本文为“2023年度中国智能制造最佳应用实践奖”参评案例。本次活动将评选出2023年度,为中国智能制造领域带来突出效益的最佳实践工程,全面介绍企业推进智能制造的步骤、重点与难点、获得效益等,分享建设过程中的经验,供广大制造业行业企业学习供鉴。
一、企业简介
上海纳铁福传动系统有限公司是国内汽车零部件制造行业最早成立的中外合资企业之一。主要投资方是GKN传动系统国际有限公司和华域汽车系统股份有限公司。公司于1988年9月合资开业,目前在上海设有康桥、周浦、申江、叠桥四个分公司;在武汉、长春、平湖、仪征分别设有四个分公司和一个装配基地(其中平湖同时设有子公司);并在重庆设有纳铁福重庆公司(合资)。公司主要生产汽车传动系统总成产品及零件,立足于“秉承精益,追求卓越,成为国际一流的传动系统供应商”的企业愿景,竭诚为国内外主机厂提供配套服务,占据国内市场领导地位,核心产品“等速传动轴”在国内市场占有率超41%。公司设有对于汽车传动系统具有原始研发功能的技术中心,拥有一流的工程技术开发团队和完整的试验验证体系,为客户提供一体化的传动系统解决方案。
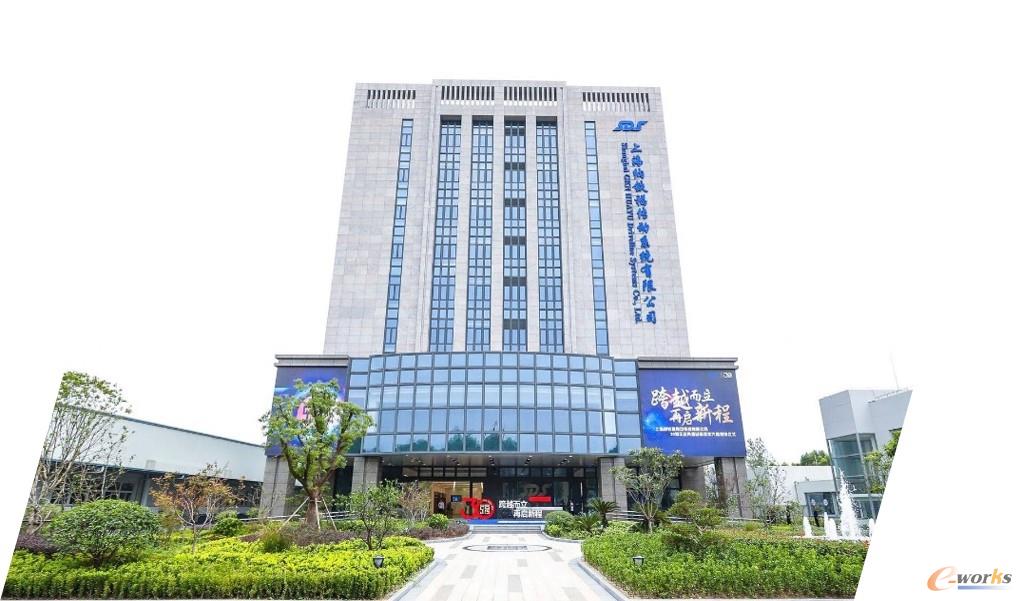
图 1 上海纳铁福传动系统有限公司
二、企业在智能制造方面的现状
在华域汽车的指导下构建的公司数字化推进框架,构建符合自身发展的上海纳铁福数字化工厂“三四八四”转型框架并梳理数字化战略应用项目推进现状(图2)。
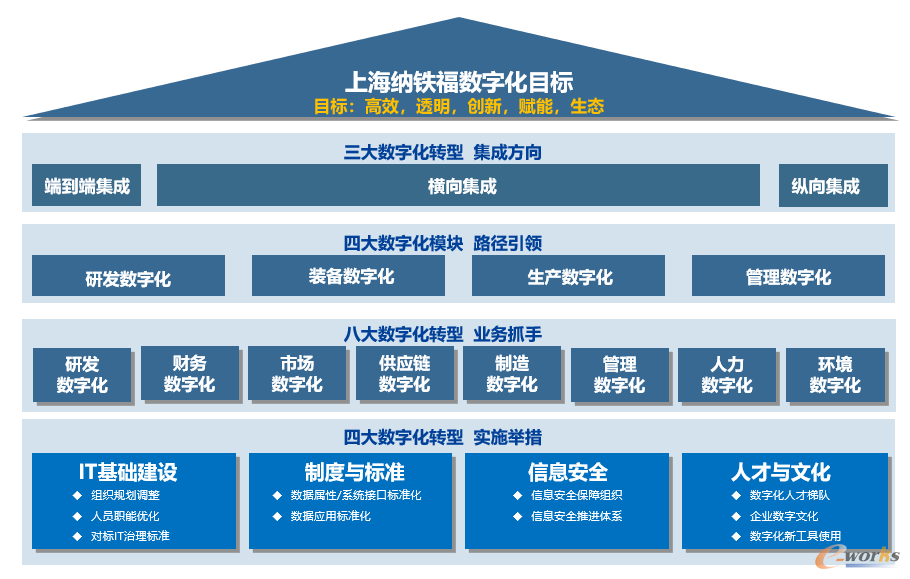
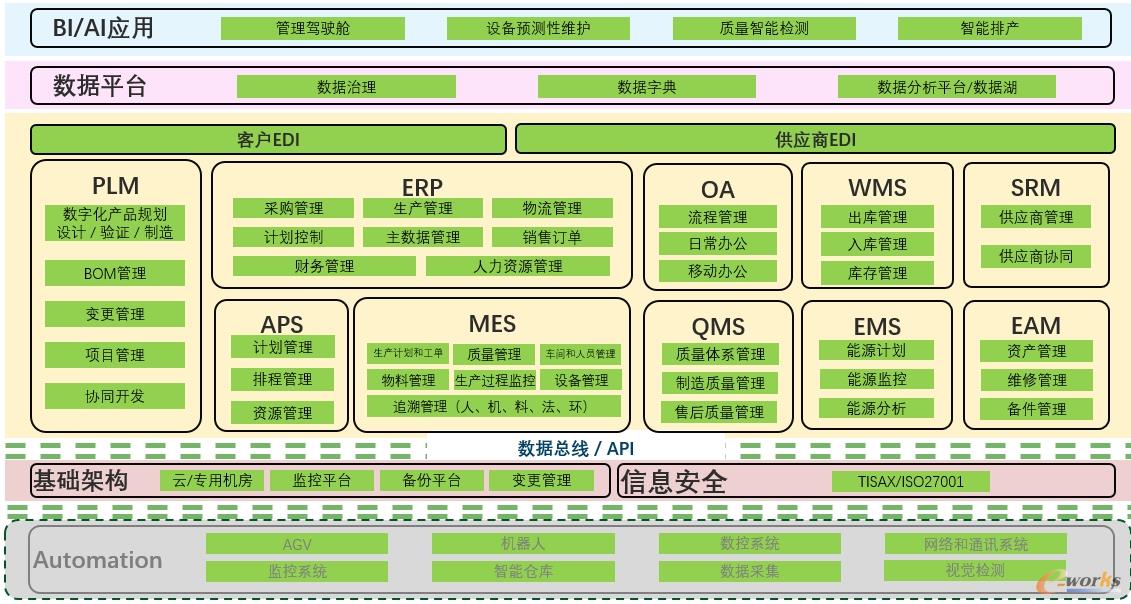
图 2上海纳铁福数字化工厂“三四八四”转型框架和数字化战略应用项目推进现状
三个数字化集成方向:工厂整体数字化工厂建设围绕公司三个集成作为建设方向,围绕产品全生命周期的数据集成,从客户工程到SDS设计研发的端到端的信息集成。在研发过程中通过跨设计平台的数据自动转换和流动,实现产品全生命周期管理,大幅缩短项目开发周期。围绕产品全供应链信息集成,SDS实现了在项目批产后从原材料采购到产品加工及成品交付的横向集成。SDS在生产执行中,各业务系统间信息流完全打通,实现正反双向追溯及精细化成本管理。从生产设备到运营管理系统最终至数据分析和决策平台的纵向集成,SDS实现了生产运营趋势的透明化。从物理层链接到分析层,实现人、物、系统的多维度分析,对公司决策决定提供数据支持。
端到端集成:打通了客户需求输入,设计研发,工艺开发,样件试制、客户交付、市场反馈,通过不断的产品迭代满足客户需求。根据客户输入,通过数字化工程平台,为用户提供高效优选的工程开发方案打造协同化开发、系统化方案、智能化选型、数字化设计的快速高效准确的研发平台。共享工程开发数据,建立完整的仿真体系,通过结构化数据,配合电子实验室平台,数据积累和算法沉淀,提高零件试验效率和可靠度。通过内外部信息收集,不断对比、优化、完善,提供用户满意的新一代产品和工程服务。
纵向集成:打通线边设备到数据分析平台,利用IT 、OT和DT技术赋能智能制造。运用工业互联网及5G技术实时采集能耗记录、设备运行状态,实现精细化能源、设备全生命周期管理及跨系统数据链路备份。公司全域部署制造执行系统MES,质量管理系统等生产系统,以工单为中心的制造全过程可视化、原材料到成品完整生产追溯、工艺质量的监控与分析,提升质量稳定性和生产效率。企业资源管理系统ERP,将计划、采购、生产、销售、财务成本有机协同,实现业务财务一体化,洞察企业运营状态。通过底层信息的纵向集成,有机衔接各个业务系统,消除信息孤岛,不断提升企业的运营效率,快速支撑和响应业务需求。实现数据驱动业务,提供实时现场可视化、KPI数据查询服务及管理驾驶舱,用数据驱动辅助决策。
横向集成:打通从客户需求到制造再到客户交付的全链信息集成,产业链协同工作。电子信息交互平台EDI实时高效的获取客户最新需求计划并传递至企业资源管理系统ERP,物流人员借助高级排程系统APS开展计划排程工作,通过实时共享互联信息和系统内嵌的精密算法,大幅提升计划排产的效率和准确程度。由供应商EDI系统快速准确进行物料的采购与拉动。AGV和上下料机器人协同工作,实现物流智能配送,大幅提高物流运作效率。通过APS与MES等系统的信息实时交互与动态匹配,全面提升生产计划执行准确性。运输管理系统TMS实时监控物料流动状态,保证货物安全准时交付。结合数仓系统对大数据进行即时运算、实时分析与动态调整,打造横向集成的智能化产业链。
四个数字化模块路径:构建研发数字化、装备数字化、生产数字化、管理数字化。
八个数字化业务抓手:根据公司基本业务拆分,并且有业务领导委外数字化专员与数字化小组一同制定分业务数字化规划与计划,讨论项目实施可行性,专题学习等,避免“闭门造车”。内部有研发、财务、市场、供应链、制造、管理、人力和环境等8个数字化内容。
四个数字化实施底座:全面建设IT基础建设如机房建设、网络建设、数据保证等措施为数字化建设保驾护航;重点关注信息安全建设,实施ISO27001及TISAX认证提升公司整体信息安全水平,关注工控信息安全实施;关注数字化人才梯队建设,开展“请进来,走出去”的调研学习活动,培养数字化人才,构建企业数字化文化;关注数字化赋能管理,以数字化推动公司创新变革、统一管理、降本增效的任务,将数字化工作落在实处。
三、参评智能制造项目详细情况介绍
1. 项目背景介绍
上海纳铁福申江工厂的数字化工厂建设始于2017年。该工厂是上海纳铁福传动系统有限公司在周康地区的一个分厂,主要生产纵向传动轴的一个工厂。该数字化工厂的建设是基于上海纳铁福公司的“三四八四”数字化战略理念,旨在通过引入先进的自动化和智能化设备,部署高度集成的信息化系统,提高生产效率和质量,降低生产成本,优化供应链管理,实现数字化、智能化和绿色化的工业生产。
在数字化工厂的建设前,系统之间没有交互集成,增加了实物流和信息流不一致的风险。工人技能水平不高、设备维护不及时、生产计划不准确、能源消耗大、质量控制不严格,都增加了工厂的生产运营成本。
在数字化工厂的建设中,上海纳铁福申江工厂引入了自动化生产线、智能仓储系统、智能物流系统、智能化质量检测系统等先进的生产设备和系统。这些设备和系统通过互联网、物联网等技术实现了互联互通,形成了一个数字化、智能化的生产流程。同时,上海纳铁福申江工厂还通过智能化供应链管理系统,实现了供应商、仓库、生产线、物流等环节的全程跟踪和管理,提高了供应链的透明度和效率。
2. 项目实施与应用情况详细介绍
系统联通数据交互:随着PLM、MES、SAP三大系统的逐步上线,纳铁福基本实现多系统互联及数据集成(图3)。主数据方面由PLM将物料、产品结构、替代物料、工艺、生产版本、变更记录下发至SAP。同时PLM将控制特征、临脱工艺、组件分配、工艺指导书、工艺资源、标准操作规程、防错布局图下发至MES。功能数据方面由SAP将工单、仓库配料、巡线送线、扫描上线、AGV和立库管理信息同步至MES。同时MES将工单拆分、实验委托、道序委外、成品下线、隔离报废、完工报交、Safe Launch检验、返工拆解信息同步至SAP。
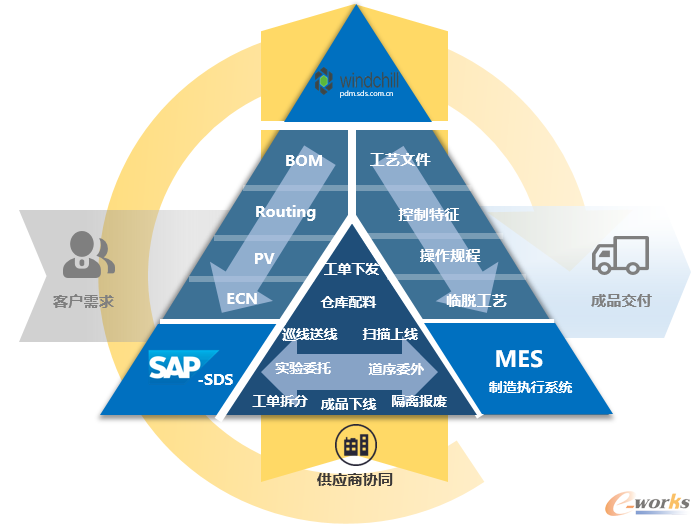
图 3三大核心系统集成
纳铁福的生产供应链从EDI平台或RPA抓取客户网站/邮件接收到客户需求,SAP拆解成主生产计划和物料需求计划,一方面根据生产需求平衡形成颗粒度更细的物料需求计划,借助APS高级排产系统形成工单。另一方面SAP下发采购计划至SRM供应商管理平台,供应商按计划创建送货单,仓库收货后需要质检的物料在QMS质量管理系统判定,随后在EWM系统上架。SAP将工单下发至MES系统,物流通过EWM完成移库上料,质量在MES里创建精测金相委托单,MES根据工单产品的控制特征,记录过程检验数据。如果有道序委外通过EWM将库存信息发送至SRM系统,随后委外收货,MES投料至线上继续完成生产,下线报交,Safe launch质量判定合格后,产成品入库,报工和库存信息同步至SAP。最后SAP创建销售发运单,通过TMS运输管理系统跟踪发运情况,确保成品销售发运至客户处完成交付。从客户计划、采购需求、生产制造、仓储管理至销售发运实现了数据交互不落地,提高系统时效性,保证信息流和实物流的高度一致(图4)。
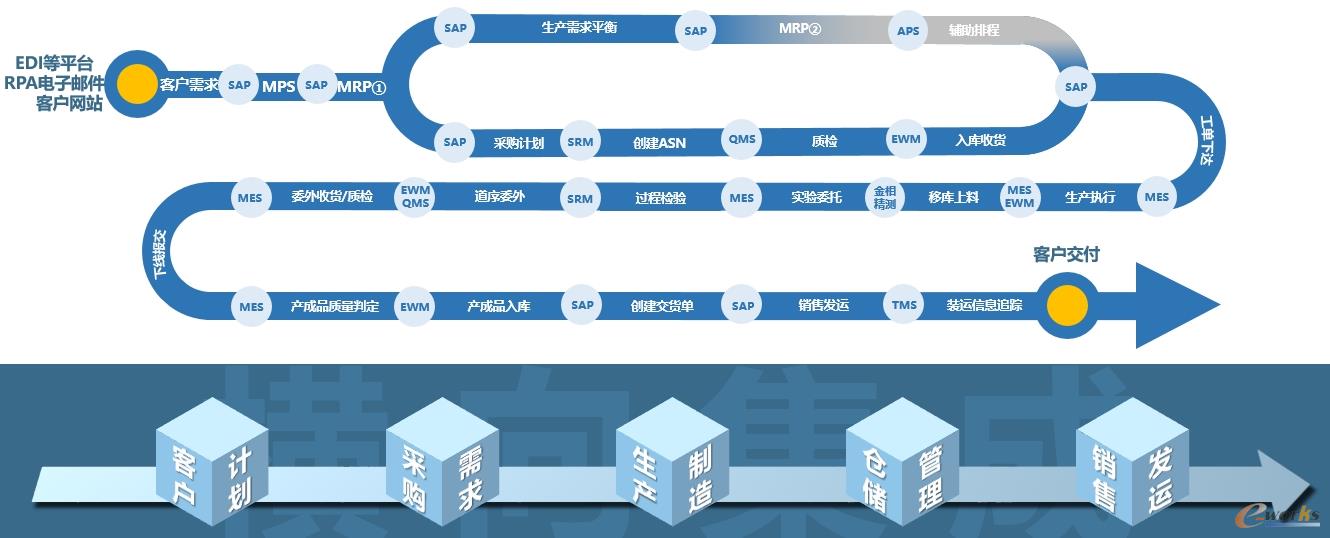
图 4横向集成
自动化技术创新:申江数字化工厂开创公司内首个针对PS传动轴花键轴零件开发的一条集生产自动化、送料智能化、信息可视化为一体的标杆产线。线内采用一台机器人及独立的PLC总线,将NACHI搓齿机、EFD中频热处理设备,结合为整体,实现信号交互与联动,实现全自动生产。
同时通过产线外部配备一台机器人,两套梅卡曼德3D视觉系统,以及自动化料道,并结合虚拟仿真系统,通过3D视觉系统的深度学习数据采集功能识别零件及料框状态,分析出零件点云,自动智能地为机器人规划抓取、放置路径,同时实现来料上料的无序抓取及成品下料的无序码垛(图5)。现场的屏幕也能实时模拟仿真自动上下料的状态,观测视觉检测零件识别信息等,经过信息的集成,生产线才得以以数字孪生的形式准确透明的展示给我们工程师的面前。
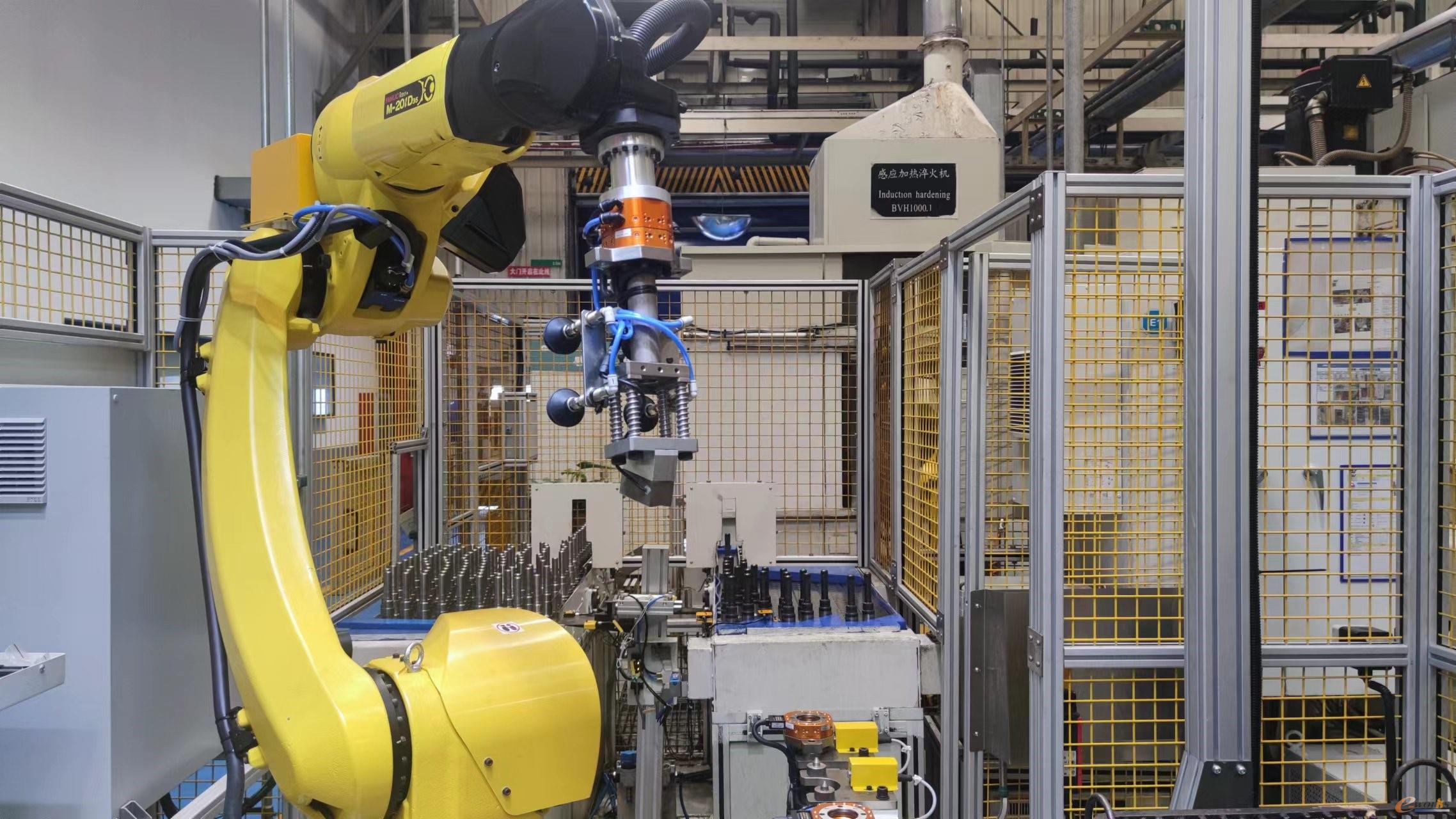
图 5带相机识别的自动抓取机器人
IOT技术创新:申江数字化工厂连接轴自动装配线同时运用光学、信号、机械等多种方案实现生产所有零件的防错,同时设备内部配备高精度伺服电子压机,所有生产过程参数直观可控。通过固定式读码器识别轴体端面二维码,进行产品的重复性及符合性校验,确保产品质量的同时也凭借此信息将本地生产数据与供应商生产数据绑定,确保精确追溯链的完整;产线还配备两条独立的NG料道,一旦出现不合格品,第一时间踢出并提示异常;产线内由每台装配设备配置的独立PLC,同时产线另有一台总控PLC控制整体生产流程,并赋予每根连接轴总成一个唯一特征标识(虚拟ID),结合MES系统获取ID信号更新后,采集所有设备的加工参数进行跟踪,最后使用自动在线标签打印功能整合、绑定所有信息后存入MES系统,实现产品的精确追溯。
设备预测性维护:申江工厂目前拥有300多台生产设备,设备的数量和种类都非常多。目前和基恩士合作试点预测性维护系统,为了实现这么多设备的更优质更高效的管理及方便后期的维修保养作业。通过对各设备的不同维度的数据进行采集,利用采集到的数据建立模型来生成实时健康分和趋势图,从而对于设备的健康状态做出有效的评判,对于设备潜在的问题做出可靠的提前趋势预测并进行预警提示。同时还可以建立相关的测点数据规则,方便日后的预防性维护作业,有效降低故障率,减少设备的非计划性停机时间,提升设备MTBF、MTTR这些关键指标。
增材制造3D打印技术:产品的特定位置需要经过“中频淬火”这一工艺工序来提升强度与硬度,所以针对这种工艺使用工装“感应线圈”进行3D打印新技术尝试。人工制造的感应尺寸精度差、焊接成本高,且由于焊接导致线圈导电性能和冷却性能的下降,增加了热处理能耗,3D激光打印新技术解决了上述传统感应线圈人工制造中的痛点(图6)。
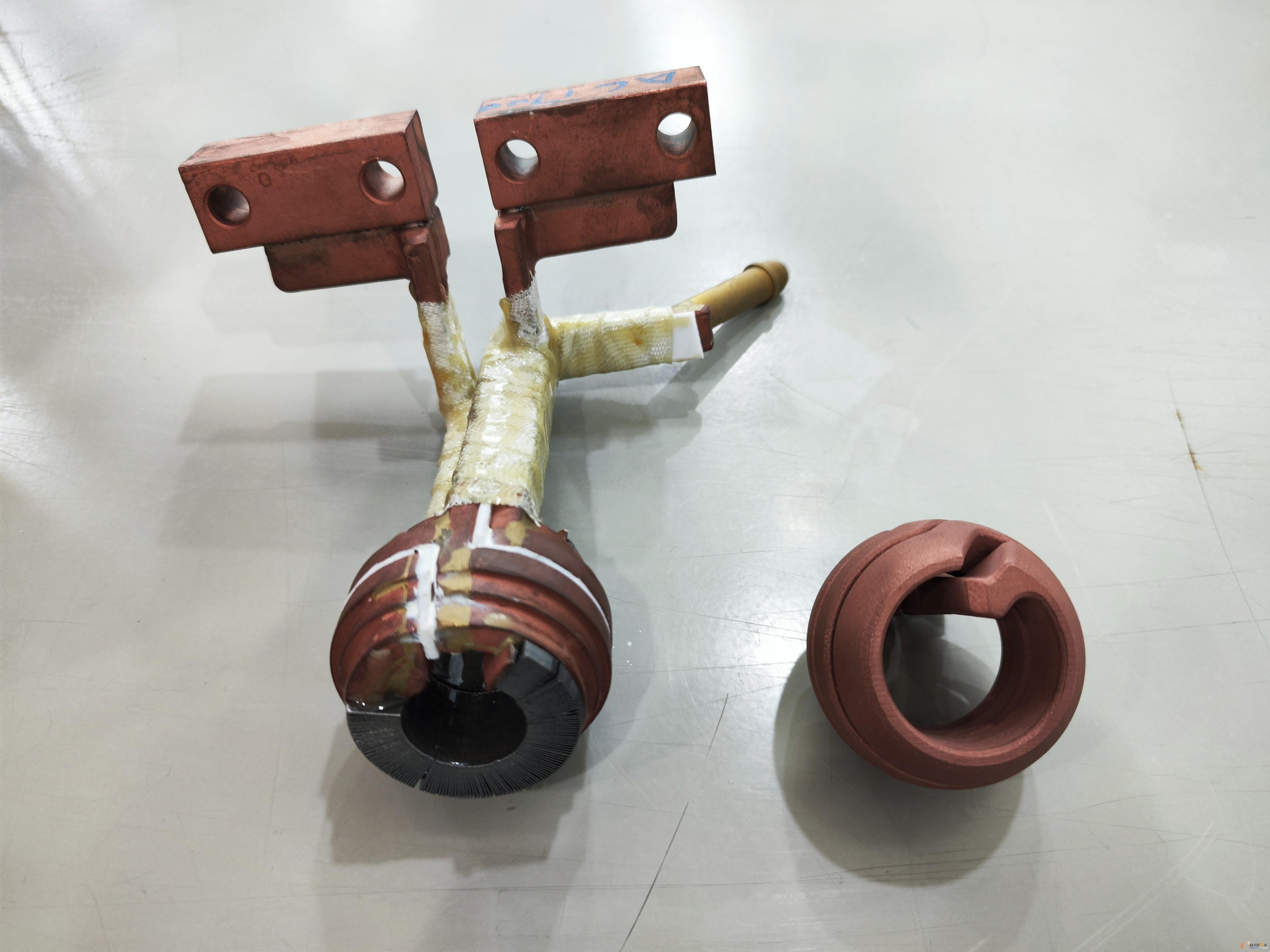
图 6传统感应线圈与3D打印感应线圈(右)
从近一年公司整体投入的数据显示,从时间、成本、工艺效果等方面我们发现:首先投入产出有极大的提升,基于设备的优势,同一时间可以多个生产;加工成本上节省了大量的人工与原材料;并且基于3D打印一体成型的工艺优势,新感应线圈的间隙、壁厚按照设计要求生成,并且没有了焊点焊缝,工艺加工的寿命与效果得到极大的提升,根据多工厂数据表现可以看到寿命提升超200%,还有意外之喜就是新材料更好的电传导率与加工精确性,在中频设备内零件加工时所需要的能量能耗有近25%的下降,当然也在制造工程部门中开创的新的3D打印新工艺的职能探索。
RPA流程机器人自动获取客户计划(图7):基于工厂核心骨干完成RPA新工具的培训,供应链方向开发了数条自动获取客户需求的机器人流程:如一汽大众周需求、上汽大众周需求、北京奔驰亦庄工厂周需求等,定时自动触发,提升人员工作效率。
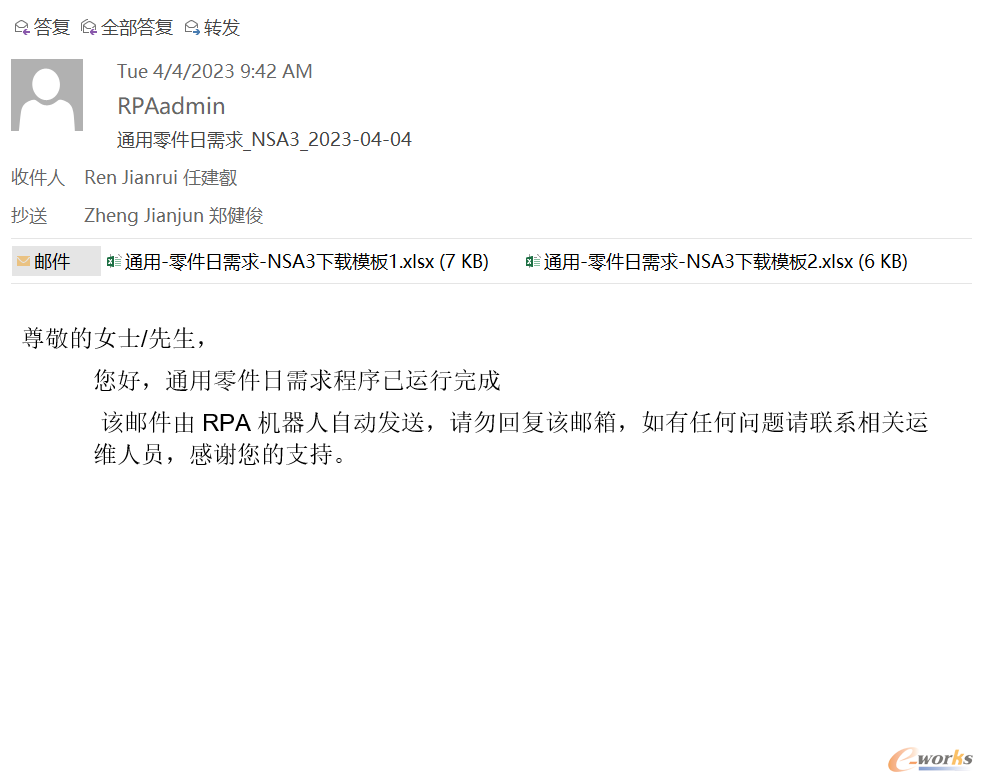
图 7RPA流程机器人自动完成工作后的邮件交付
APS高级排产系统:申江工厂2022年完成APS系统部署,在工厂多品种、多客户、多层级BOM的排产条件下,在排产效率、计划准确率、库存管理、风险防控、计划协调等方面有很大提升空间,通过采用APS高级辅助计划与排程系统,将客户端需求计划、生产作业排产计划、采购计划等供应链业务进行升级提质,通过资源条件约束、智能算法、仿真模拟等智能化算法,并对接公司的SAP/MES系统等系统,全面集成生产相关的业务流程,确保生产计划顺畅运行,提升生产效率,优化库存管理,降低库存金额 10-20%,提升排产作业效率70-80%,提高企业生产力和竞争力。
厂内智能物料配送:申江工厂共有7台激光SLAM激光引导叉车式AGV(图8),5台二维码潜伏式AGV,覆盖全厂内物流搬运业务,包括零件,BOP,料箱送线,线内搬运,成品下线等物流业务,配合EWM仓储系统,MES智能制造执行系统实现厂内物料自动配送。叉车式AGV可直接铲运原有BOP笼车、铁箱、折叠箱、托盘等工位器具,减少工位器具投入。在同一地图上,两种车型混行,路线和上下料点位均需要针对不同的车型设置不同的准入限制。对于单向道路设置避让点和断头路逻辑判断。项目实施后,减少库存金额10%,提升库存周转次数8.2%。

图 8正在工作的SLAM激光引导叉车式AGV
3. 效益分析
依托智能制造大数据,IOT等系统和项目的应用,上海纳铁福力求不断提升企业运营效率、打通信息孤岛、实现产业链协同。数字化工厂基本建成后,设备联网率为70%、数字员工(包含AGV、机器人、视觉检测、RPA)总数提升500%、提升设备综合效率OEE10%。智能制造推进项目除了带来每年数百万的经济效益以外,还起到很好地新型数字化及自动化解决方案的探索示范作用,其中纳铁福康桥工厂被授予上海市首批20家智能工厂荣誉称号,申江工厂作为标杆工厂经验横向推广的项目也将具有示范效应,助力“上汽新四化”迈向高质量发展新阶段。
工厂驾驶舱:申江工厂2023年完成工厂驾驶舱(图9)的部署,立足工厂视角、基于精益生产管理理念的数据化运营,梳理各个职能在数字化方面的需求,力争将各类系统打通消除信息孤岛。累计梳理了60个工厂相关的核心业务指标,主要连接了八个应用系统,95%以上的数据是通过数仓进行自动对接,从业务职能来看,驾驶舱实现了八大业务职能,分别是EHS、安全、质量、效率、物流、设备、能源、人事、财务;从场景应用来看,实现了工厂会议、BI数据分析、实时监控三大应用场景。实现从设备物理层向上打通应用系统并将信息抽取汇总到分析决策层的纵向集成,通过驾驶舱可视化手段进行展现,供管理者进行决策,在原有基础上提升工作效率60%。
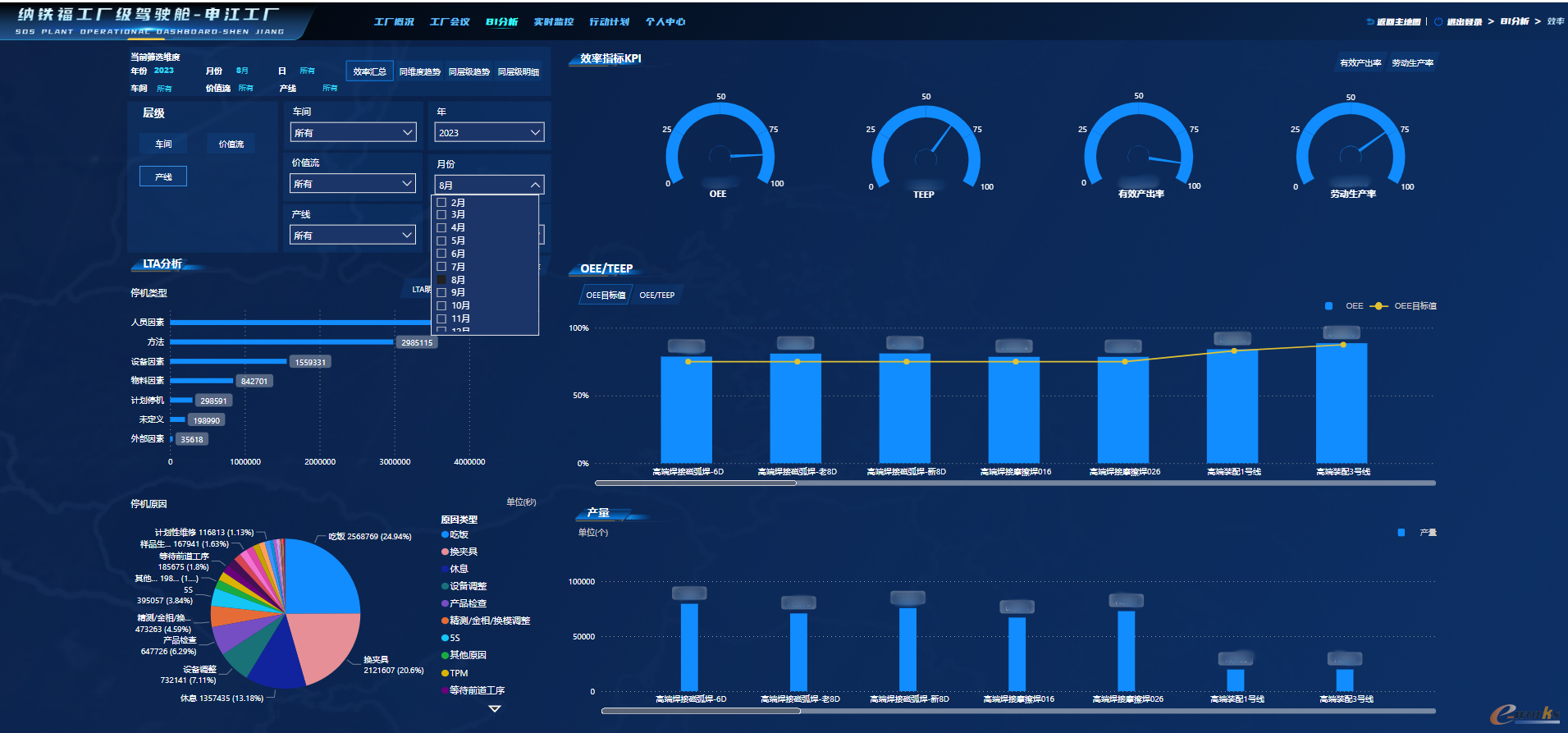
图 9申江工厂驾驶舱分析页面
数字化质量管理:质量管理系统100%覆盖申江工厂所有产线,通过问题管理、批次和精确追溯管理、数字化量具、3D视觉检测技术等提升一次合格率19%,工厂内部报废率损失降低15%,降低客户抱怨率和质量索赔金额。
智能物流:结合厂内智能物料配送、APS高级排产系统、TMS运输管理系统项目减少库存金额10%,提升库存周转次数8.2%,提升排产作业效率70%,OTD从订单到交付的全过程时间下降18%。
光伏部署:申江工厂实现分布式光伏发电,装机容量1MW,每年平均发电量80万度电。本项目不仅削减能耗双控指标的压力,减少二氧化碳排放,也提高了可再生能源比例。
节能措施:申江数字化工厂智能照明控制系统是在实现智能时控光控的基础上集合无线网络通信等多方面技术组成的一套智能控制管理系统。工厂对传动轴车间的照明系统进行了智慧照明改造,根据车间照明灯布局,按照两种区域做划分,生产区域:通过照度传感器控制开关,根据环境光照照度值,自动控制灯的开启或关闭。在白天自然光充足下,通过照度感应器自动调节灯具的开闭状态,从而达到良好的节能效果、有效延长灯具的寿命等效果,累计投资10万元,年度节约7.08万度电,相当于年度节省19.81吨标煤。
能源管理系统(图10):申江数字化工厂2022年落地部署全工厂的智慧能源系统EMS,累计310块数字表具,水表17块,电表8块,工厂总的能耗可下降约2-3%,年节约约50万元,合理调配峰平谷用电量,可降低用电成本;减少相关工作人员的工作量30%。
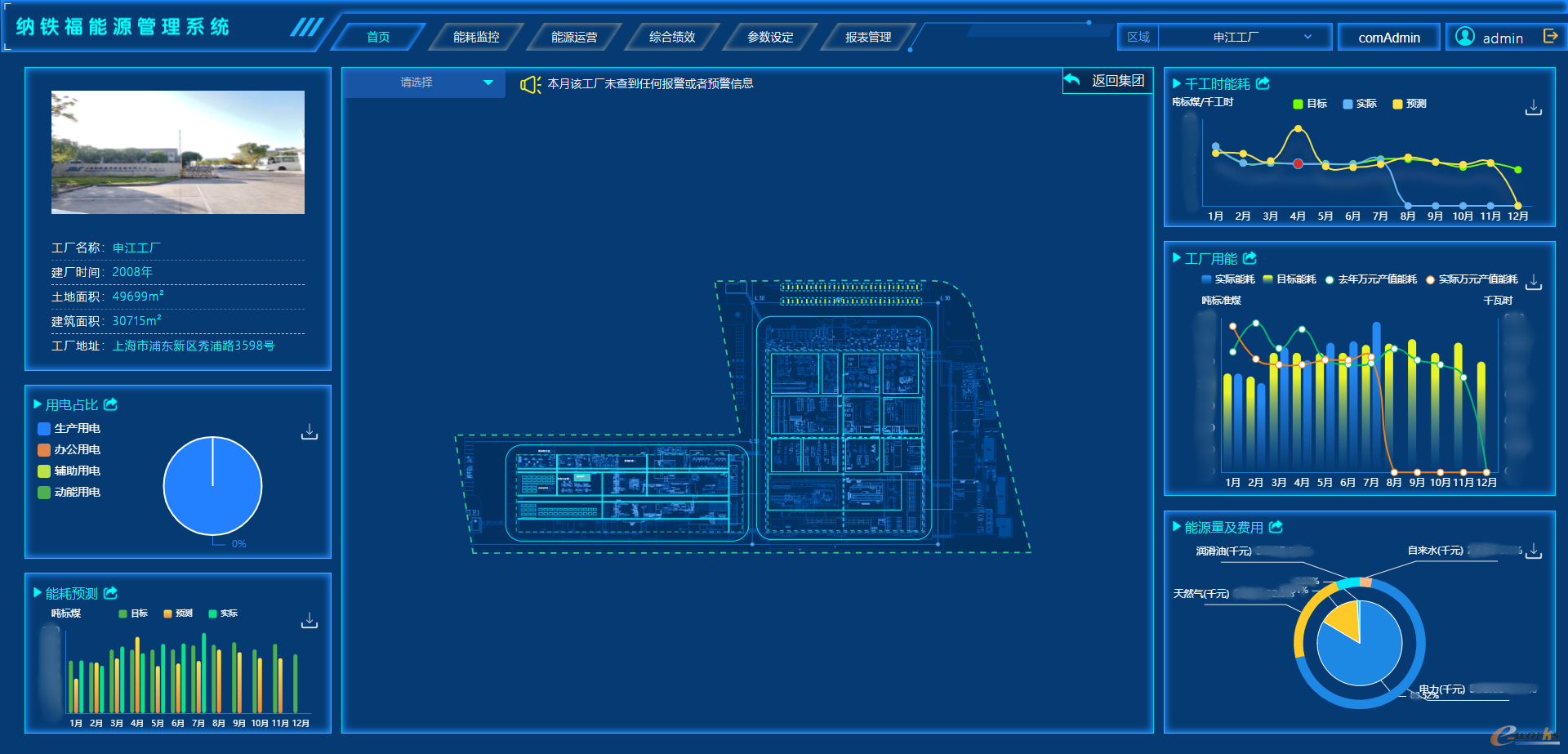
图 10上海纳铁福传动系统有限公司申江工厂能源管理主界面
产线余热回收:主要内容包括热水炉加热及空压站富余的余热利用两个部分,为了简化系统提高设备运行可靠性,空压站余热利用主要作为自来水及纯水箱的预热加热,热水炉主要保证1号喷漆线运行过程中的水箱温度稳定在工艺要求范围内。由于增加了预热水箱这一工艺环节,将明显缩短早上水箱加热投运的时间从而提高生产效率,也将减少因生产过程中补水引起的温度波动从而提高清洗效果。2023年喷漆线年产量186万根,燃气使用量为353745.2m³,其中燃气锅炉利用率21.6%,为76256.5m³,按测算热效率从36.55%上升到80%,一年可以节省41416m³,每年可节约21.45万元。