2024年9月25-27日,e-works数字化企业网成功组织了首届“湖北标杆智能工厂考察”。本次考察中,e-works企业服务中心总经理江艳芬带领来自制造企业的高管,通过实地考察、专家讲解和深度探讨交流,考察团不仅身临其境地领略了不同行业智能工厂的最佳实践,也开拓了视野,并共同学习了标杆企业的成功之道。
湖北省作为全国领先的智能制造创新基地,不仅拥有雄厚的汽车产业基础,也是领先的光电子信息产业高地。近年来,在传统制造向智能制造转型升级的浪潮中,湖北省已建成武汉光电子信息与“武襄十随”汽车两大国家级先进制造业集群,并涌现了一大批大胆创新、务实进取推进智能工厂建设的优秀企业,成为了中国制造企业考察学习的标杆。
2024年9月25-27日,e-works数字化企业网成功组织了首届“湖北标杆智能工厂考察”。本次考察中,e-works企业服务中心总经理江艳芬带领来自制造企业的高管,在3天的时间里前往武汉与襄阳,参观走访了岚图汽车科技有限公司、牧野汽车装备(武汉)有限公司、武汉天马微电子有限公司、华工法利莱切焊系统工程有限公司、东风本田汽车有限公司、东风康明斯发动机有限公司,共6家行业翘楚的标杆智能工厂。通过实地考察、专家讲解和深度探讨交流,考察团不仅身临其境地领略了不同行业智能工厂的最佳实践,也开拓了视野,并共同学习了标杆企业的成功之道。

e-works 2024湖北标杆智能工厂考察团合影
一、自动化铸就“智造”之美
自动化是智能制造的重要标志,也是企业在推进智能制造过程中的必须要面对的课题。本次考察的企业在关键业务环节均实现了高度自动化,不仅提高了生产效率,减少了人力成本,还提升了生产的一致性和产品质量水平。
汽车,作为自动化设备与工业机器人应用场景最为成熟的行业之一,其自动化水平领先,并对其他行业的自动化建设具有借鉴意义。
岚图汽车冲焊车间建设有21条自动化线体,可将200多种冲压件合拼成白车身总成,430余台柔性机器人同步工作,焊接自动化率达100%;涂装车间,应用工业机器人进行全自动化涂装作业;总装车间,车身、车门等沿自动化输送线有序移动。此外,岚图汽车还建设有联通五大车间的空中物流系统与车间AGV、输送线地面物流系统,实现了物料运输、车身与零部件工序流转的自动化。基于高度自动化的作业水平,每118秒就有一台岚图汽车从自动化流水线诞生。
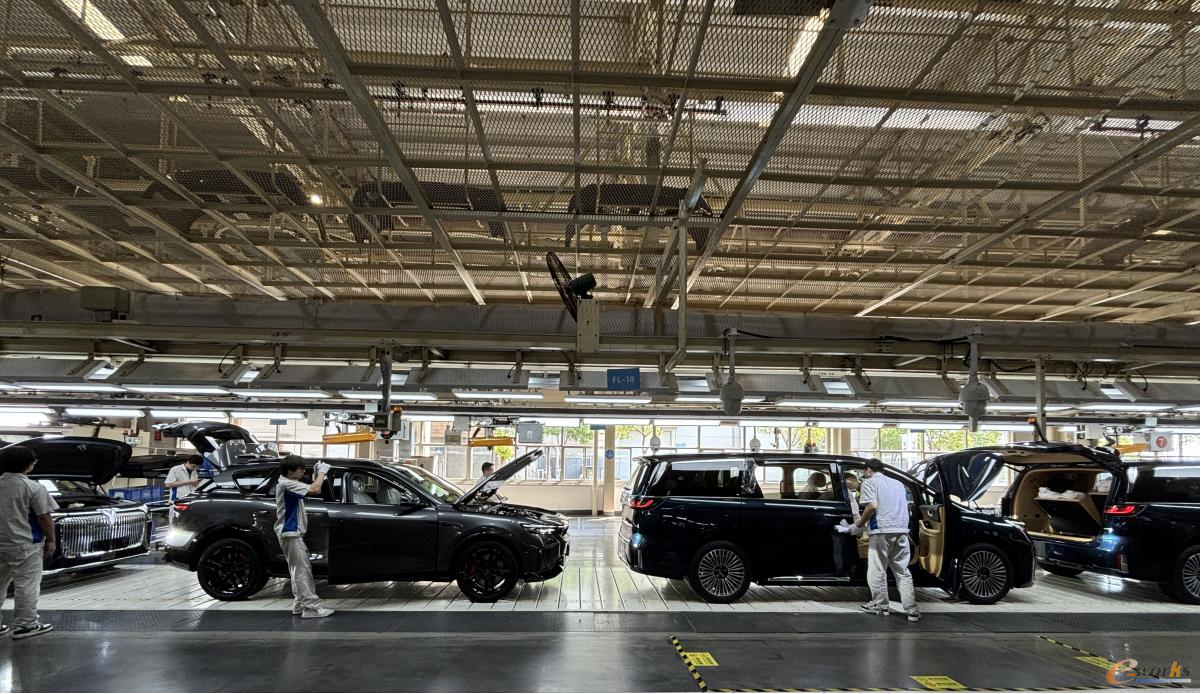
岚图汽车总装车间装配线
东风本田第三工厂,作为东风本田全球先进的标杆工厂之一,应用了大量的高度自动化设备。例如,焊装车间应用了300余台工业机器人实现100%自动化作业,仅需43秒就可以完成一辆车身“骨架”焊接;涂装车间的自动化率也可达到85%以上;总装车间内,机械悬臂有序挥舞,AGV智能小车来回穿梭,空中物流伴送线环绕运行,长达1.7公里的流水线上工人围绕车架熟练装配,每50.1秒就有一辆新车完成总装下线。东风本田第三工厂的高度自动化作业,在确保产品的先进性和可靠性的同时,也大幅提升了生产效率。
东风康明斯基于多元化产品结构,构建了中马力、重马力两个发动机制造工厂双线运营的生产模式,形成了2条总装线、12条机加线、1条AMT装配线的制造布局,发动机日产量高达1000台。其中,重马力工厂以黑灯工厂为建设目标,机加自动化率达90%,传奇机加线将于2024年率先建成“黑灯示范线”;涂装线应用机器人干式喷涂,实现喷涂作业自动化;总装线广泛应用工业机器人,自动化率达28%;此外,车间基于AGV小车实现了物料全自动化配送。
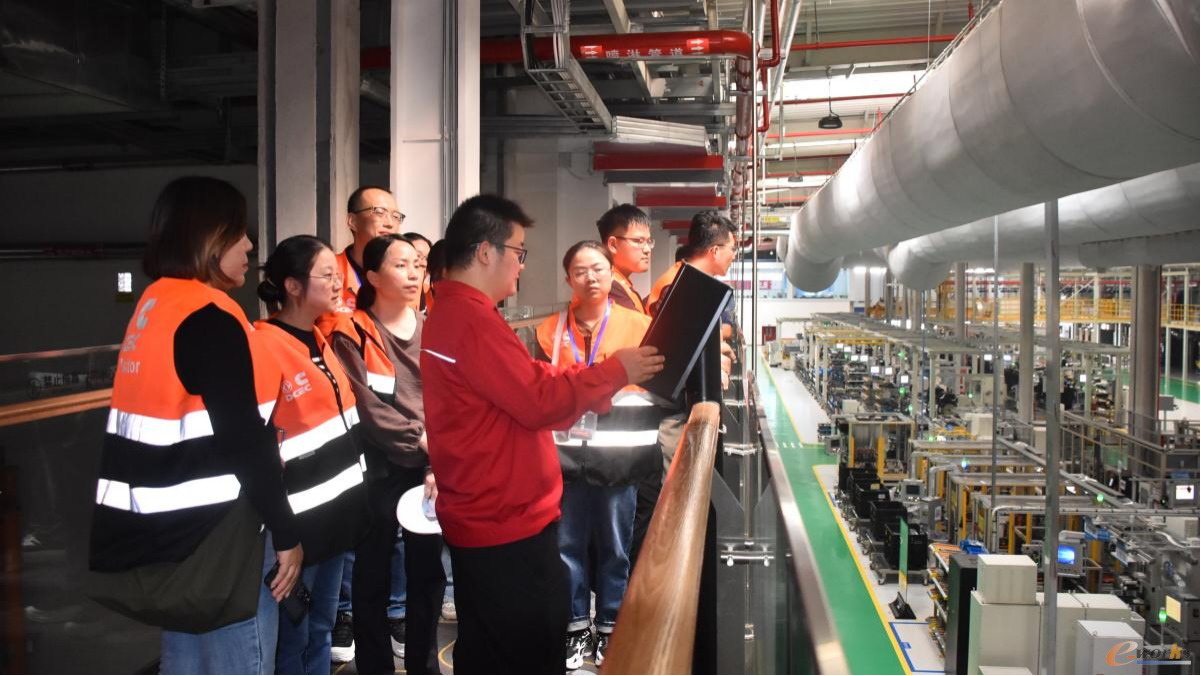
e-works考察团参观东风康明斯重马力工厂
高科技电子行业产品种类繁多、生产工艺复杂高精,在外部竞争愈发激烈的市场环境下,越来越多的企业正在加速推进生产自动化改造升级,通过高精确度、高稳定性、低成本的自动化作业,力争实现生产效率、安全性以及经济效益的显著提升。
武汉天马依托整体的智能工厂规划理念,加速生产自动化布局,其核心是通过自动化设备替代人工,实现重复劳动的自动化,进而实现单业务生产活动的自动执行。目前,武汉天马G6工厂通过自动化制程设备及物流搬送设备的应用,自动化率达92.3%,达到行业领先。其自动物料搬运系统(AMHS)集高度自动化与数智化于一体,由Rail轨道、CSC穿梭车、OHCV高空运输机、Crane堆垛机、AGV自动导引车、Stocker立体仓库等组成,可实现玻璃基板的高效流转与精准对接,全生产流程几乎无需人工干预。
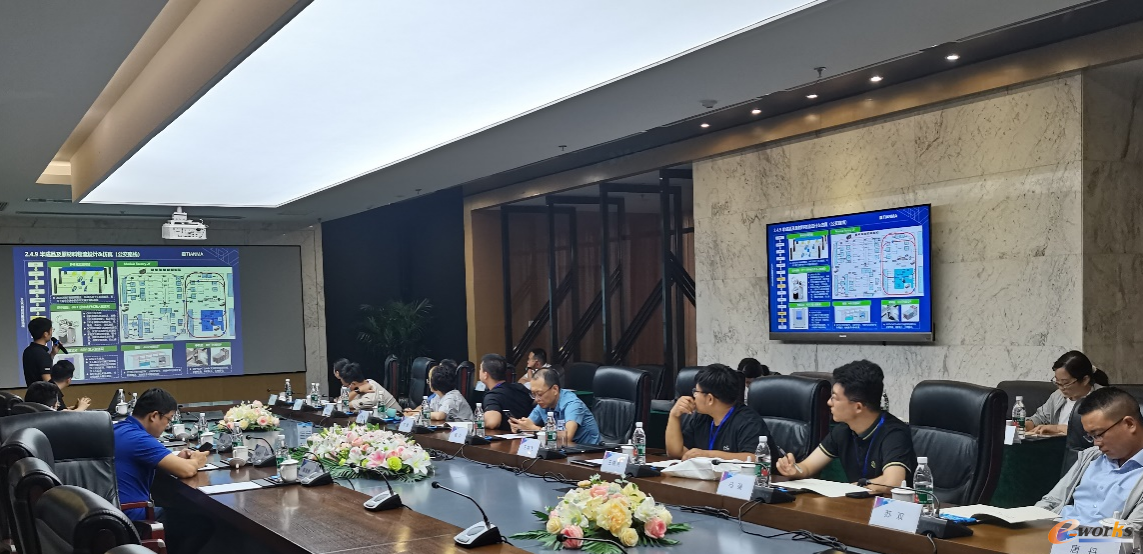
e-works考察团与武汉天马进行自动化物流系统建设交流
二、柔性化彰显“智造”之美
随着客户需求的日益多样化与个性化,制造业的生产模式正从大规模、批量化生产逐步转向多品种、小批量的定制化生产。因此,如何实现周期可控的柔性生产,已成为企业未来生存和制胜的关键。这也使得领先企业纷纷结合行业特点与公司现状,探索建设柔性生产体系与研发柔性生产解决方案,以满足混线生产与柔性制造需求。
岚图汽车在冲焊车间通过模块化NC柔性伺服定位系统搭建了柔性生产线,实现了岚图品牌SUV、MPV、轿跑SUV以及轿车等多车型在同一条产线上随机混流生产,最大限度地提高了设备利用率和生产效率;在总装车间,岚图汽车配备了智能力矩工具与全球首创T形柔性化车身吊具,并采用4连杆随行可灵活调整助力臂,提升了装配操作的准确性与稳定性。
东风康明斯采用柔性制造技术,在核心关键工序应用了全自动拧紧设备和全机型高柔性化托盘,通过自动变距、自动换套筒、自动程序选择等进行全自动换型,实现了10个平台100多种型号发动机的混流生产。

e-works考察团参观东风康明斯全机型高柔性化托盘
东风本田第三工厂则采用了柔性化生产线布局以及柔性化生产设备选型,可根据不同的产品特性和生产要求进行调整,从而实现多种车型在同一生产线上的共线生产。同时,总装车间使用自动升降功能台板,可在200~1750毫米范围内任意设定车下作业空间,充分满足了新能源车型和传统燃油车型的柔性化生产需求。
长期以来,牧野武汉也在积极进行柔性自动化生产技术的探索与创新。牧野PZ系列柔性自动化生产线,通过自动搬运小车实现托盘装载夹具与工件的机床自动化上下料与自动加工,为客户释放了更多劳动力的同时,实现了夜间以及休息日的无人生产,并提升机床开动率、生产效率及能力。未来,牧野武汉仍将致力于为客户提供高效率、高智能、高性价比的柔性自动化生产解决方案,助力客户实现高质量转型。
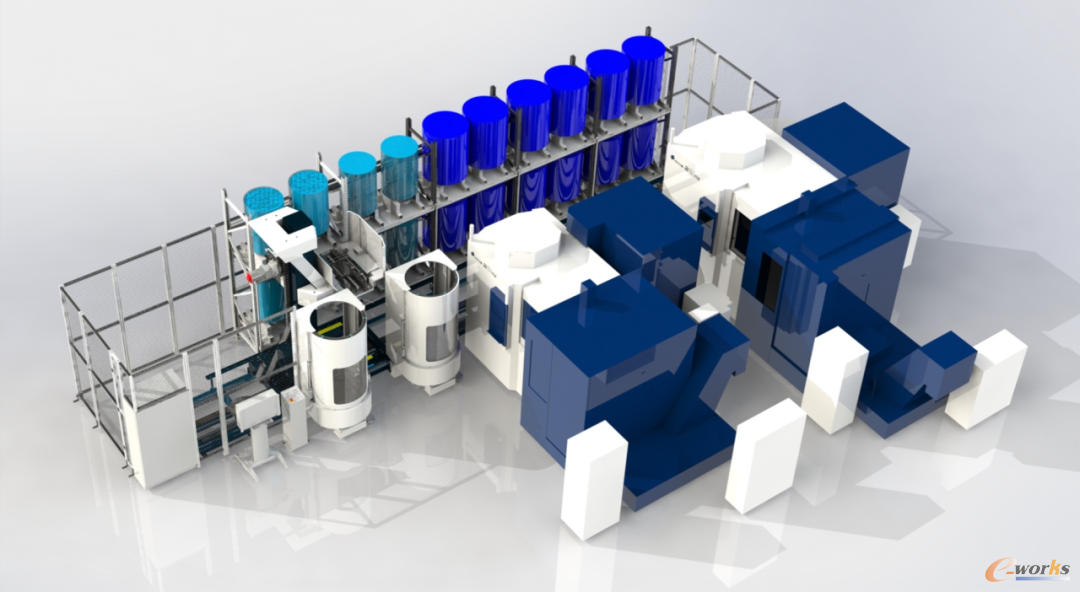
牧野PZ系列柔性自动化生产线(图源:牧野武汉)
华工法利莱作为全球领先的激光智能装备解决方案提供商,成功研发并实施了众多行业领先产品及解决方案。例如,华工法利莱成功研发了国内首套汽车白车身激光焊接成套设备——“轿车车身顶盖激光焊接柔性生产线”,仅需43秒就能完成一台白车身顶盖自动化焊接;其自主研发的三维五轴激光切割智能装备,可对工件进行多角度、多方位的柔性切割,B柱切割可达50s,最大切割速度18m/min、最大空走速度170m/min,可有效满足新能源汽车热成型件高质、高效、柔性加工的需求。

e-works考察团参观华工科技激光科技馆新能源汽车白车身激光焊接模型
三、数字化描绘“智造”之美
数字化是企业实现智能制造的重要基础,与智能制造相互促进,共同推动着工业生产的进步与革新。本次考察的标杆企业也都在持续不断地推进自身的数字化建设,为企业全价值链业务管理决策赋能。
例如,武汉天马G6智能工厂整体的建设目标是消除各业务信息孤岛,基于数字化需求、数字化研发、数字化制造、数字化运营、数字化服务,连通产品端到端的流程,实现基于全流程数字化的企业决策。
岚图汽车自成立之初便开始了数字化建设的探索之旅,并战略布局了岚图数字化转型的蓝图。目前,岚图汽车已形成“6+N+1”的数字化建设布局,主要包含1个大数据平台,助力运营决策,实现数字化决策;3个覆盖岚图研产销三大领域的数字化孪生平台,助力岚图核心业务数字化转型;1个高效协同办公平台,打造岚图协同化、高效化、无纸化办公场景;1个云管理平台,实现岚图云资源的高效规划与资源平衡;该布局也明晰了岚图汽车的数字化转型路径。
自2019年始,东风康明斯便以“数据驱动价值、卓越客户体验”为总体目标,以打通端到端价值链作为数字化工厂建设的主线,以提升制造运营能力为数字化工厂建设目标,踏上了从信息化向数字化的转型之旅。沿着“7312”战略,东风康明斯稳步推进,已实现营销、研发、供应链、制造、产品运营、质量管理、企业运营等业务环节的数字化。
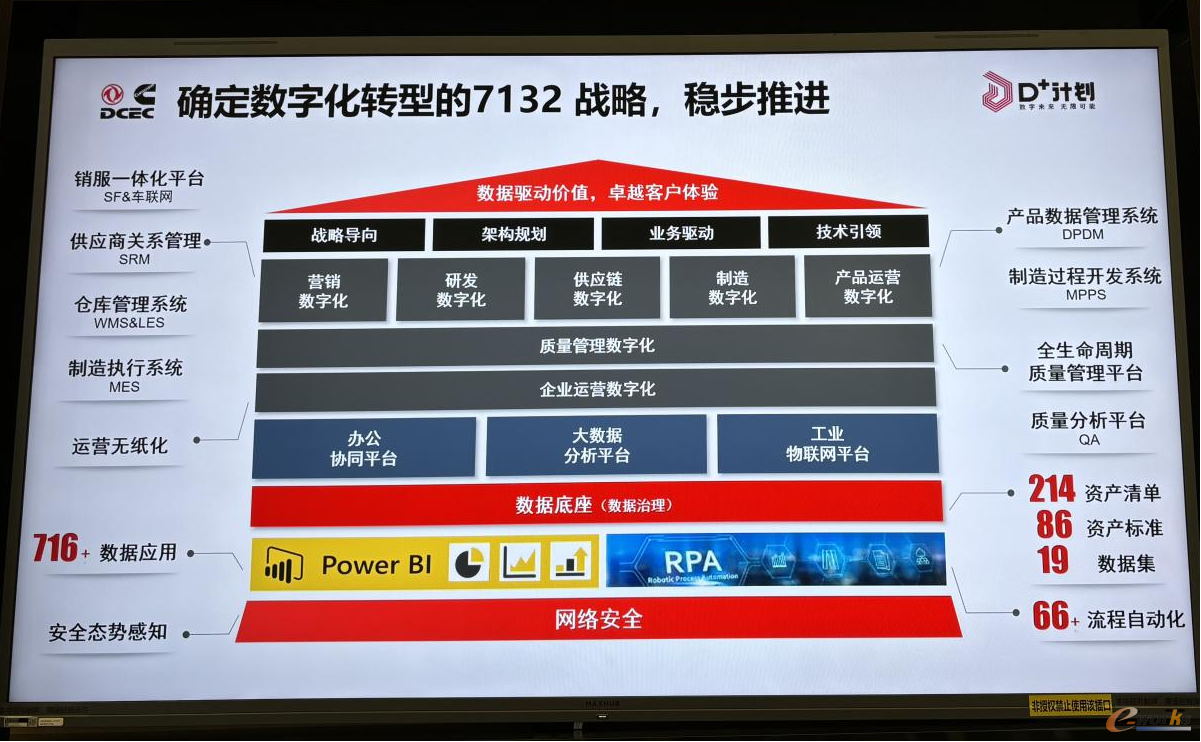
东风康明斯数字化转型7132战略
四、智能化演绎“智造”之美
新一代人工智能技术与先进制造技术的深度融合,升华成了新一代智能制造技术,并成为了新一轮工业革命的核心技术,是制造业高质量发展的核心驱动力,也驱动着行业领先企业积极探索生产制造新模式,实现智能化转型升级。
例如,岚图汽车通过构建AI认知思维、提升AI应用技术、驱动AI场景化能力来为企业培养AI人才,聚焦AI大模型在研发、生产、供应链和销售等业务环节的应用,并取得实效。东风康明斯工厂基于先进的智能制造技术,实现了包括机器人视觉定位模糊抓取、AI视觉检测、设备状态检测和预防性维护等智能化场景应用,产品质量与生产效率均实现有效提升。
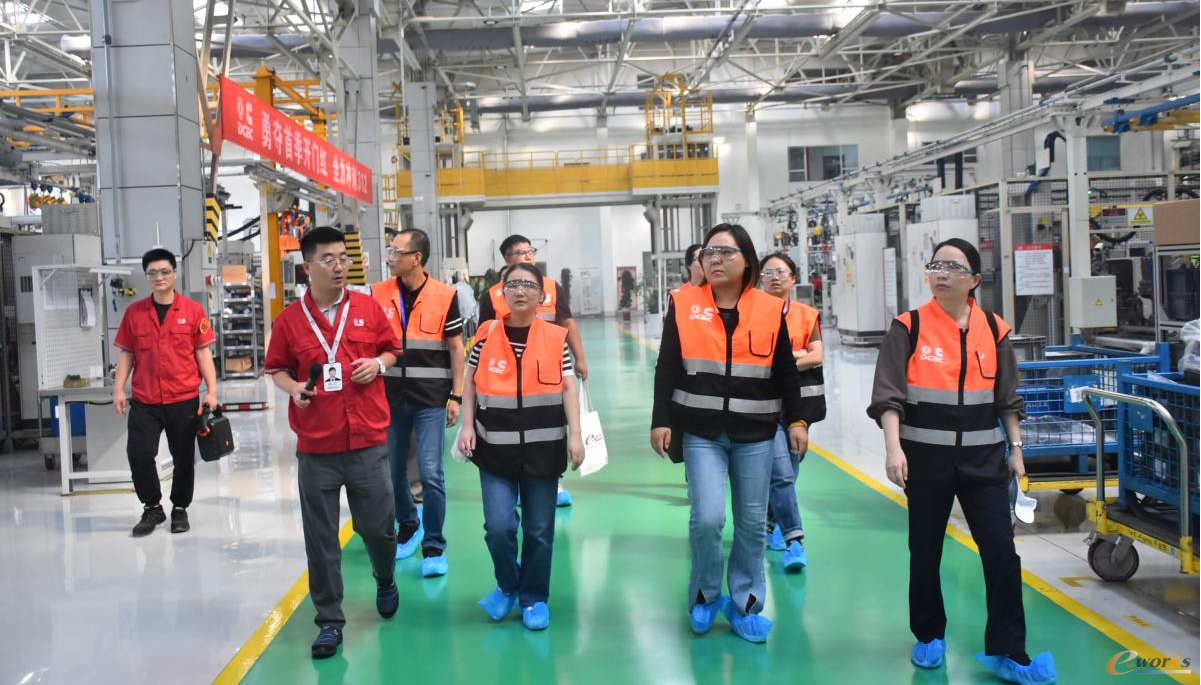
e-works考察团参观东风康明斯生产现场
武汉天马G6工厂通过自研与引入智能管理系统,应用数字化仿真、AI、物联网等先进技术手段,成功构建了一个高效、灵活、智能的生产体系,其中数智化缺陷智能检测系统(ADC)尤为突出。ADC系统依托AI技术,通过深度学习模型将智能检测的触角延伸至工厂的每一个角落,实现了实时监控、实时追溯、实时数据集成,最终达成跨机台间的数据整合及智能判定,全面提升了检测准确率及效率。此外,该系统每月自动检测图片1000多万张,提升检测效率的同时,大幅降低了人力成本。
五、绿色化点亮“智造”之美
随着碳达峰、碳中和纳入经济社会发展全局,为实现可持续、高质量发展,我国制造业绿色化发展步伐加快。通过本次考察可以发现,行业领先企业都在围绕绿色低碳发展战略,积极探索绿色智能制造。
作为全球领先的机床制造商牧野亚洲集团旗下全新绿色节能工厂,牧野汽车装备(武汉)有限公司工厂建设有屋顶光伏项目与生产车间光伏系统可视化系统,整个厂区屋顶的光伏发电与碳减排数据一目了然。可以看到,在用电量不太大的月份,牧野武汉能够实现电力自给自足,不仅降低了资源与成本消耗,也充分体现了其绿色、可持续的发展理念。
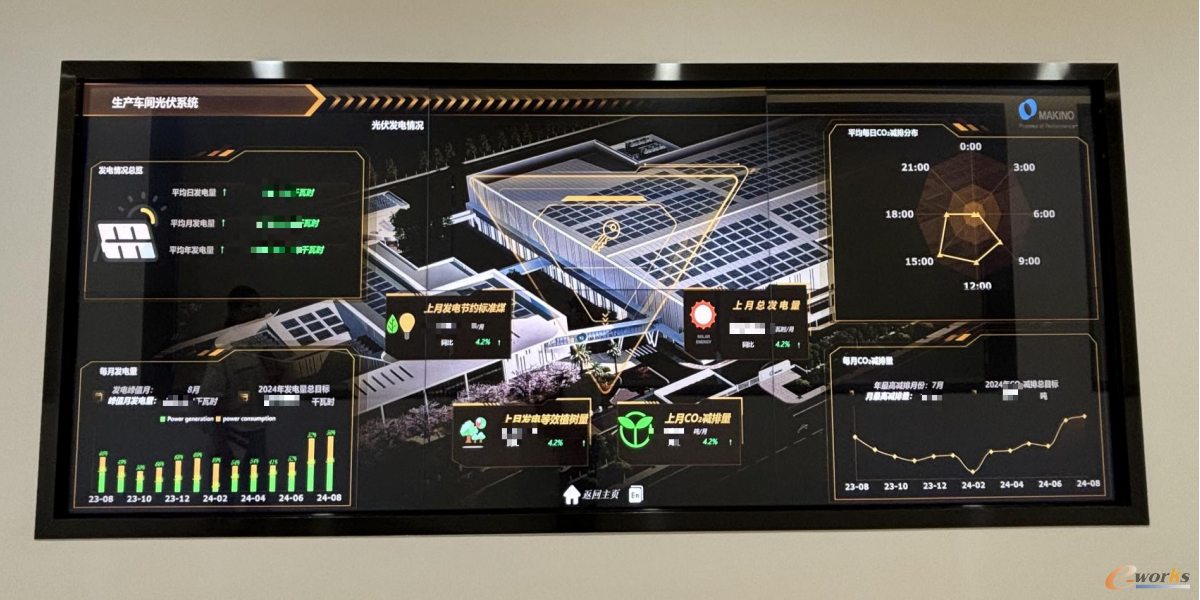
牧野武汉生产车间光伏系统可视化大屏
作为襄阳首个绿色工厂,东风康明斯始终坚持产品全生命周期绿色理念,推动产品设计、采购、制造、报废全过程转型升级。例如,开发生产绿色产品,推广绿色设计和绿色采购,进行产品减重化设计,替换有毒有害物质,并采购合规、环保的零件与材料;应用采用先进适用的清洁生产工艺技术和高效末端治理装备,淘汰落后设备,通过前端改进(使用环保水性漆)和后端治理(将漆雾收集通入环保设施处理后排放),减少了90%的挥发性有机化合物(Volatile Organic Compounds,VOC)排放;建设光伏屋顶、新污水处理与中水回用项目,配合高效机房、公用动力集控等技术,降低了公用动力与资源消耗。此外,东风康明斯还建设有公用动力数字化中心,能源管理系统实时监测厂区及设备用能情况,一旦出现用能数据异常,系统就会通知员工进行检查处理,实现节能减排。
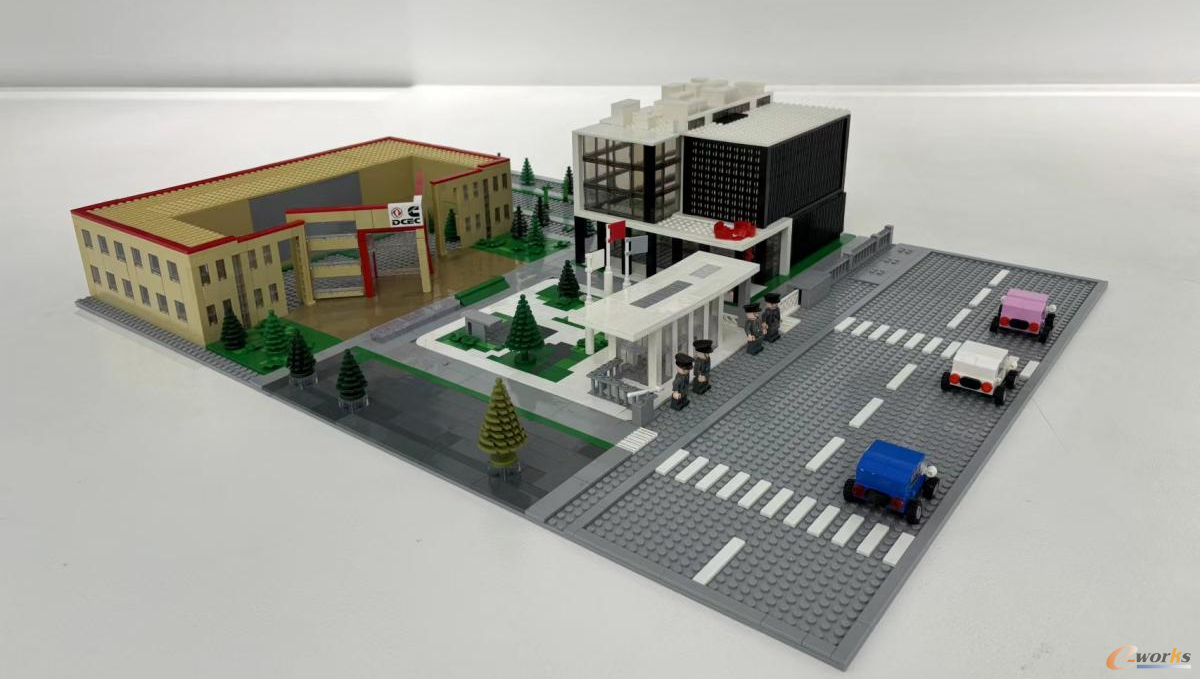
东风康明斯工厂微缩模型
除了高度自动化、智能化的生产流程,隐藏在东风本田第三工厂高效率生产背后的环保理念,同样值得关注。在“绿色工厂”的理念下,东风本田第三工厂将光伏发电、中水回收、节约能源视为三大要素,大量使用环保材料来减少对能源的消耗。例如,工厂配备屋顶光伏发电和先进废水处理系统,实现电力自给和废水循环利用;同时,智能能源管理系统实时监测能源消耗,优化调度,提高利用效率,再生电流回收装置节能20%。在生产环节,车身及内饰采用生物基塑料、轻量化铝合金等可再生材料,减少资源消耗与污染;涂装作业采用锆盐绿色工艺,实现镍零排放和废渣的减少。
后记
湖北省是智能制造产业的重要发展地区,本次考察遴选了湖北省极具代表性的标杆企业,涵盖高端装备、光电子信息、汽车零部件等行业,通过不同维度和视角的参观学习,考察团成员领略了湖北标杆智能工厂的魅力与成功之道,对今后推进智能制造有了更直观的认识,也为今后的工作创新提供了新思路。
关于本次考察的更多详细内容,请查看e-works特别报道:
2024湖北标杆智能工厂考察
e-works作为致力于推进智能制造与两化深度融合的第三方专业服务机构,将通过考察、论坛和实训等多种形式,持续为广大制造企业提供更多与知名企业面对面学习交流的机会。
本文为e-works原创投稿文章,未经e-works书面许可,任何人不得复制、转载、摘编等任何方式进行使用。如已是e-works授权合作伙伴,应在授权范围内使用。e-works内容合作伙伴申请热线:editor@e-works.net.cn tel:027-87592219/20/21。