本文为“2023年度中国智能制造最佳应用实践奖”参评案例。本次活动将评选出2023年度,为中国智能制造领域带来突出效益的最佳实践工程,全面介绍企业推进智能制造的步骤、重点与难点、获得效益等,分享建设过程中的经验,供广大制造业行业企业学习供鉴。
一、企业简介
加西亚电子电器股份有限公司(以下简称,加西亚)初创于2002年,专业致力于断路器的研发与制造,低压断路器全国出口排名前三,是工信部“专精特新小巨人”企业。现拥有温州、上海、江西三大基地2022年三地共实现产值10亿元。是通用电气、伊顿电气、现代重工、法国罗格朗电气等世界500强供应商,并发展了同海外20多家地区知名品牌的合作。
公司历年来持续投入销售额近5%的研发费用用于新产品开发,打造优势研发平台。先后建成“浙江省博士后工作站”、“浙江省智能断路器研发中心”、“浙江省企业技术中心”、“浙江省智能断路器研究院”等多个企业研发平台。获得各类专利160余件,其中发明专利19件,计算机软件著作权6项,并参与制定国家和行业标准12项。同时,是浙江省级制造业与互联网融合发展试点示范企业、浙江省绿色低碳工厂、温州最美工厂、乐清市第一批智能工厂示范企业。

图1 加西亚电子电器股份有限公司
二、企业在智能制造方面的现状
加西亚智能制造建设目标:构建以SICA断路器为示范产品的数字化设计、数字化排产、自动装配及检测、自动包装、智能物料及成品输送信息化管理链条,建立可复制、有行业推广意义的小型断路器智能工厂样板,提升企业竞争力,形成行业智能工厂标杆。
加西亚断路器智能制造项目针对公司的核心业务和未来的发展愿景,进行了智能制造蓝图的规划。建立了设备层、控制层、执行层、管理层、决策层的智能制造架构。通过构建数字化管理平台,打通了销售、研发、计划、采购、生产、指令、仓储、物流等核心业务的数据采集、共享和分析决策,实现了业务透明化和精益化管理。
技术线路规划原则:总体规划、分项实施、并行推进、多点突破、融合集成。
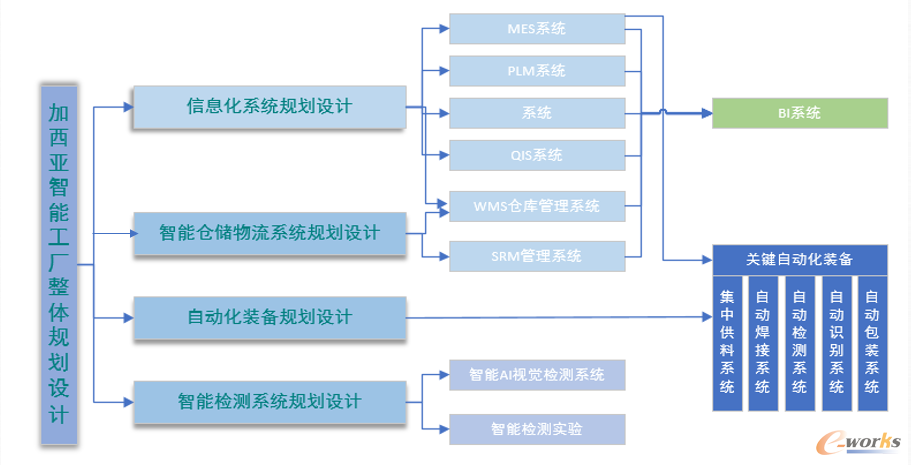
图2 加西亚智能工厂整体规划
1、流程再造
对公司业务流程重新梳理并以系统实施落地,实现计划调度、采购仓储、生产作业、物流配送、质量和设备管理等关键业务的数字化管控,实现生产过程精细化和数字化管理,提高了工厂生产整体运作效率。
2、集成应用
建立数据集成平台,通过PDM、ERP、MES、WMS、SRM、QIS系统和物联网平台的集成应用,实现采购、研发、计划、采购、工艺、制造、设备、质量、仓储、物流等企业运营各环节之间的数据交互和共享,建立智能工厂营运管理体系。
三、参评智能制造项目详细情况介绍
1.项目背景介绍
(1)国产低压电器面临新的市场机遇
低压电器行业竞争格局相对稳定。全行业可区分为三类竞争企业和以下特点:产品门类齐全,相互间进行全方位竞争的企业。以ABB、施耐德电气、罗格朗、西门子为代表的跨国公司占领中高端市场的主要份额;专注于若干子产品,参与行业局部竞争的企业。常熟开关制造有限公司、上海人民电器厂和上海良信电器有限公司处于第二梯队,聚焦于S2市场的争夺;无明显产品优势和特点的中小型企业。公司一开始定位于低端市场,迅速成为了S3市场的龙头企业。外资占据高端市场,施耐德作为整个行业的龙头企业,占据15%的市场份额;施耐德、西门子和ABB总共占据超过四分之一的市场份额。公司作为S3市场的领军企业,市场份额达到15%左右。中高端市场主要采取B2B的模式进行销售,公司所处的低端市场大部分采用渠道进行批发销售。在目前行业由三角形向纺锤型发展的阶段,低端市场大企业开始逐渐向中端领域扩张,开始争夺中端市场。内资品牌技术突破将加速推动中高端低压电器国产化,目前我国高端低压电器市场份额依旧主要在外资品牌手中,但随着内资品牌研发和生产能力的提升,同时越来越多的企业在采购低压电器时会更加关注产品的性价比,而非一味追求外资品牌,所以在这种环境下,质美价优的国产低压电器有望获益。在行业格局演变和产品升级的趋势下,行业竞争格局“马太效应”将逐渐显现,具有较强研发实力且规模效应明显的低压电器企业将有望快速成长。
(2)加西亚电子智能化转型的需求与痛点
加西亚公司业务以出口订单为主,是典型的多品种、小批量接单生产型企业,随着市场发展和竞争加剧,订单交期越来越紧,加西亚需要通过智能工厂建设,进一步加强生产过程的透明化、信息化,提升生产效率,解决以下问题:
●提升制造过程自动化水平,解决断路器注塑、冲压、装配等关键生产工艺的自动化,提高生产制造效率和良品率,实现减员增效;
●针对出口型订单,建立快速反应的敏捷生产体系,实现从研发设计、生产制造、销售和服务的数据共享和管理效率;
●通过原材料、半成品及成品的条码化管理,实现对关键物料的跟踪和质量追溯;
●解决生产过程数据不透明,生产过程数据时效性差,产品追溯困难,决策数据不充分等问题,实现对各产品线的生产进行管控,实现从作业单的下达到产品的入库的全过程的数字化管理;
●通过智能工厂建设,以及PLM、ERP、MES、WMS等项目的实施,借鉴行业最佳业务实践的经验,进一步优化并规范公司各个生产制造产线的业务流程,并逐步在整个集团建立起标准化的工厂管理体系。
2.项目实施与应用情况详细介绍
加西亚电子电器有限公司的“加西亚断路器智能化工厂”项目,面向断路器行业多品种、小批量、定制化、高质量、快速相应市场的行业需求,建设加西亚断路器智能工厂,围绕智能制造模式,利用绿色智能制造的理念,以装备自动化为基础,以设备数据采集与监控系统、物联网为纽带,采用实时生产控制信息系统为核心,基于统一模型,在研发设计、供应链管控、生产制造、质量监控、设备管理、物流服务、仓储管理等各环节,实现端到端的横向无缝集成。
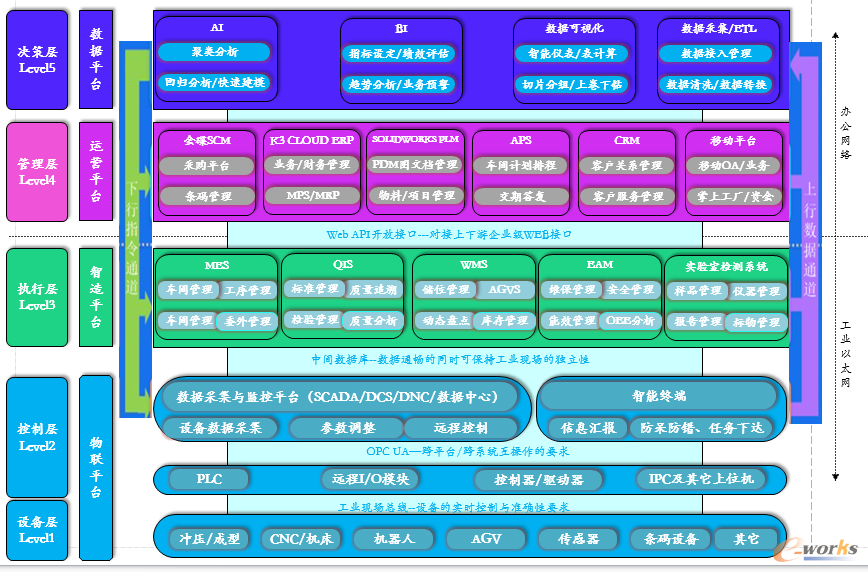
图3 加西亚智能工厂体系框架
加西亚断路器智能工厂项目进行了智能工厂规划蓝图,建立了设备层、网络层、系统层和分析决策层的智能工厂架构,打通设备、设计、生产、采购、质量等关键业务环节的数据采集、共享和分析决策。
在设备层,对断路器的生产工艺进行了优化,对注塑、冲压、组装检验、包装等关键生产工序和物料配送装备进行了设备的改造和升级,提高了生产过程、质量检测、物料配送管理的自动化水平,提高了产能、质量稳定性、物料配送效率和人均生产效率。
在控制层,通过覆盖车间的工业以太网,将现场的设备通过PLC、远程I/O模块、SCADA、控制器等与控制系统、智能终端连接,构成物联平台。实现对设备的远程监控和生产过程的数据采集,通过二维码实现物料出入库、工序流转、工单、生产信息等跟踪和记录,提高物料流转效率,减少生产异常等待。
在执行层,实施健新智能的MES系统实现车间的计划排程、生产调度、工序流转、过程质量管理、模具管理、设备管理、能耗管理。通过物联网平台和二维码的使用,实现生产数据、设备数据、检测数据、传感器数据的采集和数据交互。实施国坤智能WMS系统,实现物料的条码批次管理、库位库存管理、物料配送管理、线边库管理,与MES系统集成,提高了物料配送的及时性、透明性和准确性。实施安必兴QIS系统,实现质量追溯和质量分析。实施EAM系统,实现设备OEE、能效管理、维保管理。实施研发检测控制系统,实现样品管理、仪器管理等。
在管理层,全面推进CAD、3D设计,实施SolidWorks PLM系统实现了研发设计的数字化,提高研发设计效率。通过实施金蝶的ERP、SCM系统,实现财务业务一体化和采购信息化管理。实施健新智能的APS系统,实现周计划的进行排程和交期答复。运用数字孪生技术,对工厂布局、工艺设计、生产进行仿真和优化。
在决策层,构建运营管理平台,集成各业务的关键数据,分析建立企业常用业务的数据分析模型,通过数据挖掘和分析,实施数据可视化管理,建立工厂运营指挥中心,并对注塑、组装、智能检测中心和仓库等重点业务部门建立数字化看板,实现车间级、工厂级的可视化管理,为企业运营提供分析决策支持,全面提高企业的综合竞争力。
(1)工艺改进和优化
加西亚对断路器的生产工艺进行了优化,通过使用高速自动冲压机床、焊接机器人、数控注塑机、自动合模机器人、自动检测线、自动组装线、自动穿钉铆合设备、自动包装机等自动化设备对断路器的冲压、焊接、注塑、装配、校验、铆合、移印、包装等关键工序实现了自动化生产,大幅度提高了生产自动化水平。
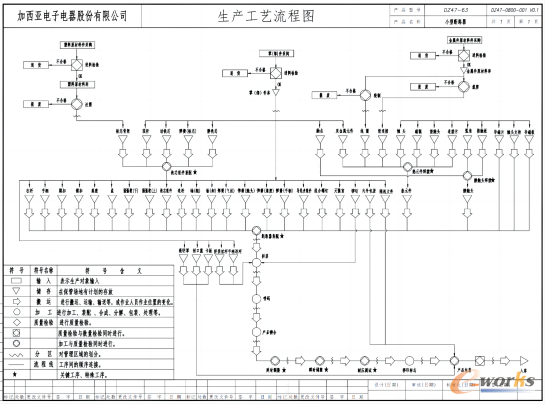
图4 加西亚实施前的工艺
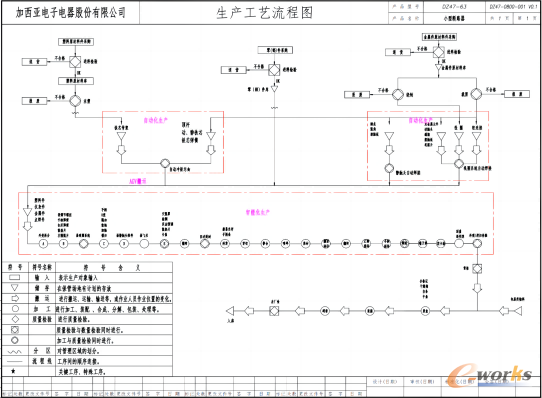
图5 对全流程工艺进行了优化和改进
通过工艺优化和设备升级,实现了注塑工序减少用工约30%,冲压工序减少用工约60%,装配工序减少用工约75%,断路器检测工序少人71.8%,其他工序减少用工约40%的能力。车间用工人数减少106人,极大的提高了生产效率,降低了用工成本。
(2)完成设备改造和数字化车间建设
1)部件事业部-注塑数字化车间建设
注塑数字化车间共有22台套注塑机,采用集中供料装置统一进行供料,配套24台套4轴机器手进行注塑口回收,其中配置6台套全自动合模机器人的注塑机实现了无人全自动化生产,可实现每1人同时看顾5台机器,每天产量断路器塑料件19万套。工作环境噪音减小5%,工伤几率减小40%,生产效率提升26%,人员减少24人,合计直接产生经济效益120余万元/年。目前MES已经覆盖22台大机,系统可以自动发送工艺参数、产量效率、质量比对等信息,实现注塑工艺的数字化管理。
智能注塑单元,由中央供料系统、全节能注塑机+自动供料系统+自动合模监控器+断路器自动装配单元等构成,可以实现供料、注塑、模腔监控、断路器外壳组装(码放)的自动化生产,极大的提高生产作业效率。以前6台机器24小时生产需要12人,现在只要4人,人员减少8人,节省人员67%;以前拼装单价0.017元/单级,现在单价0.005元,单价下降71%;以前产量,24小时生产12000只,改进后产量提升24小时生产16000只,产量提升33.33%。

图6 自动注塑单元(自动供料+机械手+自动装配)
2)部件事业部-冲压数字化车间建设
冲压数字化车间共有6台全自动高速冲压机,可以实现6台冲压机只需要2个操作工值守,负责模具的上下维护,6台高速冲压机每分钟节拍300次左右,根据原材料带的厚度有自动送料和机进模压成型,每月为总装车间生产0.18亿只金属零部件。
3)断路器事业部-断路器数字化车间建设
加西亚电子断路器车间有7条自动生产线,产线由取料分料、装配打底、内件组装、静触头组装、盒盖和视觉检测产线实现了自动瞬时校验、自动延时校验、自动穿钉、自动铆合、自动正面和侧面移印、自动耐压、自动包装等工序。断路器自动化装配线一出二,生产节拍1.8S,一小时2000极,每天生产1.5-2万极,每月生产小型保护断路器500万台,涵盖市场主流A、B、C型等主流产品。自动装配线按一班产量原需要20人,现需要7人,减少13人,可以实现少人化和自动化生产。断路器车间通过设备改造,大幅度提升了生产效率,改善了生产线缺料、故障、正常生产的状况,降低了95%工作环境噪音,工伤几率减小95%,生产效率提升68%,人员减少90余人,合计直接产生经济效益945万元/年。
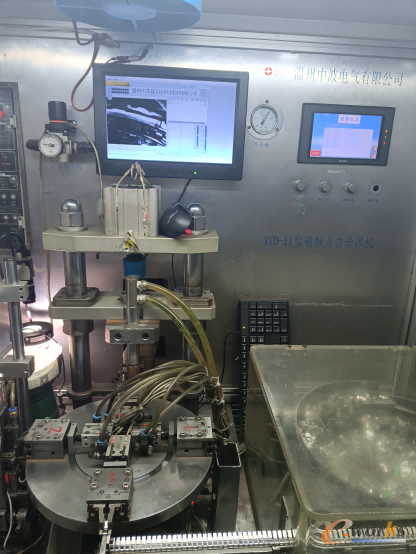
图7 自动化视觉检测设备
4)断路器研发中心建设
加西亚断路器研发中心,按照CNAS研发检测资质认可标准进行建设,完成总监控室、电寿命试验室、温升特性试验室、运行短路试验室等10几个产品研发检验功能的建设。研发中心拥有多工位小型断路器标准试验设备、小型断路器瞬动脱扣试验设备、小型断路器温升/功耗试验设备、28周期试验设备、63kVA三相多磁路系统、直流特性试验系统、电子元件抗老化试验设备、B型漏电开关测试仪、5台步入式环境箱等先进检测设备。研发中心建立安防监测与数据管理系统、试验状态监测与数据管理系统、设备管理系统,对研发试验公共区域图像信息、研发科室图像信息、研发设备实时运行状态数据及试验设备报警故障事件进行远程监测,同时可对历史图像信息、试验数据进行回放、分析和管理。
(3)智能工厂信息系统建设
公司以金蝶K3 ERP系统为核心,结合SolidWorks PLM系统、国坤智能WMS系统、国坤智能MES系统、安必兴QIS系统和SRM系统、HR系统、SCADA系统、OA系统等的集成,实现客户寻源、销售订单管理、产品研发、MRP运行、采购订单、供应链管理、仓库收货、生产计划、工单派工、生产执行、完工入库、销售发运、报关、财务核算等业务流程的信息建设。
1)建立面向个性化订单的数字化研发管理
加西亚全面推进数字化设计,应用达索SolidWorks2019、SolidWorks MBD Standard、SolidWorks Composer等SolidWorks三维CAD设计软件等实现了研发设计的数字化。
实施完成SolidWorks PLM系统的建设,建立了统一的设计研发管理平台,实现面向个性化订单的数字化研发管理。实现了对设计研发数据管理、项目管理、物料管理、图文管理、产品管理、工艺管理、变更管理、需求管理等功能。通过CAPP工具与PLM的集成,实现产品数字模型的统一管控。并通过PLM与ERP/MES集成,输出BOM、图纸和工艺信息。
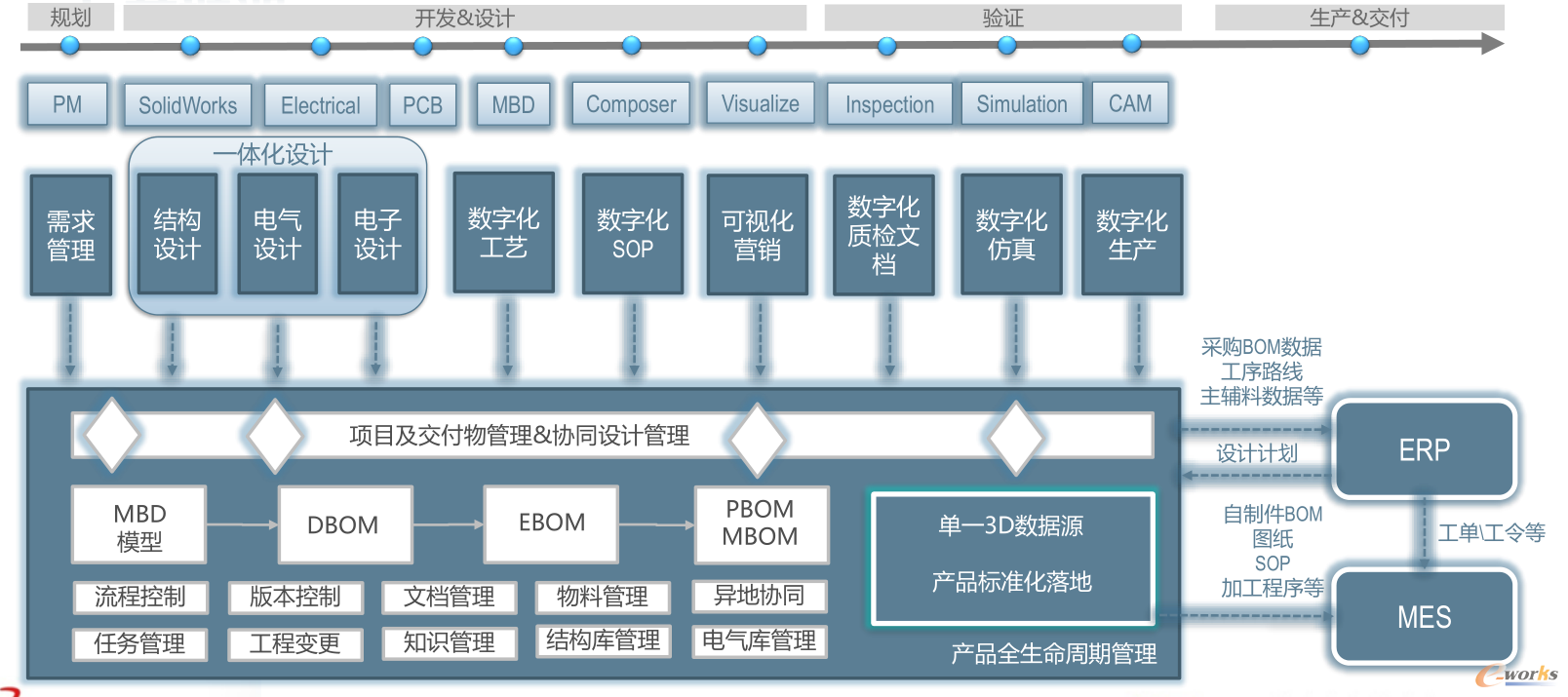
图8 加西亚PLM系统架构
2)建立客户销售服务管理的数字化
加西亚实时应用了金蝶K3 CLOUD ERP系统的销售管理模块,实现客户信息、销售价格、销售订单等业务管理,并将销售信息传递给计划和财务系统进行计划编制和财务核算。
3)建立生产计划协同管理
加西亚实时应用了金蝶K3 CLOUD ERP系统生产计划模块和MES系统的计划排程模块,实现主生产计划、作业计划的编制,并考虑物料、制造资源、设备运维等制造资源等情况。通过设备联网、数据采集和物料跟踪实现对计划的跟踪和动态响应。
4)建立生产制造过程管控系统
加西亚智能工厂实施制造执行系统(MES),实现计划排程、生产调度、工序流转、生产数据采集、产品追溯管理、过程质量管理、条码管理、设备管理、工装模具管理、SPC集成管理、SOP电子化管理、可视化、能效等管理功能。通过MES系统的执行,实现生产过程的透明化。
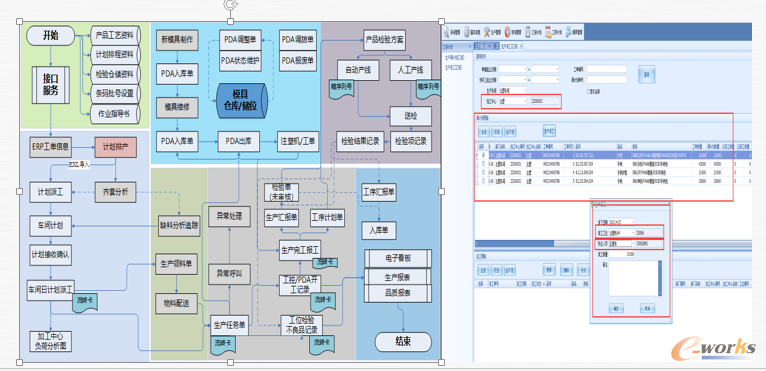
图9 MES系统业务功能图
5)建立产品质量管理数字化
加西亚智能工厂建设完成质量管理系统(QIS),实现了产品质量数据采集、追溯、分析和优化提升。QIS质量管理系统使用标准管理、质量追溯、检验管理、质量分析,找出生产中的质量异常,提高产品的质量稳定性。
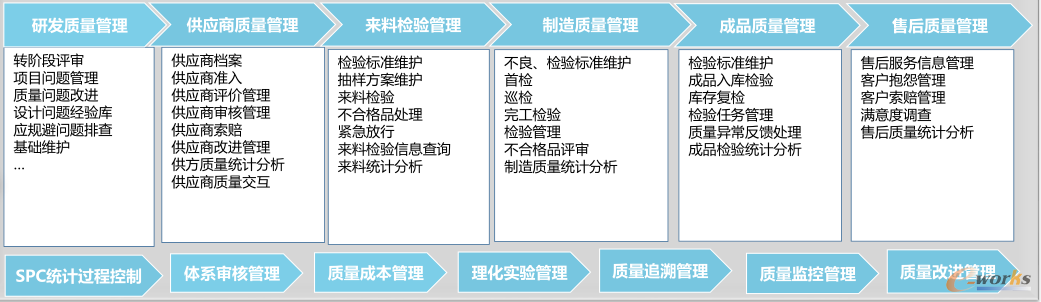
图10 QIS系统业务流程
6)建立敏捷供应链数字化管理
加西亚智能工厂建设完成供应链管理系统(SRM)、仓储管理系统WMS和AGV配送系统,实现采购、仓储、配送、运输与生产计划、制造执行以及企业资源管理等产品实现和业务过程的动态跟踪和集成管理,能够基于车间、产线实际情况拉动物料精准配送,根据客户和产品需求调整目标库存水平,实现精益物流管控。
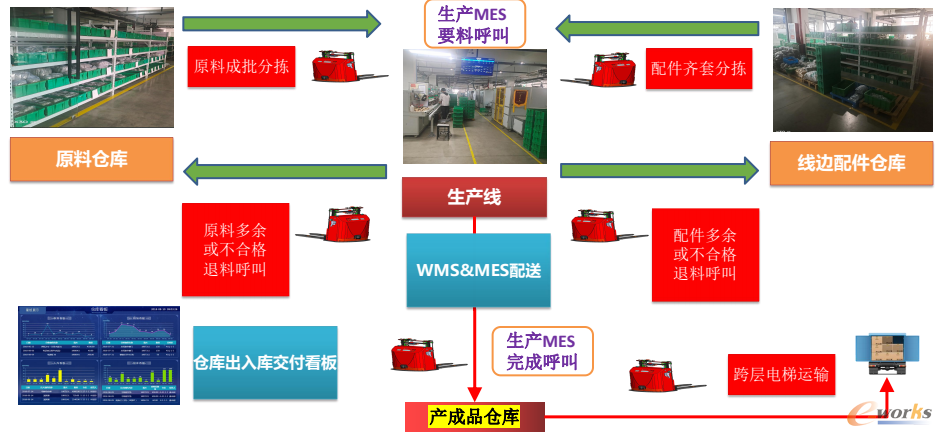
图11 物流配送的业务框图
7)建立业财一体化管理系统
加西亚智能工厂通过金蝶K3 CLOUD ERP系统的实施,打通上下游,实现内部数据的统一与外部数据的沟通,实现财务管理、销售管理、采购管理、计划管理、生产管理、成本管理等一体化管理。实现销售、采购、计划、生产、财务的业财一体化管理,覆盖企业日常运营工作流程的电子化工作平台。
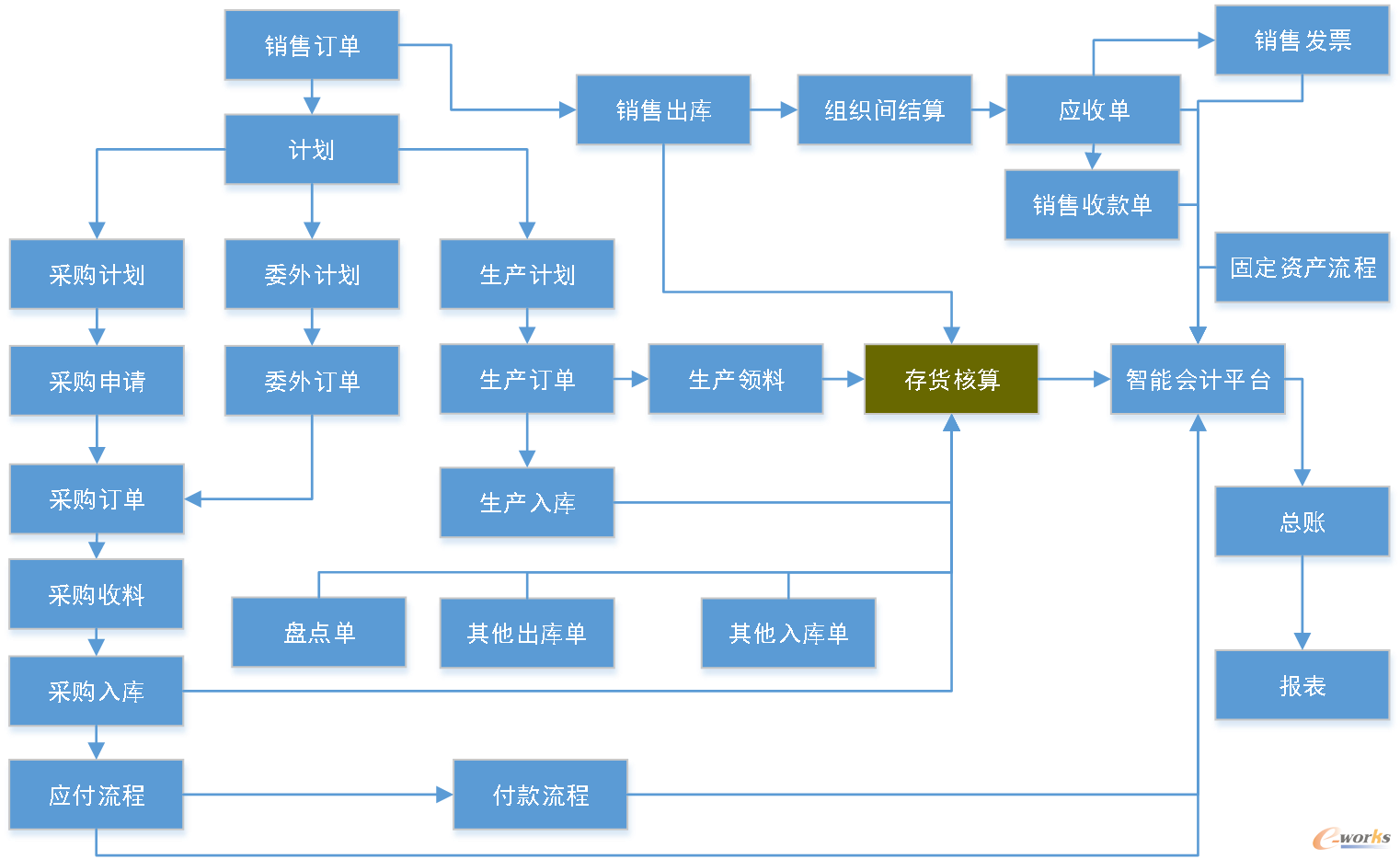
图12 金蝶ERP系统业务系统架构
8)IT基础设施与信息安全管理
·数据中心建设
加西亚断路器智能工厂项目的数据中心已建成8台主机应用,建立虚拟服务器42台,桌面云10台,使用了75TB的数据存储,实现了3种方式的数据备份,能够支持智能工厂的建设。
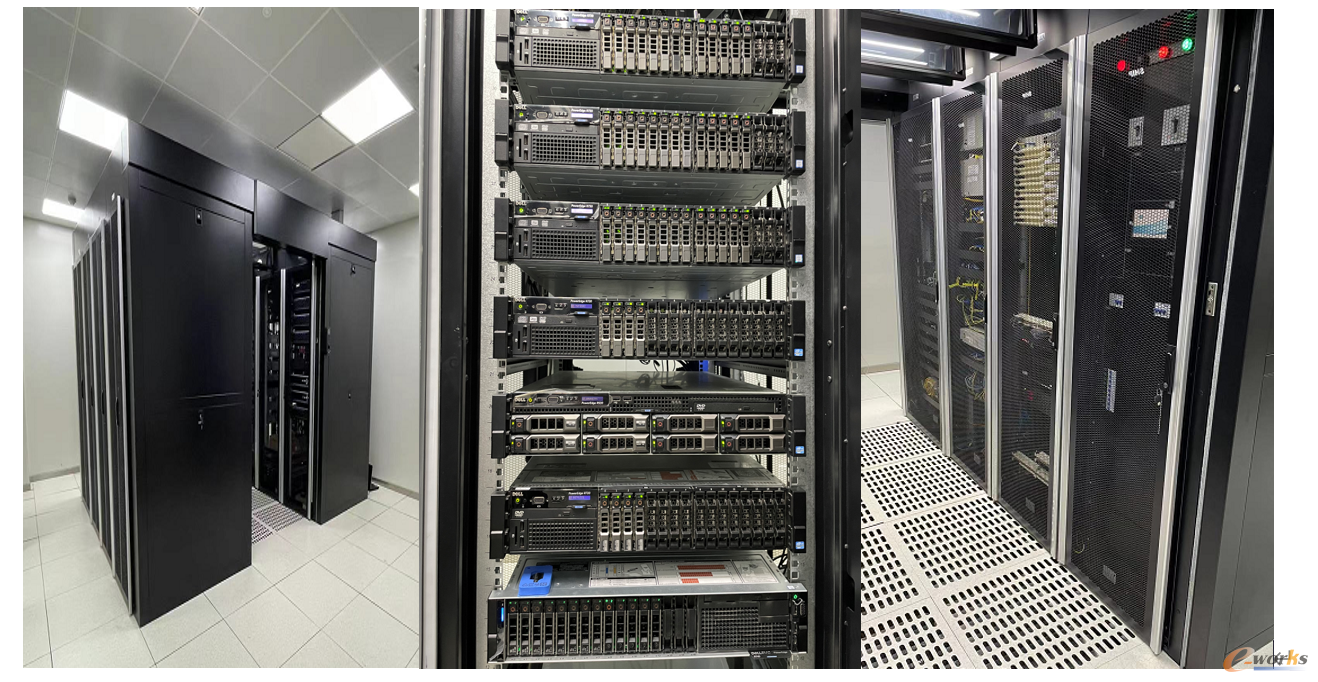
图13 数据中心
·信息安全管理
企业建立了信息安全管理制度,定期对办公网络和工控网络进行安全评估和安全检查,进行补丁升级和系统更新。企业所有终端电脑均安装了防病毒软件,所有软件的安装、更新由专业部分人员进行。安装实施应用了安全防火墙系统,深度安全防护系统应用,实施上网行为管理审计进行安全管理。应用了多业务企业级核心交换和企业级模块化高端路由器、隔离网关、绿盾加密控制系统、AP-MAC地址绑定进行安全管理。
应用信息安全管理平台5.52-190710 SC正式版,包含数据防泄密系统、桌面管理系统、行为审计系统模块,进行安全管理。
数据防泄密系统(简称数据防泄密系统)采用文件过滤驱动实现透明加解密,对用户完全透明,不影响用户操作习惯,从源头上保障企业数据安全;桌面管理系统(简称桌面管理系统)实现终端桌面的标准化管理,解决桌面安全管理问题,提升信息运行维护部门的工作效率,同时规范员工操作行为。行为审计系统(简称行为审计系统)实时追踪终端电脑的操作行为,并生成各项统计报表,对泄密事件的事后溯源提供了有力支持。通过对服务器内部的软件策略与制度管控方式,实现应用安全与数据安全。
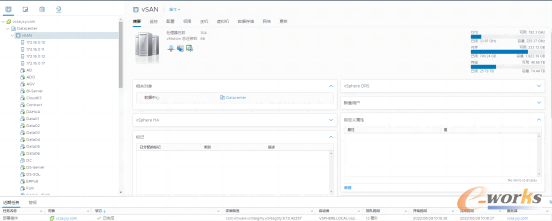
图14 数据安全策略配置
(4)数据互联互通与系统集成
1)设备联网与数据采集
加西亚断路器智能工厂建立了车间工业互联网络,实现了对生产车间的全面覆盖,采用网关和TCP/IP的方式进行网络连接。关键生产设备165台套,关键检测联网设备和原有联网设备45台套,新增关键生产设备联网数量92台,关键设备联网总数为137台套,联网比例83.03%。
设备状态、生产进度、完工数量、质量信息、能源信息等通过设备联网实现自动采集和上传,通过管理体系进行分析和控制。生产工单、物料和完工数据、设备信息管理等采用二维码进行数据采集和进度管理。
设备联网通过PLC、SCADA、I/O远程模块等方式实现设备联网。注塑机通过I/O远程模块,实现设备联网,同时外加计数器和感应器,实现设备运行数据的采集,冲床和流水线采用PLC串口连接,通过PLC转译,串口模块转换为以太网连接。增设无线转发器或5G,将读取的设备信息上传到服务器,减少有线线路,减少车间施工周期。
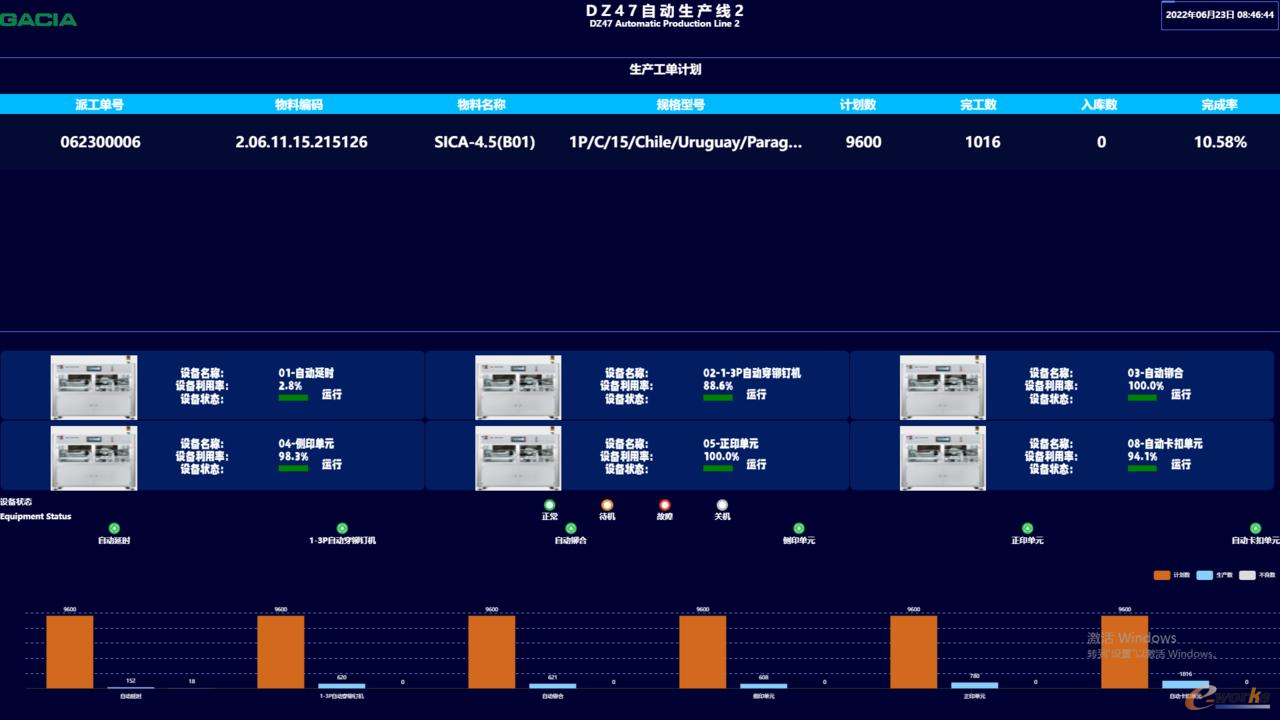
图15 设备联网数据采集
2)数字化工厂系统集成平台
加西亚智能工厂建立了基于数据库和API接口的集成平台,通过PLM、ERP、MES、WMS、SRM、QIS系统和物联网平台的集成应用,实现采购、研发、计划、采购、工艺、制造、设备、质量、仓储、物流等企业运营各环节之间的数据交互。建立企业级的数据监控与决策平台,对采集的企业运营数据进行概念模型、逻辑模型、物理模型的设计、并从公司、制造部、车间、产线、工序五个层,展示了生产、质量、设备、能耗等方面的实时情况,实现通过生产运营、需求计划、库存金额、运行监控、重要订单交付、产销存分析、万元产值耗能、人力资源等关键指标、辅助高层管理决策。
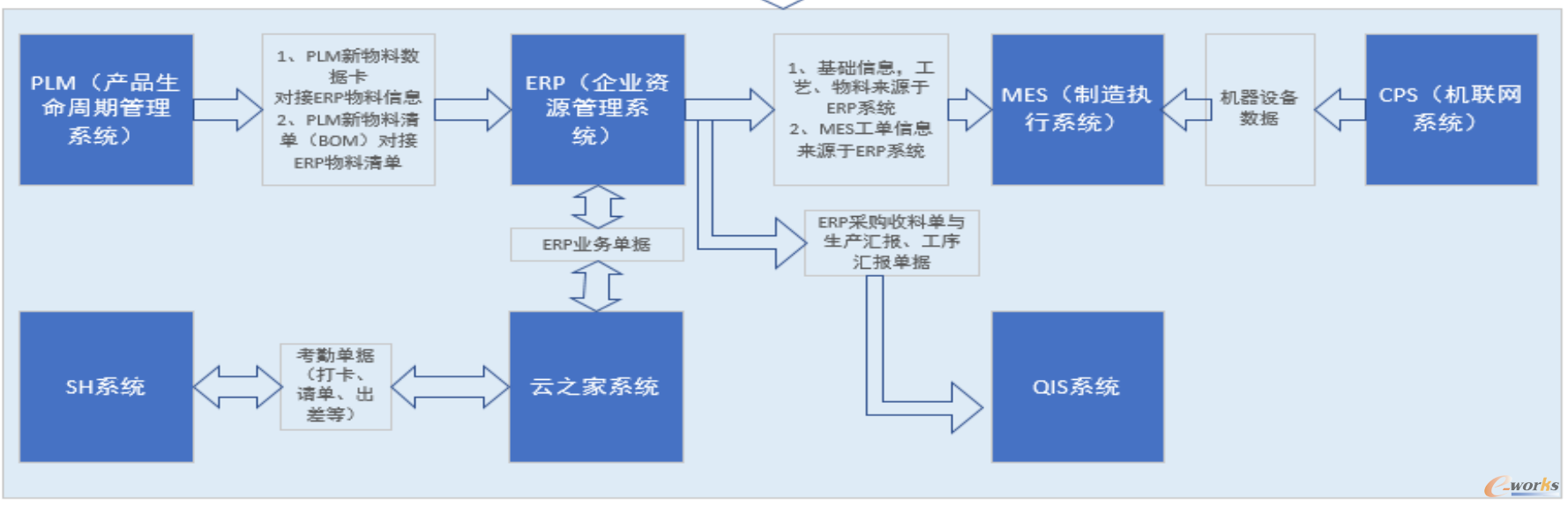
图16 数据集成框架图
3)数据分析与可视化管理
加西亚智能工厂基于ERP/MES/WMS等系统的集成应用,挖掘数据分析价值,建立了可视化管理系统。并实现从工位、车间、工厂多层级的数据分析和可视化管理。通过数据分析,企业不断进行业务优化,企业生产计划准确率提升了40%,库存周转率提升了41%,订单准时交付率提升了29%,运营成本降低了26%。
生产单元可视化管理,在关键工位设立了显示屏,各工位可以通过控制屏了解工作订单和工艺要求,可以在工位上通过扫码完成工单、物料的确认和报工。
车间的可视化管理,通过MES系统采集车间内各关键设备、工序的相关信息,通过车间可视化看板系统的呈现,便于管理者了解车间的实际情况。
工厂综合指挥中心,将各产线、车间的关键数据进行采集、统计、分析和汇总,予以可视化呈现,可以帮助高层管理里着全局的掌握企业整体运营管理的实时情况。
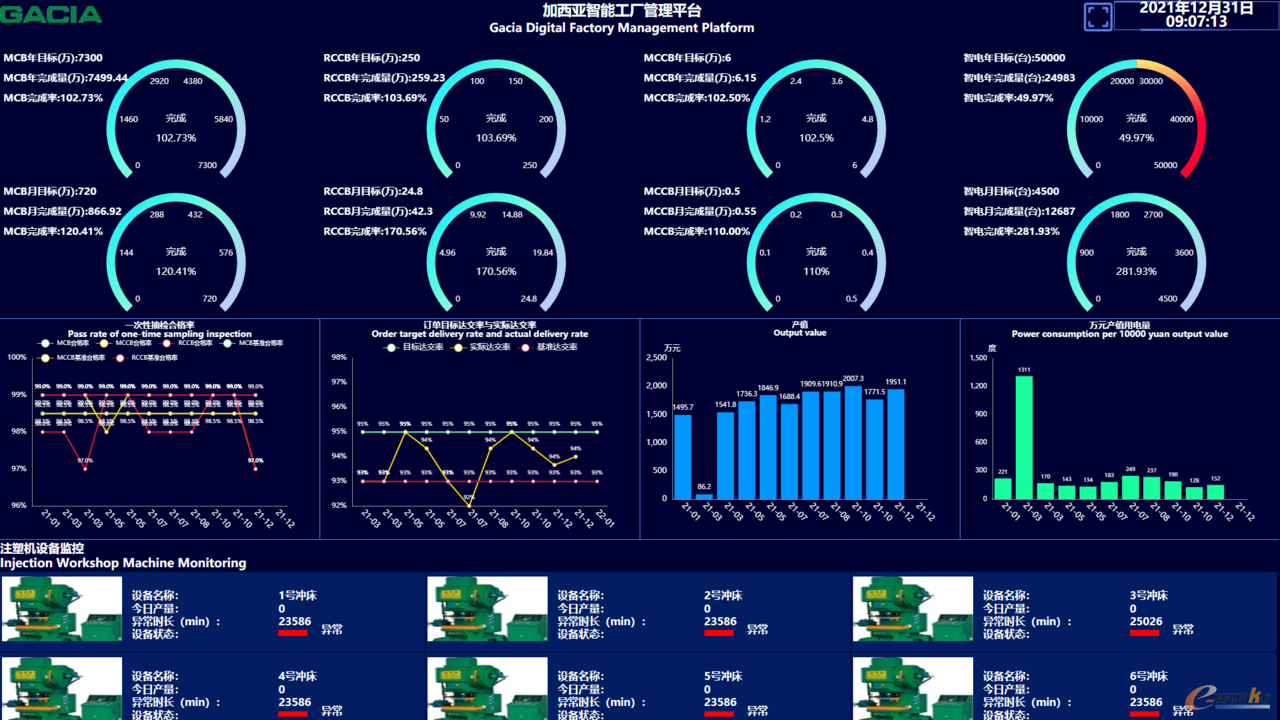
图17 加西亚中智能工厂可视化看板营指挥中心
(5)能源资源利用集约化
加西亚智能工厂建立了能源管理规范,建立能源综合管理监测系统,实现对主对要耗能设备实现动态监测与控制,为企业提供的生产作业提供辅助决策,实现能源资源利用集约化管理。
项目立足于自主研发制造的带计量和远程控制的互联网断路器产品自主开发自有的电力管理系统。其主要技术路线是监视和控制总用电量和智能控制终端动力和照明用电。
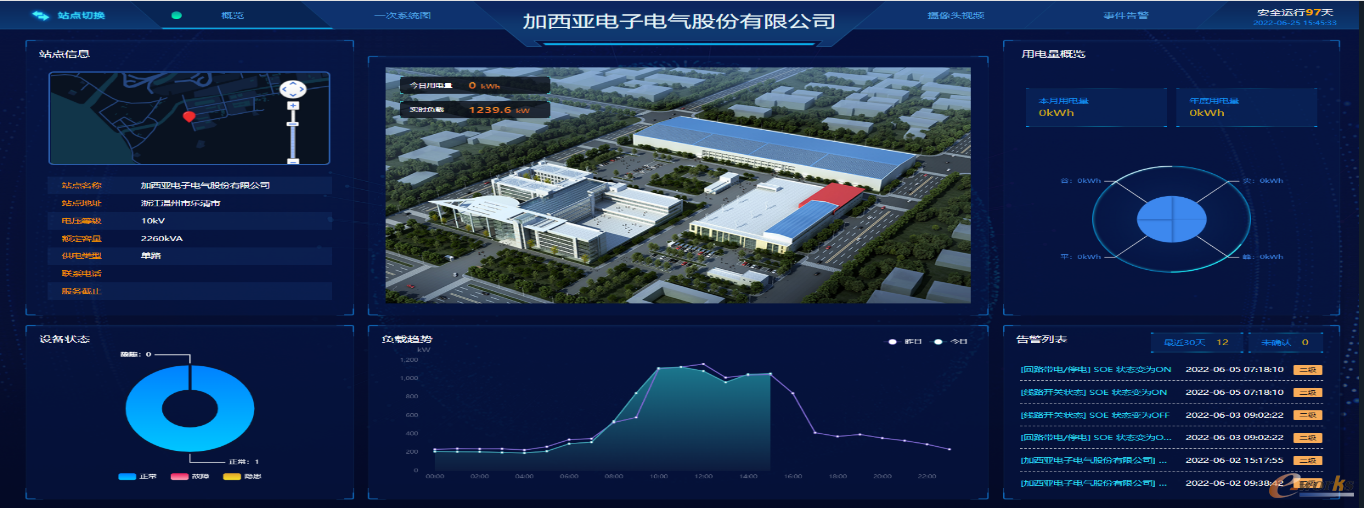
图18 能源综合管理监测系统展示
3.效益分析
在数字化转型和双碳经济背景下,公司加速向智能电气转型,加快与新能源融合发展。在现有装备基础上,公司投资近4000万元向智能断路器、直流、新能源电器转型发展,全面进行数字化、智能化改造,通过导入精益自动化生产模式以及设备自动化升级,设备国产化率达到98%以上,极大的提高了生产效率;通过PDM/ERP/MES/WMS等系统的集成应用,实现生产、管理、服务各环节的互联互通,实现产品的全程可追溯和全业务协同,做到透明化和智能化管理。改造升级后,建成集数字化设计、智能化生产、智慧化管理、协同制造、绿色制造、安全制造于一体的现代工厂,人均效能提升59.7%,运营成本降低21.5%,产品不良率降低35.4%,研发周期缩短33%,能源利用率提升32.6%。
本项目的实施过程,应用了数控加工装备、机器人、自动化线、自动检测设备、自动焊接、智能配送设备AGV等先进的智能化装备,应用了设备联网、数据采集和PLM/ERP/MES/WMS等信息化系统,较好的解决了断路器行业多品种小批量产品的生产制造过程管理和运营管理的智能化发展需求,在技术方面具有一定的领先性。
加西亚智能工厂遵循“一个流”精益理念,对注塑车间与小型断路器车间的整体设计,并利用三维建模技术、可视化技术和数字孪生技术建立车间数字孪生模式,通过设备联网和数据采集实现动态监控。
加西亚断路器的自动化产线解决了断路器生产全过程的自动化,解决行业中的普遍存在的难点,实现了自动组装、自动测试和自动包装的全过程的自动化,并且可兼容一极、二极、三极、四极的产品的快速换线和柔性生产,缩短了产品的周转周期,提高了生产效率(生产节拍为1.2秒/极),降低了制造成本,提高了产品质量,提高了生产过程连续性,生产效率提升50%以上。检测流水线的改造,提升了产品检测的效率,提升了检测数据的准确性,生产效率提升50%以上。加西亚断路器智能工厂项目的设备自动化水平在行业内拥有一定的领先性。
加西亚智能工厂智能工厂建设过程中,实施了PLM、MES、ERP、WMS等系统,构建了覆盖企业关键业务全流程的智能化管理体系。通过PLM系统,实现了设计研发数据管理、项目管理、物料管理、图文管理、产品管理、工艺管理、变更管理等功能,提升了公司的研发效率和质量。通过ERP升级提升实现财务管理、销售管理、采购管理、质量管理、库存管理、物料管理、需求管理、生产订单等功能完善了公司的业务及作业流程;通过MES系统实现生产进度、现场操作、质量检验、设备状态等生产现场数据自动上传,并实现可视化管理。通过WMS系统,实现物料库存管理、物料配送管理,实现库存管理的精细化。通过PLM/ERP/MES/WMS等系统的集成实现生产、管理、服务各环节的互联互通,支持工厂的全业务协同。推动企业在销售、采购、生产、加工、制造、流通、质量、财务各环节之间的数据关联、互通与共享,为断路器行业建立智能制造的技术、生产、物料规范、标准及管理体系的示范应用,同时,对于我国其他行业的智能化管理建设起到很好的引领,并具有重要而深远的影响。
加西亚断路器智能工厂的建设和实施,现有的装备基础上进行自动化改造,通过改造自动化焊接线、自动合模机器人、自动检测流水线,提高了自身生产过程的自动化水平,本项目的设备改造将引领断路器行业的发展方向,为断路器配件企业应用工业机器人消除了顾虑,为断路器行业建立智能制造的技术、生产、物料规范、标准及管理体系的示范应用。