本文为“2021年度中国智能制造最佳应用实践奖”参评案例。本次活动将评选出2021年度,为中国智能制造领域带来突出效益的最佳实践工程,全面介绍企业推进智能制造的步骤、重点与难点、获得效益等,分享建设过程中的经验,供广大制造业行业企业学习供鉴。
一、企业简介
长城汽车泰州分公司为长城汽车股份有限公司旗下分公司,注册资金人民币80亿元,主要建设汽车整车、内外饰及底盘制造项目。同时,规划实施以汽车整车制造为核心、关键零部件为配套以及汽车金融、汽车保险、共享出行等业务。构建完整的汽车产业链体系,将打造为华东地区最具影响力的汽车科技产业园。
2019年2月20日与泰州市人民政府签约,在泰州高港经济开发区建设整车生产基地,并于2019年11月11日举行了奠基仪式。项目于2020年10月实现投产,包含冲压、焊装、涂装、总装全工艺链生产线。
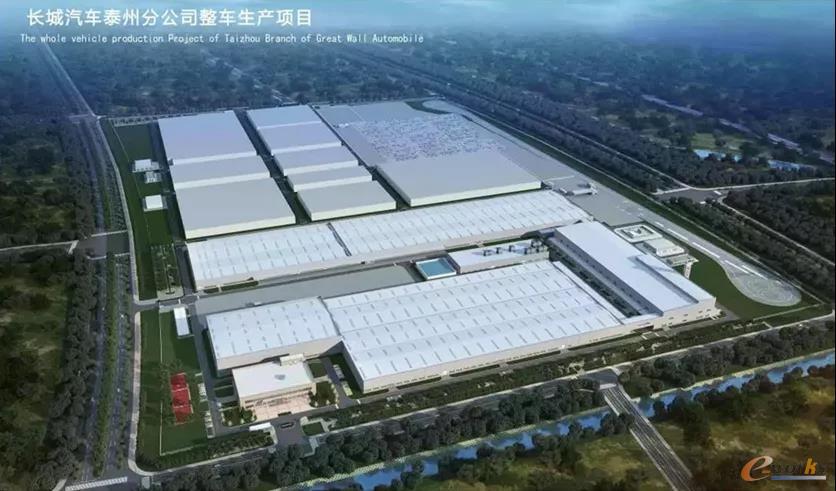
长城汽车股份有限公司泰州分公司
二、企业在智能制造方面的现状
长城汽车股份有限公司泰州分公司先期投资48.59亿元,占地约1174亩,产能规划18万辆/年。工厂围绕“绿色环保、智能精益”的理念,建设包含冲焊、涂装、总装四大全工艺车间。
生产基地采用了大量全球先进生产工艺及设备,极大的提高了生产效率,并时刻践行着对于节能、环保的坚持。在生产制造方面,大量采用机器人代替传统人工生产,例如冲压、焊装车间实现100%自动化,不仅提升了工厂整体自动化水平,实现多车型共线柔性生产,更提高了生产效率,有效保障了整车产品品质。在节能方面,通过采用先进的工艺技术和节能设备、有效降低各项能耗指标,贯彻节能环保、可持续发展的理念。
三、参评智能制造项目详细情况介绍
1.项目背景介绍
1)实施前企业主要痛点问题
目前中国制造业人工成本逐年增高,且人工生产效率低、失误率高等问题也开始制约企业的发展,例如:当日生产计划需人工统计分析;工厂设备使用传统的控制系统,过程维护需人工点检、识别;车间物流配送为传统叉车配送,工厂内产品流转耗费大量人力;产品检验过程需人工纸版记录,档案保存易丢失;公司职员、部门与高层领导之间呈现孤立状态。
2)项目主要目标及方法
围绕“绿色环保、智能精益”的理念,长城汽车泰州智慧工厂通过研、产、供、销、人、财、物全面协同的智能信息系统,建立智慧园区,打造真正的绿色智能工厂,不仅实现能源低碳化、生产洁净化、废物资源化,更从根本上实现“两个智能化”:智能化生产制造和智能化运营管理。
2.项目实施与应用情况详细介绍
目前长城汽车泰州分公司以提升先进汽车制造的智能化水平为出发点,通过对现有先进汽车制造过程中的智能化装备、智能化信息系统、工业大数据、云计算等关键技术的应用,为我国汽车制造向高端智能制造转化提供新模式,并将打造成为全国自主品牌数字化、信息化、自动化、可视化的标杆示范项目,也为我国汽车制造的智能化升级提供可复制可推广的范本。本工厂先进性主要表现在以下几个方面:
①数字化仿真模拟,开展产品设计仿真、工厂设计仿真、工程设计仿真、工艺设计仿真、工厂设备虚拟仿真及调试等工作,达到快速建厂,快速工艺实现,大幅缩短工厂建设周期。为满足智能化发展的需要,通过规划集团级PDM系统,集成设计工具及G-BOM等其他集团级项目,建设跨部门、跨地域、全产业链的协同汽车设计研发平台,增强研发过程管理和协同,确保数据交互;工艺开发通过搭建TCM数字化信息平台,是以技术和产品引领的大数据、智能化的制造平台,推动产品数据平台(3DE)与工艺信息化平台(TCM)集成,实现产品数据与工艺数据互联互通。
②数字化装备应用,采用全自动涂胶设备、精细化输调漆系统、智能化输送系统实现高品质的整车生产。例如:涂装喷漆生产线全部采用6轴或7轴机器人喷涂,机器人喷涂快速高效,膜厚均匀,并配合使用伺服喷枪和视觉质量检测系统,实现车身涂装柔性生产。车身涂胶及面涂生产线采用36台全自动喷涂机器人及自动输调漆系统,实现自动输胶/漆、自动喷涂、换色,以保证车身焊缝的密封性及漆膜表面的光泽度和鲜映性。
③自主开发大供应链智能物流系统,围绕物流过程,搭建标准化的物流现场,采用自动的数据采集与处理技术,构建10个核心信息系统VMS、APS、LES、SIP、P-TMS、WMS、LMS、MES、V-TMS、ERP,将公司销售、计划、采购、仓储、物流、生产直至交付等所有环节进行标准化及拉通,使得物流过程高效、可视、透明。
④数据采集及分析,首次应用企业云平台,数据包含数据采集、监控及分析,涵盖了生产过程中设备状态、工艺参数、产品质量、能耗数据等层面数据。系统分为三个层次,即顶层企业云平台层,中层厂区云服务层和底层车间信息层。同时通过ERP(SAP)、MES、LES、APS等系统借助PMC系统与下层自动化设备的联通,实现车间生产、制造、物流、仓储、财务链条整体数据流、信息流的协同生产。
⑤计划协同平台,打造以ERP系统为核心,以MES(制造执行系统)、LES(物流执行系统)、WMS(供应商门户)、SRM(供应商关系管理)为四大支柱,构建整车与零部件工厂的计划协同平台,现已形成了主干传输带宽500M,通过VPN线路、网络专线、光纤直连等方式,将国内的保定、天津、徐水、重庆,以及海外的巴西、俄罗斯、泰国、印度等全球工厂进行互联,形成了覆盖全球的企业网络。实现了策略统一和管控平台统一,构建完成了互联互通、便捷、安全可靠、统一管理的“长城汽车集团网络平台”。实现集团ERP系统、MES系统、LES系统、SIP系统、SRM系统全面覆盖;实现财务、制造、采购、物流、供应商管理等业务的平台化、一体化管理。
以下针对三大车间重点智能制造项目进行详细介绍:
2.1 冲焊智能车间
冲焊智能车间分为冲压工程与焊装工程两部分,其中冲压工程智能车间占地2.3万㎡,建设2400T和2000T两条A0级全封闭自动生产线,设计节拍14次/min,采用济二高速连续压机及高速机械臂,具备一键换模和一键换端拾器功能。车间主要生产大型车身覆盖件及成型复杂的内板件。
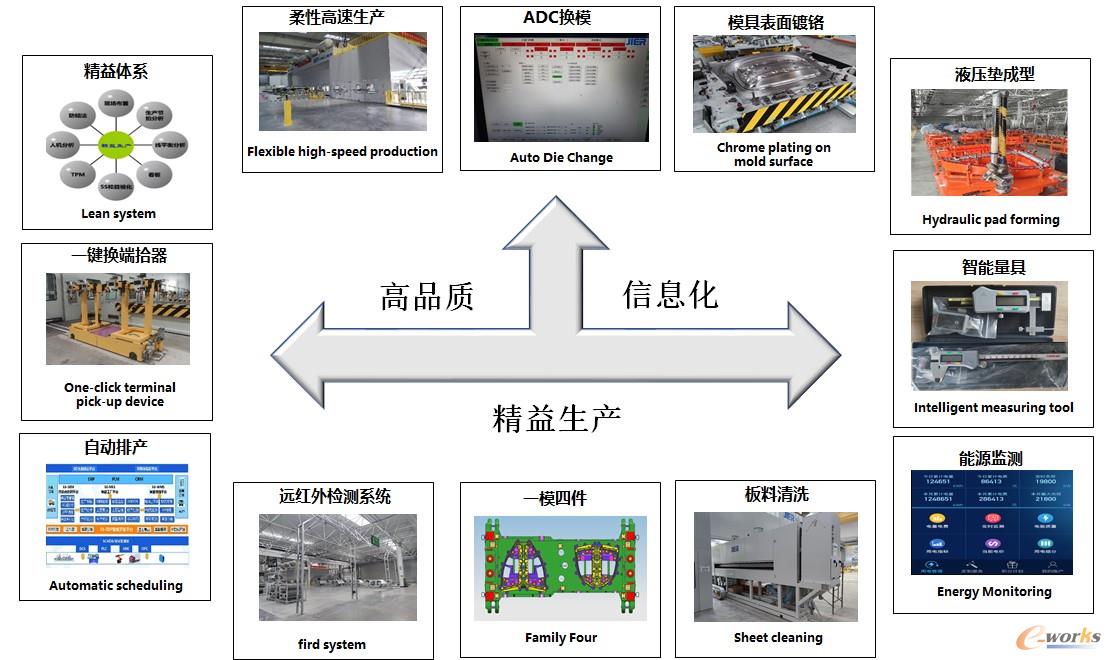
冲压工程智能化装备
焊装工程智能车间用地面积约3.8万平方米。生产节拍114秒,生产线分为机舱、前/后地板、左/右侧围、主线、车门/车装8条主线体,其中生产设备共618台,法那科机器人共211台,博世自适应焊机共155台。
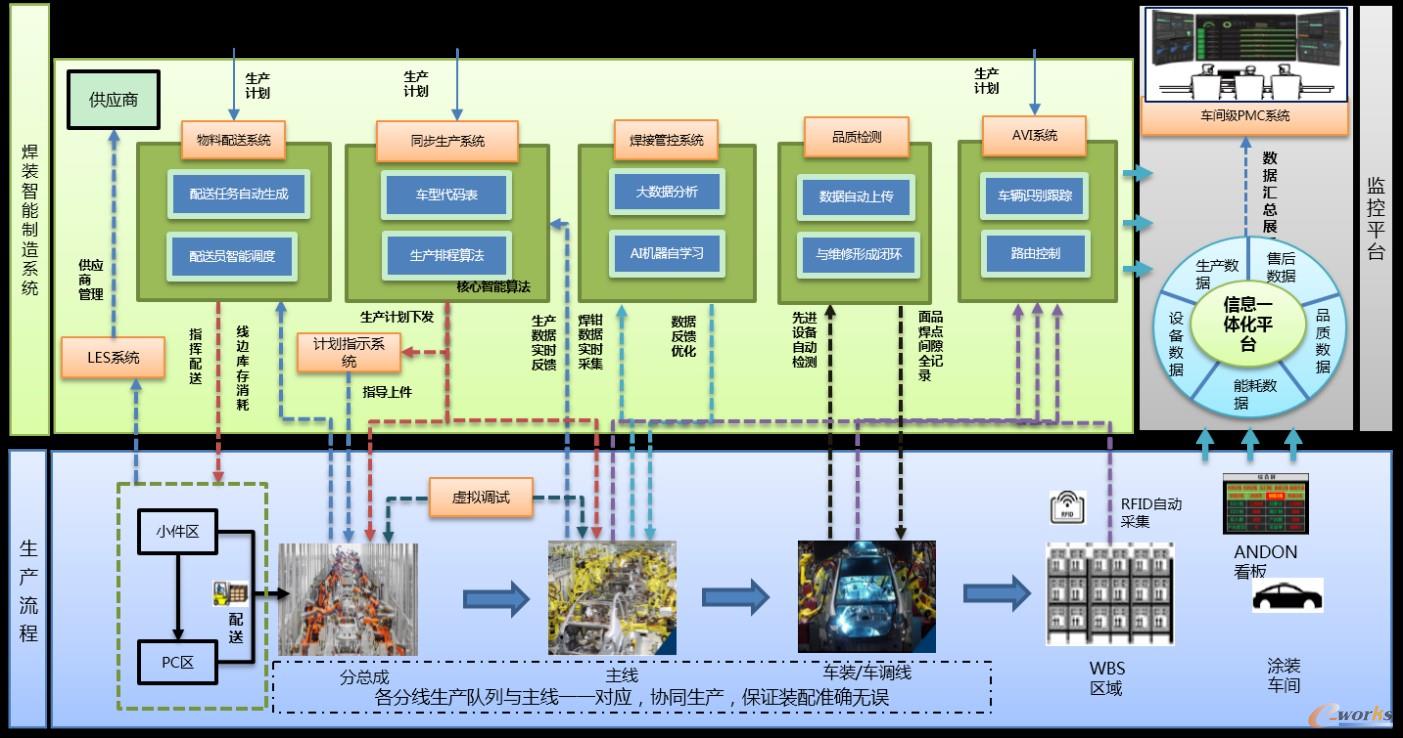
焊装工程智能化装备
1)高档数控机床和工业机器人
机械臂冲压线由济南二机床集团有限公司的机械压力机和自主研发的新一代六轴机械臂组成。
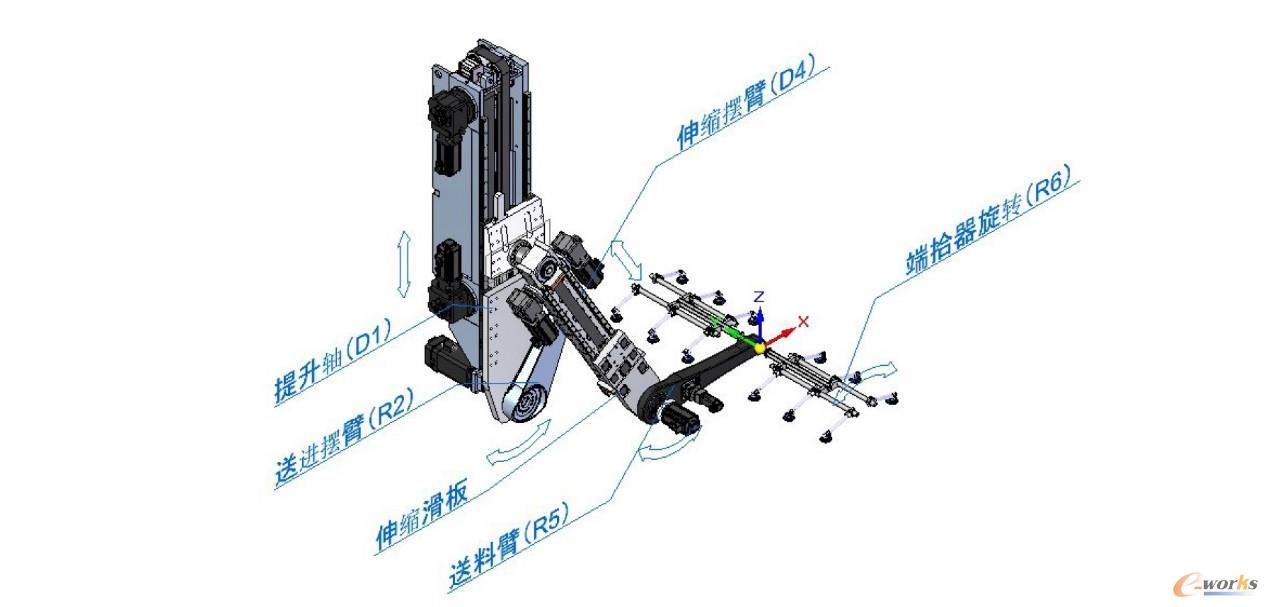
六轴机械臂
每条生产线共有四台压力机、五台六轴机械臂、一台两轴拆垛机械臂、四台六轴机器人。线首有两个承载板料的上料台车,在生产中轮流上料,实现不停机切换板料。操作人员确认板料一致后上料台车自动行驶到拆垛位置,两侧的磁力分张器通过伺服控制器精准运行到指定位置,当电机扭矩到达指定数值后自动回退指定距离并充磁,使上料台车上面的板料实现分张,便于板料一张张抓走。
拆垛机械臂自动行驶到抓料位置,抓取板料的同时进行双料检测,确认板料为单张后行驶到放料位置,真空发生器自动吹气将板料放到送料皮带机上。磁性皮带机带动板料送入清洗机。清洗机按程序设定自动对板料表面进行清洁并把板料送入涂油机。涂油机按程序设定给板料指定区域喷涂指定强度的拉延油。然后被过渡皮带机送到对中位置等待对中。
对中位置采用光学摄像对中,高分辨率的摄像头拍摄下板料的实时位置并和存储的模板位置进行对比,把对比的数据以偏移量的形式发送给对中机器人,机器人按特定轨迹把板料抓起调整到模板位置,放到皮带机上,皮带机把板料运输到上料位置。
6轴上料机械臂将板料放入压力机,压力机进行冲压,然后压力机间的6轴机械臂实现制件的转运,各序压力机执行冲压,最后一台压力机冲压完成后,下料机械臂把产品从模具取出放到穿梭机上,穿梭机自动运行到下料位后线尾机器人抓取制件并放至在皮带机上,皮带机把产品运送出线体,等待检验、装运。压力机的冲压和机械臂的转运是完全自动协调的,取放件的配合、转运的节奏、安全条件的实时检测完全是自动和同步实现的,在高节拍、高效率生产的同时还大大降低能源的消耗。
自动化冲压生产线,从生产的配方管理、计划的下达、模具和参端拾器的更换到板料的运送、冲压的生产,完全是自动化的。操作人员只需按下循环启动启动按钮,系统完全自动实现所有的控制和任务的执行,是真正意义上的自动化生产。
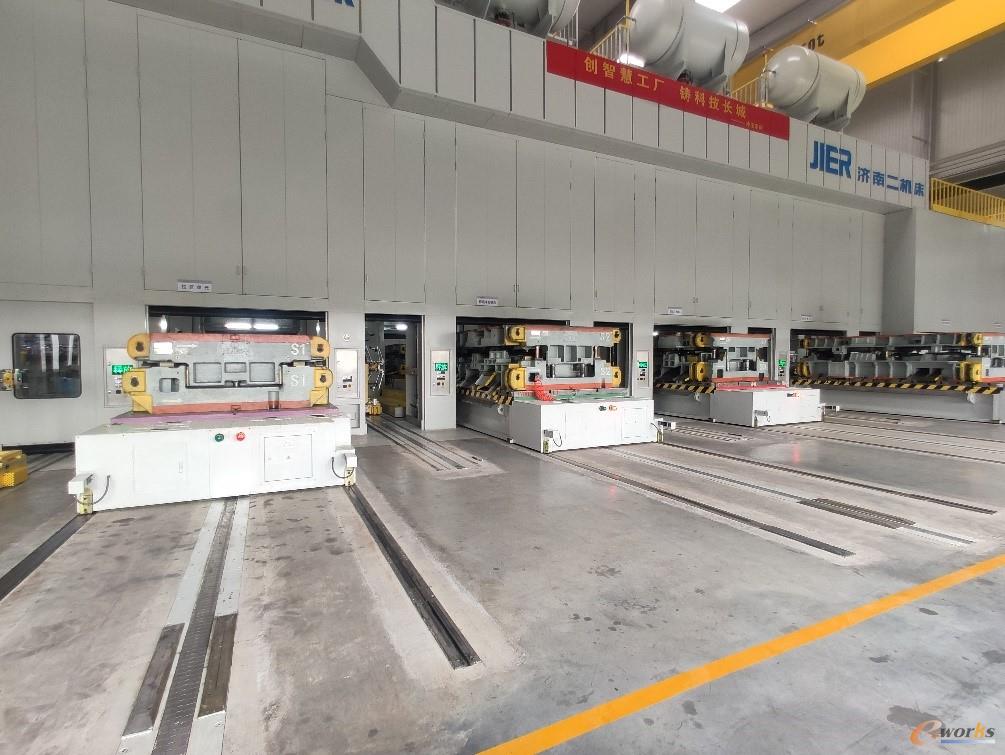
整线一键换模
车身焊接生产线全部采用6轴或7轴机器人焊接,机器人焊接快速高效,焊缝均匀,按程序设计焊接,不存在错焊、漏焊问题。而且焊接机器人高柔性的特点可以完成人工不能完成的复杂焊接。
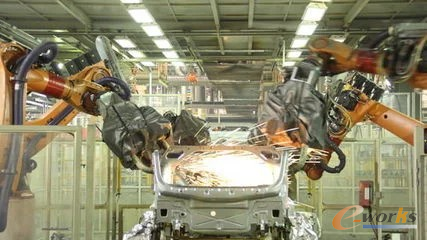
焊接机器人
与专用涂胶设备集成,既能独立实行半自动涂胶,又能配合专用生产线实现全自动涂胶。 柔性高,适用能力强,可以完成复杂的三维立体空间的涂胶工作。操作程序存储容量大,能存储100种不同产品型号。触摸显示屏操作简便。工作台安装传感器进行精密定位,提高产品生产质量。使用光栅确保工人生产安全。
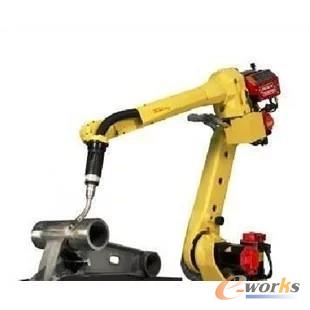
涂胶机器人
2) 超高频RFID射频识别
通过无线电讯号识别特定目标并读写相关数据,具有数据存储量大、识别距离远、识别速度快、寿命长、环境适应性好以及能同时识别多标签等诸多优势,取代条形码在汽车生产线上对车辆进行标识和跟踪,整个过程无人工干预,极大程度降低工人的劳动强度和出错率,提高了产品下线合格率。
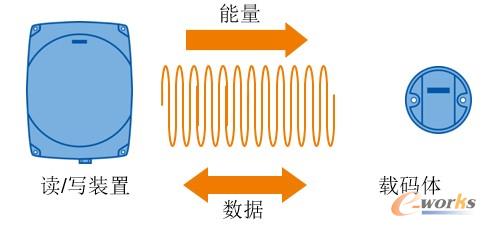
???????
超高频RFID射频识别
3) 板料双料检测器
在冲压件生产过程中,如果模具内同时放入两张板料,冲压时会损坏压力机机械机构和模具。采用双料检测器对板料厚度进行检测,确保只有一张板料放入模具。进行双料检测的系统是一套智能系统,配备独立的控制器和专用的传感器,能快速准确地对板料厚度进行检测,和设定值进行对比判断后若超出设定范围则发出警报,通知自动化控制系统停止运行,就可保护压力机和模具不被损坏。每条自动化线配置两套双料检测系统,检测精度高,运算速率快,还有参数存储功能,最多可存储255套板料参数。生产时,随设备参数一起被调用运行。从而达到可靠、精确的判断处理。
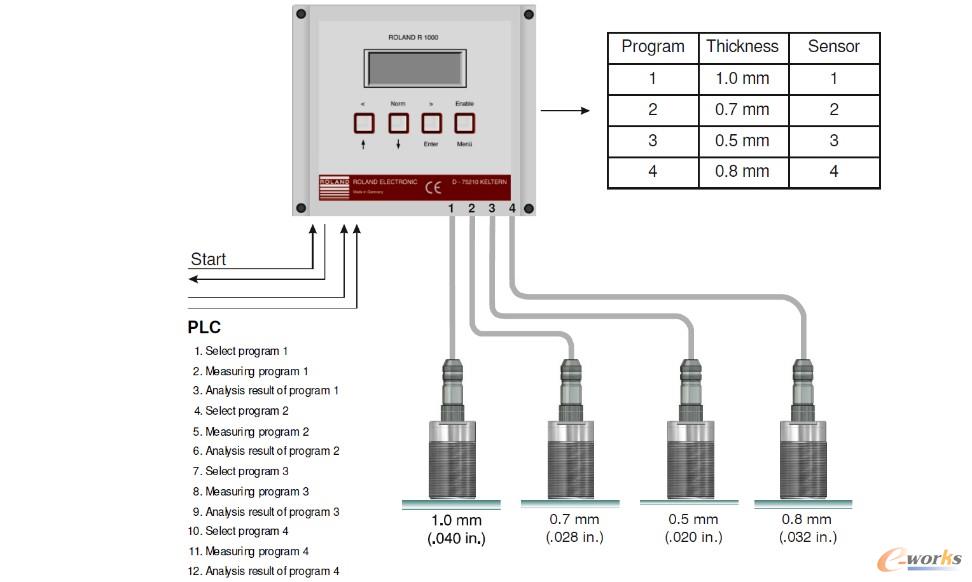
双料检测器
4)冲压件机器视觉对中
板料被放入第一台压力机前要进行位置调整,确保准确的放进模具中,如果位置偏离,就会在冲压时损坏模具。对中位置采用光学摄像对中,高分辨率的摄像头拍摄下板料的位置,和存储的模板位置进行对比,把对比的数据以偏移量的形式发送给对中机器人,机器人按特定轨迹把板料抓起调整到模板位置,皮带机把板料输送到上料位置,再由上料机械臂抓起放入到第一台压力机中。
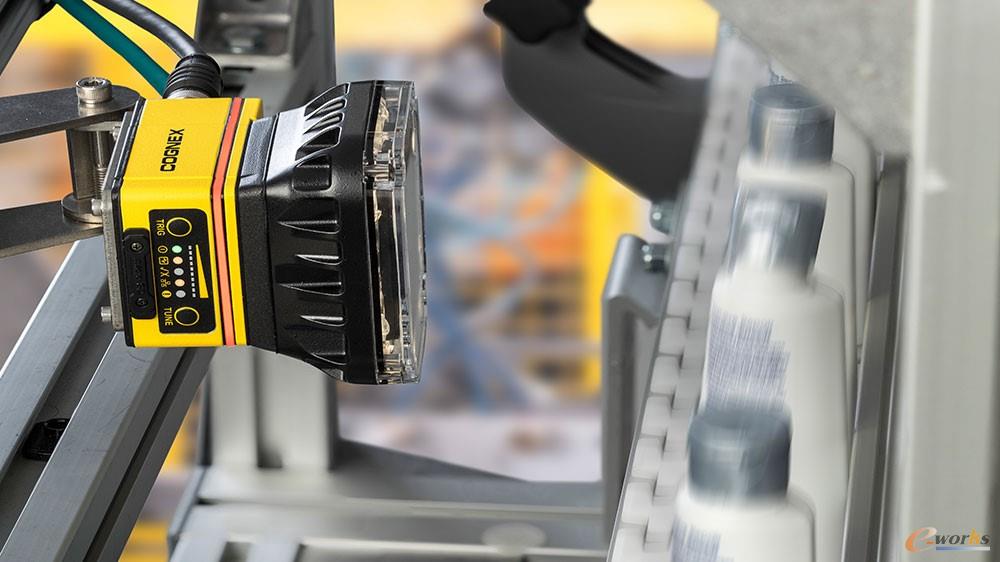
机器视觉对中
5)滚床自动输送系统
用于车身总成线工序间输送、调整线输送以及焊装车间空中储运线车身储存输送,自动化程度高,输送速度快、定位精度高,实现一个车间多车型生产线联线。
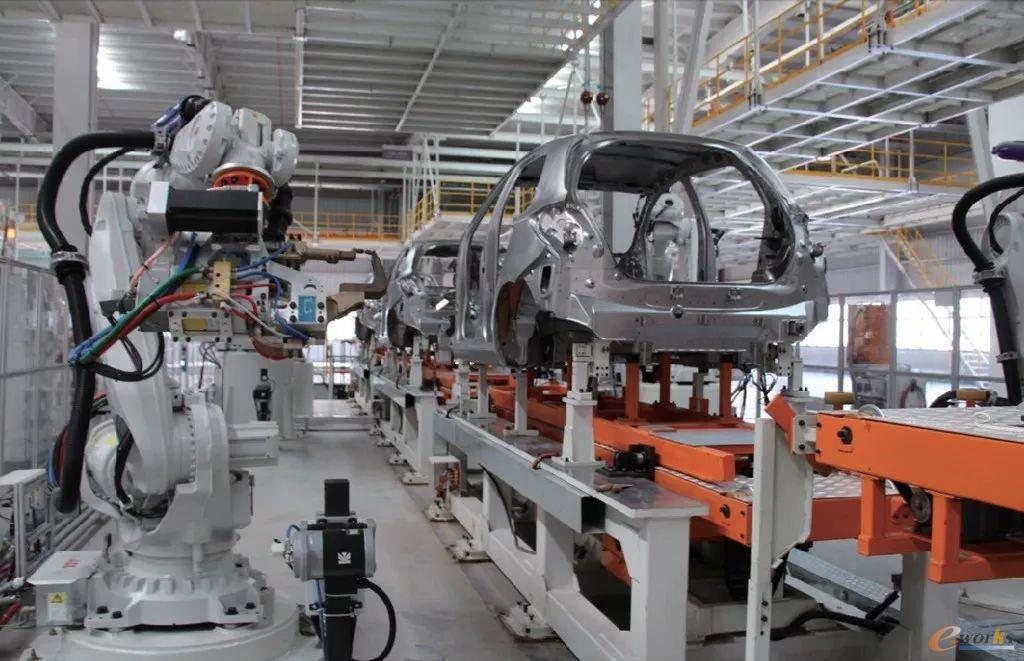
滚床自动输送系统
6)设备远程诊断
自动化线还具备远程诊断功能。远程诊断是指现场设备出现问题时,远在异地的工程师可以通过网络远程解决设备故障,以及在监控中心远程监控设备状态并分析数据实现设备故障预判并可将设备数据存储在监控中心实现设备数据的历史追溯。
远程故障解决可以实现远在千里之外控制生产现场的电脑或PLC,看到设备数据解决现场设备故障。
2.2涂装智能车间
涂装车间占地面积2.16万㎡,为2层半独立钢结构厂房,耗资2.5亿元,由前处理电泳、涂胶、面涂、终检、小修、报交、注蜡7个线生产设备160台,其中喷漆机器人26台、涂胶机器人11台,烘干设备4套,设计节拍114S/台。
(1)连续式喷漆机器人
泰州涂装喷漆生产线采用B1B2环保水性涂装工艺,喷漆机器人面漆自动线包括擦净站、BC1外喷站、BC2内喷站、BC2外喷站、CC内喷站、CC外喷站共39台ABB机器人,其中擦净站采用IRB 6700鸵鸟毛擦净机器人;内喷站为走停式喷涂,采用ABB IRB 5350 3轴开门机器人和IRB 5500 7轴喷涂机器人;外喷站采用连续式喷涂,全部采用IRB 5500 6轴喷涂机器人。过程中输送与机器人运行精密无缝配合,机器人喷涂快速高效,膜厚均匀,按程序设计喷涂,消除错喷、漏喷问题。而且喷涂机器人高活动空间的特点可以完成人工不能完成的大跨度部位喷涂。
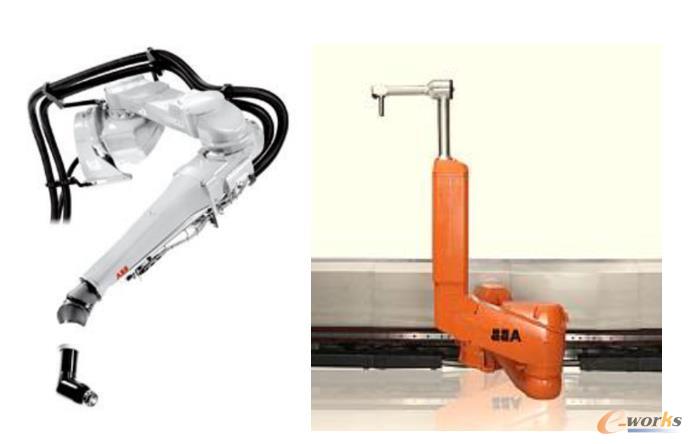
喷漆及开盖机器人
(2)智能车身检测系统
在喷涂机器人、涂胶机器人运行过程中,需要对车身进行识别,涂装车身识别采用智能化视觉系统,主要分为三个部分:
图像收集:车型识别区域布置ISRA机器视觉设备,对车身外观进行图像取样,标记图像特征点,存入工具库中;
图像分析:车身进入识别区域后,视觉设备自动抓取图像特征点,并与工具库中样本进行匹配、对比、分析。
图像反馈:将图像分析的车型反馈给现场显示设备。从而实现对车身进行识别检测,确保判定结果准确,准确率高达100%,将停线时间缩短到1min以内。
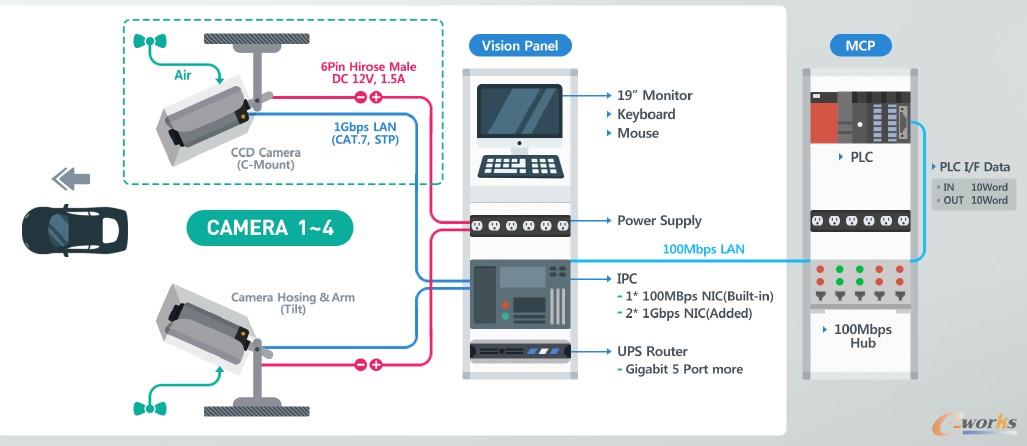
系统架构图
(3)涂装数字化自主实施输送控制系统(PMC监控系统)
涂装车间前处理、电泳输送设备项目电控由PLC、传感器、HMI、软件和网络接口所集成的系统,能对过程进行自动控制、生产操作、监视信息。具有灵活性并便于修改,能适应设备、控制系统配置变化的优势。
整个输送系统的自动化控制系统中,采用“集中监测,分散控制”的典型控制模式,依据这一原则,将整个涂装车间生产设备的控制系统分为二层网络(以太网+ProfiNET总线),三个层次(监控层、控制层和设备层)。每个层次中使用不同的网络结构及软硬件配置,以实现不同的功能。
电控系统首先满足各线体的工艺要求,结合目前国际、国内自动化水平和汽车行业的实际运作方式,选择在业内应用成熟,技术先进可靠,功能实用的控制方式与控制设备。整个电控系统稳定可靠,反应迅速,能够及时提供生产线状况和设备运行状态,能够快速提供故障信息,提示检修。每个电控子系统都对自己系统的独立性,完整性,工艺符合性负责。
元器件的选型以产品质量好,技术性能高,使用安全可靠,通用性强,升级换代方便,备品备件充足,技术服务优良等为原则,选择国内外知名生产厂商的优秀产品,使得自动化控制水平总体上在国内处于领先地位。
控制系统采用两层网络(工业以太网和工业现场总线)和三层结构(监控层、控制层和设备层)的典型控制模式,网络架构如下图:
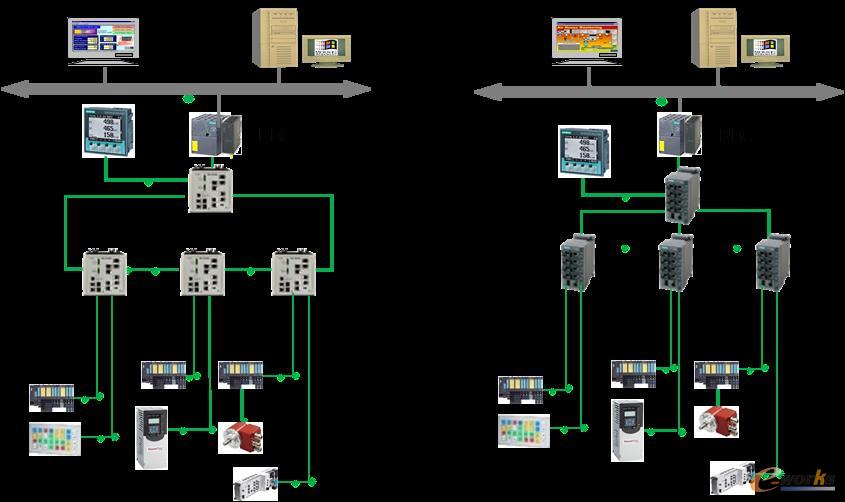
输送控制系统
控制系统采用SIEMENS 1500F系列PLC作为其控制核心,PLC使用PTOFINET总线用于连接现场IO模块,通过现场总线IO模块,接收现场的数据信息,经过本身CPU中所存储的控制程序的运算与处理后,发出相应的指令(输出信号)对现场设备进行控制。
监控层—中控系统通过以太网与各区主控制系统PLC进行链接、通讯以及数据交换,监控车间各个受控设备的状态、故障等情况,进行中央监控、历史记录。
控制层主要由PLC及其系统组成。由PLC及其系统接受现场发来的数据信息(包括人工通过触摸屏发出的指令信息),经过PLC自身的运算与处理后,发出相应的指令对现场设备进行控制。对现场设备出现的所有故障及时的进行分析处理,实时将故障信息反映在触摸屏上,并进行相应声光提示,配合CCR系统完成产品在整个车间的流程监控。通过PROFINET总线使得控制层内各个站点之间进行方便有效的数据交换。
设备层主要由总线模块、变频器、软启动器、温度控制仪表、现场设备检测元件(接近开关、传感器、光电开关等)、现场执行机构(电动机、调节阀、电磁阀等)等组成,直接或通过现场总线与控制层中的PLC进行数据交换,将现场信息发送给PLC,并按PLC输出指令执行设备动作。
控制系统的控制参数、运行参数及状态可以送到中央控制室,由上位监控计算机处理、显示、故障诊断、报警(且要声光输出)、记录、打印等,并可在中央控制室实时数据显示、实时状态监视和实时在线修改设定数据连接在网络上的生产设备。
每套主控系统预留一个以太网接口用于连接甲方中控系统,实现自身控制功能及与车间中控系统的信息交换。
控制系统安装操作员接口(HMI)设备一台,用于现场操作提示、故障报警、运行参数显示、控制参数设定、及设备状态实时监视、实时设备控制和实时在线修改数据。
(4)涂装协同生产系统
汽车白车身的涂装工作大部分由机器人完成,生产线的自动化程度越来越高。白车身处理包括前处理、电泳、涂胶、喷漆、注蜡等多个阶段,每条生产线均为多车型混合生产,必须保证每种车型严格按照生产计划拼合在一起。若其中一个环节出现错误,则会导致在涂胶(每种车型涂胶位置不一样)、喷漆线(每个车的喷涂颜色不一致,喷涂轨迹不一致)出现车型不能匹配的问题,对生产造成严重影响。 组态软件CIMPLICITY 11.0能够在Windows平台上快速构造计算机监控系统。系统基于以西门子S7-1500系列PLC为控制核心,配合WinCC来完成系统的数据采集、参数显示、超限报警等任务。系统选用HPE作为上位系统的服务器,双硬盘镜像,确保系统的可靠性。操作系统选用MS Windows Server 2016 ,上位软件选用WinCC V7.0 SP3,达到工业级稳定性。按生产计划各线体同步自动生产,应对车间生产过程异常导致的计划调整,确保车间生产精准率100%。
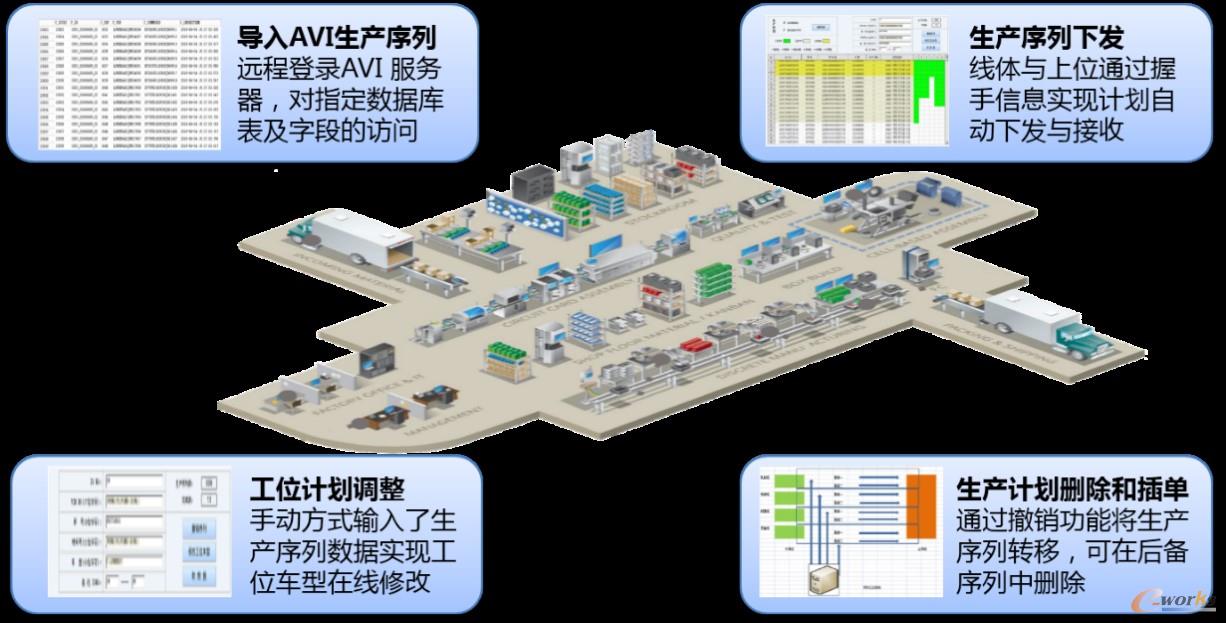
涂装协同生产系统
(5)移动终端扫描防错
员工使用移动扫描终端(简称:PDA)扫描物料的二维码、条形码等物料标识进行识别拣选物料是否正确。及时发现物料拣选错误问题,更换物料保证配料送上线体“0”失误。
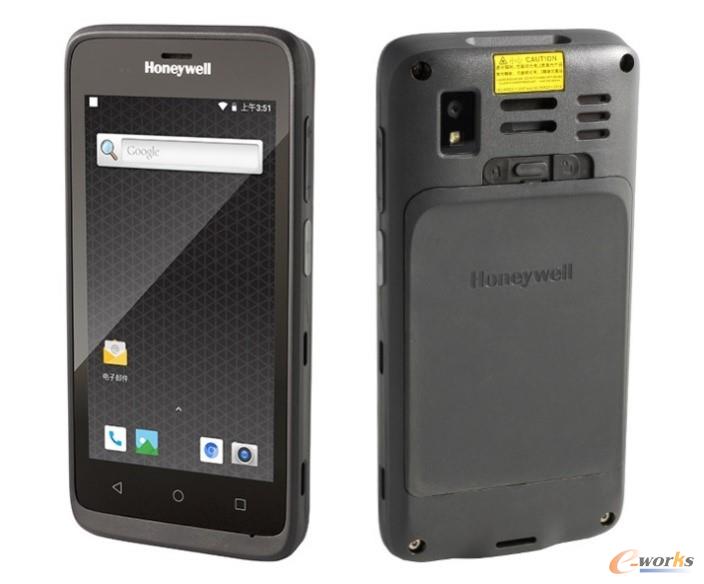
移动扫描终端
2.3总装智能车间
总装车间占地面积6.4万平方米,投资1.3亿,生产节拍114S/台,总装车间以卓越品质、精益生产、智能制造、舒适环境四项理念开展车间的建设,自2019年11月11日开工至今,车间生产线体包含内饰一/二线、底盘一/二线、组装一/二线6大线体,合计124个有效作业工位;规划采用双层平台运输、U型布局、线边分总成模块化。
(1)智能捡料的功能
信息系统(如LES、WMS等)生成捡料任务并发送给NOAH物联网平台。NOAH系统将订单分解为执行信号,下发至拣选设备。现场智能拣料区接收到拣选任务后,货架上的拣选终端根据任务亮灯并显示拣选物料的数量。员工拣料期间通过佩戴RFID手环可以被货架的RF智能探头主动读取员工手环,识别到拣选是否正确:拣选正确,系统会自动灭灯;拣选错误则会报警,并且员工动作数据会被自动实时记录并上传。
智能拣料通过亮灯指引实现无纸化专业,亮灯显示物料位置以及数量,提高拣选效率。利用先进的物联网技术全程主动防错、按灯自动灭灯并且全程记录执行数据,在不改变员工原有的操作习惯前提下,实现友好的人机功效,提高了作业效率、减少认为差错,降低企业成本。智能拣料可进行可视化展示,屏幕显示内容:拣选命令二维展示、拣选进度、拣选零件号、错误提示、异常提醒等内容。
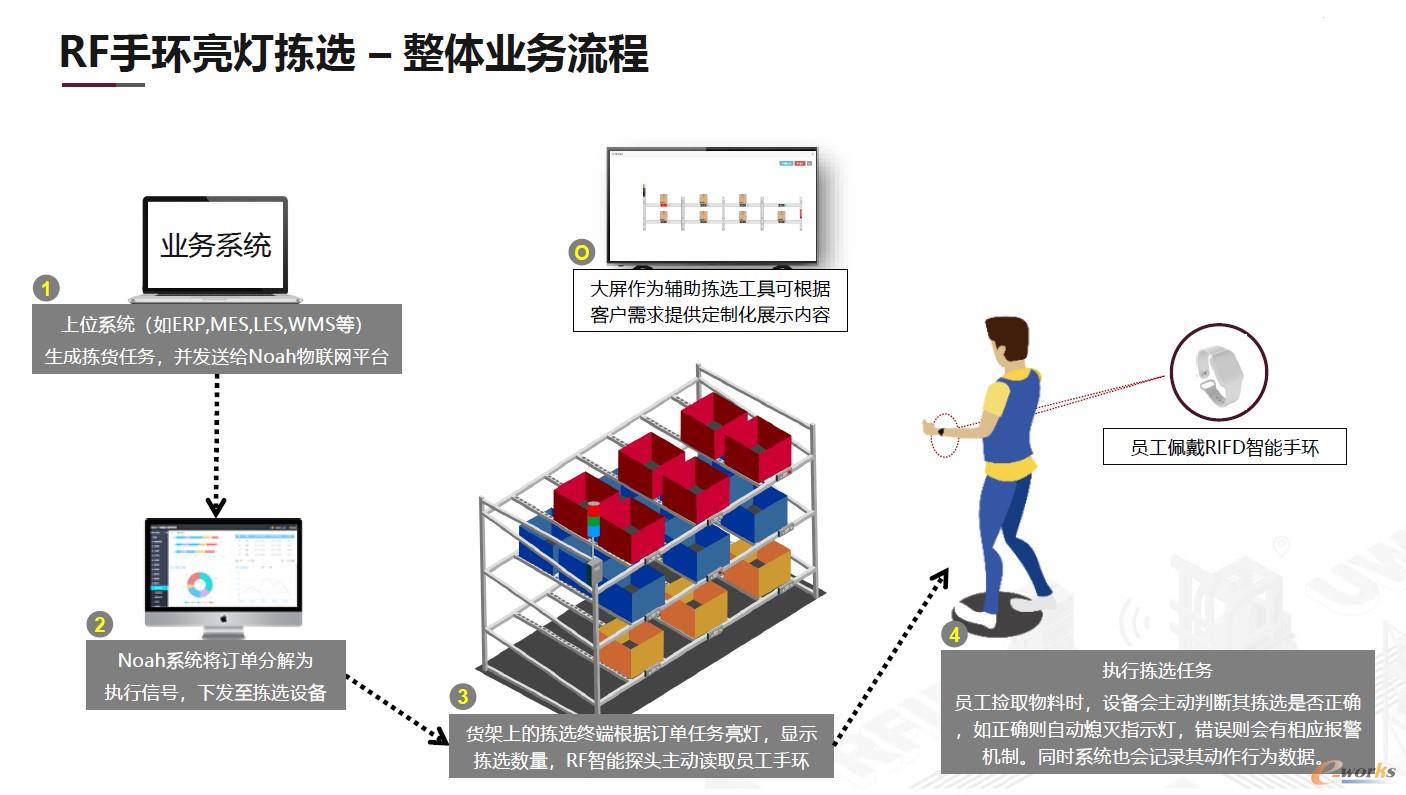
RF手环亮灯拣选-整体业务流程
(2)搬运AGV自动运输
在拣选、扫码防错都已经确认无误,备料车随轨道移动到末端停住,等待AGV小车拖走。AGV搬运机器人均采用RFID感应式控制,通过RFID标签与读取装备自动检测坐标位置,实现AGV搬运机器人的自动运行。通过接收到相关控制指令,最终AGV接受并执行-将物品配送至指定地点,实现自动输送功能。
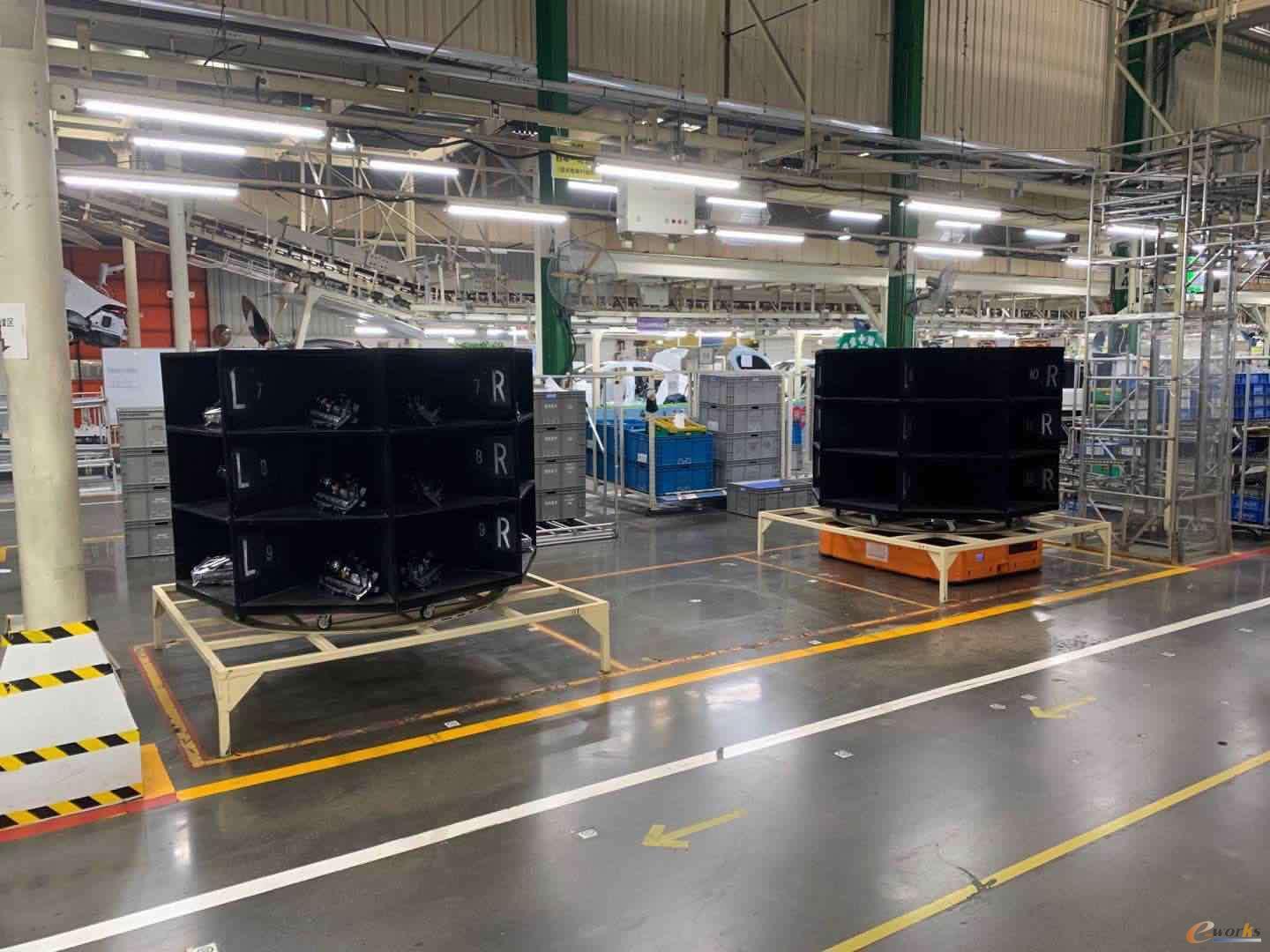
AGV小车正在运输物料
AGV小车架构为,使无线按钮呼叫系统发起一个器具备料完成任务指令,调度系统接到任务指令后,根据上游系统移位任务指令信息直接或间接确定目标料车、起始坐标点、目标停靠点、任务类型、库区,然后生成移位任务。调度系统分配AGV并执行搬运任务,运动过程中系统自主规划行走路径,到达目标停靠点后货架离线或在线,任务执行完成并回报上游系统
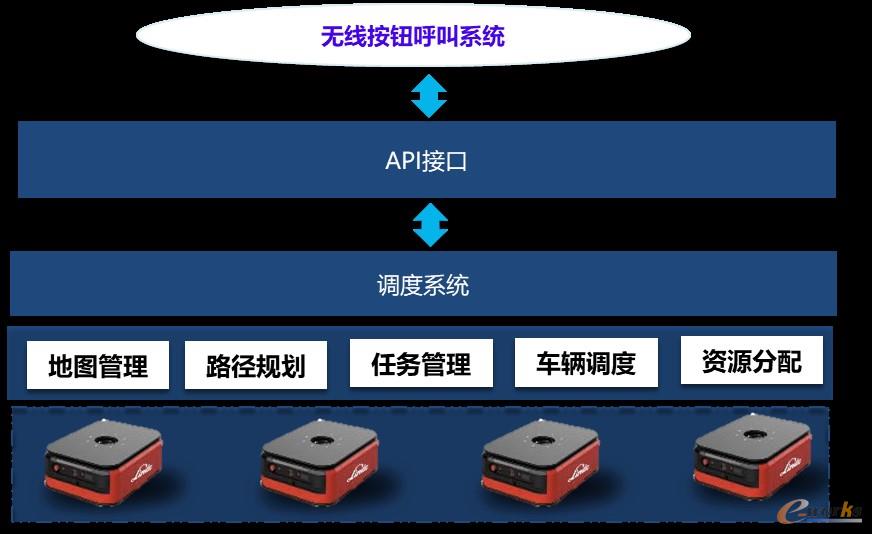
系统架构流程
(3)底盘视觉检测
底盘检验采用机器人搭配工业相机的方式对检测项进行检验,主要的检验范围包括但不限于:螺栓、线束、管路、胶堵、隔热垫、环箍、插接件等,控制系统架构为:
①视觉系统与AVI系统进行交互,获取本线体车辆信息,选择对应的机器人与视觉系统;
②与输送系统和ANDON系统交互,检验出问题后发出报警或停线;
③当线体停止时,视觉检验系统同时停止。线体旁放置上位机进行检验状态的实时显示,并存储检验数据,数据上传至服务器保存后,本地进行自动覆盖。
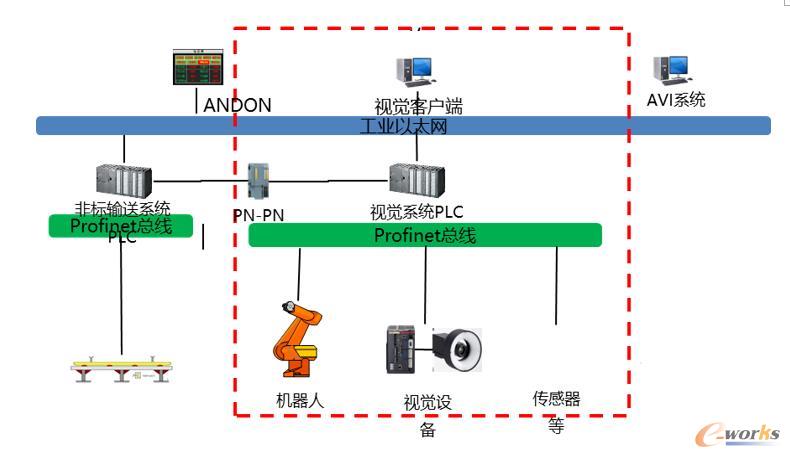
视觉检验系统架构
(4)生产计划智能排布
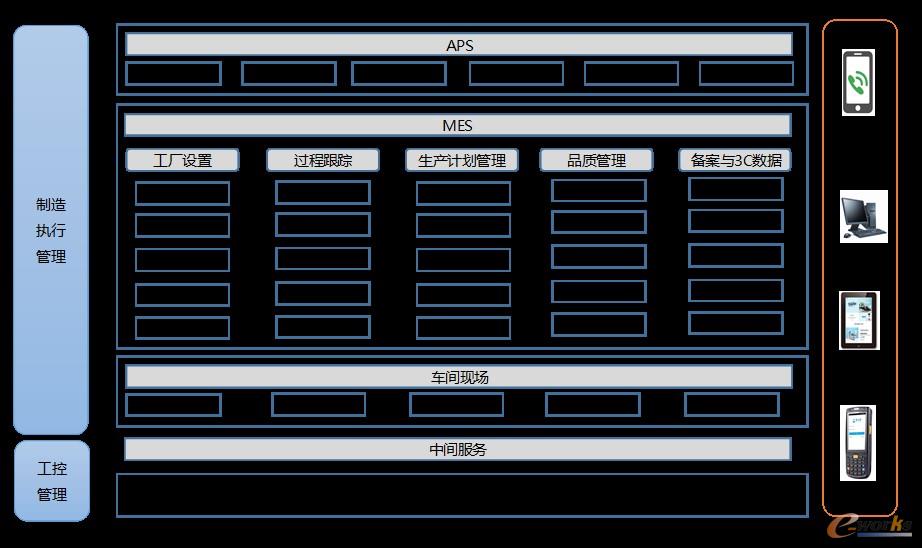
MES系统架构
总装车间通过MES系统建设与应用实现生产计划、调度、统计、操作与计量管理的业务集成,而且能将生产过程和经营管理的信息进行转换、加工和传递。保证调度与统计的数据一致性,并协调各个部门之间的工作,堵塞管理漏洞。同时,通过ANDON、AVI、作业指示等功能模块,与设备结合紧密,为ERP提供完整、及时、准确的生产执行数据,
整体功能中,生产排程是MES系统实现生产计划管控、为各个生产单元提供可执行生产作业计划的核心功能模块。生产排程是在考虑能力和设备的前提下,在物料数量一定的情况下,安排各生产任务的生产顺序,优化生产顺序,优化选择生产设备,使得减少等待时间,平衡各机器和工人的生产负荷。从而优化产能,提高生产效率,缩短生产周期。生产排程可以对上游下达的生产计划,按照生产进度、生产工艺流程和生产标准等要求,运用MES系统的精密排程算法,自动展开,生成具体的细化的生产执行计划。
3.效益分析
冲焊车间通过智能化改造,整体自动化率达90%以上,机器装备水平得到大幅提升,通过采用高精端机器人,并结合远程维修等智能系统,使冲压件及白车身生产焊接精度得到保障,提升了整车产品质量。
涂装车间通过工业机器人、智能传感器、智能识别系统及在线质量检测装置等先进装备,构造全自动化的生产线,运用工业网络技术、计算机技术将所有装备互联,实现对涂装设备、物流设备和检测设备的在线监控与管理,及生产过程和物流过程的集中监控,实现了生产环境自动控温,保证了油漆恒温、恒速、使油漆品质更稳定、漆膜更丰满、色彩更艳丽。
总装车间通过设备改造,实现了能源管控与合理调度,极大地支撑了生产过程的节能降耗,并通过信息化系统与现场控制系统对接,保证了实物与生产计划相对应,实现了对关键数据、重点问题的监控与追溯。
本文为e-works原创投稿文章,未经e-works书面许可,任何人不得复制、转载、摘编等任何方式进行使用。如已是e-works授权合作伙伴,应在授权范围内使用。e-works内容合作伙伴申请热线:editor@e-works.net.cn tel:027-87592219/20/21。