本文为“2024年度中国智能制造最佳应用实践奖”参评案例。本次活动将评选出2024年度,为中国智能制造领域带来突出效益的最佳实践工程,全面介绍企业推进智能制造的步骤、重点与难点、获得效益等,分享建设过程中的经验,供广大制造业行业企业学习供鉴。
一、企业简介
承德建龙特殊钢有限公司成立于2001年,是国内唯一一家把钒钛资源综合利用和特钢生产有机结合的企业,是国家高新技术企业、国家知识产权优势企业、国家级绿色工厂、河北省科技领军企业、承德钒钛基地的核心骨干企业、承德市行业龙头民营企业。公司建有国家企业技术中心、承德建龙河北院士工作站、河北省锻造用钢技术创新中心、河北省企业技术中心、河北省企业重点实验室、钒钛资源综合利用研究所和检测中心等科研创新平台。
公司总资产 214亿元,现有员工3900人,2023年实现营业收入141.53亿元。
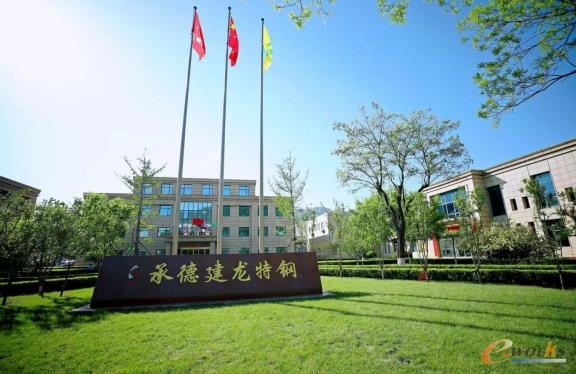
图1 承德建龙特殊钢有限公司
二、企业在智能制造方面的现状
近年来,承德建龙建成了全工序集控中心、无缝钢管智能工厂、中棒智能制造工厂及能源、环保、安防、物流、生产5套智能管控平台。2021年,承德建龙无缝钢管厂成功入选国家级智能制造试点示范工厂。2022 年,承德建龙作为唯一一家钢铁企业入选“2022 年智能制造标杆企业”。
2023 年,热轧无缝钢管智能工厂关键技术及装备荣获“冶金科学技术一等奖”,并入选“钢管产业十大创新案例”;中棒数字孪生系统入选工信部“工业互联网试点示范项目”。2024年,215烧结机智能制造系统技术应用项目入选工信部国家2024年钢铁行业重点场景数字化转型典型案例,承德建龙热轧无缝钢管智能工厂入选河北省2024年度先进级智能工厂名单。
三、参评智能制造项目详细情况介绍
“承德建龙热轧无缝钢管智能工厂”项目是河北省钢铁行业数字化转型专项行动(2020-2022 年)的重点项目,总投资 11.2亿元。项目针对无缝钢管生产设备管理维护差、产品质量全生命周期追溯难、生产线数据贯通难度大、物流仓储效率低等行业痛点,联合北京科技大学等多家供应商,在前期建立自动化生产线、MES 及 EMS 系统的基础上,搭建数据治理及集成平台、智能成品库等,配备大量智能检测设备,推动传统无缝钢管生产模式变革,覆盖生产作业、质量管控、设备管理、安全管控、能源管理、计划调度、仓储配送等 13个环节的 24 个智能制造典型场景,致力于打造世界首条“无缝钢管智慧工厂智能制造示范生产线”。
项目创新点有:一是国际首创采用机器人标识+视觉识别+软件跟踪技术,实现无缝钢管全流程逐支跟踪。二是行业首创通过激光扫描+机器视觉技术取代人工目视检查,实现钢管内表面缺陷和平直度检测。三是推动智能成品库首次应用于无缝钢管领域。四是构建数字孪生工厂,实现物理实体与数字虚体的实时交互与操控。
项目的成功实施树立了无缝钢管智能工厂标杆,形成的模式经验将在集团公司内部以及全行业中复制推广,有效推动钢铁行业转型升级。
1.项目背景介绍
(1)实施背景
从“十三五”期间我国在深入推进“三去一降一补”的供给侧结构性改革以及国内外钢铁企业发展经验来看,智能制造已经成为了制造业高质量发展的必由之路,建设智能工厂巳经成为传统制造业转型升级的主要突破方向。无缝钢管智能制造目前在国内还处于空白,用户对无缝钢管产品质量的要求也越来越高。在行业、市场环境和企业目身发展的需求影响下,承德建龙致力于打造国内首条无缝钢管行业“黑灯工厂”,实现生产过程的可视化和产品质量追溯的透明化,全面提升生产的智能化水平,打造无缝钢管行业智能制造领跑者。
(2)基础条件
本项目前期建立了自动化生产线、MES 及 EMS 系统,数控化率达到 100%且 100%接入工业网。项目建设定位为建设无缝钢管数字化工厂,通过搭建集数据采集、挖掘、分析的综合性平台,助力构建新型智慧信息体系,为后续智能工厂的升级扩展奠定了良好的发展基础。
(3)总体实施架构
本项目分以下三层进行建设:
第一层为生产线设备,主要生产设备有管坯区、环形加热炉、穿孔机、连轧管机、脱管机、定径机、冷床、排管锯、预精整线等,在此基础上建设:
1)物料逐支跟踪系统,采用机器人标识+视觉识别+软件跟踪的综合应用,实现生产线的全流程物料逐支跟踪;
2)多套智能装备,实现钢管生产过程关键质量在线全自动检测,并应用机器人在线逐支打磨钢管两端毛刺,生产效率提升20%,优化人员比例 40%。
第二层为数据治理集成平台及工序级能源介质管理系统、生产过程质量管控系统、设备智能运维系统,具体如下:
1)数据治理及集成平台,汇集来自现场各系统的各类专业数据,构建全链路的数据模型,支撑无缝钢管厂数字化转型;
2)工序级能源介质管理系统,实现在线集中“监测、分析、评估”,提高企业现有供能设备的效率,实现节能、高效生产,运营成本下降10%;
3)生产过程质量管控系统,实现全流程时空统一分析,实现产品不良率下降90.94%;
4)设备智能运维系统,利用在线监测、智能诊断等手段,使设备综合利用率提升 5%。
第三层为面向多场景及融合技术的数字孪生工厂,融合各类智慧管控系统信息,实现对工厂快速、科学、有效的管理,从而达到降本增效的目的。以上三层架构共覆盖生产作业、质量管控、设备管理、能源管理、仓储配送等 13 个环节,24 个场景。
(4)总体建设情况
目前,智能在线检测、数据治理及集成平台、物料逐支跟踪、设备智能运维、数字孪生工厂等系统已经全部上线。
2.项目实施与应用情况详细介绍
(1)系统集成方案
承德建龙钒钛高科无缝钢管智能工厂进行分层规划和建设,分别为生产线设备,数据治理集成平台及工序级能源介质管理系统、生产过程质量管控系统、设备智能运维系统,面向多场景及融合技术的数字孪生工厂等三个主要层面。围绕加热炉、穿孔机、连轧机、定径机及精整等工序,建立生产数字化、过程模型、在线检测、集中操控、机器人等智能系统,逐步形成了流程横向贯通、管控纵向协同、信息物流一体化的架构;建成了供应链整体优化模式下全流程质量管理控制、一体化智能调度、能源生产协同调配的精益化管控平台;构建了以生产过程大数据为基础的数据中心,以钢铁行业模型库为主的轧制模型,以及数字孪生无缝钢管热轧的模拟仿真平台。
此外,通过重点打造生产作业、质量管控、设备管理、安全管控、能碳管理、环保管控、计划调度、仓储物流等 13 个环节 24 个智能制造典型场景,通过搭建集数据采集、存储、加工、质量、计算、分析、挖掘和开发的综合性平台,支撑企业内外部信息资源的整合共享、海量异构数据的高效处理与智慧服务能力的灵活扩展,助力构建新型智慧信息体系,致力于打造国内首条无缝钢管行业“黑灯工厂”,秉承“指标牵领、流程透明、业务协同”的理念,打破业务之间的运营管理边界,构建企业精益管控新模式,以实现客户价值和企业价值的协同为主线,聚焦数据感知、知识认知、优化决策,挖掘海量数据背后隐藏的潜在价值,实现生产过程的优化及运行过程的多业务协同。
(2)项目的先进性与特色
项目针对热轧无缝钢管智能工厂和智能装备难点技术问题进行攻关,自主创新研制了热轧无缝钢管车间智能制造技术及装备。主要创新点如下:
1)首次研发了基于物理逻辑与深度学习 AI 标识的无缝钢管热轧生产线逐支跟踪系统,实现了单支无缝钢管生产过程的精准跟踪与数据映射;并依托逐支跟踪建立了无缝钢管工业互联网数字化平台,实现了多业务协同数字化精益管控及为每支钢管开具三维数字质保书。
2)首创了无缝钢管内表面缺陷、轮廓、平直度检测设备,自主开发与集成了无缝钢管外表面缺陷、直径、壁厚等检测设备,建立了“在线判定-监控预警-一键追溯-质量优化”工艺质量管控系统,提升了产品质量与稳定性。
3)自主研发了基于动态视觉识别的钢管端部打磨装备、无缝钢管库区无人化控制装备,并对整个产线流程进行整合,建立了“坯料-加热-轧制-精整-库区”全工序远程智能集控系统,实现了无缝钢管高效集约生产控制。项目申请发明专利 28 项,已获得发明专利 18 项、实用新型专利 5 项、软件著作权 28 项,主持及参加制定行业标准 1项、团体标准 4 项,发表论文 11 篇。
项目成果成功应用于承德建龙特殊钢有限公司 258 无缝钢管连轧生产线,被工信部评为“2021 年智能制造示范工厂”与“2022 年智能制造标杆企业”,并获得“2023 年冶金科学技术一等奖”。该项目经济、社会、环境效益显著,推广前景广阔。
3.效益分析
承德建龙钒钛高科无缝钢管智能工厂项目的总体目标是实现“数字化、网络化、绿色化”的智能制造。项目成功实施后,对于实现“岗位少人化,产线自动化,工厂信息化、整体智能化”方面取得重大进展,加快促进企业数字化转型。基于数据采集与集成平台,数据完整真实可靠,把企业成本做到最优、效率做到最佳、经营无限贴近客户需求和市场变化、管理无限贴近现场和一线员工,促进生产规模优势、协同效应的充分发挥,提高综合竞争力。
项目在科学技术、经济效益、社会效益等方面产生显著成效。
(1)项目科学、技术、产业成效
本项目建立联合研发团队进行协同创新,针对无缝钢管生产流程,通过智能化控制方法与生产工艺融合,实现产品质量一致性、稳定性以及定制化。在无缝钢管生产全流程工艺参数-产品质量影响关系及演变机理研究基础上,建立工艺质量关联知识数据库,提供各工艺参数对产品综合质量的关联与量化方法;在开发无缝钢管生产流程大数据平台的云架构体系基础上,针对提升产品质量一致性、稳定性需求,建立基于工业大数据的智能工艺控制技术。项目将对无缝钢管生产线实现产业化示范应用,有效提升综合生产效率、劳动生产率,降低制造成本等技术指标,形成一系列论文、专利、标准,推动无缝钢管生产企业的智能化产业升级。
(2)经济效益成效
本项目通过解决基于工业大数据的无缝钢管智能化工艺控制技术一系列科学和关键技术问题,以及基于工业大数据的智能化工艺控制,实现无缝钢管生产工艺和生产管理的优化,提升工艺质量及生产稳定性,本项目经济效益十分显著,具体体现在关键设备数控化率 100%,生产效率提升 20%,资金综合利用率提升5%,研发周期缩短20%,运营成本下降11.7%,产品不良率下降37.5%,优化人员比例40.5%,设备综合利用率提升4.65%,库存周转率提升 11.81%,订单准时达成率提升20%。
(3)社会效益成效
本项目基于工业大数据的无缝钢管智能化工艺控制基础理论与共性技术,进而建立具有自主知识产权的示范工程,形成信息化、智能化在无缝钢管行业应用典范,有力拉动产业结构升级,克服长期以来制约产品质量一致性、稳定性、定制化的技术问题,提升产品档次。项目实施过程中通过不断地解决科学问题和开发出关键共性技术,为科研院所、高校和生产企业培养大批无缝钢管领域的青年人才,为科研院所、高校、生产企业协同创新提供持续动力,具有显著的社会效益。
本文为e-works原创投稿文章,未经e-works书面许可,任何人不得复制、转载、摘编等任何方式进行使用。如已是e-works授权合作伙伴,应在授权范围内使用。e-works内容合作伙伴申请热线:editor@e-works.net.cn tel:027-87592219/20/21。