本文以青山公司某变速器箱体的三维模型为研究对象,运用Altair公司的HyperWorks系列软件中的OptiStruct拓扑优化工具,借助有限元方法进行仿真优化,得到了变速器箱体的拓扑优化设计方案,减轻了箱体的重量,对复杂箱体类零件的轻量化设计具有较大的指导和借鉴意义。
1 概述
拓扑优化是在均匀分布材料的设计空间中找到最佳的设计方案。美国Altair公司HyperWorks系列软件中的OptiStruct[1]工具,采用HyperMesh作为前处理器从而实现连续体拓扑优化。连续体拓扑优化是把优化空间的材料离散成有限个单元(壳单元或者体单元)然后根据算法确定设计空间内单元的去留,保留下来的单元即构成最终的拓扑方案,从而实现拓扑优化。
变速器箱体结构复杂,功能繁多,对于结构设计有较高要求,因此其轻量化设计不仅要兼顾功能和工艺性,同时还要考虑刚度和强度的要求。在传统设计模式中,设计人员先凭经验对变速器箱体进行设计,在设计分析之后再修改原设计进行减重,反复修改设计不仅花费大量的时间,而且增加了人力和计算成本。使用拓扑优化方法对汽车变速器箱体进行轻量化设计,在设计初始阶段就已经考虑了各个设计指标,减少设计过程的反复迭代,缩短设计周期,提高设计质量。
2 变速器箱体的拓扑优化设计
本文以青山公司某款变速器箱体为例进行拓扑优化设计,并与现状态的变速器箱体进行对比。
2.1 定义拓扑优化设计空间
设计空间的定义是拓扑优化设计中重要的一环,如优化空间过小,得到的结果可能不是最优解;如给定空间过大,优化结果可能在装配过程中与其他零部件形成干涉,优化结果不符合实际情况。因此,在优化时必须综合考虑结构的装配性和使用位置的极限性,利用零部件最大的活动空间作为其优化设计空间[2]。
变速器箱体设计空间的定义流程如下:
(1)确定非设计空间:确定几何结构中不可改变的部分,如变速器箱体上的功能性螺栓孔、齿轮轴连接处均不可改变;
(2)确定设计空间:确定原结构中可以改变的部分,如变速器箱体上分布于内外表面的加强筋,箱体拓扑优化的主要目标是优化加强筋的数量及分布;
(3)设计空间的几何建模:去掉原变速器箱体上的所有加强筋,在需要加筋的位置建立几何包络面;
(4)划分设计空间网格:对各个设计空间分别用四面体划分网格;
(5)定义拓扑优化变量:对每个独立的设计空间分别定义拓扑优化变量。
图1展示了本例变速器箱体不同部位的拓扑优化设计空间。
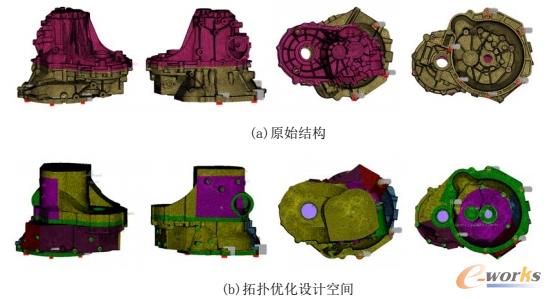
图1 箱体原始结构与拓扑优化设计空间对比图
2.2 对箱体施加载荷和约束条件
本文以一档100%即155Nm内部齿轮啮合力作用下的载荷作为工作载荷施加在箱体各轴承孔处,在变速器箱体大端面与发动机连接处的6个螺栓孔处施加全约束,载荷和约束如图2所示:
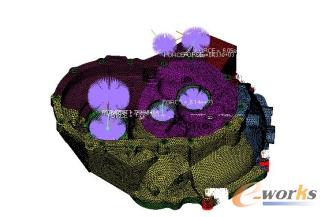
图2 箱体载荷和约束条件
2.3 定义拓扑优化目标
拓扑优化一般以柔度最小化(即刚度最大化)作为优化目标,优化目标的设定如图3所示:

图3 定义柔度和优化目标
2.4 定义拓扑优化约束
以青山公司变速器箱体有限元分析规范中的判定标准作为约束条件,设定应力的最大值不超过材料的屈服强度,同时设定箱体的拔模方向;设定箱体轴承孔中心点的最大径向位移和轴向位移;设定箱体的自由模态最小值和约束模态最小值;设定箱体体积比的上限为0.4。
2.5 拓扑优化结果解读
经过多次迭代后,得到了变速器箱体拓扑优化后的单元密度云图,如图4所示。云图表示优化后单元密度值,密度值越大的单元越重要,是设计中需要保留的单元(红色区域的单元是必须保留的),相对应的区域是需要保留的区域,密度值较小的区域则是优化后可以去除的区域。根据云图结果确定箱体上的加筋方案,如图4上蓝色曲线所示。
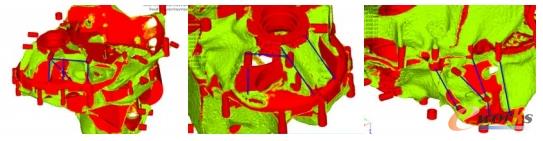
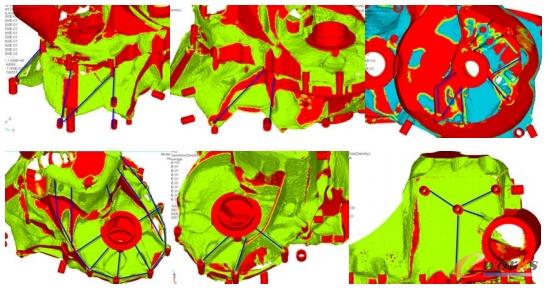
图4 拓扑优化单元密度云图
2.6 绘制新箱体几何模型
根据箱体拓扑优化结果确定的加筋方案,利用UG等三位造型软件重新设计该箱体,其几何模型如图5所示:
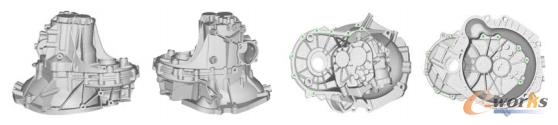
图5 拓扑优化后的箱体
2.7 对新箱体进行有限元分析
依据青山公司变速器箱体有限元分析规范对拓扑优化后的新箱体重新进行CAE分析。
3 拓扑优化结果对比
为了验证拓扑优化后新箱体的性能水平,以一档100%即155Nm工况为例,将现生产状态的原箱体和拓扑优化后新箱体的CAE分析结果汇总于表1,其左箱和右箱的应力对比云图如图6所示。
表1 两种状态箱体CAE分析结果汇总
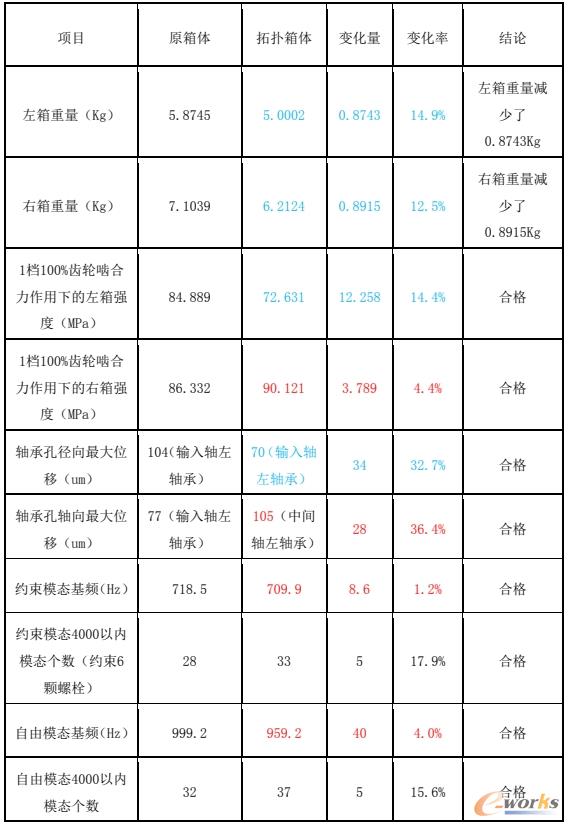
注:蓝色数据表示性能有所提升,红色数据表示性能有所下降。
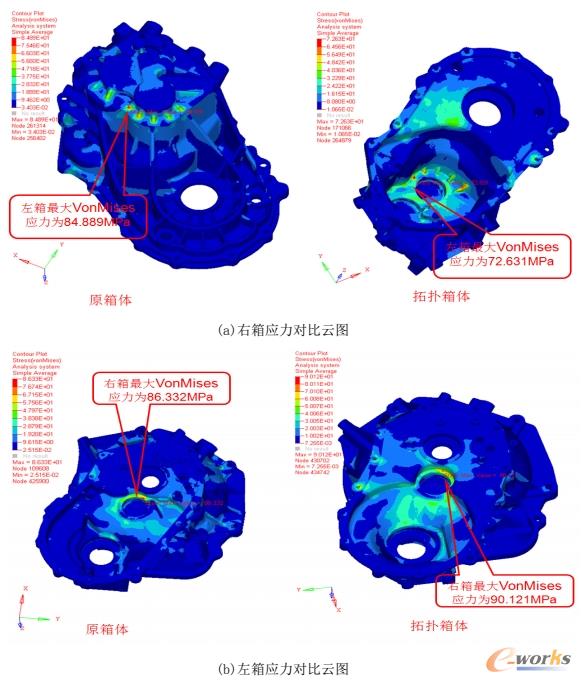
图6 原箱体和拓扑箱体应力对比云图
由表1中数据可以看出,拓扑优化后的新箱体在重量上比原状态箱体减小了1.7658Kg,但其静强度、刚度和模态水平均满足判定标准,有些指标甚至优于原状态箱体,在不改变原箱体性能表现的前提下,成功实现了箱体的轻量化设计,可以带来明显的经济效益。
4 总结
汽车轻量化已是大势所趋。本文从结构优化的角度出发,以青山公司某变速器箱体为例,结合当今流行的拓扑优化方法,在其基础上应用OptiStruct进行拓扑优化,成功的实现了轻量化设计。拓扑优化技术的应用不仅可以提高公司变速器正向设计分析能力,而且可以缩短设计周期,为公司带来明显的经济效益。
本文来源于互联网,e-works本着传播知识、有益学习和研究的目的进行的转载,为网友免费提供,并以尽力标明作者与出处,如有著作权人或出版方提出异议,本站将立即删除。如果您对文章转载有任何疑问请告之我们,以便我们及时纠正。联系方式:editor@e-works.net.cn tel:027-87592219/20/21。