本文为“2023年度中国智能制造最佳应用实践奖”参评案例。本次活动将评选出2023年度,为中国智能制造领域带来突出效益的最佳实践工程,全面介绍企业推进智能制造的步骤、重点与难点、获得效益等,分享建设过程中的经验,供广大制造业行业企业学习供鉴。
一、企业简介
苏州璨鸿光电有限公司成立于2002年,是全球第一家液晶背光制造商——中强光电集团的全资子公司,是中强光电在中国液晶显示器五大生产基地的总部中心,产能达到1.1KK/月,是目前苏州市乃至全省光电显示行业产能规模前三大(行业平均产能1KK/月左右)工厂之一,并将世界最先进OLED/LCD智能产线设在江苏。璨鸿光电主要产品为液晶屏、背光、TP贴合、防窥屏、OLED、Mini LED等液晶屏及关键零组件的研发、加工生产和销售,终端产品应用于计算机、电视、手机、医疗、拼接显示器等,年销量3200万台,拼接屏/OLED NB全球市占率>20%。并为品牌厂商(Brand Name)/系统整合厂(SI)及面板客户提供最佳研发设计、生产及全球售后之相关服务,现已和世界许多知名厂商建立业务合作关系。主要合作伙伴包括三星、友达、京东方、华星、夏普、群创、惠科、视睿等,主要合作品牌戴尔、惠普、华硕、联想、宏基、微软、希沃等。
中强光电集团的液晶背光模组市场占有率全球30%以上,借助集团的全球营销据点,璨鸿光电不断开拓市场和产业转型升级,逐渐在新型车用显示解决方案领域占得重要一席。
图1 苏州璨鸿光电有限公司
二、企业在智能制造方面的现状
璨鸿光电已经积极投身于智能制造领域多年,并取得了一定进展。建立了一套完整的智能制造系统,能够自动化地进行生产,大幅提高生产效率,降低成本,并提高产品质量。此外,璨鸿光电还积极探索新的技术,如IOT物联网、大数据、AI人工智能等,以进一步优化智能制造系统,提高其智能化程度和生产效率。不断在智能制造方面积极挖掘,并致力于不断优化和提升其智能制造系统。
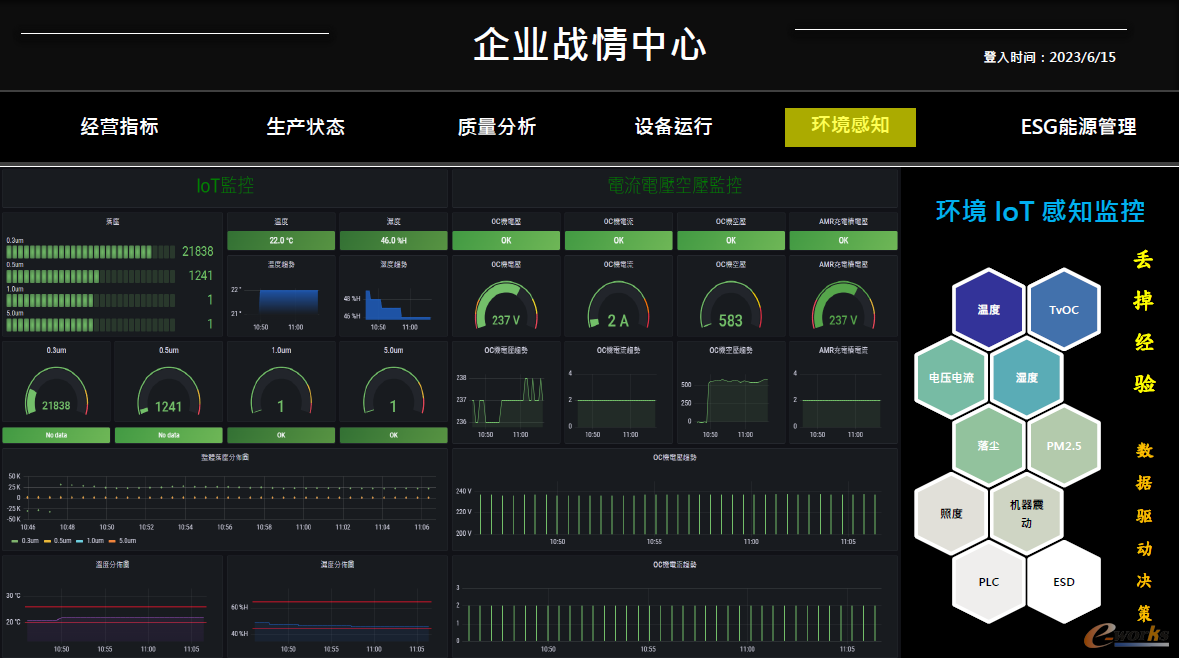
图2 IOT感知系统
三、参评智能制造项目详细情况介绍
璨鸿光电自主开发并搭建各类生产、管理用软件、系统及辅助网络设备,并实现系统的集成互联,核心系统主要有 ERP系统、MES系统、e-Planning智能排程系统、PLM系统、SPC系统、iWMEC系统(WMS智能仓储系统)等。自主开发Power BI大数据互联分析系统,并实现云端应用,移动版APP;基于该系统建模(40套)分析,实现产品设计、品质、设备、生产、环境等各环节的交互分析提升管理决策。
图3 全系统整合解決方案
1.项目背景介绍
液晶模组制造行业,用工大、人工成本高、人员流动性大、人工劳动强度大、落尘管控敏感肉眼不可见、多品种、品质不稳定、不良率高等诸多瓶颈问题。传统的单纯经验式管理已不再适应现有的发展。基于此,璨鸿光电基于智能装备应用及联网、系统集成、数据互通及挖掘分析,打造模组智能制造车间。
该智能车间示范及创新做法已辐射推广至集团子公司15家,巩固了中强光电在光电行业内的领先地位;也辅导了苏州及江苏本地装备商的新技术建立,并在光电显示行内技术平展导入7家(面板/背光等行业,涉及业务机密),将继续辐射扩大到更多同行业;产业链上游及供应链企业7家已导入我司基于行业痛点自主研发的Power BI大数据及AI技术,这更有利于带动江苏省乃至全国光电显示产业链的智能制造转型升级。
图4 NB全自动线
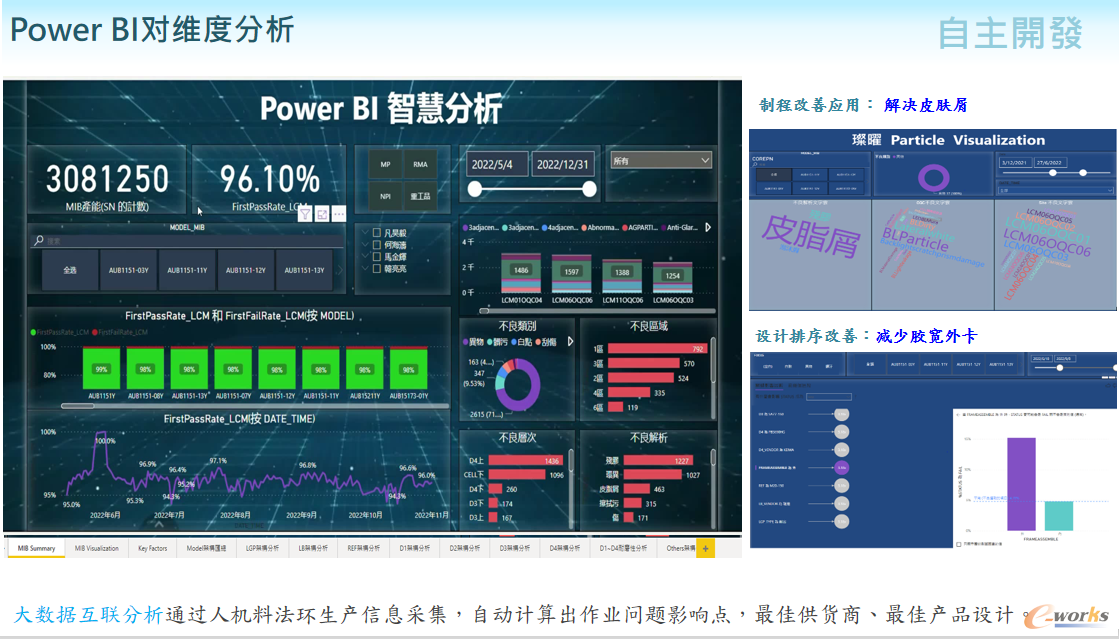
图5 Power BI 智慧分析
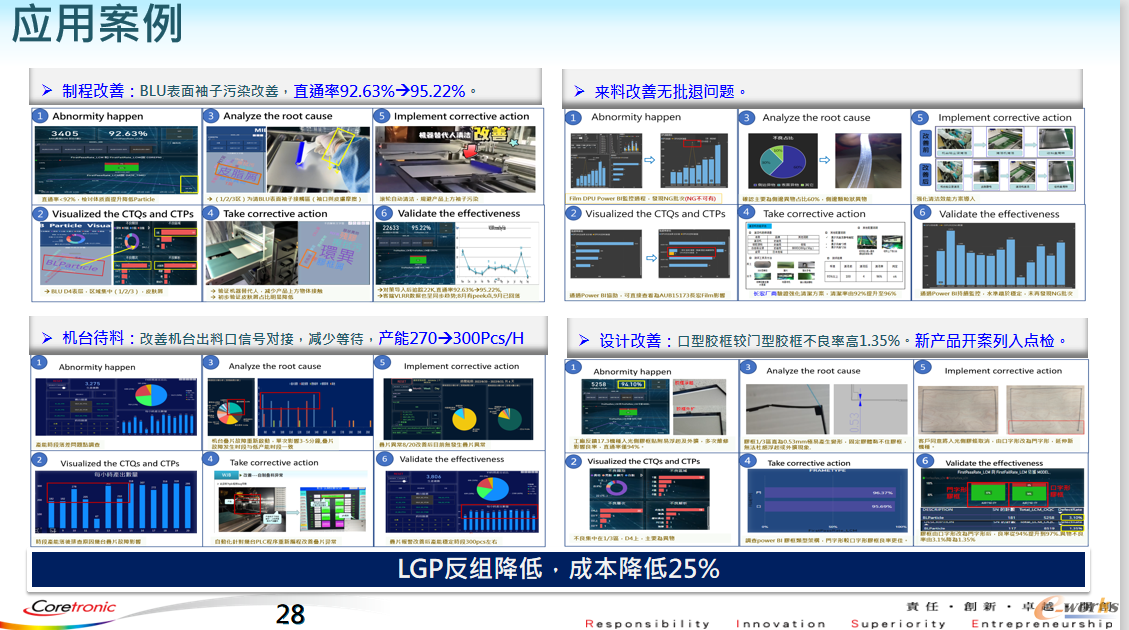
图6 应用实践
2. 项目实施与应用情况详细介绍
璨鸿光电通过智能化设备与系统、系统与系统之间的互联互通,以及二维码、条形码等信息标识技术配以自动扫码机、3D扫描系统、手持PDA、手持式一体机(程序联网)等识别设备,实现对生产过程实时调度、物料自动配送和智能仓储、产品信息可追溯。
建立了完善的可视化平台,包括SFCS系统实时数据显示、BI大数据互联分析平台中“可视化警示牌”、产线看板以及车间中控中心、公司战情中心等,对生产全过程实现了可视化、透明化管控。本智能车间内外均实现了信息化软件应用全覆盖,其中:车间内的设备控制系统与SFCS系统(生产制造系统)互联,VNC软件远程操控设备;车间环境采集设备(洁净度、温湿度、烟感、能源等)与厂务自控系统互联;SFCS系统与设计软件(AutoCAD、PRO/E)、e-Planning智能排程系统、ERP系统、SPC系统、Power BI大数据分析平台互联,实现车间内外系统联通。
图7 SFCS系统实时监控设备状态
车间业务及数据以混合云形式实现了上云,其中车间设备及各系统数据存储至私有云端,BI、AI/ML存储至公有云端。
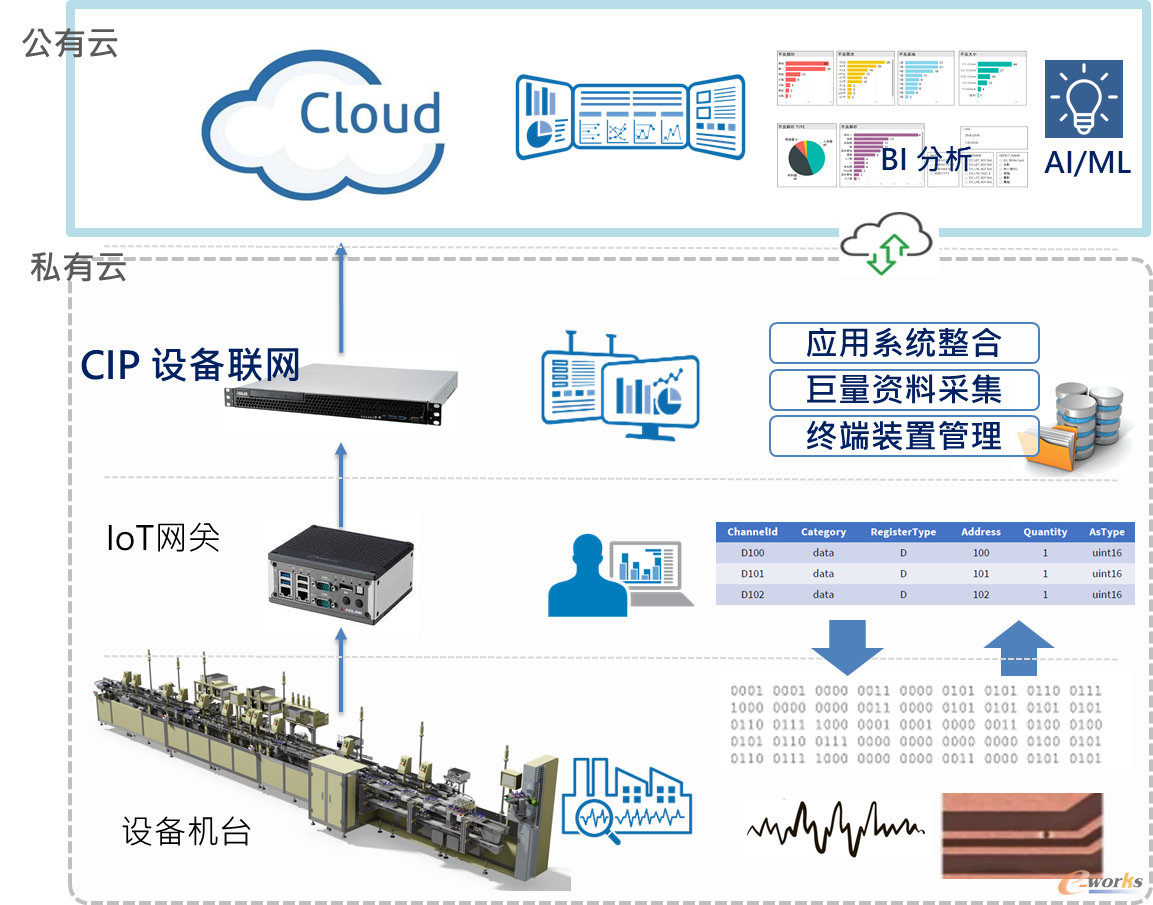
图8 智能制造框架
自主开发了e-Planning智能排程系统,包括OPS(业务订单管理)、MPS(主生产排程)、VDS(物料准备管理)3大功能模块,通过与ERP系统对接实现了作业计划自动生产及自动排产。ERP系统接收到客户讯息,e-Planning智能排程系统从ERP系统提取业务订单信息,生成物料需求计划,并进行物料调料、产线排产作业。
图9 e-Planning智能排程系统主界面
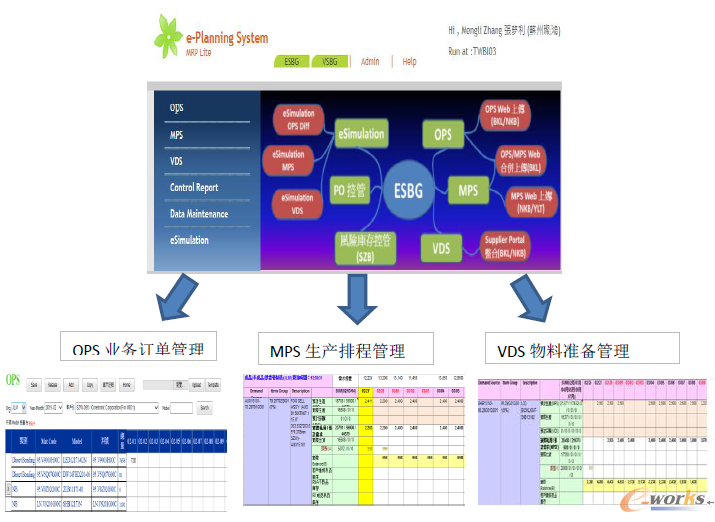
图10 e-Planning智能排程系统排产逻辑示意图
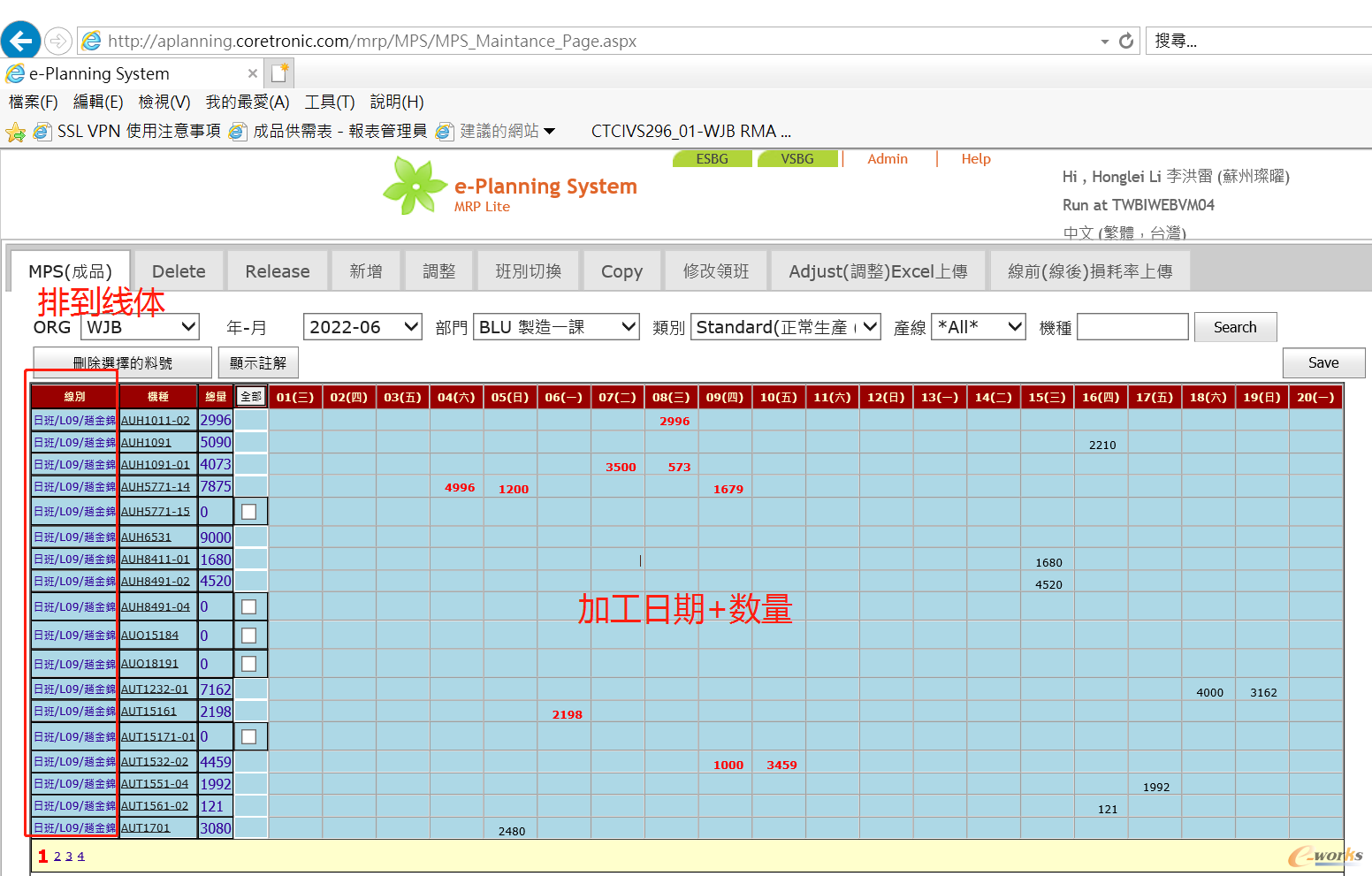
图11 e-Planning智能排程系统实例图1(排日期+数量)
SFCS系统自动获取e-Planning系统的排产计划,实时接收工单,并发至生产车间及生产线。e-Planning智能排程系统根据工单向仓库下达领料指令,iWMEC系统(智能仓储系统)实时获取物料需求单,并通过车辆管理系统(VMS)调度AMR移动机器人自动到相应的货架库位取料,自动配送至车间线边仓。物料调度人员通过扫描工单条码在线边仓领料,配送至车间产线及相应工位。
模组车间生产线及各工站所需物料采用机械手、传送带、传送机构等不同方式实现了全过程投放及传送的自动化。
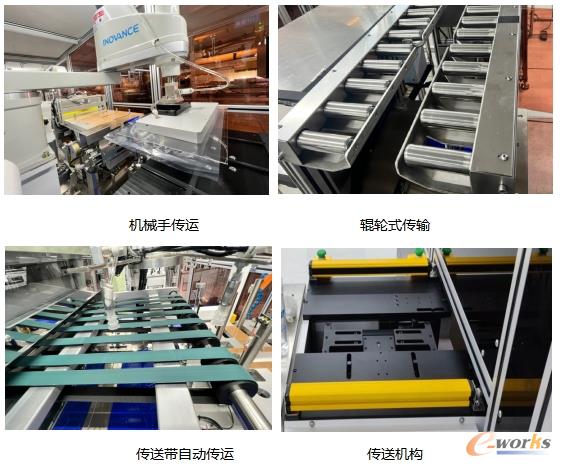
图12 模组车间生产线
在排定生产计划的同时,e-Planning系统会自动生成库存数据、所需物料数量等信息,并考虑在途库存、安全库存等采购条件以保持公司存货水平。如有缺料情况发生时,系统会显示红色字体报警信号,引导生管人员进行生产计划调整。
e-Planning排程系统还可依据市场需求及客户订单来建议生产进度;基于订单的优先级、交货期限等情况,紧急插单;对滞留时间较长的工单及其它异常情况实时提醒,便于生管人员给予精准的排产、插单等决策。
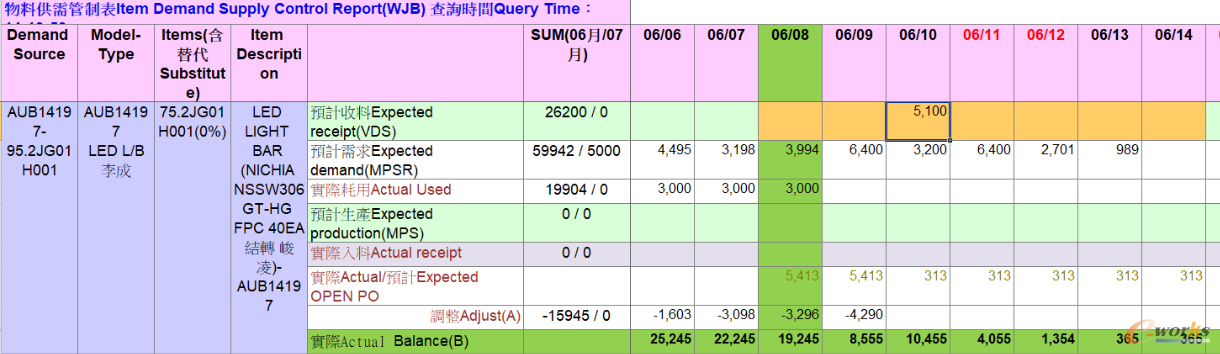
图13 应对物料情况异常的优化调整
公司建立了完善的可视化平台,包括SFCS系统实时数据显示、BI大数据互联分析平台中“可视化警示牌”、产线看板以及车间中控中心、公司战情中心等,对车间作业实现可视化。
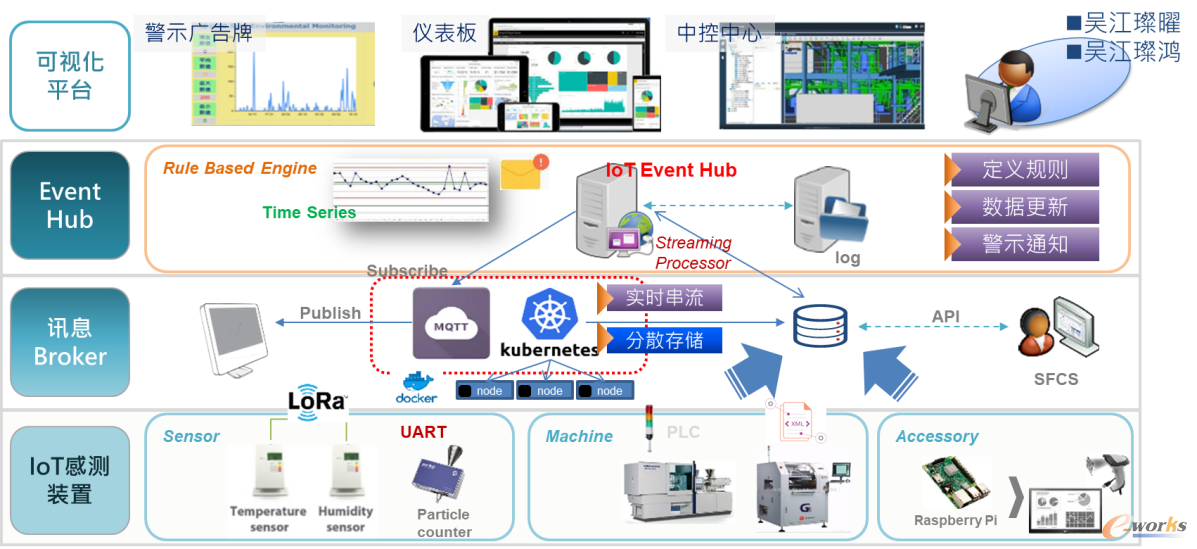
图14 车间任务指挥调度可视化
例如:除设备运行状态实时上抛至SFCS系统外,生产过程产品数据也实时上抛至SFCS系统,可按时间、线别、机种、工单号等10余种方式显示及查询。
图15 SFCS系统采集生产数据(按不同时间段抓取所有机台数据)
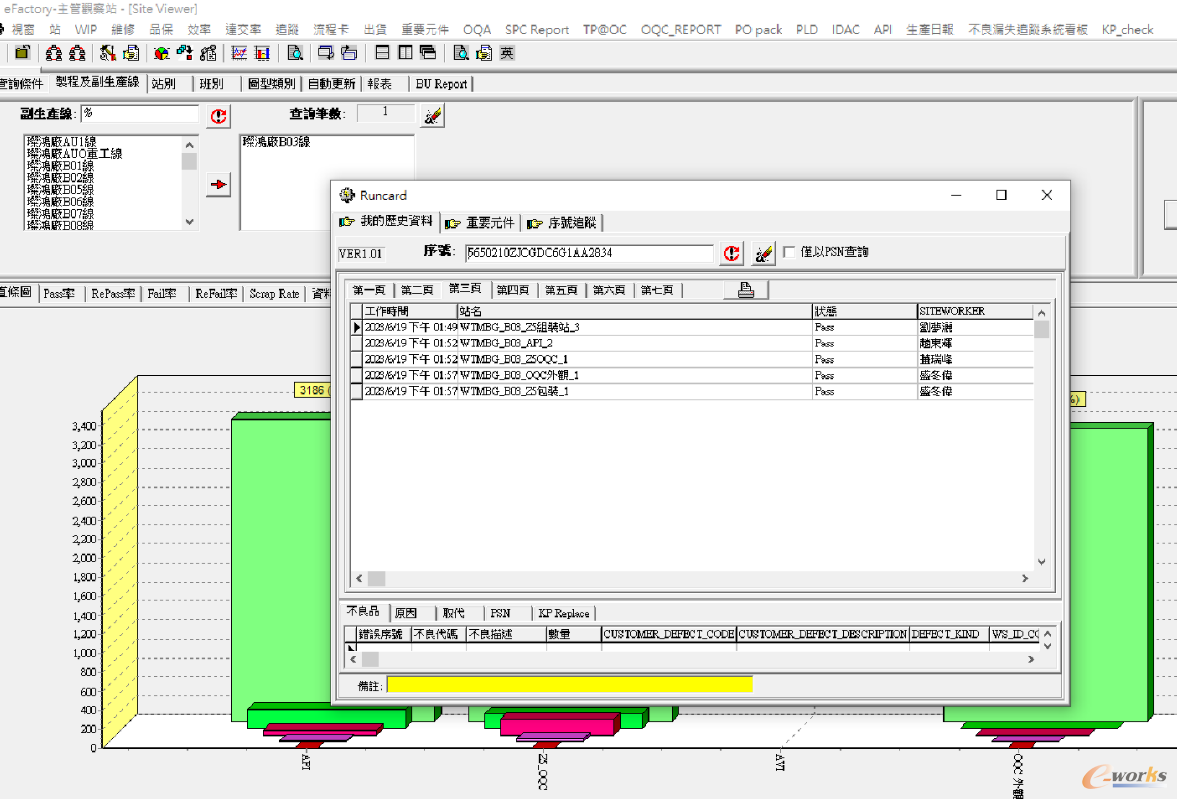
图16 SFCS系统采集生产数据(按过站记录查询)
Power BI大数据互联分析平台可自动抓取SFCS系统中上述采集信息,建立分析模型,分析结果以各种图形、报表更直观、详细的展示,包括:设备实时稼动率(OEE)、设备停机时长、设备运行状态占比、设备异常原因分析、产能数据及分析。
图17 设备稼动率(可分厂区、线别、机台等不同维度展示)
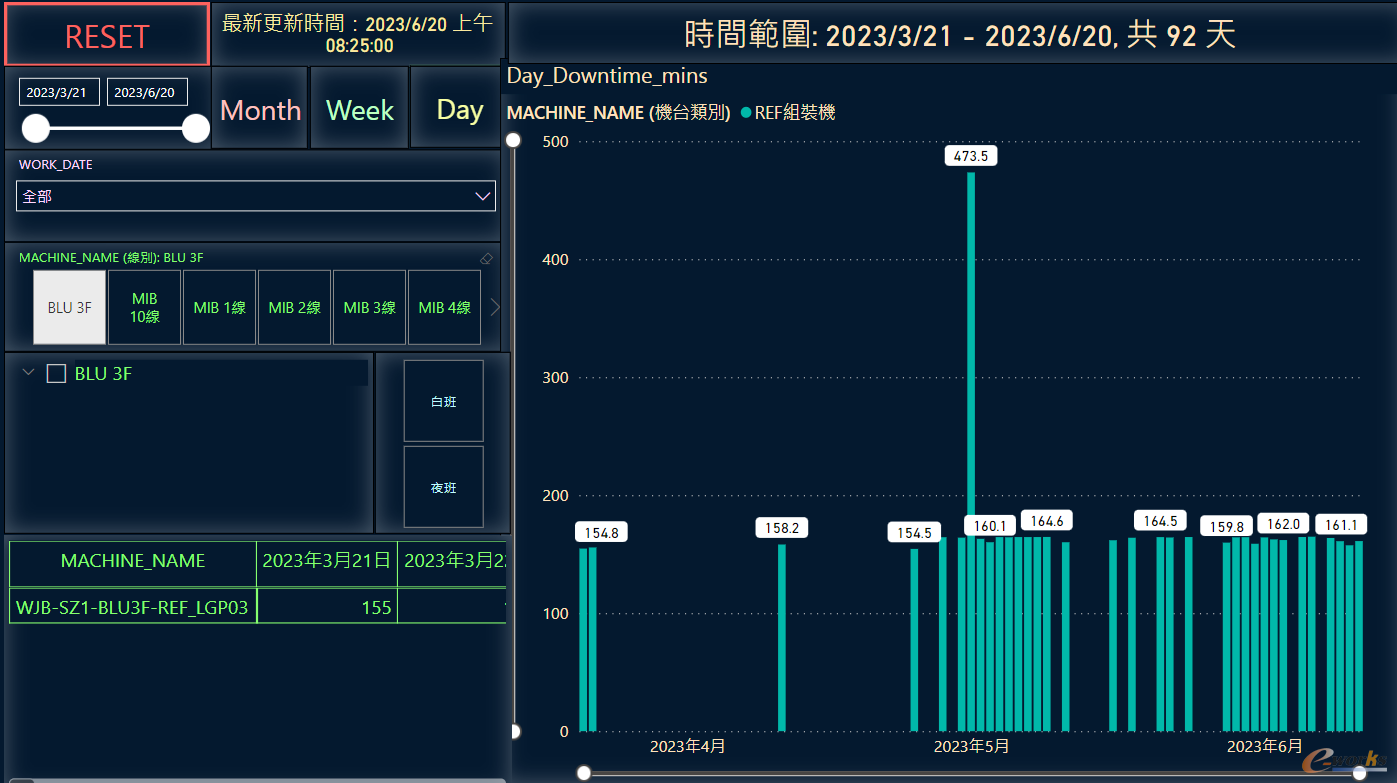
图18 设备停机时长(可厂区、线别、机台等多维度自动统计)
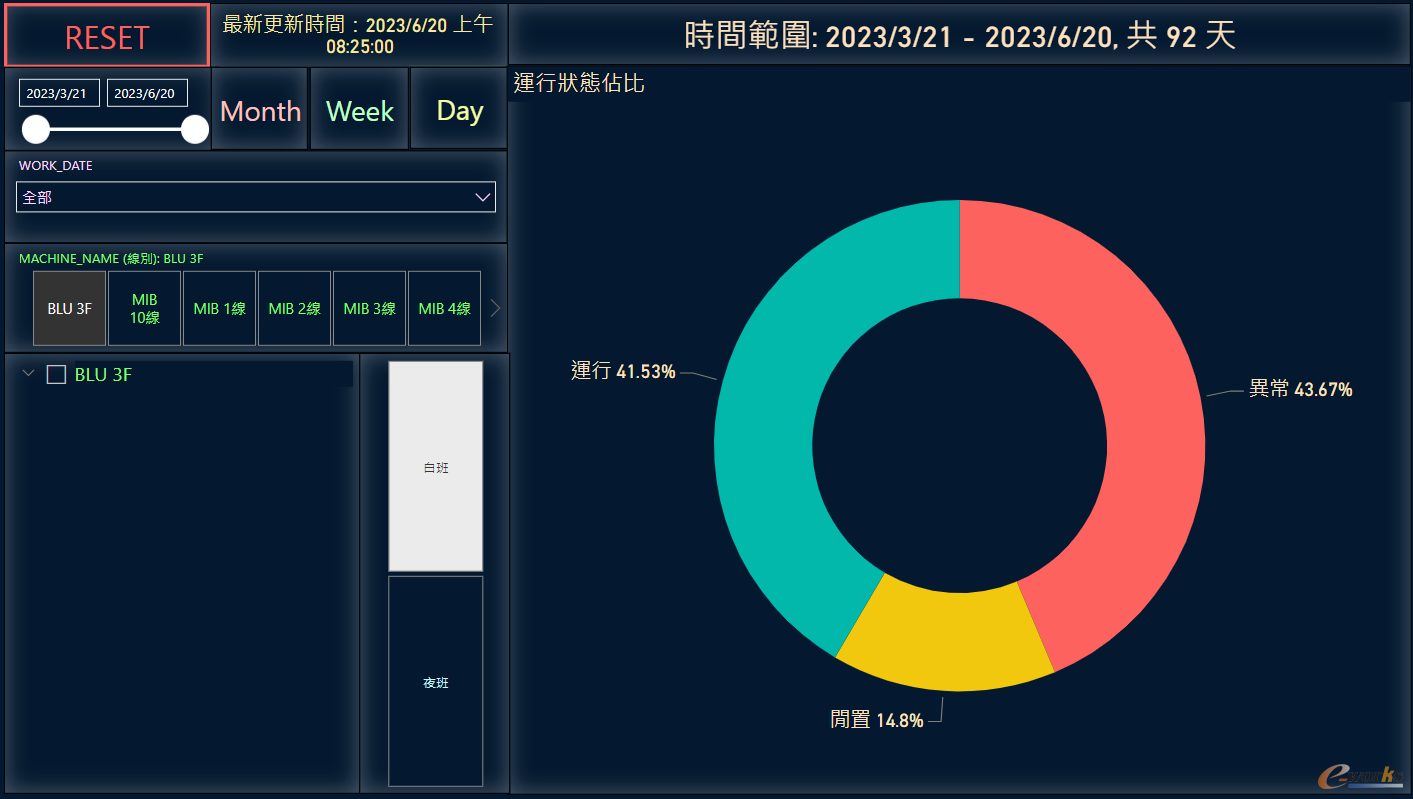
图19 设备运行状态占比
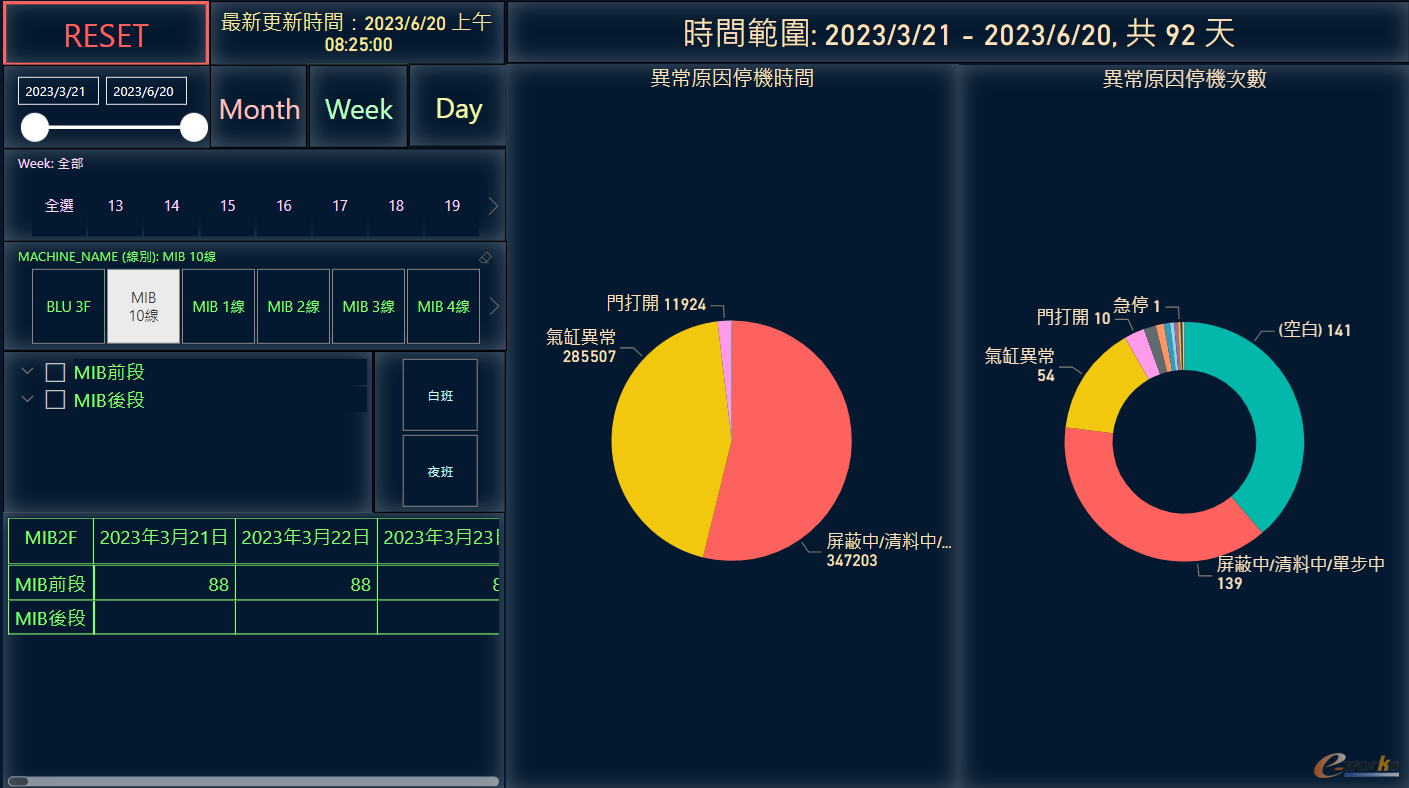
图20 设备异常原因分析
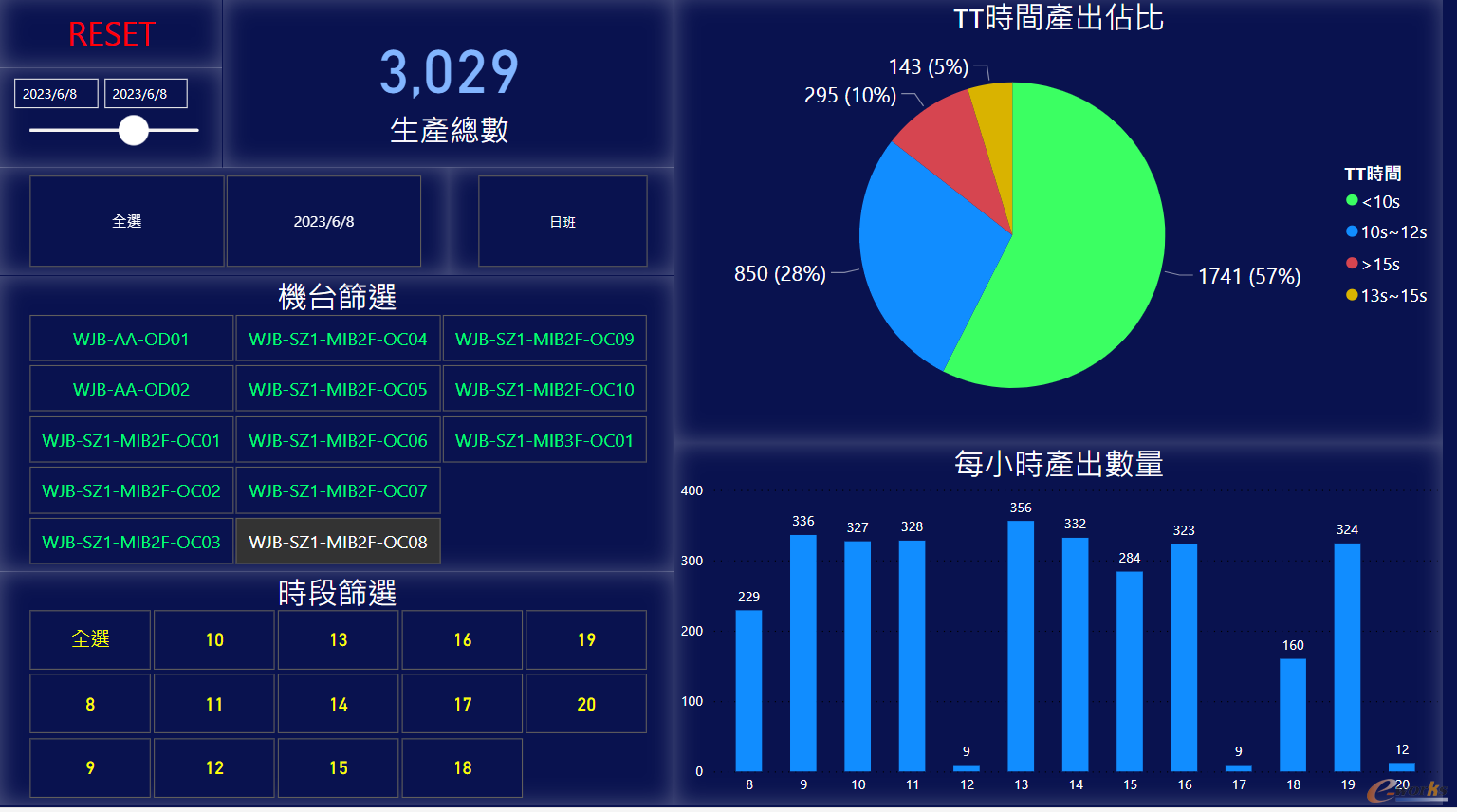
图21 产能(生产节拍、时段产能、总产能)
车间设有监控中心,在办公区设有公司战情中心(大数据智慧监控中心),针对生产各信息进行可视化展示,实时监控生产KPI,主要包括:生产效能监控、环境感知监控、品质互联监控、设备运行监控。
基于Power BI大数据互联分析平台,实现产品研发、品质、设备、生产等各环节的交互分析。该平台是第一家在液晶显示行业应用,拥有40多套模型,具有AOI不良损失追踪、产能/TT、API报表、AOI漏检误判、设备OEE、品质竞争力分析、LGP分析、解析报表、OI报表等功能,有效解决了传统行业面临的大数据流动分析缺少工具、用人多、品质不稳定等痛点。
3. 效益分析
1)节省人工及成本:以智能化设备替代人工操作,1条产线操作人员平均节省104人。在Power BI大数据互联分析平台可自动计算机台设备投资效益并展示,本车间自2022年1月运行至今,“机器换人”纯效益(节省的人工费剔除设备采购及折旧费、运行费等成本)最高为62.4万元。
2)提高效率:所有智能化设备均联网和数据采集,设备运行状态实时监控并采用Power BI大数据分析,设备综合利用率从85%提高到94%。
3)提升品质:智能化装备自带在线检测功能,并建立SPC系统、Power BI 大数据分析对不良品进行解析,为生产制程提供优化支持,不良品率从4%降低到2%以下,不良品率降低了50%。
4)更节能降耗:本车间的单耗量为0.0050tce/万元产值,相比其它车间的0.0057 tce/万元产值,能源利用率提升12.28%。按本车间设计的产值3亿元计,一年节能量为21万吨标煤。