有限元分析(FEA),对于设计而言,是非常有必要的手段。通过电脑辅助计算,能够使设计师提前评估设计结构的合理性,大大缩减了设计的成本。Solidworks(以下简称SW)的simulation插件为设计者提供了静应力、频率、热力、屈曲、疲劳、非线性、线性动力、跌落、压力容器等各种分析计算功能。而静应力分析,在机械设计中占了很大一部分比重,本文通过事例演示使用simulation静应力分析,需要注意的问题。
静应力分析步骤:将实物转化成简单模型(零件或装配体)—被分析物体(以下简称“模型”)材料的选择—待分析模型单元类型确定(实体,壳体,梁)—连接(装配体)—夹具固定选择—添加外部载荷(力,力矩)—对分析物体进行网格划分—运行分析—求解后处理—查看图解—对结构进行优化设计。
其中材料,夹具,连接,外部载荷,网格等为软件所列步骤,操作无先后顺序。可根据实际需要,逐个设置。
如图1,汽车在立体车库车道上行走,分析车道的受力大小和对车库单元的材料优化。汽车重量以2吨计。
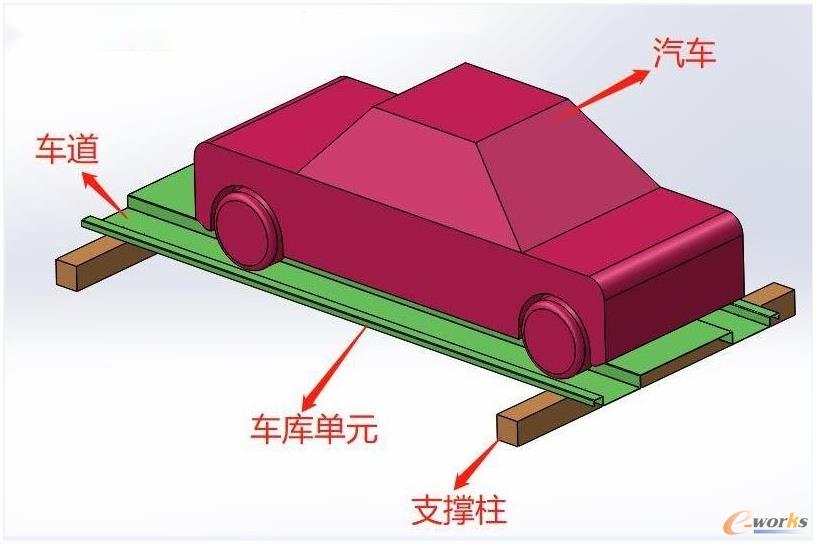
图1 模拟汽车驶入立体车库道
一、将实物转化成简单模型(静应力分析前的准备)
①将动态力学转化成静态力学:通过所学的物理及力学知识,汽车在车道上行走时对车道力矩最大的作用点应该是前轮在车道中点(相对于车库单元的两支撑柱),如图2。此时单个前轮对一侧车道中点作用500kg力(计5000N)。
②对称模型简化(以下简称简化切除)
条件:1.模型的几何条件对称;2.模型的材料对称;3.施加的边界条件对称。
目的:减少网格划分和分析求解时的计算量,降低对电脑的硬件要求。模型简化切除,对分析结果基本没有影响(但会有误差)。(如模型非对称,则可跳过此步骤。)
图3中将车库单元一分为二:a,b。其中a,b符合模型几何对称,材料对称(暂定车库单元用4mm钣金折弯),受力对称。故将车库单元沿中心面切去一半(1/2切),若模型为圆柱体,则在满足上述条件时,可1/2切,1/4切,1/8切等。图4为被1/2切后的车库单元。
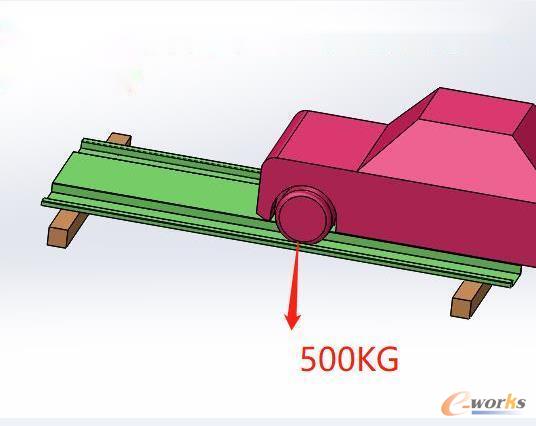
图2 将汽车的动态力学转换成静态力学分析
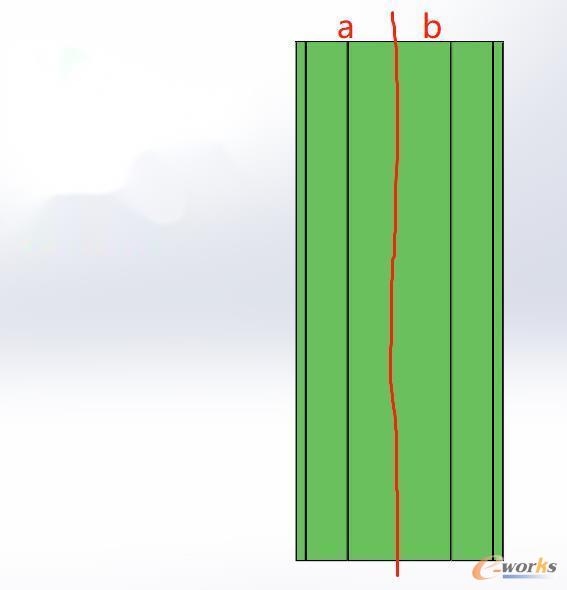
图3 车库单元以a,b两部分几何对称
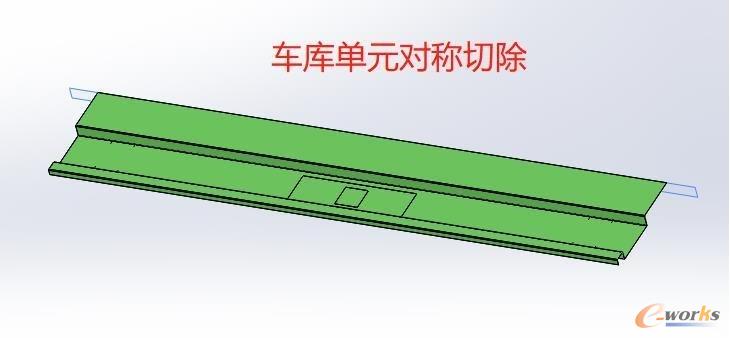
图4 车库单元对称切除
激活simulation 点击新算例,选择静应力分析。
二、模型材料的选择
此模型材料为4mm厚普通碳钢,折弯而成。力学性能类似Q235,如图5。
(在做轴类零件分析时,如轴有热处理,则材料选取有相应标识热处理的材质,如正火,调质等。若SW软件中没有对应材料,则可通过输入弹性模量,中泊松比等参数,自定义添加材料。)
模型分实体,壳体,梁这3类。实体可以是轴,厚度不一的各类零件,由实体建模生成。壳体为曲面,钣金生成。焊件对应梁单元(槽钢,角铁等型材)。但这个没有绝对,无论是哪种建模方式,只要建立出来的模型满足我们使用某种单元进行划分的要求,那么就可以使用那种单元划分。例如小件钣金,某些曲率半径大于数倍厚度的钣金件也可以用实体划分单元。用哪种单元划分网格的初衷是减少电脑计算量,并不改变分析结果。
此车库单元若以实体划分网格单元(可以用实体划分),4mm板厚与5000mm长度相差过大,中间的过渡网格将会消耗大量计算,所以将车库以壳体进行划分。
图5 选取与实际工况相符的材料
三、将由钣金建模而来的车库壳体化操作
方法A:返回零件的模型界面,点击“插入→曲面→中面“,再依次点击车库(4mm钣金件)的同一部位的正反面,如图6示。
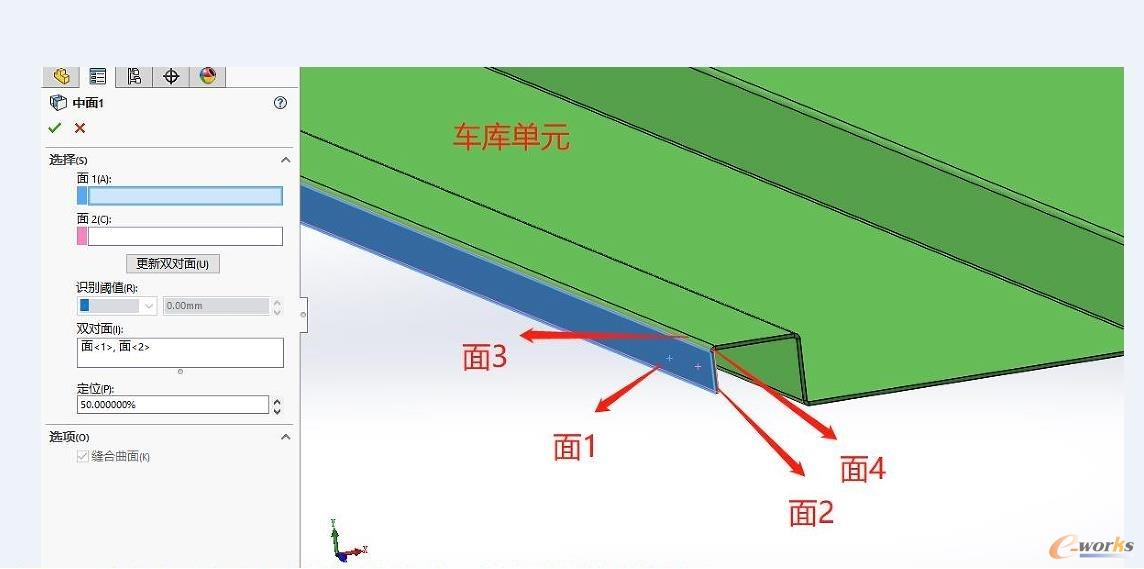
图6 为插入的中面指定材料同一处厚度的正反面
将车库的所有面依次点击,打钩确认后,此车库的中间曲面即可生成,为后续划分网格做准备。
方法B:在静应力分析界面,右键单击模型名称,选中“按所选面定义壳体” ,如图7所示完成操作,曲面生成,待网格划分。
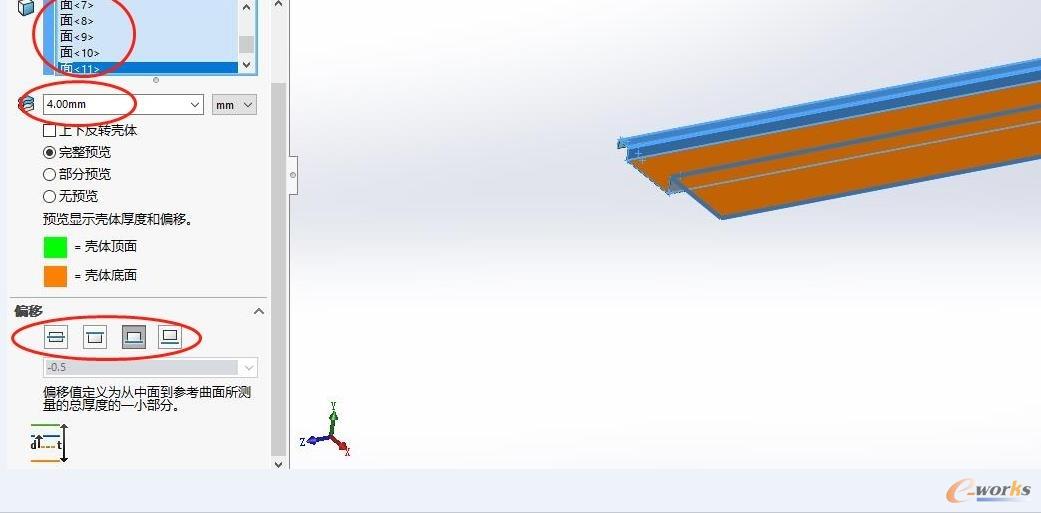
图7 在静应力分析界面
四、连接
因为是零件,没有与别的零件配合,所以此算例里可以忽略。具体用法见下文的装配体分析算例。
五、固定夹具的选择
右键单击夹具,按需选择不同的夹具类型。夹具选择要根据模型在实际工况中所受的约束,不能随便简化或漏选,少选。错误的夹具选型会造成分析计算的失败或结果的错误。
在对分析模型做的简化切除中,“切到”的所有平面或边线(曲面)均需高级夹具固定,根据不同的切法(1/2,1/4,1/3)选择不同的高级夹具,如图8示。
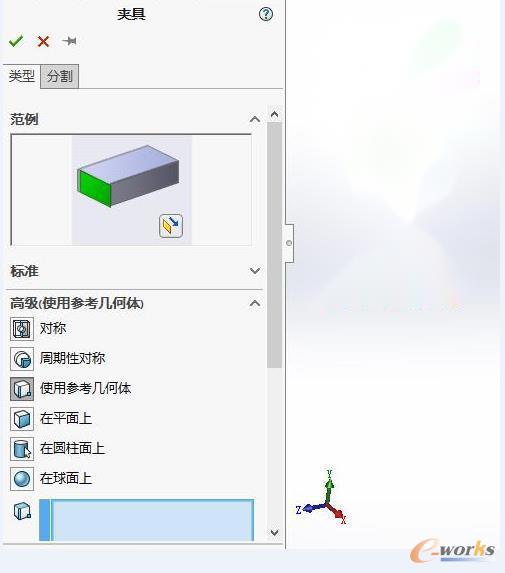
图8 “夹具”步骤里选择合适的高级夹具
“在平面上”适合实体切除时使用,在其下面对话框“夹具的面”选中被切到的所有面。在选中所有平面中的一个平面时,软件会预览显示被切掉的另一部分模型。这会一定程度上造成漏选剩余平面的假象。“在圆柱面上”亦可用在圆形曲面的切除中(选择圆柱面轴)。
此算例中(车库受力分析),选取“对称”高级夹具,选中车库被切到的平面,对车库的简化切除(1/2)做夹具约束。这只是对分析对象做简化计算,不影响分析结果。
此算例中,还需对车库两支撑柱处做固定,因为支撑柱与车库是焊接连接,在去掉支撑柱后,该固定形式可简化成普通夹具,选择固定几何体即可。选择的平面为支撑柱与车库的相交面(暂定200*200)。
相交面的生成:在零件的模型界面对零件做分割线处理,或者在夹具对话框选分割一栏,按提示完成分割线处理,图9示。
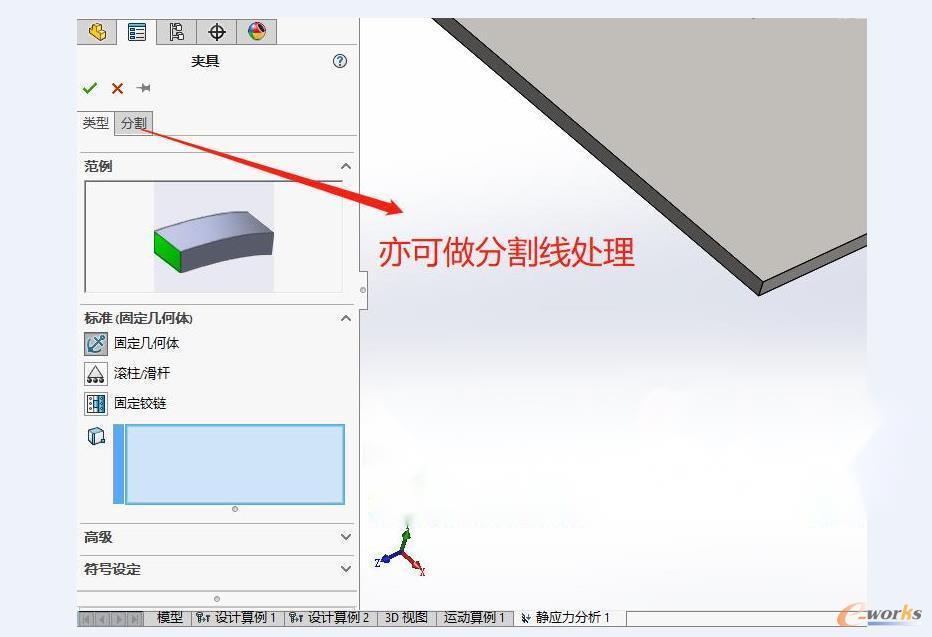
图9 在零件的模型界面对零件做分割线处理
六、外部载荷
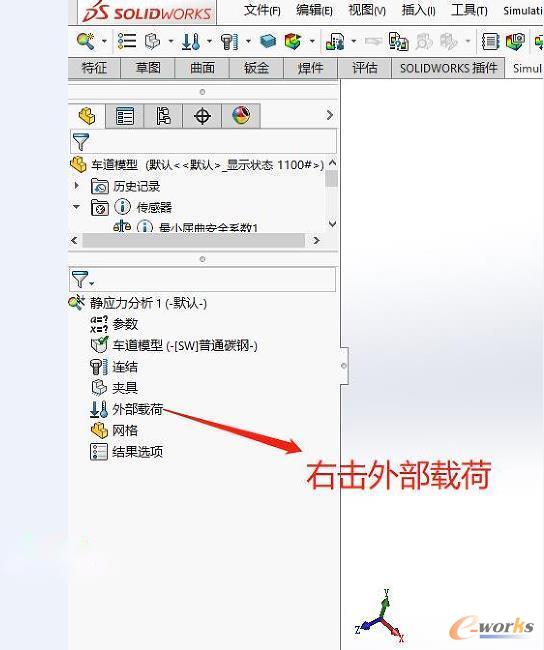
图10 外部载荷
右击外部载荷,按模型受到的实际力,选取轮胎对车道5000N的力和本身所受的重力(引力),图11示。
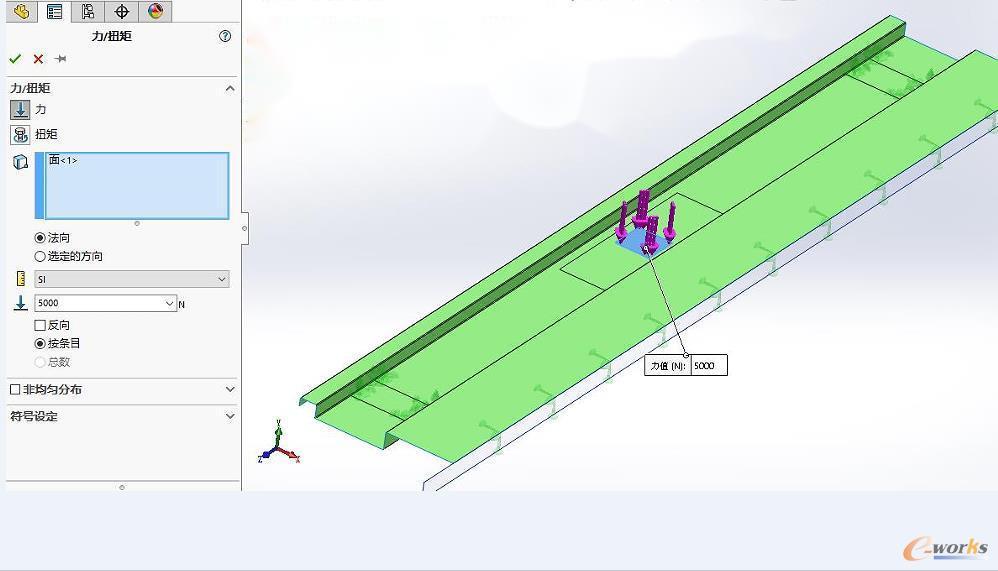
图11 根据工况,指定外力对车道的作用
此算例中,力的大小输入为5000N,选择按条目。
按条目:为一处作用点的力大小。
总数:各处作用点力之和。
即,如果有2处作用点,选择“按条目”,力大小输入5000N的话,力的总大小为10000N。
七、网格的划分
网格划分要求控制好网格的精度。网格过于精细,计算量成倍增长,耗时;过于粗糙,分析结果误差会加大。在对模型做整体网格化时,simulation允许在模型局部进行网格化控制。右键单击网格,在弹出菜单栏选应用网格控制,对重要区域(关键受力点)做单独网格控制。
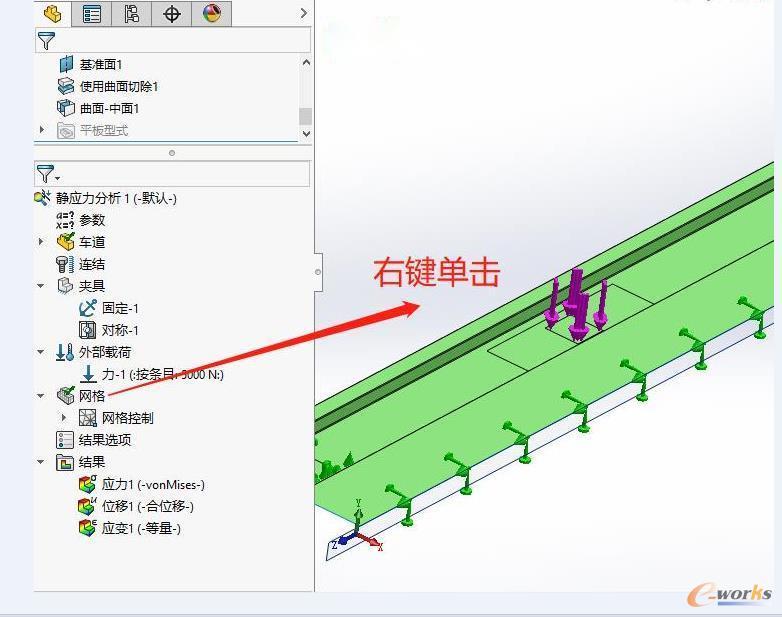
图12 对重要区域做单独网格控制
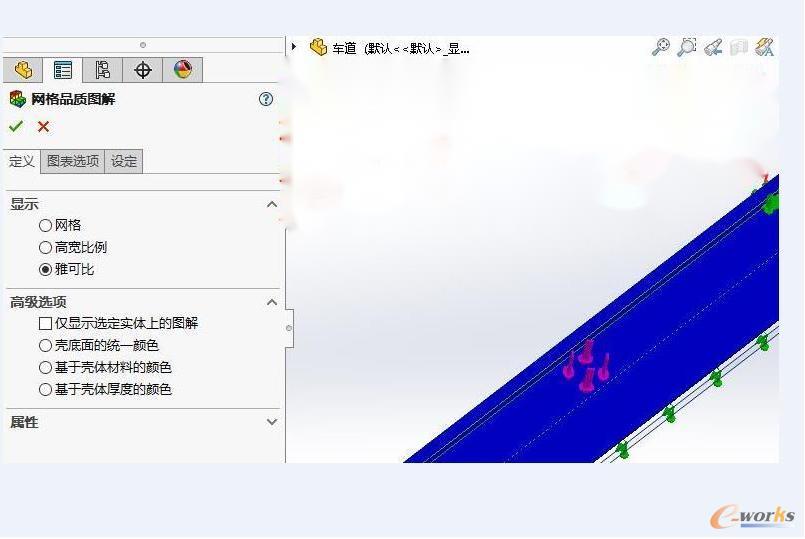
图13 评判网格精度
局部进行网格控制时,一般单元大小先选整体网格单元大小的一半,且比率(大小网格过渡)要适合,一般选取1.1,1.2,1.5。
评判网格精度(大小)的依据一:网格划分好后,右键点击网格,点击查看网格品质图解,选择雅克比,模型灰色区域说明网格大小合适,标注区域需要调整网格大小。
评判网格精度的依据二:在分析结果出来后,应力强度(图解)的区域需要覆盖2层或2层以上的网格,若只覆盖一层,则需要返回网格划分,重新调整网格大小,并再次运算该算例。直至区域覆盖2层或2层以上的网格。判断网格一般以依据二为最终依据。
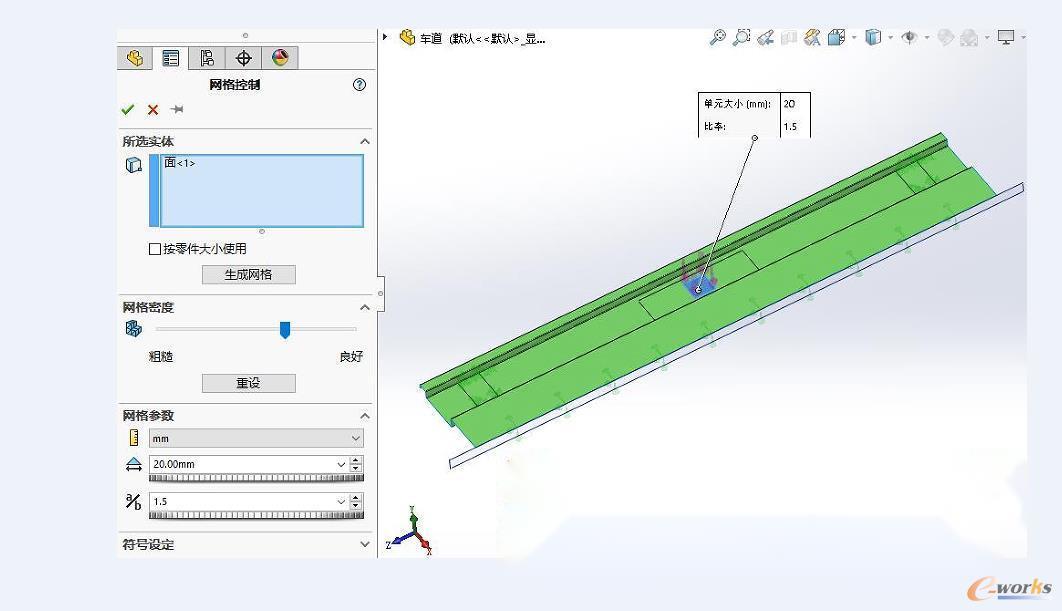
图14 对轮胎压迫车道面进行网格控制
此算例中,对轮胎压迫车道面(车道中间,模拟轮胎与车道接触面,以200*200计算)进行网格控制,网格大小20,比率1.5。
若用上述的方法B进行的钣金壳体化操作的,则可直接划分网格,整体网格大小为50,公差2.5。操作如图所示。
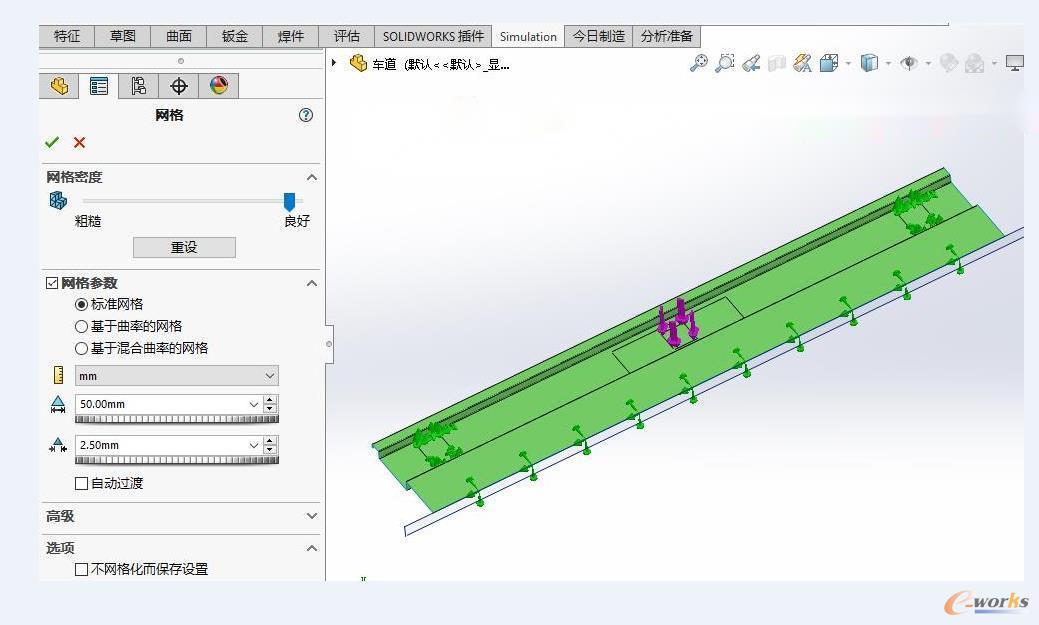
图15 因车道其他面为非重要受力面,故其他面均采取整体网格
若用方法A进行的钣金壳体化操作,则需进行如下步骤:
①“不包括在分析中”,如图16示。
②定义车道曲面—中面(添加厚度):右键单击surfacebody,选择“编辑定义”,如图17示,完成壳体定义。
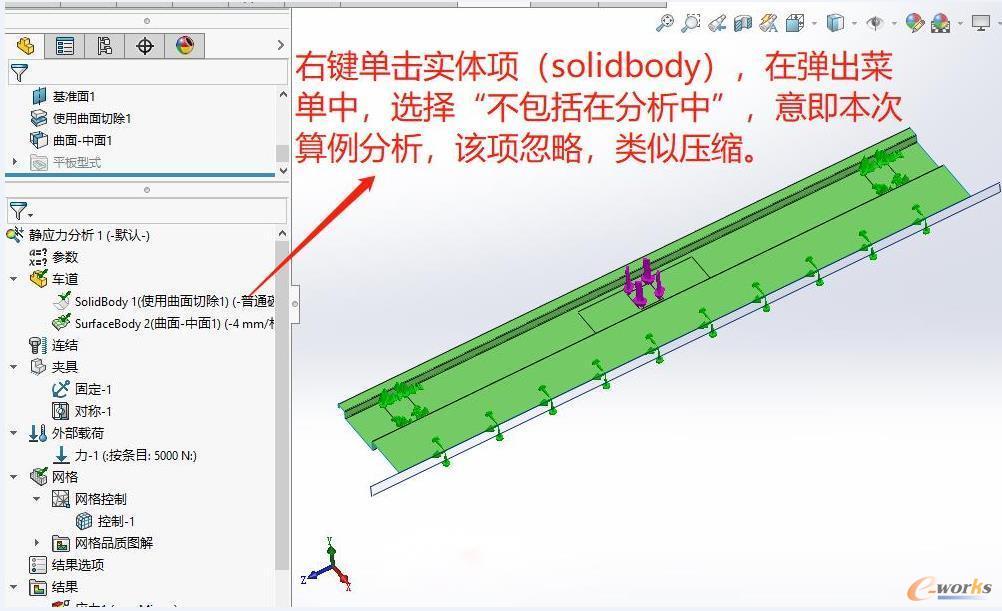
图16 不包括在分析中
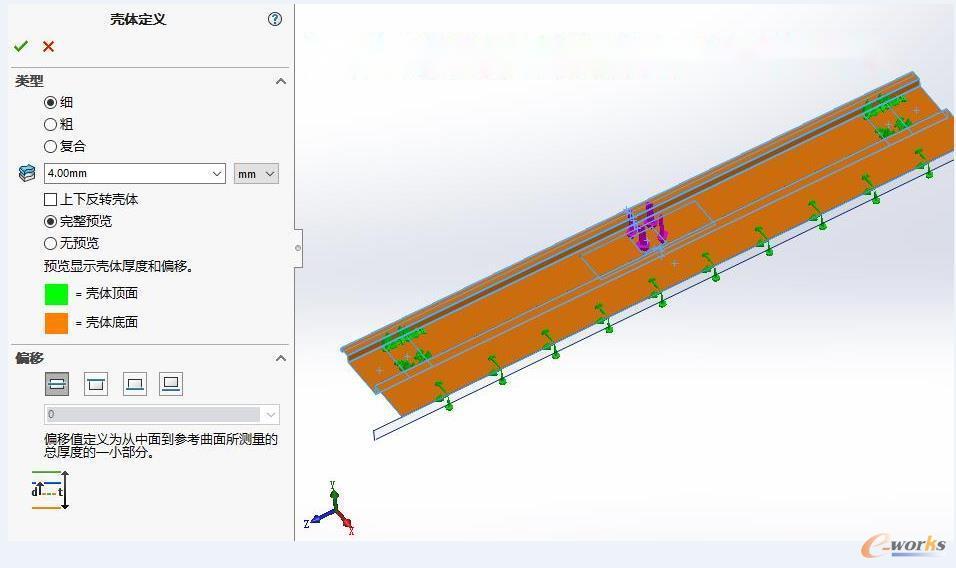
图17 完成壳体定义
上诉操作后,对模型开始网格划分。再运行此算例。计算后结果如图18示。
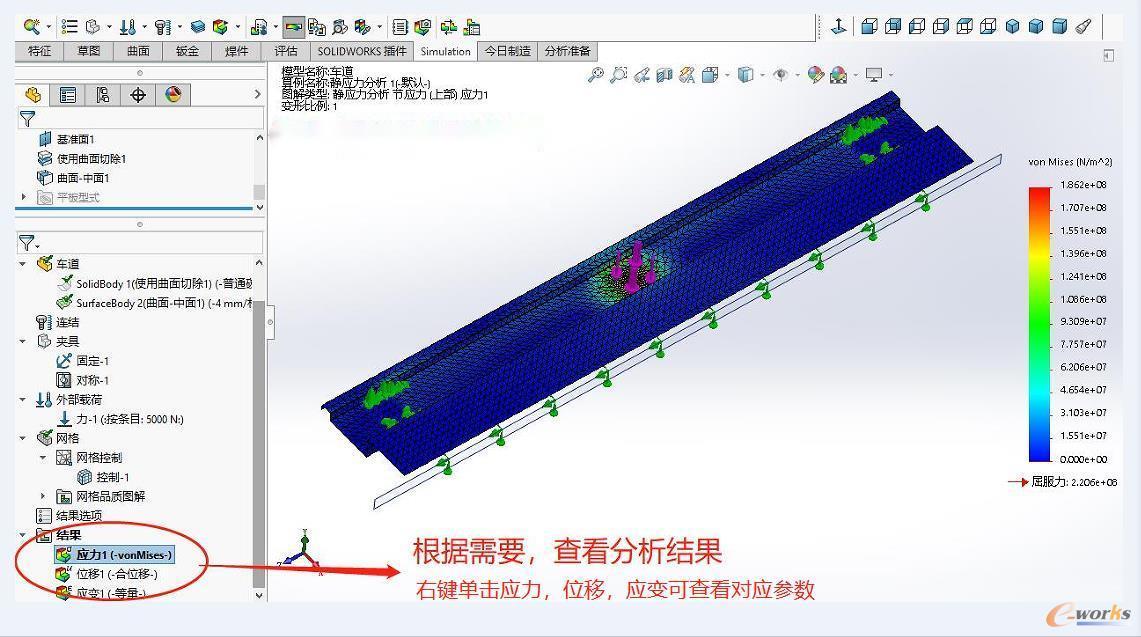
图18 对模型开始网格划分
右键单击应力,选择“编辑定义”,查看应力图解,图19示。
边界选项为网格,即可查看在危险区域的网格分布情况。由上图可以看出网格精度满足要求。
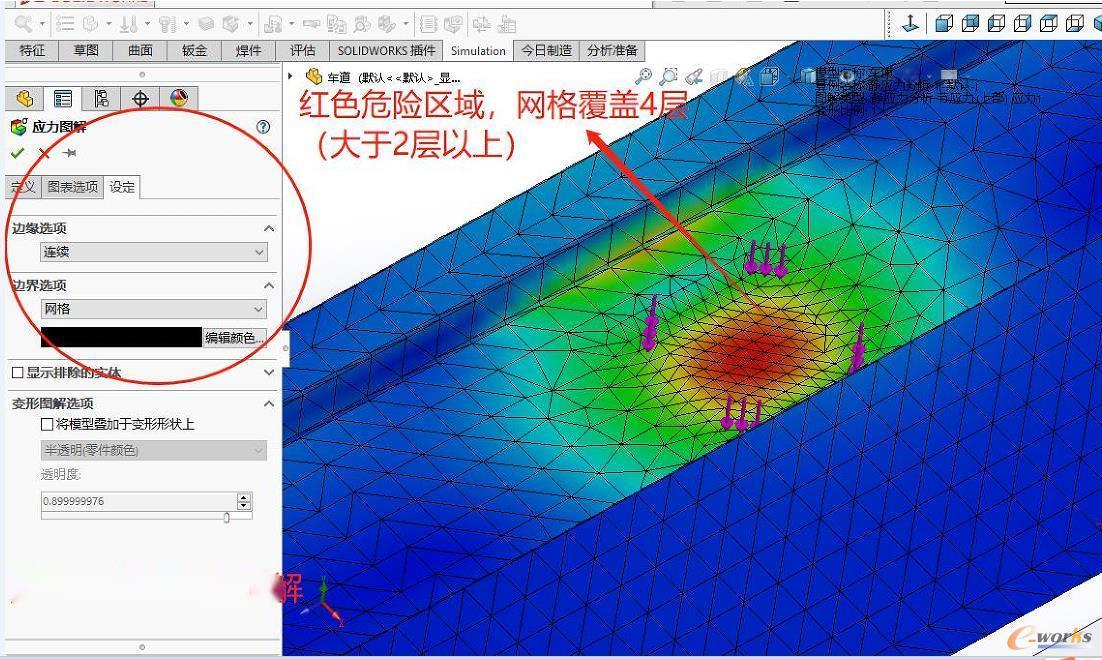
图19 查看应力图解
此分析得出车道中间点(200*200)处,受应力大小1.86*10∧2Mpa,普通碳钢的屈服应力2.206*10∧2Mpa,最小安全系数1.2(右键单击结果,选安全系数图解)。车道的和位移为6.23mm,即轮胎在车道中间时,车道变形量在6.23mm。
关于划分网格前的补充
应力集中:是指物体中应力局部增加的现象,这种现象一般出现在物体形状急剧变化地方,包括:缺口,孔洞,沟槽以及有刚性约束的地方。
应力奇异:受力体由于几何关系在求解应力函数的时候出现的应力无穷大,因为物体都是有一定的强度的,不可能出现应力无穷大。所以在实际结构中是不会出现应力奇异的。
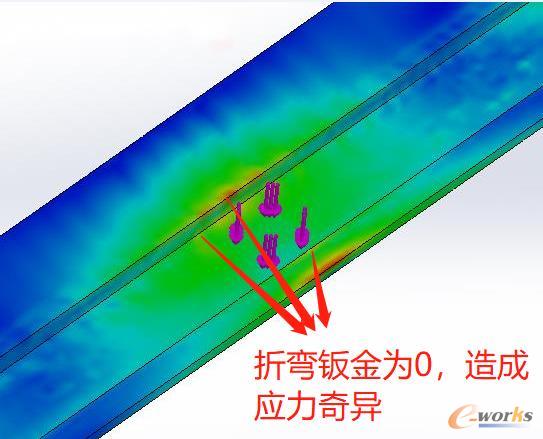
图20 应力奇异
进行模型分析时,若车道以实体生成(折弯半径为0),则转折处会出现应力集中(无圆角),进而造成应力奇异。
出现应力奇异,无法用2层或以上的网格覆盖区域,因为这个时候应力会无穷大。不管用多小的网格划分,分析结果中,始终不会出现“2层或以上的网格覆盖区域”。分析算例中,需要避免应力奇异现象。即在实际生产中要避免应力集中的地方,软件分析前,都需要在这些地方增加圆角,避免形状急剧变化。尤其在轴类零件做受力分析时,轴肩处(大小轴过渡处),需要增加圆角。
而对于那些只方便装配用圆角,倒角(轴端倒角),不会引起应力集中,故这些倒角可以去除,以减少网格划分的计算量。
八、设计算例
通过设计算例,优化设计的模型结构。
在生产成本一定时,提高产品质量和性能;在满足产品质量和性能时,使生产成本最低。
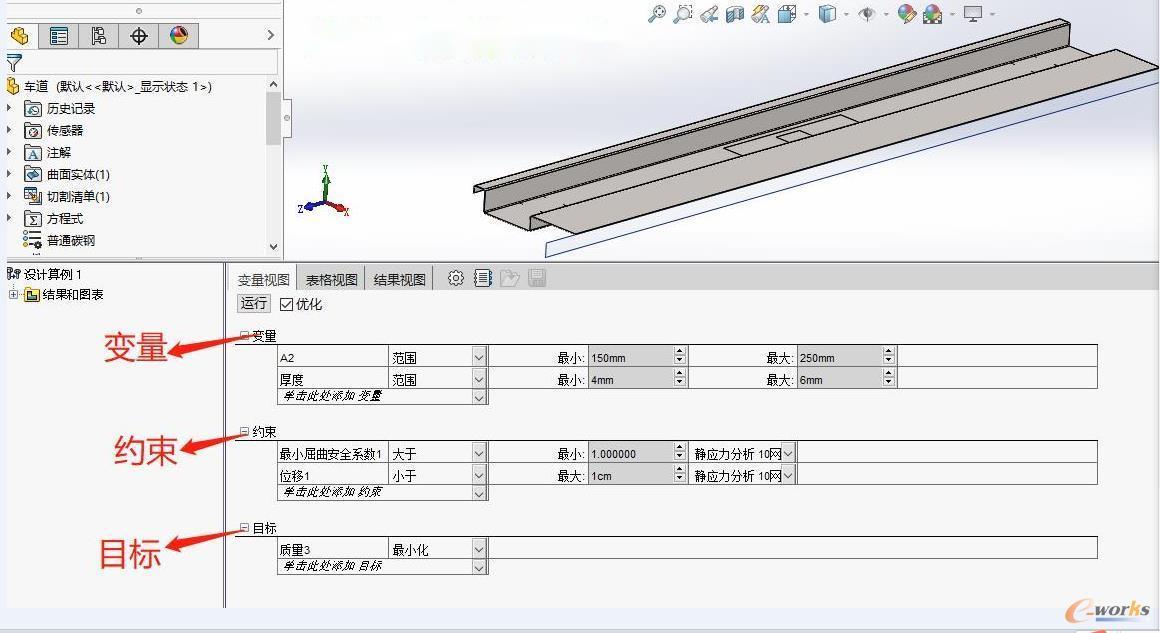
图21 优化分析界面
如图21,在优化界面,分3部分操作区块:变量,约束,目标。优化分析的思路为:实际工况中,遵守一定的准则(满足某一条件即约束),通过变化一个或多个(尺寸)参数(变量),来达到某一目的(目标)。
变量:模型上可变化的参数,点击“单击此处添加变量”→“添加参数”,弹出如图22对话框。
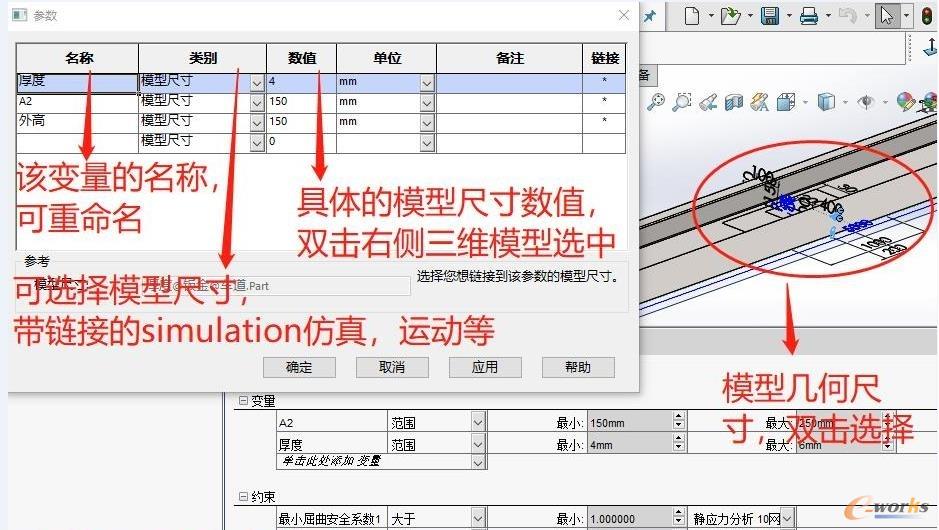
图22 变量的各组成部分
本优化针对车库钣金厚度,U型(单侧)高度对车库安全系数的影响大小,故变量处输入厚度和U型高度。厚度可选“带步长范围”,步长1mm,意为计算机分析完4mm厚度后,会选择5mm继续分析,跳过4.2,4.5之类的厚度(此类板材厚度实际工况中可忽略)。U型高度选“范围”,因为高度范围不一定是整数值,可以是符合要求的任意小数值,选定后的变量参数如图23示。
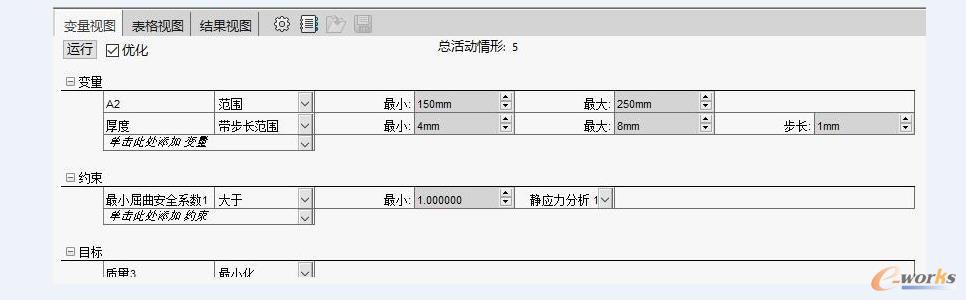
图23 变量选定
“约束”在此处为安全系数大小。在之前算例求解中,右键单击“结果”,可选择安全系数图解,点击确定后,软件显示:最小安全系数为1.2,如图24示。
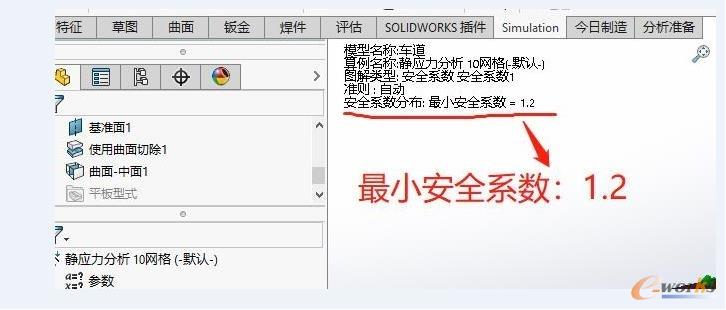
图24 查看最小安全系数
所以关于约束,选择添加传感器→simulation数据,确定后,选择对应的分析算例解算器(得出安全系数那个算例),如图25示。
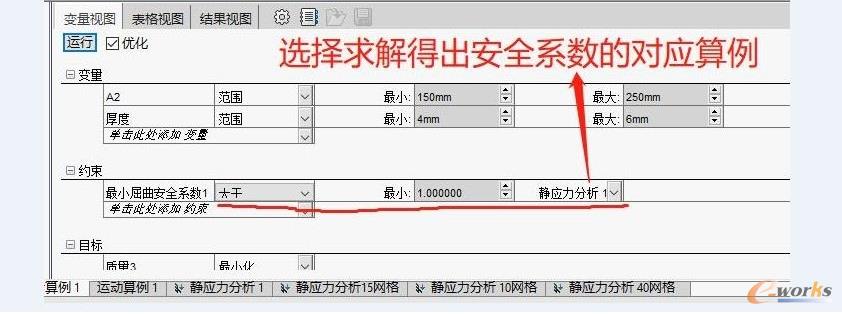
图25 选择求解得出安全系数的对应算例
安全系数应该选大于最小安全系数值“1”,这样符合逻辑。
在满足安全系数大于“1”时(暂定为1),车库质量最小(成本最低),即质量最小化。其中,质量也属于传感器类数据。三类参数确定后,点击运行(优化打钩),计算机会列举许可的情况,算出对应的安全系数和对应的变量。并自动筛选出满足安全系数大于1的最小质量车库。供设计者计算参考,如图26示。

图26 自动筛选出满足条件的最小质量的方案
SW的simulation受力分析和优化设计步骤到此结束。
从提出问题(单个轮子压在车道上)到优化计算出多少参数的车道满足这一条件,给零经验设计者提供数据支持。
对模型分析的进一步讨论--装配体分析
实际工况中,分析优化往往复杂的多。比如在车道下面(车库背面)焊接加强筋。图27示。同样对其静应力分析。此为焊接装配体(筋与车道背面焊接)。加强筋与车道均为壳体(曲面)分析(实体不包含在分析中),操作如上诉零件模型分析一致。
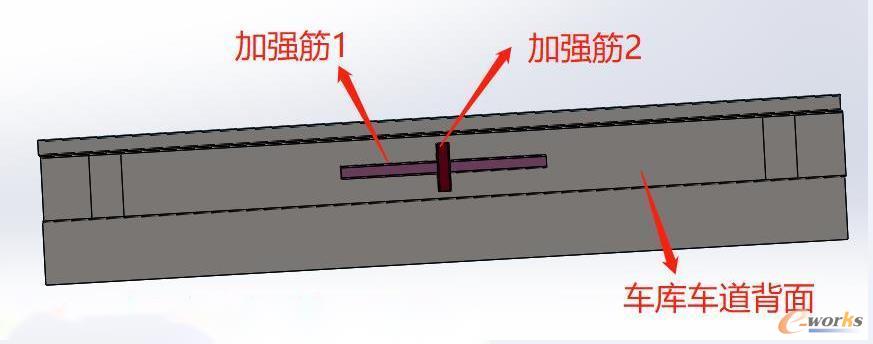
图27 由零件分析到装配分析
“夹具操作”,“外部载荷操作”也与零件模型分析一致。因为此为焊接装配体分析,系统默认均会给出“零部件接触”,“全局接触”,且为“接合”。此算列中接触符合实际工况,故不做修改。
“相处面组”选中的都是工作面(面),当然也可以是虚拟面(如基准面),定义为局部的面接触类型。
“零部件接触”是定义零件与零件之间的接触类型。
“全局接触”定义为所有零部件接触类型均一致。
其中“无穿透”意为两个面或实体,不产生干涉,允许有一定缝隙,如相对滑动。
“接合“意为两接触面或两零件间无相对运动,无间隙,可看做焊接在一起。
“冷缩配合”意为两个配合的实体相互干涉(过盈配合),如键与键槽,轴承与轴的接触等。在轴的静应力分析中,可以先将键与轴的键槽过赢配合,接触即为冷缩配合,即可求解出键对键槽的作用力。
在此车库加筋模型分析中,进行2处网格控制。除了对轮胎压迫车道中间处(800*500空间)以网格控制,同时还对加筋处进行网格控制,为了对比准确性,网格控制规格与零件模型一致(20,1.5)。其中800*500空间意为与200*200的受力空间错开。若重合,则会发生应力奇异问题,发生奇异问题点为200*200的边缘区,此边缘处又有局部网格过渡到整体网格。此区域受力急剧变化。故网格控制区域暂定800*500。(增大网格控制区域,不影响分析结果,只影响分析计算量,即计算速度。(该文后面会提到。)同时,用同样的方法,对两处支撑点也进行网格控制,且控制区域先略大于(200*200),对加筋模型进行运行算例(求解),得到图28。
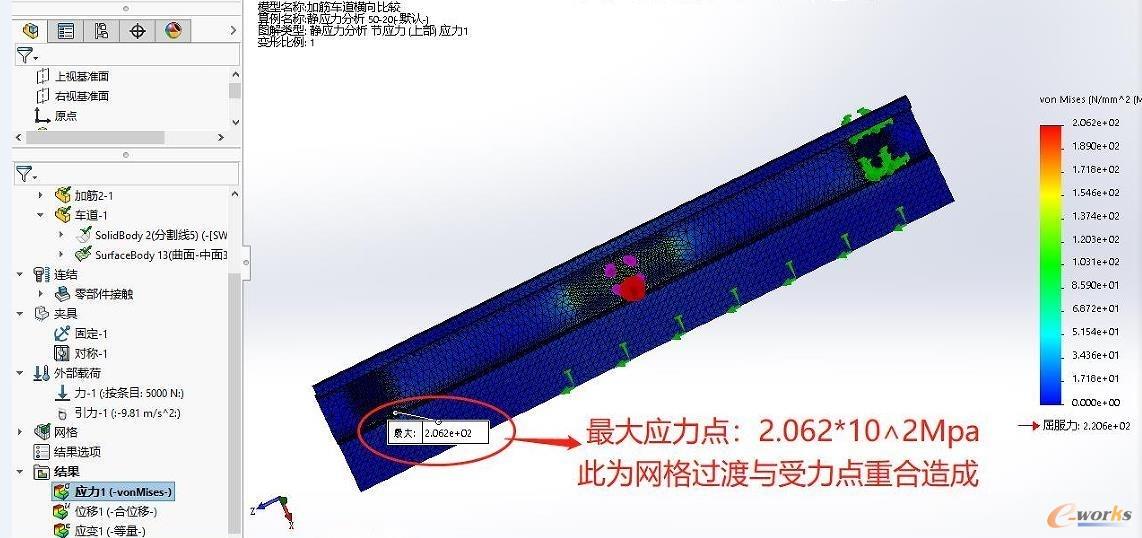
图28 车库加筋模型分析
车道支撑点不可能是受力最大点。造成这个问题,是此处网格控制空间只略大与受力空间造成。(该问题后续可增加网格控制空间解决。)
右键点击“结果”中的“应力”,选“探测”,对车道受力最大真实点,探测受力大小,如图29示。
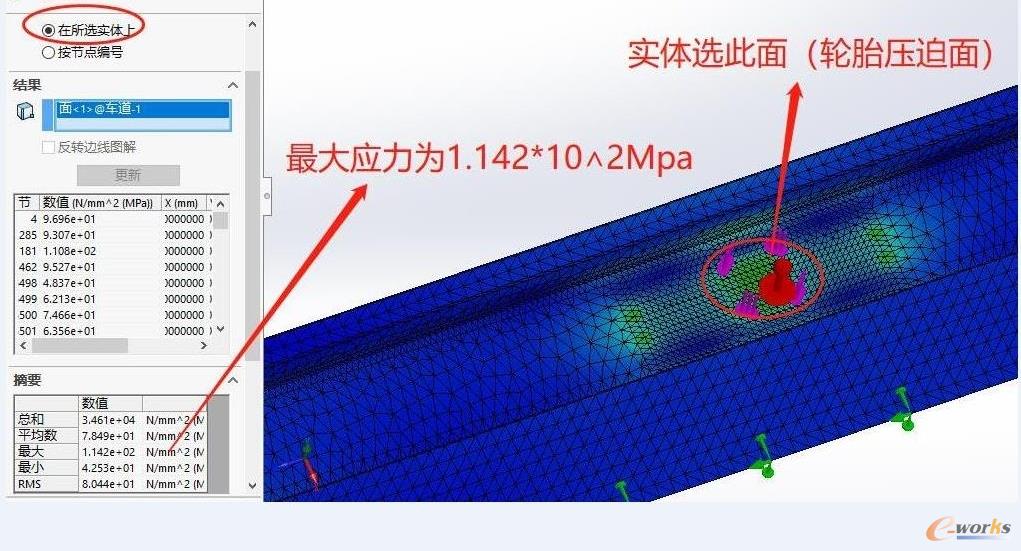
图29 探测受力大小
即在加筋后,车道中间点受应力最大是1.142*10∧2Mpa。
为了对比准确性,对上面提到的零件模型做再次分析。其中,增加支撑点的网格控制,增加车道中间网格控制空间大小,网格规格与空间大小与加筋模型一致,通过对零件模型算例后,探测车道中间处受力结果如图30所示。
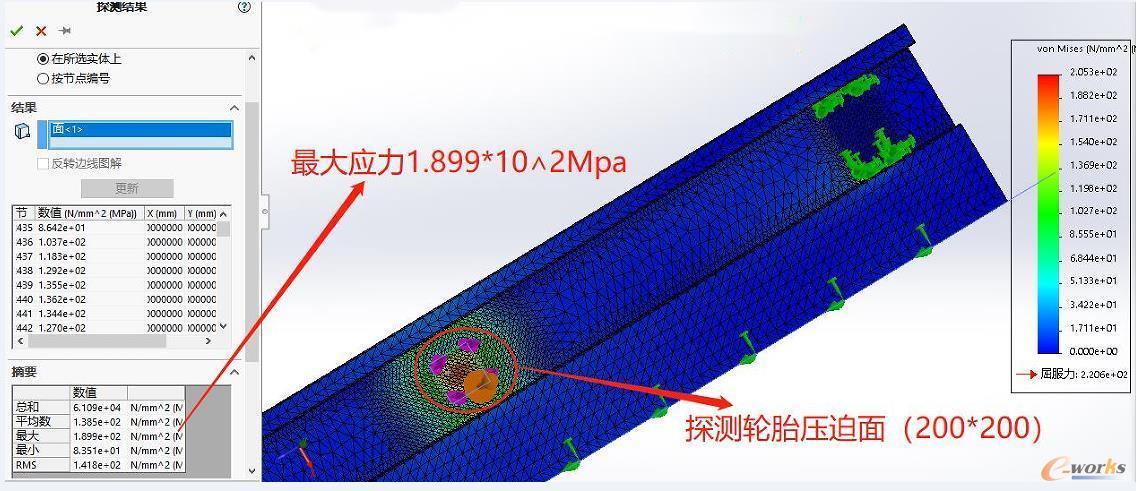
图30 探测车道中间处受力结果
对比上面两图和之前首次分析的零件模型,可得:
1.对模型增大(增加)网格控制空间,除了增加计算量,不影响分析结果,但会有误差。(首次分析时应力大小1.86*10∧2Mpa)
2.网格控制时,若控制空间不当(控制空间与受力区域重合),亦会引起应力奇异。
3.加筋后,车道所受应力明显减小,(符合实际工况)。关于这点,其实设计者可以通过布置别的加筋方案,通过分析对比,掌握不同的加筋对车道的受力影响。
这样,有限元静应力分析,可为我们提供以往需要实验才能获得数据。大大简化设计过程。再通过结构优化设计,有限元分析筛选出满足设计者要求的最优方案。这为设计者大大缩小设计成本,节省了不少时间,也为实验提供数据准备和理论支持。
本文为e-works原创投稿文章,未经e-works书面许可,任何人不得复制、转载、摘编等任何方式进行使用。如已是e-works授权合作伙伴,应在授权范围内使用。e-works内容合作伙伴申请热线:editor@e-works.net.cn tel:027-87592219/20/21。