本文为“2024年度中国智能制造最佳应用实践奖”参评案例。本次活动将评选出2024年度,为中国智能制造领域带来突出效益的最佳实践工程,全面介绍企业推进智能制造的步骤、重点与难点、获得效益等,分享建设过程中的经验,供广大制造业行业企业学习供鉴。
一、企业简介
广汽传祺汽车有限公司(以下简称“广汽传祺”)是由广州汽车集团股份有限公司独资设立的子公司,作为广汽集团自主品牌乘用车项目的实施载体,致力于生产销售具有国际先进水平的整车、发动机、零部件及汽车用品,以及汽车工程技术的研究与开发。广汽传祺成立于2008年7月21日,占地面积118万平方米,为国家高新技术企业。
二、企业在智能制造方面的现状
广汽传祺致力于打造世界级智能制造标杆工厂,其中宜昌工厂以世界级行业高标准打造,实现了生产自动化、信息数字化、管理智能化、智造生态化的有机融合。依托国家与集团整体数字化转型战略,2023年广汽传祺承接启动全面制造数字化转型,建立统一的智慧工厂平台,兼容多工厂数据,提升生产与经营水平。
广汽传祺智慧工厂分五个子项目推进,分别是:透明工厂项目、IOT工业物联网平台项目、智慧能源项目、设备预测性维护项目和AVI精准队列和生产指示项目。在智能制造技术应用方面:
(1)透明工厂
通过开发参观大屏和各层级管理可视化界面,提高生产过程的透明度和可控性。实现制造领域从管理层到执行层,从工厂到车间线边各层级生产运营管理可视化。
(2)IOT工业物联网平台
打通IT层与OT层,实现设备之间的互联和数据交换。实时监测设备运行状态,提高设备管理的效率和准确性。
(3)智慧能源管理
通过智能传感器实时自动采集水、电、气等能耗数据。实现对能源消耗的监控和优化,减少能源浪费,提高能源利用效率。
(4)设备预测性维护
实时监测设备的振动、温度数据。利用数据分析和智能预测算法实现对设备运行状态的监测和健康预测,提前发现设备故障和维护需求。
(5)AVI生产数字化指示
生成实时、精确的车身队列数据。实现拧紧管理、装配指导、质量门等功能,提升产品车的品质保证能力。
三、参评智能制造项目详细情况介绍
1、项目背景介绍
广汽研究院的的产品和工艺开发已有工艺数据平台,而广汽传祺端的工艺规划设计、工装开发、试制验证暂无工艺数字化平台系统,无法实现工厂端与其上游(研发)、下游(工装设备供应商等)数字化衔接,需要建设工艺平台来打通实现工艺从线下手工方式到全流程数字化的提升。
本项目梳理了工艺业务需求痛点,共有以下几大板块课题,包括数据安全、版本管理、数据查询、知识积累、工艺分析、设计变更、工艺账票等,从而推动了本项目规划和实施。
企业走访调研行业内其他工艺数字化平台建设经验,结合广汽工艺业务现状现状,规划广汽传祺的工艺数字化项目的总体目标。
工艺数字化平台主要对S/Q领域改善、C领域改善、数字化实现方面规划进行项目建设,本项目主要重点内容和方法是打通产品的数据流、数据管理、数字化工艺、离线仿真,优化工作流程和方法,从而提升工艺设计效率,提升工艺质量,降低设计成本,最终实现数字化转型和智能制造。
2、项目实施与应用情况详细介绍
项目的主要规划:
(一)搭建产品/工艺数据平台,实现唯一的数据源管理:
为了确保工艺设计与生产制造过程中的数据准确性和一致性,传祺需要构建一个高度集成的产品/工艺数据平台。通过特定的数据传输模式,确保接收数据的唯一性、准确性和时效性。工艺部门各专业可以实时访问、共享和更新工艺设计数据,避免了数据孤岛和信息不一致的问题,从而提升了整体的工作效率和工艺设计质量。
(二)构建焊装、总装、冲压、涂装等领域的结构化工艺BOP,统一研发及生产的BOP结构标准:
为了优化生产流程和提高工艺效率,系统在焊装、总装、冲压、涂装和尺寸领域构建结构化的工艺BOP。这些BOP包含了每个工序的操作步骤、材料、工装设备、质量标准等信息,以结构化的形式进行村存储和管理。通过标准化BOP结构,可以提高工艺文件的复用性,以及不同专业之间的有效沟通和协作。
(三)构建产线数字化资源库,提高工装设备的重用率,为资源库的建设奠定坚实基础:
为了充分利用现有的工装设备资源,降低生产成本和提高生产效率,系统将构建一个全面的产线数字化资源库。资源库将收录所有工装设备的详细信息,包括型号、规格、使用工位、对应车型、存放位置等,通过数字化手段进行管理。工艺工程师能通过访问资源库以快速找到所需的工装设备,提高设备重用率。而且资源库能作为工装设备维护和升级提供数据支持,确保资源库的持续优化和更新。
(四)平台化工艺分析,焊点、基准分配及工艺文件:
系统采用平台化的工艺分析方法,可以快速导入和分析产品设计数据,生成焊点布局、基准分配等关键工艺参数;可以根据预设的规则和模板,自动生成详细的工艺文件,包括工序流程图、作业指导书、检证标准等。工艺分析和文件生成功能大大缩短工艺准备周期,提高工艺文件的准确性和一致性。
(五)实现工艺账票自动输出,直接传递至生产现场,提高生产执行效率:
系统实现工艺账票的自动输出功能,可以将工艺账票以电子形式直接传递至生产现场的设备或终端上,供一线员工查阅。这种方式可减少工艺账票人工传递和打印的成本和时间,提高了准确性和可追溯性。
项目实施的主要思路:
当前汽车产品设计阶段基本实现了数字化设计,制造阶段也大量采用自动化设备和生产管理系统等数字化手段,为了更好地衔接设计与制造,许多主流主机厂(如长安,吉利、长城、东风、奇瑞、上汽、一汽、北汽等)都应用数字化工艺,并取得一定的收益。本项目通过对标长安工艺数字化项目规划,最终选定采用西门子的TC平台作为本项目的主体系统。
系统建设主要功能:
(一)系统主要架构
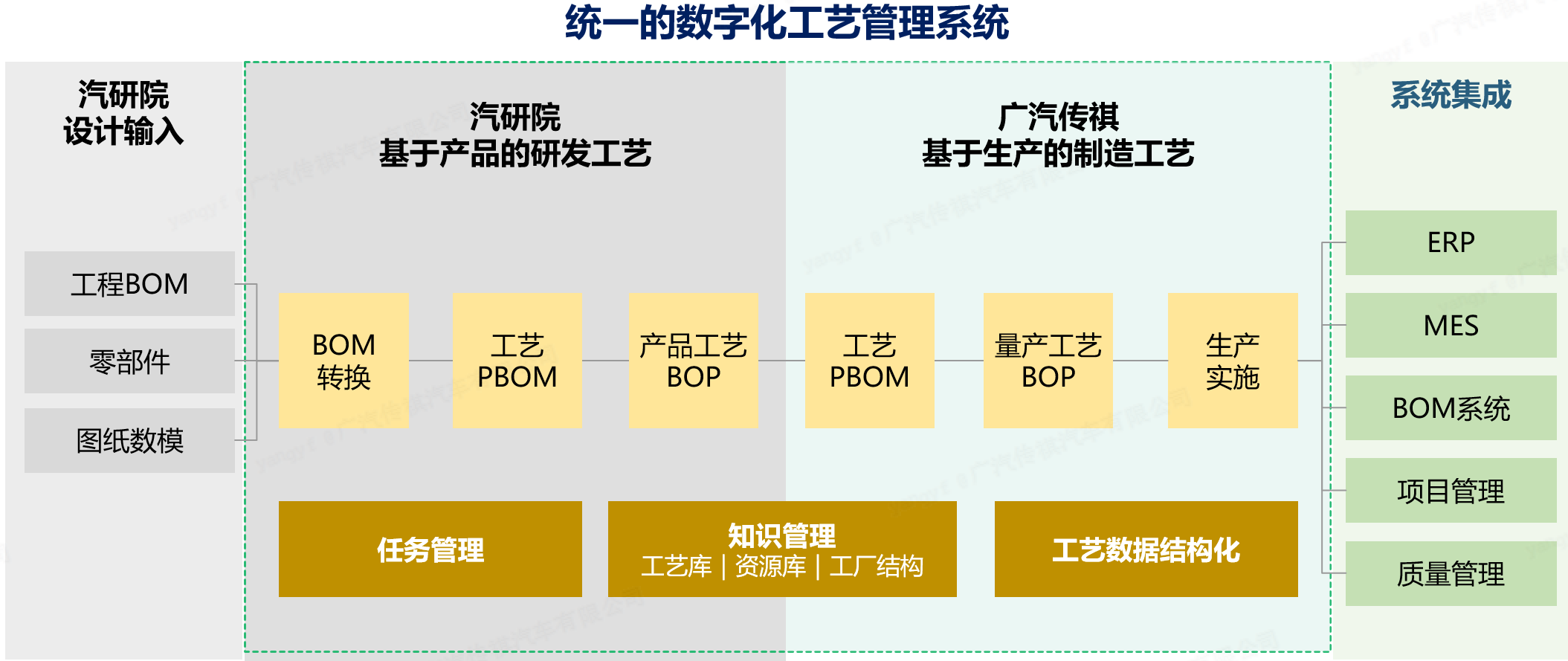
图1.系统的主要架构
(二)设计数据接收及更新功能
①课题:无统一的数据源,线下手工U盘拷贝/多渠道数据获取途径。工艺人员通过线下手工的方式获取车型产品数据;各工艺员用PC保存车型数据,协同效率低,安全风险;没有形成一台套的完成的工艺数据。
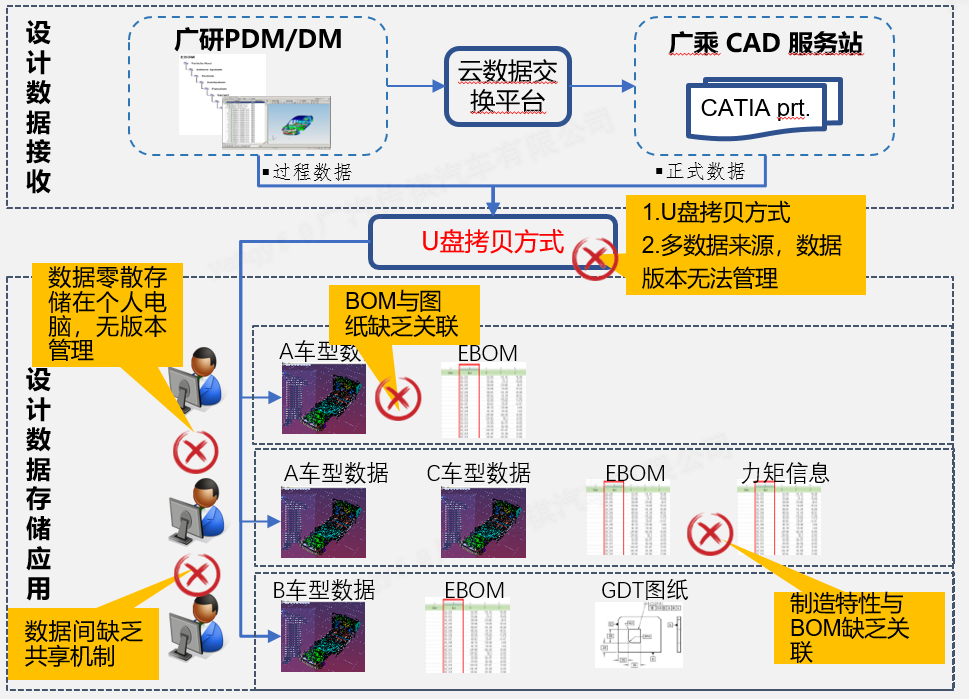
图2.设计数据接收课题
②解决思路
统一规格为车型产品数据接收唯一窗口;
完成BOM与CAD数据关联性管理;
基于统一数据平台进行数据轻量化查看。
③解决方案/系统功能:统一数据接收窗口/系统自动获取数据。保证了数据版本及时更新可控,上下游数据唯一性;减少因数据不一致导致的设计变更;统一平台管理数据,大幅提升数据管理安全。
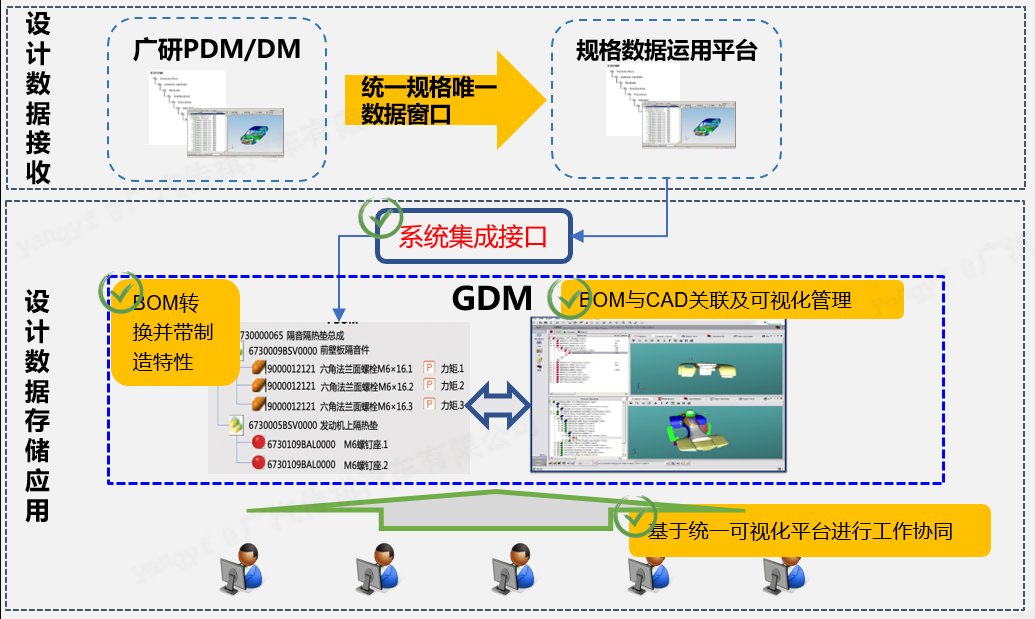
图3. 统一数据接收
(三)工艺结构化管理(PBOM、BOP构建)功能
①课题:无系统支撑,工程师依据CAD以及经验,使用EXCEL进行工艺规划编制。工艺部门无工艺BOM,同步工程阶段仅能够实用CAD BOM(设计BOM)进行基础检证,该BOM仅有基础产品信息,无相关工艺信息,且缺乏工艺结构,以该BOM进行工艺规划耗时长,精度差;工艺规划使用excel表格人工编辑,效率低且重用性差;工艺规划无统一信息来源,需多方收集数据整合,团队协作性差。
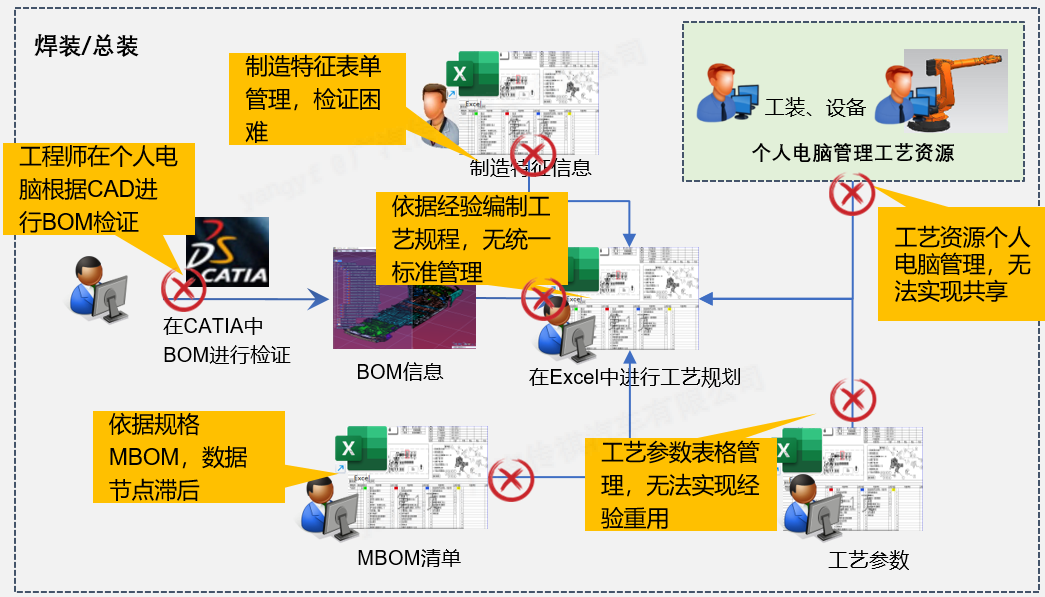
图4. 工程师依据CAD以及经验进行工艺规划编制
②解决思路
搭建工艺结构化PBOM管理机制,并承接研究院BOM制造特征,提供可视化BOM检证平台;
搭建结构化BOP管理机制,实现产品、工艺、资源、工厂关联的协同作业模式;
搭建工艺资源库,提升工艺规划协同过程效率与质量。
③解决方案/系统功能:基于同平台协同完成工艺规划工作。基于同平台构建工艺专用BOM及工艺规划,数据来源统一,规划精度高,团队协作性高;数据来源自动接收及转化,工艺规划效率高;知识资源统一平台管理,重用性高。
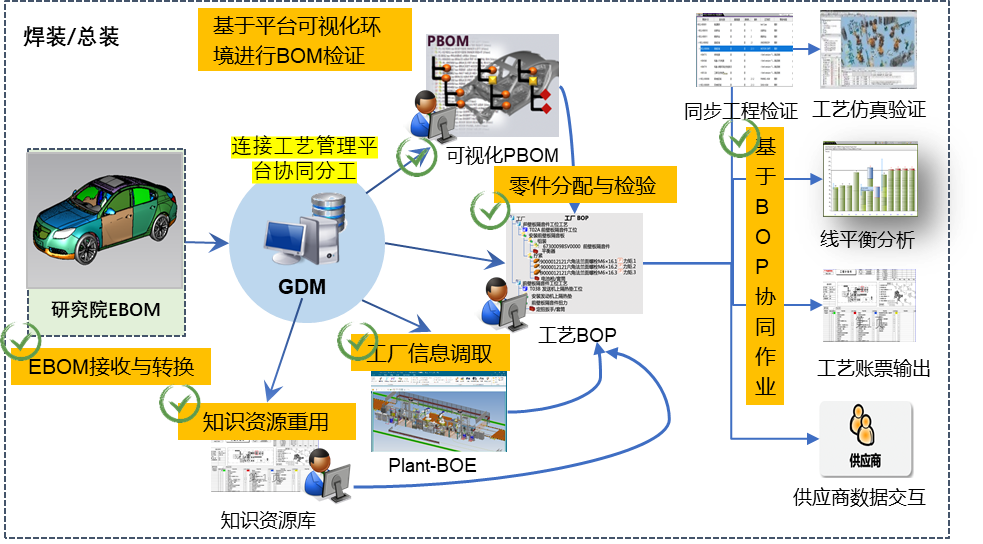
图5. 基于同平台协同完成工艺规划
④现场效果
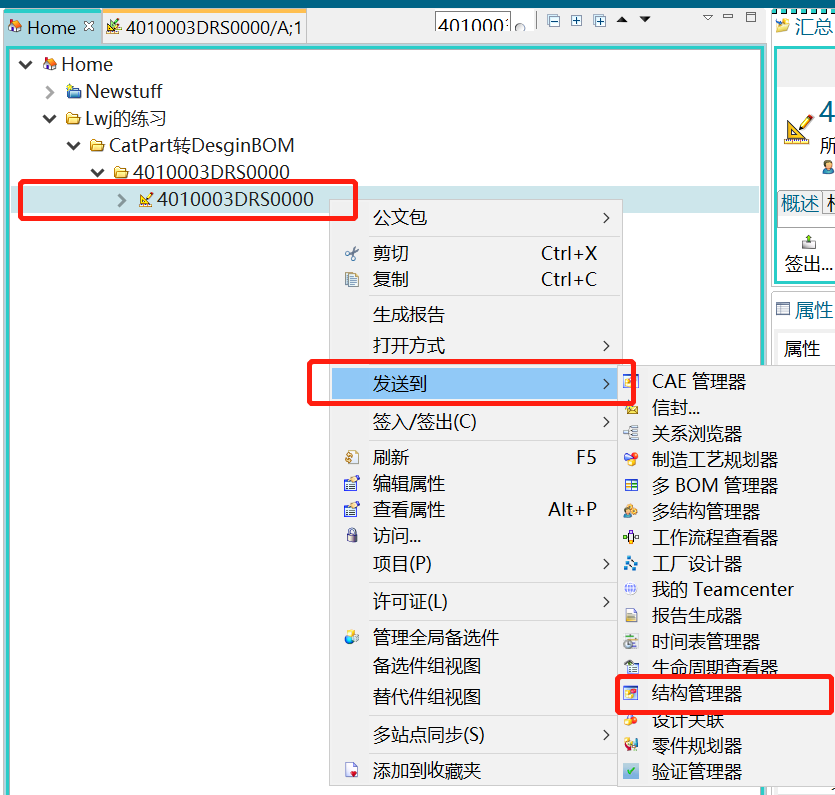
图6. 工艺BOP结构管理器
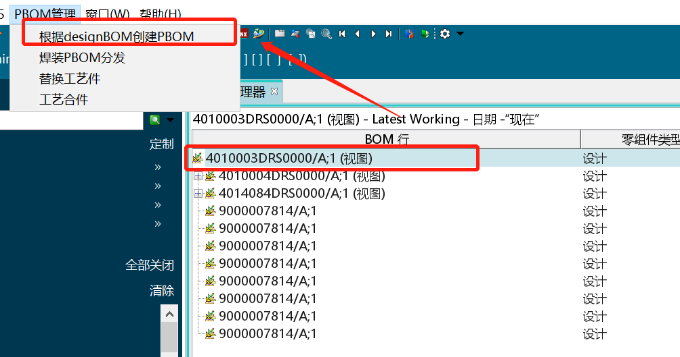
图7. 设计BOM转换PBOM
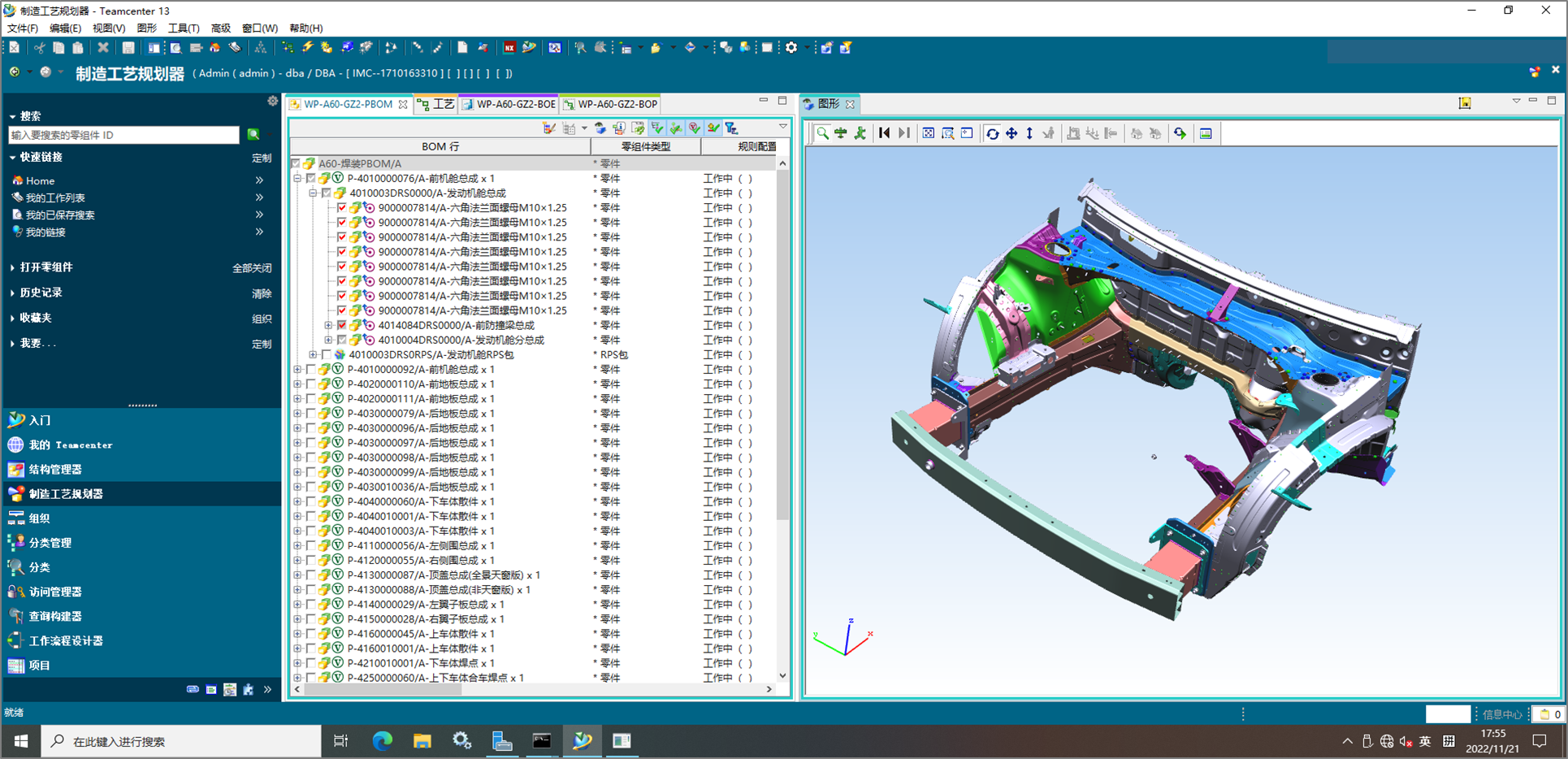
图8.转换后得到的PBOM
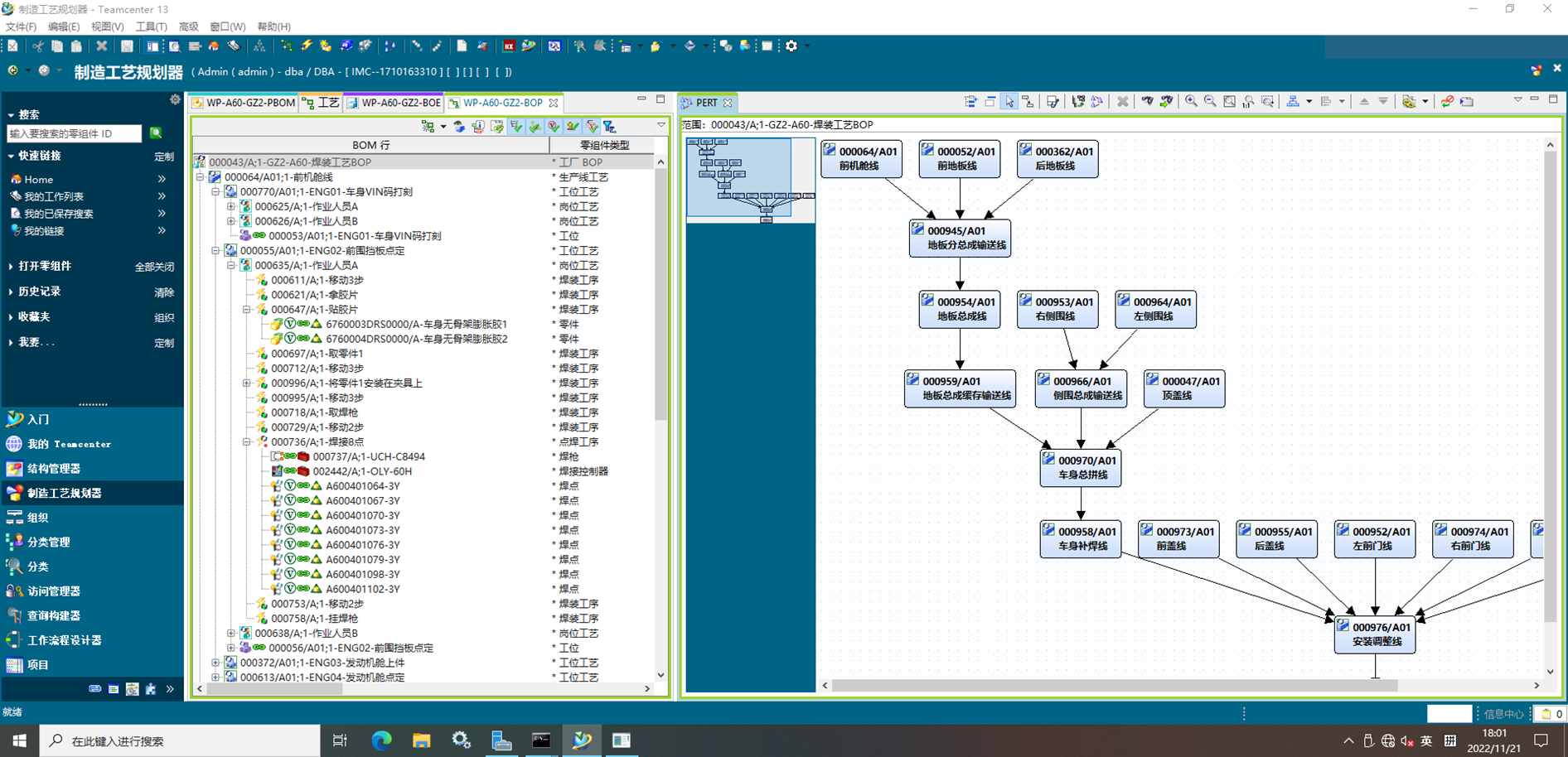
图9.工艺BOP搭建与更新
(四)焊点管理、RPS设计高效实施
①课题:焊点管理对比难度高,白车身RPS设计效率低下。焊装领域通过离散小程序到处焊点表格,线下人工对比差异;尺寸领域使用专用软件进行RPS基准设计,设计涉及白车身所有点定工位,且各工位基准无法重用,需逐个涉及;尺寸领域设计RPS基准时,当前端数据变更后,RPS基准变更需逐个相关工位进行确认,易造成缺漏,引起设变。
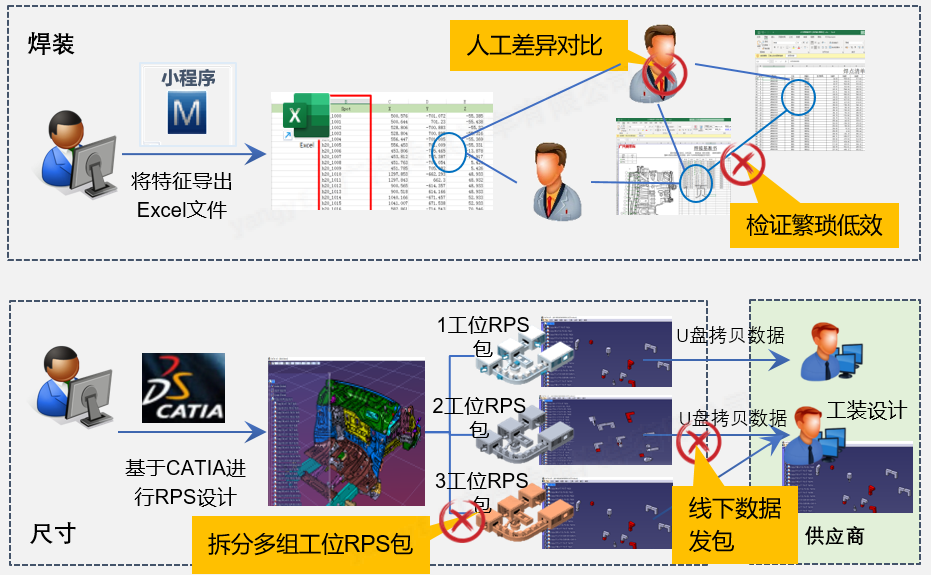
图10. 焊点管理对比难度高,白车身RPS设计效率低下
②解决思路
通过CATIA程序快速将焊点特征转为系统识别的模型;
基于NX进行高效RPS设计,跟随尺寸设计变化而更新;
③解决方案/系统功能:开发程序焊点特征转模型,基于NX的RPS快速设计联动更新。通过程序开发实现焊点特征转模型,避免数据错误,降低人工差异对比工时约5%;基于工艺平台标准设计功能高效完成RPS设计,可关联同属性工位同步设计,数据变更引起设计更改时可快速关联更改,预计提高开发效率30%。
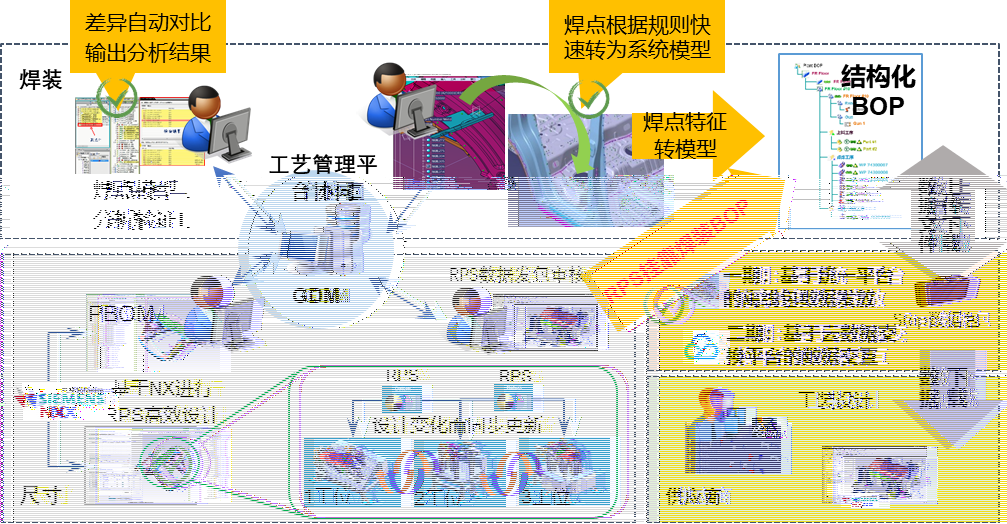
图11. 开发程序焊点特征转模型,基于NX的RPS快速设计联动更新
④现场效果
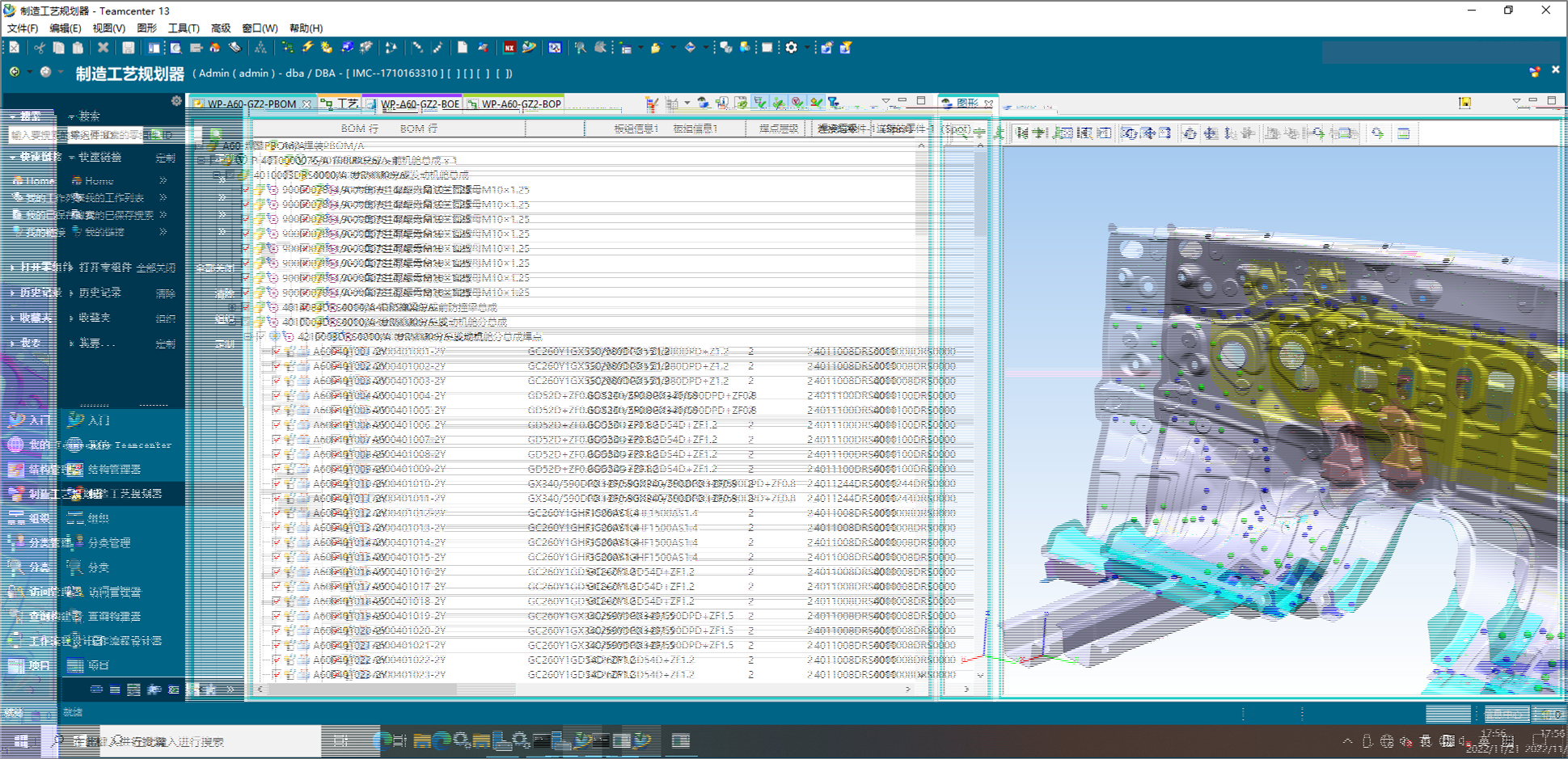
图12.结构化焊点模型
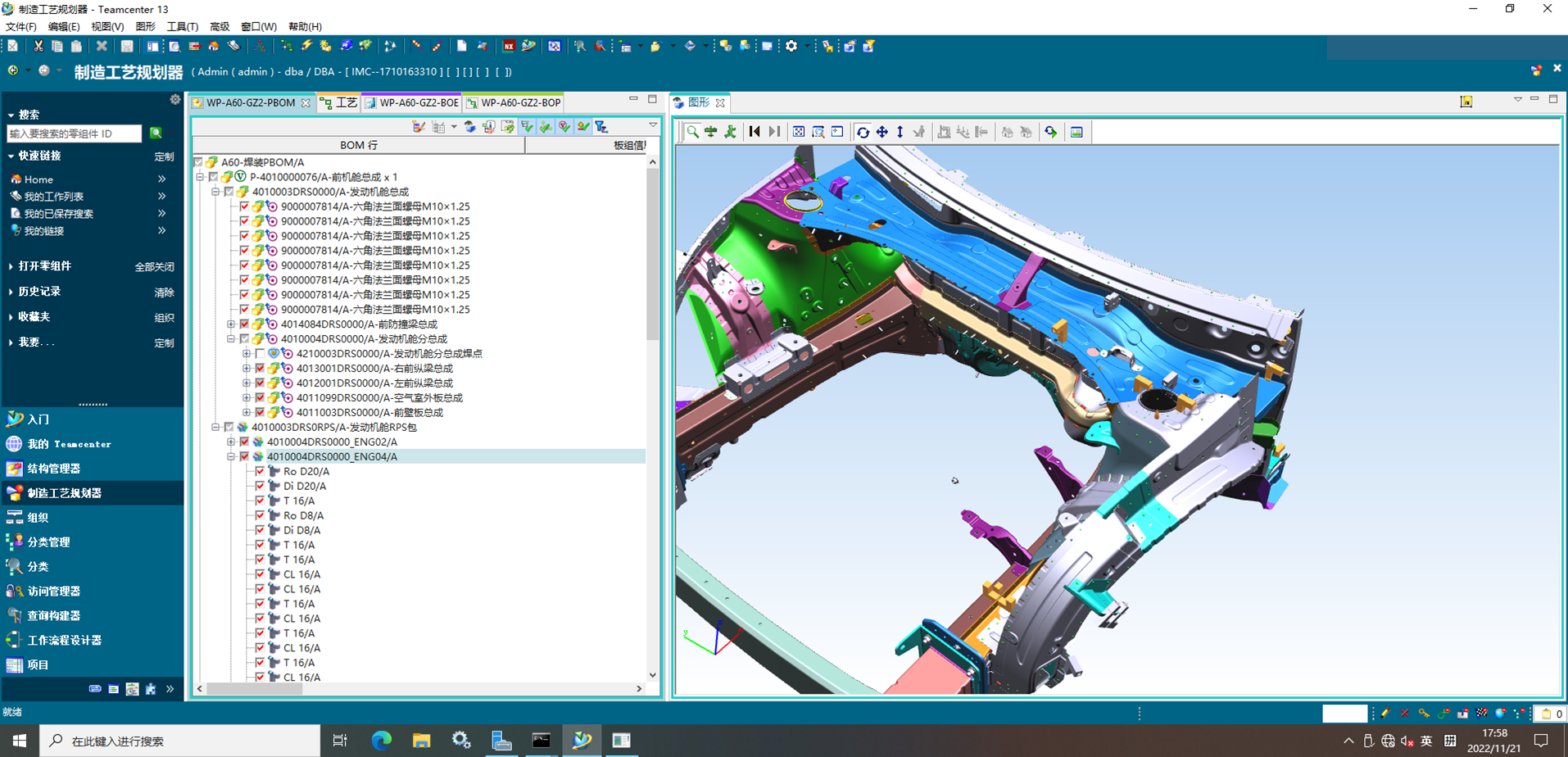
图13. RPS关联同属性工位同步设计
(五)同步工程检证
①课题:纸质检证清单,个人单独检证,协同效果差。工程师各自采用检证清单进行检证确认,检证清单版本存在差异风险,造成检证质量不合格;参照检证清单不同,各工程师间协同质量低,存在重复作业或检证漏项;过往知识经验无法重用,完全依赖工程师个人经验;采用纸质清单检证,异常追溯难度较大。
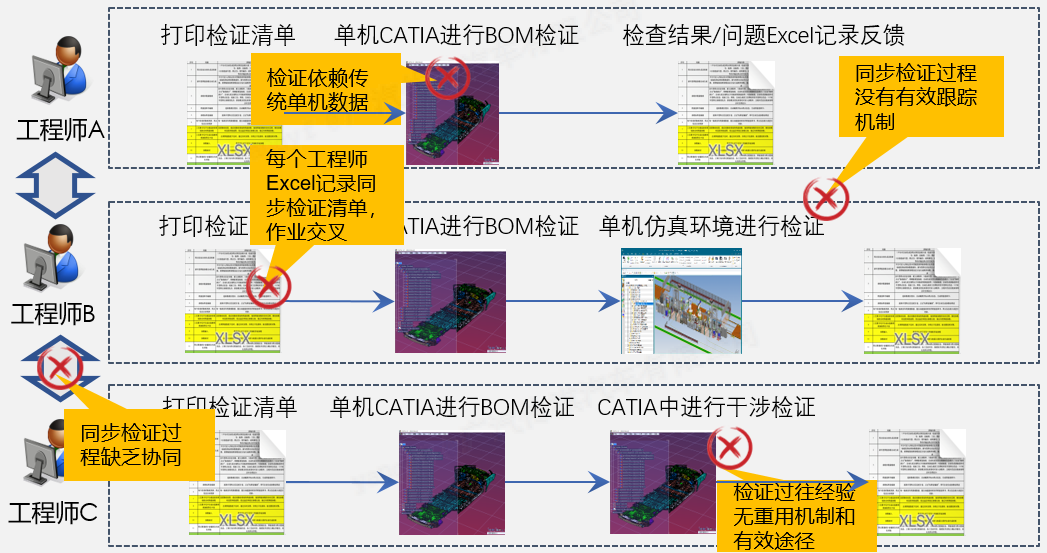
图14. 个人单独检证,协同效果差
②解决思路
基于同一检证清单实现检证协同工作、检证进度及结果透明化管理;
基于可视化或仿真集成进行快速检证验证;
通过对检证内容快速发起ECR并同步至研究院;
③解决方案/系统功能:基于系统化Checklist检证,快速发起检证、仿真及设变。所有工程师均基于统一checklist进行同步工程检证,检证质量提升5%;过往知识经验可随时调用,重用率高;结构化checklist,检证一项关闭一项,工程师协同效率提升10%,降低重复作业、漏项风险;系统化管理,异常追溯方便快捷。
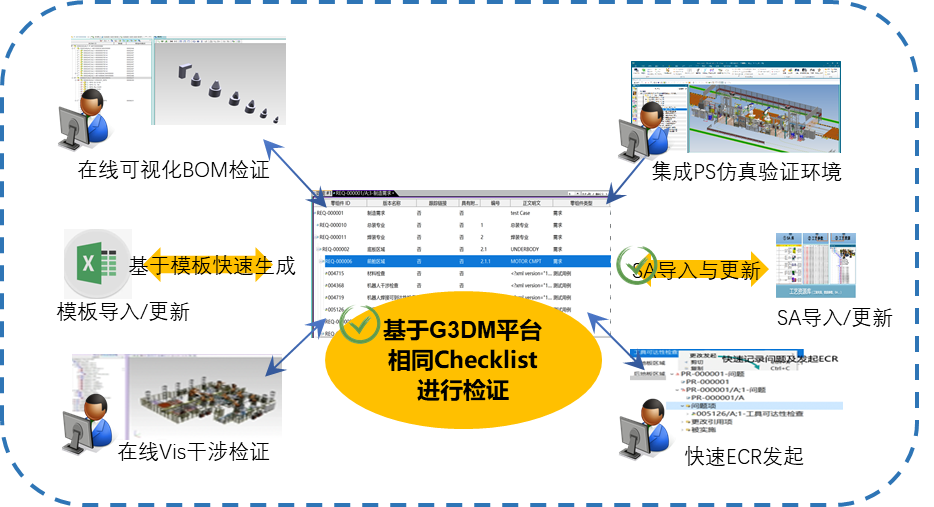
图15. 基于系统化Checklist检证,快速发起检证、仿真及设变
④现场效果
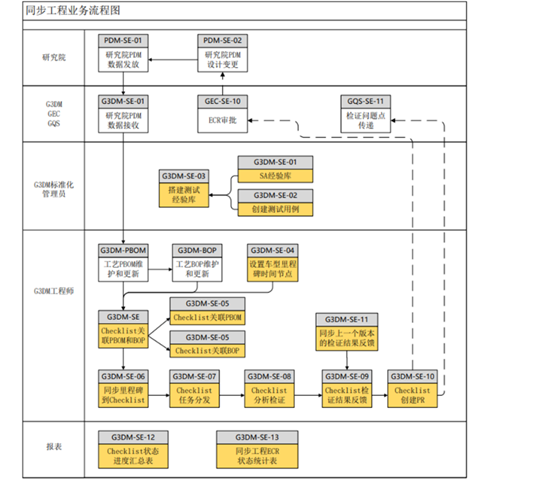
图16. 同步工程流程
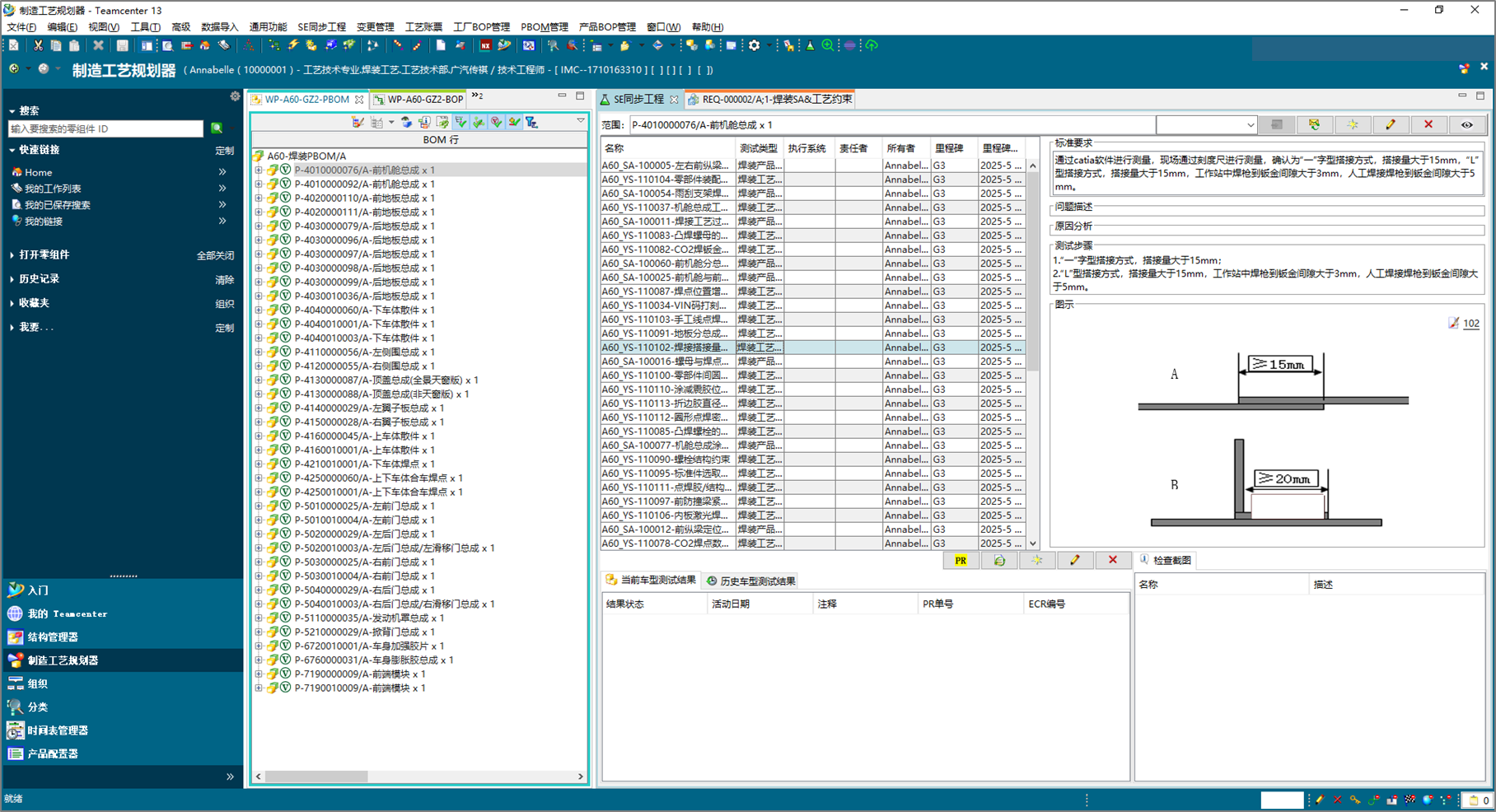
图17. 同步工程SA及工艺约束清单
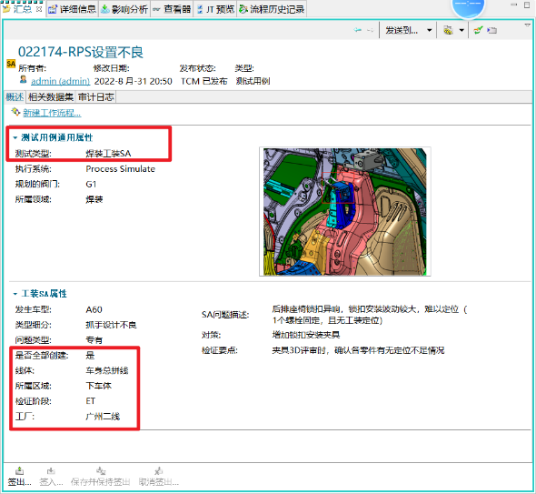
图18. 同步工程Checklist创建
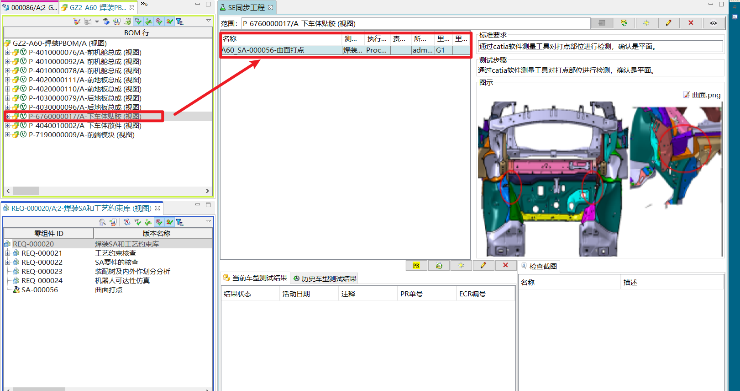
图19. 同步工程Checklist创建完成
(六)基于结构化BOP的工时管理
①课题:线下编制工时以及手工汇总评估。岗位工时通过人工经验编制,缺乏统一基准;工时统计、分析、调整均为人工手动调整,调整耗时长;工时分析文档通过传统方式传递,调整后无法与工艺一致。
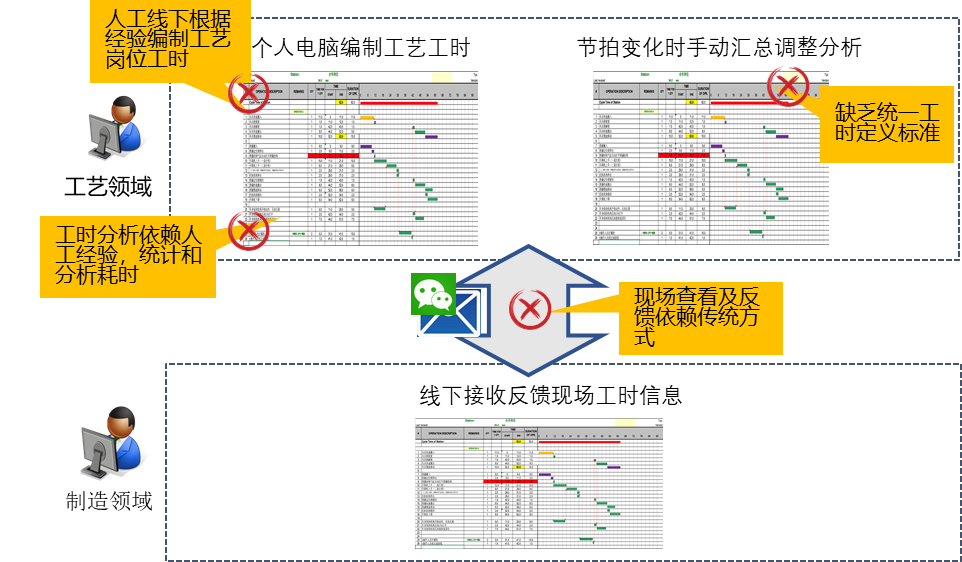
图20. 线下编制工时
②解决思路
通过建立标准工时库,实现工时标准化管理;
通过BOP实现快速仿真验证;
基于BOP实现工时自动汇总分析、以及岗位工时快速调整;
③解决方案/系统功能:标准工时管理,同时实现基于结构化工艺工时评估。建立统一标准工时库,整合工艺、生管、制造领域工时核算依据;基于结构化工艺自动实现工时汇总、报表输出,预计节约工时10%;可通过拖拽方式实现岗位工艺分配,快速匹配生产线各岗位工时平衡;制造端通过客户端查看、修订工时,实现多领域协同维护;
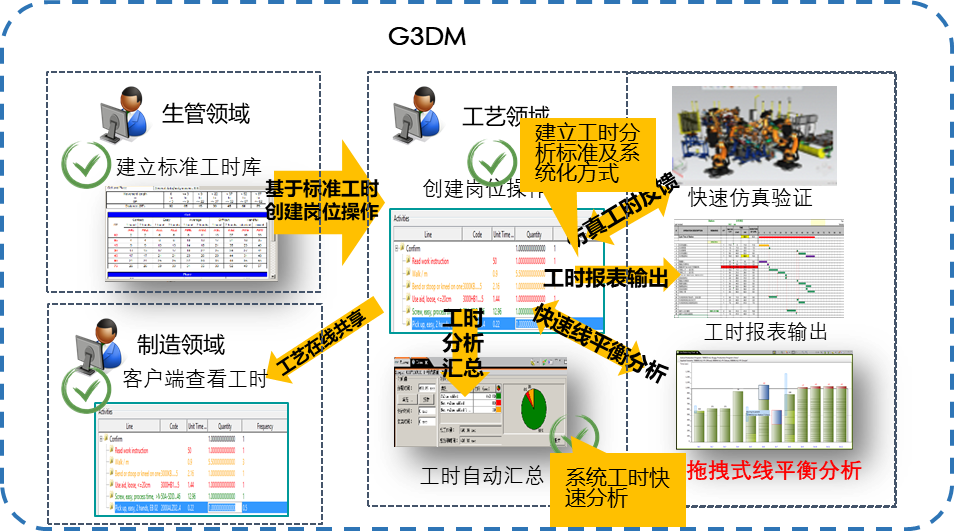
图21. 标准工时管理
④现场效果
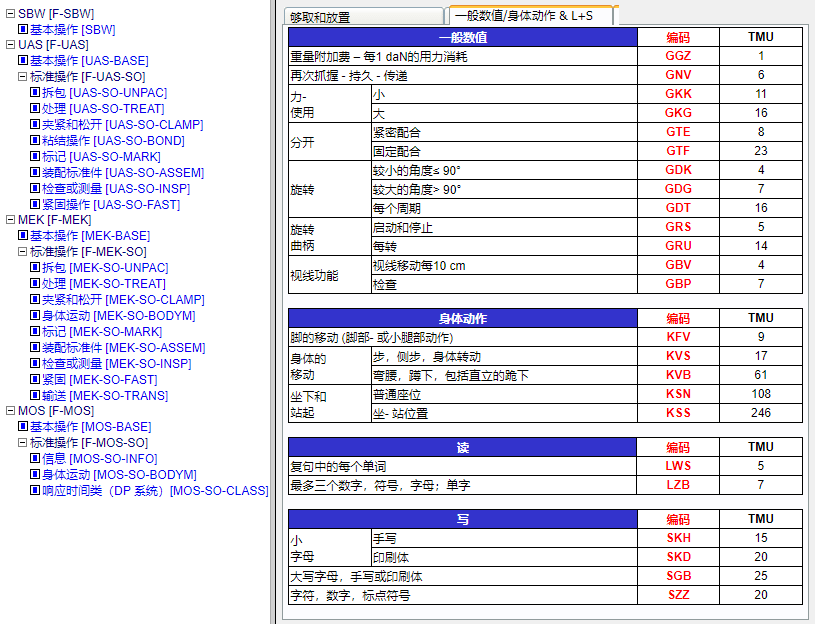
图22. 标准工时管理
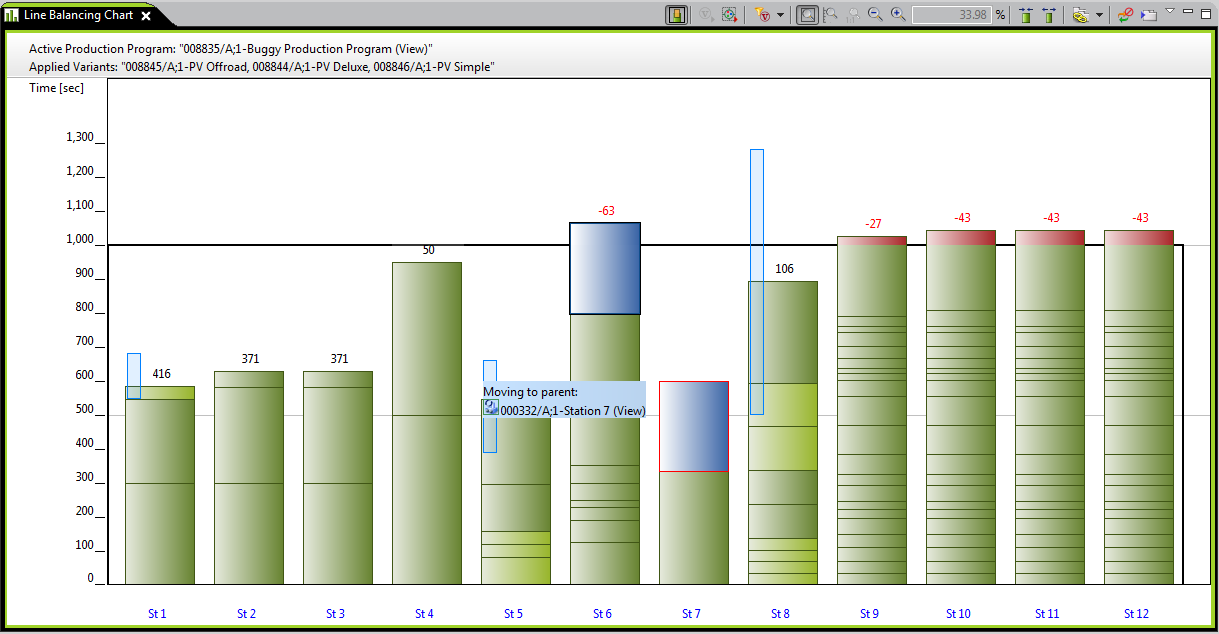
图23. 生产线平衡
(七)工艺账票自动输出、审核发布&直达现场
①课题:账票线下人工编制与更新维护,并人工同步至现场。手工制作工艺账票,人工核对确认,耗时耗力;线下审批确认,签批周期长;资源数据缺少统一关联管理,查阅需在各个不同平台进行查看调用。
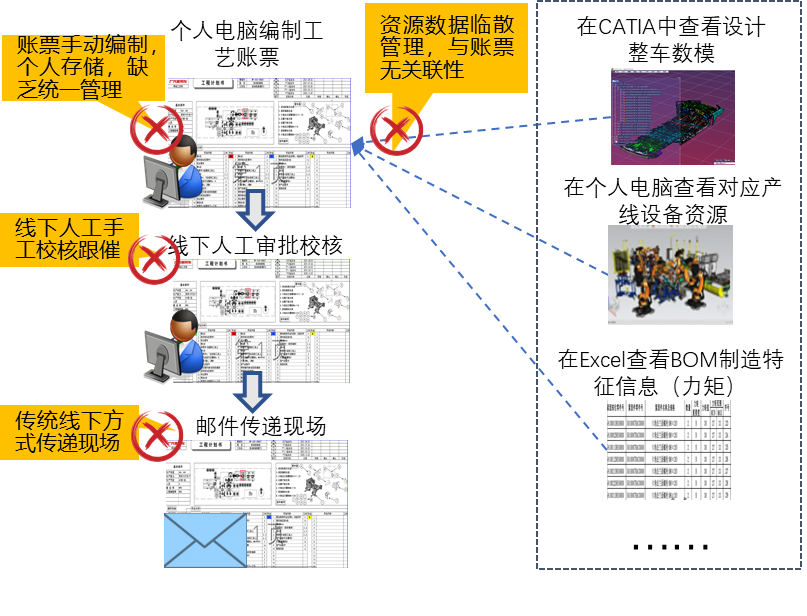
图24. 账票线下人工编制与更新维护
②解决思路
根据工艺BOP结构快速输出工艺账票,并实现在线签审;
通过与现场设备集成,将工艺账票传输至线边指示。
③解决方案/系统功能:系统辅助输出账票,并与现场打通直达现场。基于从研发-工艺-制造现场的数据流,结构化工艺信息自动生成账票,输出精度高;系统自动生成工艺账票,人工维护工时低,工时节约20%;系统内电子签批,签批效率高;知识资源库承载所有需求资源,可同平台直接查阅复用。
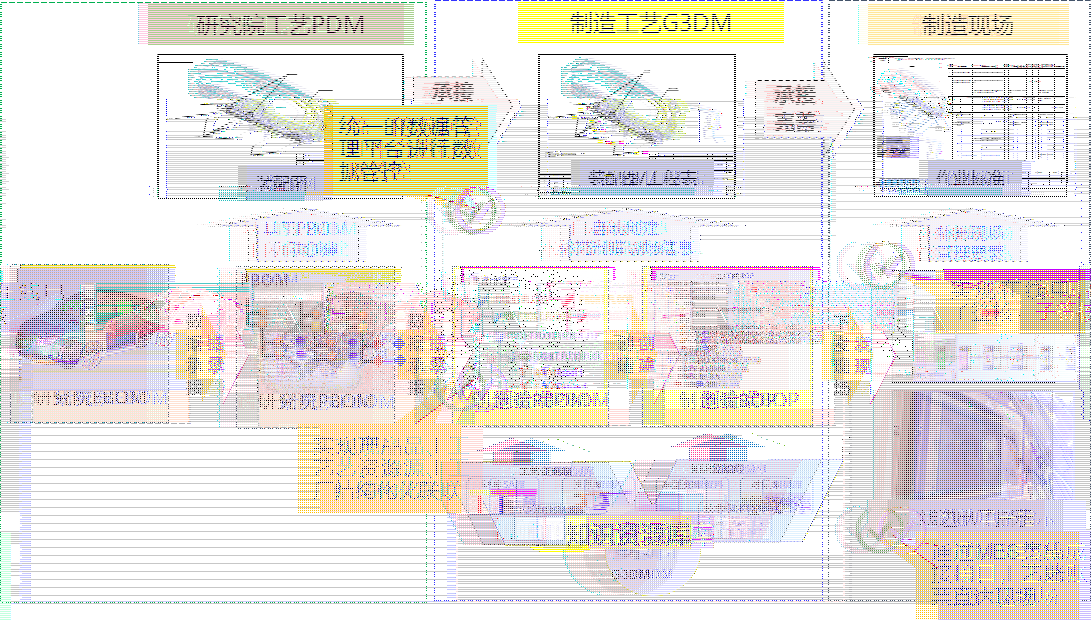
图25. 系统辅助输出账票
④现场效果
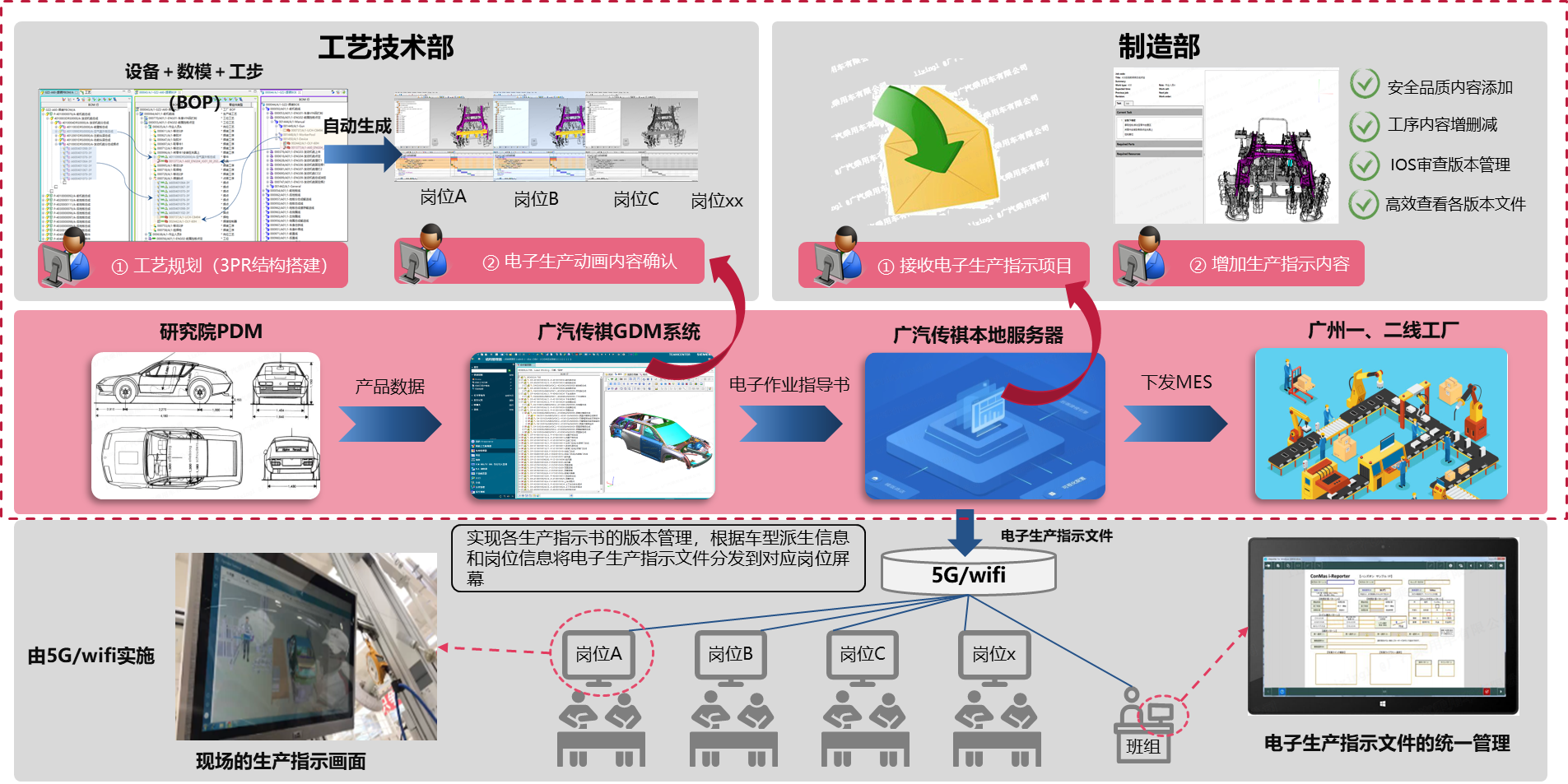
图26. 直达现场
.
图27. 线边电子指示
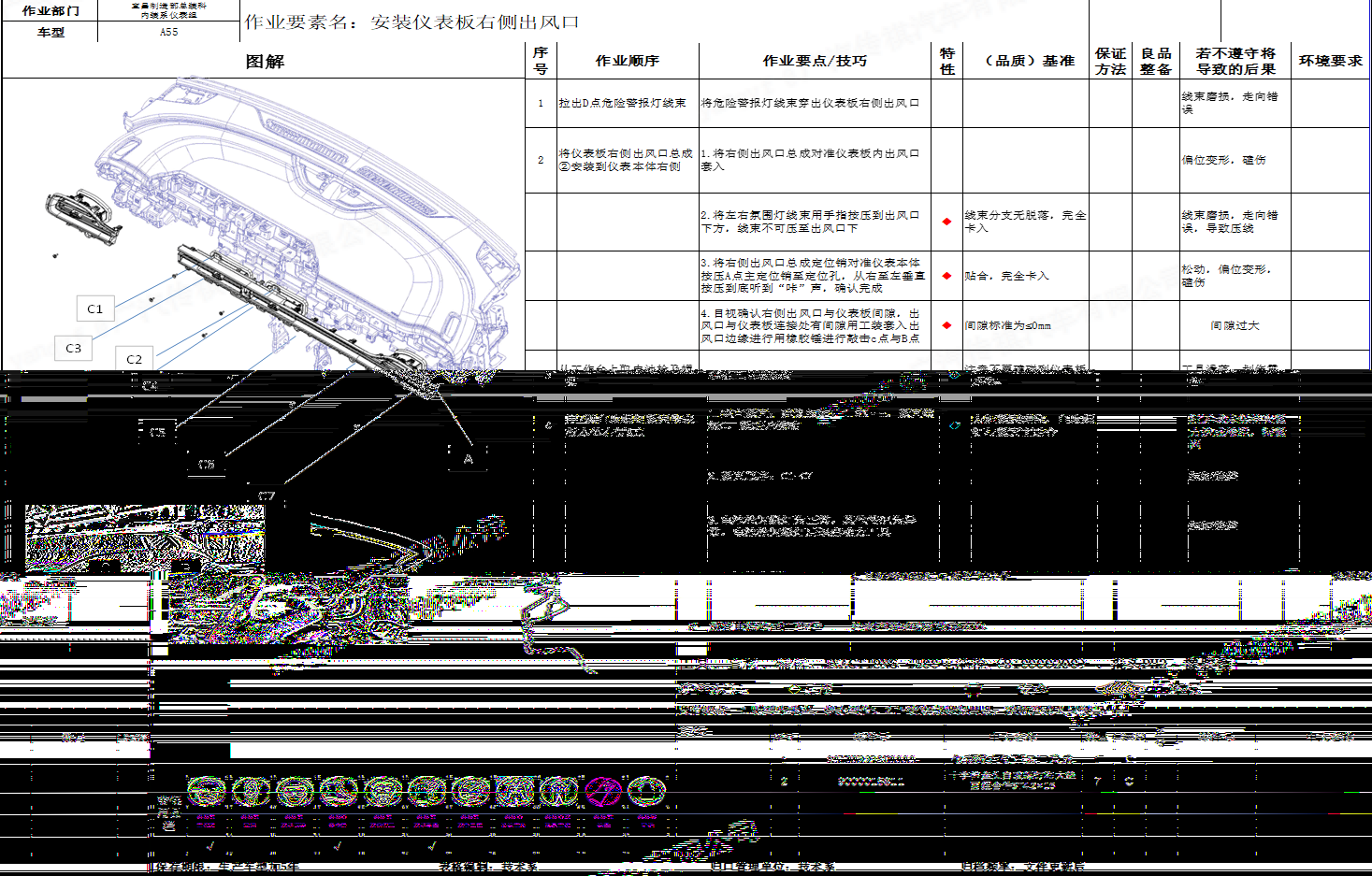
图28. 实现在线电子签核
3、效益分析
①系统自动生成工艺账票,人工维护工时低,工时节约30%;系统内电子签批,签批效率提高约20%;践行无纸化办公,下发效率提升20%;
②促进产品优化(VAVE),减少后期设变投入,预计可节省120万/车型/年;
③提高工艺工装重用率,车型平台化策略实施率提高到20%-95%;同线体同平台车型投资预计削减200万/车型。