本文为“2024年度中国智能制造最佳应用实践奖”参评案例。本次活动将评选出2024年度,为中国智能制造领域带来突出效益的最佳实践工程,全面介绍企业推进智能制造的步骤、重点与难点、获得效益等,分享建设过程中的经验,供广大制造业行业企业学习供鉴。
一、企业简介
运达能源科技集团股份有限公司(简称“运达股份”)是一家在新能源领域具有深厚底蕴和卓越成就的企业。公司成立于2001年,前身为浙江省机电研究院风电研究所,至今已深耕新能源技术研究与产品开发50余年。公司总部位于浙江杭州,是一家大型国有上市企业。
运达股份的主营业务涵盖大型风力发电机组的研发、生产和销售,以及新能源电站的投资运营。同时,公司还积极培育智慧服务业务,拓展储能、新能源项目EPC总承包等多元化业务。其产品主要为陆上及海上风电机组,并围绕新能源、智能电网及综合能源开发,提供全生命周期整体解决方案。在技术创新方面,运达股份取得了显著成果。公司曾研制出我国第一台并网型风力发电机组,并多次获得国家和省级科技进步奖。此外,公司还承担了多项国家和省级重大科技专项项目,为新能源领域的技术进步做出了重要贡献。
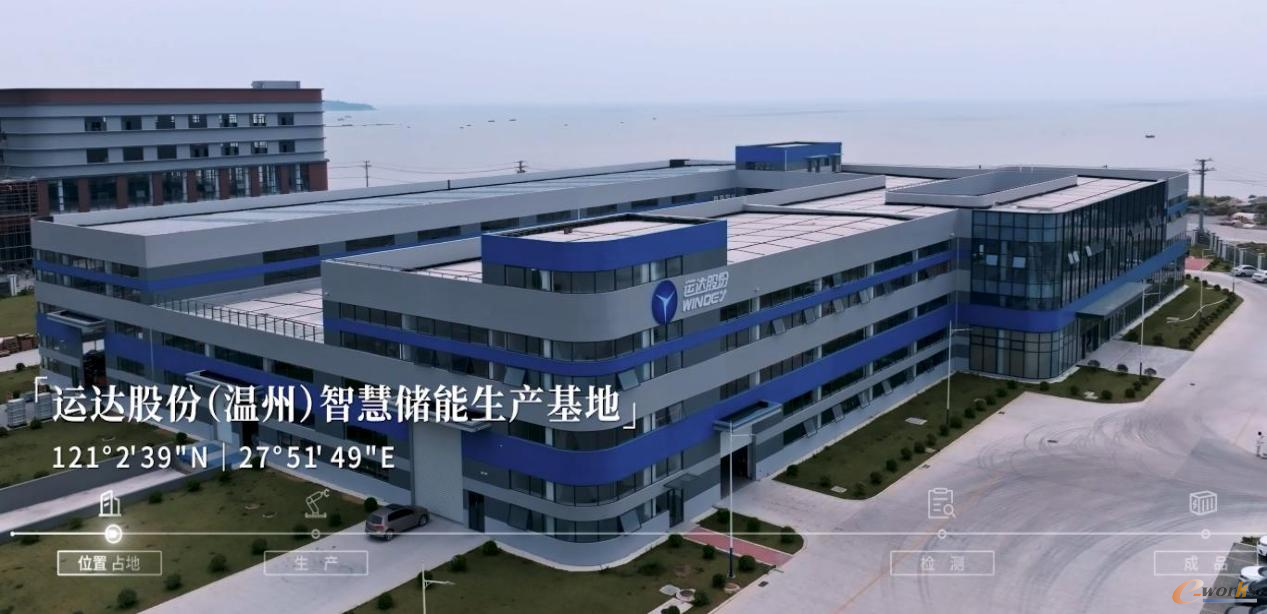
图1运达股份
二、企业在智能制造方面的现状
运达祥运储能数字化车间项目,投资建设了高度自动化的磷酸铁锂电池PACK生产线、储能电池系统集成一体化装配线和全过程PQC(产品质量控制)检测体系。规划建设了IOT平台,实施赛意储能CRM、用友NCC ERP系统、广域铭岛储能MES,实现生产、经营、管理过程的数字化和智能化管理。通过BI、大数据和AI等技术的综合应用,为企业生产运营提供分析和决策依据,推动全业务链、全生产流程的数字化转型与升级。

图2温州祥运新能源有限公司数字化车间
1)数字化车间项目先后投资建设90余台先进生产装备,建成包括电芯上料、分选、贴胶、输送等复杂工序的高度自动化的磷酸铁锂电池PACK生产线及储能电池系统集成一体化装配线,建成全过程PQC(产品质量控制)检测体系,实现了储能电池的柔性制造,降低能耗,减少人工,提升产品量。
2)建设IOT平台,进行设备联网和数据采集,联网设备46台套,设备联网率达到83%,实现生产现场设备、人员、物料和工单等现场信息的数据采集、跟踪、统计和分析,实现了车间的透明化管理。
3)实施了赛意储能CRM、广域铭岛储能MES、用友NCC储能ERP、启安智慧安全生产平台等系统,实现ERP/MES/CRM信息系统数据集成,实现从订单、计划、物流、生产、质量和设备等的过程的数字化管理。
4)应用BI、大数据和人工智能等技术,建立数字化和可视化系统,推进产线数字化、过程透明化、管理信息化为核心的智能制造转型,实现基于数据的分析决策支持。
三、参评智能制造项目详细情况介绍
1. 项目背景介绍
全球能源转型与储能需求增长
随着全球对清洁能源和可持续发展的重视,能源转型已成为不可逆转的趋势。风能、太阳能等可再生能源的广泛应用,使得电力系统面临出力波动性、调节能力不足等问题。储能技术作为解决这些问题的重要手段,其重要性日益凸显。特别是电化学储能,因其高效、灵活等特点,正逐渐成为储能领域的主流技术。随着全球储能市场的快速增长,对储能数字化车间的需求也随之增加。
国家政策支持与推动
为实现“双碳”目标,构建清洁低碳、安全高效的能源体系,各国政府纷纷出台相关政策支持储能技术与产业的发展。例如,中国国家发改委、能源局等政府部门发布了《关于加快推动新型储能发展的指导意见》等一系列政策文件,明确提出要加快新型储能的推广应用和规模化发展。这些政策为储能数字化车间的建设提供了良好的政策环境和市场机遇。
技术进步与产业升级
随着数字化、智能化技术的不断发展,储能行业也迎来了产业升级的契机。数字化车间通过运用先进的信息技术、自动化技术和智能化技术,可以实现对储能产品生产过程的精准控制、优化管理和高效协同。这不仅可以提高生产效率、降低成本,还可以提升产品质量和市场竞争力。因此,储能数字化车间的建设已成为储能行业转型升级的重要方向。
2. 项目实施与应用情况详细介绍
温州运达储能电池数字化车间,打造高度自动化的磷酸铁锂电池PACK生产线、储能电池系统集成一体化装配线和全过程PQC(产品质量控制)检测体系,形成年产680套(2000MWh)高端储能装备生产能力。通过对车间的工艺流程和产能设计进行设备、物流等的布局规划和建模仿真进行车间的整体布局规划,建设成为高度自动化和智能化水平的数字化车间。
储能电池的设备布局采取自动化流水线的排布方式,对电池物流、上下料、加工、装配和检测等工序进行建模、规划和优化,提升生产过程自动化,优化制造和物流节拍,生产强度大幅度减少,打造了智能制造新模式。
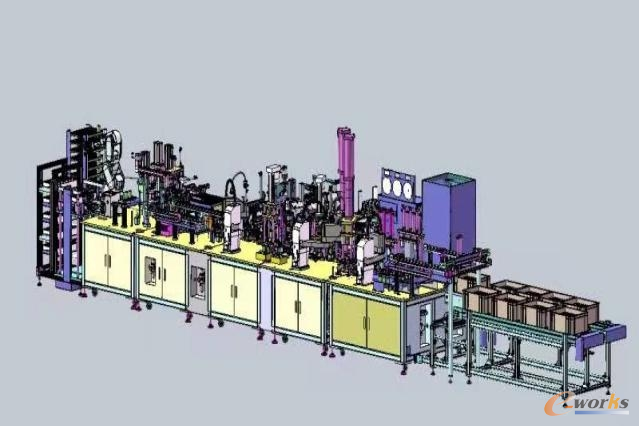
图3储能电池装配产线建模
1)工艺和装备技术先进性
运达祥运为解决储能产品生产过程长,装配要求高、测试环节严等制造工艺特点,运达祥运针对储能电池工艺、装配工艺核测试工的制造工序核制造设备进行了改进和优化。
通过自动化产线建设,实现了电芯上料、电芯分选、电芯贴胶、电芯/风道隔板预装、电芯堆叠、模组捆扎等工艺的自动化。产线采用工业机器人替代人工上下料、工序和测试定位装夹。实现储能电池上下料、工序流转和智能检测,实现设备先后动作、节拍、协作和检测过程的一致性,达到自动化生产和敏捷生产的目的。车间通过极性/绝缘检测、模组EOL测试、充放电测试和绝缘耐压测试等实现储能电池的自动化综合测试。运达祥运的储能电池全自动模组产线水平达到行业领先水平。
2)储能产品生产数字管控体系先进性
运达祥运数字化车间项目,建立储能电池自动化生产线和检测线,实施了PTC PLM、用友NC ERP、广域铭岛MES系统和安全管控平台,实现生产过程工单信息、设备信息、质量信息、安全等关键制造过程数据的采集、统计和分析,实现生产过程的透明化管理。
通过数据集成,实现计划自动下发和进度跟踪、质量数据采集和追溯、设备状态和关键数据监控,打通运营层及设备层的衔接,提升了生产管控的精益化水平,提升了产品质量与生产效率,实现生产过程的数字化管控和调度优化,提质增效成果显著。
3)建成先进储能研发试验平台
运达祥运建立储能研发试验平台,配置高精度1500V/400kW充放电测试系统、3000L高低温试验箱、MW级变流器检测等设备,具备储能电池单体、模块、簇、电池管理系统(BMS)、电池簇到集成系统的全链条、多尺度研究试验能力。涵盖倍率阻抗特性、热管理性能、环境耐久性能、电能质量、电网适应性、系统转换效率和不同场景下的寿命与安全评估,以及BMS上下高压、均衡算法、故障录波、显示通信等能力,满足不同层级先进储能产品试验和测试,满足不同层级储能部件关键性能实测,并高效支持自主研发产品的测试开发。
4 ) 建成储能产品数字化精益生产管控体系
运达祥运储能产品数字化车间项目,通过引进高度自动化的磷酸铁锂电池PACK生产线、储能电池系统集成一体化装配线和全过程PQC(产品质量控制)检测体系,应用IOT平台、ERP、MES、CRM、BI系统,实现生产、经营、管理过程的数字化和智能化管理,为生产运营提供分析和决策依据,推动全业务链、全生产流程的数字化转型与升级。
3.效益分析
运达祥运洞头基地数字化车间于2023年6月开始建设,2024年6月全面生产,目前已经形成年产680套(2000MWh)储能装备的生产能力。
社会效益
1.储能技术助力区域绿色节能发展
运达祥运位专注于磷酸铁锂电池及储能电池系统等高科技、智能化、绿色化储能产品的研发与生产。主要产品包括磷酸铁锂电池、储能电池系统等储能产品,具备年产能2GWh高端储能装备生产能力。运达集团温州运达祥运产品包括集装箱式、柜式等多种形式,可用于周边企业开展绿色能源管理、峰谷电调度优化等的应用。运达祥运通过项目建设,在企业内建立储能、调度和能源优化利用的样板,并可将相关产品和技术为周边地区企业提供服务,助力区域地区制造企业的绿色节能发展。
2.为洞头地区企业打造数字化车间模板
温州洞头地区绝大多数制造企业的生产模式仍采用传统制造模式,制造设备落后、生产效率和质量稳定性不高,阻碍了洞头区制造企业的转型升级发展进程,急需通过智能制造实现转型升级。
运达祥运通过探索并完善生产过程自动化、制造管控数字化,综合应用了设备改造、工业机器人、智能检测、工业互联网、数据采集、MES系统等多种技术,打造了行业领先的储能电池数字化车间,为温州和洞头地区制造行业的自动化、数字化和智能化改造建设树立了样板。项目实施过程中所积累的管理、技术、软硬件、实施方案和实施经验等,可以帮助洞头区域制造企业,认识到自动化和数字化的价值,推动地区企业积极引进数字化、自动化设备,推进数控加工、机器换人和人机协作制造模式和智能制造的发展。有助于推动洞头乃至周边地区的企业的智能化改造的积极性,推动洞头地区制造产业的快速发展,具有较高的示范价值。
经济效益
运达祥运通过数字化车间建设,人均生产效率提升20.37%,万元产值成本降低20.83%,产品不良品率降低38.98%,新产品研制周期缩短30.77%,能源利用率提升12.48%,物料配送准确率达到98.5%,仓储周转率提高了25%。