随着技术的不断进步,智能系统将在汽车制造中发挥越来越重要的作用,提供更高效、更精准的质量控制手段。这些技术进步不仅提高生产效率和产品质量,还显著降低生产成本,增强企业的市场竞争力。通过持续的技术创新和应用优化,推动汽车制造业迈向新的高度。
一个风和日丽的早晨,打工人的你带着多年积蓄早早来到4S店提关注已久的Dream Car。激动的心,颤抖的手,终于来到交付口,拉开车门那一刻,诗和远方在向你招手。突然!几条细小的白线闯入眼中,不仔细看都没发现,竟然是一道道划痕!原来由于厂家检验人员的失误导致缺陷车流到4S店,给消费者和厂家带来严重损失!
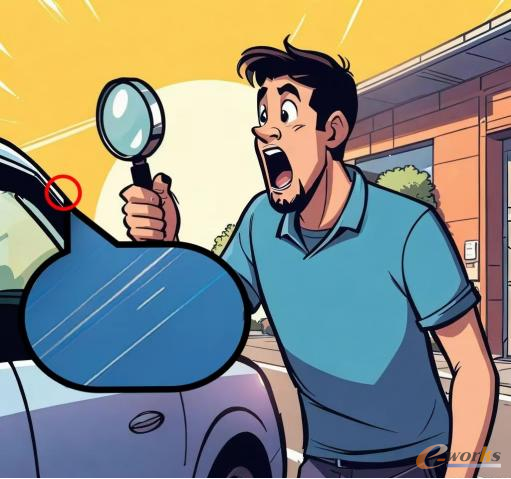
图1 检查发现车辆表面瑕疵漫画示意(图片来源:图片由腾讯混元AI生成)
当下汽车产品迭代速度加快,对于质量管控也提出更高要求。外观检验作为新车下线前最后一道检验工序,直接影响新车质量和交付速度。传统人工检验存在效率低、易出错、主观性强的缺点,而人工智能相关技术将为汽车主机厂外观检验提供更多可能。
“通则不痛,痛则不通”:汽车主机厂外观检验三大痛点
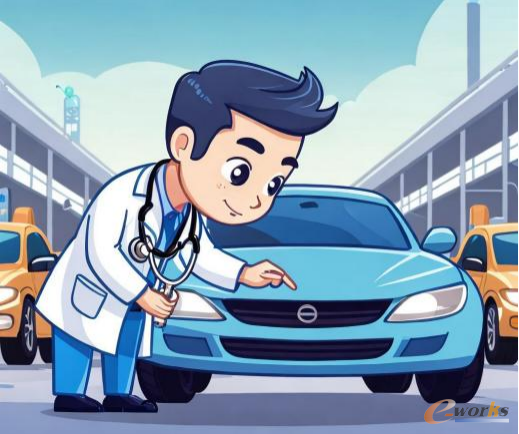
图2 为汽车做外观检测漫画示意(图片来源:图片由腾讯混元AI生成)
如果把汽车主机厂质检线比作医院、检验人员比作医生,那么外观检验涵盖三大科室:“汽车皮肤科”、“汽车整容外科”、“汽车骨科”,分别对应三大检验环节:表面质量检验、配置选装检验、零件匹配检验。
“汽车皮肤科”——表面质量检验:表面质量检验是确保交付车辆外表面无瑕疵,保证整车外观品质。就像医院的皮肤科,检查汽车的皮肤状态是否光滑细腻无皱纹。检验位置包括车身外钣金(前盖、车顶、四门外板、前后翼子板等)、内外饰件(前后保、大灯、外后视镜、内外饰板等),常见缺陷如图1所示,包括表面凹坑、划痕、破损、漆损等。
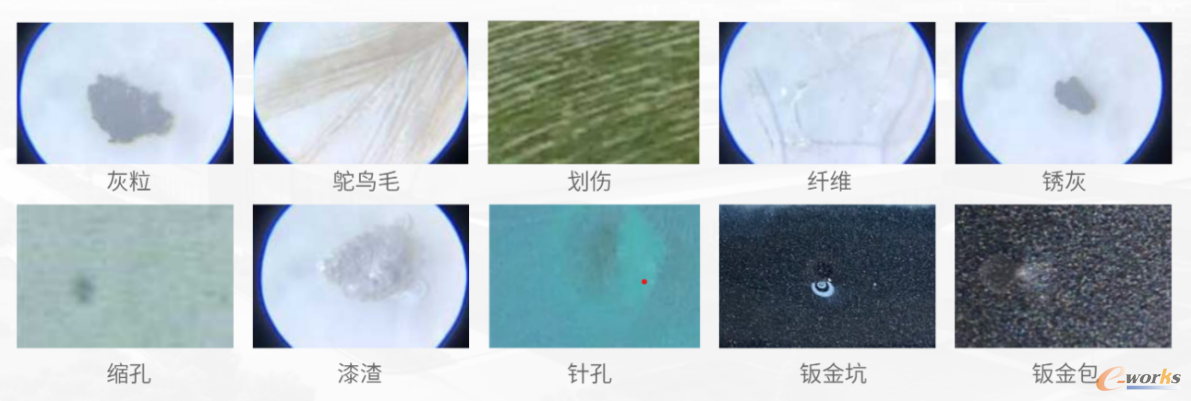
图3 表面质量常见缺陷类型(图片来源:菲特FITOW官网)
“汽车整容外科”——配置选装检验:配置选装检验是确保客户选择的所有选装件都正确装配到车上,无漏装错装。就像医院的整容外科,对车辆的“五官”进行升级后,再次确认是客户想要的“浓眉大眼”,不是“柳眉细眼”。检验位置如图2所示,包括但不限于轮胎轮毂、后视镜、天幕、大灯、保险杠、座椅、仪表板等。通过检查零件颜色、样式、零件号等方式来核对订单配置与装车零件的一致性,确保所有配置项准确无误装车。
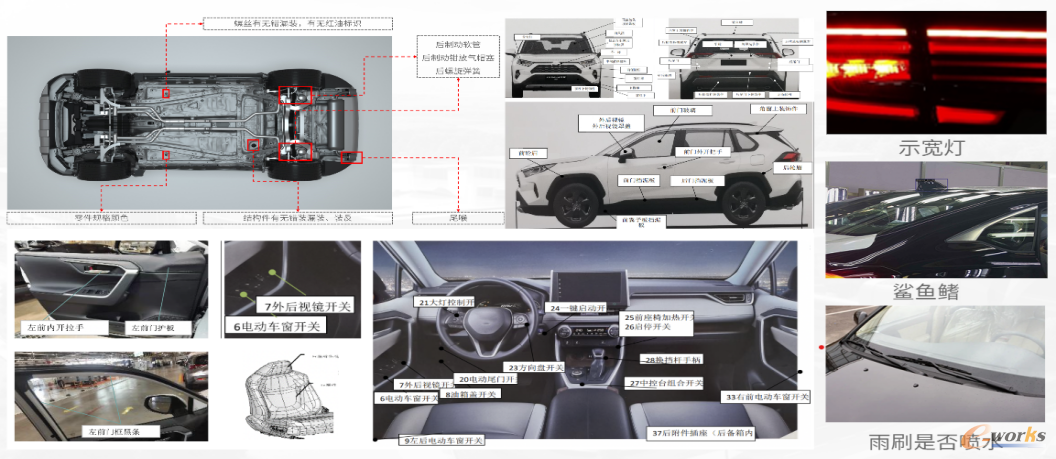
图4 配置选装检验内容(图片来源:菲特FITOW官网)
“汽车骨科”——零件匹配检验:零件匹配检验是确保车辆各零件装配符合尺寸标准,无间隙面差超差情况,保证整车外观的协调。就像医院的骨科,检查车辆内外骨骼是否衔接完好、有无错位。检验内容如图3所示包括卷边间隙、锐边间隙、平行间隙、斜边间隙等。检验位置包括但不限于前保险杠与大灯、后保险杠与尾灯、前盖与翼子板等。通过零件匹配检验确保各零件的安装精度,保证整车外观质量。
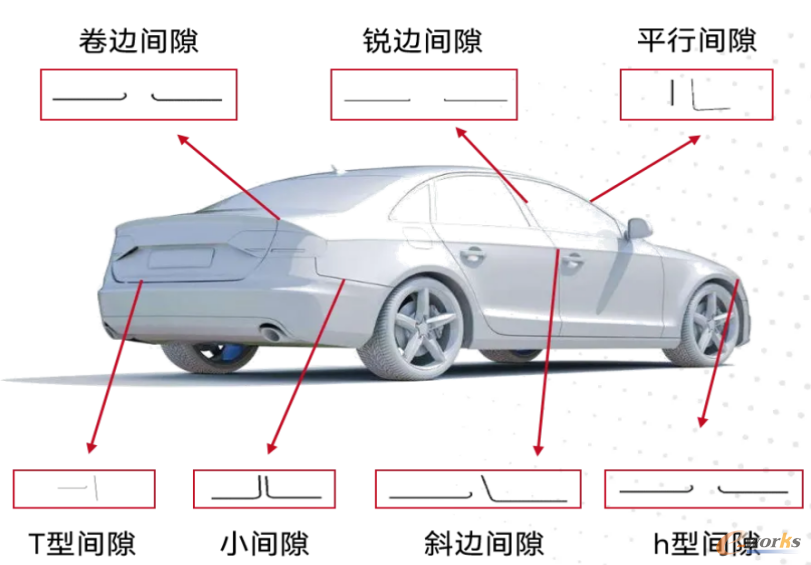
图5 零件匹配检验内容(图片来源:易思维ISV微信公众号)
表面质量检验痛点——细微缺陷人眼难识别:表面质量类问题在整车质量问题中占5成以上,而且是质量溢出风险最高的检验环节。目前主要靠人眼目视,虽然有灯光辅助,但是细微的划伤凹陷往往不明显,容易被忽略导致缺陷溢出。另外员工长时间进行重复性工作,注意力容易分散,即使培训监督到位,注意力也无法长时间高度集中,使得依赖人工的表面质量检验存在较高漏检率,影响整车质量。
配置选装检验痛点——配置过多人脑难记忆:目前配置选装检验主要依靠人工核对,只一款车就有近百种配置,对于多车型共线的工厂,涉及的配置就更多。车辆配置的多样性和复杂性给人工检验带来巨大挑战,员工需要记住大量特征信息,任何记忆疏忽都会导致漏检错检。此外,配置信息的传递主要依靠检验作业指导书,当下产品迭代速度非常快,产品变更也非常多,文件更新本身存在延时,导致变更信息无法实时同步在线检验人员,进而导致错检漏检。
零件匹配检验痛点——检验精度和效率难兼得:零件匹配检验方式主要有人工目视、手摸、塞尺测量。目视和手摸测量精度较低,塞尺测量精度相对较高。目前大部分汽车主机厂的操作循环时间在50到70秒之间,如需准确测量出具体数值,塞尺单点检验时长至少在10秒以上,那么单人单操作循环的精确测量点只有5个左右,相比整车近百个点位显然是不能接受的。因此为了满足效率只能选择目视或手摸的方式,缺点则是大大增加了误差,也增加了缺陷溢出的风险。
“听诊把脉,对症下药”:汽车主机厂外观检验三副良药
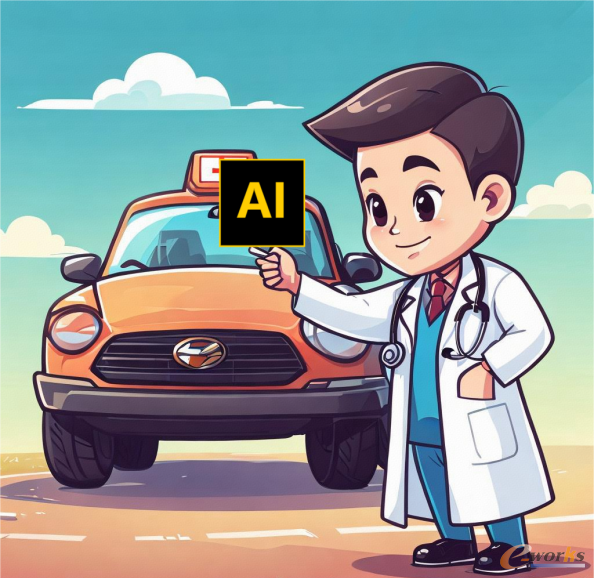
图6 为汽车外观缺陷进行治疗漫画示意(图片来源:图片由腾讯混元AI生成)
药方之表面质量自动检验系统——机器视觉高精度识别细微缺陷
表面质量自动检验系统基于机器视觉技术和深度学习算法,通过高分辨率工业相机和AI计算成像技术对车身进行拍照扫描、图像处理、特征提取,实现表面细微缺陷高精度识别。表面质量自动检验系统主要由3D偏折面阵相机、高精度传感器、光源、机械臂及滑轨、车身定位系统、图像采集卡、传输线缆、图像处理软件、结果显示器、安全光栅等部分组成。
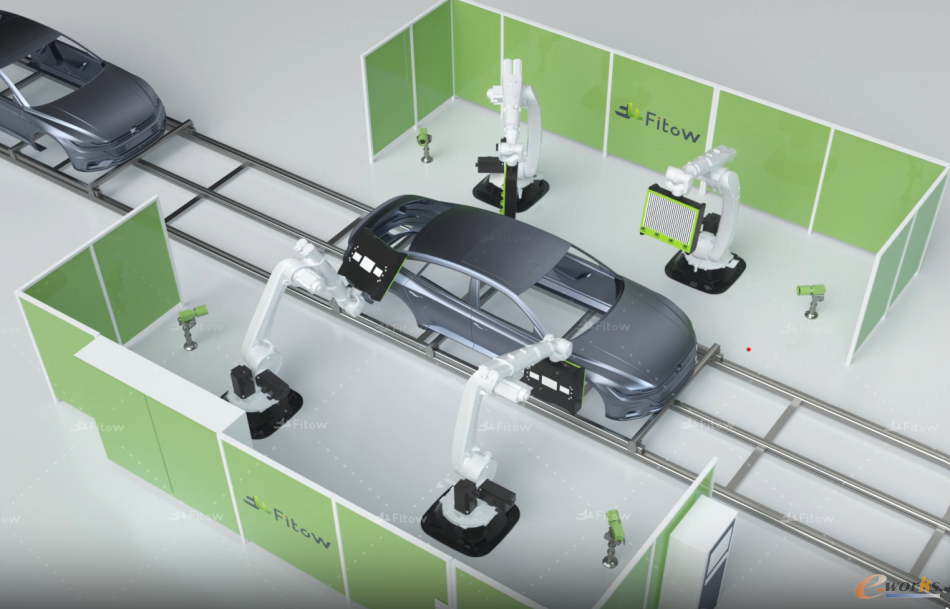
图7 表面质量自动检验系统(图片来源:菲特FITOW官网)
检验过程包括图像采集、图像处理、数据汇总、结果反馈。当车辆进入检验工位时,车身定位系统对车身进行高精度定位,结合人机交互软件,控制机械臂移动到指定位置,然后3D偏折面阵相机对车门、前盖、翼子板、侧围等区域拍照,拍摄图像经图像采集卡、传输线缆上传至图像处理软件,利用二值化算法进行图像处理,将处理后的图像叠加拟合,生成与车型相符的模板,系统根据模板进行分析识别,识别出的缺陷类型、位置、图片等信息显示在结果显示器上,方便相关人员对车辆进行跟踪。如图5所示,表面质量检验平台能够自动记录数据,通过线边显示屏实时显示车型信息、缺陷种类、缺陷等级、划分区域、检出图像等,缺陷数据统计还能为质量管控、工艺改进提供决策依据,从而提升智能化管理水平。
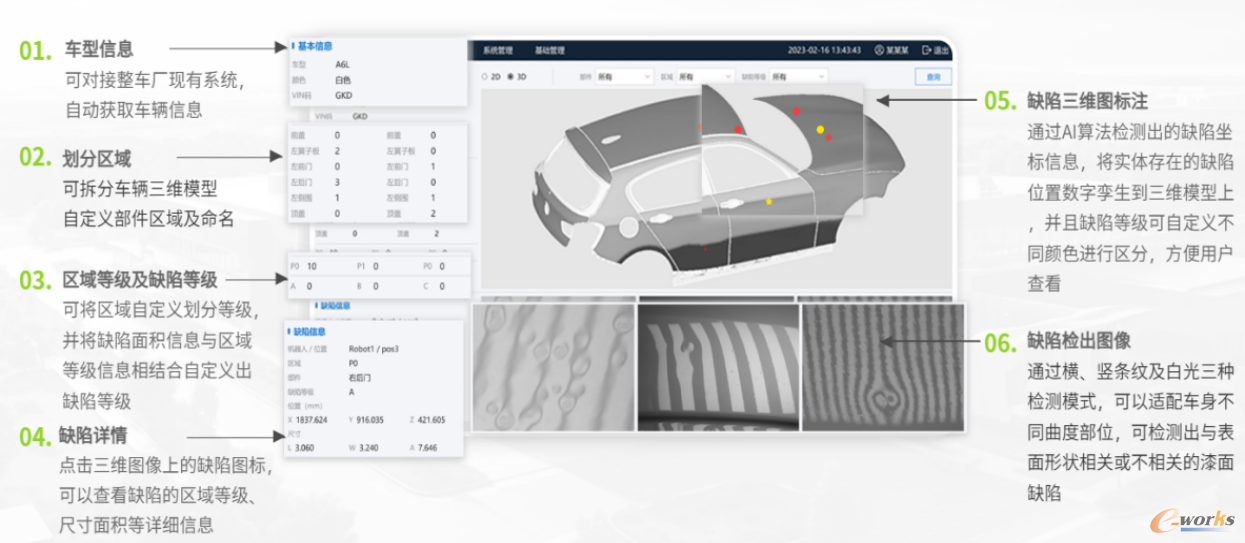
图8 表面质量检验(图片来源:菲特FITOW官网)
系统可实现检验精度≦0.15mm,检出率≧98%,误检率≦2%,单车检验时长≤50秒,分类准确率≧85%,全天候24小时不间断检验,相比人工检验大大提高了准确率和效率。此外,系统能够兼容80%的车型和颜色,提供跟随式、走停式两种检验方式,不仅占地面积小,而且满足不同节拍的产线需求,实现柔性化检验。
药方之配置选装自动检验系统——机器视觉自动匹配海量选装
配置选装自动检验系统基于机器视觉技术和多种深度学习算法,包括目标与关键点检测、场景文字及OCR识别、颜色区域分割和特征匹配等。采用协作机器人进行拍照,通过多台工业相机高效协同作业,实现车辆外观全方位、多角度在线采集和防错检测。配置选装自动检验系统主要由工业相机、光源、传感器、机械臂及滑轨、图像采集卡、传输线缆、图像处理软件、结果显示器、安全光栅、RFID系统等部分组成。
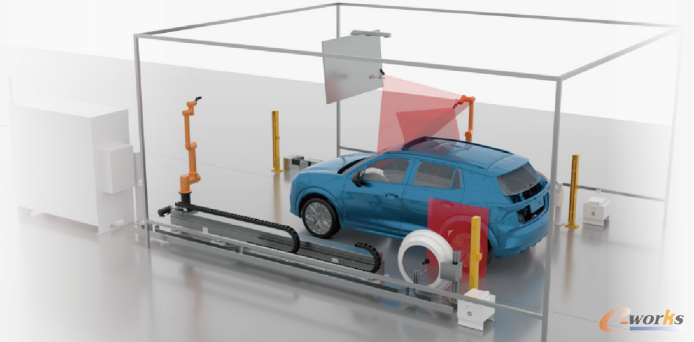
图9 配置选装自动检验系统(图片来源:视比特官网)
检验过程包括图像采集、图像处理、数据统计、结果显示。当车辆进入检验工位时,RFID系统自动读取车辆全部配置信息,同时机械臂及滑轨根据程序设定移动到指定位置,工业相机对车辆外饰、内饰、前舱、底盘区域进行多角度拍照,覆盖整车所有关键检验项,包括但不限于:保险杠、轮胎、车灯、玻璃、后视镜等。拍摄的图像经图像采集卡和传输线缆上传到图像处理软件,利用目标/关键点检测、场景文字/OCR识别、颜色区域分割、特征匹配等深度学习算法进行图像处理,将处理后的图像与标准配置图像对比分析,识别装车零件是否正确。结果实时上传检验平台,通过线边显示屏可以实时显示车辆列表、配置信息、工件实图、检验细节、测点状态等信息,方便相关人员对车辆进行跟踪,同时收集数据进行SPC统计分析,为质量改进、工艺优化提供数据参考。
系统可实现所有车型全部配置自动检验,准确识别外观件、内饰件、底盘件,准确率≧99.95%,消除人工记忆偏差导致的错漏检风险。通过连通超级BOM,实现产品变更信息实时传递,实现从产品研发到质量检验的信息同步。系统还提供龙门架式、固定式、模组+机器人式等多种产品方案,根据不同型号和款式的车辆进行适配,满足产线柔性化需求。还可以实时收集、记录和分析大量数据,用于产线优化、质量改进、问题排查,数据实时上传便于追溯,更好地管控生产过程。
药方之零件匹配自动检验系统——激光高精高效测量间隙面差
零件匹配自动检验系统综合运用激光测量、3D视觉、机器人柔性控制、3D重建、点云匹配等技术,通过对车辆表面拍照扫描获得完整轮廓,利用多种评价算法计算点位间隙面差值。零件匹配自动检验系统通常包含四个部分:间隙面差子系统、车身定位子系统、大屏显示子系统、工位自动化设备。间隙面差子系统用于获取车身3D空间坐标并结合软件计算准确的间隙面差值;车身定位子系统用于获取车身位姿偏差并发送给机器人,引导其移动至准确位置进行测量;大屏显示子系统用于实时显示测点数据及趋势。后台软件支持多屏功能,能展示各点位测量结果,为在线操作人员提供参考;工位自动化设备包括测量机器人、光电触发装置、VIN扫码设备等。
检验过程包括:车辆VIN扫描、车身位姿偏差获取、间隙面差测量、数据结果显示。当车辆进入检验工位时,触发光电开关,扫码设备扫描车辆VIN并同步到测量软件。定位传感器对车身位置定位,并把位置偏差同步给机器人。机器人根据程序设定移动到指定位置,激光发生器发射线激光到待测物体表面,激光扫描仪根据设定角度测量激光在物体表面的反射,利用三角测量法获取表面几何形状,经算法处理得到测量点位的间隙值或面差值。将测量值与标准对比判断该点位尺寸是否超差。如图9所示,将车辆信息、测量点位、尺寸标准、测量结果、测点趋势、数据统计等信息实时显示在线边显示屏上,方便检验人员跟踪,还能指导在线装配人员进行调整。
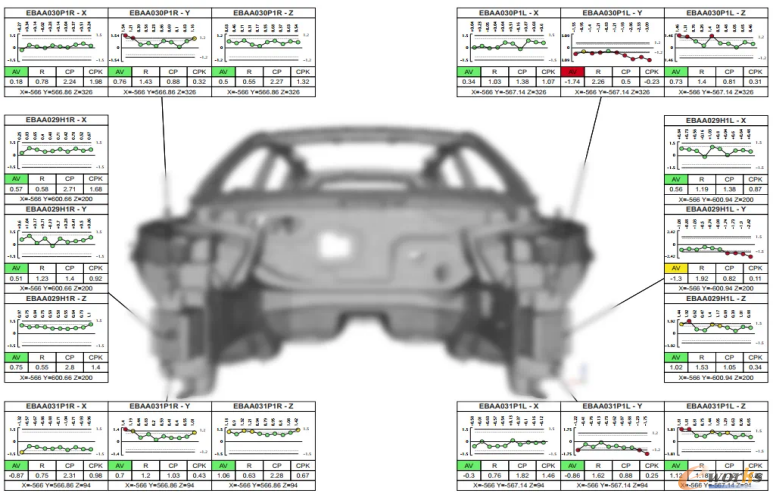
图10 零件匹配检验结果显示平台(图片来源:易思维微信公众号)
系统可以实现在线快速测量,相比人工单点10秒的测量时长,系统单点测量时长不超过3秒,精度达到0.05mm,满足高效率的同时实现高精度检验。系统可实现24小时不间断检验,支持多车型混检。还可以自动调取尺寸标准,通过软件分析平台,提供CP/PP、CII、合格率等统计报表、趋势图、相关性趋势图、直方图等数据分析图表、Excel和PDF等格式报表,方便质量人员分析问题,提高问题解析效率,将检验工作自动化的同时,实现数据在线化,打造数据生产、采集、分析、优化的闭环。
总体而言,未来的汽车主机厂外观检验将更多地朝着自动化、数字化、智能化的方向发展。随着技术的不断进步,智能系统将在汽车制造中发挥越来越重要的作用,提供更高效、更精准的质量控制手段。这些技术进步不仅提高生产效率和产品质量,还显著降低生产成本,增强企业的市场竞争力。通过持续的技术创新和应用优化,推动汽车制造业迈向新的高度。
参考文献
[1]Speedbot视比特-3D视觉产品-自动化产线-视觉缺陷检验-PaintPro漆面缺陷检验及磨抛修复系统https://speedbot.com/cn/production/details?id=2fd0260e-1c06-4383-9d97-f1cc8520299f
[2]菲特Fitow漆面缺陷检验系统https://www.fitow.com/tuzhuang
[3]菲特Fitow总装配置查验系统https://www.fitow.com/zongzhuang
[4]易思维ISV效率提升数十倍,易思维间隙面差测量系统在老牌车企落地https://mp.weixin.qq.com/s/VAYlrNgIQq3bhZcw2DrSQA
[5]易思维ISV双相机双线激光在间隙面差测量中的应用https://mp.weixin.qq.com/s/oIXzdDSnEZlzgYBbyNo3IA
[6]Speedbot视比特-3D视觉产品-自动化产线-视觉缺陷检验-间隙面差在线测量系统https://speedbot.com/cn/production/details?id=a6f03c2c-a530-43ed-a80e-3712fa86e9cc
[7]Speedbot视比特-3D视觉产品-自动化产线-视觉缺陷检验-全车身防呆在线检验系统https://speedbot.com/cn/production/details?id=e9f0245f-6537-4244-ab44-55b87e48652d
[8]吴国辉.车身间隙面差在线测量技术及应用【J】.汽车实用技术1671-7988(2022)16-123-05
[9]高钰.激光扫描仪在测量车身间隙面差中的应用【J】.汽车实用技术1671-7988(2021)07-101-03
本文为e-works原创投稿文章,未经e-works书面许可,任何人不得复制、转载、摘编等任何方式进行使用。如已是e-works授权合作伙伴,应在授权范围内使用。e-works内容合作伙伴申请热线:editor@e-works.net.cn tel:027-87592219/20/21。