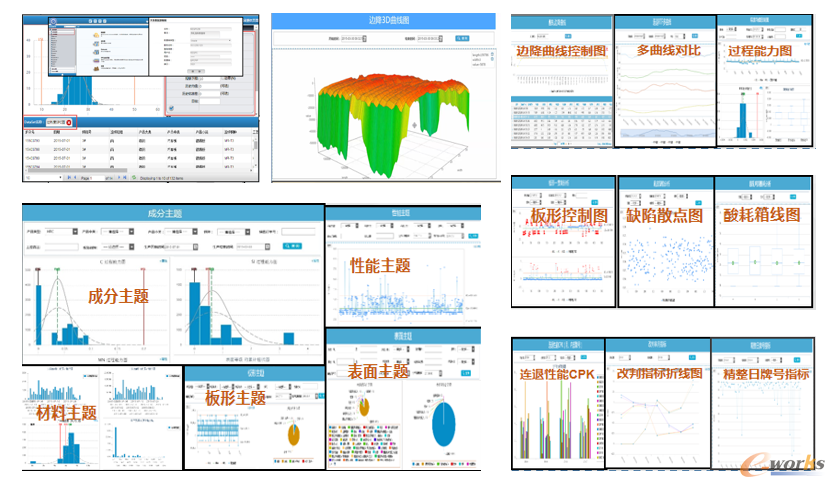
图13 图形化展示自定义分析
(1)表面质量缺陷遗传性追溯
采用多工序工艺质量数据协同处理方法,根据不同工序、不同设备的工艺参数和质量缺陷等的对应关系,进行数据的统一处理和分析,以提高质量追溯和问题定位的准确性,尤其是进行工艺质量遗传性分析。通过传统规则设定和大数据模型计算两种方式,对带钢厚度检测、表面缺陷分布、工序平移、规格变化、开卷次数、翻面次数等各种与质量相关信息进行综合处理运算,以满足跨工序快速定位缺陷的要求,自动给出前后工序缺陷对应位置和最佳匹配缺陷,实现缺陷的一贯制快速反查。技术路线图如图13所示:
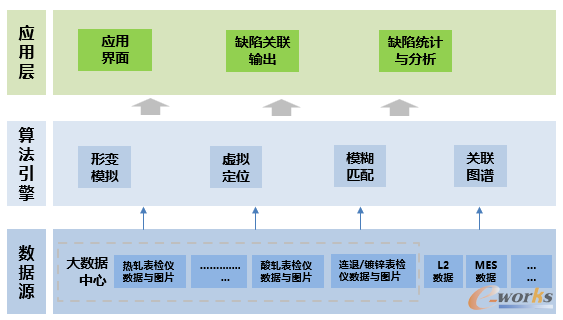
图14 技术路线图
如图15所示,板坯、热轧钢卷、冷轧钢卷之间存在表面缺陷位置、大小等对应关系,如果板坯上表面缺陷经热轧、冷轧后仍然存在,则该缺陷在热轧卷、冷轧卷上的位置、大小、左右侧均会发生变化。表面质量缺陷遗传性追溯功能界面如图16所示。
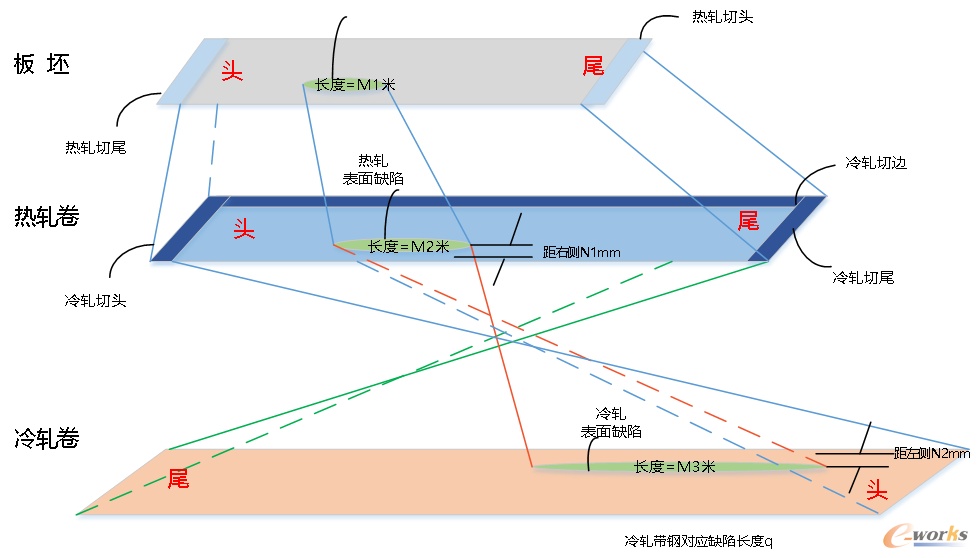
图15 表面缺陷示意图
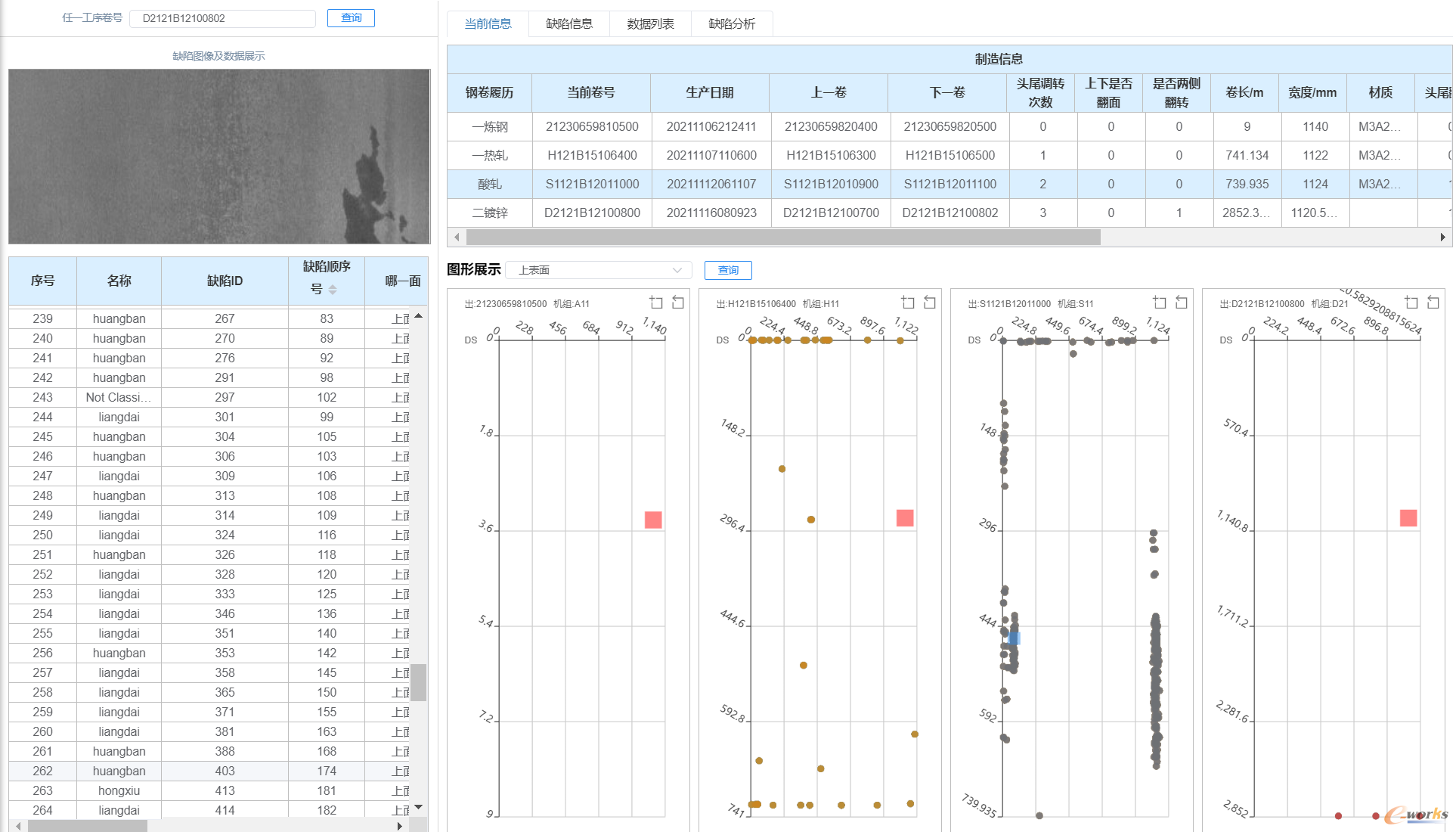
图16表面质量缺陷追溯系统界面
(2)重点管控指标监控及推送
通过数据的清洗以及数据主题的构建,实现跨工序工艺参数、质量数据的交互式正向追踪、逆向追溯,形成供业务人员进行分析的基础主题数据,最终通过可视化组件进行图形化展示(如图17),对业务的自定义分析具有很好的效果。另外对于关键指标进行自动统计、原因自动定位以及异常主动推送,方便业务人员及时发现异常问题,调整现场工艺。
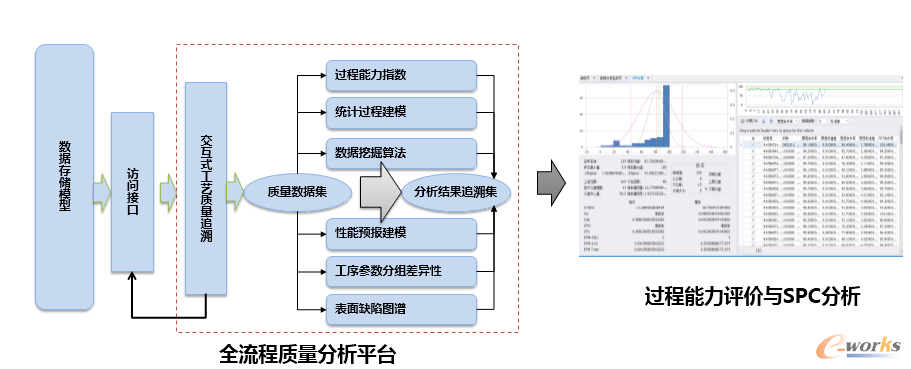
图17质量分析和图形化展示
(3)跨工序产品质量异常诊断
跨工序产品质量异常诊断是对产品工艺过程参数进行全流程跨工序的全面分析的过程,对于把握整体质量控制水平和进行异常诊断具有重要的指导意义。
跨工序工艺曲线与表面缺陷联合分析,按物料树,将钢后工序的工艺曲线和表面缺陷集成到一个画面中进行对照分析,如图18所示。并可通过单卷分析和多卷查询对比进行分析,针对不同物料的同一工艺参数,进行对比,找出差异及异常,如图19所示。
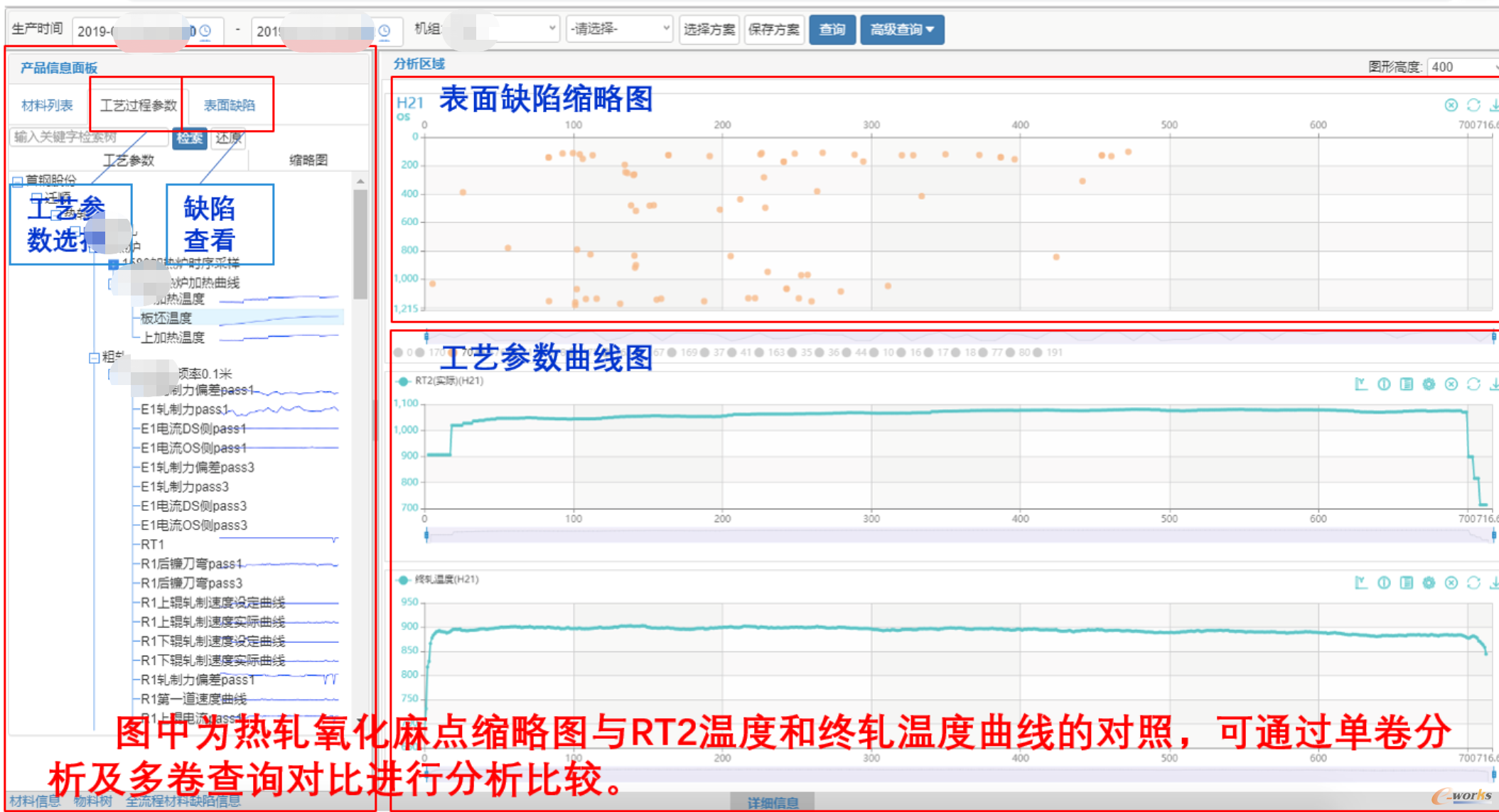
图18跨工序工艺曲线与表面缺陷联合分析图
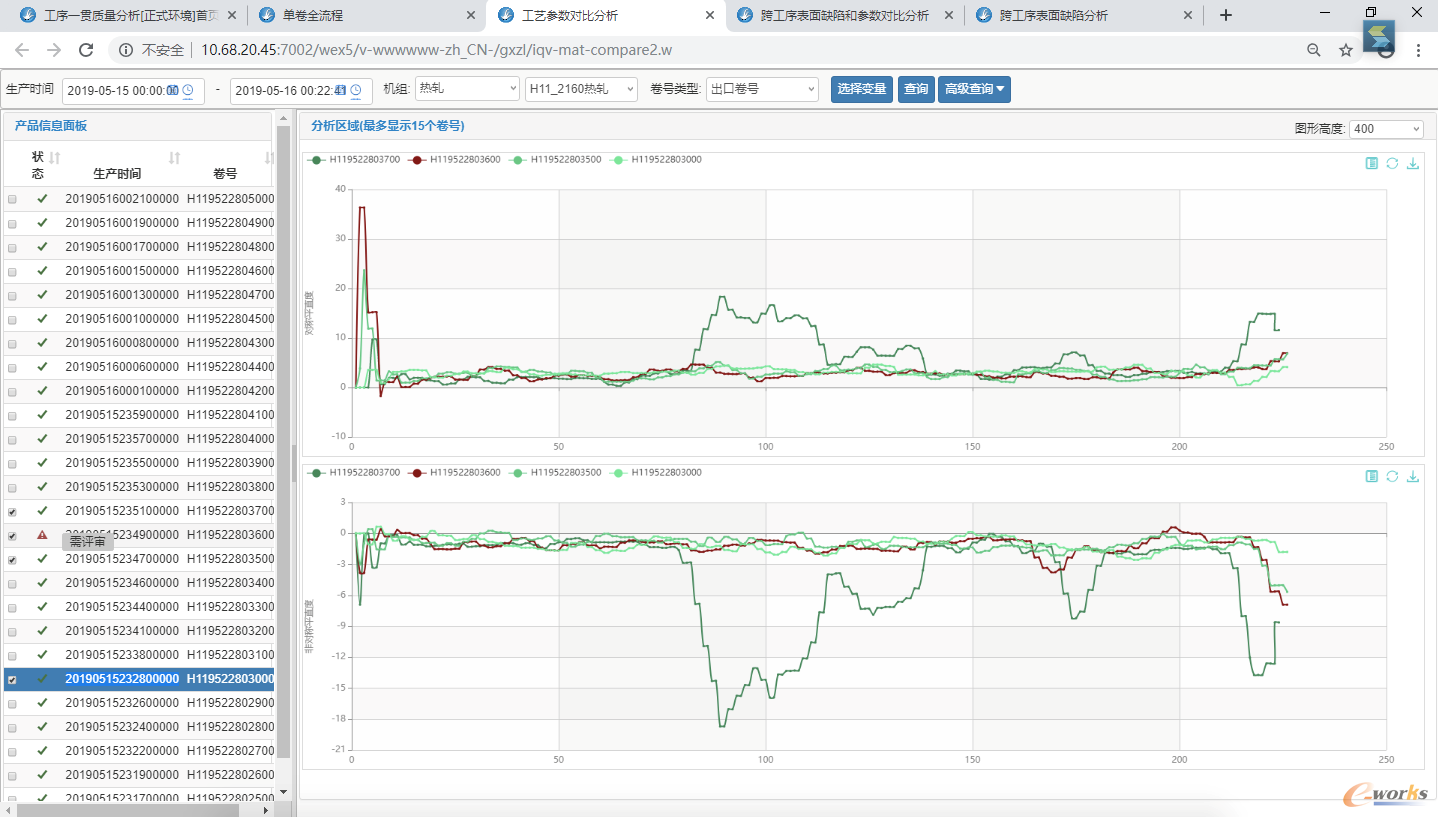
图19异常诊断功能界面
(4)客户质量异议快速反查
针对表面,尺寸,板型和性能这几类异议按照可能影响到异议产生的材料基本信息(包含材料的卷号、机组、牌号信息、合同规格要求等数据),过程参数信息(主要包含各种高频曲线、曲面数据,以及相应的单值数据),质检判定信息(包含在线系统判定结果信息,以及粗糙度、抗拉强度等实验信息)进行集成,承接客户服务系统质量异议及抱怨可以快速的查询到异议卷的生产,质检和放行信息,从而进行质量异议的综合分析。
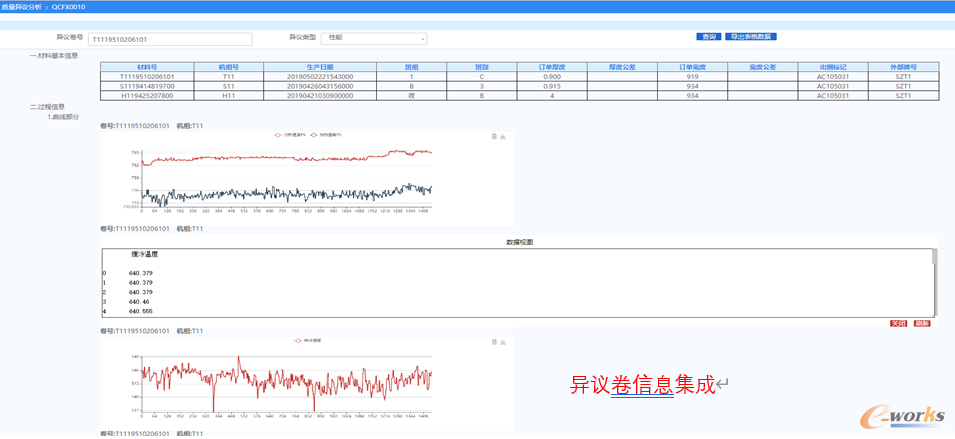
图20质量异议反查系统功能界面
3. 效益分析
(1)完善全面质量管理体系:全流程过程质量管理弥补了质量过程控制的空白,为质量设计和改进提供支撑,实现了从钢水投入到成品产出整个过程的监控、调整、判定、预测、检验和处理,实现了全流程一体化闭环质量管控,并优化了客户服务、质量异议等处理流程,大大提高客户满意度。
(2)优化业务流程和组织结构:以过程控制系统的数据为基础,利用统计方法对生产过程进行监控、诊断、分析和改进,实现全线自动质检,简化了质检流程,提高工作效率及客户满意度。
(3)支撑远距离、跨基地的工序协同:基于统一平台的数据共享,实现跨基地上下游质量缺陷追溯与定位分析,各基地可以直观了解上下游质量问题,并做出相应改善及工艺调整,解决跨工序质量问题。
该项目的实施,提高了产品过程控制的稳定性,提高了质量过程控制的效率和精度,自动判定率达100%,判定周期由30分钟降低到5分钟。机器替代人工判定,实现了由人工管控到全流程自动过程质量监控及预警,临时封闭率下降了16.84%,现货发生率下降了4.9%,返修率下降了0.89%。缺陷分类的准确率提高了12%,对各工序表检数据进行集成,实现对全流程表面缺陷演变情况的快速、准确、便捷定位和追溯,可快速锁定缺陷来源工序和产生原因,对迁顺产品质量的改进提升起到重要促进作用。汽车板PPM值成下降趋势,2021年奔驰为0 ppm,宝马月均39.6 ppm,日系产品月均7.3 ppm,一汽大众月均6.8 ppm。按照现货和正品的平均差价计算,全年产品质量提升带出的经济效益约为1733万元。