本文为“2022年度中国智能制造最佳应用实践奖”参评案例。本次活动将评选出2022年度,为中国智能制造领域带来突出效益的最佳实践工程,全面介绍企业推进智能制造的步骤、重点与难点、获得效益等,分享建设过程中的经验,供广大制造业行业企业学习供鉴。
一、企业简介
一汽-大众汽车有限公司(以下简称一汽-大众)于1991年2月6日成立,是由中国第一汽车股份有限公司、德国大众汽车股份公司、奥迪汽车股份公司和大众汽车(中国)投资有限公司合资经营的大型乘用车生产企业,是我国第一个按经济规模起步建设的现代化乘用车生产企业。经过29年的发展,一汽-大众产能布局已覆盖东北长春、西南成都、华南佛山、华东青岛以及华北天津,拥有轿车一厂、轿车二厂、轿车三厂、轿车四厂、轿车五厂、轿车六厂、动力总成事业部以及冲压中心八大专业生产厂。一汽-大众引用世界领先的大众集团MEB、MQB和MLB平台,生产的各个环节大量运用了在国际上具备领先优势的设备、工艺,从根本上保证了一汽-大众产品在每一个生产环节的精密和稳定。
动力总成事业部深入贯彻落实党的二十大精神,砥砺奋进,创新驱动,在设备领域践行“能快则快、进中求优、变中求省”,作为技术密集型生产基地,生产经验丰富,维修能力强,高精尖进口设备多,拥有国家技能大师工作室,技术人才储备雄厚。
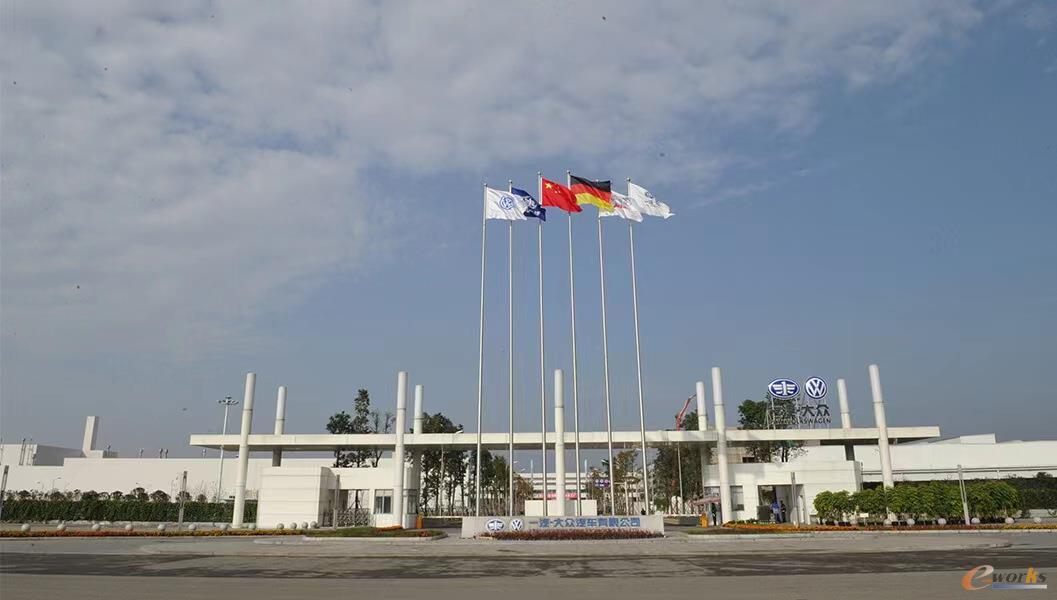
一汽-大众汽车有限公司
二、企业在智能制造方面的现状
一汽-大众在大众集团内率先启动Go digital项目,注重精益化生产,并致力于打造智慧工厂,完成五大基地从传统生产向高度灵活、数字互联、持续学习的智慧生产转变。该项目在2021年已经实现了七百多个创新案例,节约超过6000万元人民币。
在科技革命的浪潮下,汽车产业的发展也逐渐朝电气化,智能化,网联化等方向进行开展,如果说智能制造是一汽-大众未来蓝图的方向,那么华南基地就是指引的指南针。在仪式现场充斥着“智慧”、“智能”、“智造”等关键词,以 “智慧赋能新未来”为主题。在展示区,可以通过全息投影技术,与华南基地“亲密接触”,从多角度感受华南基地的创新力量;“未来驾舱”也是描绘了未来智能出行方案。沉浸式的数字化、智能化体验尽展未来美好出行生活。
动力总成事业部发动机车间,参加过很多智能制造项目及比赛,也取得了很多不错的成绩。如中德智能制造合作示范项目、第五届全国设备管理与技术创新成果、2022科创中国应用案例入库、第七届中国设备管理大会主题论文、第十六届、第十七届“东风日产杯”清华IE亮剑全国工业工程大赛三等奖等。
三、参评智能制造项目详细情况介绍
1. 项目背景介绍
1.1项目背景
习总书记指出,要坚持和完善社会主义基本经济制度,推动经济高质量发展,完善科技创新体制机制。弘扬科学精神,加快建设创新型国家,支持大中小企业和各类主体融通创新,创新促进科技成果转化机制,积极发展新动能,提升产业基础能力和产业链现代化水平。一汽集团在徐留平董事长的带领下,深入贯彻十九届五中全会精神,提效·变革,开展作风、体系、改革、成本四大攻坚战役,重点打造红旗品牌,努力提升合资企业行业地位。一汽-大众在潘占福总经理的带领下,积极落实十九届五中全会精神,认真学习十四五规划,全面打牢一汽-大众2025战略体系,做好年度经营,积极推动数字化转型工作,为企业再赋新动能。动力总成事业部积极响应公司号召,形成了以学习先进的工业工程方法,以人为本,推进事业部的转型升级,并服务全流程降本增效为目标,充分发挥老生产基地的管理和技术优势,培养数字化意识,实现数字化转型变革,并根据现有工作难点,重点推进工业工程领域的四方面工作:
(1)创建数字化的业务管理方式,提升管理效率;
(2)研究智能制造技术在实际生产中的落地转化,助力人效提升;
(3)助力新项目及产品快速迭代抢占市场,缩短项目建设周期,降低投资成本;
(4)卡脖子技术的解决和突破,持续的创造价值。
1.2项目目标
(1)效率提升
HPU是企业成本控制的核心数值之一,通过提升自身技术能力,对生产线自主实施自动化改进,优化操作人员。
(2)成本优化
利用互联网思维和工业工程方法转变维修工作模式,建立互联网思维+客户关系导向,鼓励员工加强自身学习能力,利用各类数字化工具不断优化现有工作流程,利用3D打印等技术进行自主设计及实施设备的自动化改造,降低项目成本。
(3)质量促进
质量是企业的生命,产品质量的优劣决定着企业的发展命运。利用机械视觉等自动化检测技术对发动机生产过程中的质量关键点进行100%监控,覆盖操作者不易发现的质量盲区,从而有效的保证产品合格率。
(4)产能保证
设备状态是保证产能的必要条件,利用数字化手段对设备的维修、维护进行实时、有效的监控,对设备的刀具和备件进行规范的数字化管理,有效的保证设备运行状态。
2.项目实施与应用情况详细介绍
针对以往公司存在的各个设备和维修相关的系统,多以孤岛形式出现,相互独立,无法互通。数据得不到共享和融合,在此基础上,通过对各个系统进行融合,打通系统和业务壁垒,避免了原有系统推倒重来,提升效率,节约成本,优化体系。同时,针对设备管理全生命周期流程中存在的具体痛点和问题,进行客户旅程分析,通过数字化方式进行业务模式重构和效率提升。
设备前期痛点:存在相同的业务数据在不同的系统中数据不一致的情况,如设备台账在维修APP和EAM两本账,查询应用困难,前期资料数据与服役期脱节;设备服役期痛点:生产数据缺乏联动,设备运行数据缺乏抓手,数据价值挖掘不够,无法实现设备运行数据采集、分析、指导、可视化等功能;设备服役期状态及参数管理管理粗放,缺乏追溯性;无法实现量化的维修人员技能评价与技能提升;无法实现量化的设备健康状态评价与提升,知识及技术积累没有体系;维修运维费用预算和成本管控粗放;同样的设备问题在不同的基地间重复发生;项目完成后验收资料查询困难,不利于快速解决问题;设备末期痛点:备件报废中对潜在需求备件识别不足容易造成误报废,资产处置效率慢,影响库房周转。为此,通过构建数字化业务模式和智能制造技术应用,来搭建设备全生命周期管理平台,解决设备各个阶段存在的问题。
数字化业务模式构建:集团公司在五大攻坚战中提出将全面体系与数字化建设作为重要战略,各地纷纷响应开展数字化转型,数字化的浪潮正以不可抗力滚滚前行。为实现制造领域全体系全流程的数字化变革,尝试利用数字化相关技术,通过python、java、JavaScript、php进行自主编程、自主设计、自主开发,通过Power Bi进行数据处理、数据清洗、数据再加工,通过tableau进行可视化展示和数据开发。通过利用先进数字化技术,围绕生产开展全流程全业务数字化,实现工厂管理数字化变革,提高人员数字化能力。经过数字化赋能,为工厂提高效率、降低成本、增强质量注入了新的活力。
智能制造技术应用:目前,我国仍处于“工业2.0”(电气化)的后期阶段,质量基础相对薄弱、产业结构不合理、资源利用效率偏低、行业信息化水平不高、劳动力成本提高。基础此,动力总成工厂正在加速产业升级,通过运用工业工程方法理论,加速推进工厂自动化、网联化进程,逐步向智能制造迈进,目标打造标杆级智慧工厂。
2.1数据采集——硬件IOT建设+软件
硬件采集:设备+重点零部件。对储存在现场设备CPU中的数据进行数据传输、转存得到设备运行的详细参数。设备运行状态参数,包括主轴、夹具、流体、电机等部件的温度、压力、震动、流量、电流等。设备运行参数,包括涵盖转速、进给、温度、功率的机床运动部件关键质量参数。
软件采集:维修APP+宜搭低代码。维修APP的优化升级后,增加基于用户体验和实际需求的功能升级包含了四种不同的数据采集模式,分别为设备数据、故障数据、备件数据、人员数据等。从设备维度上来讲,实现了设备开动率的提升以及设备全生命周期的管理;从故障维度上来讲,可以做到故障真因分析,有利于打造零停台体系。同时做到维修的三阶段解析,针对性的提升维修效率;从人员维度上来讲,提升了人员能力,实现了人员工作的量化考核;从备件维度来讲,实现了单台设备维修成本的全生命周期管控,于降低成本而言,利于实现备件的国产化以及对废旧备件进行二次利用。宜搭低代码,可以实现关于设备、安全以及其他日常管理数据的实时采集。
SAP-PM系统融合-信息集成,SAP系统(systems applications and products in data processing),又称企业管理解决方案,其功能为:借助软件程序为企业定制并创建管理系统,对企业的人力资源、物流运输、销售服务、交易支付、产品规格及质量、生产活动、原材料采购、货物仓储及库存管理等全部经营活动与环节,实施监督、分析及管理,形成数据化的资源管理系统,为企业生产、决策、组织运营提供指导及依据,有利于企业财务管理质量的提升,有利于企业资金的合理分配。PM设备管理系统,为工厂提供了关于设备、成本、库存的一系列管理内容,涵盖设备清单、故障通知、预防维修工单、故障维修工单、故障维修反馈。将两系统进行融合,为为生产实现了一个数字化的库房,从成本、备件、工单、领料发料等方面,实现了数字化、智能化的管控方式。
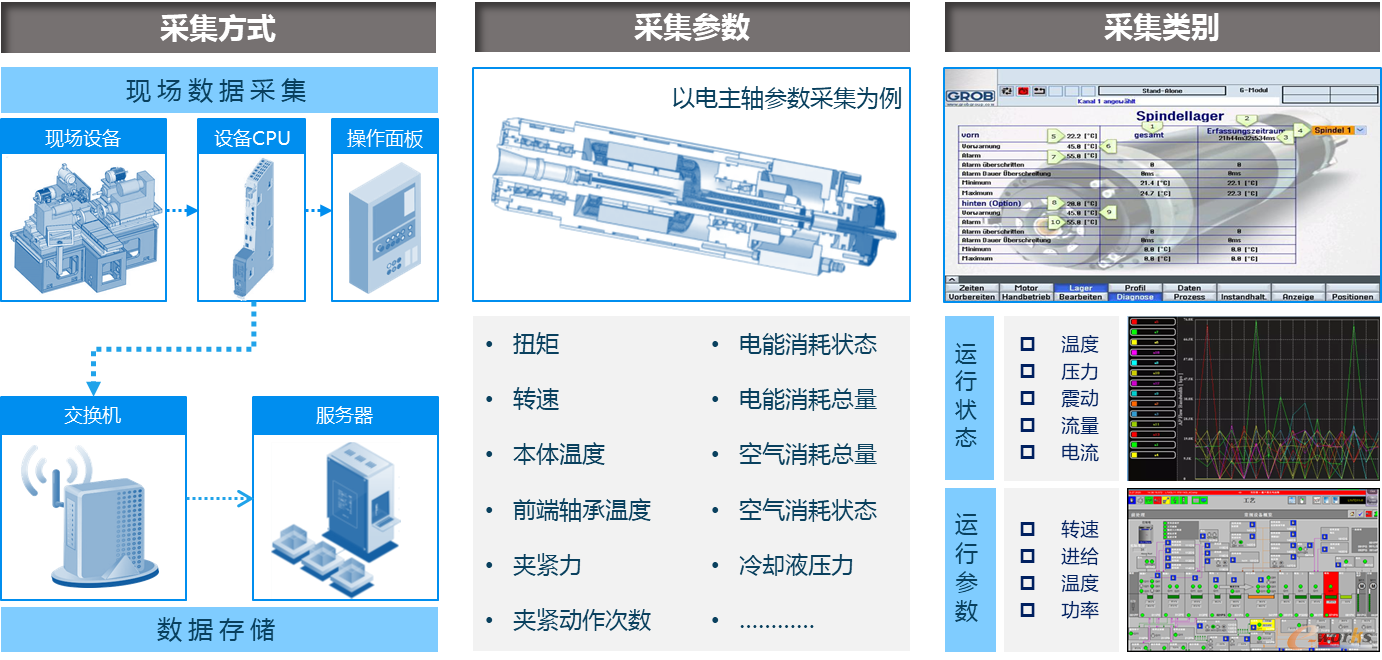
图1 硬件数据采集
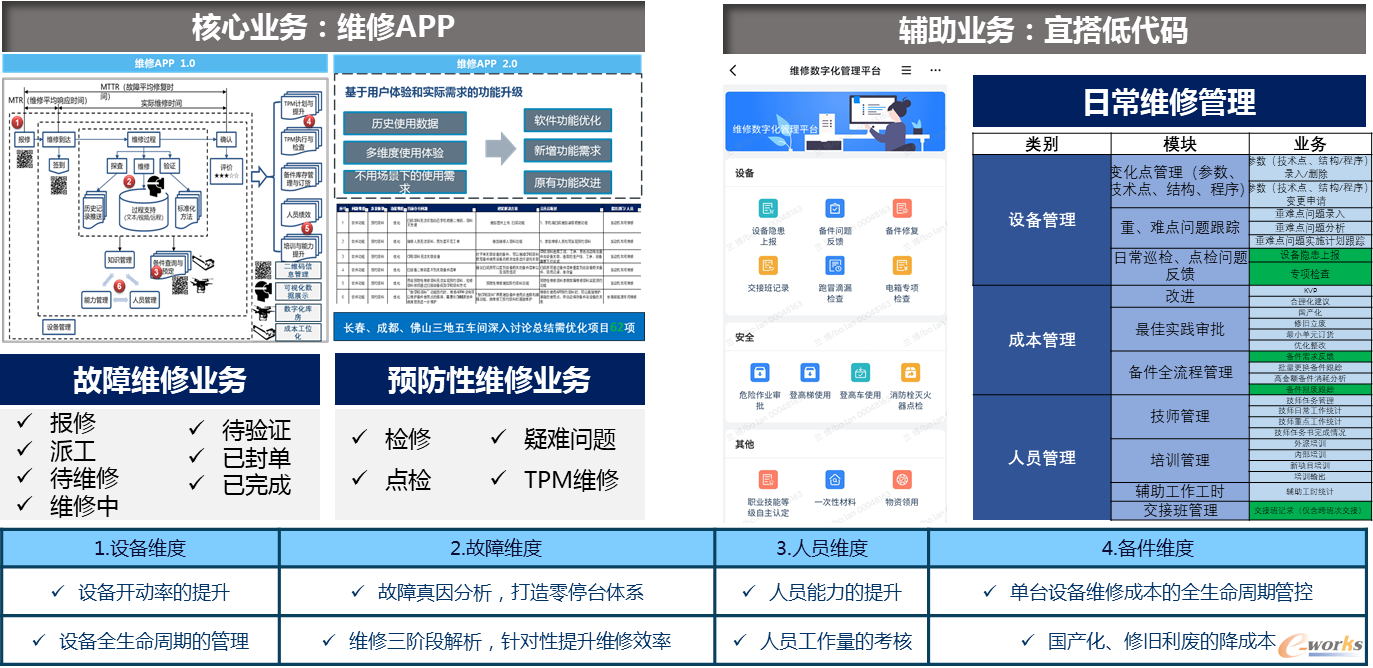
图2 软件数据采集
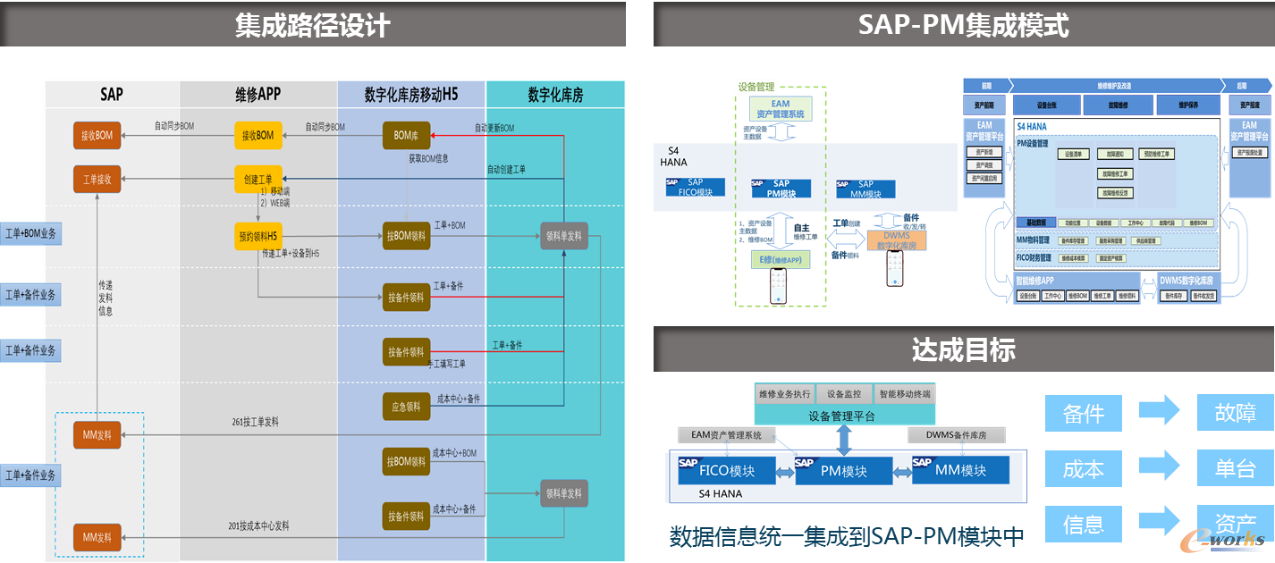
图3 数据信息统一集成
2.2数据监控——数据监控平台
数据监控的接入方式有很多种,PC端、手机、手持设备PAD、现场屏幕以及其他智能设备都可以接入,实现在线的实时监控以及不同设备之间的相互连接。数据监控是通过使用低代码平台构建一个设备管理平台移动端,通过移动化的应用实现标准化、体系化、架构化的数字化生产流程。该种方式的业务场景很多,可以应用到设备管理平台,作为维修APP的拓展;还有已经上线的备件数字化库房,可以实现关于备件入库、备件调拨、备件出库、备件跟踪、备件报废、旧件管理的一个全周期的管控。对于设备的监控而言,不仅可以监控设备运行时的实时数据以及他的运行趋势,还可以监控设备在一定时间周期内的设备综合效率(OEE)。
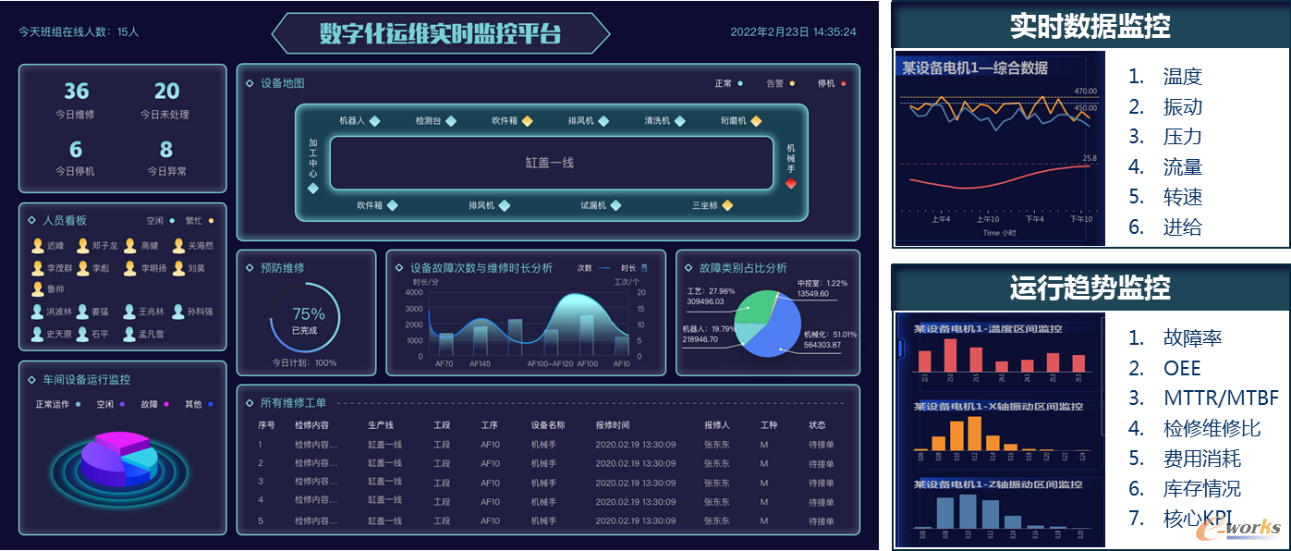
图4 数据实时监控平台
2.3数据分析——Tableau大数据分析
Tableau大数据分析,主要为设备运行状态分析、成本分析、重点指标分析、在线数据监控四大部分内容。该系统通过提取的维修APP数据,利用Power Bi软件进行数据处理、清洗和再加工,再利用Tableau Desktop进行数据可视化呈现,形成一套完整的用于维修管理的数字化驾驶舱,将数据作为发挥到最大。数字化驾驶舱项目完全自主实施,在项目实施的过程中,员工熟练掌握商业BI软件的操作和应用,提升员工数字化能力。整个驾驶舱包含六个模块:设备运行状态、维修工作状态、人员管理、设备在线状态监控、成本管理、能源管理,从时间、品牌、生产线、部件四个维度进行分析,推动维修体系变革。该系统通过全业务链数据呈现,提升了维修管理的可视化水平,实现了维修管理数字化升级;通过全业务链整合闲置数据,发掘了数据深层价值,利用数据实时性、全局性、历史性的特点实现了数据价值深度挖掘;通过全业务链数据智能分析、预测和应用,实现了智能决策。
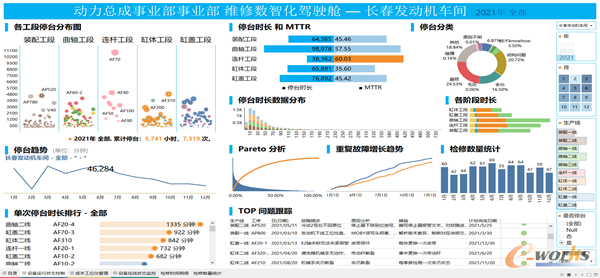
图5 设备运行状态分析
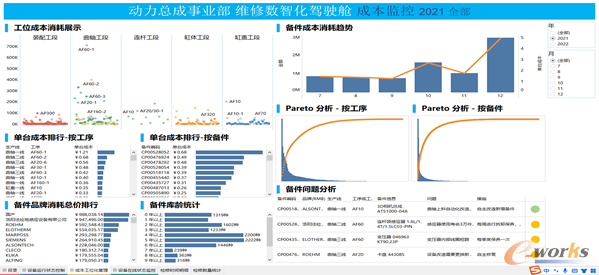
图6 成本消耗分析
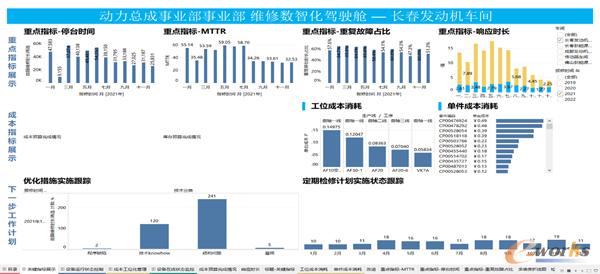
图7 指标及任务计划
2.4数据应用——智能预警、分析、诊断
通过对数据的集成分析,可以将其应用到预测性维护、设备健康管控评价、数据结果智能建议、智能任务布置、问题根本原因分析、智能预警、智能诊断等领域。智能预警:通过设置管理,实现预警指标的自定义。采集设备运行状态及故障数据后,通过神经网络算法与故障模型库进行比对,对设备运行中的异常情况实时预警,协助工作人员及时发现设备故障。模型训练:平台采用神经网络算法,通过对设备运行参数提取及特征识别,建立多维算法故障模型库,对设备运行时各种异常情况提供诊断依据。智能诊断:具有平台智能诊断功能,依托神经网络算法与故障模型库对机械设备的运行情况进行诊断,并出具诊断报告,协助维护人员“预知维修”。
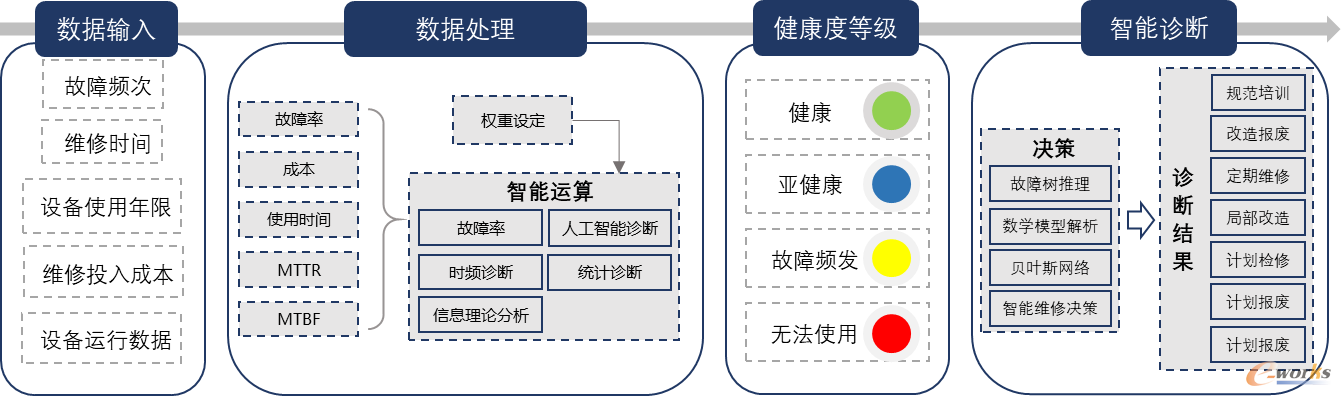
图8 智能诊断
2.5可视化展示——设备综合管控看板
数据的可视化可以通过数字化的手段实现,将数据可以集成到一个设备综合管控看板上,不同级的管控看板展示的内容及数据各有不同。公司级综合看板,重点实现公司级设备资产的卓越运营绩效管理与统计分析运营看板。厂级综合看板,以工厂的设备管理为范围,实时展示工厂设备的运行情况、成本情况、目标达成情况、重大任务达成情况。车间级综合看板,综合展示车间的重点任务、绩效指标、关键KPI指标、目标完成情况、车间设备故障情况等。个人综合看板,实现个人工作的“一目了然”。以岗位任务为基础,展示所涉及设备的报警情况、运行情况、个人KPI情况,实现岗位信息的透明化。支持APP端与PC端同步展示。通过一系列的可视化看板,可以达到解放管理者,流程透明化,强化过程管控,信息公共化的目的。
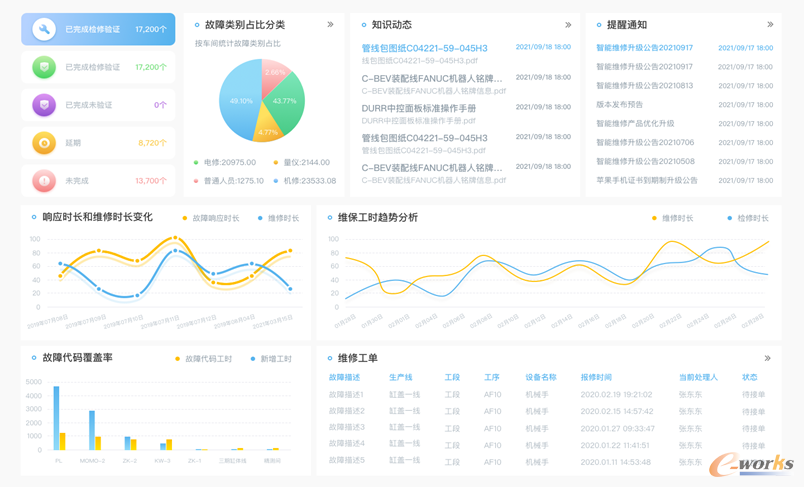
图9 设备综合管理看板
2.6知识积累——动态人员能力评级体系、知识积累平台
通过数字化的手段对人员的工时及是否停台做记录,通过对已经记录的不同人员数据进行比对分析,可以得到不同人员操作技能的差异化。同时以最优的操作技能的人员操作方式作为标准的操作方案。将该方案通过课件、视频、文件等形式搭建好,输出给技能最佳人员确认后再推送给其他人员员进行培训强制学习。培训结束后,组织全体人员进行评价考试,从而得到培训后新的标准,在以新的标准对人员进行培训。通过这种方式,可以搭建起一个动态的维修能力评价体系。可以让员工时刻了解自己的状态的同时,实现故障维修标准的刷新以及维修人员技能的提升。通过标准动态不断地刷新,形成知识的不断积累,搭建起首个专业知识积累平台。实现了管理上的变革,打造了一个知识的摇篮、技能提升的平台、提升了故障维修效率、积累了预防维修的经验、提升了人员标准掌握程度、实现了维修专业知识、经验大数据化、智能化的管理、实现维修人员知识积累工时的统计。
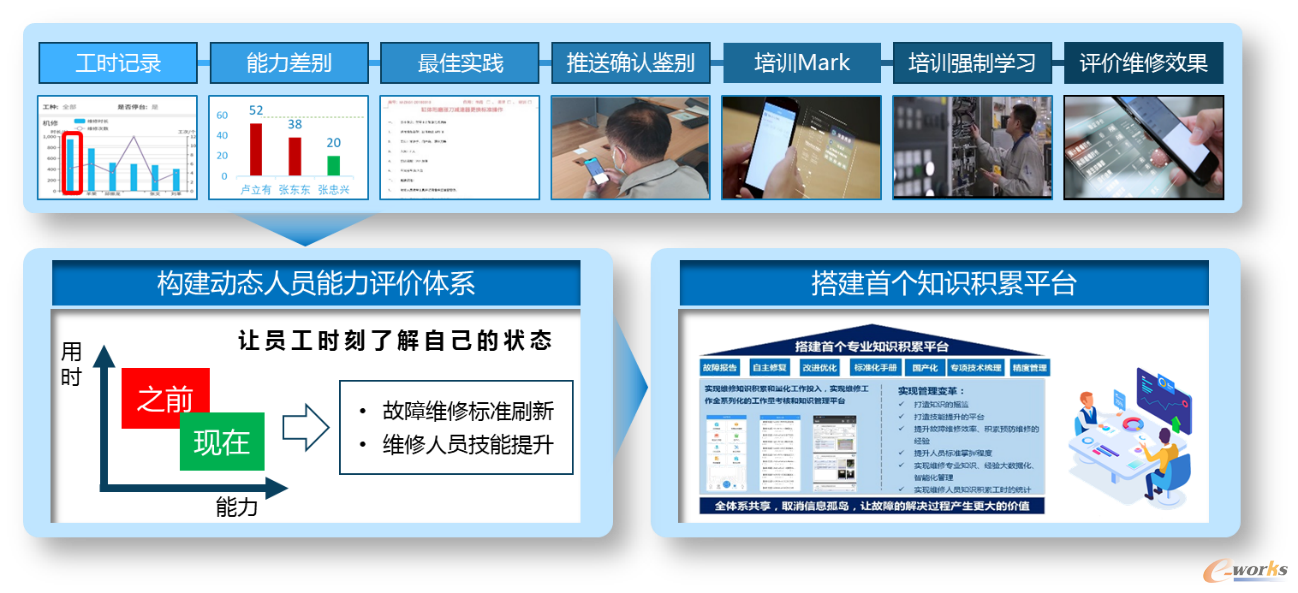
图10 知识管理
3. 效益分析
3.1效率改善效果
(1)发动机车间HPU优化降幅达到4%
(2)创新生产刀具数字化、分布式仓储模式,优化存货结构,大幅提升库存周转率
3.2成本改善效果
(1)2022年变动费用单台降低12%
3.3质量改造效果
(1)2022年质量监控器中国区排名前列
3.4生产经营改善效果
(1)2022年OEE提升2%,生产效率提升显著