本文为“2021年度中国智能制造最佳应用实践奖”参评案例。本次活动将评选出2021年度,为中国智能制造领域带来突出效益的最佳实践工程,全面介绍企业推进智能制造的步骤、重点与难点、获得效益等,分享建设过程中的经验,供广大制造业行业企业学习供鉴。
一、企业简介
山东浩信机械有限公司(以下简称“浩信机械”)成立于2003年,占地面积100万平方米,年产铸件60万吨,员工6000余人。主要从事商用车、乘用车、工程机械、农业机械底盘类和发动机类零部件的研发与制造,公司产品产品远销欧洲、北美、亚洲等国家与地区。在国内是潍柴动力、福田雷沃、中国重汽、北奔重汽、陕汽集团、中国一汽、北汽集团、安徽安凯等国内主机厂的战略供应商;在国际市场与BOSCH、WABCO、DANA、KNORR-BREMSE等国际知名公司有着长期稳定的合作关系。
浩信机械是目前国内最大的球墨铸铁轮毂研发生产制造基地,全国铸造行业综合百强企业,公司被认定为“高新技术企业”,拥有山东省企业技术中心、工程技术研究中心等3个省级研发平台,获得“中国驰名商标”、“山东省著名商标”、“山东省名牌产品企业”、“优质铸件金奖”、“省级文明单位”、“省级重合同守信用企业”、“山东明星专利企业”、“山东省制造业单项冠军示范企业”等荣誉称号。获得中国铸造协会评选的“中国铸造行业单项冠军企业”、“中国绿色铸造示范企业”、“山东省铸造行业50强企业”等荣誉称号。主营产品球墨铸铁轮毂2019年全球市场占有率11%,排名第二位,国内市场占有率22%,排名第一位。
公司从2018年开始全面实施信息化,截止2021年,共实施上线信息化项目十余个,建成高标准机房1个,普通机房2个,截止到2021年内累计投资达1200万元。现已建成集团化公司管控,基本实现业务流程化,管理信息化。
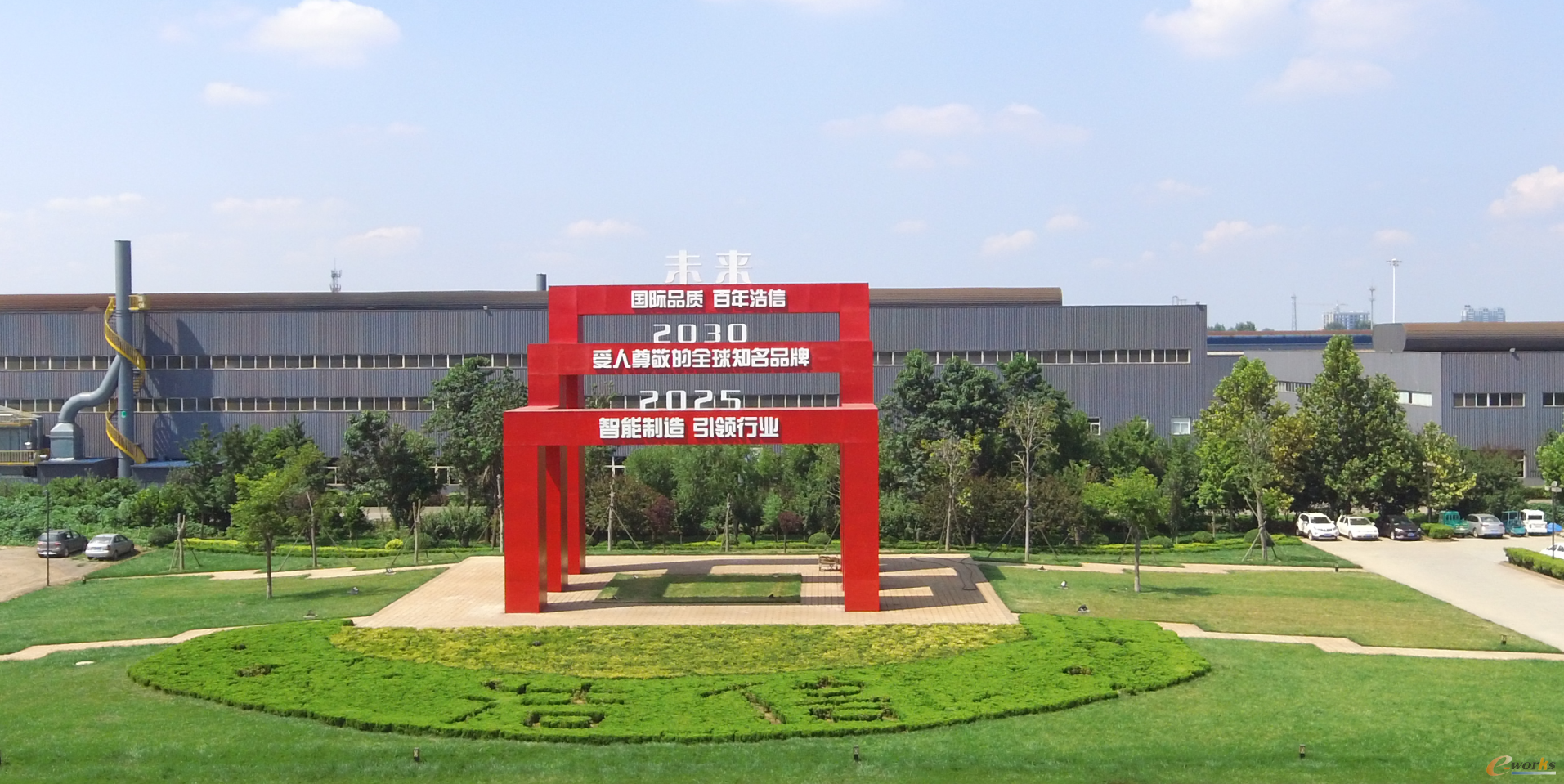
山东浩信机械有限公司
二、企业在智能制造方面的现状
2020年8月实施ERP项目,在2021年1月ERP上线完成。项目成功的上线,标志着山东浩信机械开始大步向管理精细化,流程信息化迈进。
2021年3月,公司OA上线完成,基本实现核心业务与ERP打通,全面实现公司业务流程的审批的自动化,提高工作效率,节省工作时间。
2021年5月完成公司骨干网络升级改造。实施超融合系统,搭建起真正属于浩信自己的私有云,建立成以昌邑浩信工业园为中心的数据机房。
2021年8月,潍坊分公司山东浩泰机械有限公司,数字化工厂项目实施完成,通过实施WMS系统、AGV系统、MES系统,基本实现仓储系统化,物流自动化,生产过程追溯化。
2021年10月,上线PLM系统,应用数字化三维设计与工艺技术进行产品、工艺设计与仿真,并通过物理检测与试验进行验证与优化。建立产品数据管理系统(PDM),实现产品数据的集成管理。
随着公司管理信息系统的逐步完善,公司也充分认识到生产系统信息化的重要性,公司正从企业管理信息系统向生产管理系统进行延伸,在潍坊分公司数字化项目的试点基础上,将在2022年计划实施浩信昌盛车间MES项目,现在正在做前期的调研和风险论证。
三、参评智能制造项目详细情况介绍
1. 项目背景介绍
随着在制造业竞争日益激烈,客户需求多样化,制造技术复杂,市场对质量和效率的要求不断提高,以及传统制造业面临着巨大的挑战的背景下,浩信公司必须以缩短产品设计周期、缩短产品设计周期、提高生产效率和生产方式的灵活性来应对这一变化,浩信机械浩泰分公司数字化工厂就应运而生了。
2. 项目实施与应用情况详细介绍
潍坊浩泰工厂按照数字化工厂的标准进行建设,从设备的数据采集,生产制造执行,物流自动化,自动立体库,尽可能实现少人化,无人化,减少人为的干预。
从自动化方面,与自动化生产线设备对接,车间设备互联互通,实现计划下达到车间,由系统调配原料,从原料库到生产线源头,按照设定的程序进行加工,检测,记录生产过程,产品入库,由无人AGV搬运到库房,从数字化方面,构建完善的生产体系和质量管理体系,实时排产,现场设备、产线的状态采集可视化展示,生产制造过程的信息的实时采集、管理和反馈,对生产过程跟踪和质量追溯,通过数据分析,实现整个生产过程的追溯与管理决策的闭环管理。对现有流畅的业务进行IT手段固化,提升信息化管理水平。
主要建设内容:
(1)业工厂总体设计、工艺流程及布局建立数字化模型,利用数据采集对工程重新建模,进行数字孪生模拟仿真。提供统一的生产运维可视化管理平台,通过GIS、三维可视化技术对工厂的环境、设备、管线、人物角色等进行三维建模和虚拟化呈现。集成设备资产、生产运行、安全监控等业务系统数据,围绕设备可进行资产全寿期的管理、状态和性能的监测,以及生产运营数据的可视化展示应用。
应用数字化三维设计与工艺技术进行产品、工艺设计与仿真,并通过物理检测与试验进行验证与优化。建立产品生命周期管理系统(PLM),实现产品数据的集成管理。优化企业项目管理流程,加强项目的管控力度,提高项目监控和汇报效率。同时建立基于项目管理的协作平台,提供完善的工作计划、任务、目标和绩效统一管理平台。加快产品创新设计、提高设计重用率,加快市场影响速度,缩短技术准备周期。
(2)在厂区内组建工业互联网,架设工业互联网网关及边缘计算,利用SCADA对公司在用设备进行统一管控,对设备运行数据进行实时读取。帮助企业实时采集到生产过程中的各类数据,代替了人工作业的同时,也避免因人员工作失误所带来的损失,提高工作效率,也能实时监测到生产过程中的所有不正常数据,为产品的质量又提供了一层保障。SCADA系统提供每台设备生产数据,使得生产情况直观明了,方便企业管理层人员对生产情况进行分析,同时帮助企业优化生产,使生产计划变得更科学与更合理。
实现对产品、生产进度、生产效率、质量信息、设备运行等管理过程的数字化与智能化改善,优化生产过程的数字化管控能力。建立数据采集和监控系统,一期对生产工艺数据自动数采率达到80%以上。
(3)实施企业资源计划系统(ERP),车间层级实施制造执行系统(MES),实现企业经营、管理和决策的智能优化。将工厂变成智慧工厂,在公司的生产计划、调度均建立模型,实现生产模型化分析,决策逐步实现从业务流程规范,到数据透明化再到智能化深入应用。提高员工的工作效率,实现了产品质量的全程控制,打破信息孤岛,让信息流、业务流互联互通,实现财务业务的一体化应用。
(4)利用工业云检测平台和AI模型算法,对产品实物进行分析检测,发现质量缺陷,提升质检效率,降低误判率,提升产品成品率,实现对光滑度、厚度等指标的自动判读。实现高档数控机床与工业机器人、智能传感与控制装备、智能检测与装配装备、智能物流与仓储装备等关键技术装备在生产管控中的互联互通与高度集成。
(5)对于存在较高安全风险和污染排放的项目,利用5G信息传输,实现有毒有害物质排放和危险源的自动检测与监控、安全生产的全方位监控,建立在线应急指挥联动系统。
3. 效益分析
实施项目后,给企业运营管理带来极大的提升。订单准确率提高20%,新产品开发周期缩短31%。。在订单管理上,通ERP系统下达销售订单,根据客户的不同要求,订单进行新产品研发。销售订单转到PLM上进行协同研发,公司在PLM系统上实现创新应用的大规模个性定制。生产工单通过MES系统,车间工人对生产工序进行汇报,可以实时监控到车间订单的进度,在订单交付周期上能提高10%左右。
在产品质检上,公司与专业人工智能公司进行合作,采用机器视觉进行人工智能检测。对产品的尺寸、光滑度等关键指标进行检测,取代人工单一的重复性测量,对产品进行百分百自动检测,提高检测效率,保证检测过程的准确性,提高企业竞争力。
车间产品下线后,通过AGV车进行物流调度,采用受计算机控制的各类物料搬运设备,按照工序要求将指定的物料及数量精确运送至指定工位。实现物料搬运的无人化作业,减少人工成本,实现物料管理流程的信息化,降低管理难度,提升生产效率,保障物料高效、准确地运送,杜绝差错。
通过基于SCADA平台的工业互联网,系统通过自动化接口中间件,兼容不同品牌自动化设备进行数据采集,构建完整的制造信息数据库,进而搭建生产管理和质量控制的智能平台,满足生产制程的追溯和管控需求,实现车间生产现场的透明化和自动化管理。与 ERP、PLM、CRM、SCM等信息系统整合,避免信息孤岛,提升生产职能部门的信息共享和协同效率,打造透明高效的智能工厂。
本文为e-works原创投稿文章,未经e-works书面许可,任何人不得复制、转载、摘编等任何方式进行使用。如已是e-works授权合作伙伴,应在授权范围内使用。e-works内容合作伙伴申请热线:editor@e-works.net.cn tel:027-87592219/20/21。